Introduction
Significant efforts have been made to increase the fuel efficiency and abrasion resistance of truck and bus radial (TBR) tires owing to the recent environmental regulations and emergence of electric vehicles.1 Therefore, the partial replacement of carbon black used in TBR tire treads with a combination of silica and silane coupling agents to achieve increased fuel efficiency has attracted increased research attention.2-4 However, because the TBR tire treads are manufactured using NR as the base rubber, the resulting rubber compounds exhibit low silica–SCA–NR interactions owing to the interference of NR proteins and lipids. This results in poor abrasion resistance compared to compounds prepared using carbon black limit the application of silica in TBR tire tread compounds.5,6
In addition, the recent emergence of autonomous driving technology has led to the expectation of automated cargo trucks to be operated 24 h a day. This poses another challenge for TBR tires that it would cause the migration of oils added as processing aids, thereby causing hardening of the tire material.7,8 To overcome this problem of oil migration, investigations concerning the use of liquid rubber as a new processing aid have recently gained traction. Similar research has been actively conducted considering PCR tires as the target application. Previous studies have confirmed the realization of processability improvement and resolution of oil-migration issues when using liquid rubber as the processing aid.9-11 However, no previous studies have been reported concerning the application of liquid rubber to TBR tire treads, and no quantitative analysis of liquid rubber effects on the vulcanizate structure of tread compounds has been performed.
The reduced filler–rubber interactions of the silica filled NR compounds can be improved by introducing epoxide groups to NR, thereby promoting the chemical interactions between the silica hydroxyl and epoxide groups. This has been reported to improve the abrasion resistance of TBR tires.12 Therefore, in this study, E-LqIRs, which act as coupling agents and processing aids, were applied to silica filled NR compounds for not only improving the problem associated with declining filler–rubber interactions but also solving the oil-migration problem. Furthermore, the effect of the E-LqIR molecular weight on the vulcanizate structure of compounds has been quantitatively analyzed by the vulcanizate structure analysis.
Materials and Experimental Methods
All the chemicals were purged with nitrogen. Cyclohexane (99%, Samchun Chemical Co., Seoul, South Korea) was used as the organic solvent, and n-butyllithium (2.0 mol/L in cyclohexane, Sigma–Aldrich Corp., Seoul, South Korea) was the anionic initiator. Isoprene (99%, Samchun Chemical Co., Seoul, South Korea) was used as a monomer, and tetrahydrofuran (THF; 99%, Duksan General Chemical Co., Seoul, Korea) was used as a polar modifier to increase the reaction rate. In addition, n-octyl alcohol (99%, Yakuri Pure Chemicals Co. Ltd., Kyoto, Japan) was used as the termination agent.
LqIR was converted to the epoxidized form, i.e., E-LqIR, by using hydrogen peroxide (30 wt% in H2O, Sigma–Aldrich Corp., Seoul, South Korea) and formic acid (98%, Sigma–Aldrich Corp., Seoul, South Korea).
NR (Standard Vietnamese Rubber SVR-10, dirt content = 0.1 wt%; Astlett Rubber Inc., Oakville, ON, Canada) was used as the base rubber. Silica (Ultrasil 7000 GR, Evonik Industries AG, Essen, Germany), with a Brunauer–Emmett–Teller surface area of 160-175 m2/g, was used as the filler. Bis[3-(triethoxysilyl)propyl]-tetrasulfide (TESPT, Si-69; Evonik Korea Ltd., Seoul, Korea) was used as the silane coupling agent. ZnO and stearic acid (Sigma–Aldrich Corp., Seoul, South Korea) were used as activators, and N-(1,3-dimethyl butyl)-N-phenyl-p-phenylenediamine (6PPD, Kumho Petrochemical Co., Daejeon, Korea) was used as the antioxidant. Sulfur (Daejung Chemicals and Metals Co., Siheung, Korea) was used as the crosslinking agent. N-cyclohexylbenzothiazyl-2-sulfenamide (CBS; 98%, Tokyo Chemical Industry Co., Ltd., Tokyo, Japan) and 1,3-diphenylguanidine (DPG; 98%, Tokyo Chemical Industry Co., Ltd., Tokyo, Japan) were used as the curing accelerators. N-(cyclohexylthio)phthalimide (PVI, Shandong Yanggu Huatai Chemical Co., Ltd., Liaocheng, China) was used as the prevulcanization inhibitor.
Molecular weight and molecular weight distribution were measured using gel permeation chromatography (GPC) system (Shimadzu, Kyoto, Japan). The GPC system consisted of a solvent delivery unit, reflective index detector, and three types of Styragel columns: HT 6E (10 μm, 7.8 mm × 300 mm), HMW 7 column (15-20 μm, 7.8 mm × 300 mm), and HMW 6E column (15-20 μm 7.8 mm × 300 mm). Further, the measured molecular weight was corrected using a polyisoprene standard sample (Polyisoprene standard kit, Waters Corp., Milford, MA, USA).
The epoxide content of the ENR samples was determined using proton nuclear magnetic resonance spectroscopy (1H NMR; Varian, Unity Plus 300, Garden State Scientific, Morristown, NJ, USA). Solutions of ENR (15 mg/mL) in deuterated chloroform (CDCl3, Cambridge Isotope Laboratories, Inc., Andover, MA, USA) were prepared in 5-mm NMR tubes.
The glass transition temperature (Tg) of the rubber was measured using differential scanning calorimetry (DSC-Q10, TA Instruments, USA). Rubber samples (3-6 mg) were measured from -80 to 100°C at a heating rate of 10°C/min.
The filler–filler interaction of the compound samples were determined using a rubber processing analyzer (RPA2000, Alpha Technologies, Hudson, OH, USA) according to the standard procedure given in ASTM D8059. The storage modulus (G′) of the compounds after the 1st stage of mixing was measured at 60°C within a strain range of 0.01% to 40.04%. The storage modulus was high in the low strain region because silica agglomerates were not yet disintegrated, and decreased once higher strain was applied. The change in storage modulus (ΔG′) was calculated by subtracting the value at a strain of 40.04% from that at 0.57%. This value describes the Payne effect, and represents the degree of filler–filler interaction. Thus, it was used as an indicator for the degree of filler dispersion within the rubber compounds.
The processability of the rubber was evaluated using the standard procedure given in ASTM D164. A Mooney viscometer (Vluchem IND Co., Seoul, Korea) was used to measure the torque as the rotor rotated at 2 rpm within a space filled with unvulcanized rubber. The sample was preheated to 100°C over 1 min, and the torque was measured as the rotor was rotated for 4 min.
For measuring bound rubber contents, after the first mixing stage, a sample of the compounds (0.2 ± 0.01 g) was placed on a filter paper and immersed in toluene (100 mL) for 6 days at 25°C to extract the unbound rubber. The toluene containing the extracted unbound rubber was cleaned with acetone and dried. The bound rubber content was computed based on the sample weights before and after the experiment as follows:
where wfg is the weight of the filler and gel, wt is the weight of the specimen, mf is the weight fraction of the filler in the compounds, and mr is the weight fraction of the polymer in the compounds.
The cure characteristics of the compounds were evaluated based on the minimum torque (Tmin), maximum torque (Tmax), scorch time (t10), and optimal cure time (t90) measured using a moving die rheometer (MDR, Myung Ji Co., Seoul, Korea) over 30 min at 150°C and a vibration angle of ±1°.
For the crosslink density, vulcanizate specimens (10 mm × 10 mm × 2 mm) were sequentially immersed in tetrahydrofuran (THF, 99%, Samchun Chemical Co., Seoul, Korea) and n-hexane (95%, Samchun Chemical Co., Seoul, Korea) for 1 day each at 25°C to remove organic additives inside the specimens. The weight of the specimens was recorded. The specimens were immersed in toluene for 1 day at room temperature, and the swollen specimens were weighed. The total crosslink density was calculated using the Flory-Rehner equation as follows:
where ν is the crosslink density (mol/g), Mc is the average molecular weight between crosslink points (g/mol), Vr is the volume fraction of rubber in the swollen gel at equilibrium, Vs is the molar volume of solvent (cm3/mol), ρr is the density of rubber sample (g/cm3), and χ is the polymer-solvent interaction parameter. Further, the chemical crosslink density of the unfilled compounds was calculated based on the Flory–Rehner equation (Equation (2)) and the Kraus equation (Equation (3)):
where Vr0 is the volume fraction of unfilled rubber in the swollen gel at equilibrium, Vr is the volume fraction of rubber in the swollen gel at equilibrium, and φ is the volume fraction of filler. Subsequently, the filler–rubber interaction was calculated as the difference between the total crosslink density (chemical crosslink density + filler–rubber interaction) and chemical crosslink density.
The mechanical properties of the vulcanizates, including tensile strength, modulus, and elongation at break, were evaluated. Dumbbell-shaped specimens (length = 100 mm; width = 25 mm) were tested at the speed of 500 mm/min using a universal testing machine (UTM, KSU-05M-C, KSU Co., Ansan, Korea) according to the standard procedure given in ATSM D 412.
Abrasion resistance was measured using an abrasion tester (DIN: Deutsche Industrie Normen, KSU Co., Ansan, Korea) according to the standard procedure given in DIN 53516. Cylindrical specimens (diameter = 16 mm; length = 8 mm) were tested, where an abrasive sheet was rotated on the surface of the specimen at 40 ± 1 rpm under load of 5 N. The mass loss was measured.
The dynamic viscoelastic properties of the compounds were evaluated by measuring the storage modulus (E′), loss modulus (E″), and tan δ within a temperature range of -80 to 100°C at 0.2% strain and 10 Hz using a dynamic mechanical analyzer (DMA Q800, TA Instrument, New Castle, DE, USA).
The whole synthesis process is shown in Scheme 1. At first, LqIR was synthesized by anionic polymerization in a nitrogen-purged reactor at 50°C. Cyclohexane and n-butyllithium were used as solvent and initiator, respectively. THF was added at a molar ratio of 0.25 relative to the initiator to accelerate the reaction.13 Subsequently, isoprene was introduced into the reactor under nitrogen atmosphere. The polymerization of LqIR lasted 5 h, and then the reaction was terminated by adding n-octyl alcohol (1.2 M; in excess with respect to the initiator) (Scheme 2). LqIR of different molecular weights was synthesized by adjusting the initiator to isoprene monomer ratio. After terminating the reaction, the LqIR solution was removed from the reactor and placed in a three-necked round-bottom flask along with aqueous hydrogen peroxide and formic acid. The heterogeneous solution containing the cyclohexane and aqueous phases was stirred at a speed of 1000 rpm using a high speed stirrer at 30°C and allowed to react at the suspension interface for 24 h (Scheme 3).14 After the epoxidation reaction, the aqueous phase containing hydrogen peroxide and formic acid was removed to prevent residual reaction, and the E-LqIRs were obtained by evaporating cyclohexane from the E-LqIR solution using a vacuum evaporator. The macrostructures and microstructures of the E-LqIRs were analyzed by GPC and 1H NMR spectroscopy, and Tg was measured using DSC.
Compounds were manufactured using an internal mixer (300cc, Mirae Scientific Instruments Inc., Gwangju, Korea) based on the formulations presented in Table 1. The fill factor was 80% of the mixer volume. The input unit was parts per hundred rubber (phr), and the compounds were proportional to the amount of rubber added.
The mixing procedure is outlined in Table 2, where the initial temperatures of the first and second stages were 100 and 50°C, respectively, and the dump temperature ranges were 150 to 155°C and 80 to 90°C, respectively. After mixing was complete in each stage, the compounds were formed into sheets using a two-roll mill. The vulcanizates were prepared by pressing the compound in a hydraulic press at 150°C for an optimal curing time (t90).
Results and Discussion
The results of GPC, DSC, and 1H NMR analyses of E-LqIR are presented in Figure 1 and Table 3. As described in the previous section, E-LqIRs were synthesized using LqIRs of different molecular weights to determine the molecular-weight effect of E-LqIRs on the TBR tread compound. The results of the GPC analysis exhibit the E-LqIR Mn values of 3815, 14,253, and 22,098 g/mol. The corresponding Tg values of these E-LqIRs equal -69.03, -60.55, and -58.96°C, respectively, as obtained by DSC. As can be realized, the Tg values increase with increasing molecular weight owing to chain-mobility restrictions.15,16 The results of the 1H NMR measurements reveal the presence of signals in the 4.6-4.8, 4.8-5, and 5-5.2 ppm range owing to the presence of olefinic methine protons corresponding to the 3,4-, 1,2-, 1,4- addition units of polyisoprene, respectively. The signals corresponding to epoxy methane protons were observed at 2.7 ppm.17,18 Moreover, signals corresponding to the presence of n-octyl alcohol, added as a reaction terminator for LqIR, were observed at 3.6 ppm. The epoxide contents in the three E-LqIRs were calculated as the areas under the peaks observed in the 4.6-4.8, 5-5.2, and 2.7 ppm range (Equation 4). These calculated epoxide contents equal 13.4, 12.5, and 12.9 mol%, respectively, and they are nearly identical.
The functionality—the number of epoxide groups for every E-LqIR chain—was calculated using the results of GPC and NMR analyses. The average unit number of chains was calculated (Equation 5) using the molecular weights of the isoprene unit (68.12 g/mol) and its epoxidized variant (84.12 g/mol) as well as Mn. Subsequently, the average number of epoxide groups per chain (Equation 6) was calculated using the epoxide contents obtained using Equation (4).
The results of the Payne-effect analysis, presented in Figure 2 and Table 4, demonstrate the presence of filler–filler interactions in the uncured compounds.19 In general, the storage modulus (G′) reduces with increasing strain amplitude due to the breakdown of the filler–filler network; however, a high ΔG′ value represents a strong filler–filler interaction. Accordingly, in this study, the degree of silica dispersion was determined based on the results of the Payne-effect analysis because a low Payne effect value indicates superior silica dispersion within a compound. The results of this study reveal that the Payne-effect values of E-LqIRs are smaller compared to those of the TDAE oil because the epoxide group in E-LqIR covers the silica surface. These results confirm that silica dispersion can be improved by decreasing the molecular weight of the E-LqIRs. Therefore, the findings of this study indicate that the excellent flow properties of the low molecular weight E-LqIR make it suitable for use as a processing aid in TBR tire tread.
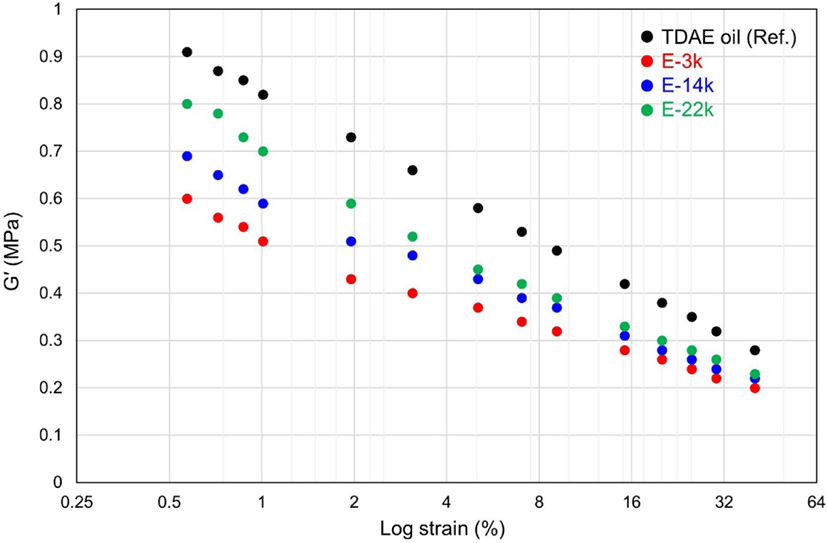
Compounds | TDAE oil | E-3k | E-14k | E-22k |
---|---|---|---|---|
ΔG′ (0.57-40.04%, MPa) | 0.63 | 0.40 | 0.47 | 0.57 |
Figure 3 and Table 5 present the results of Mooney viscosity and bound rubber content measurements, as well as the cure characteristics determined in this study using MDR. The low molecular weight of E-LqIR facilitates silica dispersion, thereby resulting in low Mooney viscosity and Tmin values. Furthermore, the observed low bound rubber content could be attributed to the decrease in occluded rubber content.20 In terms of cure characteristics, the E-LqIR compounds demonstrated small △T values owing to the increase sulfur consumption by their double bonds compared to TDAE oil. Furthermore, an increase in the E-LqIR molecular weight causes an increase in the silica covering by E-LqIRs. This limits the accelerator adsorption effect by silica. In addition, increase in the E-LqIR molecular weight increases the co-vulcanization points of E-LqIR with NR by sulfur. This results are the attainment of high △T values as shown in the case of E-LqIR compound.
Figure 4 illustrates the E-LqIR interactions that can be observed in the silica filled NR vulcanizates that contain E-LqIRs. The E-LqIRs that do not interact with rubber or silica (Fig. 4(a)) act as lubricants. Owing to the absence of interactions, these E-LqIRs can be extracted during the pretreatment stage of swelling tests. On the other hand, the E-LqIRs that form hydrogen bond and the direct silica–epoxy bonds with the silica hydroxyl groups act as silica-covering agents (Fig. 4(b)). Therefore, these E-LqIRs cannot be extracted during the pretreatment stage of swelling tests.21 In addition, some E-LqIRs that interact with silica can be coupled with NR through crosslinks with sulfur, and these E-LqIRs can act as coupling agents (Fig. 4(c)).22
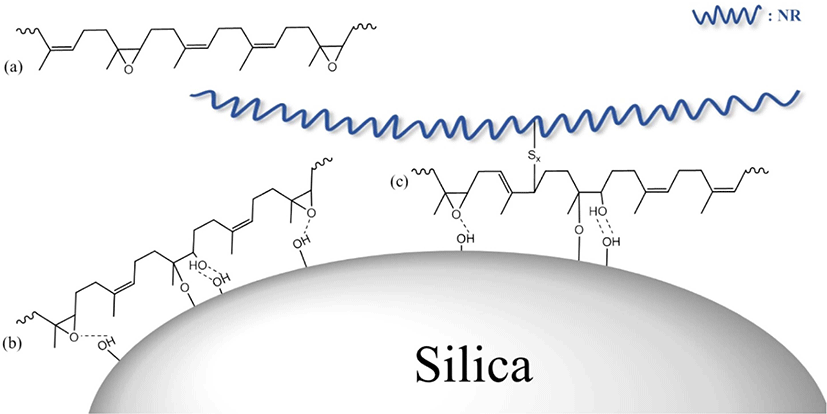
During the pretreatment stage of swelling tests, the organic matter present in the vulcanizates is extracted using two different organic solvents THF and n-hexane. Figure 5 and Table 6 present the amounts of extracted organic matter. The proportion of 10 phr of TDAE oil in the vulcanizate equals to 5.44 wt%. The TDAE oil represents the highest amount of organic matter extracted at 9.51% (10 phr of TDAE oil (5.44 wt%) along with additives, such as stearic acid, 6PPD, and TMQ (4.07 wt%)). This is because the TDAE oil can be easily extracted using organic solvents, as it does not form a chemical bond with other materials in the compound. However, the E-LqIRs are more resistant to extraction owing to the increased interactions between the epoxide groups and silica. Assuming complete extraction of TDAE oil along with that of the same amount of additives, the amount of E-LqIR that can be extracted decreases from 62% to 21.8% to 7.8% with increasing molecular weight. This confirms the high extraction resistance of E-LqIRs. Thus, it is confirmed that the larger the molecular weight of E-LqIRs, the more unlikely is the occurrence of problems associated with processing-aid migration.8
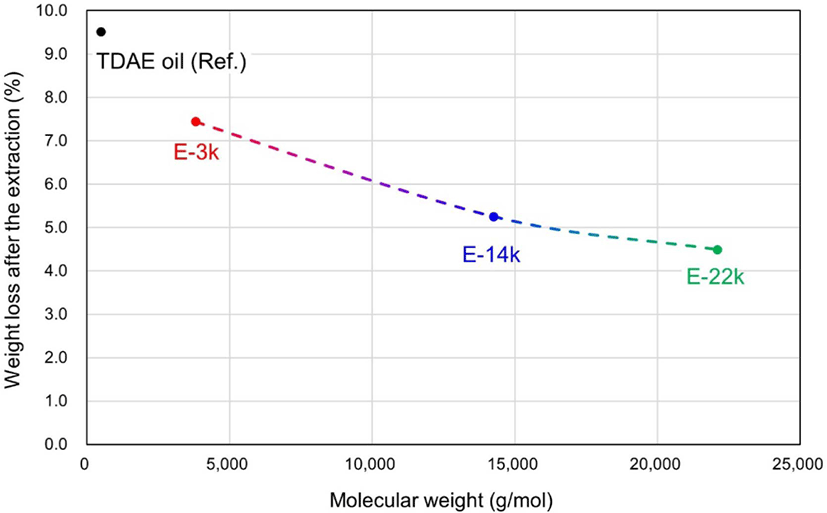
To investigate the effect of E-LqIR molecular weight on the rubber compound vulcanizate structures containing different filler contents, the total crosslink density was calculated as the sum of the filler–rubber interactions and the chemical crosslink density observed by vulcanizate structure analysis.21-30 The results obtained are presented in Figure 6 and Table 6. The chemical crosslink density of the compound with added E-LqIRs is lower than that of the compound containing TDAE oil. This can be attributed to the additional consumption of sulfur by the E-LqIR double bonds. On the other hand, a greater number of filler–rubber interactions occur in the vulcanizates containing E-LqIR owing to the presence of sulfur, which makes the E-LqIRs as coupling agents. The results of the vulcanizate structure analysis reveals that a high molecular weight of E-LqIR facilitates easy crosslink with sulfur, thereby increasing the filler–rubber interaction. In addition, without extraction, as the amount of E-LqIR covering the silica without extraction increased, it was confirmed that the chemical crosslink was increased due to the decrease of the accelerator adsorbed to the silica along with the entanglement of the E-LqIR.
Figure 7 and Table 7 list the mechanical properties of E-LqIR compounds manufactured in this study. In the stress-strain curve, the modulus demonstrates the same trend as the change in the crosslink density of the compounds. The E-3k compound demonstrates the lowest modulus owing to the sulfur consumption by E-LqIR. With increase in molecular weight to E-14k and E-22k, the corresponding modulus value was observed to increase owing to increases in chemical crosslink density and filler–rubber interactions.
The abrasion resistance of the compounds was evaluated by performing the DIN abrasion tests, and the results obtained are described in Table 7. Evidently, the E-LqIR compounds with high filler–rubber interactions exhibit superior abrasion resistance compared to those containing TDAE oil.12,31 In addition, because the filler–rubber interactions improve with increase in the E-LqIR molecular weight, the E-22k compound demonstrates the highest abrasion resistance.
Tan δ at 60°C indicates the rolling resistance (RR) of a tire.32, whereas the loss modulus E″ at 0°C indicates of the corresponding wet grip performance.33,34 Rubber compounds typically exhibit high values of tan δ at temperatures near Tg owing to the hysteresis of the rubber chains.31 In addition, the value of E″ at 0°C decreases with improvement of silica-dispersion.35 On the other hand, the value of tan δ at 60°C is seldom affected by the rubber chain hysteresis and low values of tan δ are observed under conditions of excellent silica dispersion and high crosslink density.36,37 In tire tread compounds manufactured using liquid rubber as a processing aid. The value of tan δ of the vulcanizates is greatly affected by the hysteresis loss from the chain end of the liquid rubber.9,38,39
Figure 8 and Table 8 present the dynamic viscoelastic properties of these compound. Evidently, the E-LqIR containing compounds exhibit a higher value of tan δ at 60°C compared to those containing TDAE oil. This can be attributed to the low chemical crosslink density and hysteresis loss at the E-LqIR chain end. On the other hand, an increase in the E-LqIR molecular weight causes a reduction in the value of tan δ at 60 °C owing to the decrease in the number of E-LqIR chain ends and the increase in crosslink density. Furthermore, the improvement in silica dispersion in the E-LqIR containing compounds over the TDAE oil containing counterpart causes the value of E″ at 0 °C to decrease in the former. However, the E-3k compound demonstrates a higher value of E″ at 0 °C compared to the TDAE-oil containing counterpart owing to hysteresis loss at the chain end of the E-LqIR. In addition, E-14k and E-22k compounds demonstrate comparatively lower values of E″ at 0°C owing to a decrease in the number of chain ends of E-LqIR. This confirms their inferior wet grip performance compared to the TDAE oil compound.
Compounds | THAE oil | E-3k | E-14k | E-22k |
---|---|---|---|---|
Tg (°C) | -52.3 | -52.6 | -53.0 | -53.6 |
E″ at 0°C (MPa) | 1.60 | 2.00 | 1.51 | 1.44 |
Tan δ at 60°C | 0.037 | 0.049 | 0.044 | 0.040 |
Conclusions
In this study, the effect of the molecular weight of E-LqIRs applied as a processing aid to the silica filled NR compound on the compound properties was investigated. For the compound with E-LqIRs, chemical interactions were formed with the hydroxyl group of silica by the introduced epoxide group, which improved the silica dispersion compared to that of the TDAE oil compound. With smaller molecular weight of E-LqIRs, E-LqIRs can better perform the role as a processing aid, leading to excellent silica dispersion. In addition, with interaction of E-LqIRs with silica and rubber, extraction resistance is increased compared to that of the TDAE oil compound, confirming feasibility of improvement in the problem of processing aid migration of tires. The result shows that the higher the molecular weight of E-LqIRs, interactions with silica and rubber can be easily formed, leading to a significant improvement in the extraction resistance with increasing molecular weight. As a result of the vulcanizate structure analysis, with increasing molecular weight of E-LqIRs, more silica surface was easily covered. Hence, the accelerators adsorbed to the silica surface decreased, leading to an increase in the chemical crosslink density. In addition, with increasing coupling with NR by sulfur, the filler-rubber interactions increased. Therefore, as the molecular weight of E-LqIRs increased, the abrasion resistance was improved with increasing filler-rubber interactions.
As a result of analysis of dynamic viscoelastic properties, compared to the properties of TDAE oil compound, E-LqIRs consumed sulfur and had a low chemical crosslink density, so E-LqIRs compounds showed a high tan δ at 60°C value due to hysteresis loss at the E-LqIRs chain ends. On the other hand, as the molecular weight of E-LqIRs increased, the tan δ at 60°C value decreased due to an increase in crosslink density and a decrease in the number of chain ends of E-LqIRs.
The results obtained in this study confirm that the use of high molecular weight E-LqIRs in tire tread compounds does not justify their role as processing aids. However, their inclusion significantly enhances the extraction resistance, abrasion resistance, and fuel efficiency of the final compound owing to increased filler–rubber interactions and reduced number of E-LqIR chain ends.