Introduction
고무소재는 유연하고 뛰어난 탄성력과 더불어 방진 특성이 우수하여 동적 하중을 받는 분야에 사용되고 있다. 이러한 하중에 노출되면 소재는 물성의 변화를 보이며 결국엔 소재의 파괴로 이어지기 때문에 피로 거동은 고무뿐 아니라 모든 물질에서 반드시 고려해야 하는 사항이다. 피로 거동에 영향을 끼치는 요소는 매우 다양할 수 있는데, 예로 소재의 종류, 하중의 조건, 첨가제, 가공 조건 및 외부 환경 등이 있다.1,2피로 거동을 겪는 고무 소재의 대표적인 산업 분야는 자동차 산업이다. 자동차의 부품 중 타이어, 엔진 마운트, 부싱 등에 사용되는 고무소재는 장시간 동적 하중을 겪기 때문에 다른 재료로는 대체가 불가능하다. 따라서 고무의 내구성 향상은 중요한 과제로 여겨지고 있다.3,4 최근 자동차 분야에서 방진고무 소재를 대체하기 위한 스마트 소재로 자기유변탄성체 (Magneto Rheological Elastomer, MRE)가 관심을 끌고 있다.5,6 MRE는 탄성체 내에 자기응답입자(Magneto Responsible Particle, MRP)를 분산시켜 외부 자기장 인가 여부에 따라 즉각적이며 가역적인 물성 변화를 나타내는 재료이다. MRE에서 물성 변화를 야기시키는 메커니즘은 많은 연구가 진행된 자기유변유체(Magneto Rheological Fluid, MRF)와 유사하게 탄성체 매트릭스 내에 분산된 MRP가 자기장 인가에 따라 사슬형태의 클러스터를 형성함으로써 인장력, 전단력에 대해 저항하며 발생한다.7 MRE는 MRF의 단점(MRP의 침전, 밀봉 용기의 필요성)을 개선한 소재로 특히 기존 방진 고무에 비해 더 넓은 영역의 주파수를 흡수할 수 있어 자동차 산업의 방진 분야에 각광받고 있는 스마트 재료이다.8-10 그러나 MRE의 경우는 MRF와는 달리 탄성체 매트릭스 내에 MRP의 배향이 어려우며, 배향된 MRP는 고정된 상으로 존재하기 때문에 pre-yield 상태에 의존한다.11 따라서 MRE와 MRF는 상호보완 관계에 있는 소재라고 할 수 있다. 이러한 MRE의 활용분야로 주목 받는 방진 부품은 동적 하중에 많이 노출되기 때문에 피로에 대한 저항성이 중요하지만 MRE에 대한 피로저항성의 연구는 예측이 어렵고 신뢰도가 부족하여 아직 많은 연구가 이루어지고 있지 않다.12-14
본 연구에서는 NR (Natural Rubber), EPDM (Ethylene-Propylene Diene Monomer) 및 AEM (Ethylene-Acrylic Elastomer) 3종류의 고무 매트릭스를 사용하여 카본블랙의 함량조절을 통해 동일한 경도로 MRE를 제조하였다. 피로시험을 통해 MRE 매트릭스 종류에 따른 피로저항성을 비교 분석하였으며, 그 중 EPDM계 MRE의 피로저항성에 카본블랙 함량 및 가교시스템이 미치는 영향을 연구하였다. 피로시험은 반복변형시험을 통해 동적 하중에 대한 피로저항성을 분석하였고, 크리프 시험을 통해 정적 하중에 대한 변형 정도 및 영구변형을 분석하였다. 물성 변화에 대한 메커니즘은 XPS (X-ray Photoelectron Spectroscopy), SEM (Scanning Electron Microscopy) 및 RPA (Rubber Process Analyzer)를 사용하여 분석하였다.
Experimental
EPDM은 금호폴리켐사의 Keltan KEP-960N(F) (pelletized, 70% ethylene content, 5.7% ENB unsaturation), NR은 PAN STAR의 STR 5 L, AEM은 Dupont의 VAMAC G (linear polyester)를 사용하였고 충전제는 카본블랙 N330 (Aditya Birla Chemicals), MRP로는 BASF사의 Carbonyl Iron Particle (CIP, 입자 사이즈 4.5~5.2 μm)을 사용하였다. 가교시스템을 위한 첨가제는 Puyang Wiling Chemicals사의 zinc oxide (ZnO), stearic acid (SA), sulfur (S), N-cyclohexyl-2-benzo-thiazyl sulfonamide (CZ), dibenzothiazyl disulfide (DM), Akrochem사의 di-ortho-tolylquanidine (DOTG)과 hexamethyl- ene diamine carbamate (Diak No.1), Vanderbilt사의 polyoxy-ethylene octadecyl ether phosphate (VANFRE VAM)를 사용하였다.
각 매트릭스의 상대적 피로물성 비교를 위한 기준으로 카본블랙 함량조절을 통해 Shore-A 경도 60을 나타내는 MRE를 제조하였다. NR의 경우는 카본블랙 35 phr, EPDM의 경우는 카본블랙 30 phr 및 AEM의 경우는 20 phr을 배합함으로써 Shore-A 경도 60을 맞출 수 있었다. 따라서 이들을 NR35, EPDM30 및 AEM20으로 명명하였다. 본 연구에서 상대적으로 피로저항성이 낮다고 평가된 EPDM계 MRE의 경우는 모든 조성은 유지한 채 카본블랙 함량을 0, 15, 30 및 40 phr까지 변화를 주고 각각 EPDM0, 15, 30, 40으로 나타내어 카본블랙 함량이 피로특성에 미치는 영향을 조사하였다. 또한 EPDM의 가교 구조가 피로특성에 미치는 영향을 조사하기 위해 가교제 및 첨가제의 조절을 통해 다황 가교 구조가 지배적인 conventional vulcanization system (CV-system), 단일황 가교 구조가 지배적인 efficient vulcanization system (EV-system), 다황 및 단일황 가교 구조가 적절히 섞인 semi-EV system을 구축한 후 가교시스템이 피로특성에 미치는 영향도 조사하였다. 피로시험을 위한 MRE의 제조를 위해 배합은 two-roll mill을 사용하였으며 먼저 매트릭스를 5분간 소련 후, 각 배합비에 따른 첨가제 및 CIP를 투입하여 25분간 배합을 진행하였다. 사용된 CIP는 30 vol%로 유지하였으며 각 배합물들의 조성은 Table 1과 Table 2에 나타내었다.
NR35 | EPDM30 | AEM20 | |
---|---|---|---|
Rubber | 100 | 100 | 100 |
C/B | 35 | 30 | 20 |
CIP | 192 | 204 | 175 |
SA | 2 | 1.5 | 1.5 |
ZnO | 5 | 5 | - |
CZ | 0.8 | 0.5 | - |
DM | - | 0.5 | - |
S | 1.5 | 1.5 | - |
VAM | - | - | 1.5 |
DOTG | - | - | 4 |
Diak no.1 | - | - | 1.5 |
Curing system | |||
---|---|---|---|
CV | semi-EV | EV | |
EPDM | 100 | 100 | 100 |
C/B | 30 | 30 | 30 |
CIP | 204 | 204 | 204 |
SA | 1.5 | 1.5 | 1.5 |
ZnO | 5 | 5 | 5 |
CZ | 0.3 | 0.5 | 5 |
DM | 0.2 | 0.5 | 3 |
S | 1.5 | 1.5 | 1.5 |
시험에 사용된 시편은 KS M 6518에 준하여 제작한 인장시편 형상이며 피로시험은 TA사의 electroforce 5500 series를 사용하여 반복변형 시험과 크리프 시험으로 진행하였다. 반복변형 시험은 25%의 변형을 frequency 5, 10 Hz의 속도로 5,000, 10,000, 20,000 cycle 동안 수행한 후 Universal Testing Machine (UTM, Daekyung Engineering)을 이용하여 50 mm의 initial clamp distance와 500 mm/min의 cross-head speed 조건에서 인장강도를 측정하여 피로시험 후의 인장강도 변형율을 비교하였다. 크리프 시험은 3일 동안 4 N의 일정 하중을 가하여 변형율을 측정하고, 하중을 제거하여 1일 동안 회복 거동을 측정하였다.
각 조건에 따른 반복 변형 시험에 의한 매트릭스 내의 가교도 변화를 분석하기 위해 팽윤 시험을 진행하였다. 팽윤 시험을 위한 용매로는 톨루엔을 사용하였다. 시험방법은 비이커에 톨루엔 50 mL를 부은 뒤 반복변형을 겪은 인장 시편의 neck 부분을 일정량 절단 후 침지시켜 암실에 보관하고 2시간마다 무게를 측정하여 평형상태에 이를 때까지 반복하였다. 결과는 초기 무게와 평형상태에서의 무게 변화율(%)로 표현하였다.
Results and Discussion
매트릭스 유형에 따른 피로특성을 상대적으로 비교하기 위해 동일한 경도(Shore A type : 60)를 기준으로 하였다. 동일 경도는 NR, EPDM 및 AEM에 카본블랙의 함량을 각각 35, 30, 20 phr을 첨가함으로써 얻을 수 있었으며, 카본블랙의 함량에 따라 NR35, EPDM30 및 AEM20으로 나타내었다. 제조된 MRE에 반복 변형을 각 조건에 따라 가한 뒤 인장강도의 변화를 측정하였고 그 결과를 Figure 1에 나타내었다. Figure 1에는 피로시험 전의 인장강도와 피로시험 후의 인장강도를 변화율(%)로 나타내었다. Figure 1(a)에 나타난 바와 같이 NR35의 경우 5,000 cycle에서는 변화율이 10% 가량 상승 후, cycle이 증가함에 따라 감소하는 결과를 나타내었다. AEM20은 반복 변형에 따른 인장강도의 큰 변화가 보이지 않아 피로저항이 가장 우수하다고 판단하였고, EPDM30의 경우 cycle이 증가하면서 점차 인장강도가 감소하여 20,000 cycle에서는 72.8%까지 감소하였다. 이러한 경향은 Figure 1(b)에 나타난 바와 같이 frequency가 증가하여도 유사하였으며 반복 변형의 속도가 높아진 10 Hz에서의 변화율은 5 Hz에 비해 크게 나타났다. 이러한 결과의 원인은 반복 변형으로 야기되는 응력연화 현상에 의한 에너지손실(hysteresis) 이라고 사료되며, 이에 따라 매트릭스의 가교도의 변화를 초래했을 것으로 판단하여 팽윤 시험을 통해 확인하였다. 그 결과는 Figure 2에 나타내었다. Figure 2에 나타난 바와 같이 AEM20의 경우 반복 변형에 따라 팽윤도의 변화가 보이지 않았다. NR35에서는 frequency에 관계없이 5,000 cycle에서 팽윤도가 감소했다가 cycle이 증가하면서 다시 팽윤도가 증가하는 결과를 나타내었다. 이는 반복 변형 동안 초기에는 미끄러지거나 파괴되는 사슬들이 재결합하는 확률이 더 높았으며 지속적으로 변형이 가해짐에 따라 사슬절단 현상이 더 지배적임을 예측할 수 있었다. 이러한 결과는 Figure 1의 인장강도 변화율 결과와 일치하였다. 다만 피로시험에 의한 인장강도 변화율이 가장 컸던 EPDM30의 경우 팽윤도에는 큰 변화를 보이고 있지 않았다. EPDM30의 경우는 Figure 2에 나타난 바와 같이 팽윤도가 가장 낮은 즉 가교도가 상대적으로 크기 때문이라고 판단되며, 정확한 분석을 위해 추가적인 연구가 진행 중에 있다.
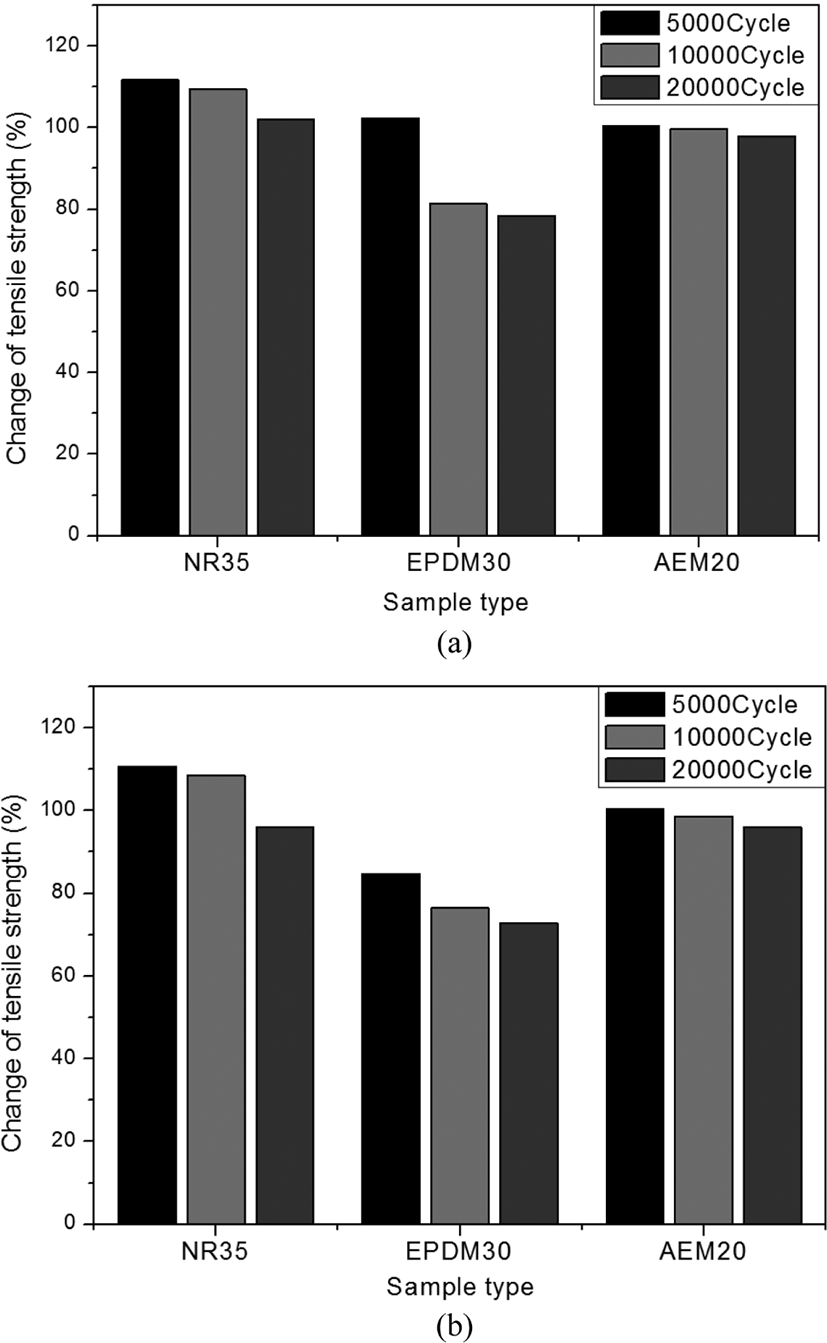
MRE들의 피로특성은 RPA를 사용하여 동적 물성 분석을 통해 자세히 분석하였다. RPA 측정 결과는 Figure 3에 나타내었다. 결과에 따르면 낮은 변형에서는 EPDM30이 가장 높은 저장 모듈러스를 나타내었으며, 상대적으로 더 낮은 변형에서 다른 매트릭스에 비해 저장 모듈러스가 급격하게 감소하는 결과를 나타내었다. EPDM30에 지속적인 반복 변형이 가해질 때, 인장강도 변화율이 상대적으로 큰 이유는 Figure 3에 나타난 Payne 효과의 결과와도 일치하였다.15 정적 피로특성은 크리프 시험을 통해 비교하였고 그 결과를 Figure 4에 나타내었다. Figure 4에 나타난 바와 같이 하중 제거 후 회복되지 않은 영구변형은 AEM20이 가장 크고, EPDM30, NR35 순으로 작아지는 결과를 얻었다. 다만 같은 하중을 가했을 때, EPDM30과 NR35는 비슷한 변형율을 나타내는 반면, AEM20은 상대적으로 큰 변형율을 보였다. 이는 Figure 2의 팽윤도 결과에서 나타난 바와 같이 AEM20이 상대적으로 낮은 가교도를 가져 다른 두 매트릭스에 비해 유연성이 높았기 때문이라고 사료되었다. 이때 같은 하중에 따른 각 매트릭스들의 최대 변형율과 회복 후 영구 변형율은 NR35와 EPDM30, AEM20이 각각 9.91%/0.42%, 9.39%/2.04%, 20.14%/4.04%로 나타났다. 이를 통해 각 매트릭스들의 회복율은 최대 변형 대비 NR35와 EPDM30, AEM20이 각각 95%, 78%, 80%로 나타났고, EPDM30이 회복율이 가장 낮았다. 이를 통해 정적 피로의 저항성은 동적 피로와 마찬가지로 EPDM이 낮다고 이야기 할 수 있다.
EPDM계 MRE의 카본블랙 함량에 따른 피로특성을 조사하기 위해 카본블랙을 0, 15, 30, 40 phr 배합하였고 이들의 반복 변형에 따른 인장강도 변화율을 Table 3에 나타내었다. 시험 결과, EPDM0은 5,000 cycle 및 10,000 cycle의 일부 시험에서 인장강도가 113.44%까지 상승하였는데 그 이유는 초기의 낮은 물성(1.86 MPa)에 의해 작은 오차에도 높은 변화량으로 나타난 결과이며 20,000 cycle에서는 90.68%까지 감소하였다. 또한 카본블랙이 첨가된 EPDM15와 30에서도 5,000 cycle에서 인장강도가 1.70% 및 2.28% 증가하였지만 시험 속도가 빨라지고 cycle이 증가할수록 점차 감소하여 82.63% 및 72.80%로 감소하였다. 카본블랙이 가장 많이 첨가된 EPDM40의 경우 모든 조건에서 인장강도가 감소할 뿐 아니라 20,000 cycle에서는 71.68%까지 인장감도가 감소하여 가장 낮은 피로특성을 나타내었다. 피로시험 결과에 따라 보강제인 카본블랙의 함량이 증가할수록 피로특성은 감소하는 것을 확인하였다. 피로특성의 변화 원인을 보강제 첨가에 따른 동적 특성의 변화라고 판단하였고, 카본블랙 함량에 따른 RPA 측정 결과를 Figure 5에 나타내었다. Figure 5에 나타난 바와 같이 카본블랙의 함량이 증가할수록 보강 효과에 의해 초기 모듈러스는 상승했지만, 변형이 증가하면 모듈러스는 감소하다가 함량에 무관하게 일정한 값을 나타내고 있다. 따라서 초기 모듈러스와 최종 모듈러스의 차는 카본블랙의 함량이 증가할수록 커지게 된다. 즉, 카본블랙의 함량이 증가할수록 Payne 효과가 크다는 결과를 보였다.16 크리프 시험 결과는 Figure 6에 나타내었다. Figure 6에 나타난 바와 같이 EPDM0의 경우 인장강도가 낮아 현조건에서 크리프 시험 진행이 어려웠기에 EPDM15, 30, 40만을 분석하였다. 정적 피로저항의 척도라고 생각되는 하중 제거에 의한 회복 후 남은 영구 변형의 정도를 보면 카본블랙의 함량이 증가할수록 보강효과에 의한 강성 증가로 최대 변형율이 감소하고 하중 제거 후 회복되지 못한 영구 변형은 증가했다. 이로 인해 카본블랙의 함량이 증가할수록 하중 제거 후의 회복율 감소 즉, 정적 피로에 대한 저항성이 감소하는 결과를 나타내었다.
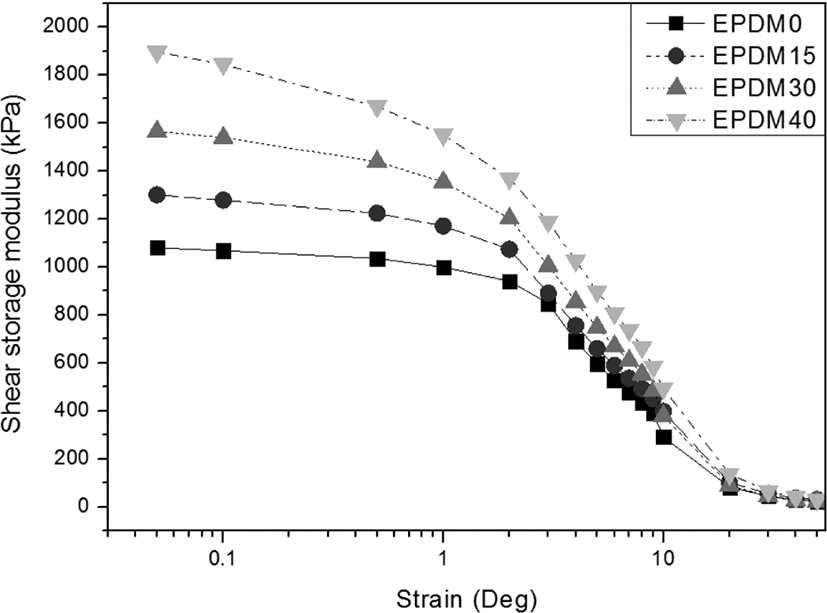

피로시험을 위해 사용한 EPDM계 MRE는 모두 Semi-EV 시스템으로 제조되었다. 따라서 다른 가교 시스템이 피로저항에 끼치는 영향을 확인하기 위해 배합비 조절을 통해 EV, CV 시스템의 EPDM계 MRE를 준비하였다. 피로시험을 하기 앞서 가교 시스템의 차이를 정성, 정량적으로 분석하고자 XPS를 사용하였고, 그 결과를 Figure 7 및 Table 4에 나타내었다. Figure 7에 나타난 바와 같이 S 2p에 대한 정성 분석 결과 모든 가교 시스템에서 다황 및 단일황 가교 결합이 나타난 것을 확인하였다. 또한 Table 4에 나타낸 정량적인 비율에서 EV 시스템은 단일황 결합이 76.77%로 48.76%인 CV 시스템보다 월등히 많은 것을 알 수 있었고, 다황 결합은 CV 시스템이 51.24%로 EV 시스템의 23.23% 보다 많은 결과를 보였다. XPS 결과를 통해 다황 및 단일황 가교 시스템이 성공적으로 구축된 것을 확인하였고, 반복 변형 시험을 각 조건에 따라 진행하여 피로시험에 따른 인장강도 변화율을 Figure 8에 나타내었다. Figure 8에 나타난 바와 같이 모든 피로 조건에서 EV 시스템은 기존 Semi-EV 시스템에 비해 인장강도가 감소한 반면, CV 시스템은 피로시험에 따른 물성의 감소가 크게 나타나지 않은 결과를 통해 결합 에너지가 강하지만 유연성이 떨어지는 단일황 가교 구조가 지배적인 EV 시스템보다 유연성이 높은 다황 가교 구조가 지배적인 CV 시스템이 피로 저항 측면에서는 우수하다고 판단 되었다.17 또한 가교시스템의 변화로 인한 가교도 차이를 확인하기 위해 팽윤 시험을 실시했고 그 결과를 Figure 9에 나타내었다. 팽윤 시험 결과 다황 가교구조의 CV 시스템이 EV 및 Semi-EV 시스템보다 팽윤도가 높은 결과를 보였다. 이러한 가교도의 차이는 가교사슬의 길이에 의한 것으로 판단되며 EV 시스템은 짧은 단일황 사슬로 이루어진 높은 가교도를, CV 시스템은 긴 다황 사슬로 이루어진 상대적으로 낮은 가교도를 가지고 있음을 알 수 있었다. 가교 시스템에 따라 가교도의 차이는 있지만 Figure 9에 나타난 바와 같이 모든 가교 시스템에서 피로 cycle이 증가하여도 팽윤도에는 큰 차이가 없었다. 다만 EV 시스템의 경우 10 Hz의 높은 속도에서 피로 cycle이 증가함에 따라 상대적으로 팽윤도가 증가하는 것을 통해 결합에너지가 높은 단일황 결합의 경우는 피로특성 측면에서는 불리하다는 것을 나타낸 결과라고 사료된다. 가교 시스템에 따른 크리프 시험의 결과는 Figure 10에 나타내었다. 시험 결과 회복되지 않은 영구 변형의 정도는 CV 시스템이 가장 낮았고, EV, Semi-EV 시스템은 비슷한 수준의 영구 변형을 보였다. 하지만 영구 변형뿐 아니라 일정 하중에 대한 변형을 보면 단일황 결합이 주된 EV 시스템이 가장 낮은 변형 결과를 나타내었다. 이로 인해 하중에 따라 변형된 정도와 영구변형의 정도를 비교하게 되면 EV 시스템의 영구 변형이 상대적으로 가장 높게 나타났으며, 따라서 정적 피로저항성 역시 다황결합을 유도함으로써 개선될 수 있음을 알 수 있었다. 결과적으로 동적 피로인 반복변형 시험과 마찬가지로 CV 시스템이 가장 뛰어난 피로 물성을 나타내었다.
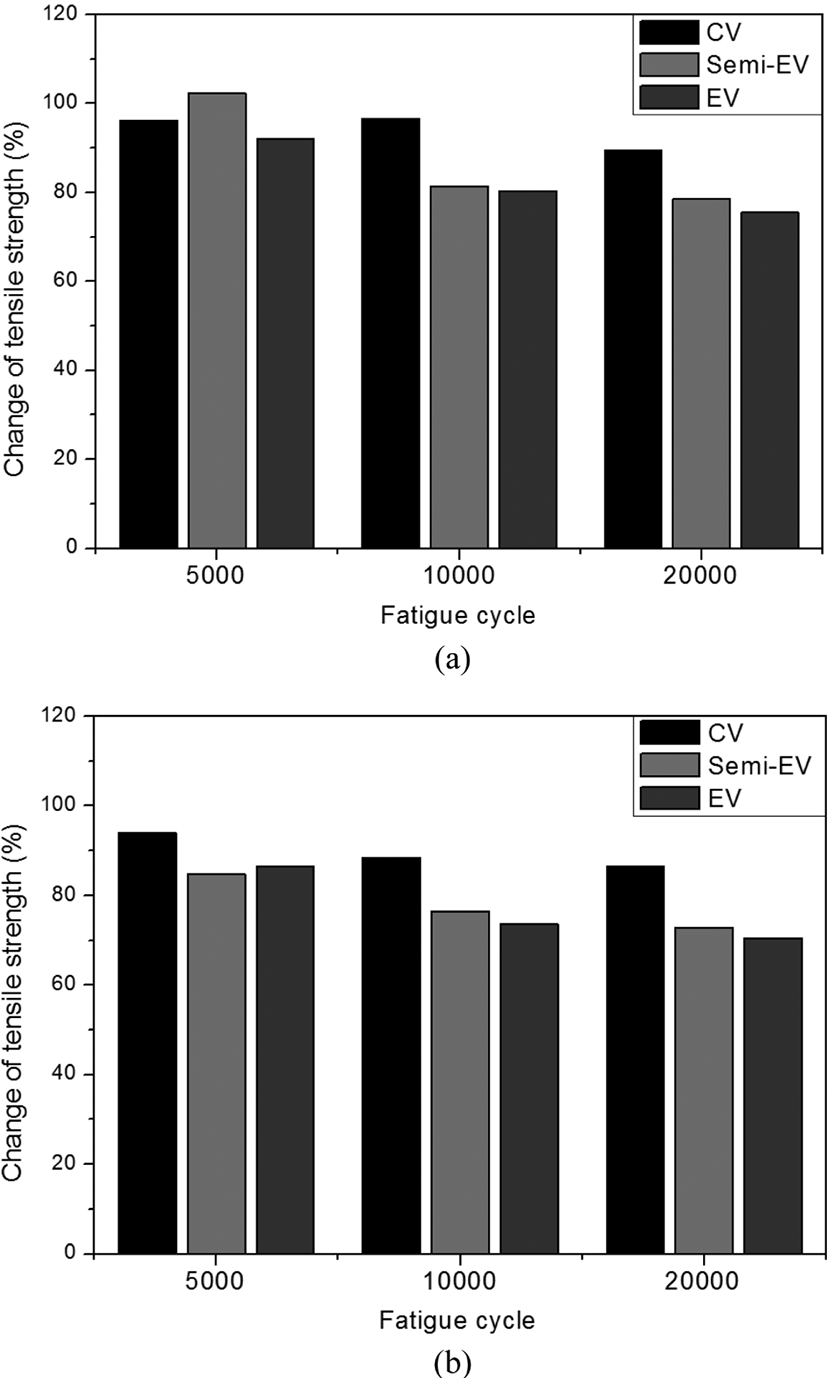
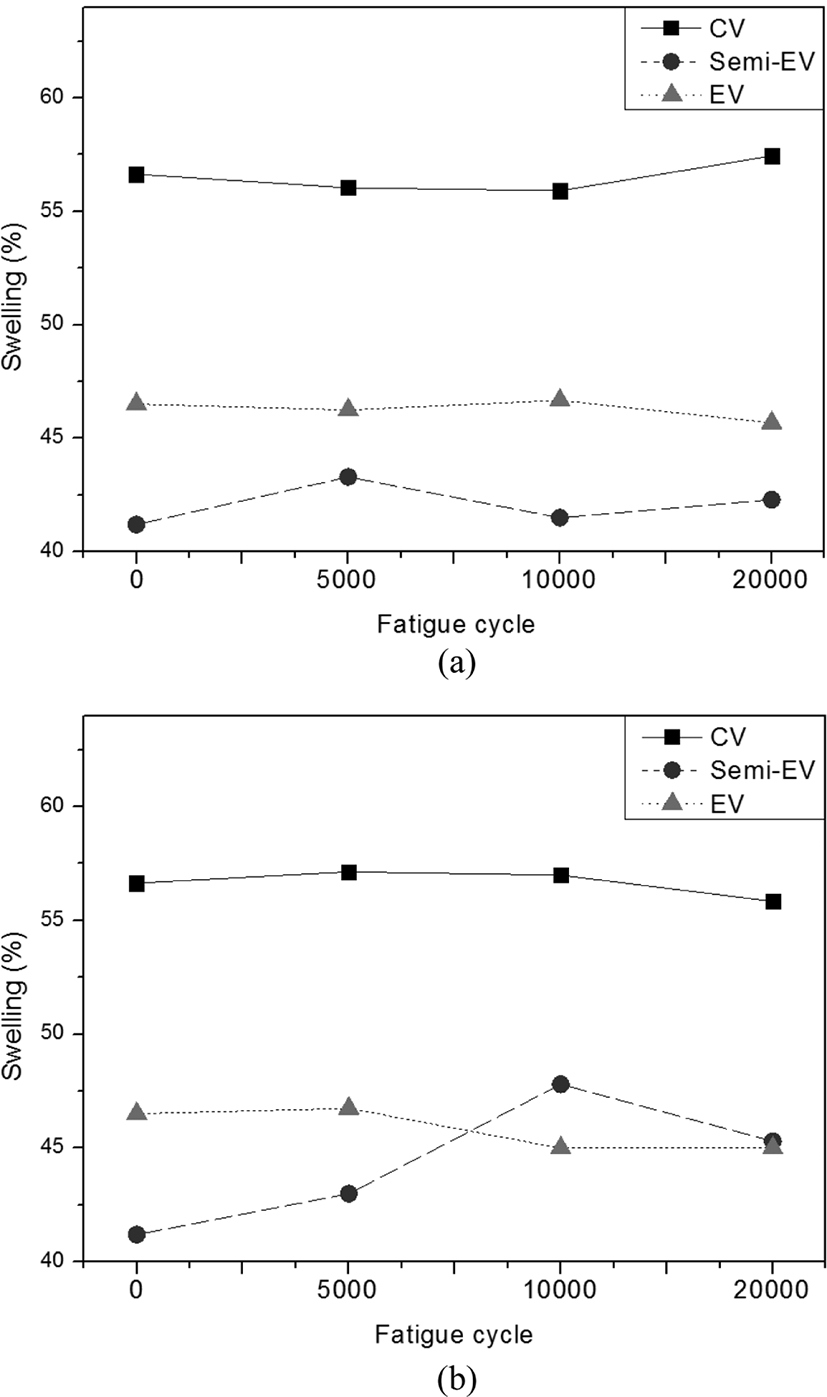
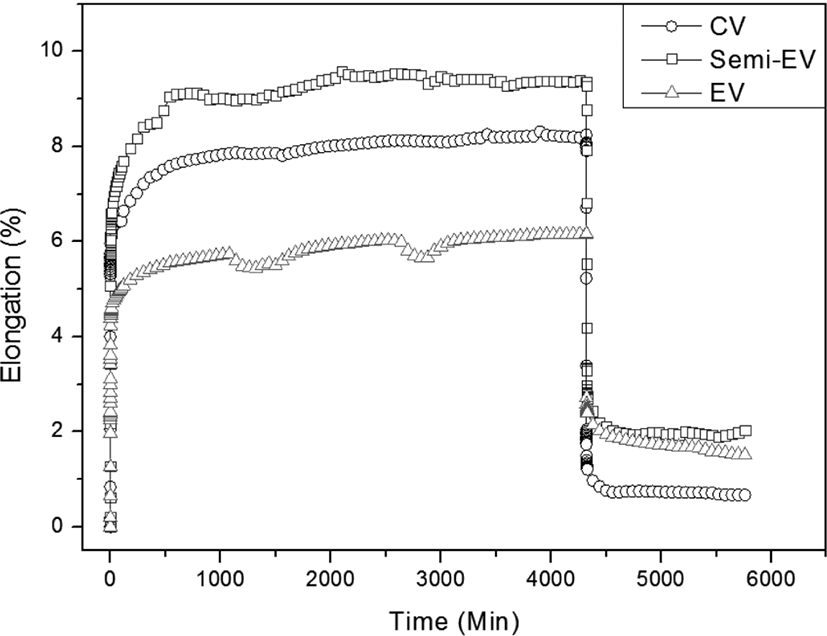
Conclusions
본 연구에서는 자기유변 탄성체의 피로 특성을 개선하기 위해 먼저 같은 경도로 제작된 NR, EPDM, AEM 매트릭스의 반복변형 및 크리프 시험에 따른 피로특성을 비교 후 개선을 위한 매트릭스로 EPDM을 선정하였다. 개선의 방법으로는 Payne 효과에 영향을 주는 카본블랙의 함량 조절과 가교시스템의 변화를 선정하였다. 카본블랙의 함량별 시험에서 반복변형 시험이 진행 된 후 나타나는 인장강도의 감소는 함량, frequency 및 cycle과 비례하여 증가했다. 이 결과가 Payne 효과의 증가와 연관이 있는 것은 RPA를 통한 strain sweep에서의 저장 모듈러스의 변화가 카본블랙의 함량에 따라 증가하는 것으로 나타내었다. 또한 카본블랙의 함량 증가에 따라 물리적 강도는 증가하여 일정 하중에 의한 최대 변형은 감소하였지만 하중 제거 후 영구 변형은 강성 증가에 의해 높아지며 정적 피로에 대한 회복율은 감소하는 결과를 나타냈다. 따라서 재료의 적용환경에 따른 정적, 동적 피로에 대한 적절한 카본블랙 함량이 선택되어야 한다. 가교시스템은 배합비 조절을 통해 CV, Semi-EV, EV-system을 선정하여 진행되었다. 이러한 가교 구조 차이는 XPS를 통해 분석한 결과 CV는 결합력이 낮지만 유연성 높은 다황 가교 구조가, EV는 결합력은 높지만 유연성이 낮은 단일황 가교 구조가 상대적으로 많이 분포되어 있었다. 반복 변형 시험 후 인장강도의 감소는 가교구조의 차이로 인해 CV, Semi-EV, EV-system 순으로 증가하였다. 이로 인해 가교 구조의 유연성이 피로 특성 개선에 영향을 준다는 것을 확인하였다. 이러한 결과는 크리프 시험을 통해서도 나타났는데, 강도가 높고 유연성이 낮은 EV에 비해 강도는 낮지만 유연성이 높은 CV가 하중에 따른 변형율이 높으면서도 하중 제거 후 영구변형이 낮은 것을 통해 회복율이 뛰어나다는 결과를 알 수 있었으며 정적 피로 특성 역시 CV가 우수한 결과를 나타냈다. 하지만 EV-system에 비해 물리적인 강도는 낮은 단점을 가지고 있어서 적절한 가교 구조의 선택이 필요하다고 사료되었다.