Introduction
상용화제는 이종의 고분자를 혼합시킬 때, 두 소재의 Flory-Huggins interaction parameter 의 값 차이를 최소화 함으로써 두 소재의 계면 접착력 (interfacial adhesion property) 을 증가 시켜서 상구조를 제어하고, 따라서, 적용된 소재에 신뢰성을 주는 일종의 첨가제 이다. 또한, 수지와 충전제와의 계면 결합의 효율을 높이기 위하여 두 소재의 계면 접착력을 증진 시키기 위하여 계면 접착제 (coupling agent) 를 충전제의 표면에 처리하여 PA 기지재와의 계면에 화학적 결합을 유도한다. 즉, 상용화제는 두 물질 (Polymer-Polymer, or Polymer-Filler) 의장 점은 보강하고 약점은 보완하며, 두 물질을 균일하게 분산시키는 역할을 한다.1
상용화제는 크게 비반응형 상용화제와 반응형 상용화제로 분류된다. 양기능성실란은 반응형 상용화제로 실리카의 표면과 고무사슬의 2중결합과 반응하여 화학적으로 결합을 한다.
Table 1은 실란의 종류, 가류형태 및 응용분야를 요약하였다.2
Experimental
양기능성실란(예, TESPT)이 가수분해 후에 치환된 알콕시기가 하이드록시기를 포함하는 충전제(예, 실리카, soft clay) 표면과의 축합반응이 진행되면서 수분이 부산물로 생성되는 것을 Figure 1에 표현하였다.5-7 현장에서는 소재 생산중에 발생되는 알코올 및 수분의 발생이 소재가 적절히 반응을 하고 있다는 간접 증거로 간주하고 있다.
Figure 2는 양기능성실란(예, TESPD or TESPT) 사슬 내의 황(sulfur)이 황 사슬간 결합이 분리된 후 말단의 황 관능기가 고무사슬의 2중결합(예, NR)과 공유결합을 형성 하는 것을 표현하였다.8 여기에서, 황은 반응활성제인 아연의 도움으로 더욱 활성화되어서 반응을 하게 된다.9
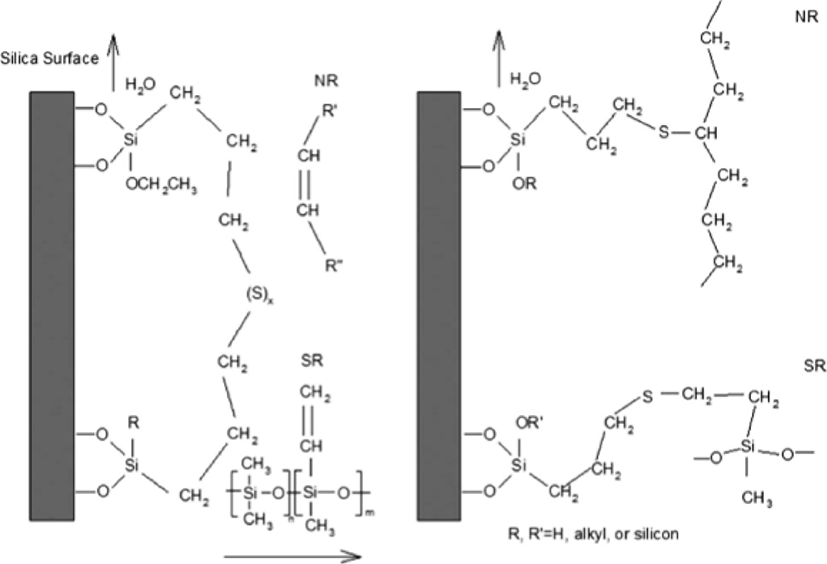
즉, 실란이 첨가되지 않은 경우 실리카-고무사슬간 상호작 용의 크기(αFP)는 카본블랙-고무사슬에 비해 낮다. 하지만 실란을 첨가하면 실리카 표면과 고무사슬 사이에 실란을 매개 체로 공유결합이 생성되고 결합력이 높게되어 상호작용의 크기(αFP)는 카본블랙-고무사슬보다 크게 나타난다. 이는 interaction parameter section에서 설명하도록 하겠다.
Figure 3은 실리카(silica)와 결합한 다양한 형태의 실란 (silane)들이, [예, triethoxysilyilpropane(TESP), bis(triethoxy-silyilpropyl) disulfide(TESPD), bis(triethoxysilyilpropyl)tetrasulfide( TESPT)], 가류(vulcanization) 후 실리카와 천연고무 (NR)간의 결합의 형태를 도식적으로 나타내었다.4 가류후에 사용된 실란의 종류에 따라 실리카와 NR과 각기 다른 3D 구조를 이룬다. TESP는 분자 내에 고무의 2중결합과 반응을 할 원소가 없으므로 Figure 3(a)와 같은 형태로 고무사슬 사이에 끼어있는 상태로 존재한다. TESPD는 황 원소가 NR사슬내의 2중결합을 공격하여 Figure 3(b)와 같은 3D 구조를 이룬다. TESPT역시 TESPD와 같은 mechanism으로 NR과 Figure 3(c) 와 같은 3D 구조를 이룬다. TESPT는 TESPD와 비교시 분자당 평균 2개의 황을 더 가지고 있기 때문에 가류 후 TESPD 를 적용한 소재보다 더욱 높은 cross-link 구조를 갖는다.
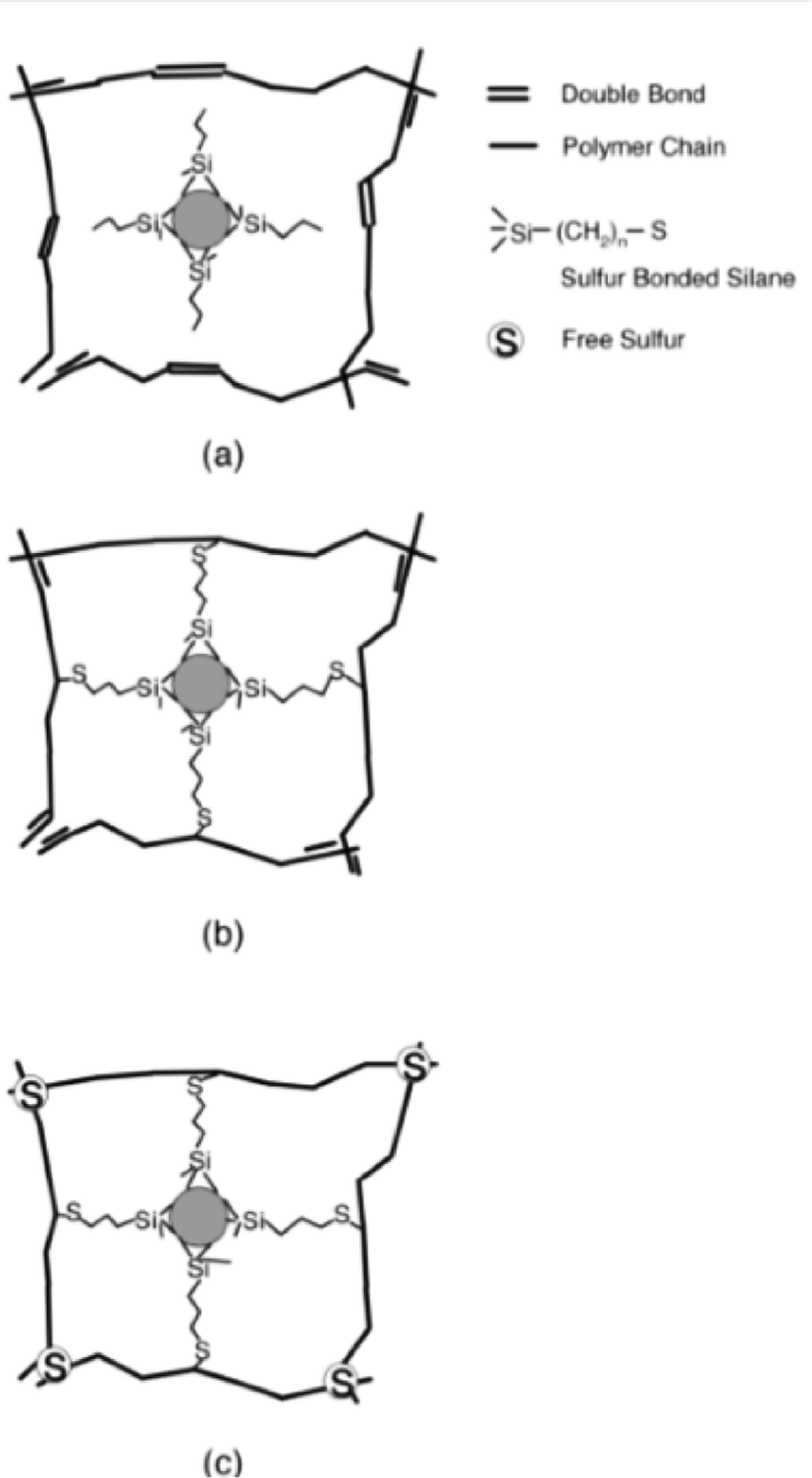
TESPT가 처린된 silica/NR 복합소재(S4)와 TESPD 가 처린된 silica/NR 복합소재(S2)의 물성을 비교하면 S4가 S2에 비하여 높은 인장모듈러스(tensile modulus), 낮은 최대인장강도 (maximum tensile stress), 낮은 인열저항강도(tear resistance) 를 갖는다. 가류전이나 후에 상온이나 100°C에서 S4는 낮은 E'' (loss modulus)로 인하여 낮은 tanδ(tan delta) (=E''/E')값을 보인다, 또한 두 소재는 온도가 올라가면서 tanδ값이 낮아지는 것을 관찰할 수 있다. 가류된 두 소재를 blow out(BO) test 를 진행했을 시 S4소재가 S2에 비해 변형으로부터의 회복이 낮음을 보였다. HBU (heat build-up) 시험에서는 S4소재가 S2 에 비해 열발생이 낮음을 보였다. Abrasion loss시험에서 S4 소재가 S2에 비해 loss양이 많음을 보였는데 이는 S4가 S2 보 다 3-D network structure가 더욱 발달되어 있다는 것을 의미 한다. 하지만 3차원구조는 임계점 이상의 변형(over critical strain)이 일어날 경우 S4 구조가 S2 구조에 비해 먼저 분해될 수 있다.
실리카-실란결합 복합소재의 제조 시 활성화제 zinc soap (ZB)을 사용하면 복합소재의 물성이 향상된다.
실란이 처리된 실리카 복합소재에 있어서 활성화제 처리를 한 소재는 특히 blow out (BO) 물성의 증가에 많은 차이를 보 여준다.10
Figure 4는 BO 시험 후 시편의 사진을 보여준다. 시험 전 (0번시편)에 비해 BO시험 후 실리카-실란만 첨가한 NR 시편 (1(S4) & 2(S2))의 변형은 활성화제(Zinc Soap(Z))를 첨가한 시편(3&4 (S4), 5&6(S2))보다 현저한 변형을 보여준다.
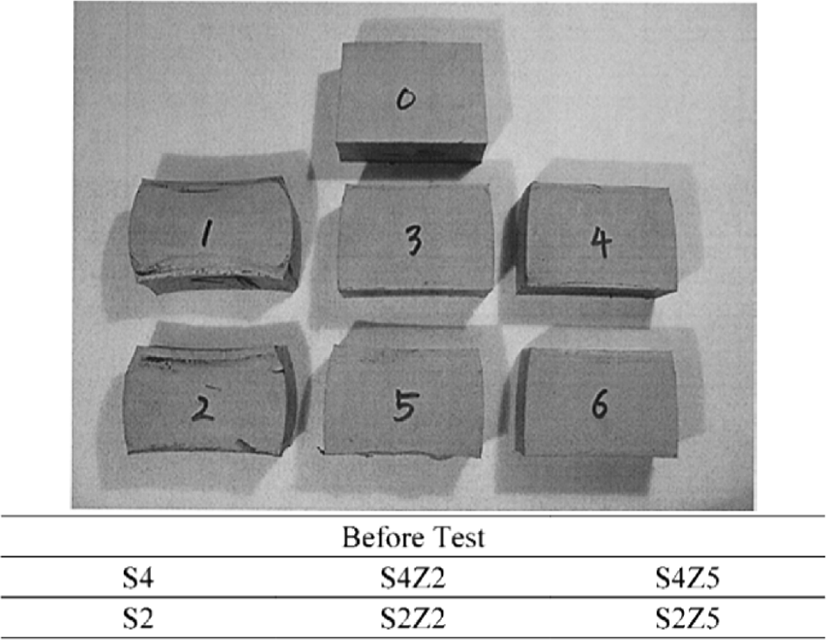
Figure 5는 위(Figure 4)의 사진을 변형율(deformation ratio(%))로 환산하여 표시한 것이다. 시험 전 (0번시편)에 비해 BO시험 후 실리카만-실란 첨가한 NR 시편 (1 & 2)은 약 6-8%의 변형을 하였지만 zinc soap를 첨가한 시편(3&4 (S4Z2 and S4Z5)), 5&6(S2Z2 and S2Z5))은 그림에서 보듯이 약 1-3%의 변형을 보여준다.
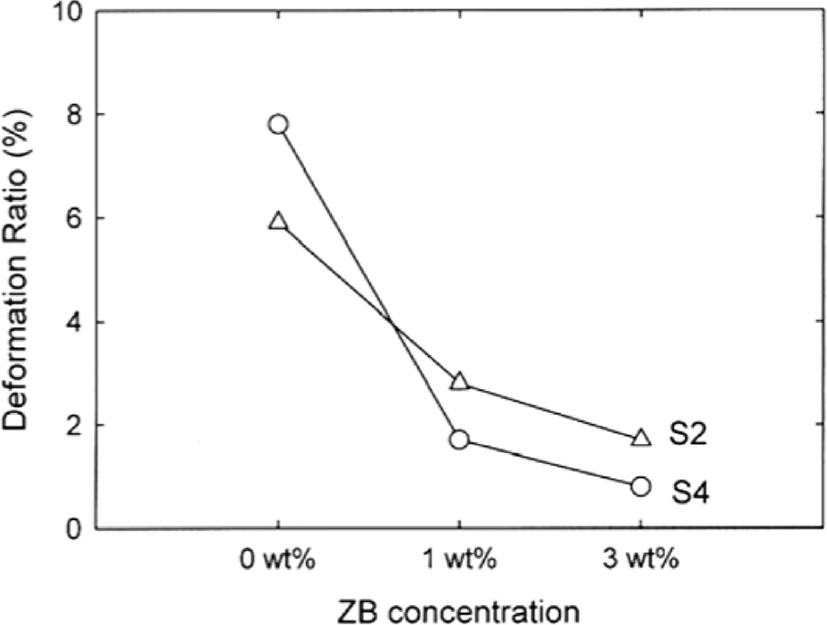
이는 실란이 첨가된 실리카 복합소재가 위에서 예시한 것과 같은 3-D network structure를 형성하여 변화률의 감소에 기여를 했다는 것을 의미한다.4 직접적인 3-D network structure가 형성된 것을 확인한 사진을 Figure 6에 보여주었다.11
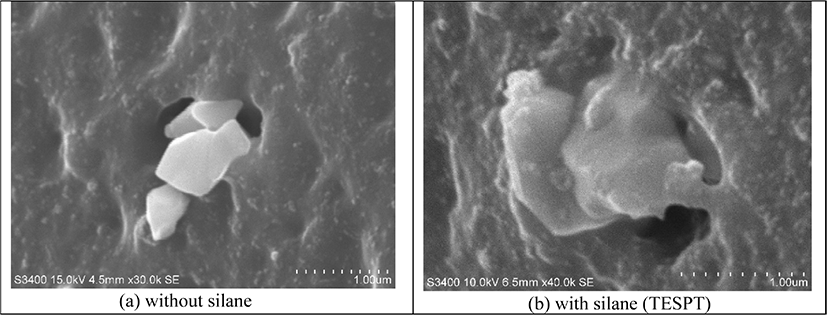
Figure 7는 활성화제 ZB가 첨가되었을때 BO시간이 현저 히 증가하였으며 ZB의 농도가 증가 할수록 BO시간이 증가 하였으며, 5 wt% 첨가 시 첨가하지 않았을 때와 비교하면 BO 시간이 약 9,000-10,000배가 증가하는 것을 보여준다.
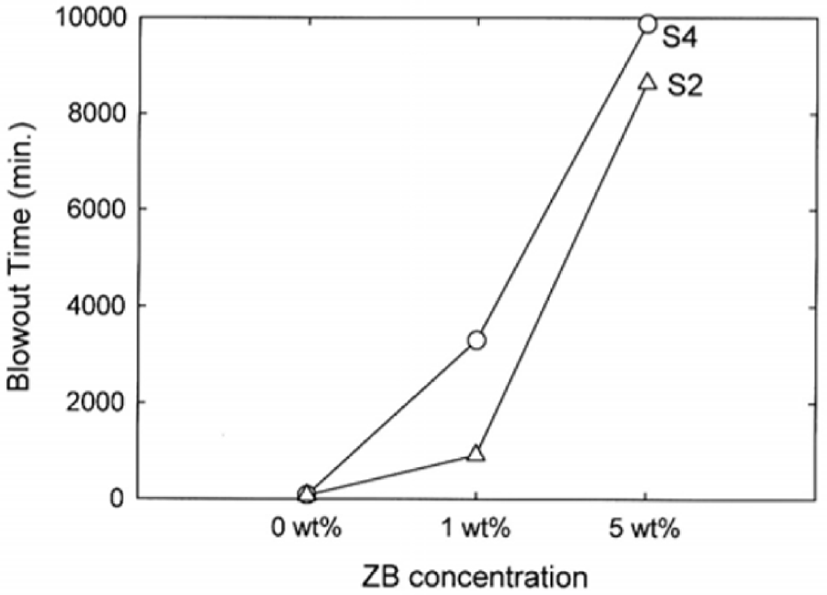
여기서 복합소재 내의 interaction parameter는 αC로 나타내 는데 αC = αF + αP + αFP로 표현된다. αF는 소재 내 filler-filler 파라미터, αP는 소재 내 polymer-polymer 파라미터, 그 리고 αFP는 소재 내 filler-polymer 파라미터를 나타낸다.11
Figure 8은 각기 다른 실리카(10, 20, 30, 40 phr)가 실란의 농도의 변화에 따른 αF (filler-filler interaction parameter) 값 의 변화를 나타낸다. 실란농도가 증가 함에 따라 αF 값이 증 가한다. 이는 TESPT내의 황이 황 기증(sulfur donor)하는 역 할을 하기 때문이다.4,6,12Figure 6(a)는 αFP의 filler-polymer interaction이 없는 상태를 의미한다. Figure 6(b)는 실란의 결합정도에 비례해서 αFP의 값이 비례하고, 또한 황의 양에 비례해서 αP의 값이 비례한다(Figure 3).
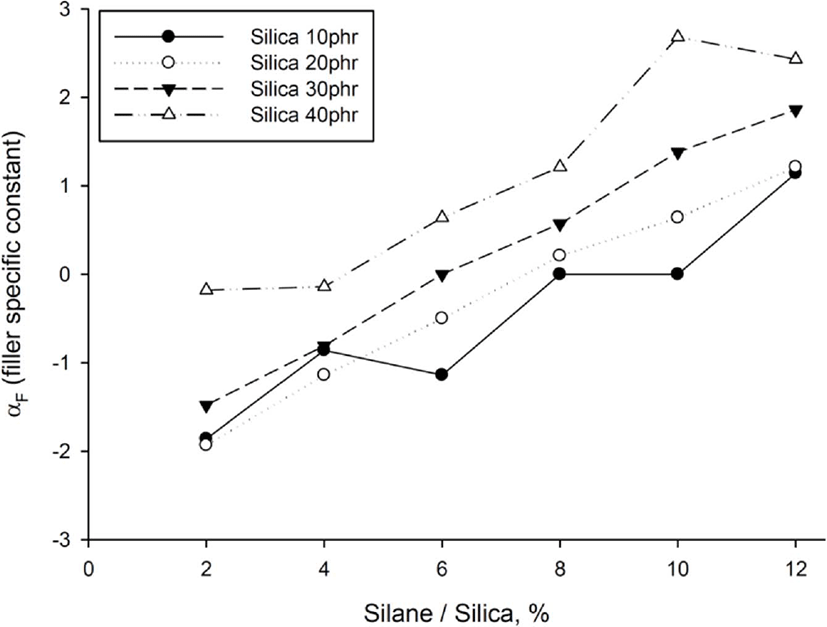
Amide 구조를 포함하는 대표적인 PA의 종류는 PA6, PA66, PA610, PA46, PA11, PA12 등이 있으며 각각의 특성들을 Table 2에 요약하였다.2
MEG (monoethylene glycol)는 말단기에 hydroxy기 (-OH) 분자구조를 가지고 있기 때문에 가수분해 반응을 진행 할 수 있는 물질이다.
Lee & Kim은 MEG가 폴리아미드66/유리섬유(30%) 복합소 재[DTR사 DTRamid (WG30DTRR, 이하 D). Zytel 70G30 HSLR (DuPont 사, 이하 Z), KDG 1030 (KOPLA사, 이하 K), A3WG6 HRX (BASF사, 이하 A)] 가수분해에 미치는 영향을 관찰하였다.15 각 사의 시편을 MEG에 함침하여 시간을 변수로 기계적 물성변화를 측정하였다. 인장과 굴곡특성은 MEG 에 노출 후 감소하는 것을 공통적으로 관찰하였다. 이는 PA/GF소재가 MEG를 흡수하였을 시, 수분이 소재 내에서 분자 사슬간의 결합력을 감소시켜 기계적 물성을 감소시킴과 동시 에 다종의 폴리아미드66/유리섬유 복합소재들의 가수분해를 확인하였다. Py-GC/MS 분석 결과, 침지된 소재에서 노출시 간이 증가할수록 가수분해 산물인 carboxylic acid와 alkylamine의 물질이 공통적으로 증가하는 것을 관찰하였다.
Polyketone (POK)과 Polyamide (PA)는 수분(-OH)과의 흡착 정도가 다르다 이는 분자 주쇄내에 존재하는 극성 원소와의 상호반응에 따라 달라지기 때문이며 복합소재의 물성에 영향 을 미친다.
Figure 9는 hydroxy기를 포함하는 monoethylene glycol (MEG)가 polyketone (POK)과 폴리아미드66(PA66)에 결합하 는 구조를 나타낸다.17 주사슬의 배열구조가 C-C 결합인 POK 는 C-N 결합의 PA66에 비해 쌍극자 상호반응에 의한 hydroxy 기 흡착에 무관하며, 따라서 가수분해 반응성이 C-N 결합보다 상대적으로 작다.17
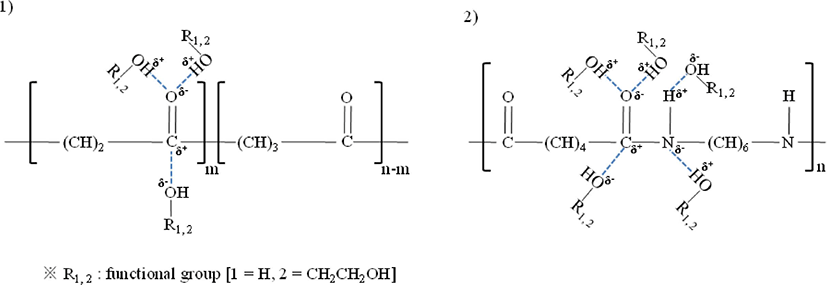
Figure 9(a)는 POK의 구조를 보여준다. 주쇄에 있는 케톤기 (-C(=O)-) 간의 강한 결합력은 녹는점 향상 등 폴리케톤의 물 성향상에 기여한다. POK는 수분에 대한 저항성, 기계적 강도, 내화학성, 내마모성, 가스차단성 등의 특성이 우수하고, 기계, 전기/전자부품, 섬유 복합재료 등의 분야에서 수요가 기대되고 있는 소재이다.16,18-23
Figure 9(b)는 물분자와 PA66와의 상호관계를 보여준다. PA66/GF소재 내에서 하이드록시기(-OH)를 함유하고 있는 극성용액은 복합소재의 분자사슬 내 극성원소(예, O, N…)들과 반응하여 수소결합을 생성하고, 분자사슬과 보강제인 유리섬 유간 쌍극자 상호작용(dipole-dipole interaction)을 약화시키며, 추가적으로 용액을 투입 시 가소화 작용을 하여 분자사슬 간 미끄러짐을 발생시키는 것으로 알려져 있다.17 이와 같은 현상은 극성용액이 분자사슬의 부피와 이동성을 증가시켜, 결국 분자사슬간 얽힘(entanglement)과 결합(bonding)을 감소시 키기 때문이다.24,25 복합소재 내 액체의 유입 및 증가는 복합 소재의 에너지 흡수와 연성(ductility)을 증가시키는 반면에, 강도(strength), 강성(stiffness) 등을 감소시킨다.26 용액 처리는 복합소재에서 인장강도(tensile strength) 및 탄성률(modulus) 을 감소시키는데 이는 용액이 분자사슬-섬유 계면간 응력전 달능력(stress transfer capability)을 저하시키기 때문이다.27
고분자의 흡습은 amide-amide 수소 결합이 amide-water 수소 결합으로 치환됨으로써 이루어지고 전체 amide group의 농 도에 많은 영향을 받는다. 흡습된 PA 복합소재는 제반 물성이 흡습의 정도에 따라 많은 차이를 나타낸다.28 사슬 내에 amide의 수가 증가할수록 수분과의 상호작용 표면이 증가하므로 수분의 흡수는 증가한다. PA의 amide(%) 양에 따른 수분 흡수에 대한 정도를 Table 3에 요약하였다.
Polyamide | H2O Absorption, 24 hr (ASTM D570, %) | % Amide |
---|---|---|
Polyamide 6 | 1.3~1.9 | 38 |
Polyamide 66 | 1.0~1.3 | 38 |
Polyamide 69 | 0.5 | 32 |
Polyamide 612 | 0.4 | 28 |
Polyamide 12 | 0.25~0.3 | 22 |
PA의 특성 중의 하나는 흡습성이다. 이는 소재의 기계적 물성을 감소시키는29 반면 연성을 증가시킨다. 이에 대한 실험 결과를 Figure 10에 나타내었다. 이는 PA의 주사슬 내에 친수성이 강한 amide group이 수분을 흡수하여 물 분자간의 미끄 러짐을 용이하게 하여 물 분자가 PA 복합소재 내에서 가소제 (plasticizer)로서의 역할을 하기 때문이다.28
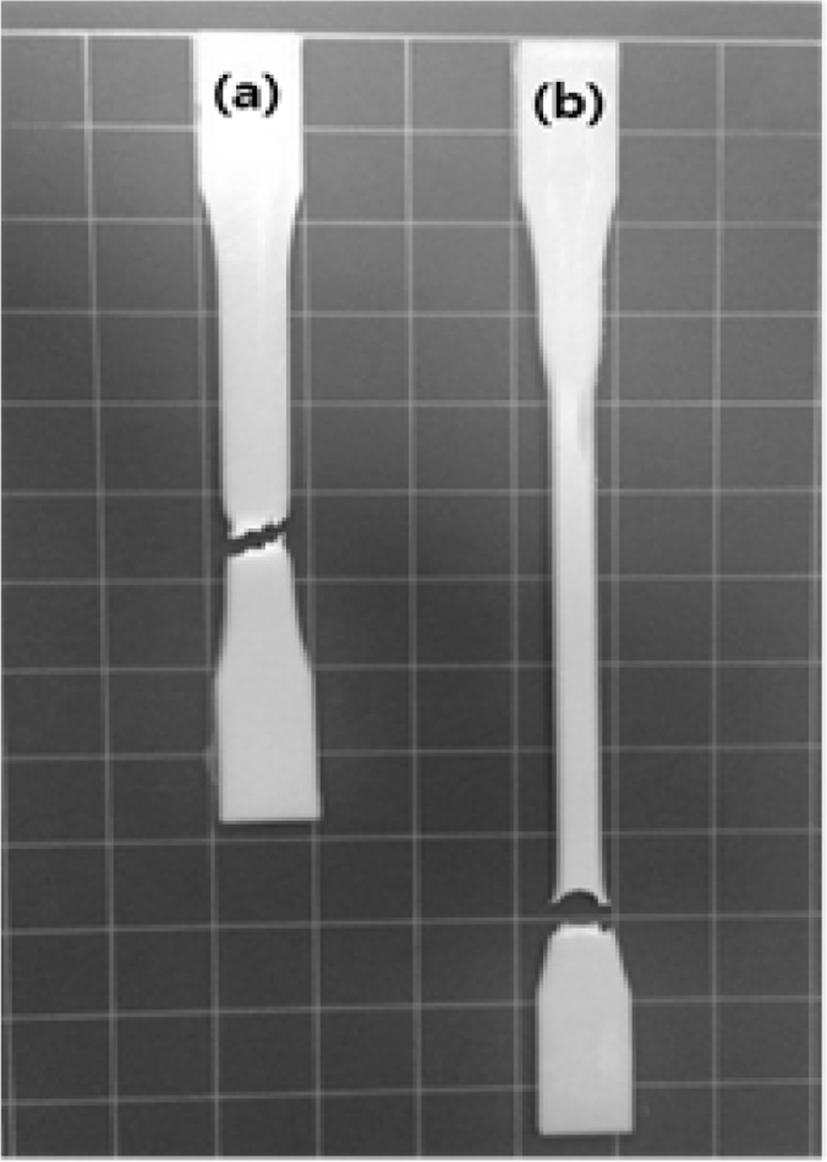
Figures 11-13은 POK와 PA66 모두 침지 후 시간이 지남에 따라 인강강도 및 탄성율은 감소하고 신장률은 증가하는 경향을 각각 보여준다.16 PA66는 POK에 비해 강도 및 탄성률 은 더 감소하고 신장률은 증가하였는데, 이는 PA66가 극성용 액과 반응성이 우수하여 물리적 거동에 더 큰 영향을 받은것 을 나타내며, 또한 수분은 복합소재 내에서 가소제로서의 거동을 보인다.28
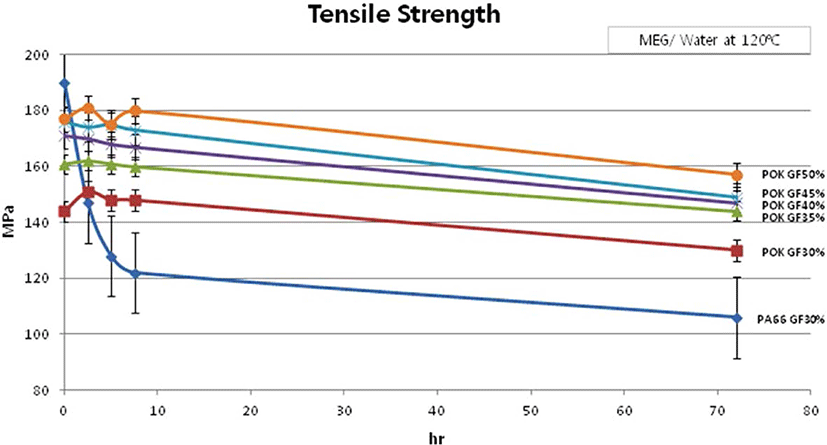
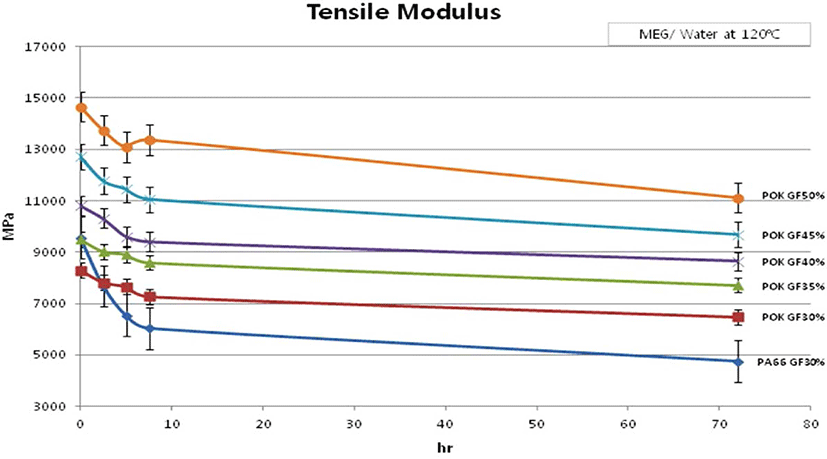
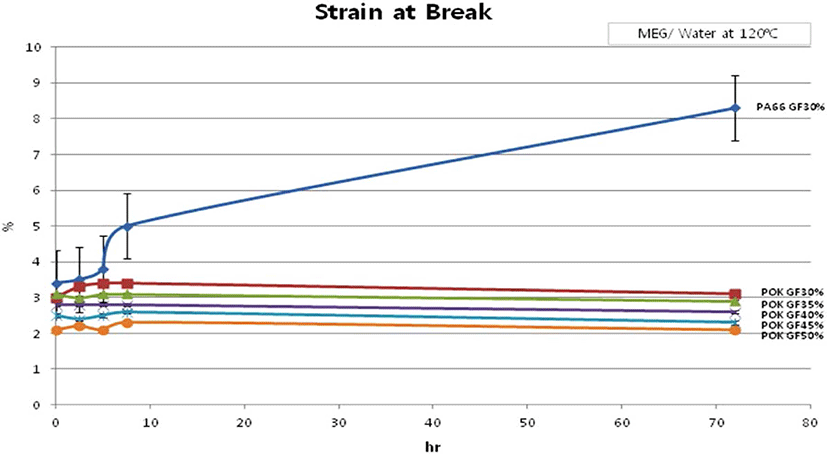
Figure 14은 PA66의 가수분해 메커니즘을 나타낸다. PA66 의 극성관능기인 아미드기에 물분자가 수착되고 아미드기의 C-N 결합이 분해된다. 그 결과 카르복실산과 일차아민이 생성되면서 PA66의 분자사슬이 분해된다.29,30 따라서 가수분해 가 진행됨에 따라 복합소재의 인장강도 및 탄성률은 감소하 고 충격강도, 신장율은 증가하게 된다. 가수분해된 PA66의 열분해 생성물에 대한 정량평가를 통해 가수분해의 정도를 측 정할 수 있다.14,31
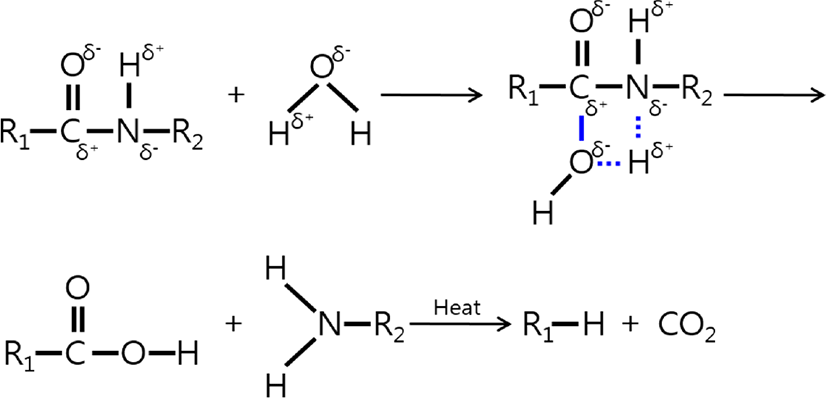
저자의 연구결과도 POK와 PA66모두 침지 후 시간이 지남 에 따라 인강강도 및 탄성률은 감소하고 신장률은 증가하는 경향을 보였다.16 또한 PA66는 POK에 비해 강도 및 탄성률은 더 감소하고 신장률의 증가를 보여준다. 이는 PA66가 극성용액과 반응성이 우수하여 물리적 거동에 더 큰 영향을 받기 때문이다. 또한 액체가 복합소재 내에서 가소제의 거동을 보인 것으로 판단된다. 또한 Figure 9에서 보듯이 주사슬의 배 열구조가 C-C 결합인 POK는 C-N 결합의 PA66에 비해 쌍극 자 상호반응에 의한 히드록시기 흡착에 거의 영향을 받지 않는다. 따라서 가수분해 반응성이 C-N 결합보다 상대적으로 작을 것으로 판단된다.
PA66 복합소재의 침지 전 및 침지 후 기계적 물성 변화16
동급 PA66/GF 복합소재들 4종[DTR(D), DuPont(Z), Kopla (K), BASF(A)]을 부동액(MEG)조건(130℃) 침지 후, 각 소재들의 열분해 생성물을 py-GC/MS을 정량적으로 확인한 결과 기계적 물성은 가수분해의 정도가 증가 할수록 감소하였 다.14,15
Figure 15은 1,008시간 침지 후 각 4사의 PA66/GF 복합소 재들의 인장강도를 측정한 결과 평균적으로 약 43~45% 정도 감소하는 것을 보여준다. 인장 모듈러스는 평균적으로 약 49~55% 정도 감소, 인장 신율은 평균적으로 약 3.5~5.4% 정 도 증가를 하는 것을 보여준다. 이는 앞에서 가수분해에 따른 Py-GCMS 분석 결과에서 보여주었듯이 각 복합소재가 MEG 및 수분의 hydroxy기의 PA66의 사슬과의 반응하여 가수분해가 진행되어 저분자 구조로 분해되었음을 확인하는 것이다. 내가수분해성이 우수할수록 침지 후 기계적 물성을 유지한 것을 확인하였다.
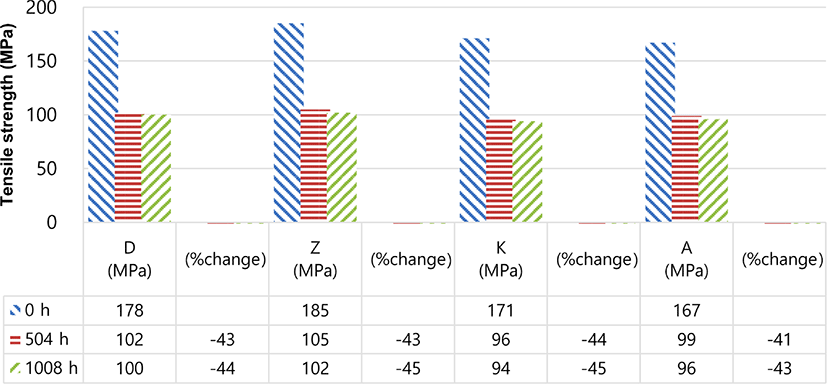
각 내가수분해성 PA66 복합소재들의 기계적 물성의 변화 를 Table 4에 나타내었다.14
Conclusion
고무복합소재내 가수분해 이후 수반되는 축합반응, PA의 가수분해 기전들을 소개하였다.
고무복합소재의 물성에 영향을 미치는 요소들은 제조 시 실란의 종류, 실란의 양, 실리카의 양, 수분의 양, 개시제 및 활 성화제의 농도에 따라서 물성변화가 있음을 확인하였다.
고무복합소재 내에서 알콕시(alkoxy)기가 포함되어 있는 양 기능성 실란(TESPD & TESPT)이 가수분해 후 실리카표면과 진행되는 축합 반응을 고찰하고 고무복합소재의 물성증가에 영향을 미치는 요소들인 실란내 황의 농도, 아연복합물 활성 화제(activator)가 물성증대에 미치는 영향 등을 고찰하였다. 또한 고무복합소재 내에서 소재간의 상호작용변수(interaction parameter) αC (alpha C)에 대하여 고찰하였다.
PA66복합소재는 수분에 의해 가수분해가 발생하며 복합소재의 물성저하 영향을 미치고 이의 원인에 대한 기전을 고찰 하였다. PA사슬 내에 존재하는 친수성인 amide의 영향으로 amide의 수가 증가할수록 수분의 흡수는 증가하며 물성의 감소를 보인다. 반면 비친수성소재인 POK는 수부의 영향을 그리 받지 않는다. 산업현장에서는 수분에 노출되는 부품의 수지 선정 시 고려해야 할 요소이다.