Introduction
Nowadays isoprene rubbers e.g. natural rubber (NR), because of their high tensile strength, high wear resistance, flexibility and abundant availability are considered fascinating for developing different materials needed in our society. For instance, NR is being widely used in nearly 40,000 kinds of products including car and aircraft tires, medical devices, surgical gloves, toys, pacifiers, etc..1,2 NR is naturally obtained from the rubber tree (scientifically known as Heavea brasilesis Muell) as a latex.3,4 Along with other organic compounds, as NR consists of polyisoprene in maximum amount, it is classified as elastomers.5,6 On the other hand, during the world War II, the important supplies of NR was cut off and synthetic rubber was developed as an alternative. The most commonly referred synthetic rubber is polyisoprene (IR), which was successfully synthesized in a solution medium employing a stereospecific polyisoprene catalysis system in 1950’s.7,8 NR and IR have many similarities in physical properties, both have high tensile strength, tear resistance, and good low temperature flexibility. Compared to IR, NR has higher tensile strength, tear resistance, and low odor. While, special properties can also be found in synthetic rubbers, synthetic rubbers can have excellent heat resistance, lower temperature resistance, and heat aging improvements. Despite these differences, both the NR and IR have a huge demand by the manufacturers due to their low costs and pleasing performance.2,9 Recently, there is a demand for developing the high-performance polyisoprene rubber having better gas barrier and adhesion properties.10 In this regard, epoxidation of polyisoprene has been emerged, and numerous studies have been reported for epoxidation of NR.11-13 But there is no such report on epoxidation of synthetic polyisoprene. Generally, all of the epoxidation of NR reported earlier are accomplished from the latex form of NR. Normally, the latex has a limited storage duration after while the sedimentation or precipitation occurs which deteriorate the latex quality. Also, the latex being a liquid is obtained in a container which additionally required a safe and cost-intensive transportation if the epoxidation needs to be performed in multiple places. On the contrary, the solid (or gum) of NR is easily transportable. In spite of latex form, the synthetic polyisoprene is also available as gum. Therefore, to resolve these problems associated with epoxidation of NR and IR, a solution based epoxidation method is elusive. In this paper, we have synthesized and studied the epoxidation of NR and IR, and compared the difference between the epoxidized form of NR (i.e., ENR) and IR (i.e., EIR).
Experimental
Natural rubber (NR, Mw: 1,454,319), polyisoprene rubber (IR, Mw: 1,3666,771, cis-form) were used. Hexane (95%); chloroform (99.5%), toluene (99.5%), and methanol (99.5%) were obtained from Daejung Chemicals & Metals Co., Korea. meta-Chloroperoxybenzoic acid (mCPBA) of 70% purity was purchased from Aldrich Chemical Co.
The rubbers (i.e. NR or IR) were dissolved in hexane (1.0% w/v) at room temperature for 8 hours. Later, the mCPBA dissolved in chloroform (6% w/v) was slowly added to the rubber-hexane solution. The reaction was allowed to proceed under constant, gentle stirring (300 rpm) at different constant temperature for different time intervals. After completion of the reaction for a fixed interval, the reaction mixture was slowly poured into the cooled methanol. The precipitated polymer was washed with water twice and dried in a vacuum oven at 60°C for 24 hours.
The FTIR spectra was recorded with a resolution of 4 cm−1, in the range of 600 cm−1 to 4000 cm−1, and the signal averaged over 32 scans on a Fourier transform infrared spectrometer (Nicolet iS5, Thermo Fisher Scientific, USA).
The 1H-NMR spectra were recorded at a frequency of 300 MHz with CDCl3 as solvent by using a Bruker DRX 300 nuclear magnetic resonance spectrometer (Bruker, Germany). And the epoxy content was calculated from the following equation Eq. (1):
where I2.7 and I5.1 are the integration of peaks at 2.7 or 5.1 ppm, respectively.
The gel content was determined by immersing the rubber (W0) in the dried toluene and kept in the dark without shaking or stirring for 1 week at room temperature. Later, the sol fraction was separated from the gel fraction, and the gel fraction was dried in an oven at 60°C until constant weight (W1) was reached. The gel fraction was calculated by Eq. (2):
Results and Discussion
From the FTIR spectra, it can be observed that both the NR and IR showed the same bands at 3100~2000 cm−1 and 1500~600 cm−1 which are attributed to the carbon-carbon and carbon-hydrogen bonds of the rubber macromolecules. The structure of NR or IR can be evidenced from the presence of C=C stretching (1663 cm−1), C-H out-of-plane bending of the cis-1,4 (834 cm−1), and CH3 deformations (1376 cm−1 and 1377 cm−1).
In addition to the polyisoprene, NR also contains 6% of non-rubber or non-isoprene compounds—containing lipids (1.5~3 wt%), proteins and polypetides (2 wt%), carbohydrates (0.4 wt%) and minerals (0.2 wt%). From the FTIR of NR, the non-rubber compounds can be figured out e.g. amine (3283 cm−1), ester (1748-1738 cm−1), carboxyl (1711 cm−1), amide I (1630 cm−1) and amide II (1541 cm−1).16
The plausible chemical reaction during the epoxidation is shown in Figure 3. During the epoxidation, the double bonds in the cis-polyisoprene chain have been converted to oxirane groups by peracid. Meanwhile, the possibility of ring-opening is also unavoidable. At low level of epoxidation, the isolated oxirane can form trans diol (Figure 3(1)). With increasing the epoxidation degree, the adjacent epoxide groups and a five cyclic ether becomes the major product (Figure 3(2)). Epoxidized natural rubber (ENR) (or epoxidized polyisoprene rubber (EIR)) consists of two parts namely, sol (soluble in organic solvent) and gel (insoluble in organic solvent). The gel is intermolecular ether having net-like structure, which is formed due to the ring-opening (Figure 3(3)). High amount of cross-linked structure of the gel content is believed to be attributed with higher degree of epoxidation.14,17 After epoxidation, the new peaks (Figure 2) at 1250 cm−1 and 878 cm−1 are related to the oxirane ring and stretching vibration of C–O–C, respectively.
Furthermore, the 1H-NMR spectra of NR and ENRs (ENR25 and ENR50) are shown in Figure 4. ENR25 and ENR50 indicate the 25% and 50% of epoxy content in NR, respectively. Compared with NR, the spectrum of ENR shows two additional peaks at 1.3 ppm and 2.7 ppm, which are related to the methyl (-CH3) and methylene (-CH2-) protons of the epoxy group, respectively.14 IR and EIR have same 1H-NMR spectra.
From Figure 5(a) and (b), the sol (i.e., epoxy content) and gel contents for both of ENR and EIR increased with increasing the mCPBA/rubber weight ratio. Apart from the ring opening reaction during epoxidation, the increased gel content of ENR than that of EIR is attributed to the existence of non-rubber compounds in the NR, i.e. protein and lipids which are hydrogen bonded with each other (Figure 5(c)).18
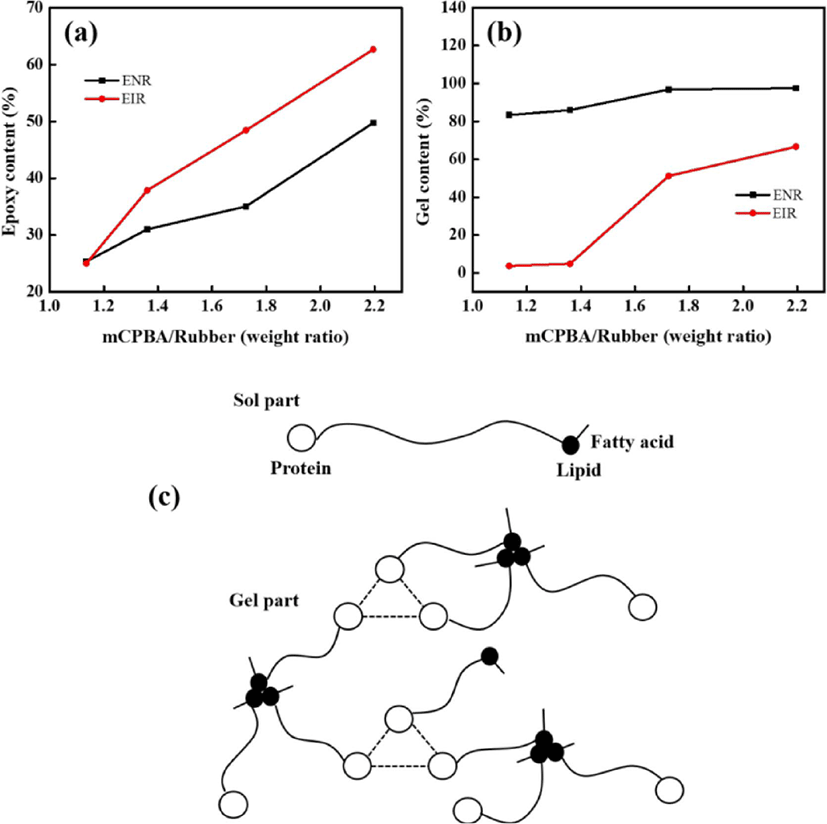
Figure 6 shows effect of reaction time on the epoxidation at the reaction temperature 30°C, mCPBA/rubber mole ratio 1.725:1. It can be observed that with increasing the reaction time the epoxy content decreases. A rapid decrease was found after the 4 hours. A presumable explanation is that, the epoxidation reaction is complete in a short reaction time (2 hours), when the reaction time is longer than 2 hours, the epoxy content decreases, indicating that the excess mCPBA caused ring-open reaction under acidic conditions. Hence, the suitable reaction time is 2 hours.
As is shown in Figure 7, the maximum epoxy content of our synthesized ENR was obtained at 30°C. Although, the EIR is not much effected by temp and the maximum epoxy content of EIR was obtained at 20°C, further increase of reaction temperature decreases the epoxy content of both the ENR and EIR because higher temperature led to an increased instability of epoxy group and favor the possibility of ring-open reaction. Thus, it can be said that under same condition, EIR has lower optimum reaction temperature while producing higher amount of epoxy content than the ENR. The demerits of ENR is associated with the non-rubber compounds in NR, especially the amine, ester which are also reacting with the mCPBA.
From Figure 6 and 7, it can be said that the optimum reaction time for epoxidation is 2 hours for both the NR and IR whereas the reaction temperatures are ~30°C (< 40°C) for NR and ~20°C for IR towards synthesizing the ENR and EIR having maximum epoxy content. With increasing the reaction time, the oxirane ring under the acidic condition becomes unstable and easily opens resulting in production of side products. Consequently, the epoxy content decreases. On the other hand, epoxidation being an exothermic reaction, increasing reaction temperature may facilitate the side reaction. So, the reaction temperature must be controlled, and it should not be too much high.
Conclusion
NR and IR have been successfully epoxidized by using solution methods, mCPBA as reaction reagent and hexane as solvent. The results turns out that epoxy content of ENR and EIR increase with mCPBA content, and decrease with long reaction time. Epoxidation of IR can be carried out at lower temperature, while the optimum reaction temperature for NR is 30°C. And we find out that at same reaction condition, EIR always have higher epoxy content than ENR, and ENR has higher gel content, that is owing to the non-rubber compounds in NR. The results have certain significance towards industrial upscaling of the proposed method.