Introduction
Ethylene-propylene-diene-termonomer (EPDM)는 Ethylene-propylene rubber (EPR)에 가교를 위한 불포화 결합을 가지는 Diene이 공중합 된 고무로 주쇄가 아닌 측쇄에 불포화기를 가지고 있어 내오존성, 내후성, 내산화성, 전기절연성 등이 뛰어나다.1,2 그래서 EPDM은 주로 창틀용 압출 채널 (Channel), 중간전압 및 고전압 케이블 커버, 자동차 타이어 튜브, 전선, 패킹, 패드, 각종 산업용품, 자동차 엔진의 방진 등의 넓고 다양한 용도에 사용되고 있다.3,4
하지만 EPDM은 탄소와 수소 원자를 가지고 있어 열에 의해 사슬이 분해되어 다량의 가스와 분해물이 발생한다. 또한, 생성된 분해물이 산소와 반응하여 연소하고 발생한 열이 다시 고분자를 분해하는 연쇄반응이 일어나게 되어 지속적인 연소가 일어난다.5 이러한 고분자 수지의 지속적인 연소를 완화하거나 억제하는 방법으로는 고분자 자체의 내열성 향상, 난연성 재료와의 복합체 제조, 난연성 물질의 표면 코팅, 난연제 첨가 등이 있다.6
그중 난연제를 첨가하는 방법을 주로 사용하고 있으며, 연소과정에서 발생하는 가연물, 산소, 점화원을 물리, 화학적 방법으로 완화하거나 억제한다. 난연제는 고분자 내에서 흡열을 통한 열에너지 제거, 연소 시 불연성 가스 생성, 활성 라디칼 흡수를 통한 연속반응, 제거 반응 등을 일으킨다. 이러한 첨가형 난연제 방법은 수지와의 혼화성이 좋아야 하며 제품의 기계적인 물성 변화가 적어야 한다.7,8
난연제의 종류로는 크게 할로겐계 난연제와 무기계 난연제로 나눌 수 있으며, 할로겐계 난연제는 브롬계와 염소계, 무기계 난연제는 인계와 수산화알루미늄이 대표적이다.8 이중 브롬계 난연제는 가격 대비 난연성이 좋아 가전제품의 외장재, PET, PS 등의 주요 난연제로 사용된다. 브롬계 난연제는 Polybrominated biphenyls (PBBs), Polybrominated diphenyl ethers (PBDEs), Tetrabromobisphenol A (TBBPA) 등 세 종류가 대표적이며, 그중 PBBs는 이미 1970년대부터 발암성과 간독성이 확인되어 사용 중지된 상황이다. 나머지 브롬계 난연제 역시 인체에 유해하다는 보고가 최근 확인되고 있다.9 게다가 환경규제 물질로 지정되어 사용이 제한되는 추세이며, 이를 대체하기 위한 친환경 난연제 사용이 요구되고 있다.
한편, 무기계 난연제는 유기계 난연제와 달리 흡열량이 높고, 연소 시 분해로 인한 흡열반응과 탈수 현상으로 연소를 억제한다. 수산화알루미늄 난연제는 대표적인 무기계 난연제로, 분해온도는 200°C 이상으로 고분자의 성형가공 온도 범위에서 안정적이며, 가격이 저렴하여 건축자재, 전선, 가전제품 등 다양하게 사용되고 있다.10,11 다른 무기계 난연제인 수산화마그네슘은 연기 발생이 적고, 부식성이 낮으며, 높은 온도 안정성이 장점이다. 또한, 분해온도가 330°C로 매우 높고, 특히 카본블랙 등과 사용하면 난연 효과가 향상된다. 특히, 수산화 계열의 난연 메커니즘은 연소 시 흡열반응과 함께 물을 생성하여 난연 효과와 생성된 물에 의한 냉각작용으로 연소를 방지한다.11 현재 가격이 저렴하고 유독가스 및 연기 발생을 억제하는 등의 특징을 가지고 있어 향후 안정적인 수요가 예상된다.
본 연구에서는 친환경 무기계 난연제의 종류 및 함량에 따른 EPDM 혼합물의 특성을 보기 위해 무기계 친환경 난연제 각 2종을 선정하여 사용하였으며 가교 특성, 기계적 특성, 열 노화 특성 및 난연특성 등을 측정하였다.
Experiment
EPDM은 Ethylene 함량이 58%이고 Mooney 점도(ML1+4 (125°C))가 25인 금호폴리켐의 KEP-2320을 사용하였다. 충전제로 입자크기가 46~60 nm인 카본블랙 Fast extruding furnace (FEF)를 사용하였다. 난연제는 구성성분에 따른 무기계 난연제 Alumina trihydrate (ATH)와 Magnesium hydroxide (MDH)를 사용하였다. 가교제는 과산화물계열인 Dicumyl peroxide (DCP)를 사용하였고 공가교제로 Methacrylate 계의 Trimethylol-propane trimethacrylate (TMPTA)를 사용하였다. 본 연구에 사용된 EPDM 및 각종 첨가제를 Table 1에 나타내었고, EPDM에 대한 난연제의 영향을 검토하기 위해서 Table 2와 같이 배합하였다.
ATH | MDH | |||||||||
---|---|---|---|---|---|---|---|---|---|---|
4 | 8 | 12 | 16 | 20 | 4 | 8 | 12 | 16 | 20 | |
ATH | 40 | 80 | 120 | 160 | 200 | |||||
MTH | 40 | 80 | 120 | 160 | 200 | |||||
EPDM | 100 | |||||||||
FEF | 20 | |||||||||
DCP | 7 | |||||||||
TMPTMA | 3 | |||||||||
TMQ | 2 | |||||||||
PEG | 1 | |||||||||
ZnO | 5 | |||||||||
St/A | 1 |
EPDM 복합체를 제조하기 위하여 국내의 엠텍사에서 제작된 밀폐식 혼합기(Kneader, 1.5 L)와 국내의 현진기계사에서 제작된 8-inch roll mill을 사용하였다. 혼련 조건은 Table 3에 나타내었으며, 1 stage는 Carbon black masterbatch (CMB)이고, 2 stage는 Final masterbatch (FMB)로 충분히 냉각된 CMB에 가교제를 첨가하여 혼련하였다.
가교 고무의 특성 평가는 가공 중의 품질관리를 목적으로 하는 소재의 가공성을 시험하는 방법으로 중합체의 최적 가교 시간은 가교 특성을 조사함으로써 알 수 있다. Moving die rheometer (MDR, MDR-2020 Myungji)를 이용하여 185°C에서 최대 토크(MH), 최저 토크(ML), 스코치 시간(ts2), 최적 가교 시간(tc90)을 측정하여 가교 특성을 조사하였다.
각 고무 배합물의 고무 시편 제조는 평판식 유압 프레스(50 ton, 신창정공)를 이용하여 185°C에서 6분간 압축성형 하여 두께 2 mm와 1.6 mm의 시트 형태로 제작하였다. 제작된 시험편은 KS M6518 (가교 고무 물리 시험방법)에 따라 경도 및 기계적 특성을 측정하였다. 고무의 경도는 스프링식 경도계(Shore A, GS-706N, Teclock)로 측정하였으며, 인장 시험기(UTM-2020, Myungji)를 사용하여 500 mm/min의 속도로 인장강도, 신율을 측정하였다.8
가교 고무의 열 노화 특성을 확인하기 위하여 Geer oven (ATC-2020, Myungji)을 사용하였다. 150°C에서 72시간, 168시간 열 노화를 시키고 실온에서 24시간 보관 후 경도, 인장강도, 신율을 측정하였다.
가교 고무의 영구압축줄음율을 확인하기 위하여 시험편을 Mold에 압축 성형하여 원두께의 25%를 압축시켰다. 그 후 상온에서 냉각 후 변형된 두께를 측정하고 시험 전 두께와 비교하여 영구압축줄음율을 측정한다. 각각의 시험편을 150°C에서 24, 168시간 유지 후 두께를 측정하고 영구압축줄음율을 측정하였다. 시험결과의 신뢰도를 위하여 3개씩 한 세트를 같은 조건에서 시험하였다. 시편의 초기 두께와 노화시킨 후 두께를 이용하여 다음의 식과 같이 영구압축줄음율을 계산하였다.
여기서 t0 는 시험편의 시험 전 두께(mm)이고 t1 은 시험 후의 두께(mm), t2 는 Spacer의 두께(mm)이다.
난연특성을 살펴보기 위하여 Underwriters laboratories (UL)의 Plastic 제품 난연성 시험 중 UL 94 V 시험방법 (Vertical burning test)을 적용하여 측정하였다. UL 94 V는 시편을 수직으로 세워놓고 버너로 시편에 불을 붙여 일정 시간 내에 저절로 시편에 붙은 불이 꺼져 주어야 한다. 여기서 시편의 불이 꺼지는 정도, 즉 난연의 정도에 따라서 V-0, V-1, V-2로 구분된다. 시편 크기는 길이 125 ± 5 mm, 폭 13.0 ± 0.5 mm, 두께 1.6 mm로 하여 메탄가스의 파란색 불꽃(불꽃 높이 20 mm, 시편의 아랫부분과 버너 끝 간 거리 10 mm)을 이용하여 10초 동안 총 2회의 점화를 하며 한 세트당 5개의 시편을 태운 후 소화 시간을 측정하여 등급을 결정하였다.
Results and Discussion
난연제의 종류 및 함량을 달리한 EPDM 배합물에 대하여 Rheometer를 통한 가교 특성을 Table 4에 나타내었다. 난연제의 종류에 따른 ts2은 유사한 수준이며, 함량이 증가함에 따라 ts2은 카본블랙 등의 충전제가 고무의 가교에 영향을 주기 때문에 미세하게 짧아지나, 저장 안정성에 영향을 미칠 정도의 차이는 아닌 것으로 확인되었다.12 tc90은 ATH의 함량이 증가할수록 감소하는 반면, MDH의 경우 함량이 증가할수록 증가하지만, 같은 가교 조건에서 가교 시간의 차이가 발생할 수준은 아닌 것으로 판단된다.
무기계 난연제 종류 및 함량에 따른 EPDM 배합물의 기계적 특성 및 노화 특성 거동을 관찰하였다. 내열 노화 전과 150°C에서 내열 노화 시간 72, 168시간 후의 경도 측정 결과를 Figure 1에 나타내었다. 대부분 고무 배합물은 산화하는 동안 가교제에 의한 가교 반응이 지배적으로 일어난다. 하지만 일부 산소가 고무와 반응하여 사슬 절단과 가교 반응을 일으킨다. 따라서, 이러한 노화 과정이 진행되면서 사슬 말단에 불포화 구조가 생성되기 때문에 강도와 신율이 저하된다.13
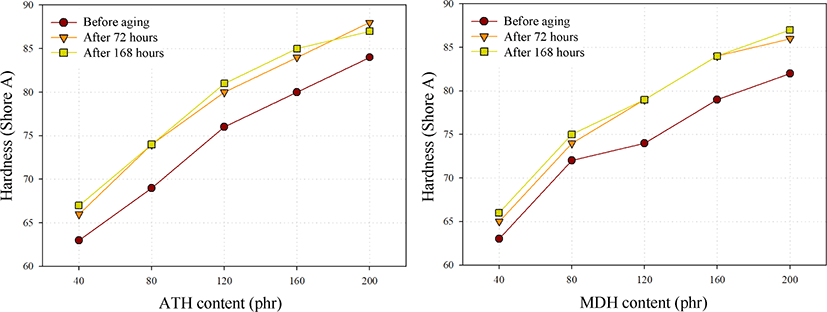
내열 노화 전의 경도는 초기 40 phr 첨가했을 때 유사한 수준이나, 난연제 함량이 증가할수록 EPDM 혼합물의 점도가 증가하여 경도가 상승하였다. 150°C에서 노화 시험 후의 경도 측정 결과의 경우 열에 의한 산화와 경화로 인해 경도가 소폭 상승하였으나, 이는 난연제 종류 및 함량 증가와는 관계없는 것으로 판단되며, 난연제 함량이 증가할수록 내열 특성이 저하된다고 볼 수 없다.
인장강도와 신율 측정 결과를 Figure 2, 3에 나타내었다. 내열 노화 전의 인장강도는 ATH를 첨가했을 때 가장 높으며, 함량이 증가하여도 인장강도의 변화는 적었다. 150°C에서 노화 시간 72, 168시간 후의 경우 노화 시간이 길어질수록 인장강도가 증가하였다. 반면, MDH는 함량이 증가할수록 인장강도가 감소하며 감소 폭 또한 큰 것을 확인하였다. 하지만 200 phr를 제외하고 노화 시간이 길어지더라도 인장강도의 변화는 적었다. 신율은 인장강도와 반대로 ATH를 첨가했을 때 가장 낮으며, 함량이 증가할수록 신율이 큰 폭으로 감소하고 내열 노화에 영향을 받지 않았다. MDH의 경우에는 인장강도와 달리 큰 변화가 없었으며, 노화가 진행될수록 신율이 감소하였다. 즉, ATH의 경우 노화가 진행됨에 따라 인장강도가 증가하나 신율의 변화는 없었으며, MDH의 경우 인장강도의 변화는 없으나 신율이 감소하였다.
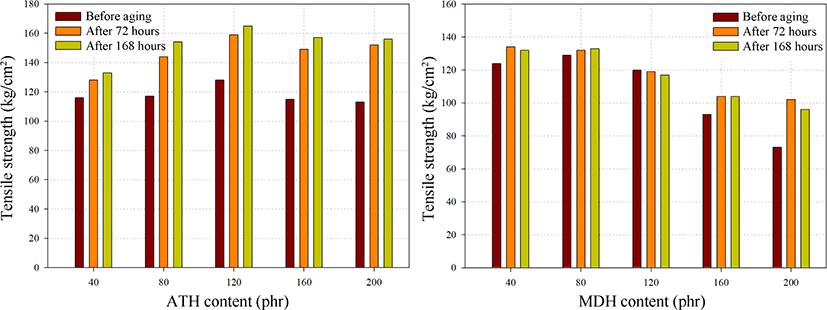
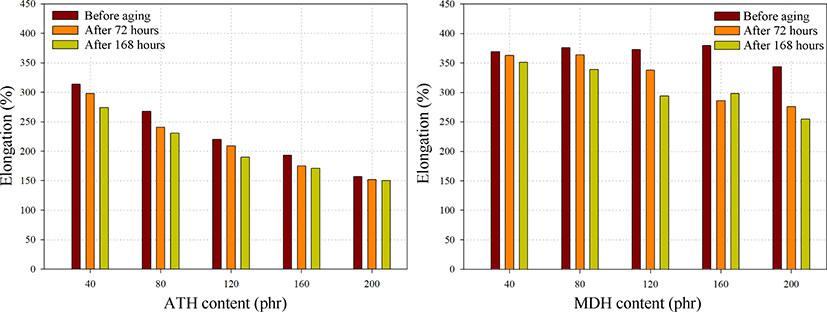
Figure 4에 무기계 난연제 종류 및 함량에 따른 고무 배합물의 영구압축줄음율 특성을 나타내었다. 영구압축줄음율이 우수한 고무는 탄성이 우수하여 외부로부터 가해진 응력이 제거되었을 때 복원하는 특성이 뛰어나다. 특히 밀봉성을 요구하는 오링, 가스켓, 오일 씰 및 각종 씰 등의 재료에 더욱 중요하다.14
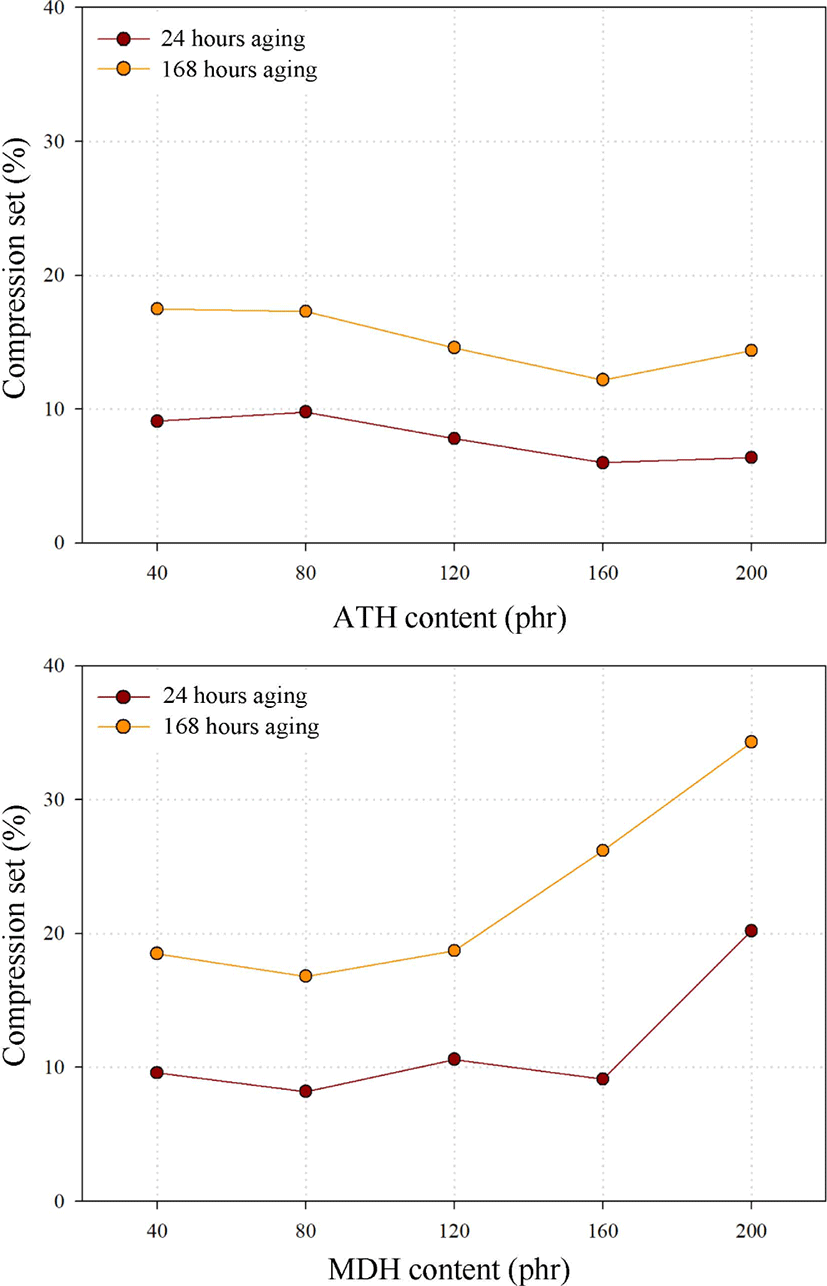
ATH의 경우 함량이 증가함에 따라 영구압축줄음율이 감소하는 경향을 보인 반면, MDH의 경우 영구압축줄음율이 증가하였다. 또한, 전반적인 특성이 ATH를 첨가했을 때가 우수함을 확인하였다. 영구압축줄음율의 경향은 난연제 함량의 증가로 EPDM 혼합물 중 상대적으로 고무의 함량이 감소함에 따라 혼합물의 탄성 감소로 영구압축줄음율이 증가하고 복원력이 저하되는 것으로 판단된다.3 결과적으로 ATH를 첨가한 경우가 영구압축줄음율이 가장 낮으며 난연제의 함량이 증가하더라도 영구압축줄음율이 증가하지 않고 소폭 감소하여 복원력이 유지되는 것으로 판단되며, 168시간의 장시간 열 노화 시험 후에도 영구압축줄음율이 18% 이하로 복원력이 가장 우수함을 확인하였다.
UL94 V의 시험 결과를 Table 5에 나타내었다. 난연제의 함량을 120 phr까지 증가시켜도 소화되지 않고 완전연소하여 난연성이 없었으며, MDH는 200 phr까지 증가시켜도 UL 94 V 등급에는 해당하지 않았다. 반면, ATH는 함량이 200 phr일 때 V-0급의 우수한 난연성을 나타냈으며, 연소 시 미세한 연기만 발생함을 확인할 수 있었다. 일반적으로 ATH, MDH와 같은 수화 난연제의 사용은 방염제뿐만 아니라 연기 억제제로도 작용할 수 있다.15
Contents (phr) | 40 | 80 | 120 | 160 | 200 | |
---|---|---|---|---|---|---|
ATH | 1st | Complete combustion | > 100s | 1s | ||
2st | > 250s | 10s | ||||
MDH | 1st | > 100s | 37s | |||
2st | > 250s | 220s |
Conclusion
본 연구에서는 EPDM에 무기계 난연제의 종류와 함량을 달리하여 배합물을 제조하였다. 무기계 난연제로는 ATH와 MDH를 사용하여 이들의 기계적 특성, 노화 특성, 영구압축줄음율 및 난연성을 살펴보았다. 물리적 특성시험결과로 ATH의 경우에는 함량이 증가하여도 인장강도가 감소하지 않고 유지되는 것을 확인하였다. 또한, 150°C에서 노화 시간 72, 168시간 후의 시험결과로 인장강도와 신율의 변화는 노화 전과 유사한 경향을 보였다. 그리고 난연제의 함량이 증가할수록 EPDM 원료 고무의 함량이 감소하여 복원력이 저하되는 것을 확인하였다. 하지만 ATH는 MDH 대비 영구압축줄음율이 낮으며, 함량 증가에 따른 영구압축줄음율의 변화도 작은 것을 확인하였다. 난연특성 또한 ATH가 MDH 보다 우수하였다. 결과적으로 친환경 무기계 난연제 중 ATH 난연제가 MDH 난연제보다 기계적 특성, 난연특성이 우수한 것을 알 수 있었다.