Introduction
대기 중 이산화탄소 가스 농도 증가로 인한 지구온난화에 따른 환경 문제와 석유, 천연 가스 및 기타 화석 연료 자원의 고갈로 인해, 새로운 천연 에너지에 대한 관심이 집중되고 있다. 수소는 가장 중요한 미래의 청정에너지원 가운데 하나로, 연소 시 물을 생성시켜 대기 오염 물질을 배출하지 않으며, 직접 연소를 위한 연료 또는 연료 전지 등의 연료로 사용이 간편하여, 전세계적으로 수소 에너지에 대한 연구가 활발히 진행되고 있다.1-5
최근, 수소 에너지를 적용한 자동차인 수소 연료전지 자동차가 전세계적으로 상업화에 성공하였다. 수소 가스의 낮은 체적 에너지 밀도로 인해, 수소 가스를 효율적으로 저장 및 운송하기 위해 높은 압력으로 압축하여 사용하고 있다.6-8 일반적으로 수소 연료 전지 자동차에는 70 MPa 로 압축된 수소를 연료 탱크에 저장하여 사용하며, 수소 스테이션에서는 수소 가스는 압축기에 의해 최대 90 MPa의 고압으로 압축하여 저장 탱크에 저장하여 보관한다. 수소 가스 충전 시 수소 연료 자동차의 연료 탱크와 수소 스테이션의 보관 탱크간의 압력 차에 의해 수소 가스가 공급되기 때문에, 고속 충전을 위해 고압의 수소 가스를 사용한다.9
수소 스테이션은 고압의 수소를 수소 연료 전지 자동차에 공급하기 위해, 저장 탱크, 벨브, 노즐, 압축기, 필더, 냉각기 등 다양한 장치로 구성되어 있다.10-12 이러한 장치들을 연결하기 위해서는, 고압 수소 환경 하에서 기밀력을 유지할 수 있는 내구성이 우수한 실링 소재들이 필요하다.
고무 소재는 탄성과 가공성이 우수하며 금속에 비해 가벼운 소재로, 수소 연료 전지 자동차 및 수소 스테이션용 가스켓, 호스, O-ring 등 다양한 부품에 적용되고 있으며, 특히 수소 스테이션에 고무 소재가 적용되는 부품을 Figure 1에 나타내었다. 수소 연료 전지 자동차 및 수소 스테이션의 안정성과 신뢰성을 확보하기 위해 다양한 수소 노출 환경에 따른 고무 소재의 물성 변화에 대한 연구가 진행되고 있다.9,10,13-17 하지만, 지금까지 보고된 문헌들은 고무 컴파운드의 수소 노출에 따른 단기적인 화학적, 기계적 물성에 관한 연구 내용이 대부분이며, 수소 노출 후의 장기내구성에 대한 보고가 거의 없다. 또한, 수소 연료 전지 자동차 및 수소 스테이션용 고무 부품에 대한 신뢰성과 안정성을 평가할 수 있는 국제적 표준 평가 방법이 확립되지 않아, 이를 위한 다양한 고무 소재의 수소 노출에 따른 장기 내구성 변화에 대한 연구가 필수적이다.
일반적으로 고무 소재의 장기 내구성을 측정할 수 있는 대표적인 시험 방법으로는 Compression stress relaxation (CSR) 측정법을 이용한 O-ring의 기밀력 (sealing force) 변화에 의한 수명 예측법이 있다. CSR 측정법은 ISO 3384에 국제 표준 시험 측정법을 규정하고 있으나,18 측정 방법과 측정환경에 따라 시험 결과가 상이하기 때문에, 측정 오차를 최소화할 수 있는 최적 시험 방법을 선정하는 것이 중요하다.19,20
CSR 측정 방법은 크게 continuous CSR법과 intermittent CSR법으로 나누어진다. Continuous CSR법은 실시간으로 O-ring의 기밀력 및 노화 거동을 관찰할 수 있으나, 측정 시험 설비가 고가이며 jig의 형태 및 크기에 제약이 있다. 반면 Intermittence CSR법은 일정 주기마다 O-ring의 기밀력을 측정하는 번거로움이 있으나, 시험편의 형태와 크기에 제한이 없기 때문에 O-ring의 실사용 환경 하에서의 노화 거동을 관찰할 수 있는 효율적인 측정법이다. 이에 Intermittent CSR 측정법을 이용한 고무 O-ring의 수명 예측에 의한 장기 내구성에 관한 연구가 활발히 진행되고 있다.21-25 앞서 우리는 intermittent CSR 측정법을 이용하여 가교 구조가 Hydrogenated NBR O-ring의 노화 거동 및 수명 변화에 대한 미치는 영향과 염소고무 O-ring과 불소고무 O-ring 의 노화 거동 및 수명 예측에 관한 연구 결과를 발표하였다.23-25
본 연구에서는 수소 스테이션용 부품 소재 중 압축부에 사용되는 고온용 씰링 고무인 불소고무 O-ring의 고압수소 노출 후의 장기내구성을 확인하기 위하여, 상용 불소고무 O-ring의 고압수소 노출 시간에 따른 고온 CSR (Compression Stress Relaxation) 시험을 통하여 고압수소 노출 후의 장기내구 변화를 알아보고자 하였다.
Experimental
본 연구에서 사용한 FKM O-ring은 ㈜삼정산업에서 생산 판매되고 있는 선경과 내경이 각각 3.53 mm, 91.67 mm인 FKM O-ring을 사용하였으며, 연구에 사용한 O-ring의 실물 사진을 Figure 2에 나타내었다.
본 연구에서는 FKM O-ring을 CHMC2 (Compressed Hydrogen gas Material Compatibility 2)에 권고한 실사용 압력의 1.35배인 94.5 MPa 압력하에 1, 3, 7일간 노출 시킨 후에 기계적 특성과 장기 내구성 측정을 위한 CSR 시험을 실시하였다. 사용된 수소는 순도 99.999%의 순수 수소를 사용하였으며 감압속도는 10 MPa/min 이다.
고압수소노출에 따른 FKM고무의 기계적 물성 변화에 대한 연구를 위해, sheet 형태로 제조한 고무 시편을 ASTM D412에 명기된 크기로 절단하여 수소 분위기 노출 전·후의 인장 강도, 100% Modulus를 만능시험기(Universial Testing Machine; UTM, Instron 3345, Instron Ltd., USA)를 이용하여 상온에서 crosshead speed 50 mm/min의 속도로 측정하였다. 수소 노출 후의 물성 변화율은 수소 노출 전의 인장 물성 (M0)와 노출 후의 인장 물성(Mt)를 측정하여 (Mt-M0)/M0 × 100에 의해 변화율을 계산하였다. 수소 노출에 따른 고무 소재의 미세 구조의 변화는 전자현미경(Video microscope system, SV-55, Sometech Co., Korea)를 이용하여 관찰하였다.
수소 노출 후의 CSR시험은 150온도에서 Intermittent CSR 측정법으로 시험하였으며 오링의 기밀력은 Instron(U.S.A)사의 UTM (3345(Q3776) model)을 이용하여 측정하였다. Indenter는 cylinder 형태이며, 크기는 2.5 mm × 18.0 mm(직경 × 높이)이다. 측정 속도는 1.0 mm/min이다. Intermittent CSR jig는 오링의 사용 환경을 고려하여 Figure 3에 나타낸 바와 같이 설계 제작하였다. Jig는 부식을 방지하기 위하여 stainless steel을 사용하였다. Bottom jig plate의 크기는 180 mm × 30 mm(직경 × 두께)로 설계하였다. 오링 장착을 위한 bottom jig plate의 홈부는 KS B 2799 (O-rings housings design criteria; Korea Standard) 규격을 기준으로 설계하였으며, 이때 기밀력 측정을 위한 추가 압축을 고려하여 0.1 mm의 여유 공간을 설계하였다. 홈부의 크기는 각각 92.79 mm × 4.75 mm × 2.58 mm (내경 × 너비 × 깊이)이다. 홈부의 평행도는 dial gauge를 이용하여 측정하였다. Dial gauge의 측정에 의한 홈부의 깊이 편차는 0.01 mm로 나타났으며, bottom jig plate의 평행도가 intermittent CSR 측정에 적합한 것을 확인하였다. UTM의 indenter와 접촉하는 metal plate의 크기는 오링의 내경(91.73 mm)을 고려하여 직경을 120.0 mm로 설계하였다. Metal plate와 indenter의 지름 비율이 약 4.8 : 1로 차이가 크기 때문에, intermittent CSR 측정에서 metal plate의 휘어짐에 의한 기밀력 측정에 오차가 발생할 것으로 사료된다. 따라서, metal plate의 휘어짐을 방지하기 위하여 두께를 5.0 mm로 설계하였다. Upper jig plate의 크기는 180 mm × 30 mm(직경 × 두께)로 설계하였다. Figure 1에 나타낸 바와 같이, upper jig plate의 일부분을 무게 감소와 metal plate의 중앙 위치 확인을 위하여 제거하였다. Upper jig plate의 바닥에 shim 역할을 하는 5.0 mm 길이의 돌출부를 설계하였다. 오링을 jig에 체결하면, 오링은 2.68 mm로 압축되며, 이때의 압축율은 실제 사용환경을 고려한 25%로 실시하였다. Upper jig plate의 중앙 홀의 직경은 indenter의 직경(25.0 mm)을 고려하여 27.0 mm로 설계하였다. Upper jig plate의 중앙 홀을 indenter의 직경보다 크게 설계함으로써, Intermittent CSR 측정에서 오링의 기밀력은 Instron (U.S.A)사의 UTM (3345(Q3776) model)을 이용하여 측정하였다. Indenter는 cylinder 형태이며, 크기는 2.5 mm × 18.0 mm(직경 × 높이)이다. 측정 속도는 1.0 mm/min이다.
이렇게 설계 제작한 jig를 이용한 상온 intermittent CSR 시험법의 오링의 기밀력 측정은 Figure 4와 같으며, region 1은 indenter가 jig의 metal plate와 접촉하지 않은 무측정 영역이며, UTM의 crosshead가 아래로 이동하면서, indenter가 jig의 중앙 홀을 통하여 metal plate와 최초로 접촉하게 된다. Indenter가 metal plate와 접촉한 후, metal plate의 stiffness가 region 2의 Line (a)로 측정된다. indenter 가 하강함 에 따라서 metal plate는 upper jig plate로부터 분리되고 오링은 metal plate에 의하여 추가적으로 압축된다. 이때, 오링의 stiffness가 region 3의 Line (b)에 측정된다. 오링의 초기 기밀력 혹은 접촉힘(contact force)은 Line (a)와 Line (b)의 교점으로 구할 수 있다.
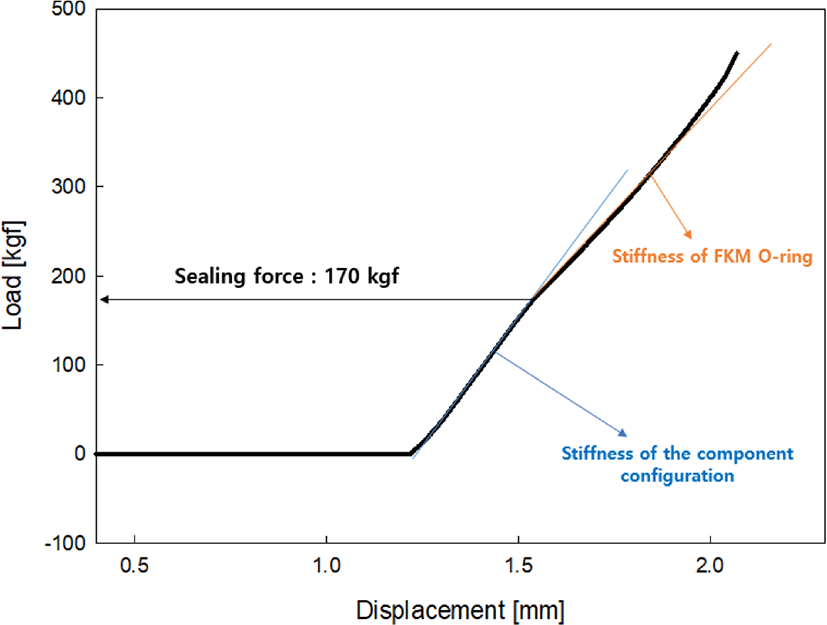
Intermittent CSR 측정은 다음과 같은 과정을 통하여 측정하였다. 1) 오링을 설계 제작한 jig에 체결한다. 2) 오링이 체결된 jig를 가속 노화를 위하여 150℃의 convection oven에 보관한다. 3) 일정 시간 간격으로 jig를 convection oven에서 꺼낸 후, UTM을 이용하여 오링의 기밀력을 측정한다. 4) 측정이 끝나면 jig를 convection oven에 보관하고 열 가속 노화 실험을 계속 진행한다. Convection oven에서 jig를 꺼내는 순간부터 jig와 FKM 오링은 공냉에 의한 수축 거동을 나타내며, 수축이 과도하게 이루어질 경우에는 1) 오링의 수축에 의한 strain state 변화, 2) 수축 혹은 팽창 시에 jig surface와 오링 사이의 마찰 발생으로 인하여 기밀력 측정에 오차가 발생할 수 있다. 따라서 일정 시간 간격으로 이루어지는 intermittent CSR 측정은 최대한 열 손실이 적어야 하며, 본 연구에서는 convection oven을 UTM 옆에 설치하여 열 손실에 의한 기밀력 측정 오차 발생을 최소화하였다.
잔류 기밀력 (Residual sealing force)는 초기 기밀력 (F0)와 150℃ 노출 시킨 후 기밀력(Ft)를 측정하여 (Ft-F0)/F0 × 100에 의해 계산하여 나타내었다.
Results and Discussion
FKM 고무시험편을 수소 압력이 94.5 MPa인 상온의 챔버내에 1일 동안 투입한 후, 상압으로 감압시켜 시험편을 취출하고, 취출 24시간 경과 후 기계적 물성을 측정하여 수소 가스 노출 후의 물성 변화를 측정하였다. 수소 가스 노출 전·후와 노출후 시간경과에 따른 물성을 Table 1에 정리하여 나타내었다.
Table 1에 나타낸 바와 같이, 시험에 사용된 고무 시편들의 수소 노출전과 노출 24시간 후 비교시 100% Modulus, 파단 신율 및 영구압축줄음률의 변화율은 5% 이내로 물성의 저하가 다소간 있지만 그 변화량은 크지 않았다. 또한 24시간 노출 후 시간의 경과에 따른 물성 변화를 살펴보기 위하여 노출 후 1, 24시간의 기계적 물성을 측정하였는데, 시간이 경과할수록 고압 수소 노출 전의 기계적 강도 수준으로 회복되었다. 이는 고압 수소 노출에 의한 고무 시편의 물리적 결함은 관찰되지 않았으나, 고무 시편에 침투된 수소 가스에 의해 고무 시험편의 부피가 팽창하였고 시간이 경과함에 따라 고무 시편 내에 잔존하는 수소 가스가 대기 중으로 확산되어 부피가 감소하였기 때문으로 판단된다.
FKM 오링을 수소 압력이 94.5 MPa인 상온의 챔버내에 1, 3, 7일 동안 투입한 후, 상압으로 감압시켜 오링을 취출하고 취출 24시간 경과 후 CSR jig에 장착하여 초기 기밀력을 측정하여 Figure 5에 나타내었다.
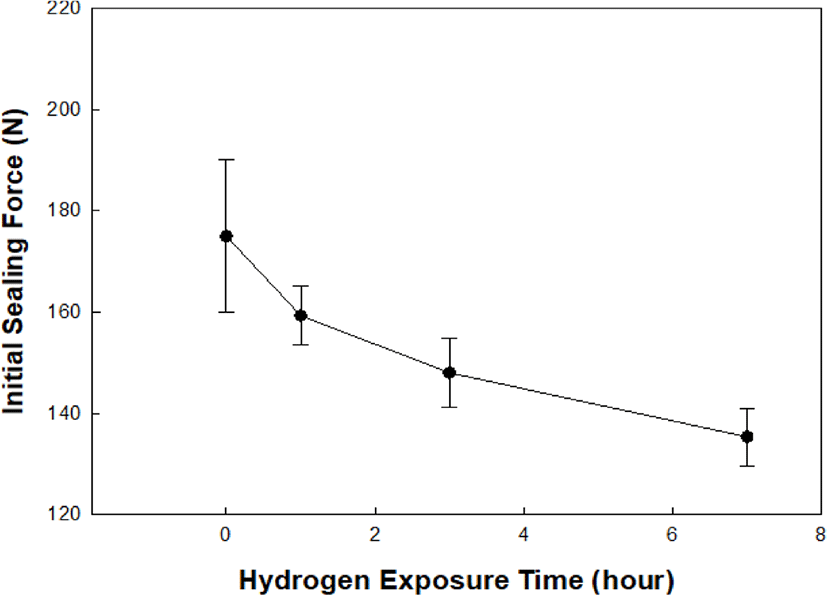
앞서 실험한 결과인 1일 경과 후 기계적 강도와는 달리 고압수소 1일 노출 후의 오링 초기 기밀력은 10% 이상 저하되었으며 고압수소 노출 시간이 길어질수록 초기 기밀력은 크게 떨어졌다. 이러한 원인은 시험편보다 오링의 두께가 두꺼워 보다 많은 수소가스의 침투가 이루어진 부분과 수소가 침투하였다가 빠져나간 microvoid가 기계적 강도에는 큰 영향을 주지 않지만 압축모드의 기밀력 시험에서는 더 큰 차이를 보여주기 때문으로 판단된다.
FKM 오링을 수소 압력이 94.5 MPa인 상온의 챔버내에 1, 3, 7일 동안 투입한 후, 상압으로 감압시켜 오링을 취출하고 취출 24시간 경과 후 CSR jig에 장착하여 150℃에서 시간에 따른 잔류기밀력 변화를 Figure 6에 나타내었다. Figure 6에 나타난 바와 같이 수소 노출전에 비하여 노출 후의 시간에 따른 기밀력 저하율은 크게 나타났으며, 노출 시간에 따라서도 노출시간이 증가할수록 기밀력의 변화가 크게 나타났다. 이러한 기밀력의 변화를 ASTM에서 기준으로 하고 있는 초기 기밀력대비 50% 수준의 기밀력을 고장조건으로 설정하여 Figure 7에 나타내었다. Figure 7에 나타난 바와 같이 고압수소 노출시간에 따라서 150℃, 50% 고장조건에 도달하는 시간(수명)은 매우 짧아지는 것을 알 수 있었으며 노출시간이 길어질수록 수명 감소 속도는 둔화되는 것을 알 수 있었다. 이를 통해서 고압 수소 노출시의 형성된 미세한 기공(Void)는 기계적 강도에는 큰 영향을 미치지 않지만 초기 기밀력과 장기 노화시 미세한 void로 인해 촉진되는 노화 산화반응이 매우 크게 발생하여 고압수소에 노출 된 오링의 수명이 급격하게 감소됨을 확인 할 수 있었다.
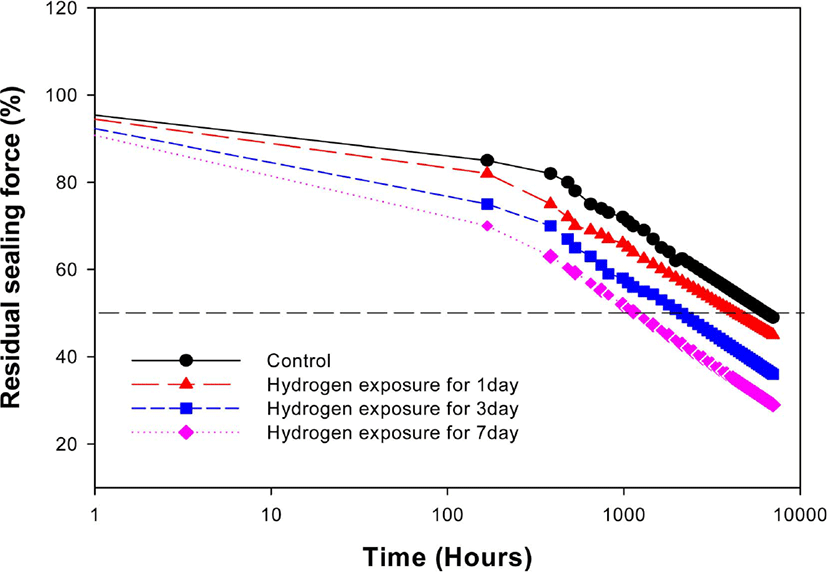
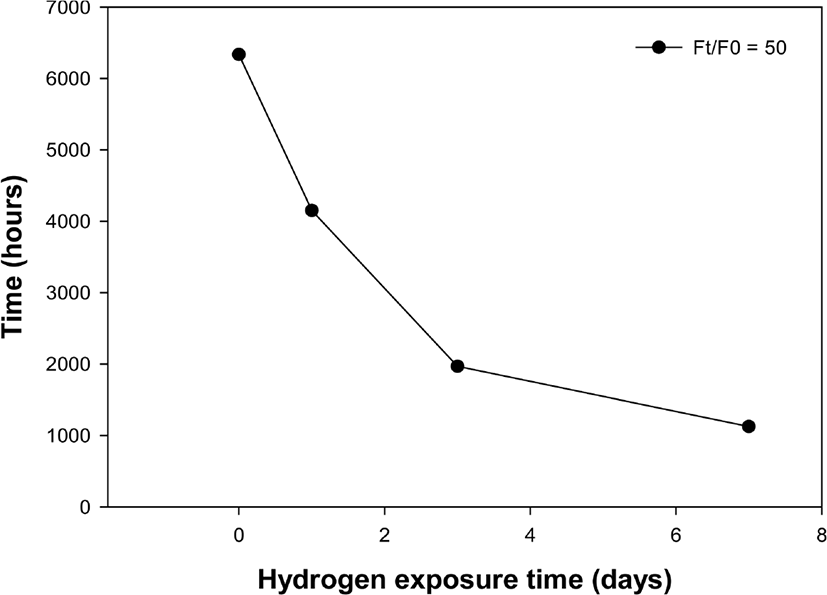
FKM 오링의 수소 노출에 따른 장기 내구성 저하의 원인를 규명하기 위해, 장기 내구 시험 후 FKM 오링을 액체 질소를 이용하여 부러뜨려 파단면을 전자현미경을 이용하여 관찰하였고, 그 결과를 Figure 8에 나타내었다. 고압 수소에 노출된 FKM 오링은 노출 전 오링의 파단면에 비하여 많은 크랙과 기공들이 관찰되었다. 특히 고압 수소에 3, 7일 노출된 오링의 경우에는 미세한 기공보다는 크랙이 많이 발생하였다. 일반적으로 고압의 수소 분위기 하에 노출 되었을 때, 고무의 물리적, 기계적 물성 변화는 고무 내에 존재하는 수소 분자들이 초기에는 고무 시편 내에 용해되어 존재하다가 시간이 지남에 따라 고무 시편 내의 수소 분자들이 과포화상태가 되고, 과포화된 수소 분자들이 서로 뭉쳐 마이크로 크기의 기공들을 형성하게 된다. 이렇게 형성된 기공이 장기 내구시험에 의해 야기된 노화 집중에 의해 고무 시편 내에서 크랙이 발생한 것으로 판단된다.
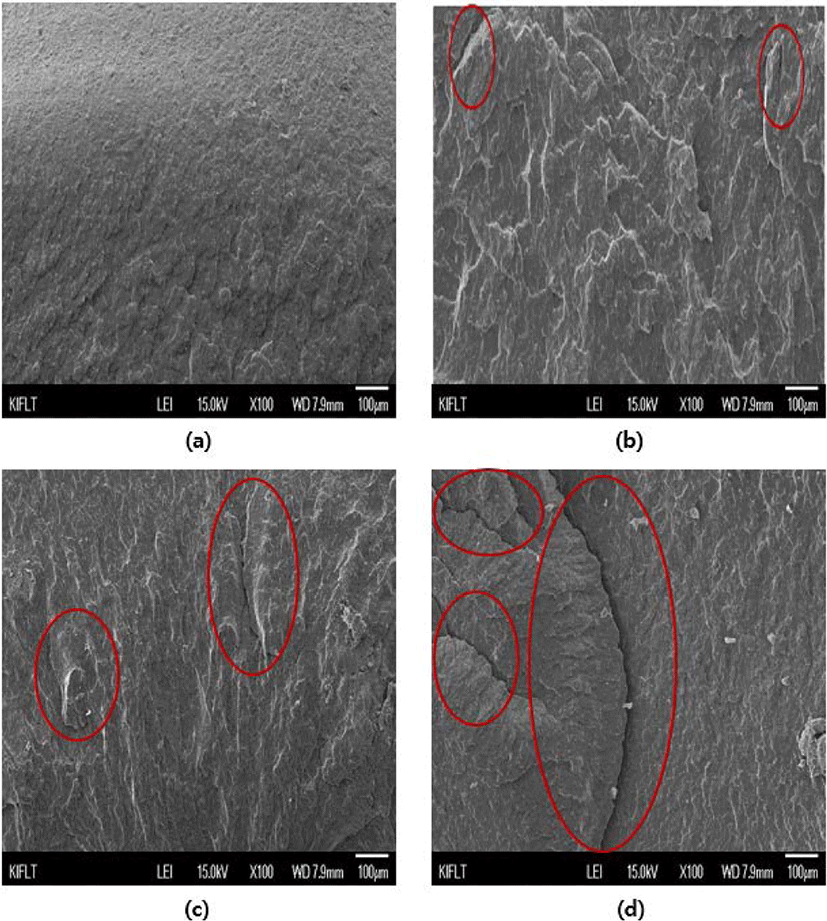
Conclusions
수소스테이션 및 수소하의 국제 시험규격인 CHMC2 (Compression hydrogen gas material compatibility 2)는 고압수소 노출 후에 취출 후 기계적강도(인장강도, 모둘러스, 신율 등)의 저하율에 대한 시험을 소재 시험방법으로 명시하고 있는데, 본 연구에서는 고압수소 노출 후의 단기적인 기계적 물성 저하가 장기적인 내구성에 미치는 영향을 간이적으로 평가하기 위해 수소 스테이션용 부품으로 사용되는 불소 오링의 고압 수소 가스 노출에 따른 단기 기계적 물성 변화와 장기내구성의 변화를 고온(150℃)에서 기밀력 변화를 측정할 수 있는 CSR시험을 통하여 비교해 보았다.
불소오링의 고압수소 노출후의 단기적인 기계적 물성과 장기내구평가 결과, 불소계 오링의 단기적인 기계적인 물성 변화는 크게 나타나지 않지만 초기기밀력과 고온에서 장기노출 시의 기밀력변화는 매우 크게 나타났다.
이러한 결과는 고압수소 노출 후의 형성된 미세한 기공(microvoid)이 노출 후 시간에 따라 최소화되어 기계적인 물성에는 큰 영향을 미치지 않지만 시편에 비하여 상대적으로 두꺼운 오링에 적용시 미세기공의 함량이 증가하여 초기기밀력의 변화를 크게 하였으며, 형성된 미세기공이 장기적인 고온 노화시 산화의 가속화 요소가 되어 고압수소 노출 시간과 고온에서의 방치 시간이 증가할수록 기밀력의 저하가 크게 나타났다.
본 실험을 통하여, 고압수소 환경하에서 고무소재 적합성 평가는 단기적인 기계적 물성 저하율 측정보다는 초기 기밀력 및 장기 내구성 평가가 보다 변별력이 있으며, 실제 고압수소 노출시 생성된 미세기공은 장기내구성 저하에 큰 영향을 미친다는 것을 알 수 있었다. 이러한 결과를 통해서 향후 수소스테이션 및 수소차에 적용되는 고무 씰링재의 고압수소하에서 실시되는 고압수소적합성 시험에서 CHMC2에서 규정하고 있는 기계적 물성평가 뿐만 아니라 장기내구성 및 수명에 대한 평가가 매우 중요할 것으로 판단된다.