Introduction
자동차는 사회에서 이슈되는 정책 및 환경에 따라 대배기량에 따른 성능향상을 중점으로 둔 제품에서부터 점차 저배기량 고연비 차량으로 개발 및 양산체제를 갖추게 되었고 최근에는 배출가스 규제 및 연비향상의 목적으로 경량화나 전장품의 전동화제품으로 이어지고 있다. 이렇듯 자동차산업은 급격한 변동기를 거치고 있기 때문에 자동차부품 업체들도 사회 흐름에 맞춘 부품들을 끊임없이 개발하고 있으며 이러한 사이클에 맞춰 조향 장치도 함께 발전하고 있다.1
조향 장치는 자동차 핸들에서부터 바퀴까지 연결되는 모든 부품을 일컫는 말인데 이때 핸들의 움직임에 따라 각속도의 변화 없이 자동차 바퀴에 원활한 동력을 전달하고 동시에 완충역할을 위해 움직임을 조절하는 부품을 등속조인트라 한다. 등속조인트는 등속으로 동력을 전달하기 때문에 구성 부품 간의 마찰이 끊임없이 발생하게 되며 이로 인해 부품 주변의 온도가 상승하게 된다. 이러한 온도 상승을 방지하기 위해 등속조인트에 부츠를 장착 시키고 부츠 내부에 윤활유를 주입하여 온도를 조절한다. 이러한 등속조인트 부츠는 윤활성을 유지시킴과 동시에 외부적으로는 먼지나 모래, 물 등의 이물질로부터 등속조인트를 보호하는 역할도 함께 담당한다.2-5
부츠는 일반적으로 자동차의 수명이 다하기전까지 사용하게 되므로 특히 변형이나 마모에 견딜 수 있는 피로 내구 특성을 가져야 하고 지면으로부터 날라오는 각종 이물질들 과의 충격에 견딜 수 있는 내충격 성능을 가져야 한다. 또한 자동차 방향의 회전에 따라 굽힘, 압축, 인장 등의 반복적인 힘들이 등속조인트 부츠에 가해지고 부츠 간의 자체접촉 또한 발생하게 된다.5-7 과거에는 이러한 기능을 유지하기 위해 클로로프렌 고무(polychloroprene rubber)로 이루어진 등속조인트 부츠를 사용하였으며 내열, 내한성이 요구되는 경우에는 실리콘 고무가 이용되어왔다. 하지만 최근에는 클로로프렌 고무재질과 실리콘 고무재질에 비해 피로 내구 신뢰성이 우수하여 10년/10마일 이상의 내구성 보장이 가능한 열가소성 폴리에스테르 고무(thermoplastic polyester elastomer, TPEE) 소재가 대두되고 있다. TPEE 소재는 강도와 내구성 성형성이 우수하기 때문에 부츠의 두꺼운 부피로 인한 문제점 해결이 가능하고 제품의 두께를 얇게 하는 동시에 부피를 작게 한 설계를 가능하게 할 수 있다. 이러한 추세로 현재는 TPEE 소재가 등속조인트 부츠용의 최대비중을 차지하고 있다.8-10
등속조인트 부츠의 초기연구는 설계자의 경험에만 의존하여 설계하고 실험을 통해 변형에 대한 취약 부위를 찾아내어 다시 설계에 반영하는 등의 방식으로 이루어졌으므로 시간과 경비면에서 비효율적이다. 하지만 컴퓨터의 발달로 유한요소법을 사용하여 고무와 같은 비선형의 탄성 거동을 보이는 재료에 대해 제품의 변형거동을 시뮬레이션으로 살펴볼 수 있게 되었다.8 클로로프렌 고무 소재를 등속조인트 부츠에 적용한 유한요소해석 연구는 S.H. Kim, 외 2명이 진행하였다.11 또한 Shashikanth. C와 K. Mahesh Dutt.는 ANSYS 프로그램을 사용하여 비선형 고무부츠의 변형양상을 확인하였다.12 해석과 실험을 비교하여 부츠의 해석을 검증한 연구는 Nelson Woo 외 2명이 하였다.13 Jeong은 고무부츠의 형상에 따른 해석연구를 하였다.14 Kim은 해석결과를 통해 취약부위를 예측하였고 실험과 해석을 비교하였다.15 Park은 해석을 통해 조향장치의 설계변수에 따른 결과를 확인하였다.16
본 연구는 상용 구조해석 프로그램(Abaqus)을 이용하여 등속조인트와 TPEE 소재의 부츠가 결합된 세 가지 형상에서 등속조인트의 이동과 회전에 따라 부츠의 변형 양상을 확인하였다. 각도가 변함에 따라 부츠의 자체접촉 및 부츠와 등속조인트의 접촉양상을 관찰하고 반복적인 접촉에 의해 변형에 취약한 부분을 확인하고자 한다. 이러한 연구는 부츠 생산을 위한 비용과 시간을 절감할 수 있으며 향후 부츠 디자인을 위한 연구자료로 사용될 수 있을 것이라 판단된다. 또한 등속조인트 부츠변형에 취약한 부분을 판단하는 결과 분석 방법을 제시하였다.
Computer Simulation
Figure 1에 부츠와 등속조인트가 조립된 형상이 나타나 있는데 본 연구에서는 세 가지 모델을 사용하였다. 세 가지 모델에서 부츠의 길이는 모두 상이하며 등속조인트의 형상은 모델 1과 모델 2가 동일하다. 모델 1의 부츠는 여섯 개의 외측 굴곡과 다섯 개의 내측 굴곡으로 이루어져 있으며 총 길이는 127mm이다. 모델 2의 부츠는 여섯 개의 외측 굴곡과 다섯 개의 내측 굴곡으로 이루어져 있고 총 길이는 124.1mm이다. 모델 3의 부츠는 다섯 개의 외측굴곡과 네 개의 내측 굴곡으로 이루어져 있으며 총 길이 128mm로, 모델 1과 2에 비해 더 넓은 간격의 외측굴곡과 내측굴곡의 형태를 가지고 있다. 모델 1과 2의 등속조인트는 지름이 30.3mm에서 31.5mm로 크기가 변한 가변 원통형상이다. 모델 3의 등속조인트는 원통의 지름이 24.6mm에서 38mm로 크기가 변하는 가변 원통형상이다.
부츠와 등속조인트의 재료 물성은 Table 1에 나타나 있다. TPEE 소재는 금속과는 달리 대변형에서 탄성을 유지하는 초탄성 특성을 가지고 있다. 초탄성 특성을 나타내는 재료의 컴퓨터 모사를 위해서는 변형률 에너지 포텐셜 모델을 사용한다. 변형률 에너지 포텐셜은 변형률 불변 계수의 함수로 식 (1)과 같이 표현된다.
Part | Material | Young’s Modulus (MPa) | Density (kg/m3) | Poisson’s ratio |
---|---|---|---|---|
Boots | TPEE | Table 2 (Ogden 3rd model) | 1146.5 | 0.38 |
CV-Joint | Steel | 2E+5 | 7850 | 0.3 |
여기서 변형률 불변 계수를 주 신장률 λ로 식 (2)-(4)와 같이 표현된다.
대부분의 TPEE 소재는 비압축성으로 J=1이다. 비압축성 TPEE 소재의 변형 해석에서 널리 쓰이는 변형률 에너지 포텐셜에는 Mooney-Rivlin 모델과 Ogden 모델이 있다. 본 연구의 등속조인트 부츠의 변형해석을 위해서 N = 3인 Ogden 모델을 적용하였고 관련 수식은 식 (5)에 표현하였다.
Ogden 모델은 주 신장률을 매개변수로 하며 두 종류의 상수를 도입하여 다항식으로 표현된다. 이 식에서 λ는 주신장률이며 μ, α는 재료 상수이다. 이러한 재료 상수 값은 Abaqus 프로그램에서 N = 3인 Ogden 모델에 진응력-변형률 곡선 데이터의 결과를 입력하면 자동적으로 적용된다. 진응력-변형률 곡선 데이터를 Table 2에 표현하였다.8,17,18
본 연구에서는 Abaqus를 사용하여 explicit 해석을 수행하였다. 실제와 유사한 결과를 얻기 위해 full 3D 모델을 사용하였다. Figure 2는 컴퓨터 모사를 위한 경계조건 중 contact조건을 보여주고 있다. 부츠 외측과 부츠 내측은 각각 self contact 조건을 주었고 이때 contact 에는 frictionless 조건을 적용하였다. 부츠 내측과 등속조인트 외측에는 contact 조건을 주었다. 부츠 끝단에는 fixed 조건을 주었고 부츠 내측과 등속조인트의 외측이 결합되는 부위는 tie 조건을 적용하였다. Figure 3은 경뎨조건 중 loading조건을 보여주고 있다. Loading 조건으로는 부츠 끝단에 이동과 회전 조건을 적용하였는데 각 모델에 따른 이동과 회전의 정도값은 Table 3에 나타내었다. Figure 4는 메시 형상이다. 해석을 위해 등속조인트와 부츠에 적용한 요소는 선택적 저감적분법을 이용하는 8절점 3차원 brick요소(C3D8H) hexa 형태를 적용하였다. 모델 1의 부츠와 등속조인트의 요소수는 총 126,223개, 모델 2는 총 101,385개, 모델 3은 총 114,602개이며 세 모델 모두 굽힘에 의한 영향을 고려하기 위해서 두께 방향으로는 3개의 요소를 생성하였다.
Loading condition | Model 1 | Model 2 | Model 3 | |||
---|---|---|---|---|---|---|
Step1 | Step2 | Step1 | Step2 | Step1 | Step2 | |
Translation (mm) | −21 | −21 | 20.1 | 20.1 | 30.5 | 30.5 |
Rotation (°) | 0 | 46 | 0 | 50 | 0 | 40 |
Results and Discussion
세 가지 모델의 초기 형상과 등속조인트가 이동하였을 때의 형상, 그리고 등속조인트가 회전을 하였을 때의 형상은 Figure 5에 나타나 있다. CV-joint의 x축 방향의 이동량 및 z축을 기준으로 한 회전각도가 Table 3에 나타나 있다. 세 모델 모두 등속조인트가 -x 방향으로 이동했을 땐 부츠가 압축된 모습을 보이고 있지만 부츠 서로간의 자체 접촉은 발생하지 않았다. 등속조인트가 z축 기준으로 시계방향으로 회전하였을 때는 회전된 방향의 부츠들이 서로 접촉하는 자체접촉의 모습을 보이고 있으며 반대 방향의 부츠들은 인장된 모습을 보인다.
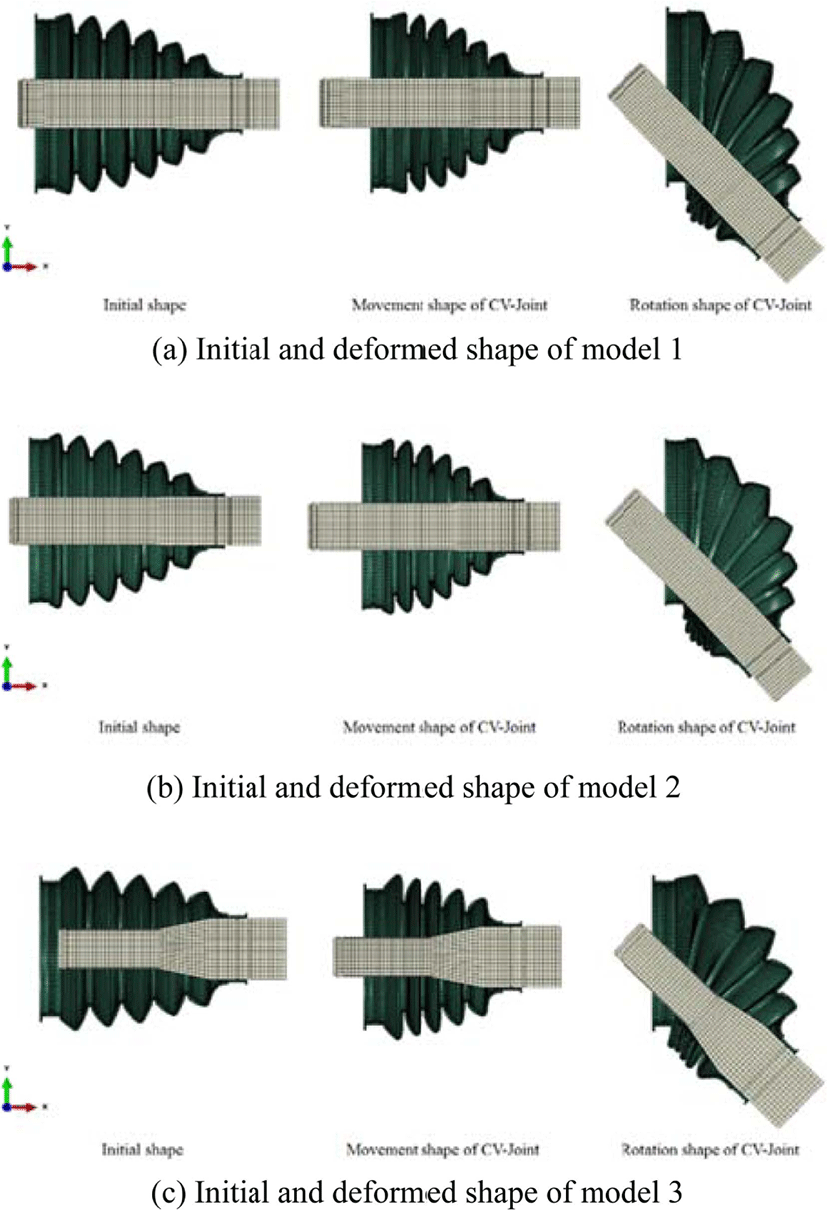
등속조인트가 최대로 이동한 상태에서 회전각도에 따른 부츠의 접촉 양상이 Figure 6-8에 나타나 있다.
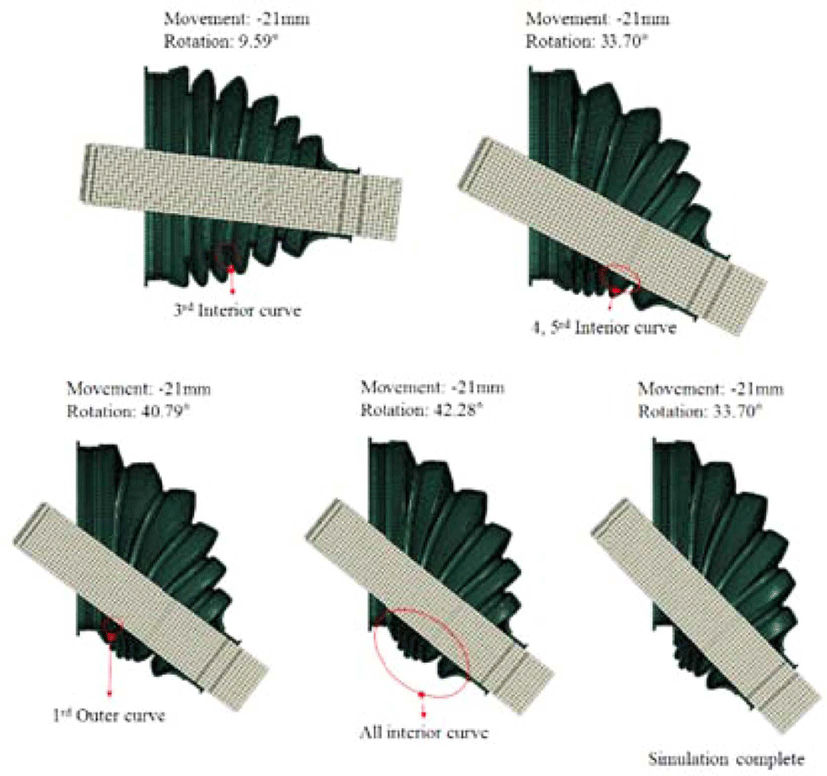
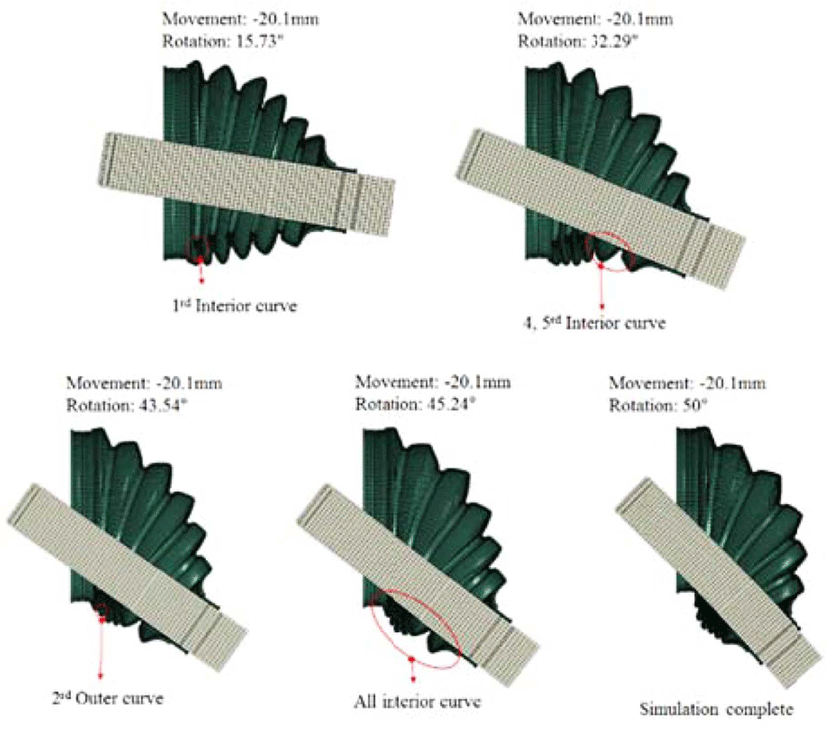
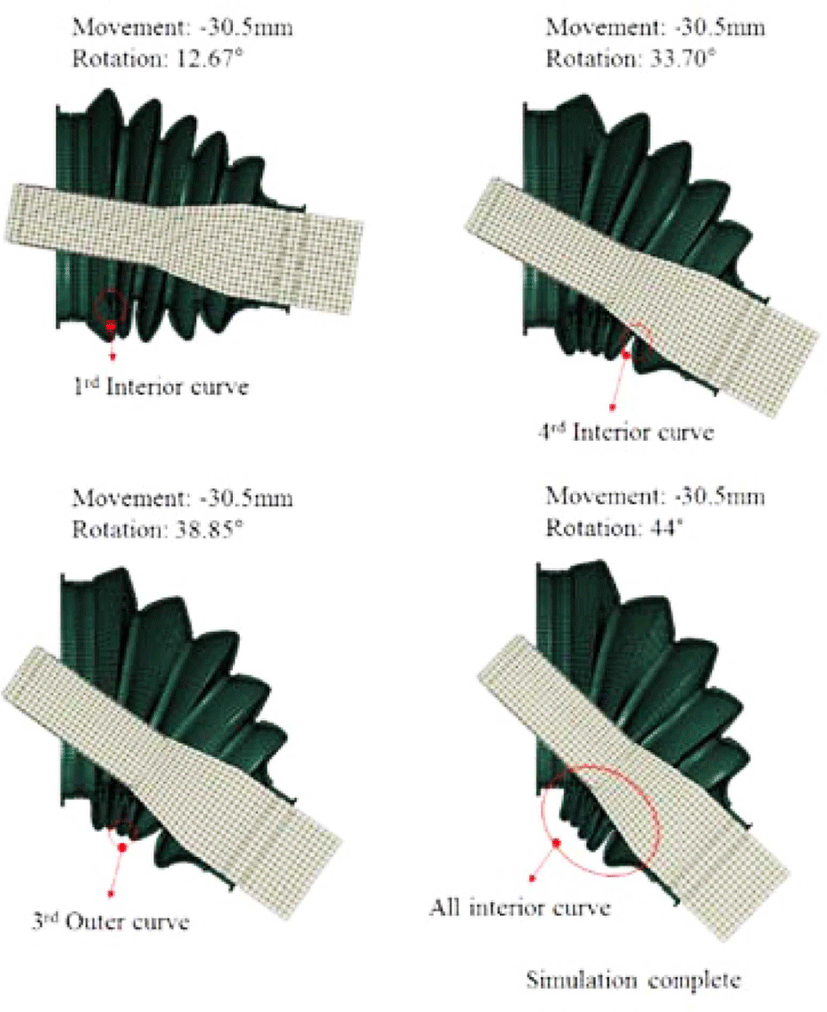
모델 1의 경우 등속조인트 9.59° 회전 시 부츠의 외측에 처음 자체접촉이 처음 발생하였다. 등속조인트 33.70° 회전일 때 부츠의 네, 다섯 번째 내측 굴곡과 등속조인트의 접촉이 시작되었고 등속조인트 40.79° 회전에서 부츠의 내측부분의 자체접촉이 처음 발생하였다. 등속조인트 42.28°에서 부츠의 모든 내측 굴곡이 등속조인트와 접촉하였다. 마찬가지로 해석 완료 시점인 46° 회전에서도 모든 부츠의 내측 굴곡이 등속조인트와 접촉하였다. 모델 1의 등속조인트 회전에 따른 변형양상을 볼 때 33.70° 회전 이후부터 부츠의 네, 다섯 번째 내측 굴곡이 등속조인트와 접촉하여 압축되면서 굽힘 변형을 방해하는 경향을 확인할 수 있다.
모델 2의 경우 등속조인트 15.73° 회전 시 부츠의 외측에 자체접촉이 처음 발생하였다. 등속조인트 32.29° 회전일 때 부츠의 네 번째와 다섯 번째 내측 굴곡과 등속조인트의 접촉이 시작되었고 등속조인트 43.54° 회전에서 부츠의 내측부분의 자체접촉이 처음 발생하였다. 등속조인트 45.24°에서 부츠의 모든 내측굴곡이 등속조인트와 접촉하였다. 마찬가지로 해석 완료 시점인 50° 회전에서도 모든 부츠의 내측굴곡이 등속조인트와 접촉하였다. 모델 2의 등속조인트 회전에 따른 변형양상을 볼 때 32.29° 회전 이후부터 부츠의 네 번째와 다섯 번째 내측굴곡이 등속조인트와 접촉하여 압축되면서 굽힘 변형을 방해하는 경향을 확인할 수 있다.
모델 3의 경우 등속조인트 12.67° 회전 시 부츠의 외측에 자체접촉이 처음 발생하였다. 등속조인트 33.70° 회전일 때 부츠의 네 번째 내측굴곡과 등속조인트의 접촉이 시작되었고 등속조인트 38.85° 회전에서 부츠의 내측부분 자체접촉이 처음 발생하였다. 등속조인트 44°에서 부츠의 모든 내측굴곡이 등속조인트와 접촉하였다. 모델 3의 등속조인트 회전에 따른 변형양상을 볼 때 33.70° 회전 이후부터 부츠의 네 번째 내측굴곡이 등속조인트와 접촉하여 압축되면서 굽힘 변형을 방해하는 경향을 확인할 수 있다.
각 모델의 등속조인트 최대 회전 시의 변형률은 Figure 9에 나타나 있다. 모델 1의 최대 변형률은 약 46% 정도로 부츠의 대경과 부츠의 주름이 만나는 부분에서 국부적으로 나타났다. 최대 변형률이 나타나는 부분을 제외하고 부츠의 평균 변형률은 약 22% 정도로 나타난다. 등속조인트 33.70° 회전 이후 굽힘 변형을 방해하는 네 번째 굴곡의 변형률을 보면 약 33% 정도로 최대 변형률을 보이는 부분을 제외하고 가장 큰 변형을 보이고 있다. 모델 2의 최대 변형률은 약 77% 정도로 부츠의 대경과 부츠의 주름이 만나는 부분에서 국부적으로 나타났다. 최대 변형률이 나타나는 부분을 제외하고 부츠의 평균 변형률은 약 35% 정도로 나타난다. 네 번째 굴곡의 변형률을 보면 약 33% 정도로 최대 변형률을 보이는 부분을 제외하고 가장 큰 변형을 보이고 있다. 모델 3의 최대 변형률은 약 42% 정도로 부츠의 대경과 부츠의 주름이 만나는 부분에서 국부적으로 나타났다. 최대 변형률이 나타나는 부분을 제외하고 부츠의 평균 변형률은 약 19% 정도로 나타난다. 또한 세 번째 굴곡의 변형률을 보면 약 27% 정도로 최대 변형률을 보이는 부분을 제외하고 가장 큰 변형을 보이고 있다.
Conclusions
본 연구는 등속조인트와 TPEE 소재의 부츠가 결합된 세 가지 형상에서 등속조인트의 이동과 회전에 따라 부츠의 변형 양상을 모사하였다. 각도가 변함에 따라 부츠의 자체접촉 및 부츠와 등속조인트의 접촉양상을 관찰하고 반복적인 접촉에 의해 변형에 취약한 부분을 확인하였다.
모델 1에서는 등속조인트 회전각도 9.59°에서 외측 자체접촉이 처음 발생하였다. 그리고 최대 변형부인 부츠의 대경과 부츠의 주름이 만나는 부분과 네 번째 내측굴곡이 다른 부분에 비해 상대적으로 취약하다고 판단된다.
모델 2에서는 등속조인트 회전각도 15.73°에서 외측 자체접촉이 처음 발생하였다. 그리고 최대 변형부인 부츠의 대경과 부츠의 주름이 만나는 부분과 네 번째 내측굴곡이 다른 부분에 비해 상대적으로 취약하다고 판단된다.
모델 3에서는 등속조인트 회전각도 12.67°에서 외측 자체접촉이 처음 발생하였다. 그리고 최대 변형부인 부츠의 대경과 부츠의 주름이 만나는 부분과 세 번째 내측굴곡이 다른 부분에 비해 상대적으로 취약하다고 판단된다.
본 연구는 등속조인트의 회전에 따라 부츠의 변형양상을 모사하였고 부츠변형에 취약한 부분을 판단하였다. 이러한 연구를 통해 부츠 생산을 위한 비용과 시간을 절감할 수 있으며 향후 부츠 디자인을 위한 연구자료로 사용될 수 있을 것이라 판단된다. 또한 부츠변형에 취약한 부분을 확인하는 분석방법으로 활용할 수 있을 것으로 기대된다.