Introduction
타이어 트레드 실리카 컴파운드에서 실리카의 분산은 내마모성, 연비특성, 습윤제동 특성에 영향을 끼치는 핵심 인자이며,1,2 실리카 분산 향상을 위하여 실리카 친화형 작용기가 도입된 고무 중합 및 배합 기술,3,4 수상 또는 유기용매상에서 표면개질된 실리카와 고무를 함께 고형화하는 wet masterbatch (WMB) 기술,5-7 현재 사용되고 있는 실란 커플링제인 bis[3-(triethoxysilyl)propyl]tetrasulfide (TESPT)를 대체하는 신규 실란 커플링제의 개발 및 이를 이용한 고분산 실리카 컴파운드 등 다양한 연구가 이루어지고 있다.8,9
WMB 기술은 1922년 카본블랙/천연고무 WMB 기술 특허 로부터 시작되어 silicate, carbon nanotube, graphite 등의 다양한 보강제를 이용한 연구가 발표되었으며,10-13 2014년 이후부터 실리카 WMB에 대한 연구 결과가 다수 발표되고 있다.5,7,14 실리카 WMB 기술의 핵심 목표는 고함량 및 고분산 실리카 컴파운드의 제조이며, 이를 통해 가공성, 내마모성, 습윤제동 특성, 연비특성을 동시에 개선하는 것이 핵심이다. 실리카 WMB는 고무 solution을 이용한 solution WMB와 합성 고무 및 천연고무(NR) latex를 이용한 emulsion WMB로 나뉘게 된다.15 그 중에서도 emulsion WMB 제조에 사용되는 고무 라텍스는 고형화 단계 이전의 고무가 물에 분산되어 있는 액체를 의미하며, 구체적으로 고무 나무에서 채취된 유액 또는 유화제(ex: rosin soap, fatty acid, sodium dodecyl sulfate, etc.)가 micelle을 형성한 후 그 내부에서 고무 분자가 중합되어 수상에서 분산되어 있는 형태이다.16 Micelle은 염기성 조건에서 표면이 음전하를 나타내므로 micelle간의 반발력으로 인해 수상에서 고르게 분산 가능하다. 고무 latex의 응고는 양이온을 투입하여 micelle 표면의 음전하를 상쇄하면 micelle간의 충돌이 발생하고, 파괴되면서 고무 사슬이 응집되며 고형화 된다. 하지만, 실리카 WMB는 응고 과정에서 실란 커플링제로 표면개질된 실리카가 고무와 같이 응고되므로 실리카 표면의 미반응 silanol group (Si-OH) 또한 응고제에서 생성되는 양이온과 반응이 가능하다.17
앞서 연구된 실리카 WMB의 연구는 주로 실리카 친화형 작용기가 없는 ESBR (emulsion styrene butadiene rub-ber)과 NR에 대해 주로 이루어졌으며,7,14 본 연구진은 ESBR/실리카 WMB에 적합한 응고제의 선정을 위한 연구를 진행하여, 기존에 ESBR 상업적 생산에 사용되던 NaCl/H2SO4 응고제가 아닌 염화칼슘(CaCl2)이 ESBR/실리카 WMB의 제조 및 이를 이용한 특성평가에서 우수한 응고제인 것을 확인했으며, 연구 결과를 Table 1에 간략히 표기하였다.17
일반적으로 실리카와의 filler-rubber interaction (F-R interaction)을 향상시키기 위해 적용되는 작용기는 silanol group과 상호작용이 가능한 작용기가 적용되며, 대표적 실리카 친화형 작용기로는 아민(-NH2), 카르복실(-COOH), 알콕시(-OR), 에폭사이드기이다.18하지만, 앞서 언급하였듯이 실리카 WMB는 응고 과정에서 응고제에서 생성되는 양이온과 silanol group간의 반응이 발생하는데, 이런 경우 silanol group의 수가 감소 가능하므로 실리카 친화형 작용기에 의한 F-R interaction 향상이 방해받을 것으로 예상된다. 따라서, 실리카 친화형 고무를 사용하여 실리카 WMB를 제조하여 특성을 비교할 경우에는 일반적인 ESBR/실리카 WMB 또는 NR/실리카 WMB와는 다른 컴파운드 특성을 나타낼 것으로 예상된다.
따라서 본 연구에서는 reversible addition fragmentation chain transfer (RAFT) 기술과 emulsion 중합법을 적용하여 실리카 친화형 작용기로 카르복실 작용기를 포함하고 있는 기능성 RAFT ESBR latex를 중합한 후 2 wt% 염화칼슘 수용액, 1 M 황산, 1 M 아세트산, 1 M 프로피온산을 응고제로 적용한 실리카 WMB를 각각 제조하고, 배합하여, 컴파운드의 미가류물 특성(Payne effect, bound rubber 함량, Mooney 점도), 가황특성, 가류물 특성(기계적 물성, DIN 마모특성, 동적점탄특성)를 분석하여 카르복실 작용기가 포함된 기능성 RAFT ESBR/실리카 WMB에 대한 응고제의 영향을 분석하였다.
Experimental
실리카 WMB 제조에 사용된 고무 latex는 카르복실 작용기가 포함되어 있는 기능성 RAFT ESBR latex (KKPC, Korea, Mw: 63만, styrene: 24.6%, vinyl in BD: 16%)를 사용했으며, 기능성 RAFT ESBR의 구조 scheme을 Figure 1에 나타냈다. 실리카 WMB 제조에 사용된 표면 개질 실리카는 BET: 175 m2/g의 실리카에 실리카 대비 8 wt%의 TESPT (Si-69, Evonik)를 적용해 표면개질한 NK-179 (Mirae Scientific Instruments Inc., Korea, BET: 126 m2/g)를 사용하였으며, WMB에 사용된 응고제의 종류는 2 wt% 염화칼슘 수용액, 1 M 황산 수용액, 1 M 아세트산(CH3COOH) 수용액, 1 M 프로피온산(CH3CH2-COOH) 수용액이 사용되었다. 배합에 사용된 가공조제는 TDAE oil이 사용되었으며, 가황 활성화제 및 산화 방지제로 각각 zinc oxide, stearic acid, N-(1,3-dimethyl-butyl)-N'-phenyl-p-phenylenediamine (6PPD)가 사용되었다. 가교제 및 가교촉진제로는 sulfur, N-cyclohexyl-2-benzothiazole sulfonamide (CBS), diphenyl guanidine (DPG), tetrabenzylthiuram disulfide (TBzTD)가 사용되었으며, 이후 bound rubber 분석 및 가교밀도 분석을 위해 acetone, toluene, n-hexane, THF가 각각 사용되었다.
100 phr의 실리카를 포함하는 실리카 WMB를 제조하기 위해, 108 phr의 NK-179 실리카를 1 L 증류수에 투입하여, 실리카 슬러리가 되도록 60°C 조건에서 15분간 교반한다. 이후 제조한 실리카 슬러리를 100 phr SBR 고형분에 해당하는 기능성 RAFT ESBR latex와 60°C에서 10분간 교반하고 2 wt% 로 제조된 염화칼슘 수용액 300 mL, 1 M 황산 400 mL, 1 M 아세트산 1 L, 1 M 프로피온산 1 L를 각각 투입한 후 응고시켜 응고제의 종류가 다른 기능성 RAFT ESBR 실리카 WMB을 제조하고 2회씩 세척한 후 60°C 오븐에서 24 시간 건조시켰다.
제조된 WMB는 밀폐식 혼합기(Mirae Scientific Instrument Inc., Korea, 300cc)를 이용하여 SMB (silica masterbatch) step에서는 시작 온도 100°C, dump 온도는 155°C가 되도록 12 분간 배합을 실시했다. 이후 제조된 SMB 컴파운드는 상온에서 24 시간 동안 냉각 후, 밀폐식 혼합기를 이용하여 50°C에서 2 분간 FMB (final masterbatch) 배합을 실시한 뒤, two roll mill을 이용해 시트화 하였다. 자세한 배합표 및 배합과정은 Table 2와 Table 3에 나타냈다. 이후 FMB는 가황특성 분석에서 구한 최적가황시간(t90)을 이용하여 가열프레스에서 160°C 조건으로 가류물을 제조하였다.
미 가류물 특성 평가는 Mooney 점도, bound rubber 함량, Payne effect, TGA를 이용한 WMB내 실리카 함량을 측정하였으며, 실리카 함량 측정법은 다음과 같다. Thermogravimetric analyzer (TGA 550, TA Instrument, U.S.A)를 이용하여 건조가 완료된 각각의 WMB를 상온에서 800°C까지 가열하여 이때의 질량 변화를 식 (1)에 대입하여 실리카 함량을 도출하 였다.17
Bound rubber 함량 평가는 200 mesh 철망에 SMB 0.2 g을 넣고, toluene 200 mL이 들어있는 바이알에 6일간 보관한다. 이때 3일째 되는 날에 toluene을 한 번 교체한다. 그 뒤에 toluene의 세척을 위해 acetone으로 용매를 교체하여 24 시간 동안 보관한 후, 105°C 오븐에서 24 시간 건조시켜 질량을 측정하였다. 이때 측정된 무게는 식 (2)에 대입하여 bound rubber의 함량을 계산하였다.
RB : bound rubber content (%)
Wfg : the weight of the filler and gel
Wt : the weight of the sample before immersion
mf : the weight fraction of the filler in the compound
mr : the weight fraction of rubber in the compound
가공성의 척도인 Mooney 점도는 Moony viscometer (Vluechem IND, Korea)를 이용하여 측정하며 ASTM D 1646에 따라 100°C 조건에서 1 분간 예열한 뒤 4분 동안 2 rpm의 속도로 rotor를 회전시켜 Moony 점도 값을 측정했다.
Filler 분산의 지표로 알려져 있는 Payne effect 측정은 rubber process analyzer (RPA 2000, Alpha Technologies, USA)를 이용하여 측정했으며, SMB를 이용하여 ASTM D 8059에 따라 60°C 조건에서 변형율 변화에 따른 storage modulus (G’)의 변화를 측정했다.
가황특성 및 가류물의 특성 평가에서는 가황특성, 기계적 물성, DIN abrasion loss, 동적 점탄특성을 비교 분석하였다. 가황특성의 측정은 FMB 제조 후 two-roll-mill을 이용하여 시트화된 컴파운드를 moving die rheometer (MDR, TOYOSEIKI, Japan)을 이용해 30분간 160°C, ± 1° 진동각 조건에서 토크 상승을 측정하여 최적 가황시간(t90)을 결정하였다. 측정값을 이용해 cure rate를 계산하였고, 최적 가황시간의 1.2배를 적용하여 160°C 프레스에서 가류를 실시하였다.
가교도의 정량적 측정은 다음의 swelling 법을 이용한 방법으로 구하였다. 가교된 시편을 10 mm × 10 mm 크기로 자른 후 THF, n-hexane을 용매로 하여 각 2 일, 1 일간 침지시켜 시편 내부의 유기 첨가물을 제거한 후 실온에서 1 일간 건조시킨 다음 무게를 측정하고 유기 첨가물이 제거된 시편을 toluene을 이용하여 1 일간 팽윤 시킨 후 무게를 측정하였다. 측정된 무게와 식 (3)을 이용하여 대입해 νr 값을 구한 후, νr 값을 Flory-Rehner 식 (4)에 대입하여 가교도를 구하였다.
νr : the volume fraction of rubber in the swollen gel at equilibrium
Wd : the dried sample weight
Wf : the weight of the filler in the sample
Ws : the weight of the swollen sample
ρs : the density of solvent
ρr : the density of rubber.
ν : crosslink density (mol/g)
MC : average molecular weight between crosslink points (g/mol)
νr : the volume fraction of rubber in the swollen gel at equilibrium
Vs : the molar volume of solvent (cm3/mol)
ρr : the density of the rubber sample (g/cm3)
χ : the polymer-solvent interaction parameter (0.34)
가류물의 기계적 물성(modulus, tensile strength, elongation at break)은 ASTM D 412 조건에 따라 아령형 시편을 제작하여 측정하였으며, universal testing machine (UTM, KSU Co., Korea)을 이용하였다.
내마모성 측정은 DIN abrasion 시험법을 적용하였으며, ASTM D 5963에 따라 DIN 마모시험기(Withlab, Korea)를 이용해 측정하였다. 시편은 직경 16 mm, 두께 8 mm의 실린더형으로 제조했으며, 연마포가 부착된 원통 모양의 드럼을 이용하여 5 N의 수직 하중 하에서 시편을 40 m 마모시켜 시편의 마모량을 측정하였다.
동적 점탄특성 평가는 dynamic mechanical analyzer (DMA Q800, TA Instruments, USA)를 이용하여 tension mode에서 0.2% strain, 10 Hz 조건으로 -80°C 부터 80°C 까지의 온도범위에서 hysteresis (tan δ)와 loss modulus (E”)을 측정하였으며, 측정된 tan δ 값으로부터 peak tan δ, tan δ at 60°C (rolling resistance index) 값을 구하였다. 또한 변형율 변화 평가는 dynamic mechanical thermal spectrometer (EPLEXOR 500N, Gabo, Germany) 장비를 이용하여 60°C 조건에서 5%, 10% strain에서의 tan δ 값을 측정했다.
Results and Discussion
WMB내 실리카 함량 및 SMB의 Payne effect를 Figure 2, Table 4에 나타냈다. 실리카 함량은 모든 WMB가 유사하게 측정되어 응고제의 종류에 따른 실리카 함량에는 큰 차이가 없는 것으로 확인되었다. 염화칼슘 및 황산을 응고제로 적용한 T-1, T-2 컴파운드가 약 유기산이 사용된 T-3, T-4 컴파운드 대비 우수한 실리카 분산을 나타냈다. 앞서 발표된 연구에 따르면 filler가 고무와 같이 응고되는 WMB 기술에서 응고 과정에서 소요되는 시간은 WMB의 filler 응집을 결정하는 인자이며, 수상에서 응고되는 속도가 느릴수록 더 많은 filler 응집이 발생한다.19 약 유기산의 경우 응고 과정에서 낮은 이온화도로 인해 대량의 응고제가 투입되어야 하고 응고 소요 시간이 길어 더 많은 실리카 응집이 발생한 것으로 판단된다. 이에 비해, 염화칼슘과 황산은 상대적으로 적은 응고제 양으로도 응고가 가능한 2가 양이온이거나 이온화도 높은 강산이므로 응고 과정에서의 투입량이 적고 빠른 시간내에 응고되므로 우수한 실리카 분산을 나타낸 것으로 판단된다. 특히, 염화칼슘의 경우 이온화 과정에서 생성되는 칼슘 이온이 실리카 표면의 silanol group의 수소와 치환되는 반응인 알칼리-실리카 반응으로 인해 실리카 사이의 수소결합을 억제할 수 있어 제일 우수한 실리카 분산을 나타내었다.17,20
T-1 | T-2 | T-3 | T-4 | |
---|---|---|---|---|
Silica content in WMB (phr) | 99.0 | 98.7 | 99.2 | 99.3 |
∆G’ (MPa) | ||||
G’ at 0.3% strain - G’ at 40% strain | 1.5 | 1.6 | 3.6 | 4.3 |
T-1~T-4 컴파운드의 bound rubber 함량을 Table 5에 나타냈다. Bound rubber 함량은 실리카와 고무 사이의 F-R interaction에 의한 효과와 occluded rubber의 증가에 따른 효과가 병합되어 측정된다.21,22평가 결과, 염화칼슘이 적용된 T-1 컴파운드가 제일 낮은 35.4%의 bound rubber 함량을 나타냈으며, 그 외 컴파운드는 45% 전후의 유사한 bound rubber 함량을 나타냈다. 황산과 염화칼슘의 bound rubber 경향은 앞서 연구하였던 ESBR/실리카 WMB에서의 평가 결과와는 반대의 경향을 나타냈다. ESBR의 경우 실리카 친화형 작용기가 없기에 염화칼슘을 응고제로 적용하였을 때 알칼리-실리카 반응에 의해 실리카의 소수화도가 향상되어 높은 F-R interaction을 나타냈다. 하지만 본 연구에 적용된 실리카 친화형 RAFT ESBR의 경우 카르복실 작용기를 포함하고 있는데, 알칼리-실리카 반응에 의해 미반응 silanol group의 수가 감소하므로, 카르복실 작용기와 silanol group의 상호작용이 감소하여 bound rubber 함량이 감소한 것으로 판단된다.
T-1 | T-2 | T-3 | T-4 | |
---|---|---|---|---|
Bound rubber content (%) | 35.4 | 44.1 | 44.5 | 46.2 |
아세트산과 프로피온산이 적용된 T-3, T-4 컴파운드는 황산과 유사한 bound rubber 값을 나타냈지만, Payne effect를 측정을 통해 확인한 미 가류물내 실리카 분산이 매우 불리하므로 occluded rubber에 의한 영향으로 bound rubber 값이 높게 측정된 것으로 판단된다.
각 컴파운드의 가황특성 및 Mooney 점도 측정 결과를 Figure 3와 Table 6에 나타냈다. 평가 결과, 실리카 분산이 우수할수록 낮은 Tmin 값을 나타냈으며 제일 우수한 실리카 분산을 보였던 염화칼슘 응고제가 적용된 T-1 컴파운드가 제일 낮은 Tmin값을 나타냈다. Tmin값은 컴파운드의 Mooney 점도와 연관되는 결과로써23 T-1 컴파운드가 가장 낮은 Mooney 점도를 나타냈다. 이에 비해, 유기산이 적용된 컴파운드(T-3, T-4)의 경우 불리한 실리카 분산으로 인해 높은 Tmin값을 나타냈으며, Mooney 점도 측정에서도 1분간 예열 이후, 측정이 시작될 때 200MU 값을 초과하여 Mooney 점도의 측정이 중지되어 over range가 기록되었다. Tmax 값은 실리카 컴파운드에서 가교도와 실리카 network의 형성이 주된 인자이다.24평가 결과, 분산이 불리해 실리카 network가 많이 형성된 T-3, T-4 컴파운드의 경우 높은 Tmax 값을 나타냈다.
기존의 ESBR/실리카 WMB의 연구 결과는 염화칼슘이 황산보다 4% 개선된 Mooney 점도를 나타내었으나, 본 연구에서는 이보다 뛰어난 20%의 Mooney 점도 개선 효과를 나타냈다. 실리카 친화형 작용기가 존재하는 경우 F-R interaction이 향상됨에 따라 Mooney 점도가 증가한다고 알려져 있다.25 하지만, 염화칼슘이 적용된 경우 알칼리-실리카 반응에 의해 미반응 silanol group의 수가 감소함에 따라 카르복실 작용기에 의한 F-R interaction이 감소하므로 bound rubber 함량이 감소하여 낮은 Mooney 점도를 나타냈다.
가류물의 기계적물성, 가교밀도, DIN 마모특성을 Figure 4과 Table 7에 나타냈다. 평가 결과, 약 유기산이 적용된 T-3, T-4 컴파운드가 높은 modulus를 나타냈으며, 염화칼슘이 적용된 T-1 컴파운드가 낮은 300% modulus를 나타냈다. 300% modulus 경향은 정량적으로 구한 가교밀도 값의 경향과 일치하며 가교밀도가 높을수록 높은 300% modulus를 나타냈다. 가교도가 높은 T-3, T-4 가류물은 불리한 실리카 분산에 따른 occluded rubber의 증가에 의해 effective filler volume이 증가했고 이로 인해 가교도가 증가하여 높은 300% modulus를 나타냈다. 염화칼슘과 황산이 각각 적용된 T-1, T-2 가류물은 염화칼슘이 적용된 T-1 가류물이 더 낮은 300% modulus를 나타냈는데 이 또한 ESBR/실리카 WMB에서의 연구 결과와는 상반되는 결과를 보였다. 이는 앞서 설명하였듯이 염화칼슘의 경우, 알칼리-실리카 반응에 의해 실리카 표면의 미반응 silanol group의 수가 감소하므로 카르복실 작용기에 의한 F-R interaction이 저해되므로 가교밀도가 낮아져 불리한 modulus 결과를 나타냈다.
DIN 마모 측정을 통한 내마모성 평가 결과에서는 실리카 분산이 우수한 염화칼슘과 F-R interaction이 우수한 황산이 적용된 T-1, T-2 가류물이 우수한 내마모성을 나타냈으며 실리카 분산이 매우 불리한 T-3, T-4 가류물의 경우 염화칼슘이 적용된 T-1 가류물 대비 약 20% 정도 불리한 내마모성을 나타냈다. ESBR/실리카 WMB의 연구 결과에서는 염화칼슘이 우수한 내마모성을 보였으나, 본 연구결과에서는 T-1, T-2 가류물이 유사한 내마모성을 나타냈으며, 이는 F-R interaction의 차이에서 기인한 결과이다.
가류물의 온도변화에 따른 tan δ curve 와 loss modulus 측정 결과를 Figure 5와 Table 8에 나타냈다. Temperature sweep 조건에서 tan δ curve에서의 peak tan δ 값은 고무의 부피 분율과 연관된 값이며, occluded rubber의 양이 많을수록 낮은 값을 나타낸다.26평가 결과, 약 유기산이 응고제로 적용된 T-3, T-4 가류물이 낮은 값을 보여 불리한 실리카 분산에 의한 occluded rubber가 많이 형성되었음을 확인하였다. 또한 염화칼슘을 적용한 T-1 가류물이 제일 높은 peak tan δ 값을 나타내어 우수한 실리카 분산으로 인해 occluded rubber가 제일 적게 형성되었음을 확인 가능하며, 황산을 적용한 T-2 가류물은 T-1 가류물보다 occluded rubber가 많이 형성된 것을 확인하였다. Peak tan δ를 나타낼 때의 온도는 가류물의 유리전이온도(glass transition temperature, Tg)를 의미하며, 정량적 가교밀도 및 bound rubber 함량이 높을수록 고무 chain의 mobility가 감소하므로 높은 유리전이온도를 나타낸다. 본 평가 결과에서도 가교도가 높을수록 높은 Tg 값을 나타낸 것을 확인하였다.
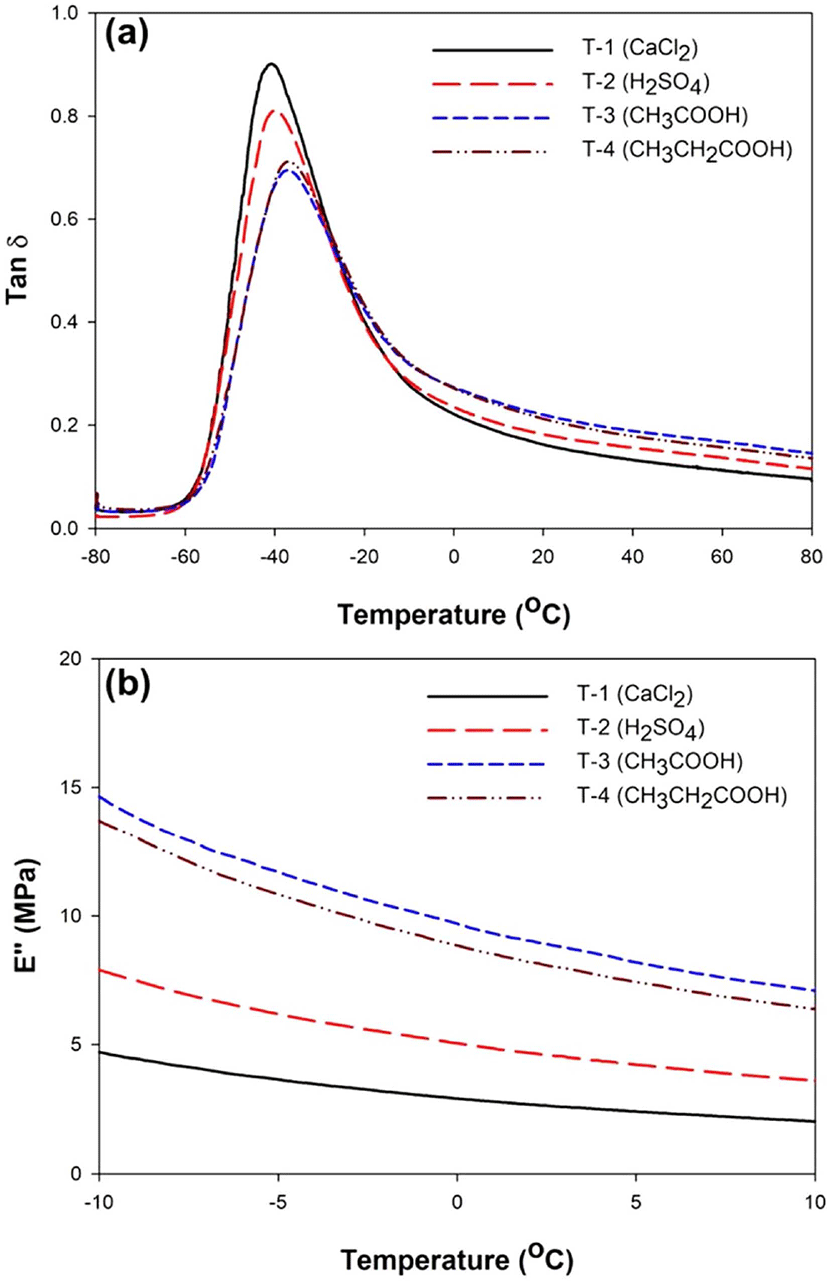
Unit | T-1 | T-2 | T-3 | T-4 | |
---|---|---|---|---|---|
Tg | °C | −40.8 | −40.0 | −37.1 | −36.9 |
Peak tan δ | - | 0.901 | 0.811 | 0.695 | 0.710 |
E” at 0°C | MPa | 2.91 | 5.05 | 9.69 | 8.84 |
Tan δ at 60°C | - | 0.113 | 0.137 | 0.168 | 0.157 |
60°C에서의 tan δ 값은 타이어 트레드 컴파운드에서의 연비특성을 나타내는 지표로써 알려져 있으며, filler network의 파괴와 재생성에 의한 hysteresis loss가 60°C에서의 tan δ 값을 높이는 주된 메커니즘으로 알려져 있다.24즉, 가교도가 높거나 실리카 분산이 우수할수록 60°C에서의 낮은 tan δ 값을 나타낸다. 평가 결과, 실리카 분산이 우수할수록 60°C에서의 낮은 tan δ 값을 나타냈고, 분산이 가장 우수했던 염화칼슘을 응고제로 적용한 T-1 가류물의 경우, 다른 가류물 대비 21~49% 개선된 연비특성을 나타낸 것을 확인하였다. Loss modulus (E”) 값 또한 동일한 filler 함량일 때 분산이 우수할수록 낮은 값을 나타낸다고 알려져 있다.22즉, filler network가 발달할수록 높은 E” 값을 나타낸다. 평가결과, 염화칼슘을 적용했을 때 제일 낮은 loss modulus 값을 나타내어 분산이 우수함을 재차 확인하였다.
가류물의 변형율에 따른 60°C에서의 hysteresis 손실 측정 결과를 Table 9에 나타냈다. 변형율이 커질수록 filler network가 파괴되면서 hysteresis loss가 커져 높은 tan δ 값을 나타낸다고 알려져있다.27 평가 결과, occluded rubber가 적고 실리카 분산이 우수한 T-1 가류물이 낮은 tan δ at 60°C 값들을 나타냈다. Payne effect에서 불리한 실리카 분산을 나타냈던 T-3, T-4 컴파운드는 높은 tan δ at 60°C 값을 나타냈다. 하지만, SMB를 이용한 Payne effect 측정 결과에서 T-1 컴파운드와 유사한 실리카 분산을 나타냈던 황산이 적용된 T-2 가류물은 변형율 변화에 따른 hysteresis 측정에서는 높은 tan δ at 60°C 값들을 나타냈다. 이러한 결과로 보아 황산을 응고제로 적용한 경우 미 가류물내 실리카 분산은 우수하지만, 가황과정에서 가황 초기 열에 의한 실리카 재응집이 많이 발생한 것을 의미한다. 가황특성의 그래프인 Figure 3을 봤을 때 T-2 컴파운드는 T-1 컴파운드에 비해 가황 과정 초기에 실리카 재응집에 의해 torque 값이 빠르게 상승한 것을 확인 가능하다. 이러한 결과로 보아 실제 실리카 컴파운드의 물성, 동적 점탄특성과 실리카 분산을 연관지어 설명하기 위해서는 Payne effect를 통한 미가류물의 실리카 분산 뿐만 아니라 가류물을 이용한 실리카 분산을 동시에 평가해야 할 필요가 있다.
Unit | T-1 | T-2 | T-3 | T-4 | |
---|---|---|---|---|---|
Tan δ at the 5% strain | - | 0.187 | 0.196 | 0.196 | 0.196 |
Tan δ at the 10% strain | - | 0.190 | 0.199 | 0.201 | 0.202 |
Conclusions
본 연구에서는 카르복실 작용기가 포함된 기능성 RAFT ESBR을 이용한 실리카 WMB에 대한 응고제의 영향을 분석하였다. 평가에 사용된 응고제는 2 wt% 염화칼슘 수용액, 1 M 황산, 1 M 아세트산, 1 M 프로피온산이 사용되었다. 약 유기산인 아세트산과 프로피온산이 적용된 경우 WMB 응고 소요시간이 길어 실리카의 응집이 많이 발생해 미 가류물 상태에서부터 불리한 실리카 분산을 나타냈고 내마모성, 연비특성에서 모두 불리한 결과를 나타냈다. 염화칼슘이나 황산이 적용된 경우 공통적으로 미 가류물내 실리카 분산은 우수하였으나, 황산이 적용된 경우 가류 과정에서 실리카 재응집 억제 효과가 떨어져 가류물에서 불리한 실리카 분산을 나타내어 연비특성이 불리한 결과를 나타냈다. 이에 비해 염화칼슘이 적용된 경우 알칼리-실리카 반응에 의해 silanol group 이 감소하므로 카르복실 작용기의 F-R interaction 향상이 방해받아 낮은 기계적 물성을 나타냈으나, 가류 과정에서의 silanol group의 수가 감소하여 실리카 재 응집 억제 효과가 뛰어나 분산과 관련된 연비특성에서 우수한 결과를 나타냈다.
본 연구 결과를 이전 ESBR/실리카 WMB 응고제 영향 분석 결과와 비교하였을 때 공통적으로 염화칼슘이 우수한 내마모성, 연비특성, 실리카 분산을 나타냈다. 하지만, 실리카 친화형 작용기가 고무 사슬에 존재할 경우에는 황산을 응고제로 사용한 컴파운드가 염화칼슘을 응고제로 사용한 컴파운드 대비 높은 F-R interaction을 나타내므로 실리카 친화형 작용기가 존재하는 고무를 이용한 WMB를 제조할 경우 목표로 하는 특성에 적합한 응고제의 선택이 필요하다.