Introduction
자동차 및 전자기기에 터치형 센서의 장착이 증가하면서 유연 필름(Flexible Film)의 역할이 중요해지고 있다. 유연 필름을 이용하여 진공 열성형(Vacuum Thermoforming)을 통해 터치용 센서에 활용되기 때문이다.1,2 진공 열성형 공정은 필름(Film) 또는 시트(Sheet)를 가열한 후 진공압(Vacuum)을 주어 원하는 형상으로 완성한다. 성형된 필름은 제품으로 사용될 영역을 제외한 부분을 제거(Trimming)한 후 인몰드 라벨링(In-mold Labeling, IML) 또는 인몰드 데코레이션(In-mold Decoration, IMD) 등의 추가 공정을 거쳐 제품 표면에 부착된다.3-6 압출공정(Extrusion Process)으로 제작되는 필름은 압출되는 방향에 따라 물성의 차이를 보인다. 압출이 진행되는 흐름 방향(Machine Direction, MD) 과 이에 수직하는 직각 방향(Transverse Direction, TD)의 물성이 다른데 이러한 물성의 이방성(Anisotropic Property)은 열성형의 성형성(Formability)에 영향을 미친다. 기존의 열성형 연구에서는 필름의 유연 물성을 고려하기 위해 G’Sell 모델, K-BKZ 모델 등 다양한 점탄성 모델을 적용하였다.7-9 또한 초탄성(Hyper-elastic) 모델인 Mooney-Rivlin, Ogden 모델 등을 활용한 구성방정식(Constitutive Equation)을 이용하여 해석을 진행하기도 하였다.10-13 그러나 필름의 이방 물성을 고려한 열성형 해석 및 연신율 분석에 대한 연구는 찾아보기 어렵다.
일반적으로 필름의 한쪽면에는 내 스크레치 특성을 부여하기 위해 표면에 하드 코팅(Hard Coating) 공정을 진행한다.14-16 그러나 코팅 이전의 기본 필름에서 기계적 물성 및 성형성을 파악하는 것이 중요하다. 본 연구에서는 압출공정으로 제작된 필름의 진공 열성형 공정을 모사하기위해 폴리카보네이트(Polycarbonate, PC) 필름의 유리전이온도에서 인장시험을 통해 기계적 물성을 측정하였다. 측정한 기계적 물성은 MD와 TD의 탄성계수와 포아송 비(Poisson’s Ratio)이다. 그리고 측정한 이방 물성을 사용하여 열성형을 위한 해석을 진행하였다. 열성형에 사용한 금형은 돔 형상(Dome Type), 사다리꼴 형상(Trpezoid Type), 그리고 사각 형상(Cubic Type) 등 총 세 종류이다. 해석을 통해 다양한 형상으로 열성형 된 필름의 등가 응력(Equivalent Stress) 및 등가 변형율(Equivalent Strain)을 파악하고 두께 분포(Thickness), 면적 연신율(Area Stretch Ratio)을 분석하였다.
Experimental and Simulation
필름 제작에 사용된 소재는 PC(L-1250Y, Teijin, Japan)이다. 시차 주사 열량계(Differential Scanning Calorimetry, DSC250, TA Instruments, USA)를 이용하여 측정된 PC의 유리전이온도(Glass Transition Temperature, Tg)는 148.4℃이다.
필름 제작에 사용된 압출기(Extruder) 형태는 단축 스크류(Single Screw)이며, 다이는 코트 행거(Coated Hanger Die)를 사용하였다. 또한 다이를 통해 흘러나온 PC 용융체는 세 개의 롤(Roll)을 통해 냉각이 되면서 필름으로 제작되었다. 압출된 PC 필름의 두께는 0.250 mm이다.
PC 필름의 물성을 파악하기 위해 인장시험을 진행하였다. 사용한 인장시험기는 MINOS-020(MTDI, S. Korea)이며, 유리전이온도(148℃)에서 물성을 측정하기 위해 항온 챔버 UC-350(MTDI, S. Korea)를 사용하였다. 인장시편의 치수는 Figure 1에 나타나 있다. ASTM D882 규격을 참고하였으며, 인장시험기 및 항온 챔버 크기에 맞춰 결정하였다. 시편은 5개를 사용하며 평균 물성을 산출하였고, 인장속도는 15 mm/min으로 설정하였다.
전단 탄성계수(Shear Elastic Modulus) Gxy는 측정한 Ex, Ey, vxy를 이용하여 식 (1)과 같이 계산하였다.17
여기서 Ex와 Ey는 각각 MD, TD의 탄성계수이며, vxy 는 MD의 포아송 비이다.
본 실험에서 측정한 물성을 해석에 적용하였다.
컴퓨터 해석은 상용 프로그램인 Ansys Workbench(ANSYS, USA)을 이용하여 진공 열성형 공정을 모사하였다. Figure 2에 진공 열성형 해석을 위한 모델이 나타나있다. 금형의 구체적 치수와 필름이 나타나 있다. 열성형을 위한 금형으로 반구형 형상인 돔 형상 금형과 사다리꼴 금형, 그리고 사각 형상 금형이 사용되었다. 해석에서 금형을 강체(Rigid Body)로 설정하였고 메쉬(Mesh) 크기는 2 mm로 설정하였다. 필름은 전체 면적에 메쉬 크기를 1 mm로 설정하였다. Figure 3에는 해석이 완료된 후 성형된 필름의 정보를 파악하기 위해 관찰한 단면의 방향 나타나 있다. 시편의 대각선 방향의 단면이다. 열성형 해석 결과는 등가 응력, 등가 변형율, 두께, 그리고 면적 연신율이다.
Figure 4에서는 해석을 위한 경계조건이 나타나 있다. 필름의 사각 모서리를 고정(Fixed)였다. 열성형 중 금형이 상측으로 수직 이동(Displacement)하면서 필름과 접촉하게 되는데 이 접촉면에는 Frictionless를 적용하였다. 진공 성형을 모사하기 위해 금형 외곽면과 필름의 아래면 사이에 음압(Vacuum)을 적용하였다. 본 연구에서 열성형 해석을 위한 음압은0.70 MPa로 설정하였다.
Results and Discussion
Figure 5에는 148℃에서 인장시험으로 얻은 응력-변형율 곡선(Stress-Strain Curve)이 나타나 있다. 5회로 진행된 실험 결과를 통해 MD, TD의 항복점은 변형율 3% 근처에서 나타나는 것을 확인하였다. 항복점 이후 응력은 급격히 감소한다. 그리고 응력이 다소 증가하다가 감소하면서 파단이 일어난다. 파단은 모든 시편에서 변형율 100% 이상에서 나타났다. MD의 응력-변형율 곡선들은 큰 차이가 없으나 TD의 응력-변형율 곡선들은 차이가 크게 나타나고 있다. MD의 물성이 TD의 물성에 비해 균일하다고 판단된다. Table 1에는 인장시험을 통해 측정한 결과가 나타나 있다. PC 필름의 압출 방향에 따른 MD 및 TD의 기계적 물성인 탄성계수(Elastic Modulus), 파단 연신율(Elongation at Break), 그리고 포아송 비를 나타냈다. 탄성계수는 압출방향인 MD의 기계적 물성이 압출의 직각방향인 TD보다 높게 측정되었다. 일반적으로 압출방향으로 흐름이 이루어져 고분자 체인이 배향된다. 고분자 체인이 연결된 방향은 1차 화학적 결합으로 강하다. 그러나 압출의 직각방향은 고분자 체인의 배향이 이루지지 않아 체인간 결합인 2차 화학적 결합으로 1차 결합에 비해 결합력이 작다.18 탄성계수의 경우 MD가 TD보다 10.0% 크게 나타나 필름의 압출되는 방향에 따라 유의할 만한 물성의 차이를 보였다. 필름의 압출 방향에 따라 다른 물성을 가지고 있어 이러한 이방성을 고려한 열성형 해석이 필요하다. 파단 연신율은 MD보다 TD에서 다소 크게 나타났다. 즉 TD로 연신이 잘 이루어졌다. 포아송 비는 MD에서 다소 크게 나타났다. 본 연구의 물성측정 실험에서 파악된 기계적 물성은 MD와 TD로 물성이 다르게 나타나는 직교 이방성의 물성을 나타냈다.
Film Properties | MD | TD |
---|---|---|
Elastic Modulus (MPa) | 1034.8 | 941.0 |
Elongation at Break (%) | 117.9 | 121.1 |
Poisson’s Ratio | 0.407 | 0.400 |
Figure 6에 성형이 완료된 후 필름의 등가 응력과 등가 변형율이 나타나 있다. 응력은 대부분 모서리에 집중되고 있다. 그리고 형상의 모서리와 필름의 고정부와의 거리가 긴 쪽(그림에서 x축)에서 짧은 쪽(y축)에 비해 응력이 높게 분포하고 있다. 사다리꼴 형상에서 가장 작은 등가 응력을 보이고, 사각 형상에서 가장 큰 등가 응력을 보이나 그 차이는 5% 미만으로 작다. Figure 7에는 Figure 3에 보여준 단면의 방향에서 시편 형상에 따라 필름에 나타난 등가 응력과 등가 변형율을 비교하였다. 돔 형상의 경우 반구형 형상의 시작점인 P3과 P9에서 응력이 98 MPa로 가장 낮게 나타났다. 이 점에서 변형율은 0.101로 나타났다. 돔 형상 중심인 P6에서 응력이 122 MPa로 가장 크게 나타났으며, 변형율은 0.127로 나타났다. 돔 형상의 열성형에서 대체로 균일한 응력상태를 보였다. 사다리꼴 형상의 경우 사다리꼴 형상이 시작하기 전인 P2와 P10에서 가장 낮은 응력인 95 MPa을 보였다. 사다리꼴 형상의 윗면 양 끝 부분인 P4와 P8에서 가장 큰 응력인 138 MPa을 보였다. 이 지점에서 변형율은 0.144로 나타났다. 사다리꼴 형상은 돔 형상에 비해 응력의 균일성이 떨어졌다. 사각 형상은 급격한 단차가 있는 지점인 P2와 P10에서 응력이 196 MPa로 가장 높았다. 이 지점에서 변형율은 0.221을 보였다. 이 두 점을 제외하고는 낮고 균일한 응력 상태를 보이고 있다. 사각 형상의 열성형에서 가장 불 균일한 응력 상태를 보이고 있다. 전체적으로 보면 성형 형상에 라운딩이 크면 응력 및 변형율이 작고 모서리가 날카로우면 큰 응력 집중 및 변형율이 큼을 볼 수 있다. 필름 재료에 따라 허용 최대 연신율이 다르게 나타나는데 날카로운 모서리가 있는 열성형 제품은 소재의 선정에 유의해야 할 것으로 사료된다. 또한 원활한 열성형을 위해서는 부드러운 라운딩이 되도록 제품설계를 해야 할 것으로 판단된다.
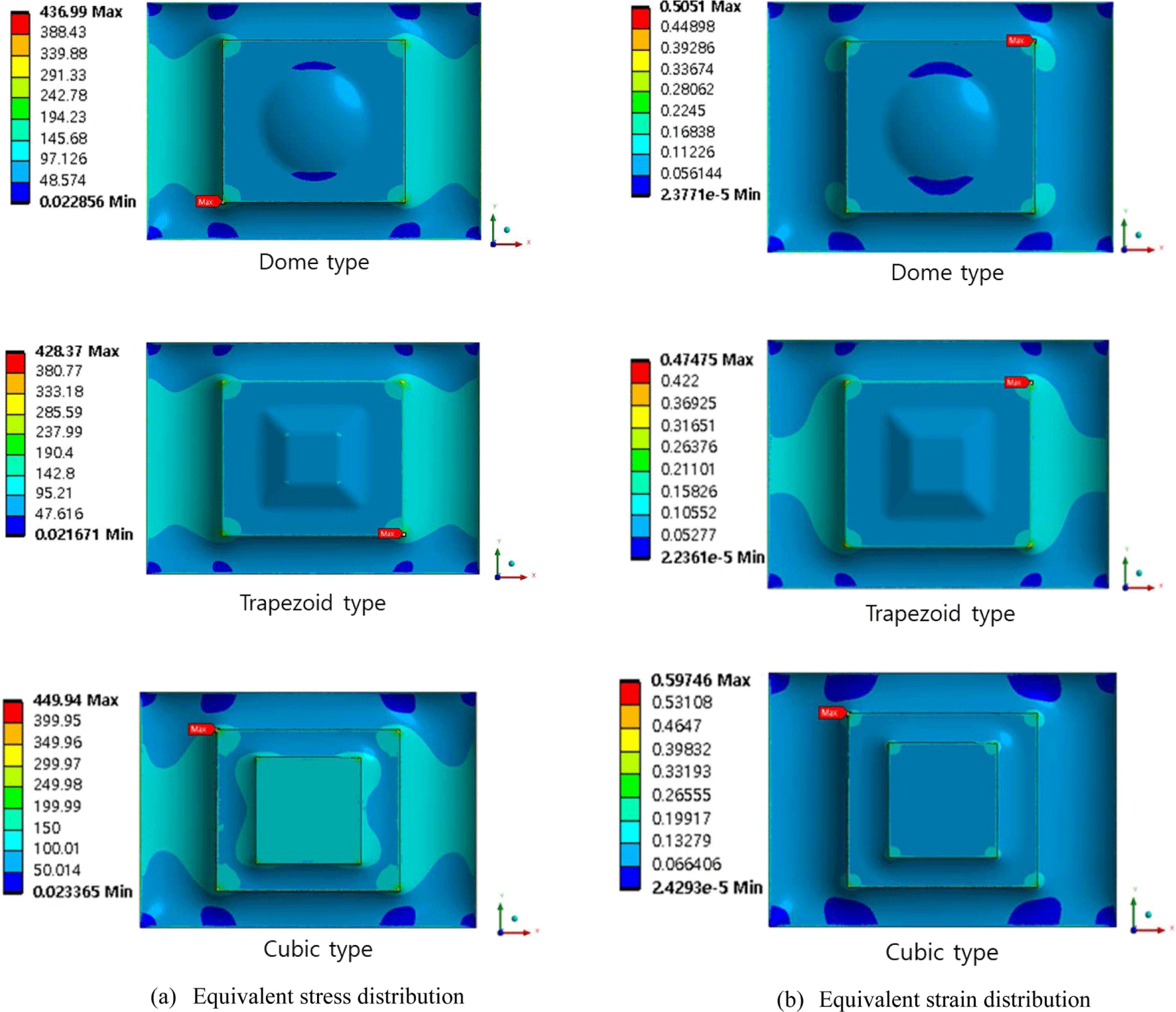
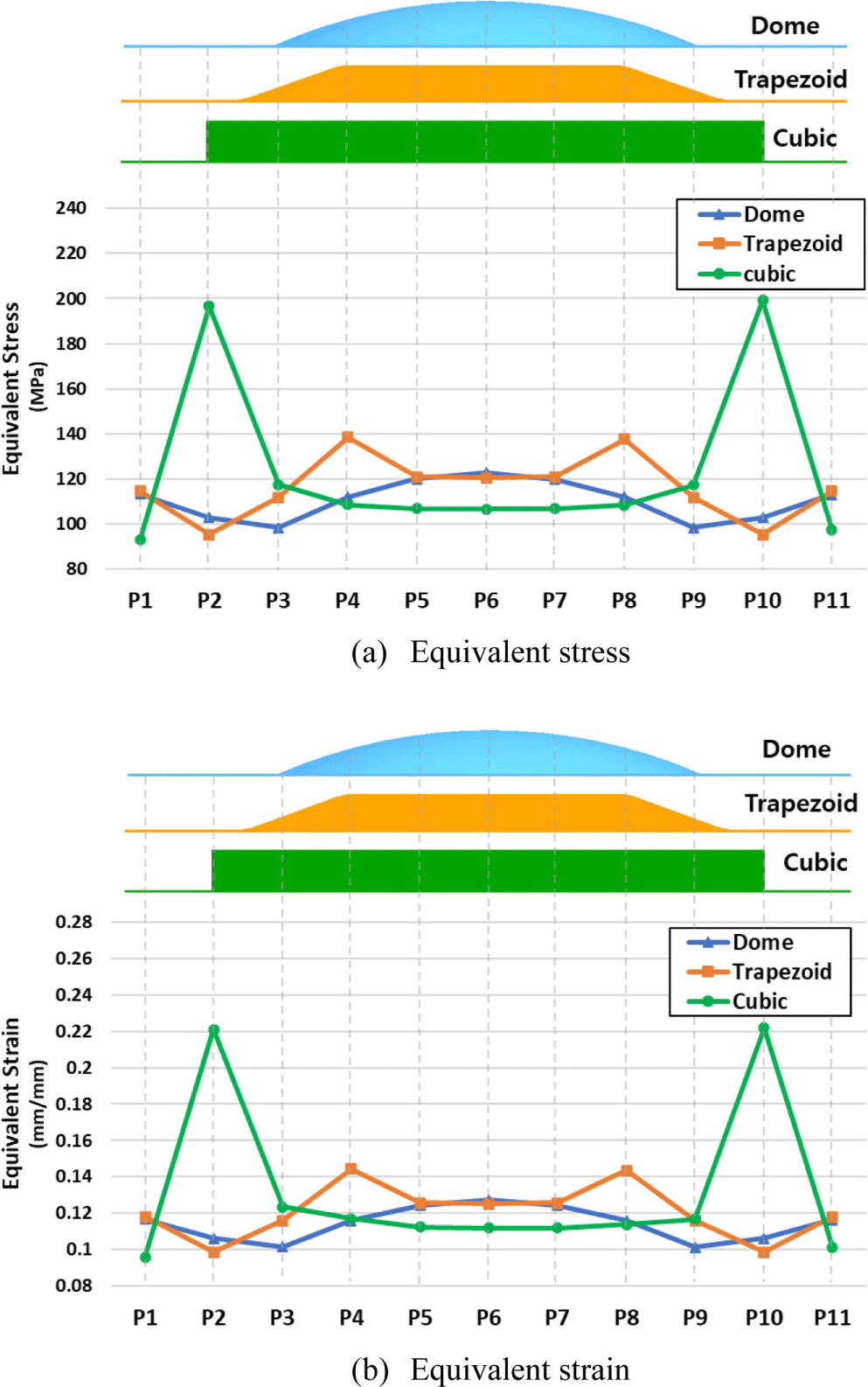
Figure 8에 금형 형상 별 두께 분포를 비교하여 나타냈다. 성형 전 필름의 두께는 0.250 mm이며 진공 열성형 시 금형 형상에 따라 스트레치가 다르게 일어나면서 두께가 감소하였다. 돔 형상의 경우 반구형 형상의 시작점인 P3와 P9에서의 두께가 0.231 mm이며 돔 형상 부 중심인 P6에서 가장 얇은 0.227 mm로 나타나 초기 필름의 두께 대비 9.2% 감소하는 결과를 보였다. 본 연구에서 사용한 금형 형상 중 돔 형상의 열성형에서 대체로 두께 분포가 균일하였다. 사다리꼴 형상의 경우 경사면이 시작되기 직전인 P2와 P10에서의 두께가 0.232 mm로 가장 두껍게 나타났으며, 사다리꼴 형상의 위 평면의 끝 점 근처인 P4와 P8에서 0.225 mm로 가장 얇은 두께를 보였으며 초기 필름의 두께 대비 10.0%가 감소하였다. 돔 형상의 열성형에 비해 두께 분포가 불 균일 하였다. 사각 형상의 열성형에서는 필름이 고정되는 부분 근처인 P1과 P11에서 두께가 0.233 mm로 가장 두껍게 나타났다. 필름이 고정되는 부분에서는 연신이 거의 없었다. 급격한 단차가 나타나는 지점인 P2과 P10에서 0.218 mm로 가장 얇은 두께를 보이며 초기 필름의 두께 대비 12.8% 감소한 것을 알 수 있다. 사각 형상의 열성형에서 두께 분포가 가장 불 균일 하였다. 두께 감소가 크게 나타나는 형상의 경우, 즉 사각 형상의 경우 날카로운 모서리에서 감소가 가장 컸는데 열성형에서 두께 분포는 금형 형상에 크게 의존함을 알 수 있다. 날카로운 모서리에서 심한 스트레칭으로 두께가 얇아지게 되고 심한 두께 감소의 경우 제품이 찢어지는 현상도 나타날 수 있다고 판단된다.
열성형 중에 나타나는 연신율은 적절한 필름의 선정과 관련이 있어 매우 중요하게 관찰해야 할 항목이다. 본 연구에서는 계산의 편의 및 정확성을 고려하여 면적 연신율을 이용하여 연신율을 분석하였다. Figure 9에 면적 연신율 측정 형식을 나타냈다. 변형 전 필름 형상에 5×5 mm 격자를 설정한 다음, 변형 후 필름에서 격자의 변형 형상을 측정하여 계산하였다. Figure 10에서는 열성형 형상에 따른 면적 연신율 분포를 보여주고 있다. 돔 형상의 경우 반구형 형상의 시작점인 P3과 P9에서 면적 연신율이 11.9%으로 가장 작게 나타났으며, 중심부로 갈수록 점차 증가하다 반구의 정점인 P6에서 가장 큰 값인 15.3%의 면적 연신율을 보였다. 사다리꼴 형상의 경우, 경사면이 시작되기 전인 P2와 P10에서 연신율이 11.4%로 가장 낮게 나타났으며, 사다리꼴 형상의 윗면 끝 부분 근처인 P4와 P8에서 16.8%으로 가장 크게 나타났다. 사다리꼴 형상은 돔 형상에 비해 필름의 고정부로 갈수록 연신율이 크게 증가하는 경향을 보였다. 사각 형상의 경우 연신율은 필름이 고정되는 근처인 P1과 P11에서 10.0%로 가장 작게 나타났으며, 급격한 단차가 시작하는 지점인 P2와 P10에서 26.6%로 가장 큰 면적 연신율을 보이고 있다. 사각 형상의 경우, 급격한 단차 부분에서 가장 큰 면적 연신율을 보이지만 필름이 금형 형상부에 완전히 밀착되지 않은 결과를 보였다. 이는 열성형의 불량으로 열성형 제품의 형상 설계가 중요함을 보여주는 결과이다. 본 연구에서 수행한 모든 열성형 형상에서 일관성 있게 면적 연신율이 가장 증가한 부분에서 두께 분포는 감소하였다. 형상 부의 라운드 및 모서리 구간에서 가장 연신이 증가하면서 두께가 줄어드는 경향을 보인다. 이는 열성형 제품설계 및 금형 설계 시에 중요하게 고려해야 할 부분이며, 급격한 단차가 있는 제품의 경우에는 금형의 제작 및 성형 전에 성형성 및 두께 분포를 파악하기 위해 열성형 해석이 적용되야 할 것으로 판단된다.
Conclusions
본 연구에서는 인장시험을 통해 압출된 PC 필름의 비등방 물성을 측정하였다. 필름의 탄성계수는 MD와 TD에서 각각 1034 MPa과 941 MPa을 보였다. 포아송 비의 경우 MD와 TD에서 각각 0.407과 0.400로 측정되었다. 측정한 직교 이방 물성을 이용하여 열성형을 수행하였다.
세 가지 금형 형상에 대해 필름의 성형과정에 나타나는 응력 및 변형율을 비교하였으며, 또한 두께 분포 및 면적 연신율 분포를 비교하였다. 형상부에 나타난 응력 및 변형율은 돔 형상에서 가장 작게 나타났으며, 급격한 단차를 갖고 있는 사각 형상에서 가장 크게 나타났다. 또한 모든 금형 형상에서 나타난 결과는 응력과 변형율, 그리고 면적 연신율이 증가하면 두께 분포가 감소하는 경향을 보였다. 돔 형상의 경우 완만한 라운드로 인해 반구형 중심부에서, 사다리꼴 형상의 경우 돌출부가 시작되는 구간에서, 그리고 사각 형상은 급격한 단차가 있는 날카로운 모서리 구간에서 응력과 변형율, 그리고 면적 연신율이 증가하였고, 이에 따라 두께 분포가 감소하였다. 사각 형상의 경우 급격한 단차에서 충분하지 않은 연신으로 필름과 금형이 완전히 접촉하지 않아 미성형이 관찰되었다. 사각 형상에 비해 구배 및 부드러운 라운드로 구성된 사다리꼴 형상 및 돔 형상의 경우 필름이 금형이 완전히 접촉하였다. 이와 같은 결과로 완전 성형을 위해 필름의 연신 특성에 맞는 적합한 열성형의 형상 설계가 중요한 것으로 판단된다.
본 연구에서 수행한 해석방법 및 결과는 해석을 통한 최적 열성형 공정 수립 및 열성형 제품 설계에 유용하게 활용될 수 있다고 판단된다.