Introduction
Bamboo charcoal has been one of the most important bio-charcoal materials. Bamboo charcoal is obtained from bamboo which is carbonized under high temperature. There are innumerable holes crosswise in its structure. It is said that the inner surface of bamboo charcoal reaches 250-300 m2/g. In such large space, microbes can be easily absorbed on it, and the volatile bamboo charcoal contains rich nutriment for microbes, so bamboo charcoal possesses great absorption effect and the microbes it absorbed can decompose the absorbed ingredients clearly. If processing bamboo charcoal under very high temperature (beyond 1200°C), it will emit far infrared ray, release negative ion and absorb electromagnetic wave. Bamboo charcoal also possesses rich trace elements and natural minerals, such as calcium, potassium, sodium, iron, etc.1
Chitosan is a polysaccharide comprising copolymers of glucosamine and N-acetyl glucosamine and can be derived by partial de-acetylation of chitin from crustacean shells. It is also naturally present in some microorganisms and fungi such as yeast. The term chitosan is used to describe a series of chitosan polymers with different molecular weights (50 kDa-2000 kDa), viscosity (1% chitosan in 1% acetic acid, <2000 mPa·S), and degree of de-acetylation (40%-98%).2 Chitosan is insoluble at neutral and alkaline pH values but forms salts with inorganic and organic acid such as glutamic acid, hydrochloric acid, lactic acid and acetic acid.3 Upon dissolution, the amine groups of the polymer are protonated and the resultant soluble polysaccharide is positively charged. The most commonly used forms of chitosan salts are chitosan glutamate and chitosan chloride.4
In recent years, polymer blending has become one of the effective methods for providing new desirable polymeric materials for practical applications. Chitosan blended with poly (vinyl alcohol) (PVA) has been reported to have good mechanical and chemical properties.5 PVA is a nontoxic, water soluble, biocompatible and biodegradable synthetic polymer, which offers good tensile strength, flexibility and barrier properties to oxygen and aroma.6 As a topic of great interest, PVA has widely been used in biomedical and biochemical applications. Chitosan/PVA has been used in the removal of lead ions from aqueous solution due to the adsorption properties. Also, some researchers found formaldehyde or glutaraldehyde have been used as crosslink agent to crosslink chitosan and PVA which could make better interpenetrating polymer network and provide better mechanical properties for the chitosan-PVA hydro-gel (shown in Figure 1),7 due to the adsorption force (hydrogen bonds) with filler particles,8 which also could increase the application of this material, such as the fillers.
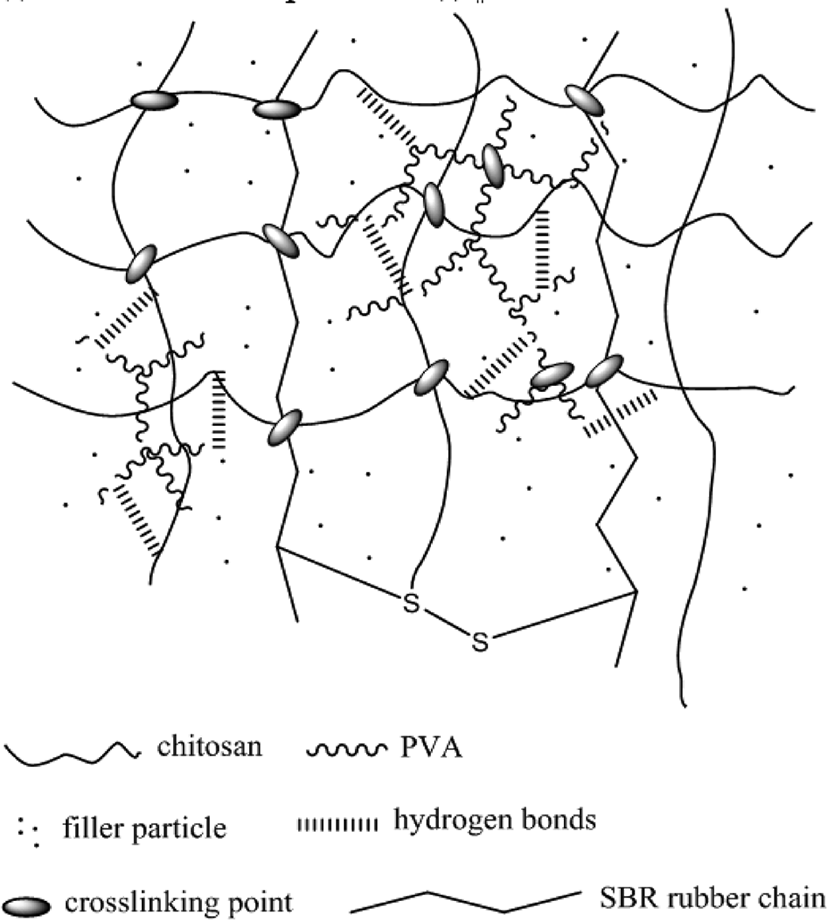
In this research, styrene-butadiene rubber latex composites compatibilized with bamboo charcoal/silica-chitosan-polyvinyl alcohol hybrids by interpenetrating polymer network method9 reported previously, and neat SBR, BC-SBR and SI-SBR composites were also synthesized as control group, and then get the vulcanizates during the curing processes. Finally, the mechanical and viscoelastic properties with various methods were characterized, such as tensile strength, hardness, swelling ratio, storage modulus, loss modulus and tan delta.10
Experimental
Styrene-butadiene rubber latex 1502 (effective mass 61 ± 1%, styrene 23.5%) was obtained from Korea Kumho Petrochemical Company (KKPC), Korea; chitosan powder (microcrystalline) was obtained from DaeJung Company, Korea; bamboo charcoal powder (BC) was provided by Quzhou Minxin Charcoal Company Company, Korea; bamboo charcoal powder (BC) was provided by Quzhou Minxin Charcoal Company, Zhejiang, China; silica was provided by Duksan Pure Chemical Company, Korea; polyvinyl alcohol (PVA) 1500, extra pure (above 95%); sulfur, powder, extra pure (above 99%), and acetic acid, extra pure (above 99%) were purchased from Dae Jung Company, Korea; methanol, extra pure (99.5%); zinc oxide, extra pure (99%); stearic acid, extra pure (95%); dodecyl-benzene-sulfonic acid, sodium salt, (DBS-Na) (50%), formaldehyde, extra pure (above 98%) were purchased from Samchun Pure Chemical Company, Korea; Dodecyl Sulfonate Sodium (DBS-Na), extra pure (above 95%), was purchased from Dae Jung Company, Korea.
A 5 g amount of chitosan flakes was dissolved in 100 mL of dilute acetic acid (2% w/w) at 60°C in a flask placed in a thermostatic water bath with a stirring speed of 148 rpm for 5 h. A 5 g amount of PVA was dissolved in 100 mL of deionized (DI) water in a beaker and agitated on a magnetic stirrer (at about 800 rpm) at 80°C for 5 h. The two solutions were then blended together with stirring on the magnetic stirrer (at about 800 rpm) at 70°C for 48 h, after that, added 10 g silica or bamboo charcoal powder into the system and stirring at about 400 rpm and 60°C for 2 h, then added about 2 g DBS-Na as the dispersion agent into SBR latex to improve the salting-out point of rubber latex. After that, put the latex with DBS-Na into the gel system and stirring at room temperature for 2 h. Finally, dropped about 15 mL 25% formaldehyde aqueous solution into the system at 40°C, then the products had been synthesized. The composites were dried in an oven at 70°C until the weight kept constantly. The compounding process was conducted on a two-roll mixing mill. And the formulation of conventional elastomeric additives was shown in Table 1. Note the sulfur and accelerators were mixed in the final step to avoid the pre-vulcanization. Finally, the compounds were vulcanized under 10 MPa for t90 at 160°C in a heat pressing machine (Auto hydraulic press type, Ocean Science). The thickness of the specimens was about 1 mm. For the purpose of comparison, we also prepared neat SBR, SBR filled with 10 phr silica and 10 phr bamboo charcoal.
The morphology of the samples after the tensile test was carried out on a FE-SEM with EDS (JSM-7500F, JEOL Ltd. Japan). FT-IR spectra of the samples were measured on a Perkin Elmer Spectrum 100S. The cure/vulcanization characteristic of composite samples were measured by a rubber process analysis (RPA) (RPA-V1, U-CAN DYNATEX INC.). The strain sweep test from 0.01 degree to 20 degree was operated at 60°C and 1 Hz, the temperature sweep test from 60 to 160°C was operated at 1 Hz and 1 degree strain on RPA according to ASTM D 6204-97. The hardness of composite samples was obtained by a shore durometer type A following ASTM D22-40. The tensile strength test was measured three times on a Tinius Olsen H5KT-0401 testing machine at a speed of 500 mm/min according to ASTM D 412. The samples were made of a dumb-bell shape with the dimensions of 25 mm × 6 mm × 1 mm after the vulcanization on the heating press machine. The OTR (oxygen transmission rate) of the vulcanizates is measured with an oxygen permeation analyzer (Illinois Instruments Inc., Model 8001, IL) following ASTM D39-85. And swelling tests were carried out in toluene for 1, 2, 4, 8, 16 and 32 h according to ASTM D71-79.
Results and Discussion
Figure 2 shows the SEM graphs of the fracture surface for (a) CS-PVA gel, (b) neat SBR, (c) SI-SBR, (d) BC-SBR, (e) SI-CS-PVA-SBR, and (f) BC-CS-PVA-SBR, all the rubber sample matrixes were characterized after the tensile test, respectively. As can be seen from the graphs, the fracture surface of chitosan-PVA gel was shown in (a), it can be found a smooth and complete surface, which meant the gel has compact structure. And (b) is for the neat SBR, compared to Figure 2-b, c, d, e, and f showed the difference between the neat SBR and composites filled with fillers. From c and d, it can be found more gully-like structure in BC-SBR than SI-SBR, which meant better compatibility with SBR latex. And from e and f, it can be found so much gully-like structure in the pictures, which also meant the interpenetrating network structure was formed into these two composites, and due to the agglomeration effect, silica showed the larger blocks state and larger porous structure into the hybrid system after the tensile strength test. But bamboo charcoal blocks looked smaller obviously, which meant bamboo charcoal had better combination effect with the chitosan-PVA gel system. And due to the hydrophilic properties, bamboo charcoal showed less hydro-philicity compared to the silica, so when fixed with SBR latex, which could improve the interpenetrating network. It also contributed to the most compact structure of matrix, which could provide the best mechanical properties for the SBR latex composites after filling process.
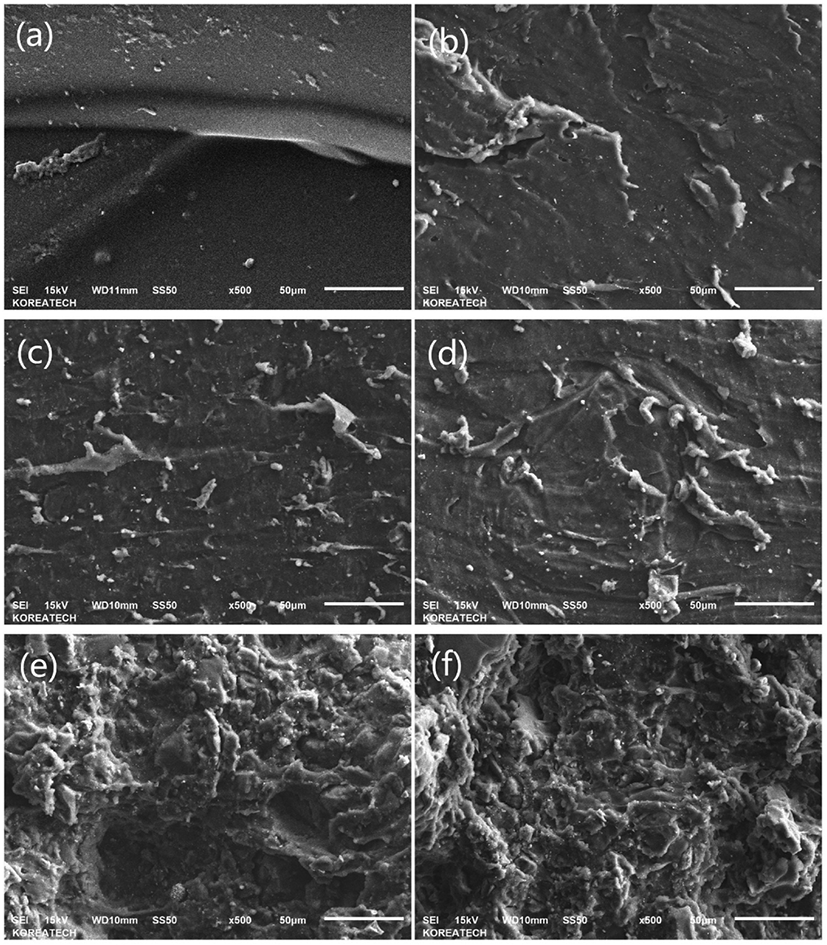
Figure 3 shows the FT-IR spectra of CS-PVA gel, neat SBR and different hybrid filler filled SBR. As can be seen, the peaks at 2915 and 2845 cm−1 are attributed to the methylene asymmetrical stretching vibration and the symmetrical stretching vibration, respectively. The absorption peaks at 1451 and 1495 cm−1 belong to the skeletal vibration of the benzene ring of styrene. The absorption peaks at 700 and 967 cm−1 correspond to the C-H deformation vibrations of the cis-1,4 units and trans-1,4 units of butadiene. The absorption peaks at 911 cm−1 are attributed to the C-H deformation vibration of the vinyl structure of butadiene, and the absorption peak at 1601 cm−1 belongs to the C=C stretching vibration of butadiene. Besides, the peak at 1083 cm−1 arises from Si-O-Si asymmetrical stretching vibration. It can be found that the typical peaks for CS-PVA gel in part A, B, C and D. In part B and C, it can be found the difference between the Neat SBR and hybrid fillers filled SBR, such as –OH group in 3535 cm−1 and during the range from 1000 cm−1 to 1300 cm−1, which meant the synthesizes of hybrid fillers filled SBR composites were successful. And in part A and D, due to the association effect, the typical peaks were not obviously.
The surface chemistry of the reinforcing filler influenced the cure parameters of the rubber. Cure traces of composite samples are shown in Figure 4. As can be seen in the figure, the values of torque difference during vulcanization increased with the hybrid fillers filling compared to the neat SBR obviously, which meant the composites filled with fillers may have better mechanical properties than the neat SBR, SI-SBR and BC-SBR,11 especially, the BC-CS-PVA-SBR had the largest △M (maximum torque – minimum torque), it showed the BC-CS-PVA may make the best reinforcement effect in this research.12 This is mainly due to the hybrid fillers provide the interpenetrating structure and make the more compact SBR matrix.13
Loss factors tan δ of all the samples as a function of strain were presented in Figure 5. From this figure, it can be found at low strain (< 1 degree), the order of tan δ is neat SBR > BC-SBR > SI-SBR > SI-CS-PVA-SBR > BC-CS-PVA-SBR, whereas at high strains (> 1 degree), this trend completely reversed. It is due to different modes of energy dissipation at low & high strain regions.14 At low strain, matrix structure was almost not destroyed, and the viscos nature of rubber would mainly be responsible for the energy dissipation.15 Due to no restriction of filler, neat SBR exhibited the highest tan δ, and BC-CS-PVA-SBR showed the lowest tan δ, which may be interpreted in terms of reduction in deformable rubber fraction. At high strain, the matrix structure was gradually destroyed, and the hysteresis was almost from filler-filler friction due to the destruction of filler agglomerations.16 And the interfacial friction between filler and matrix, the viscos characteristic of rubber fraction released from within filler agglomerations also contributed to the hysteresis.17 As BC-CS-PVA-SBR, the breakdown of filler agglomerations increased filler-filler friction, and in the meantime the weaker interfacial interaction also increased the interfacial fraction between filler and matrix.18 So BC-CS-PVA-SBR exhibited the highest tan δ in high strain region. The temperature sweep results (G’ and G”) were presented in Figure 6 and Figure 7. From the Figure 6, it can be found with increasing temperature, G’ of all the samples decreased before about 140°C, and the value of slope of BC-CS-PVA-SBR is the smallest. but after 140°C, all the sample’s G’ had increased, and the curve of BC-CS-PVA-SBR is always on the top after 70°C, which meant this composite could have the best viscoelastic properties during the vulcanization process. These results showed in the low temperature region, the destruction of matrix structure is more than in the high temperature, this is due to the vulcanization process would achieve in high temperature, before the vulcanization, the matrixes exhibited weak storage modulus which meant the matrix’s structure was also loose.19 And from the Figure 7, it can be found the loss modulus (G”) of all the sample had the same trend with storage modulus (G’), and after 140°C, all the curves turned to slightly increasing, it can be found obviously the maximum G” value of BC-CS-PVA-SBR may appear over 200°C, which meant this composite had the best deformation resistance.
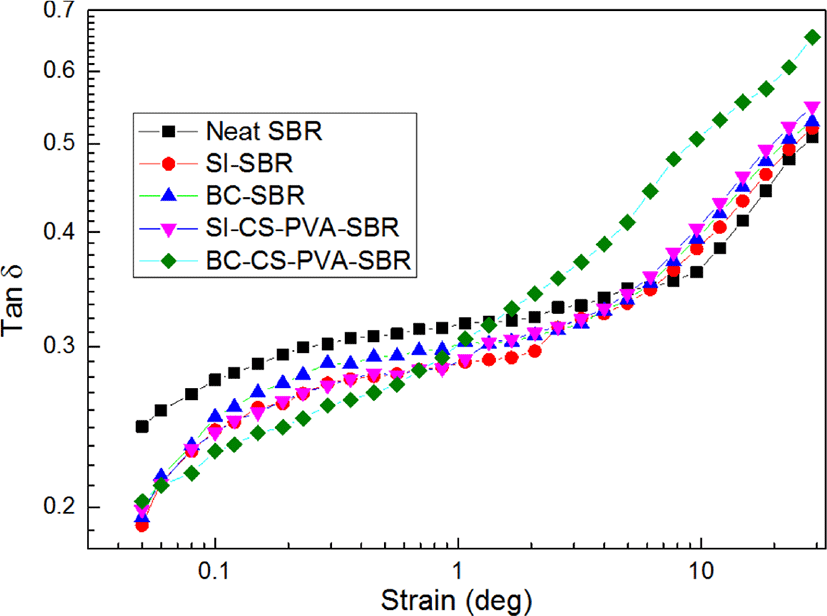
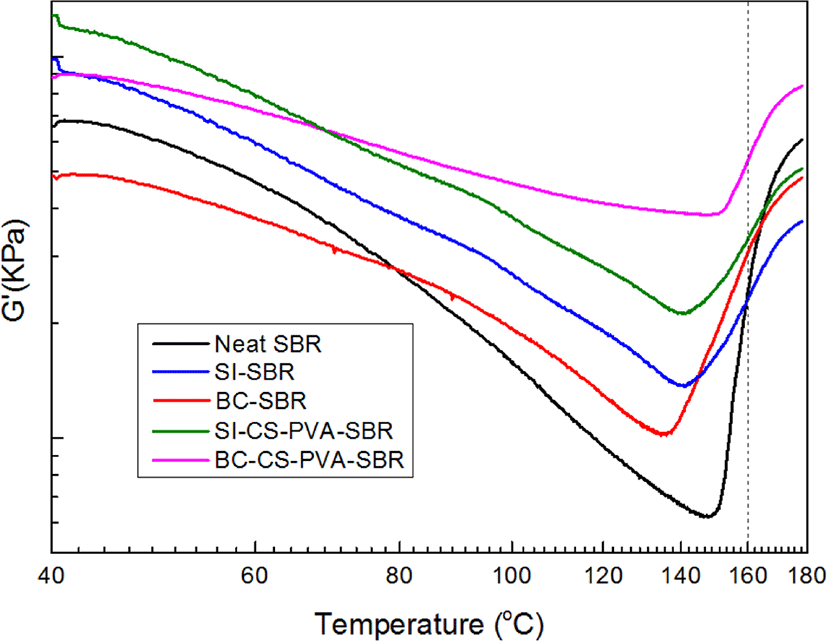
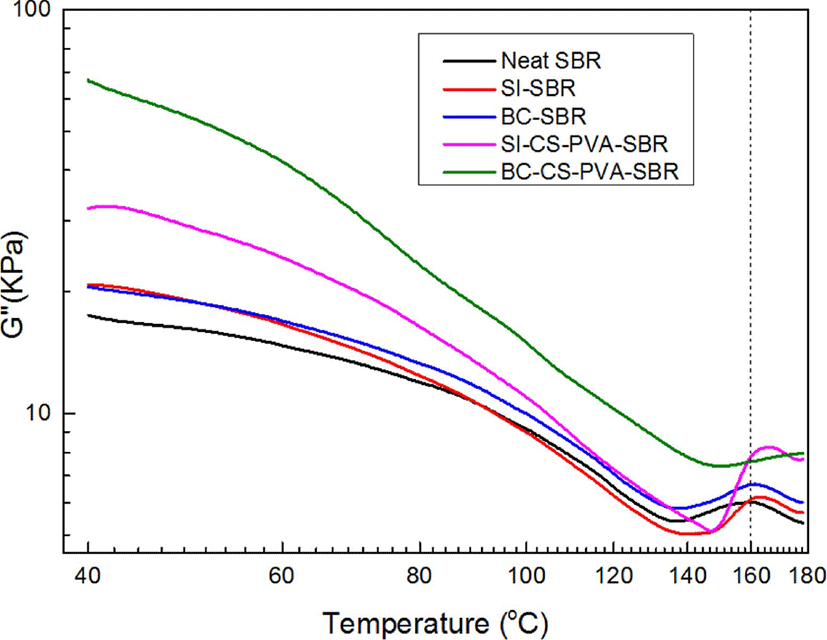
From the Figure 8. The shore A hardness values of the different fillers in the SBR matrix were stronger than that of the neat SBR. This is due to the filler could provide more crosslinking point for matrix during the vulcanization process, which could make the matrix more compact than the neat SBR. Then the rubber matrix had become a whole uniform state with interpenetrating structure,20 so the hardness value had been increase, and the larger hardness value, the more compact matrix structure. In this research, the composite filled with BC-CS-PVA showed the largest hardness value, so it may have the most compact matrix.
Figure 9 showed the results of tensile strength test, from these curves, it can be observed all the hybrid fillers had increased modulus of SBR rubber obviously compared to neat SBR, especially at the strain value of 300%. The reinforcement effect of BC-CS-PVA is the best, which curve has the largest 300% modulus value. The possible reason for this result is BC-CS-PVA not only has interpenetrating network structure which will provide physical crosslinking for rubber chain, but also has more –OH groups, they will provide more hydrogen bonds between hybrid and vulcanizing agent sulfur which form single di-sulfur bonds for chemical crosslinking.21
So it could make better combination with SBR matrix. But as SI-CS-PVA, due to the agglomeration effect, silica cannot make the same reinforcing effect as bamboo charcoal in rubber latex, so the modulus of SI-CS-PVA-SBR was smaller than BC-CS-PVA-SBR, but the elongation of this composite is better than BC-CS-PVA-SBR.
Figure 10 showed the OTR results of all the samples. It could be seen that fillers significantly deceased the oxygen permeability due to the formation of tortuous path. In this research, the more interpenetrating network structure, the less OTR value. And from the results of OTR test, it can be found the hybrid filler filled composites showed the smallest OTR values, which meant hybrid filler could form the better inter-penetrating network structure. Especially the BC-CS-PVA-SBR showed the smallest OTR value, so the interpenetrating network structure of this composite is the most compact, and the crosslinking density of this composite also may be the most.
Figure 11 showed the swelling ratio of all the samples in toluene solvent, the swelling ratio is calculated by the following eq.22
Where w1 is the origin weight of specimens and w2 is the weight of specimens after swelling, ρr is the density of solvent (ρSBR = 0.933 g/cm3), and the ρs is the density of solvent (ρtoluene = 0.867 g/cm3). It can be seen that the swelling ratio increased rapidly at the first 4 h and then flatten out at the next 12 h, indicating the adsorption saturated. The saturated swelling ratio of neat SBR was about 402.6%. When the fillers filled into the SBR matrix, the swelling ratio decreased obviously, due to the large special surface area and porous structure of bamboo charcoal, the swelling ratio of BC-SBR is higher than SI-SBR, it also can be attributed to the hydrophilicity of silica,23 which has just a little dissolved swelling effect. And the composites filled with hybrid showed the great swelling résistance results, especially the BC-CS-PVA-SBR, it showed the smallest swelling ratio during the 32 h, this may due to the most compact inter-penetrating network structure and crosslinking density of this composite, which meant the best swelling resistance.
Conclusions
The chitosan-PVA-bamboo charcoal/silica (CS-PVA-BC/SI) hybrid fillers compatibilized styrene-butadiene rubber composites were fabricated by interpenetrating polymer network (IPN) method. The structures of the composite samples were characterized by various measurements and the mechanical properties of composite samples were systematically discussed in this research. The results in the SEM graphs exhibited the fracture surface of chitosan-PVA gel and all the rubber samples in this research, which could find BC-CS-PVA-SBR has the most compact matrix structure. FT-IR also showed the typical peaks of CS-PVA gel in the curves of SI/BC-CS-PVA-SBR composites and also exhibited some difference peaks compared to the neat SBR. The results of storage modulus and loss modulus of temperature sweep clearly increased by the filling process with the hybrid fillers, which meant the hybrid fillers could improve the viscoelastic properties of SBR rubber matrix. The tensile stress and the hardness both increased with the increasing of hybrid fillers in the SBR matrix, indicated the higher interaction between filler-filler was enhanced with the increasing of interpenetrating network structure, especially the BC-CS-PVA, which showed the largest modulus and hardness values in this research. The OTR results showed that BC-CS-PVA could form the most interpenetrating network structure which could reduce the OTR value, and the swelling ratio test also showed the BC-CS-PVA make the most compact matrix with the largest crosslinking density, which could improve the swelling resistance of rubber material.