Introduction
Face seal은 궤도차량 운용장비인 기동륜, 유동륜, 보기륜, 허브 등에 장착되는 부품으로 장비운영 시 내부오일 누유방지 및 외부 이물질을 차단하는 부품으로 단면도는 Figure 1에 나타내었다.1 내마모 합금주철 금속링과 NBR (Acrylonitrile Butadiene Rubber) 재질인 고무링으로 구성된 Face seal은 고무의 특성상 구동 및 사용온도에 영향을 많이 받는다. 현 궤도차량에 사용되는 Face seal의 운용가능 온도범위는 약 –30°C에서 100°C에 해당되는데, 고무는 사용온도에 따라 그 수명차이가 크기 때문에 국내의 급변하는 기후 및 극한지역 운용에 대비하여 Face seal에 사용되는 고무의 운용가능 온도확대가 필요하다. 현재 궤도차량용 Face seal에 사용되는 고무는 혹한기 기간 중 국내 극한 지역에서 운용 될 경우 고무 사용범위의 한계치에 가깝기 때문에 고무가 취화되는 등 내구성이 급격히 떨어진다. 이 때문에 극한의 온도에서 궤도차량의 내구성 확보를 위해 고무의 사용온도범위 확대가 요구된다.
일반적으로 Acrylonitrile (ACN) 함량이 낮을수록 NBR은 저온에서 유연성이 우수한 것으로 알려져 있다. 34% Acrylonitrile을 포함하고 있는 ACN 컴파운드는 –32°C~+107°C 범위에서 사용되고 Acrylonitrile 함량을 30%까지 낮출시 –40°C까지 사용이 가능하다. 또한 18~20%까지 Acrylonitrile 함량을 낮춘 Nitrile 컴파운드는 –54°C 에서도 유연성을 가질 수 있다. 하지만 Acrylonitrile 함량을 낮춰 저온에서의 유연성을 확보 할 경우 내열성 및 내유성이 희생된다.2 또한 NBR 고무는 이중결합을 가진 불포화고무로 오존에 취약하다.
본 연구에서는 이러한 NBR의 한계를 극복하기 위해 고무의 내한/내유성을 동시에 향상시키고자 ACN, 가소제, 가교제의 함량변화에 따른 내한/내유성의 변화에 대하여 알아보고, 이를 토대로 Face seal을 제조함에 있어 적합한 고무배합 시스템을 설계하고자 하였다.
Experimental
원료는 ACN 함량이 22%인 ㈜LG화학의 NBR2255와 ACN함량이 28%인 ㈜금호석유화학의 KNB25LM을 사용하였고 충전제인 카본블랙은 오리온사의 SRF 및 GPF, 용진유화의 Sunprax 682, 가소제는 LG화학의 DOA, 연화제는 LG화학의 St/A, 고무산화제 아연화는 한일아연의 ZnO, 노화방지제는 KAIRUN의 아민계인 RD와 FUDA사의 3C, 가황제는 미원화학의 S, 가황촉진제는 SUNSHIN사의 지아졸레 촉진제인 NS, DMUNIBOND사의 티우람계 촉진제인 TT를 병용 사용하였다.
시험배합은 밀폐식 혼합기에 Rotor속도 30+/–3 rpm 온도 105+/–5°C 로 NBR 원료고무 투입 및 1분간 혼련 후 배합약품인 연화제, 고무상용화제, 노화방지제, 보강충전제, 카본블랙을 투입하여 5분간 혼합하였고 추가로 가소제를 2분간 혼합하였다. 마지막으로 가황제, 촉진제를 3분 혼합하였다. 성형조건은 온도의 경우 150°C 기준으로 가교시간을 T90 × 1.5배 산정하여 T1~T20의 시험배합 조건으로 물성 비교시험을 하였다.
시험항목은 상태물성, 내열성, 내유성, 압축영구줄음율, 오존시험, 저온회복시험이며 시험조건 및 방법은 상태 물성시험의 경우 인장강도 및 연신율에 대해 KS M 6518의 시험편 규격에 의하여 아령형3호 시험편을 제작, 상온에서 500 mm/min 속도로 시험 측정하였고, 경도는 스프링식 경도계(shore A)로 측정하였다.
시험결과는 시편 4개중 최대 최소치를 제외하고 남은 2개의 DATA의 평균인 절사평균값으로 나타내었다. 내열시험은 시험조건인 120°C × 70 hr 동안 내열시험기내에 아령형 3호 시편을 걸어 회전하면서 공기가열 시켰으며 시험종결 후 인장강도, 신장율, 경도를 측정비교 하였다. 내유성 시험은 내유도를 측정하기 위해 시험조건 120°C × 70 hr에 IRM903오일, KS M 6518 시험편 규격인 아령형3호와 체적변화 시편을 침지시킨 뒤 시험종료후 오일을 제거하고 12시간 경과 후 기계적 성질 및 체적변화율을 측정 비교하였다. 압축영구줄음율 시험의 경우 시편을 두께 12.70±0.13 mm, 지름 29.0±0.2의 원기둥형으로 금형에 압축성형 하여 제작하여,3 상온에서 두께를 측정하고 시험조건인 120°C×70 hr 노출 후 두께를 비교하였고 스페이스를 장착하여 25%로 압축율 시험을 진행하였다. 오존시험의 시편은 길이 60 mm 너비 10 mm 두께 2 mm의 표면이 평활한 직사각형을 시편에 장작하고3 20% 신장하여 시험조건인 50 pphm × 40°C × 72 hr 노출시킨 후표면 Crack을 확인하였다. 저온탄성 회복시험 시편은 양끝을 6.5 mm 정사각형으로 하여 집은 후 집게 사이의 평행부분은 너비 2.0±0.2 mm, 길이 100±0.2 mm, 두께 2.0±0.2 mm인 I자형 시험편 을4 신장하여 저온인 73°C × 15분에 침지후 온도를 1°C 씩 상승시켜 탄성회복에 의한 복원성을 측정하였고 전열매질로는 에틸알콜을 사용하였다.
Results and Discussion
Face seal의 원자재로 사용되는 NBR 컴파운드는 ACN함량에 따라 최종제품의 물성이 달라진다. ACN함량이 증대함에 따라 내유성, 내마모성, 기계적 성질이 향상되지만 내한성, 신장성, 탄성은 저하된다. NBR고무는 다른 탄성체에 비해 좋은 기계적 성질과 높은 내마모성을 갖고 있으나 내오존성은 비교적 좋지않다.5 본 연구에서는 궤도차량용 Face seal 고무의 내한/내유성을 향상시키기 위하여 ACN함량이 30% 미만인 KNB25LM (ACN함량 28%)와 NBR2255 (ACN함량 22%)를 기본 폴리머로 사용하여 Face seal 제작시 적합한 배합을 알아보고자 하였다. 먼저 KNB25LM과 NBR 2255의 배합을 실시하여 물성을 분석한 후 ACN의 함량조절, 가소제, 가교제와 같은 배합첨가제의 배합비를 조절하여 Face seal에 최적인 배합비를 찾기 위한 시험을 진행하였다. Table 1, 2에는 본 연구를 진행함에 있어 사용될 기본 폴리머 배합의 조성 및 물리적 특성을 나타내었다.
Material | T-1 | T-2 |
---|---|---|
KNB 25LM | 100 | 0 |
NBR 2255 | 0 | 100 |
St/A | 1 | |
ZnO | 5 | |
RD | 2 | |
3C | 2 | |
sunflux 682 | 1 | |
SRF | 40 | |
GPF | 30 | |
DOA | 14 | |
Sulfur | 0.5 | |
NS | 1.5 | |
DM | 1.0 | |
TT | 1.0 |
배합시험 결과 ACN 함량이 높은 KNB25LM의 경우 NBR2255와 비교 하였을 때 내한, 내열성 및 압축영구줄음율이 상대적으로 부족하였다. ACN 함량이 높을수록 오일에 대한 저항성이 높아지지만 고무의 탄성과 압축영구줄음율, 내한성이 저하된다.6 내유시험의 경우는 두 소재 모두 다소 부족하였다. 그 이유는 고무와 오일간의 Solubility parameter값의 차이가 작으면 오일이 고무의 고분자 사슬로 침투하여 고무복합체의 팽윤이 되지만 오일간의 Solubility parameter값의 차가 크면 팽윤이 적게 일어난다.7
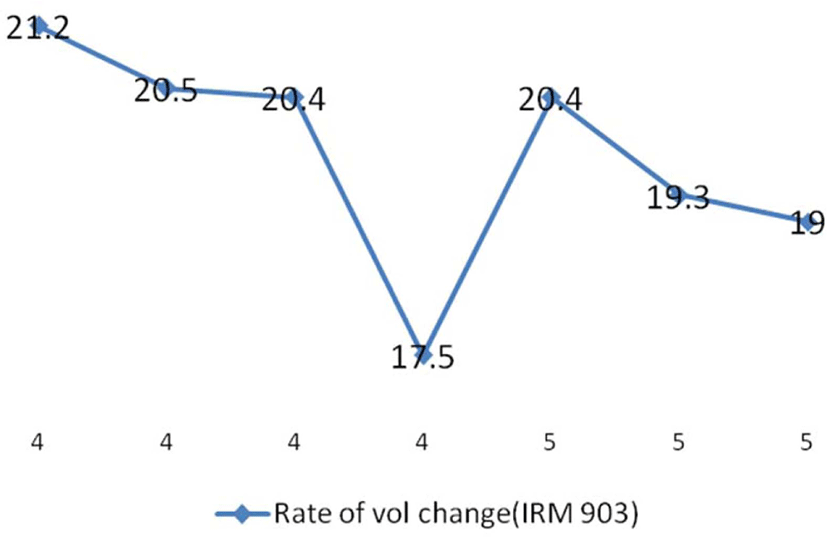
NBR의 Solubility parameter값은 ACN함량에 따라 18.4~21.5 MPa8,9 값을 가지며10 ASTM IRM901은 13.9 MPa,8,9 IRM 903은 18 MPa8,9 값을 가진다.11,12 따라서 ASTM IRM901보다 IRM903이 NBR고무 고분자 사슬로의 침투가 더 쉬워 물성값을 급격히 변화시킨다.6
실험에서는 NBR2255 고무에 대하여 내열성과 내유성을 보강하기 위한 실험을 진행하였고 그 결과를 기술하였다. 또한 시험배합조건에서 가교제, 가소제, 보강제의 배합비를 조절하여 내열/내유성개선을 시도하였다.
두 시험결과에서 모두 DOA의 함량이 14 phr인 경우 12 phr인 경우에 비하여 내한성시험인 TR-10의 결과가 더 낮은 온도에서 나타났다. 일반적으로 가소제는 고무의 내한성을 확보하기 위해 많이 사용하는 첨가제로 가소제의 함량에 따른 내한성 변화시험을 기술하였다. NBR2255의 경우 Table 2의 시험에서 내유성이 타 고무 대비 열세하였는데 이를 개선하기 위해 무기배합제, 가소제, 가교제의 함량을 조절하였다. 그 결과 IRM 903에 대한 내유성의 경우 T-7을 제외하고 무기첨가제인 ZnO의 함량이 더 높을 때 부피변화율이 20이하로 우수한 내유성 결과를 얻을 수 있었다. ZnO는 유황가교고무에 있어서 Stearic Acid와 함께 활성제(Activator)로서 작용하여 가교결합 형성의 유효성을 증가시키고 가교밀도를 향상시키는 역할을 한다. IRM 903에 대한 내유성시험에서 T8 & T9와 같이 ZnO 첨가량이 더 높을 때(5 phr) 부피변화율이 우수하게 나타난 것은 ZnO가 4 phr 함량일 때보다 가교밀도의 증가에 따른 팽윤(swelling)에 대한 저항의 증가결과로 판단된다.13
Material | T-3 | T-4 | T-5 | T-6 | T-7 | T-8 | T-9 |
---|---|---|---|---|---|---|---|
NBR 2255 | 100 | ||||||
St/A | 1 | ||||||
ZnO | 4 | 4 | 4 | 4 | 5 | 5 | 5 |
RD | 2 | ||||||
3C | 2 | ||||||
sunflux 682 | 1 | ||||||
SRF | 40 | ||||||
GPF | 30 | ||||||
DOA | 12 | 12 | 14 | 14 | 12 | 12 | 14 |
Sulfur | 0.5 | 0.6 | 0.5 | 0.6 | 0.5 | 0.6 | 0.5 |
NS | 1.5 | ||||||
DM | 1.0 | ||||||
TT | 1.0 |
KNB25LM이 NBR2255 대비 IRM 903에서의 내유성 변화에서 체적변화가 더 우수한 결과를 얻었기 때문에 NBR2255의 부족한 내유성을 극복하기 위해 ACN의 함량이 서로 다른 두 고무소재를 혼합하여 사용함으로써 내한/내열/내유성이 모두 향상되기 위한 폴리머 배합비를 구하였다.
NBR2255의 경우 KNB25LM에 비해 낮은 ACN 함량으로 인하여 우수한 내한성을 가지고 있으나 IRM 903에 대하여 내유성이 열세한 결과를 얻었다. 이는 무기배합제 및 가교제 함량을 조절하여 내열/내유성을 향상시킬 수 있었다. 본 절에서는 ACN함량이 서로 다른 두 고무소재를 함께 사용함으로써 NBR2255의 부족한 내열성과 IRM 903에 대한 내유성을 극복하고자 하였다. 또한 KNB25LM 배합에 의한 내한성 부족 부분을 해결하기 위해 가소제인 DOA의 함량을 10~20 phr까지 조절하였다. Table 5, 6은 KNB25LM과 NBR 2255의 배합비를 조절하여 ACN함량을 각각 23.2%, 23.8%로 조절하여 실험한 배합표를 Table 5, 6에 나타내었고 그 결과를 Table 7, 8에 나타내었다. Table 7, 8에서 보면 NBR2255와 KNB25LM을 함께 배합한 경우 가소제의 함량이 16 phr 보다 작은 경우에는 저온회복시험이 −50 이상으로 내한성이 열세한 값을 보였다. 같은 가소제의 함량인 14 phr에서도 NBR2255 단독으로 배합하였을 때보다 더 높은 온도의 결과를 보이는데 이는 KNB 25LM이 함께 배합되면서 증가된 ACN 그룹이 저온에서 주쇄의 유동을 방해한 결과라고 볼 수 있다.
Material | T-10 | T-11 | T-12 | T-13 | T-14 | T-15 |
---|---|---|---|---|---|---|
NBR 2255 | 80 | |||||
KNB 25LM | 20 | |||||
St/A | 1 | |||||
ZnO | 5 | |||||
RD | 2 | |||||
3C | 2 | |||||
sunflux 682 | 1 | |||||
SRF | 40 | |||||
GPF | 30 | |||||
DOA | 10 | 12 | 14 | 16 | 18 | 20 |
Sulfur | 0.6 | |||||
NS | 1.5 | |||||
DM | 1.1 | |||||
TT | 1.0 |
Material | T-16 | T-17 | T-18 | T-19 | T-20 | T-21 |
---|---|---|---|---|---|---|
NBR 2255 | 70 | |||||
KNB 25LM | 30 | |||||
St/A | 1 | |||||
ZnO | 5 | |||||
RD | 2 | |||||
3C | 2 | |||||
sunflux 682 | 1 | |||||
SRF | 40 | |||||
GPF | 30 | |||||
DOA | 10 | 12 | 14 | 16 | 18 | 20 |
Sulfur | 0.6 | |||||
NS | 1.5 | |||||
DM | 1.1 | |||||
TT | 1.0 |
Figure 3에서 볼 수 있듯이 ACN 함량이 낮을 경우 더 낮은 온도에서 Crack이 발생하였으며, 두 실험 모두 가소제인 DOA의 함량이 증가할수록 내한성이 더 향상되는 것을 확인 할 수 있었다.
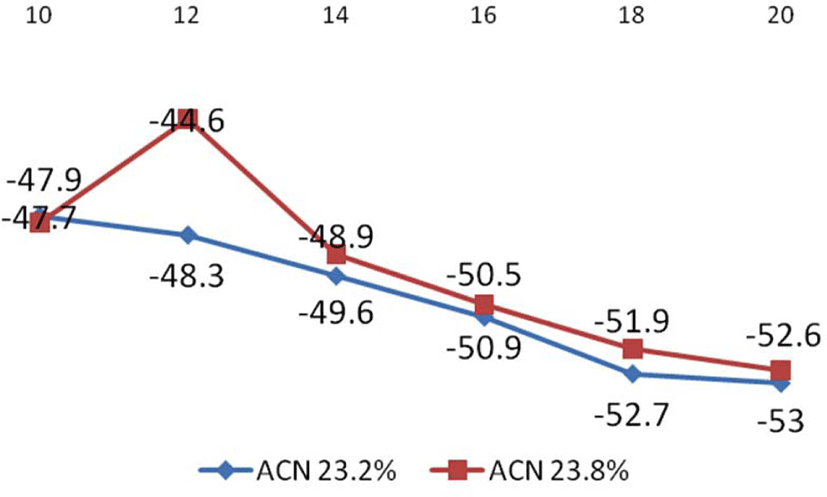
Figure 4에는 DOA함량에 따른 내유성 시험결과 중 부피변화율에 대한 값을 그래프로 나타내었다. Figure 4의 IRM901에 대한 내유성 결과인 (a)에 나타난 바와 같이 DOA의 함량이 증가 할수록 수축하는 결과를 확인 할 수 있었으며 (b)의 경우 기존의 크기보다는 팽창하지만 DOA함량이 증가할수록 팽창의 정도가 줄어 드는 것을 확인 할 수 있었다. T-19를 제외한 모든 시험에서 오일의 종류에 관계없이 내유성이 향상되는 것을 확인하였다. Face seal의 경우 외부의 이물질 차단 및 내부 오일 누유를 방지하는 것이 목적인데 외부 오일에 노출 될 경우 수축보다는 팽윤을 하는 것이 누유방지에는 더욱 유리하다. 두 결과를 놓고 보면 본 소재를 활용한 Face seal의 경우 IRM901의 주 성분과 같은 파라핀계 오일에 노출되는 것 보다 IRM903과 같은 나프틴계 오일에 노출되는 것이 Face seal로 사용하는데 있어 오일 누유방지에 더 유리 할 것으로 생각된다.
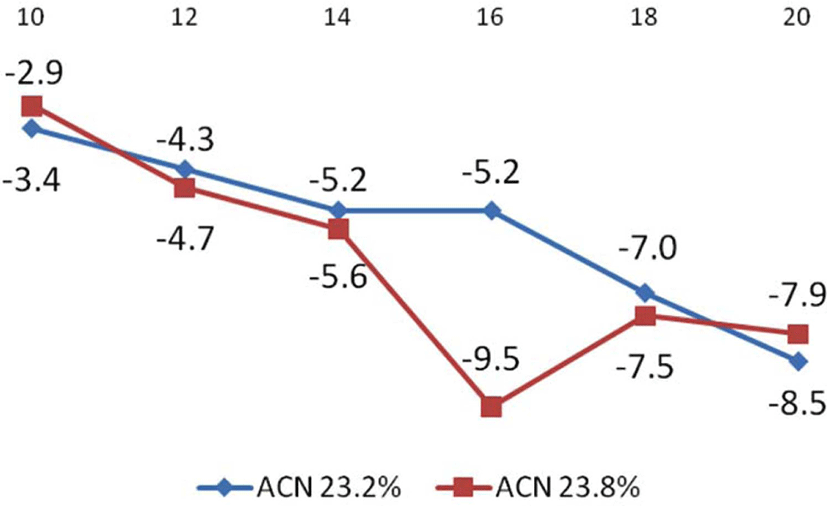
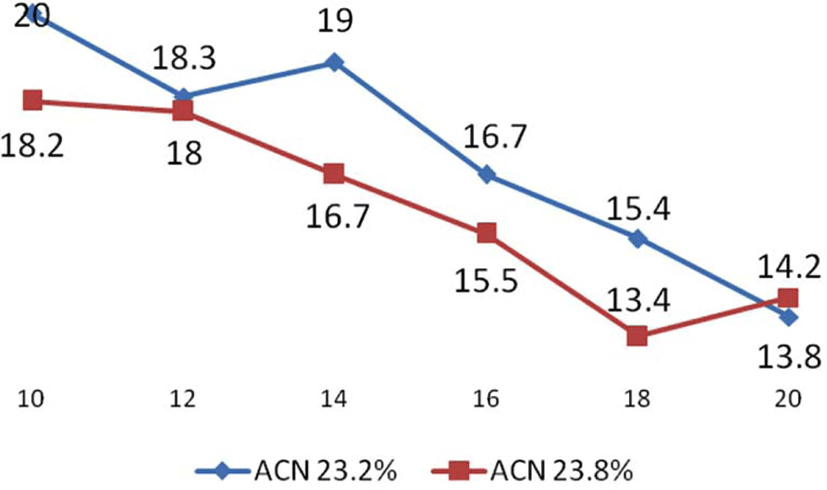
Conclusions
본 연구에서는 Metal face seal의 고무링으로 사용되는 NBR의 내한/내유성을 향상시키기 위한 최적고무배합에 관한 연구를 진행하였다. 그 결과는 다음과 같다.
내유성과 내한성은 폴리머의 ACN 함량조절과 함께 접촉시험유 ASTM IRM901 및 IRM903에 대한 DOA의 추출(Extraction)과 팽윤(Swelling)을 고려하여 18 phr 첨가하여 동시에 만족시킬 수 있었다. 이상과 같이 확보된 고무배합의 제품에 대한 장기적인 신뢰성 확보를 위해서는 사용 중 실제 접촉되는 Gear oil과 Brake oil의 Aniline point, Solubility parameter 등의 인자를 고려한 DOA와의 반응(팽윤&추출)에 대한 추가적인 관찰이 필요하다고 판단된다.