Introduction
환경 오염 및 석유자원의 고갈에 따른 각국의 환경 규제 대응 방안으로 자동차의 연비 향상과 관련된 많은 연구들이 진행되고 있다.1 또한 전력 기반 자동차로 자동차 산업의 패러다임이 바뀌는 시점에서도 전기자동차의 주행거리가 차량 경량화에 의해 많은 영향을 받기 때문에 관련된 다양한 연구가 진행되고 있으며,2 이에 따라 고강성 화학소재 및 섬유강화복합재료(Fiber Reinforced Composite)가 적용된 자동차 부품의 개발이 꾸준히 증가하고 있다.3,4 고강성 화학 소재는 기존 비보강 플라스틱 대비 강성 및 내열도가 우수하여 기존의 화학 소재가 접근하기 어려운 많은 부품에 적용이 가능케 하였다. 수퍼엔지니어링플라스틱(Super Engineering Plastic)은 우수한 기계적 강성 뿐만 아니라 높은 내열특성으로 인하여 내연기관 자동차 및 전력 기반 자동차의 적용이 확대될 것으로 예상되는 소재이나, 국내에서는 일반적으로 많이 연구되는 범용수지 혹은 엔지니어링 플라스틱 대비 상대적으로 생소한 소재이다.5-7 수퍼엔지니어링플라스틱 중 폴리페닐렌설파이드 (PPS: Polyphenylene sulfide)는 우수한 내열 특성 외에도 강한 내화학특성을 지니고 있어 향후 극한환경에 노출되는 다양한 자동차용 부품에 적용이 확대될 것으로 예상된다. 최근 국내에서도 생산 인프라가 구축되면서 관련 분야의 연구 증가되고 있는 추세이다.8-10
PPS 수지는 Figure 1에 보여지는 것과 같이 벤젠링에 황이 결합된 구조로 일반적인 경우 사용 가능 온도가 약 218°C에 이르며, 200°C 이하의 온도에서는 녹일 수 있는 용매가 아직까지는 없는 내화학성이 매우 우수한 소재로 알려져 있다.10,11
본 연구에서는 상대적으로 국내에서는 많은 연구가 수행되지 않은 수퍼엔지니어링 플라스틱으로 구분되는 PPS 수지의 압출가공 온도조건과 수조의 냉각온도에 따른 복합소재의 물성 변화를 분석 하였으며, 각기 다른 표면 전처리가 진행된 유리섬유에 적용함에 따라 발생하는 소재의 기계적 물성의 차이를 분석하였다.
Experimental
본 실험에서는 국내 SK Chemical 社에서 개발된 PPS 베이스 수지를 사용하였으며, 해당 수지의 비중은 1.35, 용융점도 600 poise, 830 g/10 min 이며 용융 온도는 281°C 이다. 보강을 위하여 사용된 유리섬유는 상업적으로 널리 활용되는 Owens Corning 社(제품명: 910-10P) 및 Jushi 社(제품명: J-584)의 PPS용 복합소재용으로 생산된 유리섬유 소재를 보강재로 사용하였다. 실험에 사용된 유리섬유의 기본 정보는 아래 Table 1에 정리하였다. 압출 온도에 따라 미치는 영향성을 보기 위하여 아래 Table 2에 표기된 것과 같이 각기 상이한 가공온도 조건에서 소재를 압출하였으며, 사출온도는 300°C 이며 금형온도는 80°C로 동일한 온도조건에서 시편의 사출을 진행하였다.
Supplier | Diameter (μm) | Shape | Fiber length (mm) | Remark (Applications) |
---|---|---|---|---|
O Co. | 10.0 | Chopped fiber | 4.0 | PPS, LCP, TPU, PPO etc. |
J Co. | 11.0 | Chopped fiber | 4.5 | PPS |
PPS 소재의 압출가공시 냉각조건에 따른 물성변화의 경향을 확인하기 위하여 압출기 앞 수조의 냉각수 온도를 다르게 설정하여 결정화도의 차이가 발생하도록 조건을 설정하였다. 냉각조건 1의 경우는 수조의 온도를 10°C ± 5 조건으로 설정하고 이축 압출기에서 혼련되고 나오는 수지를 침지하여 냉각하였으며, 냉각조건 2의 경우는 수조의 온도를 50°C ± 5 조건에서 침지하는 조건을 설정하였다.
베이스 수지와 보강재인 유리섬유의 성분비는 6:4가 되도록 투입량을 조절하였으며, 이러한 방법으로 준비된 소재는 사출공정을 거쳐 시편으로 만들어졌다. PPS 베이스 수지와 유리섬유의 혼련은 2축 압출기(SM PLATEK φ = 41, L/D = 36)를 사용하였으며, 시편제조를 위한 사출기는 150톤 사출기(LS 캠트론)를 사용하였다. 제조된 시편의 인장 및 굴곡 특성은 만능시험기(MTDI UT-100F)를 사용하였으며, 내열도 측정을 위하여 HDT (Qmesys, QM950H), 충격강도는(Tinius Olsen, IT 406)를 사용하였다. 복합소재의 상용성 분석을 위하여 시편을 액체질소에 침지하여 냉동시킨 후 파괴하여 단면을 주사전자현미경(Hitachi, S-4300)을 사용하여 분석하였다. 베이스 PPS 수지의 용융 온도는 DSC (TA Instrument)를 이용하여 분석하였다. GF의 함량은 전기로(Han Tech, C-A14P)를 활용하여 복합재의 무게와 고온 노출 이후 남은 재(ash)의 무게차이를 통하여 확인하였다. 고분자 수지의 온도에 따른 점도 변화는 레오미터(Anton Paar, MRC 402)를 이용하여 분석하였다.
Results and Discussion
압출온도에 따른 PPS 복합재의 강성변화를 분석하기 위하여 Jushi 사의 GF와 PPS 수지를 선정하여 실험하였다. PPS 수지와 유리섬유의 혼련시 가공온도 분석을 위하여 DSC와 레오미터 분석을 통하여 수지의 용융온도를 우선적으로 확인하였다. 소재의 용융 온도는 아래 Figure 2에서 보여진 것과 같이 약 270°C 에서부터 용융이 시작되며, 용융온도 값은 280°C로 나타났으며, 218°C 에서 결정화 온도를 보였다. 레오미터 분석(Figure 3)의 경우에도 PPS 수지의 점도가 급격히 낮아지는 온도는 약 270°C 인 것으로 확인되었다.
유리섬유가 고분자 수지내에서 분산이 잘 된 경우 유리섬유의 강성을 수지에 부여할 수 있게 되며, 이때 섬유의 배향방향으로 고분자 복합재의 강성을 향상시킬 수 있다. 이와 같은 이유로 비보강 수지에 비하여 유리섬유가 보강될 경우 소재의 인장강도는 매우 크게 향상된다.12 앞서 언급한 이유로 복합재의 인장강도에 대한 영향성은 섬유의 배향 방향과 섬유의 분산성으로 인한 요인이 매우 클 수 밖에 없다. Figure 4에는 압출 온도조건에 따른 PPS 복합재의 인장강도 값을 정리 하였다. 베이스 소재의 용융온도 대비 약 10도 높은 290°C에서 350°C 까지 압출가공온도에 변화를 주었으며, 가공온도 320°C 에서 혼련된 수지의 경우 가장 높은 인장강도 값을 보여주었다. 섬유형 보강재의 경우 수지내에서 분산성 정도에 따라 소재의 강성에 영향을 준다. 따라서 용융온도 대비 40°C 이상의 고온조건에서 유리섬유가 가장 효과적으로 분산된 것으로 판단된다. 또한 본 실험을 통하여 유리섬유 40%가 함유될 경우 베이스 수지 대비 최소 3배 이상의 강성이 향상됨을 확인할 수 있다. 그 밖에 굴곡, 충격강도 및 내열 특성의 경우에도 320°C 에서 가장 우수한 특성을 보이나 압출 온도별 차이점은 인장강도 결과값처럼 크지 않았다(Table 3).
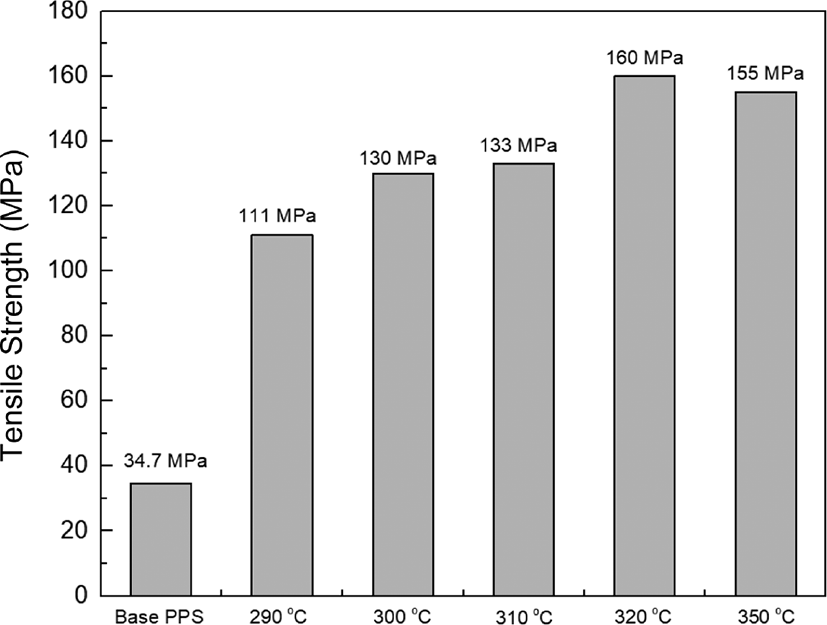
결정성 수지의 경우 냉각되는 조건에 따라서 결정화도의 변화가 발생하게 되며, 이러한 특성으로 인하여 사출시 금형의 냉각온도 조건을 최적화 해야 한다.13 PPS 수지의 경우 결정성 수지로서 압출 가공시 냉각 조건에 따라 소재의 물성 변화가 발생할 수 있을 것으로 예상되었으며, 이축압출기의 가공 후 수지가 냉각되는 수조의 온도를 조절하여 결정성 수지의 특성 변화를 분석하였다. 수조온도 10°C(냉각조건1)와 50°C(냉각조건2)의 공정변화에도 인장강도, 굴곡강도, 및 충격강도 값의 경우 앞서 기술한 압출온도 320°C 조건에서의 제조된 수지의 경우와 유사한 값을 보였다. 하지만, 냉각수의 온도가 낮은 경우 PPS 수지의 펠렛에서 상대적으로 공극이 많이 발생하는 것을 확인할 수 있었다(Figure 5). 이는 냉각이 급격히 진행되어 결정성 수지의 수축이 크게 진행되었기 때문에 수지와 유리섬유간의 분리가 발생한 것으로 판단되며, 냉각온도가 상대적으로 높은 경우 수지와 섬유간 분리현상이 감소하여 공극의 발생빈도가 감소한 것으로 판단된다. 냉각조건 1과 같은 공극은 유리섬유와 수지의 함침에 영향을 미칠 수 있으며, 따라서 PPS 수지의 물성을 최적화 하기 위해서는 사출 공정시 냉각조건뿐만이 아니라 압출가공시에 냉각조건 또한 최적화 할 필요가 있을 것으로 판단된다. 또한 이러한 공극의 발생은 초기 물성조건의 변화보다는 소재의 내구성에 영향을 줄 수 있는 요소로 판단된다.
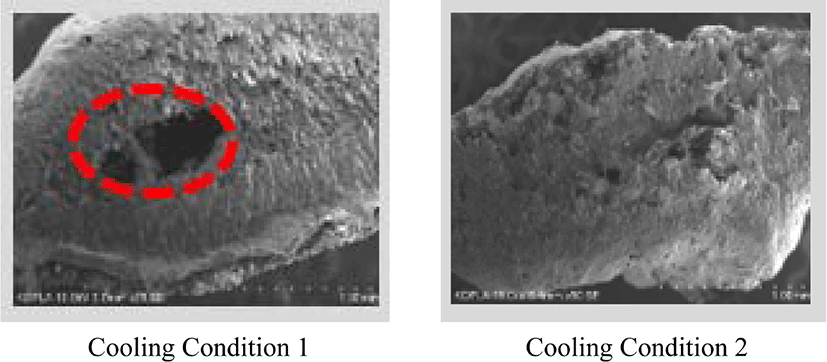
일반적으로 유리섬유와 고분자 수지는 상용성이 좋지 않으며, 따라서 유리섬유를 표면처리 없이 가공할 경우 고분자 수지와의 상용성이 현격하게 감소하여 원하는 물성을 구현할 수 없다. 이와 같은 이유로 유리섬유 제조사들은 고분자 수지와의 상용성을 향상하기 위하여 작용기와 반응할 수 있는 표면처리를 진행하여 수지와의 상용성을 향상시키게 된다.14 유리섬유의 표면처리는 일반적인 분석법으로는 정확하게 적용되는 성분의 분석을 진행하기가 용이하지 않다. 상용화되어 판매되는 유리섬유의 종류에 따른 물성값 비교를 위하여 소재의 압출가공온도 및 사출조건은 동일하게 설정한 후 제조사가 상이한 유리섬유 2종을 적용하여 압출 및 사출가공한 이후 소재의 기계적 강성을 분석하였다. 그에 따른 PPS 복합재의 물성강도 값 비교 결과는 아래 Table 4 에 정리하였다. 2종 모두 PPS에 사용이 가능하도록 사이징 처리가 된 제품으로 상업화 된 제품이지만 두 보강재를 적용했을 때 결과값은 매우 상이한 특징을 보인다. 보강제 제조사에 따라 인장강도 값은 160 MPa 와 110 MPa로 매우 큰 격차를 보여주었으며, 충격강도 값 또한 상대적으로 큰 차이를 보인다. 각기 다른 유리섬유가 적용된 복합재의 유리섬유 함량분석을 위하여 전기로를 800°C 설정한 후 고온 노출전과 후의 복합재의 Ash 함량을 분석시 J-584의 경우 실제 유리섬유 투입량과 유사한 39 ± 2 wt%의 잔류물 함량을 보인 반면 910-10P의 경우에는 이보다 적은 34 ± 6 wt%의 잔류물 함량을 보인다. 이러한 특성은 유리섬유를 압출 가공하여 수지에 분산할 경우 유리섬유(J-584)가 상대적으로 고른 분산을 보인 결과로 판단되며, 910-10P 제품은 상대적으로 분산성이 낮음에 기인한 것으로 판단된다. SEM 을 통한 복합재의 단면 분석시에도 Jushi사 제품은 수지가 유리섬유에 고르게 젖어 있는 반면에 Owens Corning사 제품의 경우는 수지와 섬유간 공간이 관찰되는 경우가 있어, 제조사별로 상이한 사이징 처리에 따른 분산성 차이에 발생한 것으로 판단된다(Figure 6). 하지만 본 실험에서는 사용된 유리섬유의 FTIR 이나 TGA 분석시 차이점은 관찰되지 않았다.
Properties | PPS GF 40% (GF: J Co.) | PPS GF 40 (GF: O Co.) |
---|---|---|
Tensile Strength (MPa) | 160 | 110 |
Izod Impact Strength (KJ/m2) | 52.7 | 38.5 |
Conclusions
본 연구에서는 상대적으로 국내에 많이 알려지지 않은 수퍼엔지니어링 플라스틱을 복합화 하면서 온도에 변화에 따른 가공조건에 영향성과 각기 다른 방법으로 사이징 처리된 것으로 추정되는 유리섬유 적용에 따른 복합소재의 물성 차이를 분석하였다. PPS 수지의 용융온도는 290°C 이지만 GF 함량이 40% 인 경우에는 이보다 높은 320도 이상의 조건에서 GF의 분산이 효과적으로 되는 것을 확인하였다. 결정성 수지의 경우 냉각조건에 따라 다른 결정화 특성을 보이며, 이에 따른 수축율의 변화가 발생할 수 있다. PPS 수지의 경우 매우 높은 온도에서 압출가공하게 되며, 냉각 조건에 따라서 GF 함침특성에 영향을 줄 수 있음을 확인하였다. 또한, 동일목적으로 제조된 유리섬유의 경우라도 제조사에 따른 복합재의 물성강도 차이가 매우 큰 것을 확인하였다. 유리섬유의 형상이 유사한 제품을 사용하였기 때문에, 물성의 차이는 유리섬유의 사이징 처리에 따른 분산성 차이에 기인한 것으로 판단되며, 섬유의 사이징 처리를 위해 적용된 성분의 분석은 추후 연구를 통하여 정밀 분석할 예정이다. 본 실험을 통하여 PPS 소재의 경우 유리섬유를 적용하여 복합소재로 제조할 경우 일반적인 엔지니어링 플라스틱 대비 가공 조건 설정이 어려운 점을 확인하였으며, 소재의 특성을 극대화 하기 위해서 다양한 실험을 통한 최적화가 필요한 것을 확인하였다.