Introduction
중공 제품을 만드는 공정은 크게 세가지로 압출 블로우(Extrusion Blow), 사출 블로우(Injection Blow), 사출 스트레치 블로우(ISBM, Injection Stretch Blow Molding) 성형이 있다. 우리가 접하는 대부분의 음료용 PET병은 축방향 연신이 중요한 ISBM공정으로 생산된다. ISBM은 사출성형을 통한 프리폼에 열을 가한 뒤 PET(Polyethylene terephthalate)병 형상의 금형에 결합하고 Stretch Rod가 축방향으로 연신과 동시에 공기를 불어넣어 최종 제품을 얻어내는 방식이다. 사출된 프리폼의 상태가 페트병 형상에 많은 영향을 주기 때문에 사출된 프리폼의 상태가 중요하다.1-5
PET는 연신에 의한 높은 인장강도와 결정화도, 우수한 내화학성으로 식음료 분야에 포장재 원료로 많이 사용되고 있다. 이러한 상황에서 환경문제가 대두되고 있으며, 그에 따라 원천 재료의 감량, 재활용, 재사용 등의 환경을 위한 적극적인 대응이 필요하다.
기존 연구에서는 PET병의 구조적 안정성을 위한 사출 특성에 대한 연구와 잔류응력과 수축을 최소화하는 연구가 진행되었다. 또 프리폼 이 아닌 PET병 디자인에 따른 잔류응력 분포의 연구가 진행되었다. 하지만 프리폼의 두께 감소에 대한 사출성형 특성 연구는 미미하다. 프리폼 감량을 위한 두께의 감소는 필수이며 사출성형 해석 이후 블로우 해석을 통해 적합성을 판단해 볼 수 있다.6-8
본 연구에서는 PET병 감량에 초점을 맞추어 기존에 사용하는 프리폼을 기준으로 감량 모델을 설계하였다. 두가지의 내압용 프리폼 모델에 대해 몸통부의 두께를 기존 대비 15%, 20% 감량한 모델을 설계했다. 이를 사출성형해석 프로그램(Moldflow)을 이용하여 감량 프리폼에서 나타나는 사출 특성을 파악하고 디자인에 따른 특성을 분석하였다. 이를 통하여 같은 용량의 용기 두께를 줄이기 위한 프리폼의 사출성형 조건을 검증하였다.
Experimental
본 연구에서 사용한 프리폼이 Figure 1에 나타나 있다. 탄산음료용 PET병을 제작하는 프리폼이다. 기존의 두가지 모델(P1, P2)에서 몸통의 두께를 각각 15%, 20% 줄여 두께가 감소된 모델을 제작하였다.
Table 1에 기존 모델과 감소된 모델의 치수와 두께 및 무게 감소량이 나타나 있다.
프리폼은 8-캐비티 금형에서 핫런너 시스템으로제작된다. Figure 2에 해석을 위한 모델링이 나타나 있다.
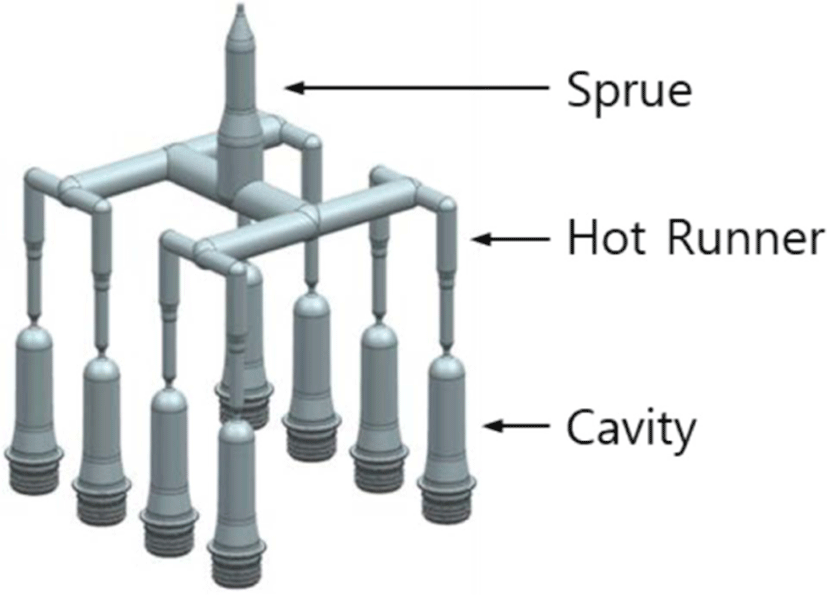
8개의 캐비티는 기하학적으로 형태가 같기 때문에 1개의 캐비티로 해석하여 8개 캐비티 사출을 고려하였다.
프리폼 메쉬 형태는 Figure 3과 같이 3D 사면체 요소(Tetrahedral)를 사용하였다. 프리폼 P1의 4면체 개수는 824,494개이고 프리폼 P2는 783,360개이다.
냉각 채널은 Figure 4와 같이 모델링 하였다. 냉각관 직경은 5 mm이고 프리폼 내부의 효율적인 냉각을 위해 적용한 버블러(bubbler) 형태의 냉각 채널은 외경 8 mm, 내경 5 mm로 설정하였다.9
해석에 사용한 사출기는 LS엠트론의 WIZ220E이다. 사출기 톤수는 220 ton, 최대 사출 속도는 150 mm/s, 스크류 직경은 45 mm, 최대 사출 압력은 163 MPa이다. 프리폼 P1의 사출 온도는 295°C, 프리폼 P2는 280°C로 설정하였고 냉각수와 금형의 온도는 각각 13°C, 20°C로 두 프리폼에서 동일하게 적용하였다. 기존 프리폼과 감량 프리폼의 사출 조건은 동일하게 설정하였으며 Figure 5에 나타나 있다.
사용한 수지는 Lotte chemical의 내압병용 수지인PET Cool이다. ARES-G2 측정장비를 이용하여 온도 280°C, 295°C, 310°C에서 측정한 전단 점도는 Figure 6에 나타나 있다.
Results and Discussion
길이 방향으로 긴 프리폼의 두께를 20%까지 감소시켰기 때문에 캐비티로 주입된 용융 수지가 좁은 통로를 지나가는 과정에서 고화가 우려된다. 특히 기존 두께 대비 20% 감소된 프리폼의 경우 얇아진 두께로 인한 수지의 고화로 미성형 우려가 크다. 그래서 우선 감량 모델의 충전 패턴을 통해 미성형이 발생 여부와 전반적인 충진 흐름을 파악하였다. Figure 7은 프리폼 P1, P1_15, P1_20의 충전 패턴을 시간에 따라 나타낸 결과이며 기존 및 감량 프리폼에서 같은 패턴으로 충진된다. 기존, 15%, 20% 감량 프리폼 순서대로 각각 93.3%, 93.6%, 94.8%의 체적에서 보압 전환이 진행되었다. 프리폼 P2, P2_15, P2_20은 Figure 8과 같은 충진 패턴을 보였으며 기존 및 감량 프리폼 전체에서 미성형이 관찰되지 않았다. 보압 전환은 Figure 5에서 보듯 스트로크로 정해져 있어서 감량 프리폼에서 보압 전환 시 충전된 체적이 증가하였다.
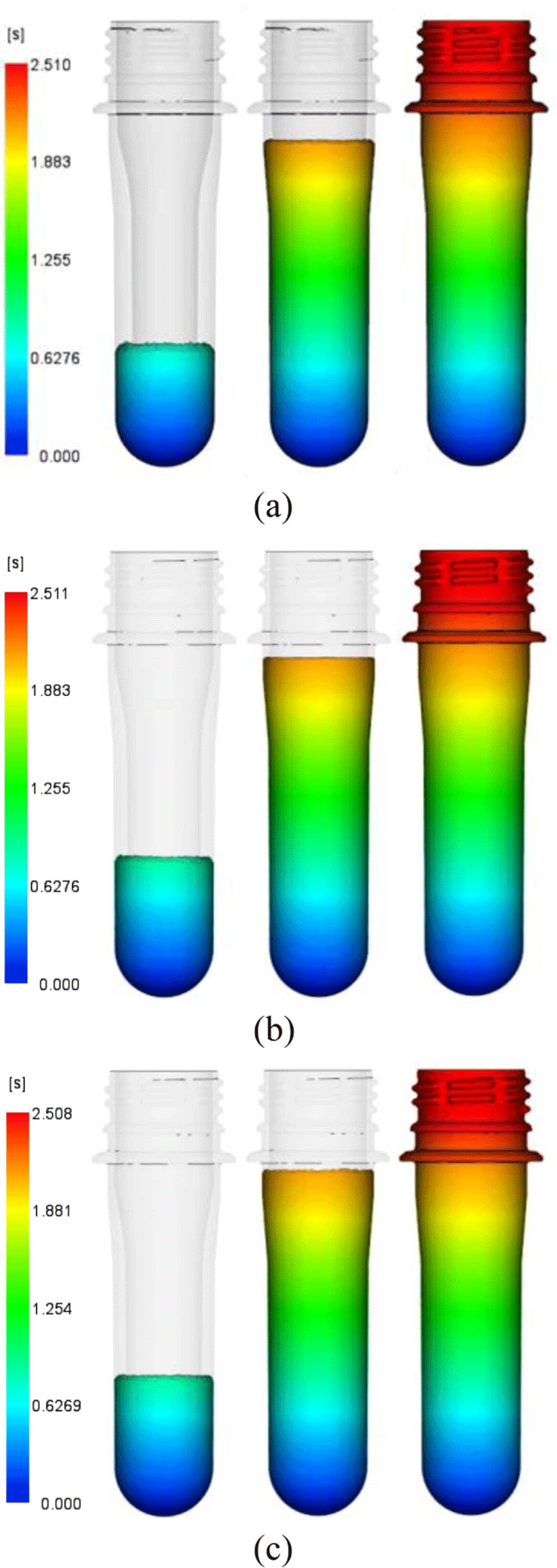
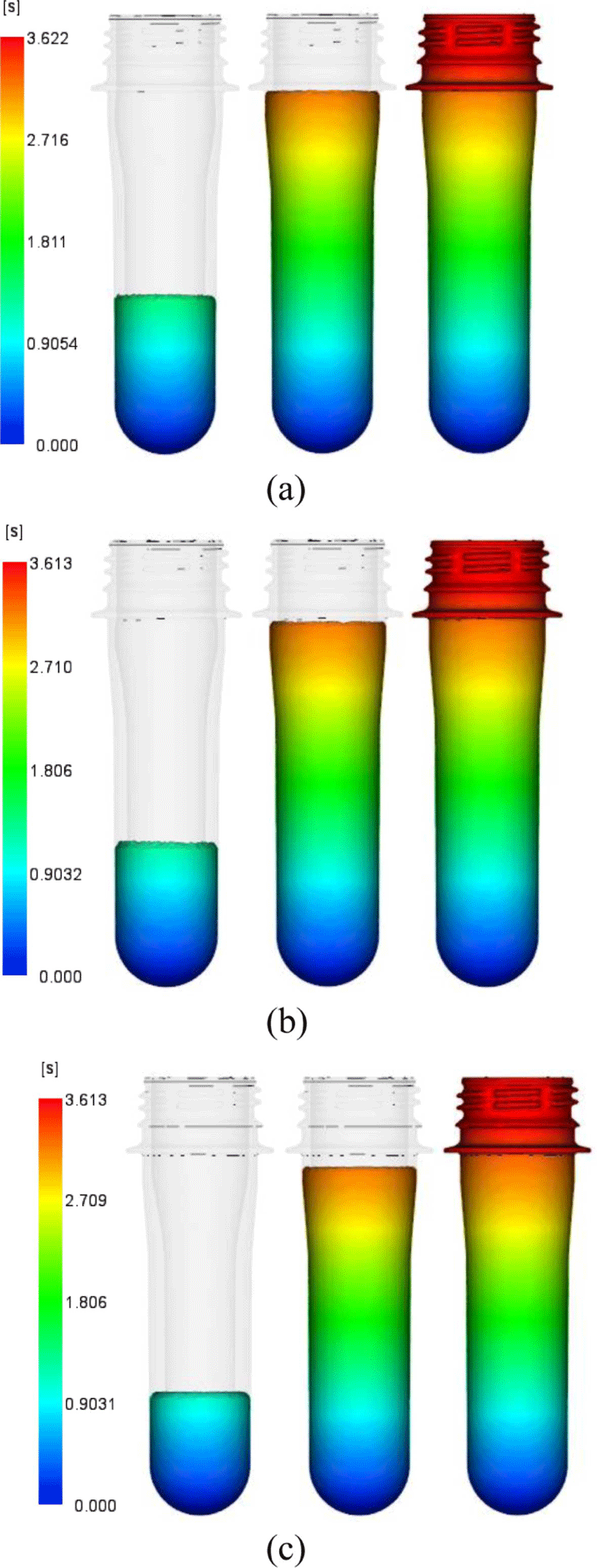
Figure 9, 10 은 충진 직후의 프리폼 온도분포를 나타낸다. 두께가 얇고 충진 말단인 네크부에서 온도가 낮게 분포한다. 또한 게이트부도 냉각 채널이 집중적으로 위치하고 있어 온도가 낮게 분포한다. 몸통부는 다른 부분보다 두께가 다소 두꺼워 가장 높은 온도 분포를 보였다. 기존과 감량 프리폼의 해석 결과를 비교했을 때 P1계열 프리폼과 P2계열의 온도 분포는 전반적으로 비슷한 양상을 보였다. 이는 기존 대비 몸통부의 두께가 20% 이내의 감소율은 P1과 P2 두 프리폼의 경우에 수지가 네크부에 도달하는데 수지의 유동과 온도 분포에 큰 영향을 미치지 않는것으로 판단된다.
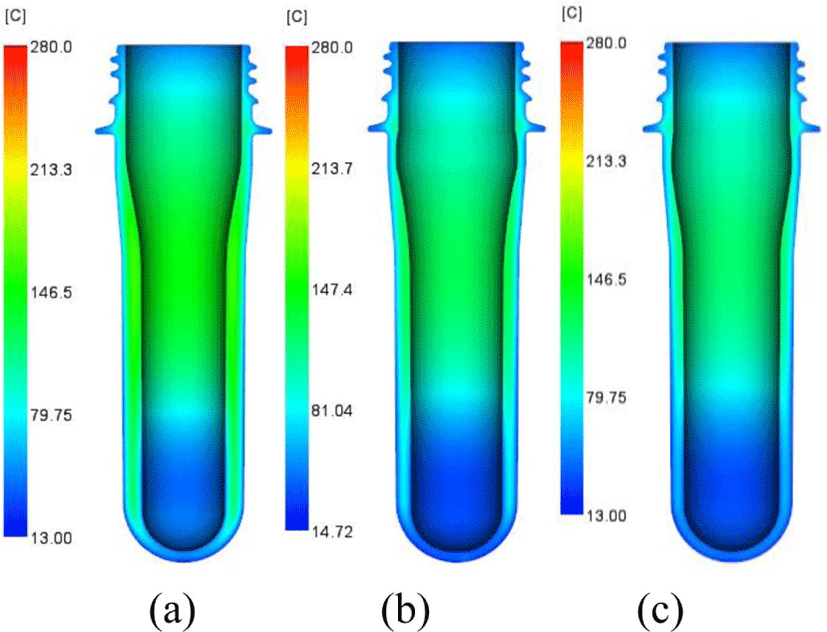
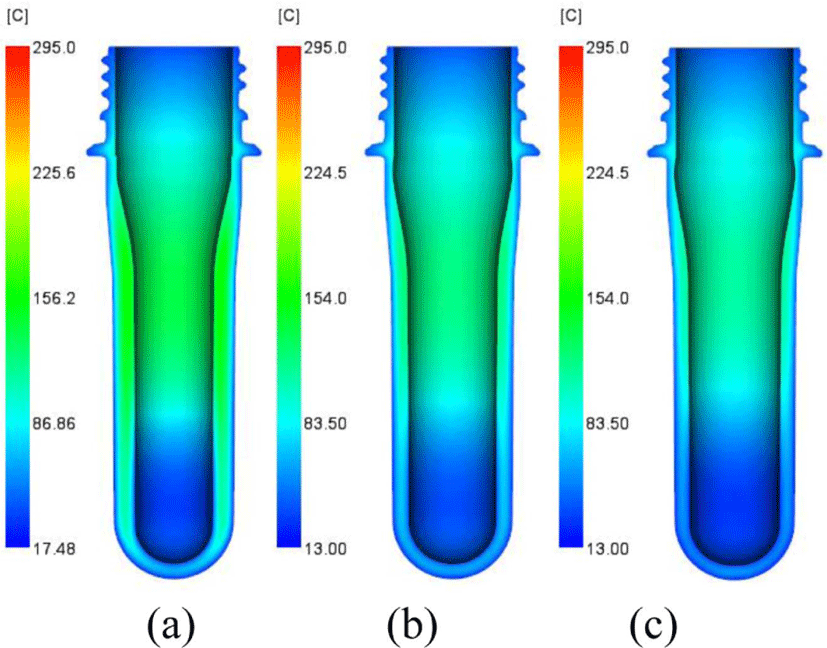
캐비티 내 압력은 Figure 11에 표시한 위치에서 관찰하였다.
사출 성형에서 금형 속의 용융된 수지가 잘 흘러 들어가 캐비티 끝까지 잘 충전이 되었는지 그리고 보압을 잘 받았는지는 양질의 제품을 지속적으로 생산하기 위한 중요한 요소이다. 수지가 들어오는 몸통부와 네크부에서 일어나는 압력 변화를 관찰하고 캐비티 내부의 온도 변화를 관찰하여 프리폼이 충진부터 보압까지 잘 이루어졌는지 비교하였다.
게이트를 통해 용융 수지가 흐르는 순서대로 몸통부(A, B)와 네크부(C)에서 압력을 관찰하였다.
Figure 12와 13은 P1계열과 P2계열의 위치별 압력 프로파일을 나타낸다. 보압이 시작되는 시점에서 압력이 급격히 증가하며 다단 보압을 적용한 P2계열에서는 보압의 크기와 압력이 비례하는 것을 볼 수 있다. 두 종류 프리폼에서 충전 이후에 보압과 동시에 급격히 증가한 압력을 통해 보압의 크기가 적절하다고 판단된다. P1계열의 몸통부 A, B 위치에서 얇아진 프리폼 두께에 따른 압력의 크기와 압력을 받는 시간의 차이는 작았다. 몸통부는 네크부에 비해 비교적 가까운 거리이기에 보압의 영향에서 큰 차이가 없기 때문이다. 하지만 게이트와 멀어진 네크부(C)에서 보압 진행 시 높아진 압력의 유지되는 시간이 줄어드는 것을 확인할 수 있다. 네크부 시작점인 C지점에서 기존 프리폼(P1, P2)과 감량 프리폼P1_15, P1_20, P2_15, P2_20)의 최대 압력값은 유사하나 압력을 받은 시간은 차이나 나타났다. 보압은 프리폼이 충진될 때 금형 안에서 냉각되는 동안 재료의 수축을 보상하기 위해 압력을 가해주는 것을 말한다. 이는 감량으로 인해 두께가 더 얇아진 통로를 따라 들어오는 용융 수지의 고화가 빨라지고 또 단면적이 줄어들어 결국 보압 전달되는 시간이 줄어들기 때문이라고 판단된다.
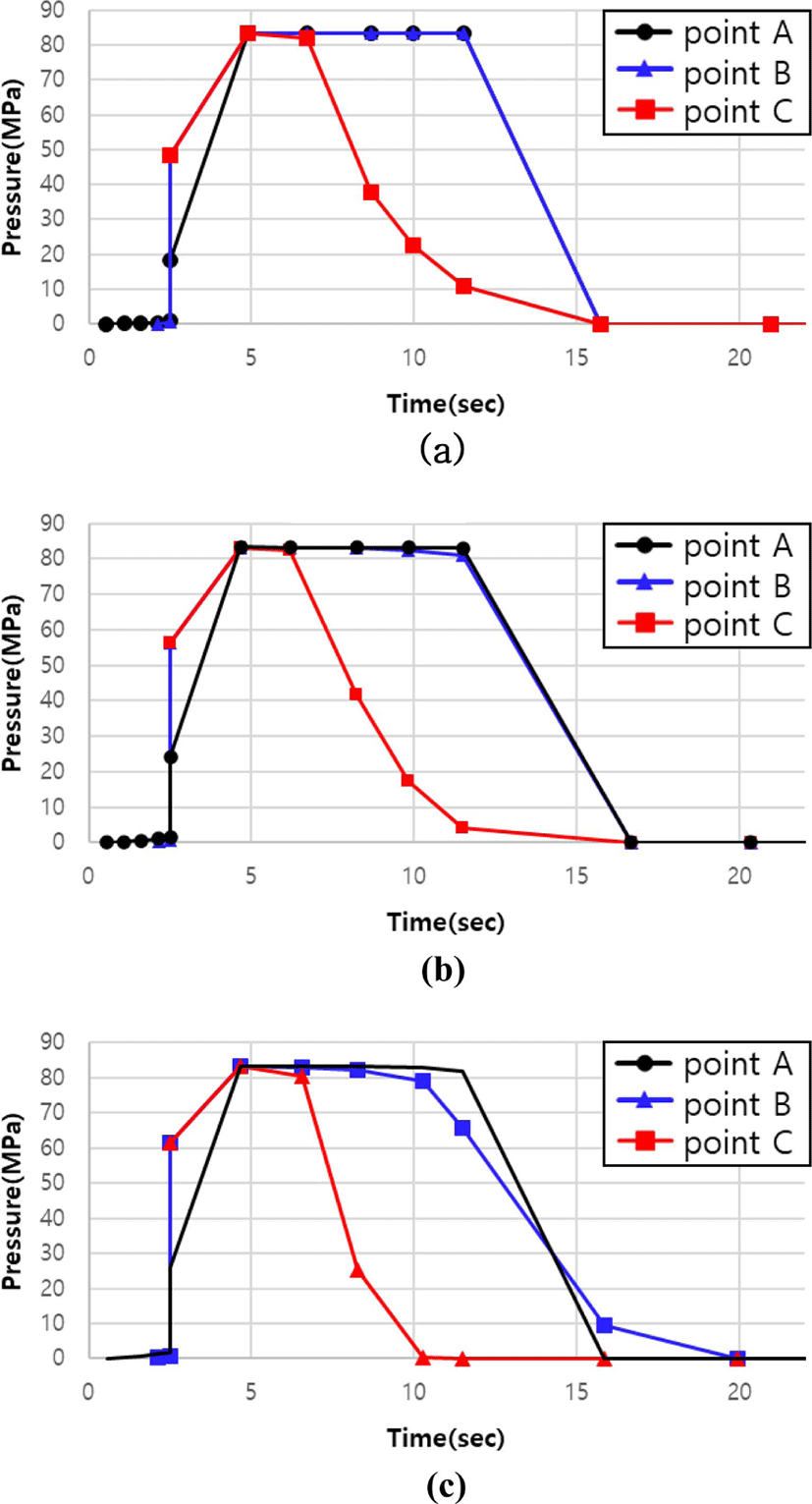
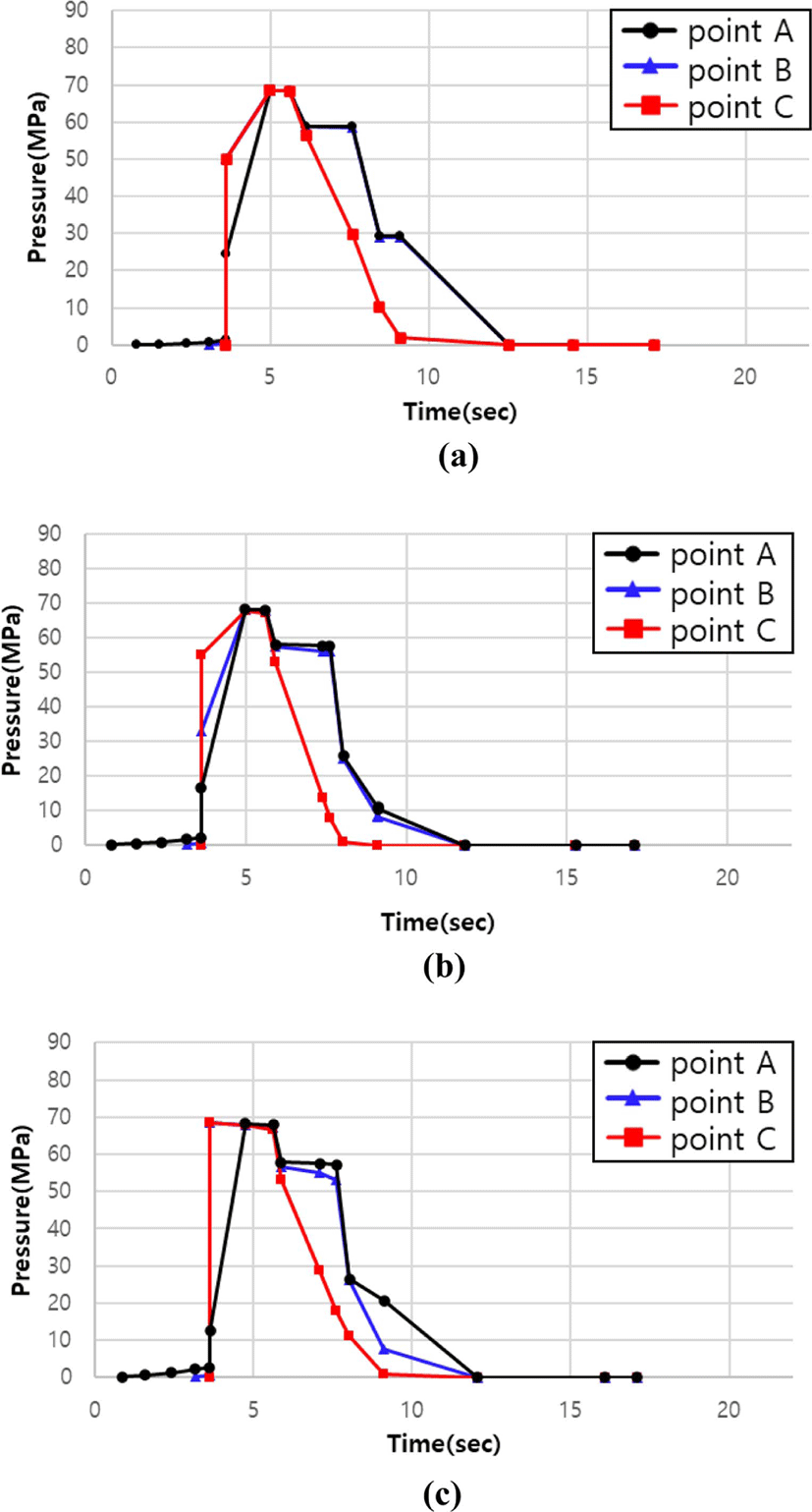
Figure 14는 각 프리폼 사출 시 나타나는 형체력을 보여준다. 감량 프리폼에서 형체력이 증가하여 사출기의 용량이 바뀌게 된다면 기존의 사출기가 아닌 더 용량이 더 큰 사출기를 사용해야 되는 어려움이 생기게 된다.
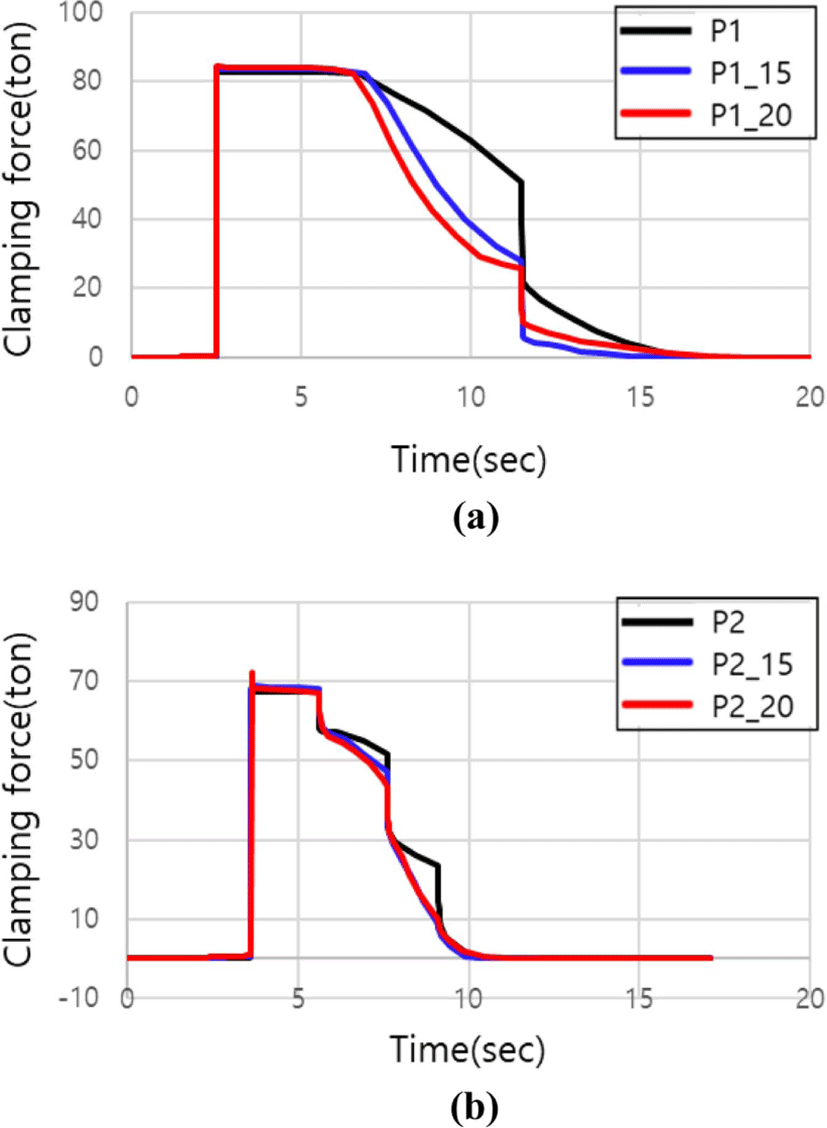
P1계열의 경우 Table 2와 같이 최대 형체력이 기존 모델에서 82.91ton이 되며 15, 20% 감량 시 2%내로 증가한 83.88ton과 84.54ton이 나타났다. P2계열의 P2_20 에서는 P2의 67.56ton 보다 7.13% 증가한 72.38ton의 형체력을 나타낸다. 따라서 보압의 크기가 같고 프리폼 내부의 치수만 줄어든 감량 프리폼은 기존과 비교하여 해석상 사출기 용량에 초과되지 않아 두 프리폼 모두 기존과 같은 사출기로 사출진행이 가능하다.10
Model | Clamping force | Model | Clamping force |
---|---|---|---|
P1 | 82.91ton | P2 | 67.56ton |
P1_15 | 83.88ton | P2_15 | 68.81ton |
P2_20 | 84.54ton | P2_20 | 72.38ton |
Figure 15와 같이 프리폼을 몸통부(body)와 네크부(neck) 두 부분에 바깥쪽에서 내부로 들어가는 방향으로 수축 분포를 확인하였다.
P1계열의 프리폼에서 각각 두 영역의 수축률이 Figure 16과 같이 나타났다. 몸통부와 네크부 수축률을 나타내는 Figure 16(a), (b)를 보면 네크부보다 몸통부에서 확연히 큰 수축률을 보인다. 이 차이는 두 영역의 두께차이로 인해 상대적으로 얇은 네크부의 수축률이 작았다고 판단된다. 몸통부에서는 감량이 진행될 수록 수축률이 작아지는데 이것 또한 감량이 진행될수록 얇아진 두께로 인한 수축률 감소로 판단된다. 네크부에선 감량이 진행될 수록 수축률이 최대 3.5% 증가한다. 이는 네크부의 기존과 감량 프리폼 두께 차이가 없으며 보압 단계에서 감량이 적용되지 않은 P1의 몸통부의 두께가 가장 두껍기 때문에 P1에서 보압을 가장 잘 받아 그만큼 수축을 보상받고 두께가 얇아질수록 상대적으로 보압의 영향을 벗어나 수축률이 커진다고 판단된다. P2계열의 수축률은 Figure 17 (a), (b)와 같이 나타난다. 몸통부의 체적 수축률은 P1과 같은 양상을 보이며 두께가 얇아질수록 수축률이 줄어드는 것을 알 수 있다. 네크부의 체적 수축률은 P1과 마찬가지로 기존과 감량 프리폼이 1.3% 이내의 작은 차이를 보였다. 기존과 감량 프리폼 모두 동일한 조건으로 보압을 적용시켰지만 네크부와 달리 몸통부에서는 두께방향으로의 감량이 진행된 상태이기 때문에 상대적으로 두꺼운 기존 프리폼의 몸통부에서 수축률이 더 크게 나온 것으로 판단된다. 이는 감량 프리폼의 몸통부 수축률이 기존 프리폼 보다 감소하였으므로 수축률 면에선 더 개선되었지만 네크부의 수축률이 미세하게 커지기에 이에 유의해야 한다.11
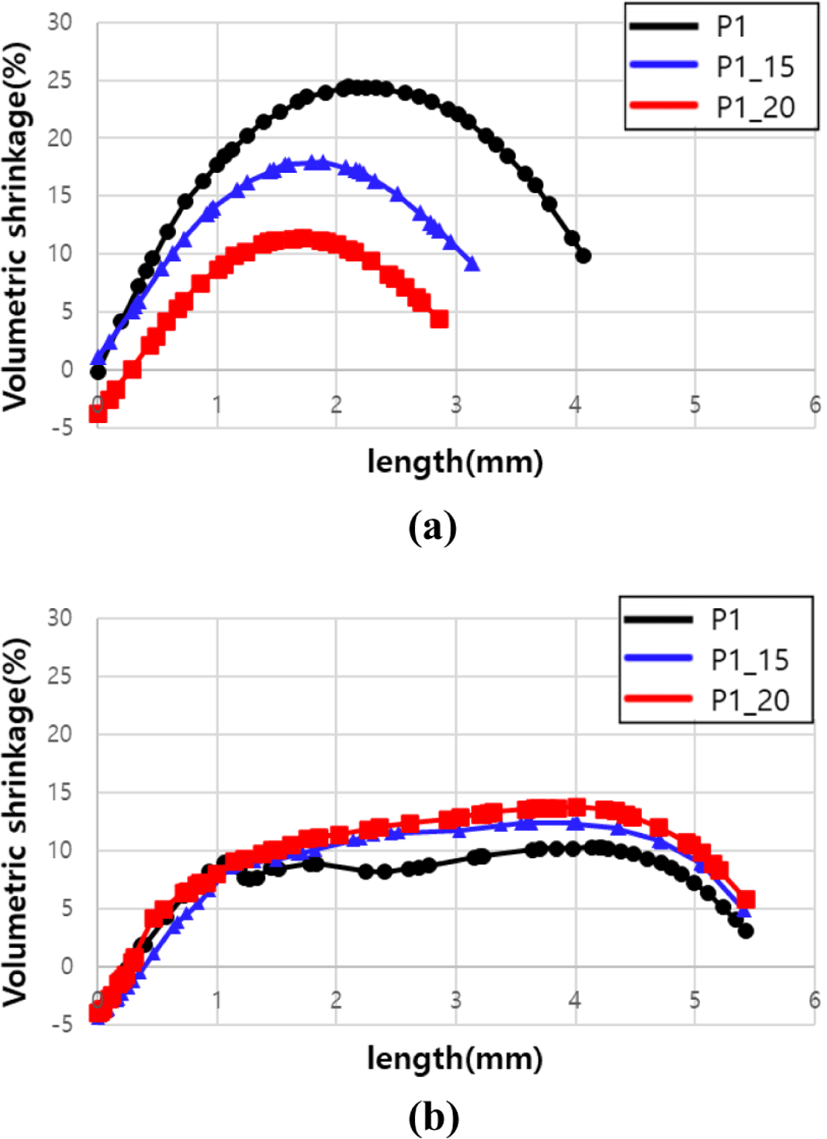
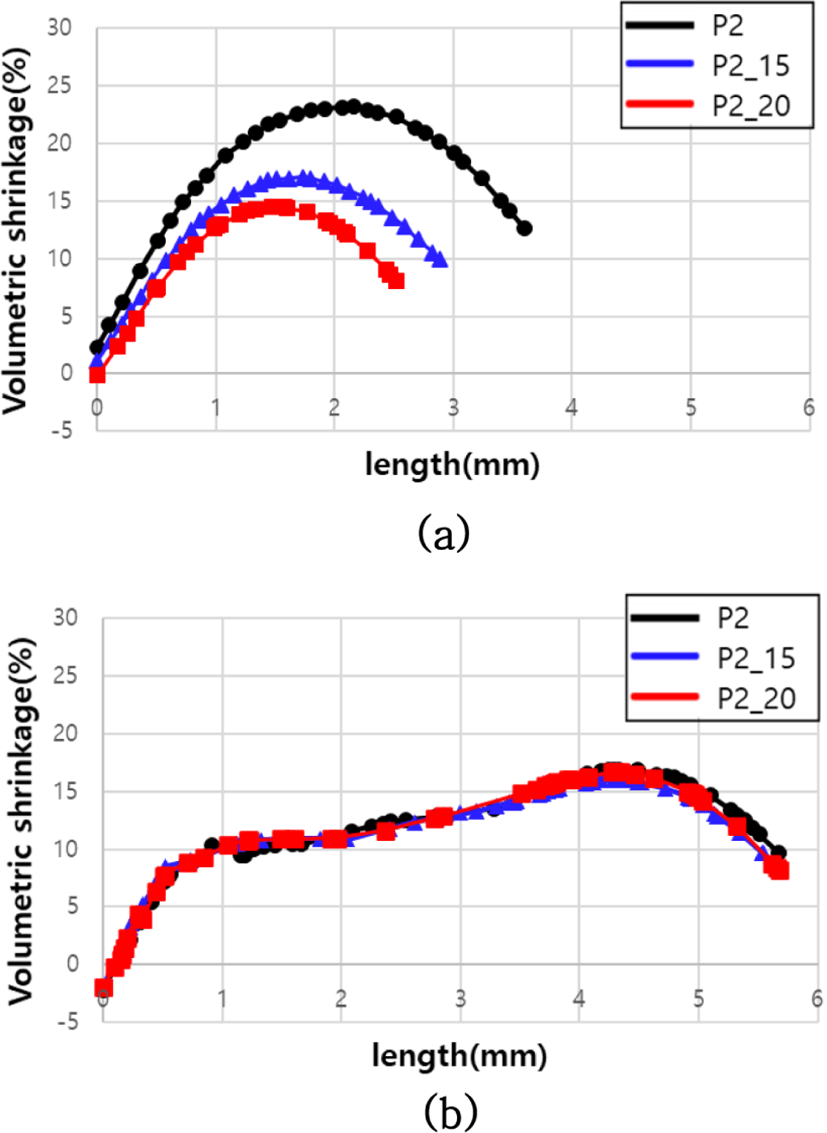
Figure 18과 Figure 19는 P1계열과 P2계열의 변형 분포로 메쉬 절점이 원래 위치에서 이동된 거리이다. 수축은 길이 방향으로 얼마나 줄어들었는지 나타내며 변형은 원래 위치에서 이동한 거리의 개념으로 휨이나 구부러진 특성을 파악할 수 있다. P1계열의 기존 모델 변형 결과를 나타내는 Figure 18(a)를 보면 게이트 부분에서 가장 큰 변형이 관찰된다. 그리고 Figure 18(b), (c)를 보면 기존 모델의 변형 결과와 같은 변형 분포를 보이지만 게이트에서 몸통을 지나 네크부에 이르기까지 전체적인 변형 크기가 감량이 커질수록 감소됨을 볼 수 있다. P1계열의 경우 기존부터 감량에 이르기까지 프리폼 최대 변형 값은 0.5378 mm에서 0.4631 mm, 0.3923 mm로 감소하였다. P1계열과 P2계열 모두 감량이 커질수록 변형 값이 줄어드는 경향을 보였다.
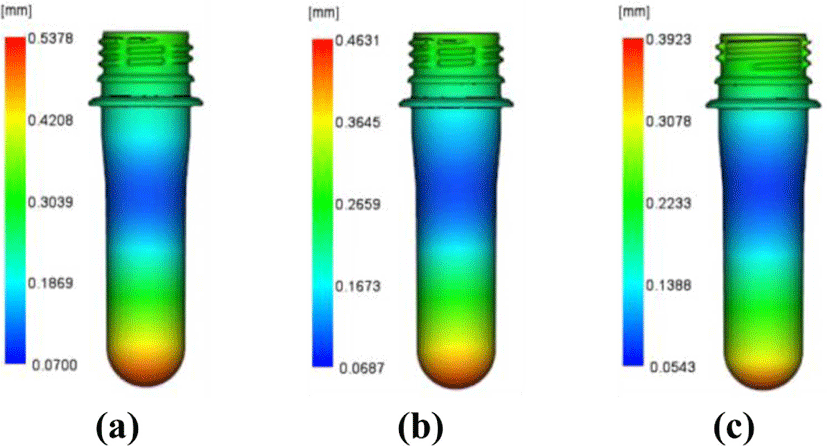
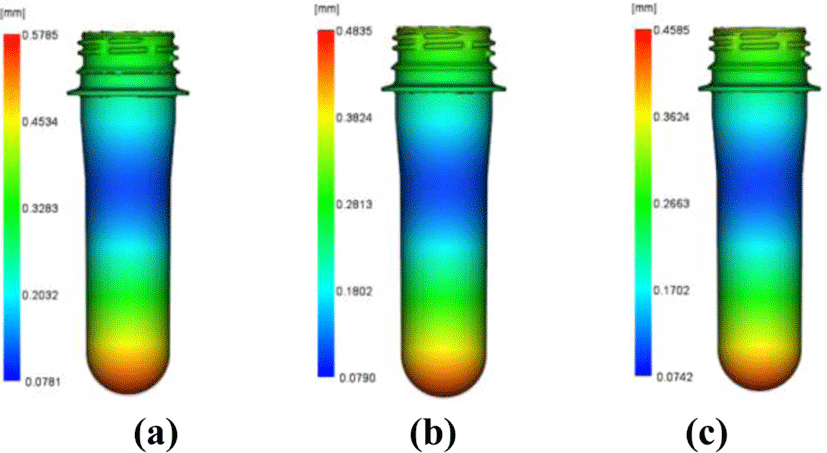
Conclusions
본 연구에서는 기존에 미진했던 프리폼 두께 감소에 대한 연구를 해석적으로 진행하였다. 디자인이 다른 두 프리폼과 각각 15%, 20% 감량한 프리폼의 사출성형 해석을 통해 디자인과 두께 변화에 따른 특성을 동일한 공정조건에서 비교했다. 두 종류 프리폼 모두 얇아진 두께로 인한 미성형이 관찰되지 않았다. 형체력은 전반적으로 감량이 될 수록 높아졌는데 두께가 상대적으로 얇은 P2계열 프리폼에서 최대 증가폭이 나타났으며 프리폼 P2_20의 형체력이 7.13% 증가하였다. 두께가 감소하여 흐름성이 떨어져도 형체력에는 큰 영향을 주지 않았다. 감량 프리폼에서 수축율은 프리폼 P1계열의 몸통부에서 최대 14% 감소를 보였고 네크부에서는 최대 3.5%의 증가를 보였다. 변형은 두 프리폼 모두 감량이 커질수록 줄어들었다. 본 해석을 통해 기존 프리폼의 성형 조건과 사출기의 용량으로 최대 20% 두께가 감소된 프리폼에 적용 가능 할 것으로 판단된다.