Introduction
석유의 사용량이 증가함에 따라 원유를 시추하는 해상플랜트와 시추된 원유를 수송하는 선박의 건조가 증가하고 있다. 하지만 중동, 미국 등의 원유자원이 점차적으로 고갈되어감에 따라 종전에는 기술력 부족으로 원유를 시추하기 어렵고 경제성을 이유로 고려하지 않았던 심해저 지역의 유전개발과 러시아, 알래스카와 같은 극지방의 유전 개발의 필요성이 증가하고 있다. 따라서, 극지방의 플랜트와 선박에서 사용 가능한 혹한의 환경에서 견딜 수 있는 케이블이 필요하다. 현재 내한성을 가지는 케이블은 −40℃에서 견딜 수 있는 전선이 국·내외 보편적으로 사용되는 기술이다. 그러나 실제 극지방에서 사용되기 위해서는 내한 −50℃ 수준의 기술이 필요하다는 것이 선박 및 플랜트 업체들의 의견이다. −50℃까지 견디는 케이블 외피용 컴파운드의 개발이 요구되어 왔지만 기술적 난이도가 높아 현재까지 어려움을 겪고 있다.
이 기술적 어려움의 배경에는 선박 및 해양플랜트용 케이블이 가져야 하는 특성들을 모두 만족하면서 극저온에서 사용이 가능하여야 한다는 것이다. 선박 및 해양플랜트에 사용되는 케이블은 기본적으로 화재가 발생하였을 때 불에 일정시간 동안 노출되어도 방화안전장치와 통신장치가 작동할 수 있도록 전기사용에 문제가 없어야 한다. 또한 불에 탈 때 유독 가스가 발생하지 않게 할로겐프리(halogen free)를 지향하고1,2 연기가 시야를 차단하지 않도록 저연기성(low smoke density)을 요구하고 있다. 특히 원유시추 설비에 사용되는 케이블은 가장 어려운 난연 시험(IEC 60332-3 Category A)에 합격해야 하며, 시추 시 케이블의 외부에 묻게 되는 다양한 화학약품과 독성이 강한 오일에 견딜 수 있어야 한다.
이런 어려운 난연 특성을 만족하기 위해서 현재 해양용 케이블들은 외피에 사용하는 고분자 복합소재에 다량의 난연제를 사용하고 불에 탈 때 char 형성에 도움이 되는 극성기를 가지는 고분자 소재를 사용한다.3-6 고분자 수지는 단독으로 소재의 성능을 발휘하지 못하는 경우가 대부분이다. 소재의 성능을 발휘하고 소재마다 가지고 있는 단점을 보완하기 위해서 여러 첨가제를 혼용하여 특성에 맞는 최종 복합소재를 만들게 된다. 이런 일련의 과정을 컴파운드 처방을 설계한다고 하며 처방 설계에 따라서 비슷한 소재를 사용한 컴파운드의 특성도 크게 변화할 수 있다.7,8
전선 외피에 사용될 컴파운드를 설계함에 있어 그 용도에 맞게 선정해야 할 가장 중요한 요소는 base polymer, 충전제, 가소제, 가교제이다. 이외에 기능성 첨가제들을 통해서 가공성 및 UV 특성 등 부가적인 특성을 부여한다. 따라서 위 4 가지 요소들을 각각 목적 및 가공조건에 맞게 적합한 소재를 선정하는 것이 컴파운드 설계의 기본이며 가장 핵심적인 요소 이다.9
본 연구에서는 고분자 소재로서 극성기를 가지는 ethylene-vinyl acetate (EVA)와 ethylene-propylene-diene-copolymer (EPDM) 및 ethylene-vinyl acetate grafted maleic anhydride (EVA-g-MAH)를 사용하고 난연제로서 silane이 코팅된 수산화알루미늄(Al2(OH)3)과 수산화마그네슘(Mg(OH)2)을 사용하며 가교제로서 dicumly peroxide를 사용하였다. 전선외피용 컴파운드의 내한성을 부여하기 위하여 가소제를 첨가하는데 가소제는 di-2-ethylhexyl azelate, di-2-ethylhexyl adipate, di-2-ethylhexyl sebacate, di-2-butyl sebacate를 사용하여 4 가지 가소제의 종류에 따른 물성의 변화를 조사하고자 하였다.
Experimental
본 연구를 위하여 ethylene-vinyl acetate (EVA) 고분자를 사용하였는데 28% vinyl acetate 함량을 가진 EVA로 Lotte Chemical에서 공급 받았고 제품명은 VC-590 이었다. ethylene-propylene-diene-copolymer(EPDM)은 ethylene 함량이 70%로 Kumho Polychem에서 공급받았고 제품명은 KEP-510 이었다. 또 다른 고분자 물질로 ethylene-vinylacetate-g-maleic ahydride (EVA-g-MAH)인데 이 고분자는 vinylacetate 함량이 15%인 EVA (Lotte Chemical, VS-440)에 maleic ahydride를 1% 가지화(grafting)시킨 것이다. 난연제로는 silane coated aluminum tri-hydroxide (S-ATH, KH-101LC, p/s; 1.0 μm)를 KC 사에서, Magnesium di-hydroxide (MDH, Ultracarb LH15X, p/s; 1.5 μm)는 Likya minerals 에서 공급받았다. 4 가지 가소제들의 분자구조는 Table 1에 나타내었는데, 가소제로 di-2-ethylhexyl adipate (DOA)는 BASF사에서, di-2-ethylhexyl azelate (DOZ), di-2-ethylhexyl sebacate (DOS)와 di-2-butyl sebacate (DBS)]는 Hallstar사에서 공급받았다. 충전제로 silica (K-200D, OCI)를, 노화방지제로 mercaptobenzothiazole (MB, Sigma Aldrich)를 사용하였다. 또한, 활제로 Rheinchemie Additives 사의 Aflux-42M을 사용하였고, 가교제로 dicumyl peroxide (DCP, Sigma Aldrich)를 사용하였다.
Plasticizer | Chemical Structure | Solidifying Point (°C) |
---|---|---|
DOZ |
![]() |
−67.2 |
DOA |
![]() |
−67.8 |
DOS |
![]() |
−69.1 |
DBS |
![]() |
−11 |
극성기가 많은 폴리머를 사용 시 내한성이 매우 좋지 않은 결과를 보였기 때문에 EVA외에 EPDM을 사용하였다. EPDM의 경우 amorphous한 특성이 강하기 때문에 저온에서도 유연성을 많이 잃지 않으리라 판단하였다. 난연성을 위해서 s-ATH와 non-coating MDH를 혼용하여 사용하면서 난연제의 총량을 높였다. EPDM이 내한성이 좋고 난연성이 떨어지므로 가소제의 양을 줄여서 내한성과 난연성의 밸런스를 맞추고자 설계하였다. 배합표는 Table 2에 나타내었다.
고분자 복합소재의 가공은 two-open roll mill (㈜한도기공의 HDM-8-16, 8″ )로 진행하였다. 배합 소재들을 3 분류로 나누어 순서대로 투입하였다. 3 분류를 나누는 기준은 1. 폴리머류, 2. 필러 및 첨가제, 3. 가교제류로 나누었다. 또한 위의 순서대로 roll mill에 투입하게 되는데 먼저 폴리머를 충분한 시간동안 roll mill에서 가공하여 열과 응력을 가해야 폴리머가 가소화되고 필러 및 첨가제들의 분산을 양호하게 해주기 때문이며 가교제를 마지막에 넣는 이유는 빨리 투입할 경우 가공 중 발생하는 열에 의해서 가교가 일어남을 방지하기 위해 마지막에 투입하였다.
모든 배합은 roll mill에서 첫 폴리머를 투입 후 약 2 분간소련시키고 그 후 필러를 투입하여 7분 가량 동안 필러를 혼련시켰다. 가교제를 첨가 후 1~2분 가량 혼련하여 배합을 종료하였으며 모든 혼련 과정에서 삼각 접기 및 rolling 같은 혼련 스킬은 배합마다 7~8회 동일한 횟수로 진행하였다. 물성 검사를 위해 2 mm 가교시트가 필요하므로 배합이 roll mill에서 완료된 고분자 복합소재는 약 3~3.5 mm 두께의 시트로 만들었다.
가교는 hot press로 180℃에서 7분간 하였으며 가교제의 양과 종류를 배합 설계할 때 모두 7분 이내에 t90을 가지도록 설계하였다. 유기과산화물에 의한 가교는 아주 오랫동안 고온의 열을 가하지 않는 이상 가황가교처럼 reversion 현상에 의한 rheometer의 torque값의 감소가 일어나지 않으므로 충분한 가교가 이루어지도록 동일한 가교 시간을 주었다. 아래 Figure 1은 배합과 가교과정을 도식화 한 것이다.
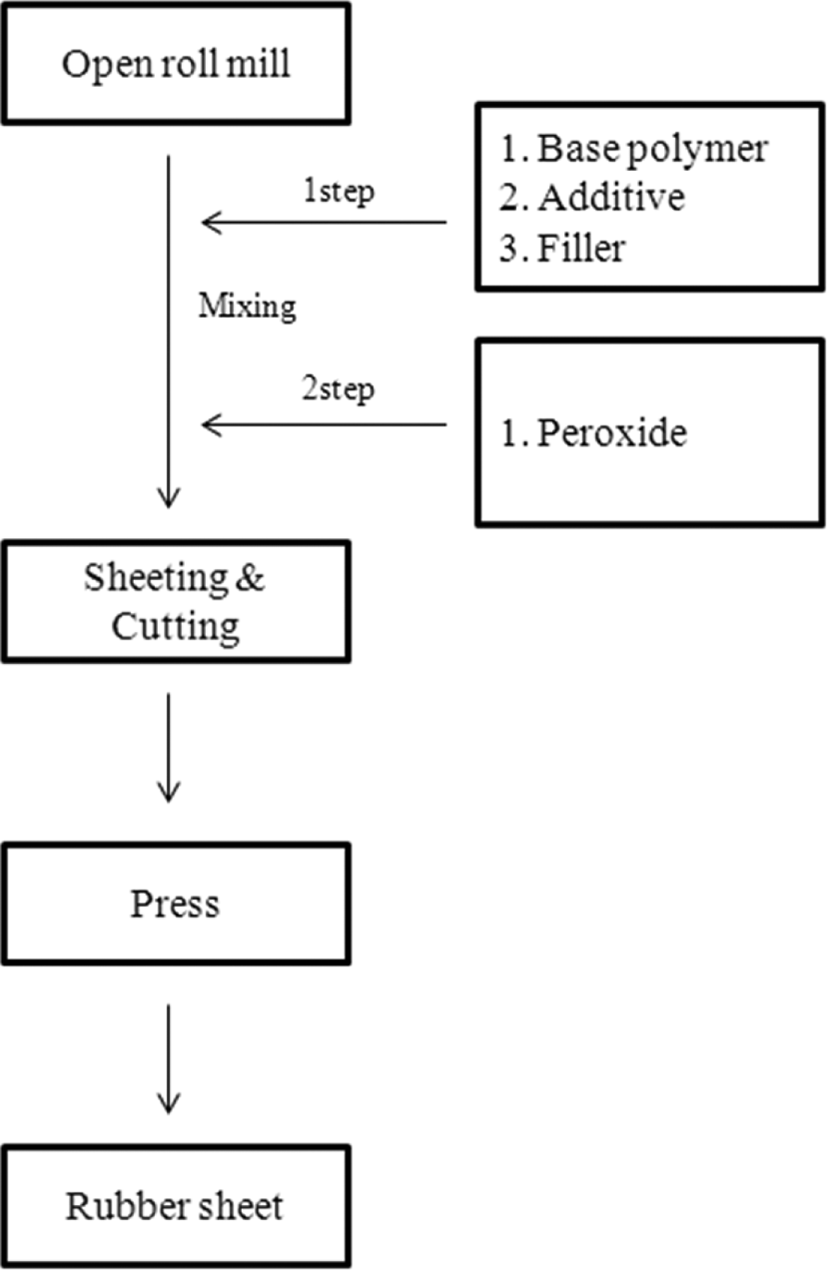
(주)대경엔지니링의 rheometer (DRM-100)을 사용하여 배합 작업을 통하여 가공된 비 가교 시트 약 5~10 g을 잘라내어 rheometer의 torque rotor 위에 올려놓고 180℃ 온도에서 5 bar 의 압력으로 720초 동안 측정하였다.
Mooney 점도는 (주)대경엔지니링 Mooney viscometer (DMV-200C)를 사용하여 가공된 비 가교 시트를 약 5~10 g을 2개 잘라내어 Mooney viscometer rotor 상하에 배치하고 130℃ 온도에서 5 bar 의 압력으로 scorch time (t5)의 시간까지 측정하였다.
덤벨(Dumbell)기로 시험편을 제작하여 인장강도와 신장율을 (주)큐머시스의 QM-100T-2T 모델의 UTM을 사용하여 IEC 60811-1-1에 준하여 측정하였다. 이 때 사용한 시험편은 5개로 가장 높은 값의 시편과 가장 낮은 값의 시편 수치는 제외한 3 개의 시편의 측정 수치의 평균값을 사용하였다. 또한 UTM기로 인장할 때의 속력은 250 mm/min로 설정하였다.
제조된 가교시트를 덤벨기로 시험편을 제작한 후 120℃로 열풍 가열하는 노화 시험기에 일주일간 두어 노화시킨 후 IEC60811-1-2에 준하여 시인장강도 및 신장율 측정할 때와 동일한 장비 및 방법으로 측정하였다. 상온상태에서 측정한 값과 노화 후 측정한 값의 차이가 IEC 60092-360에서 규정하는 잔율% 이내에 들어야 한다.
가교시트를 약 3 mm의 두께와 넓이 6 mm인 형태로 시험편을 만들어 ASTM 2863에 준하여 측정하였다. 측정은 ㈜페스텍의 LIMITED OXYGEN INDEX 2005 모델 기기를 사용하였다. 산소와 질소를 켜고 조절 valve를 2.5 bar 정도로 맞추고 농도를 45~55% 사이로 설정하여 측정하였다. 산소지수는 ± 1의 범위까지 측정하여 그 중간 값으로 산소지수를 결정하였다(ex 산소농도 35%에서 타고 33%에서 타지 않는다면 34%로 산소지수를 결정하였다.).
Results and Discussion
Figure 2과 Table 3에서 DOZ, DOS, DOA는 유사한 MH값을 가지는 반면 DBS는 낮은 값을 보였다. 이는 DBS가 낮은 내열성을 가지고 있기 때문으로 판단된다. DBS가 낮은 내열성을 가지는 이유는 분자 구조가 원인으로 판단된다. 다른 내한성 가소제들과 비교하여 DBS의 경우 주쇄에 긴 가지 사슬이 붙어 있지 않으며 이는 주쇄에 COO− 구조가 외부의 열이나 화학적 반응에 다른 가소제들 보다 쉽게 노출 될 수 있음을 예상할 수 있다. 비공유 전자쌍을 가지는 주쇄에 산소(O)와 함께 C-H구조와 비교하여 비교적 반응성이 좋은 C=O 구조가 열에 의한 라디칼 형성을 다른 가소제들에 비해 쉽게 일으킬 수 있게 되고 이는 DBS가 포함된 컴파운드의 내열성이 감소됨을 의미한다. 또한 이를 통해 비교적 가운데 C-C사슬이 짧은 DOA도 반응성이 좋은 COO− 기가 가까워 다른 가소제들에 비해 내열성이 떨어질 것을 예상해 볼 수 있다. DBS와 비교하여 상대적으로 MH값이 낮게 감소한 것을 보면 가운데 주쇄의 C-C 구조의 길이 보다는 가지 사슬의 영향이 더 큰 것을 알 수 있으며 상대적으로 가지 사슬이 가장 큰 DOZ가 가장 우수한 내열성을 가지는 것으로 예상할 수 있다.
#1 | #2 | #3 | #4 | |
---|---|---|---|---|
t90 (min:s) | 4:00 | 3:36 | 3:44 | 3:44 |
MH (torgue) | 63.3 | 61.1 | 60.8 | 56.1 |
ML (torgue) | 10.6 | 10.0 | 9.6 | 9.7 |
ΔT (torgue) | 52.7 | 51.1 | 51.2 | 46.4 |
Table 4에서 확인할 수 있듯이 Mooney 점도는 DOS와 DBS의 경우 DOZ와 DOA에 비하여 미세하게 큰 값을 보이나 전반적으로 4가지 가소제에 따라 큰 차이는 보이지는 않았다. 단지 DOZ와 DOS의 scorch time이 DOA와 DBS의 scorch time 보다 더 김을 알 수 있었다.
#1 | #2 | #3 | #4 | |
---|---|---|---|---|
Initial | 56.1 | 57.1 | 67.6 | 68.2 |
Mooney Viscosity | 34.3 | 34.5 | 35.8 | 36.6 |
Scorch Viscosity | 39.3 | 39.5 | 40.8 | 41.6 |
Scorch Time (t5) | 9:05 | 6:26 | 8:54 | 6:07 |
Table 5와 Figure 3에서 DOZ, DOA, DOS는 유사한 상온 물성 값을 보여 주었고 상대적으로 가교도가 떨어지는 DBS의 경우 낮은 인장강도와 높은 신장율을 보였다. 이러한 결과는 Rheology와 같은 이유(가장 작은 ΔT)로 해석되었다.
#1 | #2 | #3 | #4 | |
---|---|---|---|---|
Crack at −60°C | 1/3 | 2/3 | 2/3 | 3/3 |
Figure 4의 노화 데이터를 보면 알 수 있듯이 내열성이 약한 가소제가 첨가된 #2(DOA)과 #4(DBS)의 인장강도가 높으면서 신장율이 감소한 것을 확인할 수 있었다. 이는 오랜 시간 높은 온도에 노출되면서 내열성이 떨어지는 컴파운드에서 라디칼이 형성되고 이 라디칼이 반응을 일으켜 일종의 과가교 현상을 일으키는 것이 원인으로 판단되었다. 과가교 현상이 발생하면서 컴파운드가 경화되고 딱딱해지면서 유연성이 감소하고 신장율이 줄어들고 인장이 상승하는 것으로 해석되었다.
Figure 5에서 LOI 값은 31.7에서 31.9로 큰 차이가 없어 4 종류의 가소제 모두 유사한 것으로 판단되면서 가소제의 종류에 따라서 난연성은 크게 변하지 않는 것으로 판단되었다. 그러나 자기소화성(self-extinguishing)을 나타내는 LOI 값이 27 이상10으로 4종류의 컴파운드는 자기소화성을 발현하는 난연성을 가지는 것으로 판단되었다.
Table 6의 내한성의 경우 DOZ가 3개 중 1개의 crack만 발생하여 가장 우수한 내한성을 보였으며 DBS의 경우 3개 모두 crack이 발생하여 내한 가소제로 적합하지 않음을 알 수 있었다. 이는 Table 1에서 보는 바와 같이 4가지 가소제 중 DBS가 응고점이 다른 3개의 가소제 보다 유독 높은데 응고점이 높은 가소제는 컴파운드의 저온 유연성을 감소시켜 내한성을 감소시키는 것으로 판단되었다.
Conclusions
선박에 사용되는 전선피복용 고분자 컴파운드를 제조하기 위하여 EVA와 EPDM 및 EVA-g-MAH를 고분자로 사용하여 난연제, 가소제, 충전제, 노화방지제, 활제, 가교제를 넣고 배합하였다. 가소제는 4 종류(DOZ, DOA, DOS, DBS)를 사용하면서 그 종류에 따른 물성을 조사하였다. Rheology는 가지 사슬이 가장 큰 DOZ가 내열성 증가에 의하여 MH와 ΔT가 가장 큰 값을 보였다. Mooney 점도는 DOS와 DBS의 경우 DOZ와 DOA에 비하여 미세하게 큰 값을 보이나 전반적으로 가소제에 따라 큰 차이는 보이지는 않았다. 인장강도와 신장율은 DOZ, DOA, DOS는 유사한 상온 물성 값을 보여 주었고 가교도가 낮은 DBS의 경우 낮은 인장강도와 높은 신장율을 보였다. 노화시험에서는 내열성이 약한 가소제가 첨가된 #2(DOA)과 #4(DBS)가 인장강도가 높으면서 신장율이 감소한 것을 확인할 수 있었다. 그리고 가소제의 종류에 따라서 난연성은 크게 변하지 않는 것으로 판단되었다. 내한성의 경우 DOZ가 가장 우수한 내한성을 보였으며 DBS의 경우는 내한 가소제로 적합하지 않음을 알 수 있었다.