Introduction
폴리우레탄 폼은 가볍고 단열성이 우수하여 건축용 단열재로 널리 사용되고 있다. 그러나 주성분이 유기물이어서 화재에 취약한 단점이 있다. 우레탄 폼의 난연성을 보완하기 위하여 상업적으로 널리 사용되는 할로겐 난연제는 가격이 저렴하나 환경과 인체에 유해하기 때문에 사용을 규제하는 추세이다. 할로겐계 난연제의 사용을 지양하는 사회적 요구와 점차 심화되는 법적 규제에 대비하여 친환경적으로 우레탄 폼의 난연성을 높이는 연구가 활발히 진행되고 있다.
다양하고 광범위하게 수행되는 우레탄 폼의 난연성과 열안정성을 개선하는 활동의 일부를 소개하자면, 난연성을 가지는 나노 첨가제를 우레탄 폼에 도입하여 우레탄 폼의 난연성과 열안정성 기타 물성을 개선시키는 연구와,1-5 인계 또는 멜라민계 난연제를 우레탄 폼에 도입하여 폴리우레탄의 난연성 또는 열적특성을 개선시키는 연구 등이 있다.6-9
위와 같이 유기나노점토 또는 친환경적인 난연성분을 우레탄 폼에 도입하여 난연성과 열적 특성을 개선시키는 방법 이외에, 폴리우레탄폼을 합성하는 과정에서 폴리이소시아누레이트(polyisocyanurate)를 생성시켜서 우레탄과 이소시아누레이트 공중합 형태의 poly(urethane-isocyanurate) (PUIR) 폼을 만드는 시도도 수행되었다.
PUIR 폼은 이소시아네이트의 N=C=O 기와 폴리올의 hydroxyl 기가 반응하여 생성되는 우레탄기와 이소시아네이트가 과량인 조건(NCO index > 200)에서 NCO의 삼량화(trimerization) 반응으로 생성되는 isocyanurate ring이 같이 존재하는 hybrid 구조를 가지고 있다.10,11
PUIR에 관한 연구들을 소개하자면, Nicholas와 Gmitter는12 주원료인 toluene diisocyanate (TDI, 2,4- and 2,6-isomers 80/20 혼합물)와 adipate-triol의 당량비 6.3:1 조건에서 Fluoro-carbon 11 발포제와 3급 아민 촉매를 사용하여 triphenyliso-cyanurate foams을 만들고 열안정성을 연구하여, 이 PUIR 폼이 288℃에서도 안정하다는 것을 보고하였다. K. C. Frisch와 그 동료들은13 polyether diol과 triol, MDI를 주원료, 3급 아민을 촉매로 사용하여 PUIR 폼을 합성하고 TGA로 열분해 특성을 연구한 결과, PUIR에 polyether diol과 triol의 분자길이가 작을수록 그리고 원료 조성에서 polyol의 함량이 감소할수록 열안정성이 증가하여 공기 중에서 열분해 시에 500℃에서 분해 잔량이 50% 이상인 것을 보고하였다. Semsarzadeh와 Navarchian는14 dibutyltin dilaurate (DBTDL)과 ferric acetyl-acetonate (FeAA)를 촉매로, 주원료로 TDI와 PPG를 사용하여 NCO index와 촉매 농도를 변화시키며 PUIR을 합성하고 열적 특성을 연구하였다. 이들은 PUIR의 열분해가 200℃(우레탄 분해), 355~385℃ (PPG chain 절단), 400~550℃ (isocyanatr/cabodiimide 분해)의 3단계로 일어나며 NCO index가 클수록 열안정성이 좋아지고 FeAA 촉매에 비하여 DBTDL 촉매로 합성한 PUIR의 열안정성이 더 좋다고 보고하였다.
PUIR의 열분해에 대한 선행 연구 결과를 종합하면 다음과 같다.12-19 약 180~220℃에서 PUIR에 함유된 우레탄기의 분해가 시작되어 carbodiimide와 우레아를 거쳐서 isocyanurate로 전환된다. PUIR의 Isocyanurate와 우레탄기의 분해로 생성된 Isocyanurate 기는 400~450℃에서 분해가 이루어지며, 특히 isocyanurate ring 구조가 char 형성을 촉진하여 열분해에 대한 저항성을 높이는 것으로 알려져 있다.
비록 PUIR 폼의 난연성과 열안정성이 우레탄 폼에 비하여 우수하지만, PUIR 단독으로는 준불연급의 난연성을 갖추지 못한다. 본 연구는 PUIR에 친환경 난연성분을 도입시켜서 준불연급의 PUIR 복합체 폼을 개발하기 위하여 수행되었다. 이런 시도의 첫 단계로 PUIR 폼의 제조를 위한 최적조건을 확립하기 위하여, NCO index와 촉매종이 삼량화 반응과 겔화 반응에 주는 영향에 대하여 고찰하였다.
삼량화 반응을 촉진하는 촉매는 다양하게 보고되고 있다.20-23 가장 일반적 촉매로는 루이스 염기인 3급, 4급 아민과 루이스의 산인 카르복실산 금속염이 사용된다.11 아민 촉매와 Tin 촉매도 삼량화 반응에 사용되나, 반응속도가 느린 것으로 알려져 있다.22 PUIR 합성 과정에서 NCO index가 낮은 경우에는 이소시아네이트의 NCO 기가 삼량화 반응에 상당량 소요되므로, 삼량화 반응 이후에 폴리올의 –OH 기와의 부가중합이 충분하게 진행되지 못하여 분자량이 커지지 않는다. 그 결과 연속적으로 결합된 형태를 이루지 못하고 쉽게 부스러진다. 한편, 삼량화 반응 후에 NCO 기가 남아있더라도 hydroxyl 기를 2개 이상 가지는 폴리올을 사용하는 경우에는 cross-linking이 심화되어 너무 단단하고 가공이 어려워지므로 PUIR 제조에 사용되는 폴리올은 양말단에 –OH기를 가지는 에스테르 형태의 디올이 주로 사용된다.10
본 실험에서는 PUIR 폼을 합성하기 위한 폴리올로, PUIR 폼의 발포과정에서 반응-생성물의 흐름성을 높이기 위하여 분자량이 350 정도인 에스테르 디올을 합성하여 사용하였다. 촉매로는 유기금속촉매 1종(Potassium-2-ethylhexanoate, Dabco K-15)과 3급 아민으로 분자 구조에 hydroxyl 기를 포함하고 있는 2종의 반응성촉매(2,4,6-tris(dimethylaminomethyl)phenol (Dabco TMR-30), 2-(2-N,N-dimethyl aminoethyl-N-methyl-amino)ethanol (Toyocat RX-5))를 사용하였다. Figure 1은 본 실험에서 사용한 촉매들의 분자 구조를 보여준다. Potassium-2-ethylhexanoate의 선정은 이소시아네이트와 알콜의 gelation 반응에 적용한 아세테이트 금속염 촉매 중에서 Potassium acetate 촉매가 이소시아네이트의 반응활성을 가장 높게 만든다는 S. E. Entelis and O. V. Nesterov의23,24 선행 연구결과를 반영한 것으로, potassium-2-ethylhexanoate는 이소시아네이트의 삼량화 반응뿐만 아니라, 우레탄 gelation 반응도 빠르게 진행시킬 것으로 예상한다. Dabco TMR-30와 Toyocat RX-5의 hydroxyl기는 이소시아네이트와 반응하여 PUIR에 화학적으로 결합되므로, 비반응성 아민 촉매가 삼량화 반응과 gelation 과정에서 기화되어서 촉매의 농도가 낮아지고 폼 형성과 저장 과정에서 역한 냄새가 발생하는 문제를 완화시킬 수 있다.
Experimental
PUIR 폼 제조에 필요한 polyester-diol은 Tin(II)-2-ethyl-hexanoate (순도 99%, Sigma-Aldrich) 촉매를 사용하여 di- ethylene glycol (DEG, 순도 99%, 대정화금)과 adipic acid (AA, 순도 99%, 대정화금)의 에스테르 반응으로 합성하였다. 4,4-diphenylmethane diisocyanate (MDI, 순도 97%)는 대정화금에서 구입하였다. 삼량화 반응과 gelation 반응을 위한 촉매인 Potassium-2-ethylhexanoate (Dabco K-15, 순도 95% up)와 2-(2-N,N-dimethyl aminoethyl-N-methyl amino)ethanol (Toyocat RX-5, 순도 97%)은 TCI에서, 2,4,6-Tris(dimethyl aminomethyl)-phenol (Dabco TMR-30, 순도 95%)은 Sigma-Aldrich에서 구입하였다. 발포제로 증류수를, 실리콘계 계면활성제로 L-6900 (Momentive사)을 사용하였다. 모든 촉매들과 DEG, AA, MDI 등의 시약들은 별도의 정제 과정을 거치지 않고 사용하였다.
반응기에 COOH/OH 당량비가 0.5가 되도록 AA와 DEG를 투입하여 양말단에 OH기를 갖는 [(diethylene glycol)adipate]-diol을 합성하였다. 에스테르화 반응온도는 130℃부터 170℃까지 5℃(±0.1℃) 간격으로 단계적으로 높이며 제어하였다. 촉매인 Tin(II)-2-ethylhexanoate는 반응물과 함께 투입하며, 반응기 내부 물질을 범용교반기(200 rpm)로 균일하게 교반하였다. 약 3 psig의 N2를 반응기에 계속 흘려주어서 부생성물인 H2O를 제거하며 정반응을 유도하였다. H2O 제거 과정에서 반응물 중에서 DEG가 함께 유출되어 COOH/OH 당량비가 변하고, 이의 영향으로 생성물인 [(diethylene glycol)-adipate]diol의 분자량이 커지는 것을 방지하기 위하여 packed distillation column을 이용하여 DEG가 유출되는 것은 억제하고 H2O만 제거되도록 유도하였다. 반응-생성 혼합물의 acid value를 측정하여 반응 진행 정도를 계산하였으며, acid value 값이 변하지 않는 시점에서 반응을 종결 지었다. 반응종료 점에서 생성물의 평균전환율은 98.2% (± 0.2%)이었다. 이렇게 합성한 [(diethylene glycol)adipate]diol을 PUIR 폼 제조에 사용하였다.
PUIR 폼 합성에 사용한 원료들의 조성비는 Table 1에 있다. NCO index를 100~300에서 변화시켰으며, 발포제(H2O)는 2.3 php, 실리콘 계면활성제(L-6900) 1.5 php, 촉매 4.0 php로 고정하였다. 발포용기에 [(diethylene glycol)adipate]diol과 H2O, 실리콘계 계면활성제 (L-6900), 촉매를 투입하여 3000 rpm에서 60초간 혼합한 후에 MDI를 투입하고 3000 rpm에서 10초간 반응시켜 PUIR foam을 제조하였다. 발포한 PUIR foam은 50℃에서 24시간 숙성시켰다. 이렇게 제조한 PUIR 폼을 폼 제조 시에 적용한 NCO index 값에 맞추어 B-XXX (XXX는 NCO index 값)로 명명하였다.
[(diethylene glycol)adipate]diol 합성 반응의 종말점과 전환율 계산에 사용된 Acid value는 아래의 방법으로 측정하였다. 반응-생성물 시료 0.2~0.3 g을 0.1 N HCl 표준 용액 10 mL에 용해시킨 후, 페놀프탈레인 지시약을 소량 첨가하고 0.1 N KOH 표준 용액으로 적정하여 측정하였다. 반응 과정에 시료가 0.1 N HCl 용액에 녹는 정도가 불량한 경우에는 KS M 0065의 Acid value 측정법을 사용하여 측정하였다. 합성한 [(diethylene glycol)adipate]diol의 분자량 계산에 사용되는 수산화값은 KS M 0065에서 제한 방법으로 측정하였다.
FT-IR 분석을 통하여 [(diethylene glycol)adipate]diol과 PUIR의 특성 피크를 확인하여 생성물의 정성과 정량 분석을 수행하였다. PUIR 폼의 열분해 온도와 속도, 분해 후 잔량 등과 같은 열적 특성을 Air 기류 하에서 TGA (Setaram instrumentation, SETSYS Envolution)를 사용하여 50℃에서 1000℃ 영역에서 10℃/min으로 승온시키며 분석하였다.
Results and Discussion
Figure 2는 반응 전의 AA와 DEG의 혼합물과 이로부터 합성한 [(diethylene glycol)adipate]diol의 FT-IR spectra이다. AA와 DEG 혼합물의 spectra는 2400~3600 cm−1의 넓은 영역에서 AA의 카르복실 기의 -OH stretching에 의한 피크와, 1695 cm−1와 1280 cm−1에서 각각 carboxy기의 수소 결합된 C=O stretching 피크와 수소 결합된 C-O stretching에 의한 피크, 1060 cm−1에서 1차 알콜의 C-O stretching 피크를 보여준다. 반면에 이로부터 합성된 [(diethylene glycol)adipate]diol의 spectra에는 3300~3600 cm−1영역에서 양말단의 hydroxyl group에 의한 -OH stretching 피크, 1730 cm−1와 1130 cm−1에서 ester기의 C=O stretching과 C-O stretching 피크가 강하고 날카롭게 나타난다. [(diethylene glycol)adipate]diol의 spectra에서 보이는 C=O stretching과 C-O stretching 피크의 위치가 카르복실 기의 C=O와 C-O stretching에 의한 피크보다 낮은 wave-number로 이동한 것으로부터, 반응원료인 AA의 카르복실 기가 수소결합이 제한적으로 일어나는 에스테르로 전환된 것을 확인할 수 있다. 1060 cm−1에서 보이는 1차 알코올의 C-O stretching에 해당하는 피크를 같이 감안하면, 생성물은 Figure 3에 있는 [(diethylene glycol)adipate]diol의 구조를 가지고 있음을 알 수 있다.
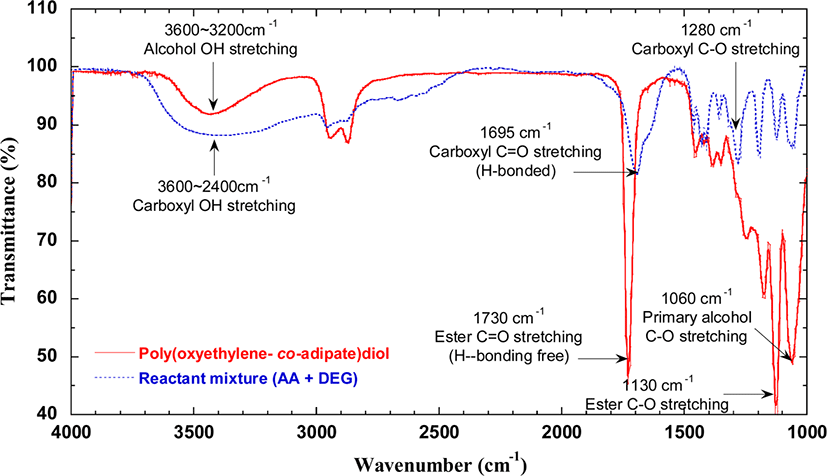
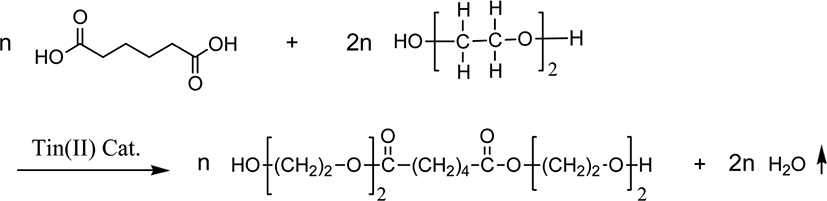
Figure 3은 관능기가 각각 2개인 AA와 DEG를 당량비(EquAA/EquDEG)가 0.5인 조건에서 반응시켜서 [(diethylene glycol)adipate]diol을 합성하는 에스테르 반응을 보여준다. [(diethylene glycol)adipate]diol의 분자량을 직관적인 Carothers equation을 사용하여 계산한 분자량과 [(diethylene glycol)-adipate]diol 생성물의 OH value를 측정하여 구한 분자량을 Table 2에 비교하였다. Carothers equation으로 계산한 분자량보다 OH value 측정값으로 구한 분자량이 약 44 정도 높은 것은 에스테르 반응 과정에서 H2O가 제거될 때 DEG도 같이 제거되어 reactant ratio (r=EquAA/EquDEG) 값이 초기 0.5에서 반응종료 시에 0.55로 증가하였기 때문이라 추정된다.
MW (g/mol) | Reactant ratio EquAA/EquDEG | |
---|---|---|
1Calculated Mn using Carothers Eq. | 330.7 | 0.5 |
2Determined Mn using the measured hydroxy value | 374.7 | 30.55 |
1 The molecular weights were calculated using Carothers equation, , DPN = (1+r)/(1+r−2rp) with the value of Mo=108, Mc=18, and p=0.982. The conversion was measured from the acid value of the reactant-product mixture.
PUIR foam 발포 시에 Base ester-diol([(diethylene glycol)-adipate]diol))과 MDI의 조성은 NCO index 100~300에서 맞추어 변화시켰으며, 기타 조성물의 농도는 발포제(H2O) 2.3 php, 실리콘 계면활성제(L-6900) 1.5 php, 촉매 4.0 php로 고정하였다(Table 1 참조). 합성한 PUIR 폼을 구성하는 관능기의 종류와 생성량을 확인하기 위하여 ATR mode로 FT-IR 분석을 시도하였다. 문헌에서 보고된 PUIR foam에 포함된 관능기들의 IR spectra를 참고하여,25-29 본 실험에서 발포한 PUIR 폼의 특성 피크를 Table 3에 정리하였다.
Figure 4는 [(diethylene glycol)adipate]diol과 MDI를 주원료로 사용하고 H2O로 PUIR 폼을 발포하는 과정에서 일어나는 주요 반응의 유형을 보여준다. 반응물인 MDI의 phenyl 기는 반응에 참여하지 않고 생성물에 원래의 형태로 존재하는 반면에, Urethane (U1), Isocyanurate (ICU), Urea (U2) 기는 반응 후에 생성된다. 반응 유형에 무관하게 항상 본래의 구조를 유지하는 phenyl 기의 흡광도를 기준으로 U1, ICU, U2와 반응물인 MDI의 NCO 기의 흡광도를 정규화하여, PUIR 폼에 생성된 Urethane (U1), Isocyanurate (ICU), Urea (U2) 기와 미반응 상태로 남아있는 NCO 기의 양의 변화를 분석하였다. Figure 5는 Dabco K-15를 촉매로 사용하여 합성한 B-100의 FT-IR spectra이며, 이 중에서 특정한 관능기의 흡광도를 phenyl ring의 stretching 피크(1598 cm−1)의 흡광도 값으로 정규화한 값을 Table 4에 정리하였다. B-100을 포함하여 Table 1에 있는 모든 PUIR 폼의 FT-IR 특성피크는 정규화시켜서 사용하였다.
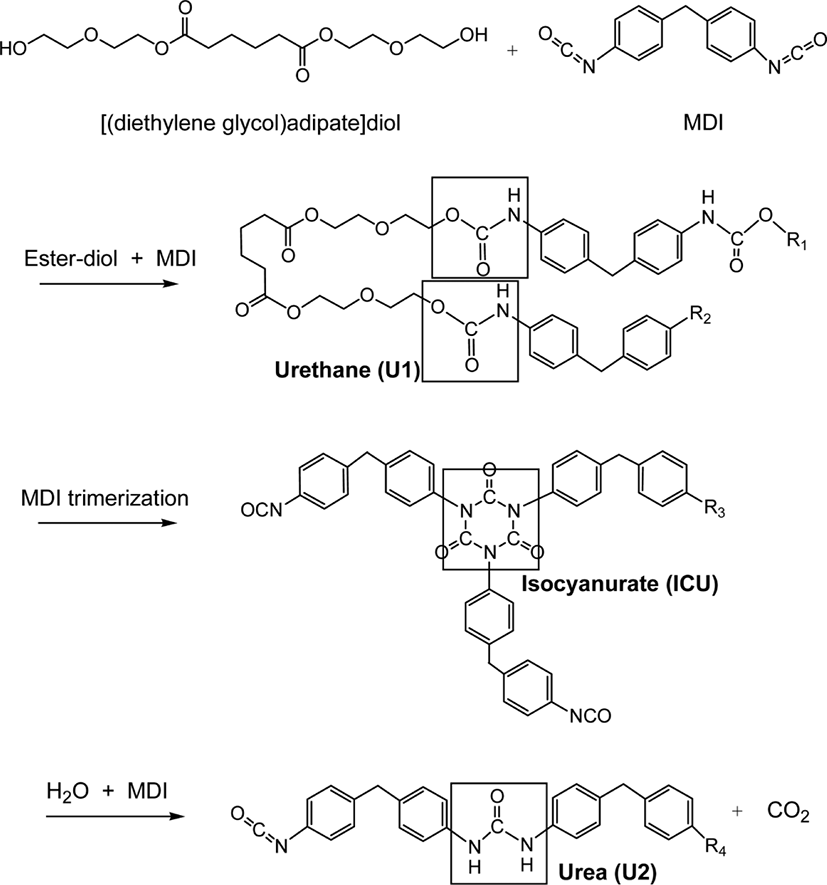
Figure 6은 Dabco K-15를 촉매로 사용하여 발포한 B-250를 50℃에서 24시간 숙성시키며, 반응이 더 진행되는지를 알기 위하여 FT-IR로 성분 변화를 분석한 결과를 보여준다. 반응 시작 후 5분 이내에 측정한 PUIR 폼의 IR spectra에 NCO 피크가 나타나지 않았으며, ICU (1411 cm−1), C=O (1710 cm−1), Urea C=O (1654 cm−1), N-H (1510 cm−1) 피크의 흡광도를 정규화시킨 A(i)/A(phenyl) 값이 시간이 경과하여도 일정하였다. 이로부터 PUIR foam 합성은 반응이 바르게 진행되어서 발포 초기에 대부분의 반응이 완료 되는 것으로 추정된다.
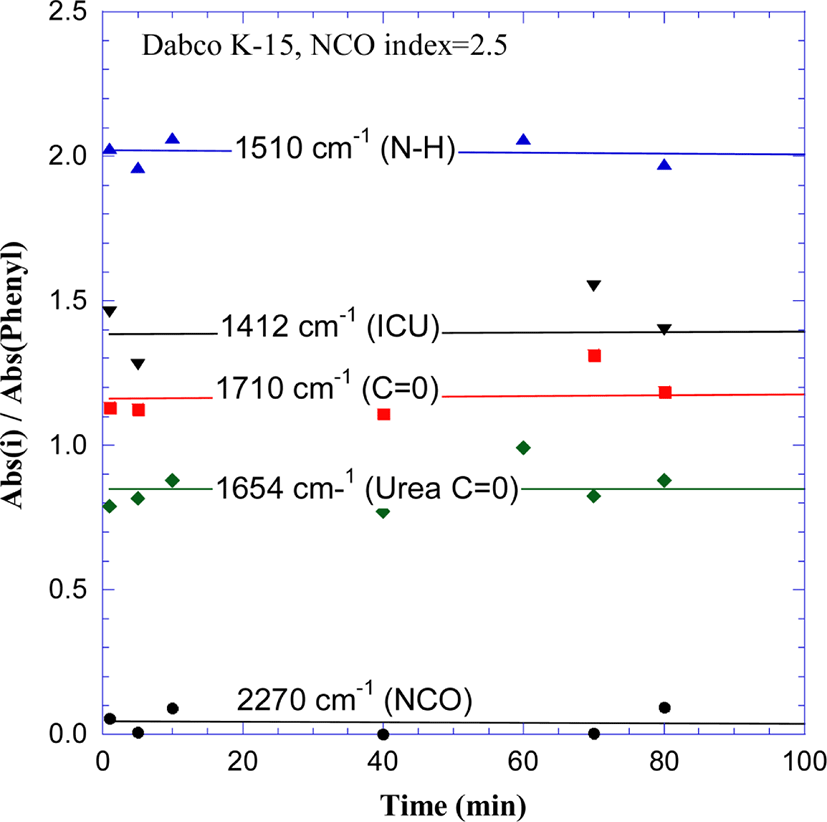
Figure 7~9는 각각 Dabco K-15, Dabco TMR-30, Toyocat RX-5를 사용하여 NCO index를 변화시키며 PUIR foam을 발포하고, 그들의 FT-IR spectra를 정규화한 결과를 그린 것으로, PUIR 폼의 구성 성분 중에서 isocyanurate (1411 cm−1)와 Urea C=O (1654 cm−1)의 양은 NCO index가 증가함에 따라 같이 일정하게 커지는 경향을 보여준다.
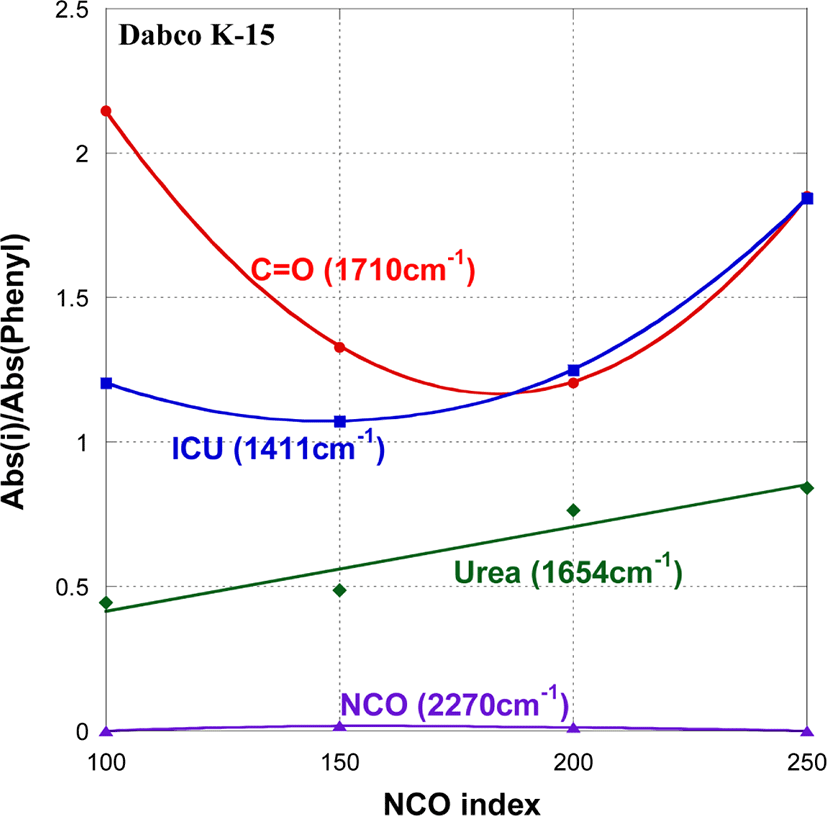
반면에, C=O (1710 cm−1) 기의 생성 정도는 촉매에 따라 다른 양상을 보여준다. Dabco K-15와 Toyocat RX-5를 촉매로 사용한 경우, NCO index가 100에서 A(C=O)/A(phenyl) 값이 A(ICU)/A(phenyl) 값보다 1.6~1.8배 크다. 그러나 NCO index가 커짐에 따라 A(C=O)/A(phenyl) 값은 감소하며 A(ICU)/A(phenyl) 값은 증가한다. Dabco K-15를 사용한 경우에는 NCO index가 200에서, Toyocat RX-5를 사용한 경우에는 NCO index가 150에서 A(C=O)/A(phenyl) 값과 A(ICU)/A(phenyl) 값이 같아진다. A(ICU)/A(phenyl) 값은 NCO index 값과 함께 계속 증가한다. 이로부터 NCO index가 낮은 조건에서 우레탄기가 많이 생성되며, NCO index가 200 이상이 되어야 isocyanurate 생성이 활성화되는 것을 알 수 있다. 한편, A(C=O)/A(phenyl) 값은 NCO index가 증가함에 따라 감소하다가 NCO index가 170에서 최소값을 가지고 다시 증가하는 경향을 보인다. 이는 isocyanurate 기도 1710 cm−1에서 C=O 피크를 가지며 한 개의 isocyanurate ring에 3개의 C=O 기가 있으므로, NCO index가 커짐에 따라 isocyanurate가 많이 생성되고 C=O stretching 의한 피크가 강해지기 때문이다. Dabco TMR-30을 촉매로 사용한 경우(Figure 8), A(C=O)/A(phenyl)와 A(ICU)/A(phenyl) 값 모두 NCO index가 커짐에 따라 일정하게 커지는 경향을 보여준다. NCO index가 200과 250에서 A(ICU)/A(phenyl) 값은 각각 2.3과 2.9로 Dabco K-15와 Toyocat RX-5를 사용한 경우에 비하여 상당히 크다. 이는 3개의 3급 아민이 벤젠에 치환된 Dabco TMR-30의 화학구조가 isocyanurate ring과 networking 형성에 유리하기 때문이라 추정된다.
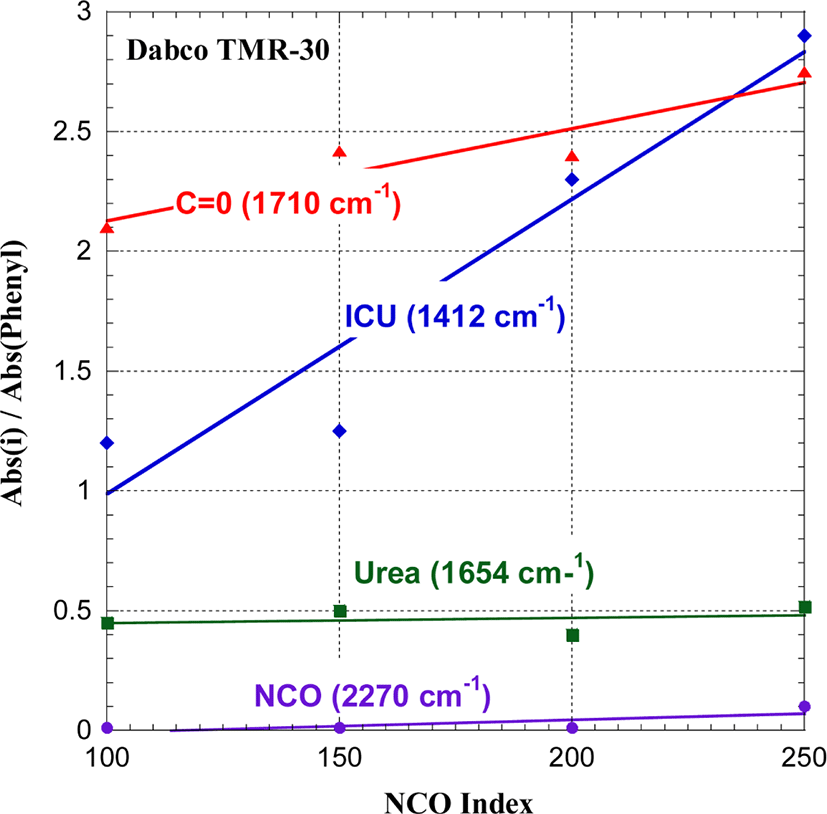
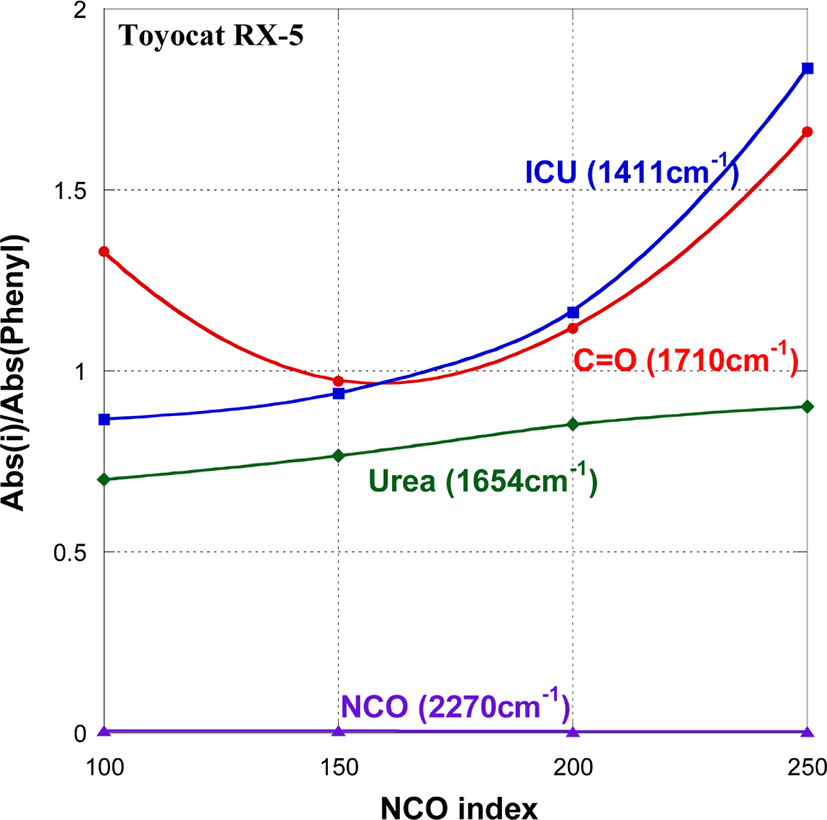
합성한 PUIR 폼의 열적 특성을 TGA를 이용하여 Air 기류 하에 10℃/min으로 승온시키며 분석하였다. Figure 10~12는 NCO index를 100, 200, 300으로 변화시키며 발포한 PUIR 폼의 열분해 곡선이다. Air 기류 하에서 PUIR foam은 크게 2 차례의 분해가 일어난다. 선행 연구 결과를 참고하여12-19Figure 10~12의 열분해 과정을 해석하면 다음과 같다. 1차 분해 과정으로 약 450 K에서 PUIR에 함유된 우레탄기의 분해가 시작되어 분해중간체인 디이소시아네이트가 생성되고, 디이소시아네이트로부터 2차 중간체인 carbodiimide가 생성된다. Carbodiimide는 약 650 K부터 우레아를 거쳐서 isocyanurate로 전환된다. 2차 분해 과정은 약 700 K에서 Isocyanurate 기의 분해로 시작되어 780~860 K에서 활발하게 이루어지며 900 K에서 모든 분해는 종료된다. 이 과정에서 isocyanurate ring 구조가 char 형성을 촉진하여 열분해에 대한 저항성을 높인다. 특히 PUIR 폼은 우레탄 분해에 의하여 isocyanurate ring이 형성되는 것 이외에도 diisocyanate 3분자가 삼량화 반응으로 isocyanurate ring 구조를 형성하고 있으므로 우레탄 폼에 비하여 열분해에 대한 저항력이 크다.
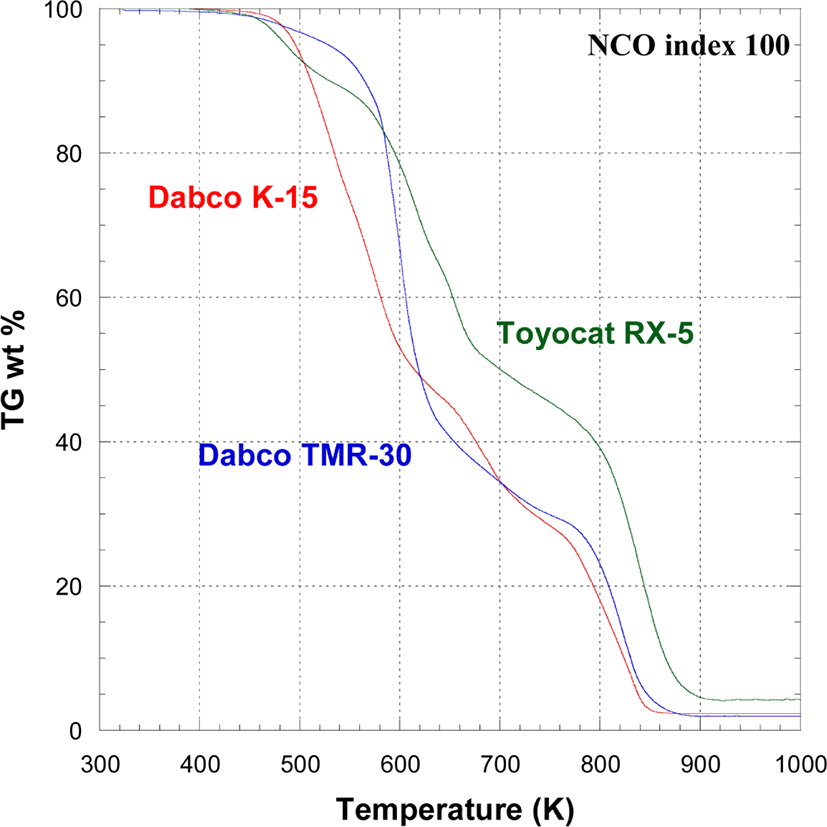
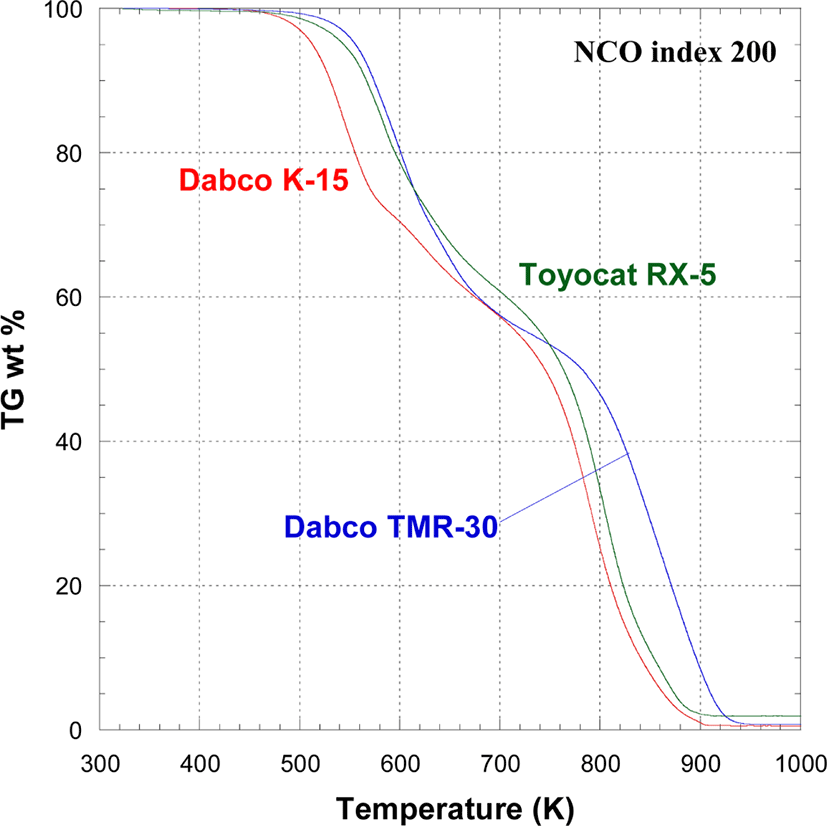
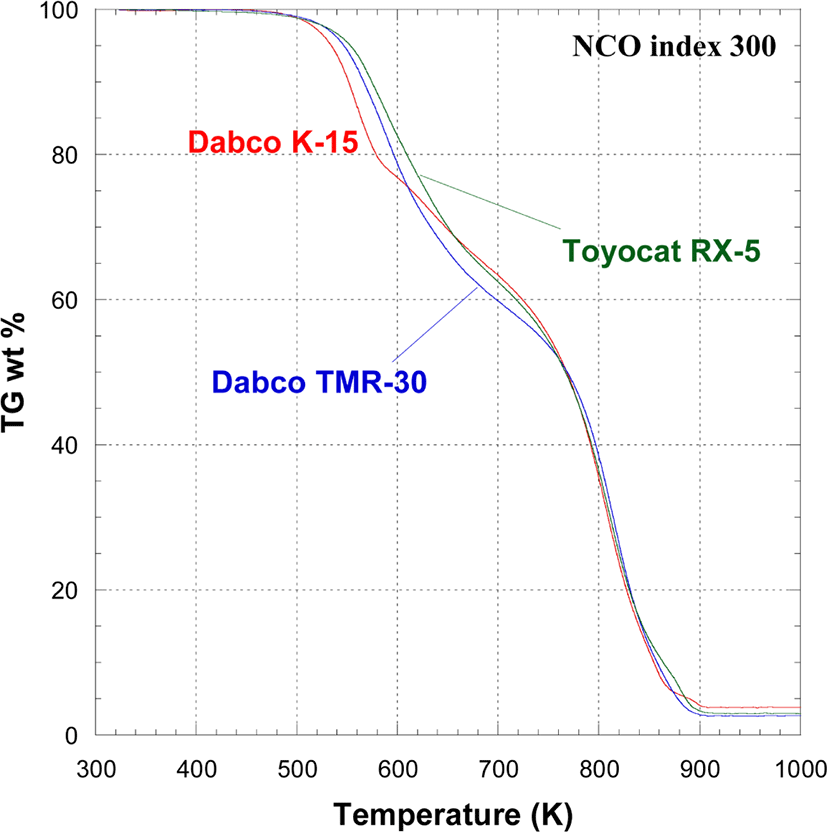
Table 5~7에 1차와 2차 분해의 시작온도(Tini.), 변곡온도 (Tinf.), 종말온도(Tterm.)를 정리하였다. 변곡온도는 열분해곡선의 (dW/dT) 값이 peak로 나타나는 지점으로 정하였다. NCO index를 100으로 맞추어 발포한 PUIR은 안전한 폼의 형태를 형성하지 못하고 쉽게 부스러졌다. NCO index가 200과 300 경우에 Dabco K-15를 사용하여 발포한 PUIR 폼의 1차와 2차 분해가 다른 촉매를 사용하여 발포한 PUIR 폼에 비하여 낮은 온도에서 시작되었다. 반면에 NCO index가 200에서 Dabco TMR-30을 사용하여 발포한 PUIR 폼은 1차와 2차 분해 시작온도는 각각 517.7 K과 742.6 K로 다른 촉매를 사용한 PUIR 폼에 비하여 상당히 높으며 900 K에서도 잔량이 8% 정도 남을 정도로 안정하였다. NCO index가 300인 경우, Dabco K-15를 사용하여 발포한 PUIR 폼의 1차 분해가 낮은 온도에서 시작하는 것을 제외하고는 2차 분해 온도와 잔량에 큰 차이가 없었다. 분해 잔량은 촉매종에 상관없이 NCO index가 커짐에 따라 증가하는 경향을 보여준다. 이는 NCO index가 큰 조건에서 isocyanurate 생성이 잘 되기 때문이다. Dabco K-15와 Toyocat RX-5를 사용하여 발포한 PUIR 폼의 800 K 분해 잔량은 NCO index가 200에서 300으로 커짐에 따라 각각 25%와 33%에서 35%로 증가한 반면에, Dabco TMR-30을 사용하여 발포한 PUIR 폼의 800 K잔량은 NCO index가 200에서 300으로 커질 때에 47%에서 37%로 감소하였다. 이는 PUIR 폼의 분해 잔량을 높이려면 사용하는 촉매에 따라 NCO index 값을 최적화하여야 한다는 것을 암시한다.
Conclusions
AA와 DEG로부터 합성한 [(diethylene glycol)adipate]diol과 MDI를 주원료로 사용하여 PUIR 폼을 발포시키고, 이들 폼에 함유된 우레탄기, 우레아기, isocyanurate ring의 IR spectra 정규화와 TGA 분석을 통하여 열안정성을 분석한 결과 다음과 같은 결론을 얻었다.
본 연구에 사용된 3종의 촉매(Dabco K-15, Dabco TMR-30, Toyocat RX-5) 모두 NCO index가 증가함에 따라 우레탄기에 비하여 열에 안정한 우레아기와 isocyanurate ring의 생성이 증가한다. 특히, 페닐기에 3급 아민 3개가 결합되어 ring과 networking 형성에 유리한 구조인 Dabco TMR-30를 사용한 경우에 isocyanurate ring의 생성이 활발한 것으로 분석되었다.
Dabco TMR-30을 사용하여 NCO index 200인 조건에서 발포한 PUIR 폼의 분해 온도가 가장 높고 분해 잔량이 가장 많게 측정되었다. 따라서 Dabco TMR-30이 열안정성이 우수한 PUIR 폼 발포에 적합하다고 판단된다. 그러나, Dabco TMR-30을 사용하여 발포한 PUIR 폼의 고온(800 K, 900 K) 잔량이 NCO index가 300으로 커질 때에 감소하므로 적절한 NCO index 값의 선정이 필요하다.