Introduction
고무는 대표적인 점탄성(viscoelasticity) 소재로, 소음, 진동, 마찰 등의 에너지 흡수성이 뛰어나 건축, 항만, 기계, 자동차 등의 산업 전반에서 진동감쇄 부품으로 사용된다. 항만용 방현재, 건축용 제진 댐퍼 등은 충격을 흡수함으로써 안전 확보가 가능하여 최근 지진, 산업재해 등의 사회적 이슈와 더불어 수요가 증가하고 있는 추세이다. 대부분의 고무는 NR, SBR, NBR 등과 같은 고무 기재(rubber)와 카본블랙, 실리카로 대표되는 충진제(filler) 및 각종 특성을 부여하는 첨가제(additives) 등으로 구성된 고무 복합재이다.1 일종의 첨가제 형태인 점착부여수지(tackifier)는 로진계열의 천연 수지와 페놀계, 석유계와 같은 합성 수지계로 나눌 수 있으며, 상온에서는 고무 기재와의 접착력을 증진시키고, 고온에서는 가소제 역할을 하는 것으로 알려져 있다.2 고무 기재와 충진제로 대표되는 고무 복합재의 각 구성요소들은 상호작용(interaction) 하고 있으며, 1) 고무 간(rubber–rubber), 2) 충진제 간(filler–filler), 3) 고무–충진제 간(rubber–filler) 상호작용으로 분류할 수 있다. 고무 복합재의 보강성을 향상시키기 위해서는 고무 기재에 충진제 입자를 고르게 분포시켜 고무–충진제 간 상호작용 개선이 필요하다.3,4 분산성 불량으로 고무와 충진제 각각이 응집체를 형성할 경우 응력집중(stress concentration)이 발생하여 균열(crack)이 생성되므로 보강성이 저하된다.5-7 고무 복합재에 하중이 작용하면 그에 상응하는 변형과 다양한 변형 지연이 발생한다. 이 변형 지연은 진동감쇄성에 영향을 주며, 고무 분자 사슬과 충진제 간의 내부 마찰(internal friction)과 이력(hysteresis) 현상에 기인한다. 고무 분자 사슬과 충진제 사이에는 반데르발스(van der Waals) 인력과 같은 결합에너지가 작용하고 있으며, 고무 복합재에 이를 초과하는 하중이 작용할 경우 고무 분자 사슬과 충진제 입자들이 미끄러지며 마찰을 일으킨다. 이 때 충진제의 함량이 높을수록 내부 마찰 및 rubber-filler interaction이 증가하여 진동감쇄성이 개선된다.8 대부분의 진동감쇄 부품은 외부 충격 등에 의해 반복적으로 변형이 발생하는 환경에서 작용한다. 따라서 고무에 일정한 변형을 준 후 다시 원상태로 회복시키는 과정에서 발생하는 이력현상, 즉 히스테리시스(hysteresis)로 고무 복합재의 진동감쇄 특성을 비교할 수 있다. 응력-변형률 곡선으로 측정 가능한 히스테리시스 손실(hysteresis loss)은 하중(loading) 곡선과 제하(unloading) 곡선의 차이에서 관찰되는 면적으로 나타낼 수 있다.9-11 이는 고무 복합재 내부에 열로 축적된 일의 양으로, 에너지 방출의 원인이 된다. 충진제가 함유된 고무복합재는 반복적인 하중이 작용할 경우, 초기 분자구조가 재배치되면서 응력이 연화되는 뮬린스 효과(Mullins effect)가 나타난다.12,13 따라서 히스테리시스를 측정할 경우 응력–변형률이 안정화될 때 까지 일정 변형률 구간에서 하중–제하의 반복과정이 필요하다. 또한 고무 복합재의 진동감쇄 특성은 동적 기계적 분석(Dynamic mechanical analysis, DMA)으로도 분석이 가능하며, 손실탄젠트(loss tangent, tan δ)는 손실 탄성률(E'', loss modulus)과 저장 탄성률(E', storage modulus)의 비율로 재료의 점탄성적 거동을 나타내는 파라미터이다. 손실탄젠트 값이 높을수록 감쇄 특성이 우수하고, 0.3이상(tan δ > 0.3)인 온도 범위를 유효 감쇄 온도 범위(effective damping temperature range)라 하며, 이 범위에서 진동감쇄가 효과적으로 일어난다고 알려져 있다.2,14,15 본 연구에서는 석유수지가 NR 탄성 복합재의 진동감쇄 특성과 제반 특성에 미치는 영향을 히스테리시스 손실 특성, 동적 기계적 분석, 모폴로지 및 기계적 강도 분석을 통하여 비교 분석하였다.
Experimental
Matrix로 사용된 NR (Natural rubber)은 SVR (Standard vietnamese rubber) 10을 사용하였고, 충진제로는 카본블랙 N220을 사용하였다. 석유 수지는 Kolon Industries의 Hikotack P-90(비중: 1.07, 연화점: 98°C)을 사용하였다. 아민계 산화방지제 RD (2,2,4-trimethyl-1,2-dihydroquinoline)와 3C (N-isopropyl-N-phenyl-p-phenylenediamine)를 사용하였고, aromatic계 프로세스 오일 A-2를 사용하였다. 가교시스템은 conventional vulcanization (CV) 시스템을 적용하였으며, 황(sulfur)과 설펜아마이드(sulfenamide) 계열의 촉진제인 CBS (cyclohexyl-2-benzole sulfonamide)를 적용하였다. 가교활성제는 zinc oxide (ZnO)와 stearic acid를 사용하였다.
NR 탄성 복합재는 tangential rotor로 구성된 3.0L kneader (Moriyama社, Japan)와 8-inch open roll mill(풍광기계, Korea)을 사용하여 두 단계에 걸쳐 CMB (Carbon black masterbatch)와 FMB (Final master batch)를 제조하였다. 1단계에서는 NR 탄성 복합재를 fill factor: 0.85, rotor speed: 25 rpm의 가공조건을 적용하여 kneader에서 혼련시켰다. NR을 1분 동안 소련시켜 가소성을 부여한 후 첨가제(ZnO, Stearic acid, 산화방지제)를 투입하여 30초 배합한 후 카본블랙과 프로세스 오일을 5회 나누어 투입하여 CMB를 제조하였다. 2단계는 open roll mill을 사용하여 CMB와 가교제 및 촉진제(Sulfur, CBS)를 혼합하여 FMB를 제조하였으며, 작업 시 발생하는 열에 의한 스코치를 방지하기 위해 10분 내에 혼합을 완료하였다. 본 연구에서 제조한 NR 탄성 복합재의 조성을 Table 1에 나타내었다. 석유수지 첨가 및 함량이 NR/카본블랙 NR 탄성 복합재에 미치는 영향을 관찰하기 위하여 석유수지를 각각 0~20 phr로 변량하여 첨가하였고, VDR-1~4로 표기하여 평가하였다.
제조가 완료된 NR 탄성 복합재의 가공성은 mooney viscometer (DMV-200C, 대경정밀, Korea)를 이용하여 100°C에서 시편을 1분간 예열하고 4분간 시험한 후 점도계에 나타난 토크값(ML1+4)을 측정하였다.
NR 탄성 복합재의 가황특성은 moving die rheometer (JIS K63002-2, Nichigo shoji Co., Ltd, Korea)를 이용하여 온도 160°C 조건으로 20분간 시편에 가해지는 torque, scorch time (t10) 및 최적가황시간(t90)을 측정하였다.
쇼어경도는 KS M 6518에 의거하여 2 mm정도 두께의 평평한 시트 형태 가황물 3장을 적층하여 6 mm 이상 두께의 시험편을 제작하였다. A형 듀로미터 경도계를 사용하여 시험편 위의 다른 위치에서 5회 경도를 측정하고 최대/최소값을 제외한 평균값으로 구하였다. 인장시험은 KS M 6518에 의거하여 시트형태의 가황물을 아령(dumb-bell) 모양의 시편(평행부분의 너비: 5 mm, 평행부분의 길이: 20 mm, 평행부분의 두께: 2 mm, 눈금 사이의 거리: 20 mm)으로 제작하고, 만능시험기(Universal testing machine, model : Instron 3345, Instron社, USA)를 이용하여 상온에서 500 mm/min의 속도로 모듈러스, 인장강도, 파단 신장률을 측정하였다. 영구압축줄음율 시험 역시 KS M 6518에 의거하여 두께(12.70±0.13)mm, 지름 약 29.0 mm의 원기둥형 시편을 스페이서를 사용하여 시편 두께의 25%로 압축한 후 70°C에서 22시간 열처리하였다. 열처리가 끝난 시편은 바로 압축장치에서 꺼내어 30분간 실온에 방치한 후 다음 식을 이용하여 구하였다.
t0 : 시험편의 원두께(mm)
t1 : 압축장치에서 꺼내고 30분 후의 시험편 두께(mm)
t2 : 스페이서의 두께(mm)
이 때 각 5개의 시험편에 대하여 시험을 하였으며 계산된 각각의 측정값은 최대/최소값을 제외한 평균값으로 분석하였다.
NR 탄성 복합재의 모폴로지는 FE-SEM (field emission scanning electron microscope, JEOL社, JSM-6701F)를 이용하여 분석하였다. 시험편은 액체질소에서 충분히 냉각시킨 후 순간적으로 파괴시켜 얻어진 파단면을 gold coating한 후 관찰하였다.
동적 기계적 특성은 KS M 6721-1에 준하여, DMA Q 800 (TA Instruments, USA)를 사용하여 측정하였다. Strain-sweep 시험은 변형률(strain) 0.1%~10%, 주파수(frequency) 10 Hz, 상온 조건으로 측정하였고, frequency-sweep 시험은 주파수 0.1~100 Hz, 변형률 1%, 상온 조건으로 측정하였다. Temperature-sweep 시험은 –80~100°C(3°C/min)의 온도 범위, 변형률 0.1%, 주파수 10Hz의 조건으로 측정하였다. 3가지 시험 모두 tension mode의 조건에서 저장탄성률, 손실탄성률, 손실탄젠트를 측정하여 NR 탄성 복합재의 점탄성(viscoelastic properties) 특성을 비교 및 분석하였다.
직경 30 mm, 높이 약 12.5 mm의 원기둥 형태의 시편을 준비하여 만능시험기(Universal testing machine, model: DUT-500CM, 대경엔지니어링, Korea)를 사용하여 측정하였다. 상온에서 5mm/min의 속도로 Mullins effect를 고려하여 응력-변형률이 안정화될 때까지 시편 두께의 50%(약 6.25 mm)를 5회 반복 측정하였다.
NR 탄성 복합재의 반발탄성은 KS M ISO 4662의 트립소미터(tripsometer) 방법으로 지름 약 45 mm이고, 두께가 2 mm인 원판을 3장 겹친 시험편으로 측정하였다. Mullins effect를 고려하여 시험편에 3회 이상의 충격을 가하고, 3회의 탄성값으로 비교 및 분석하였다.9
Results and Discussion
본 연구에서 제조한 FMB 컴파운드의 100°C 무니(Mooney) 점도 측정 결과를 Table 2에 나타내었다. 무니점도는 석유수지의 함량이 증가할수록 감소하는 경향이 관찰되었다. 석유수지가 첨가되지 않은 VDR-1의 무니점도는 79.7MU이며, 석유수지가 20phr 첨가된 VDR-4는 54.8MU로 무니점도가 약 31.2% 감소하였다. 이는 연화점이 100°C 이하이고, 분자량이 약 1,200 g/mol로 저분자량인 석유수지에 의한 NR 탄성 복합재의 가소화로 인하여 NR 탄성 복합재의 가공성 및 카본블랙의 분산성이 향상되기 때문으로 사료된다.
VDR-1 | VDR-2 | VDR-3 | VDR-4 | |
---|---|---|---|---|
Mooney viscosity ML1+4(100°C) | 79.7 | 73.0 | 67.4 | 54.8 |
석유수지 함량에 따른 NR 탄성 복합재의 가황특성 분석 결과를 Figure 1과 Table 3에 나타내었다. 석유수지의 첨가량이 증가함에 따라 1) Δtorque 감소, 2) 스코치 시간 증가, 그리고 3) 최적가황시간 증가 경향을 나타내었다. 석유수지가 첨가되지 않은 VDR-1의 Δtorque, 스코치시간, 그리고 최적가황시간은 각각 1.281, 1.94분, 그리고 3.75분으로 나타났다. 반면 석유수지가 20phr 첨가된 VDR-4의 Δtorque, 스코치시간, 그리고 최적가황시간은 각각 0.839, 2.16분, 그리고 3.98분으로 나타났다. 이러한 석유수지 첨가에 따른 가교도 감소, 스코치시간 및 최적가황 시간의 증가는 저점도의 석유수지가 가교제나 가교촉진제 일부를 둘러싸는 현상(covering effect)에 의한 반응 지연 때문인 것으로 사료된다.14
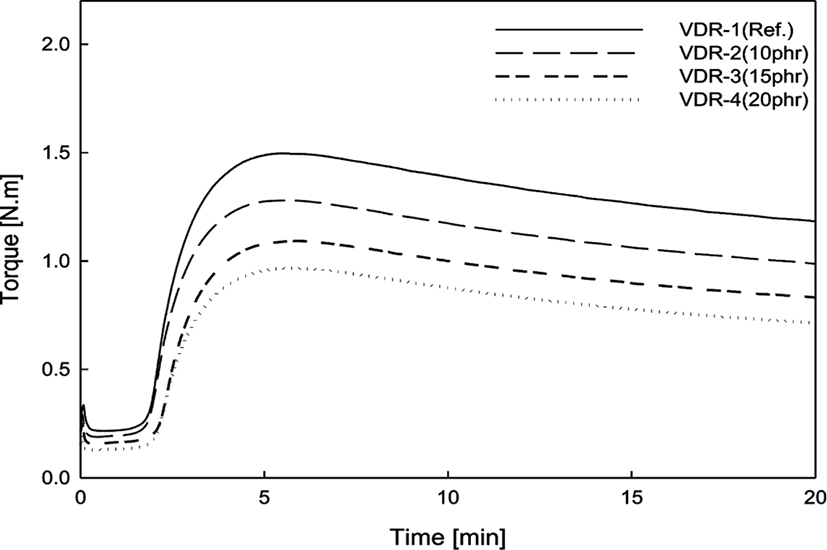
VDR-1 | VDR-2 | VDR-3 | VDR-4 | |
---|---|---|---|---|
ML (N.m) | 0.216 | 0.188 | 0.158 | 0.128 |
MH(N.m) | 1.497 | 1.281 | 1.093 | 0.967 |
ΔTorque (N.m) | 1.281 | 1.093 | 0.935 | 0.839 |
t10 (min) | 1.94 | 1.91 | 2.10 | 2.16 |
t90(min) | 3.75 | 3.71 | 3.95 | 3.98 |
석유수지 함량에 따른 기계적 강도 측정 결과를 Table 4에 나타내었으며, NR 탄성 복합재의 stress–strain curve와 영구압축줄음률을 Figure 2와 Figure 3에 각각 나타내었다. 석유수지의 함량이 증가함에 따라, 경도, 100% 인장 모듈러스, 300% 인장 모듈러스 그리고 인장강도는 감소하는 경향을 나타내었다. 이에 반하여 신장율과 영구압축줄음율은 증가하는 경향을 나타내었다. 석유수지가 미첨가된 VDR-1과 비교하여 석유수지가 20phr 첨가된 VDR-4는 경도가 12.2% 감소함에 따라, 100% 인장 모듈러스 약 42.1%, 인장강도 약 5.0% 감소하였고, 영구압축줄음율이 약 33.3% 증가하여 기계적 특성 감소가 관찰되었다. 반면, 신장율은 약 26.7% 증가하여, 결과적으로 석유수지 첨가 시 고무 분자 사슬 간 강성(stiffness)이 저하되고 유연성(softness)이 증가하는 것으로 나타났다. 이는 물리적 가소제 역할을 하는 석유수지가 고무 컴파운드의 사슬 내부로 침투하여 각 구성요소를 둘러싸(covering effect) 고무 분자사슬과 카본블랙 간의 계면 상용성(interfacial compatibility)을 개선하지만, NR 고무 대비 green strength가 낮고 저분자량인 석유수지 함량이 증가함에 따라 NR 탄성 복합재의 탄성이 저하되기 때문인 것으로 사료된다.
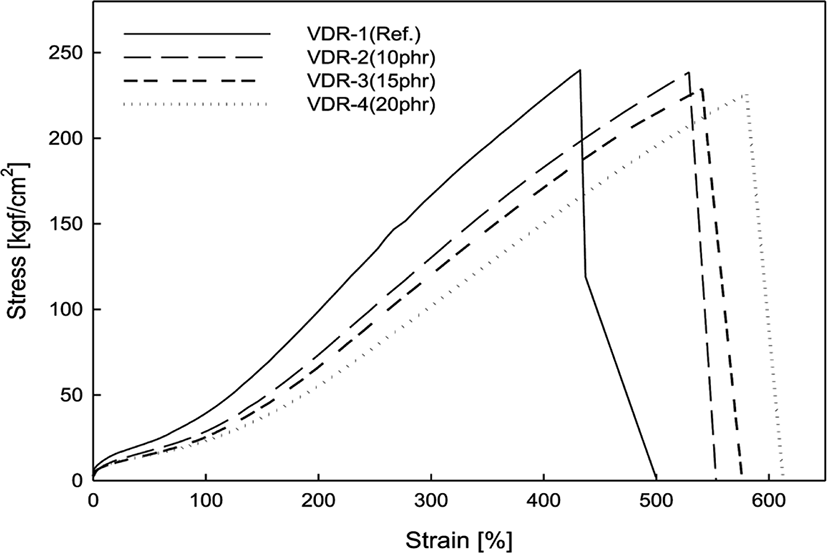
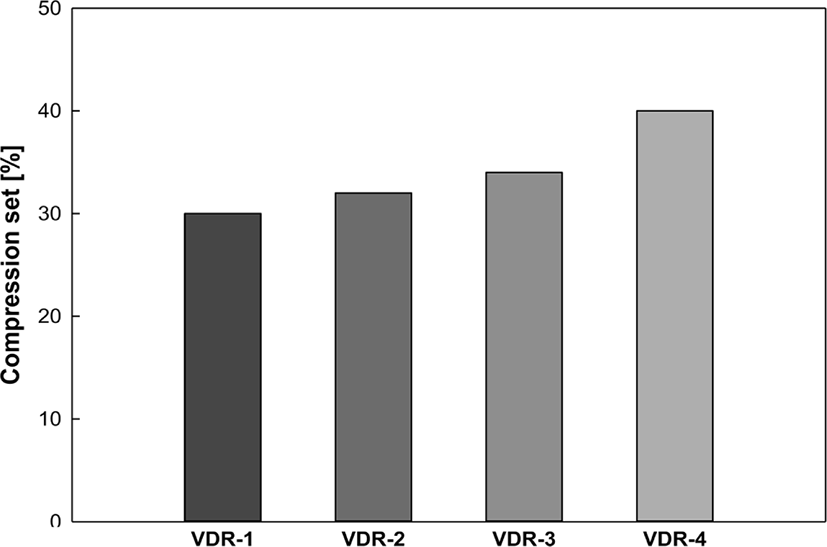
석유수지 함량에 따른 NR 탄성 복합재의 모폴로지를 분석한 결과를 Figure 4에 나타내었다. 석유수지가 첨가되지 않은 VDR-1(Figure 4(a))의 경우 카본블랙 미분산에 의한 직경 25 μm 이상의 응집체(aggregate or agglomerate)가 다수 관찰되나, 석유수지가 증량될수록 파단면에서 관찰되는 카본블랙 입자가 감소하였다. 이러한 현상은 점착부여수지가 고무 분자사슬과 카본블랙 입자를 둘러싸면서 고무 분자사슬에는 점도를 부여하고(viscous effect), 충진제는 캡슐화(encapsulated)한 것으로, 고무 분자사슬과 카본블랙 간의 젖음성(wetting) 및 결합력(rubber-filler interaction) 향상에 의한 분산성 개선으로 사료된다.2,14 따라서 석유수지 첨가 및 증량이 고무 분자사슬과 카본블랙 입자의 계면 상용성 및 분산성 개선 효과가 있는 것으로 판단되며, 이러한 결과는 NR 탄성 복합재의 무니점도 결과와도 일치하였다.
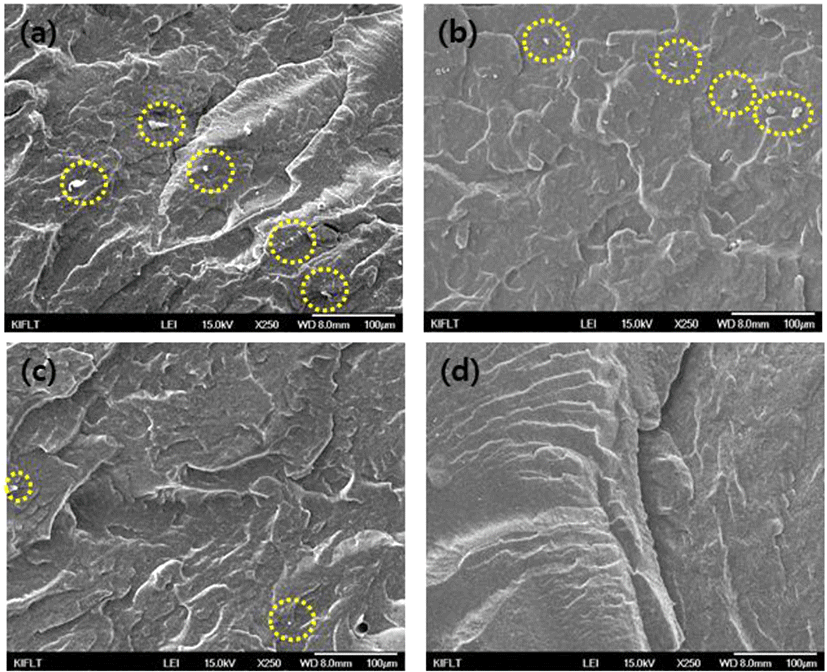
NR 탄성 복합재의 변형률에 따른 DMA 분석 결과를 Figure 5에 나타내었다. Figure 5(a)에서 저장탄성계수는 변형률 증가 및 석유수지 함량 증대에 따라 감소하였다. 이는 1) 변형률이 증가할수록 측정 조건이 가혹해져 NR 탄성 복합재의 회복력이 저하되고, 2) 물리적 가소제로 작용하는 석유수지가 증량됨에 따라 NR 탄성 복합재의 가소화가 가속되어 저장탄성계수가 감소하는 것으로 사료된다. 또한 Figure 5(b)의 손실 계수 역시 석유수지 함량이 증가하고, 변형률이 증가함에 따라 감소하는 경향을 나타내었다. 특히, 변형률 1% 이상의 고변형률 영역에서 크게 감소하는 경향을 나타내었고, 변형률 1% 미만의 저변형률 영역에서는 낮은 감소율을 나타내었다. 이는 변형률이 크게 증가할 경우, 석유수지 첨가에 따른 에너지 손실 및 진동감쇄가 크게 증가하기 때문인 것으로 사료된다. 고분자 물질의 내부 마찰 또는 감쇄(damping) 특성을 나타내는 파라미터 중 하나인 tanδ는 Figure 5(c)에서 나타난 바와 같이 변형률이 증가함에 따라 감소하고, 석유수지 함량이 증가함에 따라 증가하는 경향을 나타내었다. 석유수지를 20phr 첨가한 VDR-4은 tan δmax가 약 0.45로, 석유수지를 첨가하지 않은 VDR-1의 0.37 대비 약 21.6% 증가하였다. 이는 석유수지 첨가로 인하여 반복 변형에 대한 진동 감쇄 특성이 향상된 것으로 사료된다.
석유수지 함량에 따른 NR 탄성 복합재의 주파수에 따른 DMA 분석 결과를 Figure 6에 나타내었다. Figure 6(a)에서 저장탄성계수는 주파수 증가 및 석유수지 증량에 따라 감소하는 경향을 나타내었다. 이는 앞서 언급한 Figure 5(a)의 변형률에 따른 분석 결과와 유사하게 관찰된다. Figure 6(b)의 손실 계수 역시 석유수지 함량이 증가하고, 주파수가 증가함에 따라 감소하는 경향을 나타내었다. 주파수에 따른 손실계수는 50 Hz 미만의 저주파수 영역에서는 낮은 감소율을 나타내었으나, 50 Hz 이상의 고주파수 영역에서 일정한 경향이 관찰되지 않을 만큼 큰 폭으로 변화하였다. 이는 주파수가 50 Hz 이상으로 크게 증가할 경우, 고무 사슬 절단과 같은 비가역적인 변화가 일어나 고무탄성을 잃은 것으로 사료된다. 따라서 주파수에 따른 tanδ를 나타낸 Figure 6(c)에서 50 Hz 이상의 결과 분석은 신뢰성이 떨어져 제외하고, 50 Hz 미만 영역에서 비교할 경우 석유수지 함량이 증가함에 따라 tanδ도 증가하는 경향을 나타내었다. 이는 석유수지 첨가로 인하여 반복 변형에 대한 진동 감쇄 특성이 증가한 것으로 사료되며, 변형률에 대한 동특성 분석과 동일한 결과를 나타내었다. 이상의 결과를 바탕으로 유효 감쇠 온도 범위를 파악하기 위해 온도에 따른 DMA 분석을 진행하였고, 그 결과를 Figure 7에 나타내었다. 측정 조건은 분자 사슬 절단과 같은 급격한 특성 변화가 관찰되지 않는 범위인 변형률 0.1%, 주파수 10Hz로 선정하여 측정하였다.
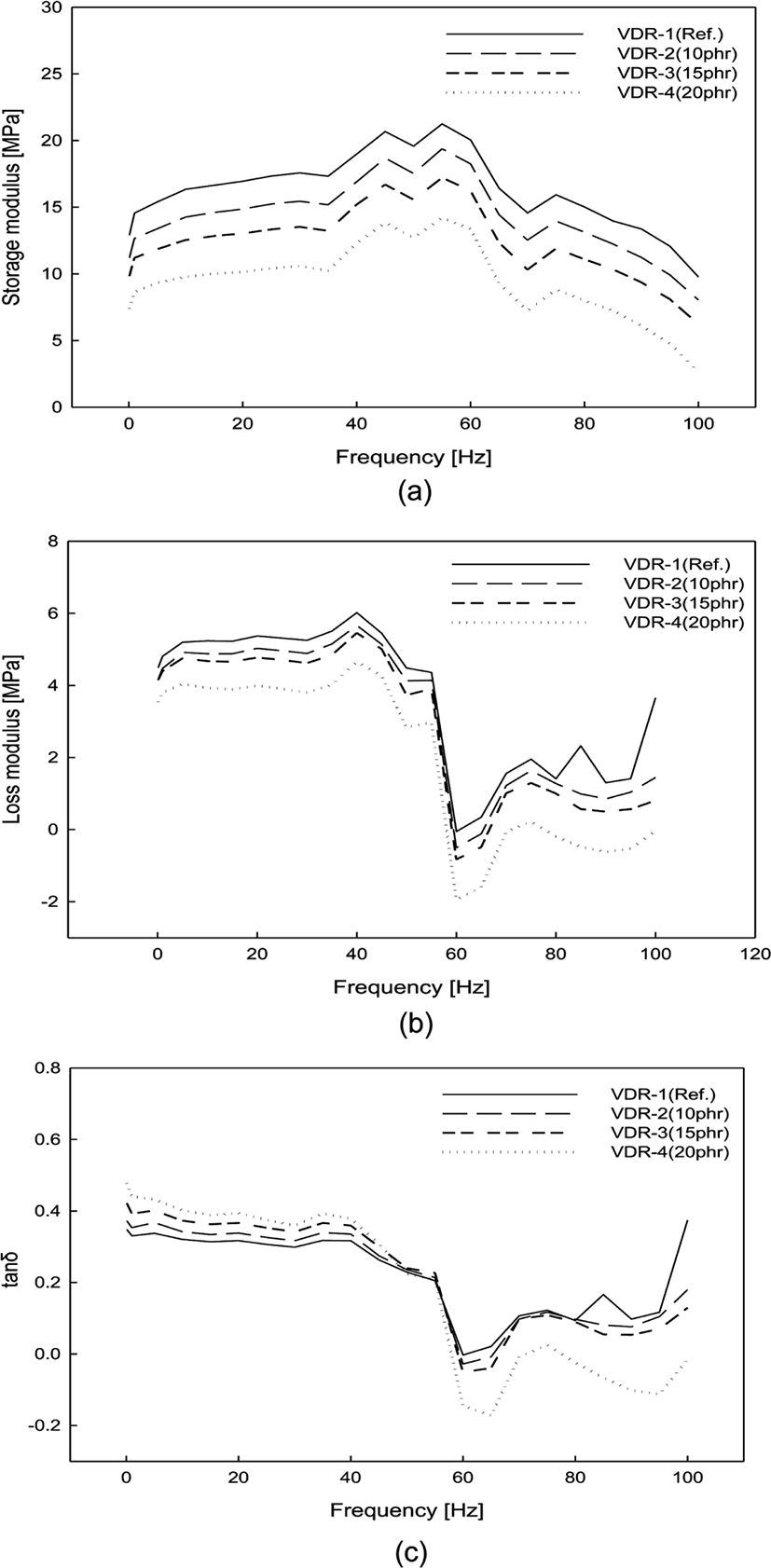
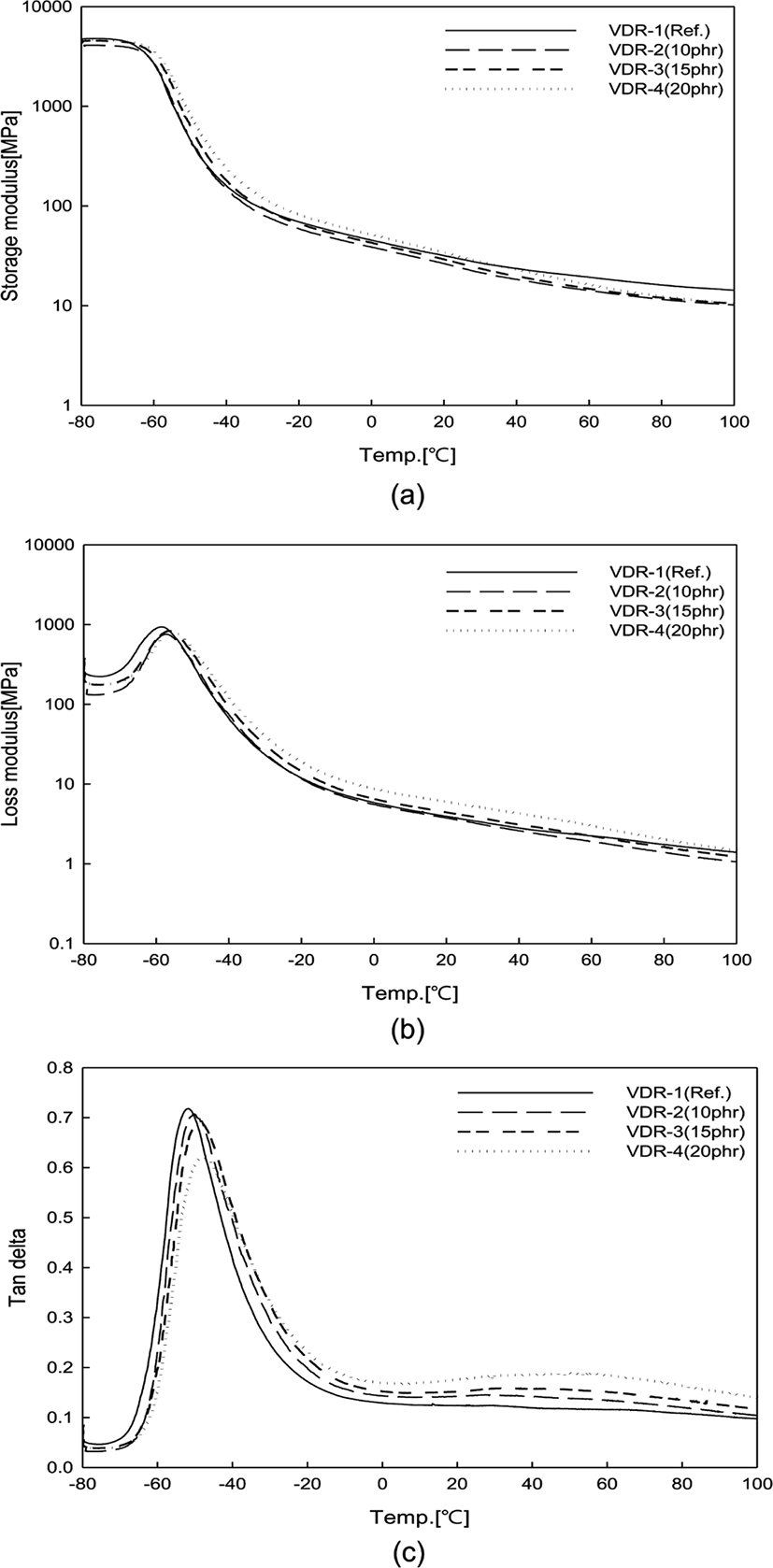
Figure 7(a)의 저장탄성계수와 Figure 7(b)의 손실계수 모두 온도가 증가함에 따라 감소하는 경향을 나타내었다. 이러한 결과는 온도가 높아질수록 NR 탄성 복합재 구성요소들의 운동성(mobility) 증가로 인한 점도 감소에 기인한 것으로 사료된다. Table 5에서 석유수지를 20phr 첨가한 VDR-4의 유효감쇄온도범위(ΔT)가 29.4°C로, 석유수지를 첨가하지 않은 VDR-1 대비 ΔT가 약 11.4% 증가되었다. 반면, tanδ 최대값은 소폭 감소하였는데 이는 석유수지가 증량됨에 따른 가소화 효과로 사료된다.16 온도에 따른 tanδ의 변화를 Figure 7(c)에 나타내었다. Figure 7(a)에서 NR 탄성 복합재의 저장탄성률의 급격한 감소가 관찰되는 온도와 Figure 7(c)에서 석유수지 증량에 따라 tanδ 최대값이 관찰되는 온도가 약 –50°C로 유사하게 관찰되며, 이 지점에서 NR 탄성 복합재의 상(phase)이 변하고 있음을 알 수 있다. 일반적으로 고무와 같은 무정형 고분자의 마이크로브라운 운동(microbrownian motion)이 시작되는 온도를 유리전이온도(Tg)라고 하며, 이 때 에너지 손실률이 가장 크다. 따라서 Figure 7(c)의 tanδ 최대값에서 NR 탄성 복합재의 유리전이온도가 관찰되며, 석유수지가 증량될수록 유리전이온도는 증가하였다. 석유수지가 NR 탄성 복합재 내의 고무 분자 사슬과 카본블랙에 상호 젖음성(wetting)을 부여함으로써 결합력(rubber-filler interaction)을 향상시킨 결과로 사료되며, 이는 앞선 모폴로지 분석 결과에서 석유수지 첨가 시 NR 탄성 복합재의 계면 상용성이 향상되는 결과와도 유사하다.
히스테리시스 손실(hysteresis loss) 5회 측정 결과를 Figure 8에 나타내었고, 히스테리시스 손실율과 반발탄성(resilience) 측정 결과를 Table 6에 나타내었다. 히스테리시스 손실률은 Figure 8(a)의 응력-변형률 곡선에서 하중(loading) 곡선과 제하(unloading) 곡선의 차이에서 관찰되는 면적으로 측정할 수 있다. 석유수지가 첨가되지 않은 VDR-1과 20phr 첨가된 VDR-4의 히스테리시스 손실률은 52.1%에서 60.0%로, 15.2% 증가하였고, 반발탄성은 VDR-1이 41%, VDR-4가 26%이므로 약 36.6% 감소하였다. 이는 앞서 동적기계적 특성 분석에서 언급한 바와 같이, 석유수지의 증량으로 NR 탄성 복합재의 결합력(rubber-filler interaction)이 향상되어 점성적인 변형 거동이 증가한 결과이며, 공급된 에너지는 NR 탄성 복합재 내부에 열로 축적 및 방출되므로 진동감쇄 특성이 우수해지는 것으로 사료된다. 이상의 동적 기계적 특성, 히스테리시스 손실 특성 및 반발탄성 분석 결과를 통해 NR 탄성 복합재의 진동감쇄 특성을 비교한 결과, 석유수지가 증량됨에 따라 유효감쇠 온도범위(tanδ>0.3)가 넓어지고, 히스테리시스 손실률 증가 및 반발탄성이 감소하였다. 따라서, NR 탄성 복합재의 석유수지가 증량됨에 따라 진동감쇄 특성이 개선됨을 확인하였다.
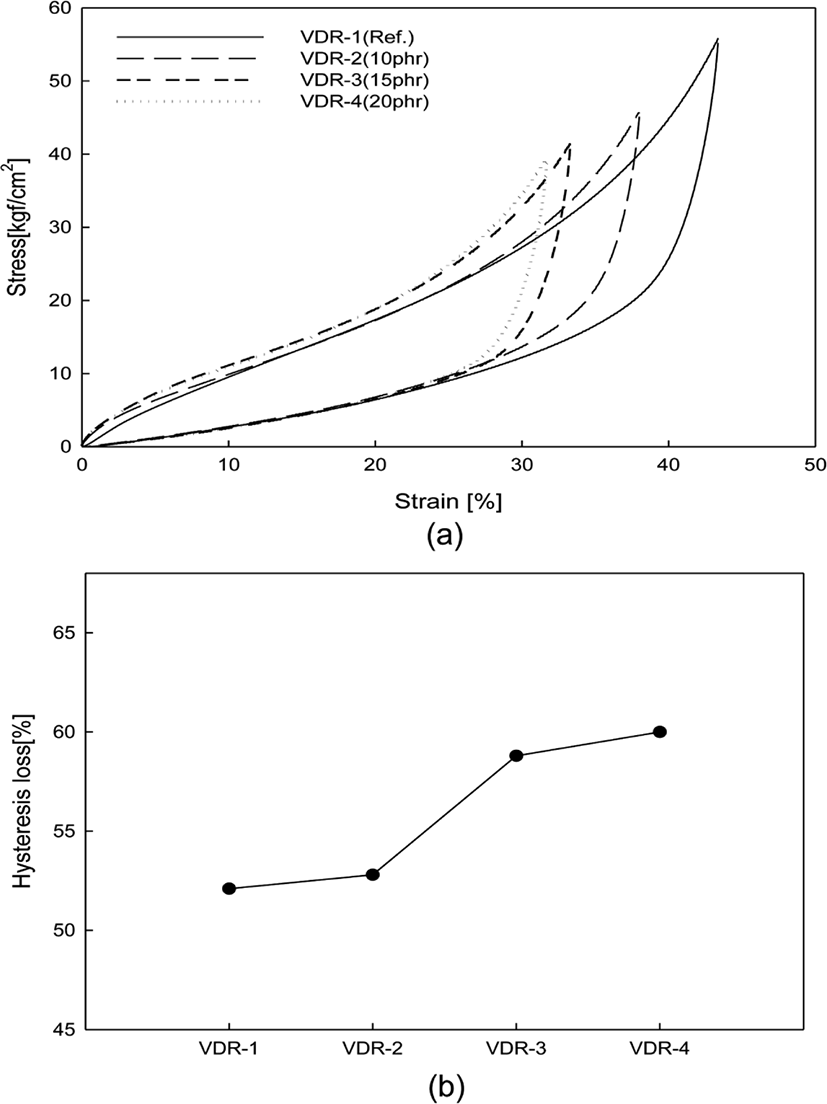
VDR-1 | VDR-2 | VDR-3 | VDR-4 | |
---|---|---|---|---|
Hysteresis loss [%] | 52.1 | 52.8 | 58.8 | 60.0 |
Resilience [%] | 41 | 39 | 28 | 26 |
Conclusions
본 연구에서는 석유수지의 함량에 따른 NR 탄성 복합재의 진동감쇄 특성을 비롯한 제반 특성을 관찰하였다. 석유수지가 증량됨에 따라 NR 탄성 복합재의 가소화가 증가하여 무니점도 및 가교도(Δtorque) 그리고 기계적 특성이 감소하는 경향을 나타내었다.
NR 탄성 복합재의 모폴로지 분석 결과, 석유수지가 증량됨에 따라 파단면에서 관찰되는 카본블랙 응집체(aggregate or agglomerate)가 감소하여 계면 상용성(interfacial compatibility) 및 분산성이 향상되었다.
동적 기계적 특성 분석 결과, 석유수지가 20phr 첨가됨에 따라 효과적으로 진동이 감쇄되는 온도범위(effective damping temperature, ΔT = tan δ > 0.3)가 약 11.4% 증가하였고, 히스테리시스 손실률은 15.2% 증가하였으며 반발탄성은 36.6% 감소하여 진동감쇄 특성이 개선됨을 확인하였다.
따라서 석유수지 함량이 증대됨에 따라 NR 탄성 복합재 내의 카본블랙 분산성 및 rubber-filler interaction이 증가되어 진동감쇄 특성이 향상되었다.