Introduction
세계적으로 산업화가 진행됨에 따라, 이동 수단의 발달 등으로 인해 차량의 수요가 지속적으로 증가되었고, 계속적으로 증가 추세이다. 이로 인해 주 연료인 화석에너지로 인한 환경오염과 CO2 등으로 인한 GWP (Global Warming Potential)의 증가 등이 우려되고 있다.1 이로 인해 개발도상국 및 선진국들이 차량의 경량화를 통한 연비 개선에 대한 연구와 관심을 지속적으로 기울이고 있다. 차량 내부 등에 발포 소재 적용 등으로 경량화를 적용하고 있으며, 또한 차량 외부에서 시작되는 소음과 차량 바닥면의 진동을 완화하기 위한 연구가 지속적으로 이루어지고 있다. 특히, 차량 하부의 부식 방지와 소음 문제로 코팅후 발포공정을 거치는 방식을 주로 사용하고 있으며, 이를 underbody coating (UBC)이라고 한다.2 많은 시도들이 적용되고 있으나, 경량화를 위해 고분자화된 마이크로캡슐 등을 충진제(filler)로 사용되고 있다.3 마이크로캡슐 중에서도 특히, 열팽창성 미소구는 외곽에 고분자 쉘로 구성되어 내부에는 액체 탄화수소를 갖는 10-50 μm 의 평균 입도를 갖는 고분자이다.4,5 이 열팽창성 고분자를 이용하여 PVC와 블렌딩한 졸을 상압에서 차량 하부에 분사 후 가열공정을 거쳐 발포하는 형태를 UBC 공정으로 보고 있으며, 통상적으로 전착 도장 후, air less type 코팅을 진행하며, 도장과 부착을 위한 전처리 과정, 1차 baking, 2차 baking, 3차 baking 로 인한 발포 과정이 진행된다. 이러한 과정을 거치며 차량 하부에 고착된 PVC졸에 있던, 열팽창 미소구로 인한 팽창으로 외부 및 차량에서 전달되는 진동 및 소음에 있어서 보호 받을 수 있는 환경이 유지된다.6,10 하지만, 이때, 1차, 2차, 그리고 3차의 열에 의한 부착, 발포 과정을 거치는 공정 중 다른 산업에 적용되는 열팽창 미소구와는 달리 오랜 시간 열에 노출 된 채로 과정이 진행되므로, 이로 인한 내열성이 요구된다.
본 연구에서 차량용 underbody coating용 열팽창성 미소구에서 요구되는 내열성 향상은 오랜 시간 고온에 노출시 수축 으로 인한 발포율 감소를 막기 위한 것으로, 열팽창성 미소구와 블렌드 된 PVC졸을 철판 위에 부착한 뒤 이를 테스트하였다. 기존에 연구되었던 내변색 특성 향상을 위한 내용은,11 본 연구에서는 배제되었고, 이는 차량용 PVC졸 자체는 차량 하부에 사용되는 것으로 변색의 차이는 중요한 요소가 아니기에 본 연구에서는 제외하였다.
많은 연구에서 밝힌 바와 같이 열팽창성 미소구는 외부의 열가소성 수지와 내부에 탄화수소의 형태로 이루어져 있다.4 본연구도 이와 마찬가지로 탄화수소의 상변화로 인한 내부압 증가로 열가소성 수지가 연화되는 시점에서 부피가 크게 팽창되는 메커니즘을 이용한 연구이다.5,10 본 연구는 AN (Acrylonitrile), MAN (Methacrylonitrile) monomer 등을 합성하여, 열팽창 미소구의 외벽이 개시제로 인해 고분자화 되고, 가교로 인해 내부의 탄화수소가 봉입 되는 형태이다.
본 연구는 내열성 강화를 위해, 개시제와 가교제의 양에 의한 외벽의 두께에 관련된 시험을 중점적으로 진행하였다. 이는 열팽창성 미소구가 계속해서 열에 노출이 된다면, 내부 압과 계속된 외부 열로 인해 고분자의 degradation 등으로 인한 열팽창성 미소구의 수축이 빨리 진행 될 것으로 판단하여, 열팽창성 미소구 외곽 쉘 벽을 두껍게 하고자 하였으며, 이에 대한 변수를 개시제와 가교제의 비율로 하였다.
Experimental
열팽창성 미소구의 제조는 colloidal silica (C.S.)를 포함한 수상과 monomer, hydrocarbon (iso-pentane), 개시제(beznoyl peroxide)와 가교제(BDDMA, 1,4-butanediol dimethacrylate)를 포함한 유상을 혼합하기 위하여 1,000 rpm, 10 min 동안, 고속 회전시켜 현탁액(suspension)을 제조 후, 합성 반응기 내에서 16시간 반응 후 수세 과정을 거쳐, 건조 후 샘플을 취했다. 합성 반응기 내에서 반응시, 질소 치환 3 min, 2 kgf/cm2 의 압력을 가하고 62°C 에서 16시간 400 rpm으로 합성을 진행하였다. 이때 본 실험에서는 가교제의 양을 조절 하여 열팽창성 미소구 샘플을 합성하였다.
열팽창성 미소구의 열팽창 특성은 열팽창분석기(TA instrument, TMA Q400)를 사용하여 50°C에서 250°C까지 10°C/min 의 승온 속도로 가열하면서 열팽창성 미소구의 팽창이 개시되는 온도(Ts, Tstart), 최대 팽창에 도달된 때의 온도 (Tm, Tmax), 최대 팽창에 도달했을 때의 높이(Dmax)를 측정하였다. 합성한 미소구의 표면은 전자주사현미경(Seron, SEM AIS2300C)과 광학현미경(Nikon, E200LED)을 이용하여 촬영을 하였다. 또한, 합성한 열팽창성 미소구의 평균입도 크기는 입도분석기(Malvern, Mastersizer 2000S)를 이용하여 측정하였다. 또한, 열팽창성 미소구의 벽 두께를 확인하기 위하여, 집속 이온 빔(FEI, Hellios Nanolab 600)을 이용한 관찰을 시도하였다. 합성한 열팽창성 미소구를 테스트 하기 위하여, 매질 역할을 할 PVC (Poly Vinyl Chloride)졸을 만들었고, 졸의 제조는 PVC (100g, LG화학, LP170), 디옥틸프탈레이트(30g, Sigma-Aldrich), 중질탄산칼슘(60 g, Sigma-Aldrich), BZ810P-5 (1g, Songwon)를 혼합하여 PVC 졸을 제조한 후 PVC 졸에 건조된 열팽창성 미소구 1g을 추가로 첨가한 후 블렌드 하여 혼합물을 제조하였다. 이후 제조한 혼합물을 냉열 압연 강판(Cold Rolled Steel, CRS), 152×76 mm, 0.8T 위에 200 μm 두께로 코팅하였다. 코팅된 시편은 110°C에서 10초간 노출시켜, CRS 위에 고착화 시켰다. 이후, 150°C에서 15분간, 3번 굽기(baking)를 상압 하 조건에서 발포 공정을 진행하였고, 발포전과 발포후 두께를 측정하여 팽창전과 팽창후의 두께를 나누어 팽창비를 계산하였다.
Results and Discussion
반응기내 투입량은 AN 80, MAN 20으로, monomer 총량을 100을 기준으로 하여 hydrocarbon을 15, 개시제 1.0, 가교제 0.5, colloidal silica 20 중량을 계량하였고, 시험 반응기 부피의 60% 로 총량을 계량하여 반응을 하였다. AN과 MAN monomer를 비롯한 개시제 양과 샘플 제조 환경은 동일시 하였고, 가교제의 양을 변량하여 시험을 진행하였다. Table 1에 개시제 변량 정도를 나타내었다.
Figure 1의 TMA결과를 보면 가교제의 양이 가장 작게 들어간 샘플의 Dmax가 가장 높은 것을 볼 수 있으며, A (r 0.5)에 비해 A (r 2.0)은 3배 이하로 낮은 dimension change 값을 나타낸다. 이는 그만큼 내부의 탄화수소가 발포역할을 하지 못한 것으로 보여진다. A (r 2.0)의 경우는 TMA curve 상, 발포를 거의 하지 못한 상황이므로 가교제의 양이 많았던 것으로 보이며, A (r 0.5)의 경우는 Dmax의 값은 높으나, curve가 sharp 한 형태를 나타낸다. 이는 열이 계속 상승 될시, Dmax 이후 미소구의 수축이 크다는 것을 보여 준다.
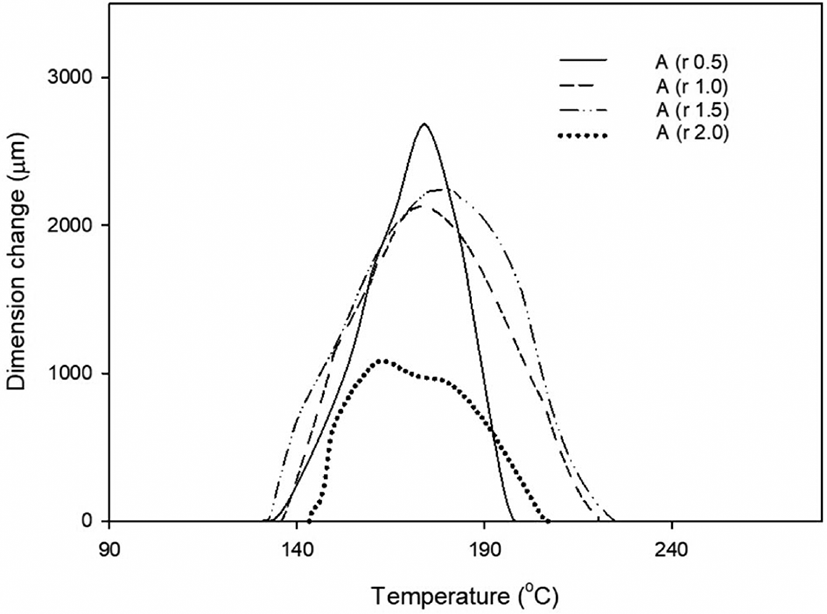
Table 2의 합성된 결과 역시 가교제가 가장 많이 함유되었던 A (r 2.0)가, 낮은 Ts, Tm, Dmax를 나타냄을 알 수 있다. 입도 크기는 가교제의 양이 증가할수록 입자는 크게 형성되는 것과 입도의 균일성을 나타내는 span 값이 크게 상승됨을 확인하였다.
Codes | A (r 0.5) | A (r 1.0) | A (r 1.5) | A (r 2.0) |
---|---|---|---|---|
Ts (°C) | 132.8 | 135.7 | 134.1 | 143.2 |
Tm (°C) | 174.2 | 173.9 | 179.8 | 162.8 |
Dmax (μm) | 2689 | 2122 | 2238 | 1082 |
Particle size (μm) | 25.5 | 27.3 | 27.8 | 34.2 |
Span | 1.7 | 1.7 | 1.7 | 2.1 |
이에 따라, A (r 0.5)의 경우, Dmax 는 높은 값을 나타내었으나 내열성이 취약함을 예상할 수 있었고, A (r 2.0)의 경우는 발포 배율 등에 문제가 있었으므로, 가교제의 양을 A (r 1.0)과 A (r 1.5)의 양이 적절함으로 예상하고 추가적으로 실험을 진행하였다.
시험 결과 A (r 0.75), A (r 1.0), A (r 1.25), A (r 1.5)의 입도는 27~28μm로 평이하였으며, Figure 2에서 보는 바와 같이 Dmax 에서는 큰 차이를 보이지 않는다. 다만, A (r 0.75)의 경우 최대 팽창후 온도 상승시 급격하게 수축됨을 확인할 수 있었다. 특히, A (r 1.25)의 경우 Dmax 이후에 수축되는 정도가 가장 적은 것을 확인할 수 있으며, 이는 Tmax 혹은 Dmax 이후에 dimension change 값이 완만하게 줄어드는 것으로 차후 테스트시 고분자 내, 발포시에도 동일하게 결과를 도출하고자, PVC 졸 50g과 1g의 열팽창성 미소구를 블렌드 한 후, 블렌드 된 PVC 졸을 CRS에 고착화 시키기 위해 110°C에서 10 초간, 건조하여 고착화 후, 150°C에서 15분 공정 후 배율 측정, 다시 15분, 최종적으로 15분, 각 발포 시점 후 발포제품의 발포율을 측정하였다.
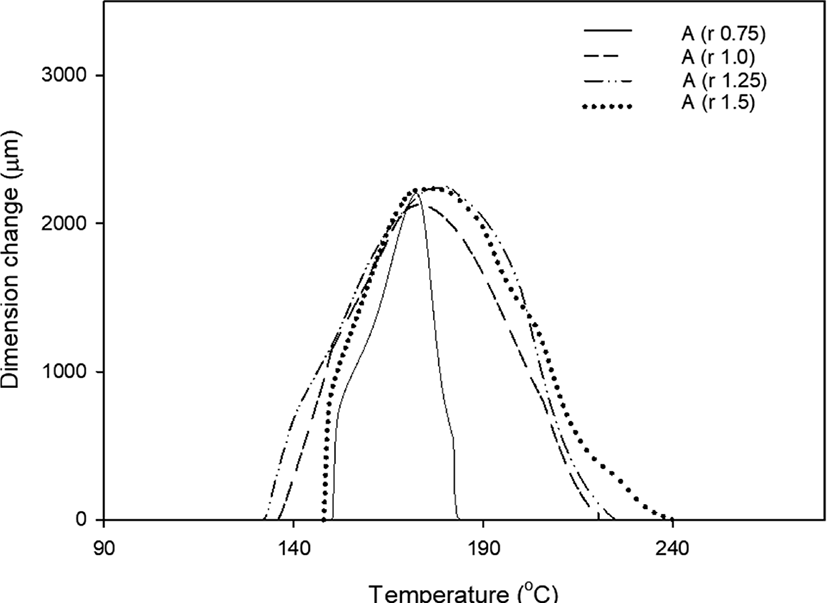
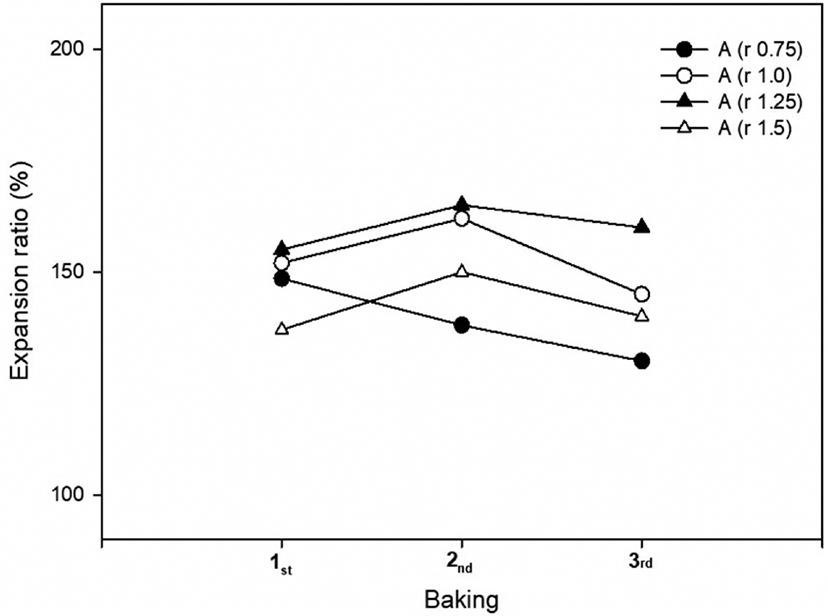
각 15분 마다, 발포 배율을 측정하였고, 초기에는 모두 발포를 하였고 배율이 150%까지 증가하였으나, 2차와 3차 진행후, 발포율이 모두 감소하였다. 특이한 사항은 TMA 결과와 유사한 내용으로 A (r 0.75)의 경우 초기의 발포배율 보다 급격하게 수축 감소가 일어났고, A (r 1.25)의 경우 수축 감소가 거의 일어나지 않았으며, 이는 UBC용 열팽창성 미소구 적용시 수축으로 인한 내열성 약화에 가장 적합한 내용으로 판단되었고, 시험편을 현미경을 통하여 표면을 관찰하였다. Figure 4의 (c) 1.25 phm이 적용된 A (r 1.25) 시험편의 표면의 셀이 다른 시험편에 비하여 가장 확연하게 보였으며, 크기는 200~250 μm로 측정되었다.
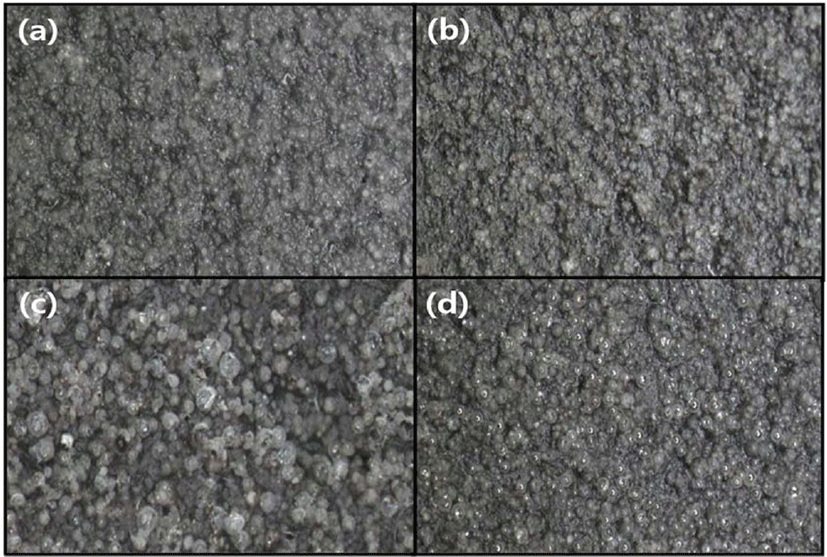
조금 더 구체적으로 시험편을 확인하기 위해 SEM을 이용하여, 표면 관찰을 시도하였고, Figure 5의 (c)를 제외하고는 부풀거나 수축으로 인한 셀의 터짐 현상이 관찰되었다.
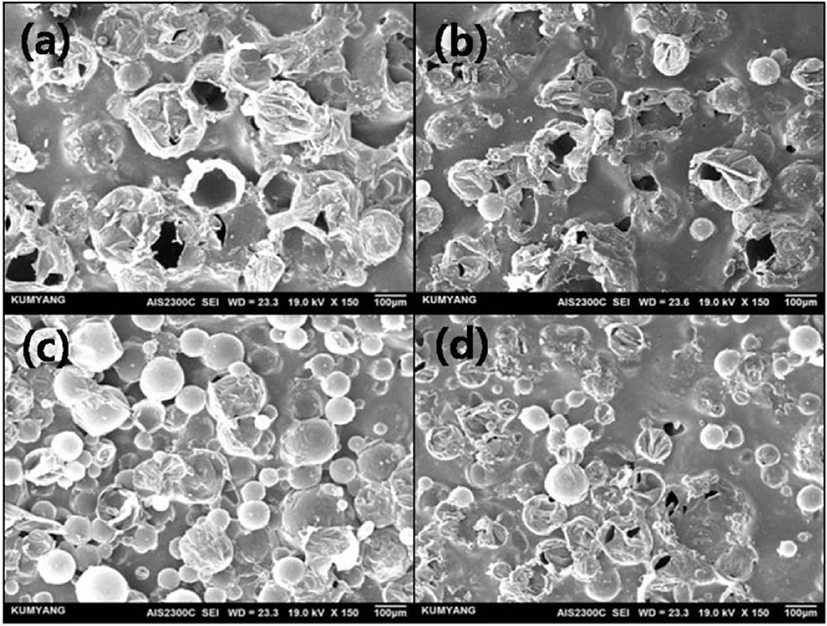
실제 본 연구의 목적이 가교제의 함량을 증가시켜 열팽창성 미소구 외곽 벽의 강화를 통한 내열성 강화로 인한, 고온에서의 수축 방지를 목적으로 하였기에, 실제 열팽창성 미소구 벽 두께를 확인하고자 하였다. Figure 6은 집속 이온 빔을 이용하여 분석을 실시한 내용으로, 가교제 0.75, 1.0 phm이 적용되었던 (a)와 (b)는 벽이 균일하지 않았고, (d)의 경우는 두꺼운 부분과 얇은 부분의 편차가 다른 샘플에 비해 크다는 것을 확인할 수 있다. 가장 이상적인 형태인 (c)의 경우는 벽의 두께가 다른 샘플에 비해 두꺼웠으며 부위 마다 일정한 형태를 나타내었고, 이로 인해 초기 발포율에 비해 고온에 지속적으로 노출되어도 발포율이 감소하지 않은 것으로 보여진다.
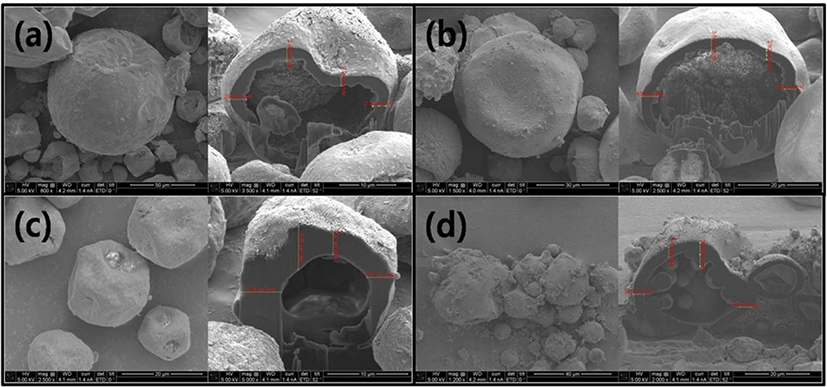
Conclusions
다양한 용도로 사용되는 열팽창성 미소구를 차량 하부, underbody coating 용으로 적용시키기 위하여 연구를 진행하였다. 특히, 열팽창성 미소구의 합성시 가교제의 양에 따른 내열성 향상을 도와 고온에서 적용 시, 수축되는 경향을 줄이기 위한 부분에 연구의 초점을 두었으며, 특히 가교제 1.25 phm 적용시, 열팽창성 미소구 외곽쉘이 가장 두꺼우면서도 안정적인 형태를 나타내었으며, 실제 발포 후 표면 SEM 관찰시에도 미소구가 터진 부분이 가장 적었고, 현미경 관찰시에도 200-250 μm의 균일한 구를 형성하였다. 이는 개시제로 인한 고분자화와 진행될 시, 가교의 영향으로 더욱 안정한 형태의 구조를 가지게 된, 열팽창성 미소구가 내열성이 더욱 뛰어난 것으로 판단되며 이는 집속 이온 빔을 통한 단면 확인을 통하여 더욱 확실히 내용을 확인할 수 있었으며, 내열성이 요구되는 열팽창성 미소구 적용에 용이할 것으로 판단된다.