Introduction
기존의 금속 소재를 대체하기 위해 엔지니어링 플라스틱(EP)은 자동차 소재, 항공우주 부품, 3D (three-dimensional) 프린터 필라멘트 등 다양한 산업 분야에서 사용되고 있다. 특히 슈퍼 EP 중 하나인 폴리페닐렌 설파이드(polyphenylene sulfide, PPS)는 벤젠 고리에 황이 결합된 구조가 반복되는 열가소성 플라스틱이다. PPS는 구조적 특성으로 인해 내화학성이 우수하여 200°C 이하에서는 녹일 수 있는 용매가 알려지지 않다. 또한, 자체 난연성, 높은 열 안정성 및 치수 안정성의 장점을 가지고 있지만, 순수한 PPS는 잘 부러지는 특성을 가지기 때문에 단독으로 사용하기 어렵다.1-4
이에 PPS의 단점을 보완할 뿐만 아니라 기계적, 열 및 전기적 특성을 강화하기 위해 PPS 복합재료에 대한 연구가 수행되고 있다.5,6 우수한 물성의 PPS 복합재료를 제조하는 방법은 대표적으로 보강재를 활용한 방법과 서로 다른 고분자를 혼합하는 방법이 있다. 우선 보강재의 활용은 소재의 목적에 따라 다양한 형태의 보강재를 선정하여 사용할 수 있다. 보강재는 형태에 따라 particle, fiber 및 structural 세 가지로 구분할 수 있으며, 형태에 따른 보강재의 구분은 Figure 1에 나타내었다.7 이 중 가장 많이 사용되는 보강재는 유리섬유(glass fiber, GF)로 높은 강성, 쉬운 가공성 및 높은 경제성의 장점이 있어 가장 많이 사용되고 있다.8,9 고분자 혼합(blending)을 활용한 방법은 서로 다른 장점을 가진 고분자를 혼합하여 가공하는 방법이다. 이 방법은 고분자의 특성, 가공 기술 및 혼화성에 따라 소재의 특성이 달라진다.
최근 다양한 고분자와 보강재를 활용한 PPS 복합소재 연구가 활발히 이루어지고 있다. 본 논문에서는 물성 향상 및 기능성을 부여하기 위한 PPS복합소재의 연구동향을 소개하고자 한다.
열전도도 개선
전자 기기의 수명은 작동 온도에 영향을 받는 것으로 알려져 있다. 따라서 전자 기기의 온도를 적정 수준으로 유지하기 위해 복합재료의 방열 문제가 중요한 이슈로 부각되고 있다.10,11 이에 복합소재의 열전도도를 개선하기 위해 많은 연구가 진행되고 있다. 고분자 기반의 복합재료는 열전도도가 매우 낮기 때문에, 주로 질화 붕소(boron nitride, BN), 팽창 흑연(expanded graphite, EG), 탄소섬유(carbon fiber, CF) 등의 보강재를 사용하여 열전도도를 향상시킬 수 있다.
질화 붕소는 높은 열전도도 및 내화학성, 전기 절연성을 가져 고분자 복합재료의 열전도도 향상에 적합한 물질이다.12 Hexagonal boron nitride nano-ribbons (BNNRs)의 이론적인 열전도도는 약 350-3800 W/m‧K으로 알려져 있다.13 또한, 질화 붕소를 사용할 경우, 복합 재료의 열팽창 계수(CTE) 감소, 기계적 특성 향상 및 유전 특성 향상 등의 이점이 있어 주로 사용된다.12,14 하지만, 가공과정에서 서로 응집(agglomeration)되어 계면의 단열(interfacial thermal barrier)을 유도하기 때문에 이를 최소화하기 위한 연구들이 보고되었다.10,11
Zhang 연구팀은15 micrometer BN (mBN)과 nanometer BN (nBN)을 동시에 사용하여 열전도도를 평가 및 모델링을 수행하였다. mBN과 nBN 질량비에 따른 열전도 계수(λ)를 Figure 2(a)에 나타내었다. mBN 혹은 nBN의 단일 사용보다 mBN/nBN 복합 사용이 열전도도 개선에 더 효과적인 것으로 나타났다. 또한 BN의 함량이 30% 이상일 때, 열전도가 급격히 증가하며 60%에서 2.64 W/m‧K으로 가장 높은 값을 나타낸다. 이는 비결정질 영역에 존재하는 mBN과 nBN이 열전도 통로를 형성하고 PPS의 결정도를 향상시켰기 때문으로 보인다. 이와 같이 BN은 복합 재료 내에서 효과적인 열 통로를 제공하는 것이 중요한 요소 중 하나이다. 중앙대학교 김주헌 교수 연구팀은16 에폭시(epoxy) 코팅을 통한 PPS의 표면 개질 후, BN/PPS core-shell 구조를 형성하여 c-BN/PPS 복합 필름을 개발하였다. Core-shell 구조를 가지는 c-BN/PPS 복합 필름은 에폭시 표면 처리를 거치지 않고 제조된 p-BN/PPS 복합 필름보다 공극이 덜 발생하여 계면 특성이 향상되었고, 붕화 질소 입자의 응집(agglomeration)없이 잘 분산되었다(Figure 3). 이러한 현상은 c-BN/PPS 복합 필름 내부에 열 이동 경로(heat flow path)를 잘 형성하는데 기여하여 우수한 열전도도를 나타내는 것으로 보고되었다. Sui 교수 연구팀은17 sulfonated PPS 입자를 질화 붕소 플레이크(BN flake)로 감싼 BN@PPS core-shell 구조를 제안하여 PPS 복합소재의 열전도도를 향상시켰다. BN@PPS 입자를 핫 프레스(hot press)공정을 통해 제조된 복합체는 질화 붕소와 PPS 기지(matrix)가 잘 분리되어 열 전도 경로(thermally conducting pathway)를 효과적으로 형성하였고, 이는 단면 광학현미경 이미지를 통해 잘 관찰되었다(Figure 4(b)). 또한, 용융 혼합(melt blending)법을 통해 제조된 PSS/BN 복합 재료와 비교했을 때, 열전도도가 4.15 W/m‧K으로 1.68배 향상된 것으로 나타났다. 이처럼 기존의 용융 혼합법에서 벗어나 제안된 BN@PPS core-shell 구조는 PPS 기지 내에 열전도 네트워크를 만드는데 유리하고, 포논 전달 효과가 우수하여 PPS의 열 전도도를 크게 향상시킬 수 있음이 증명되었다.
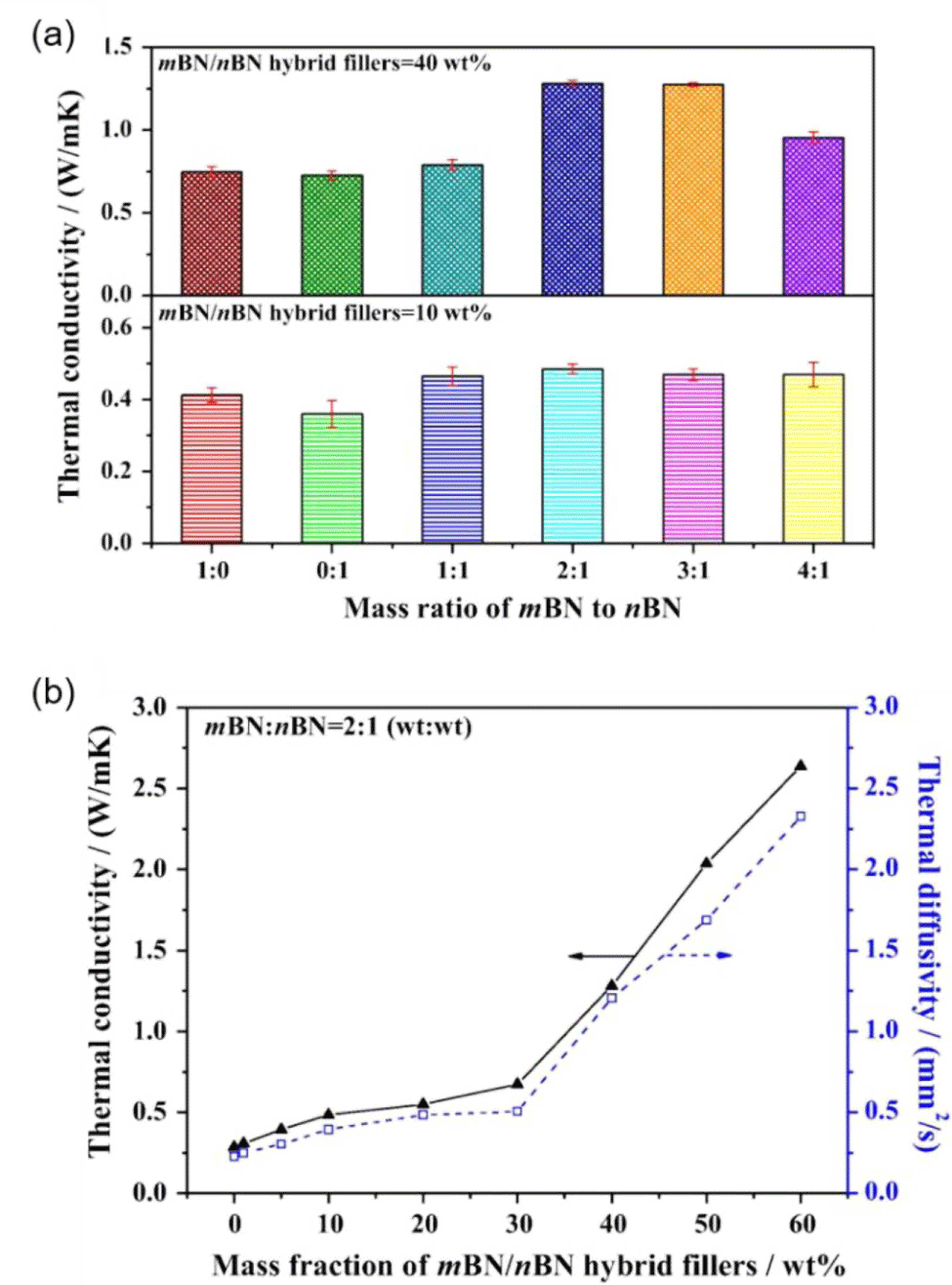
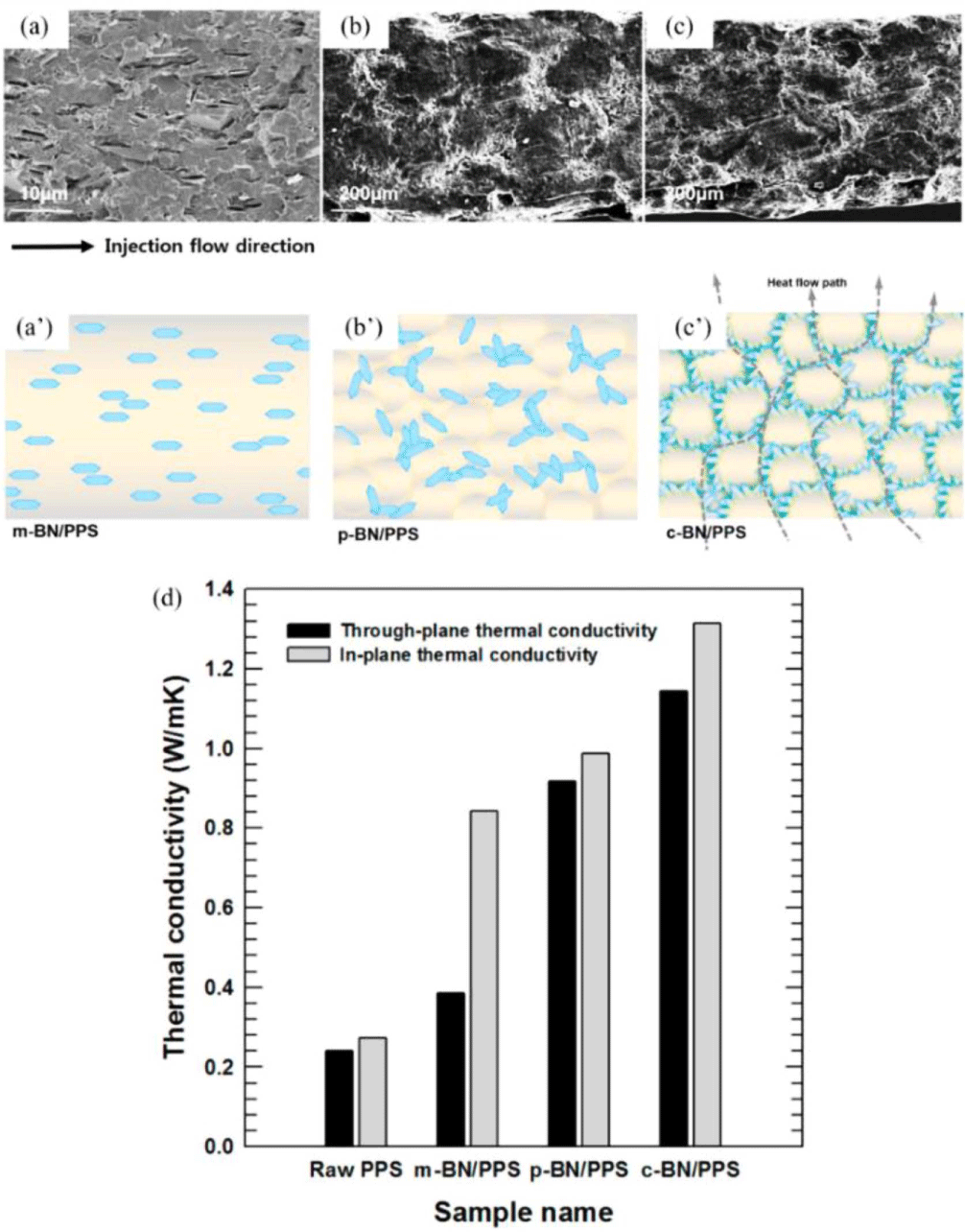
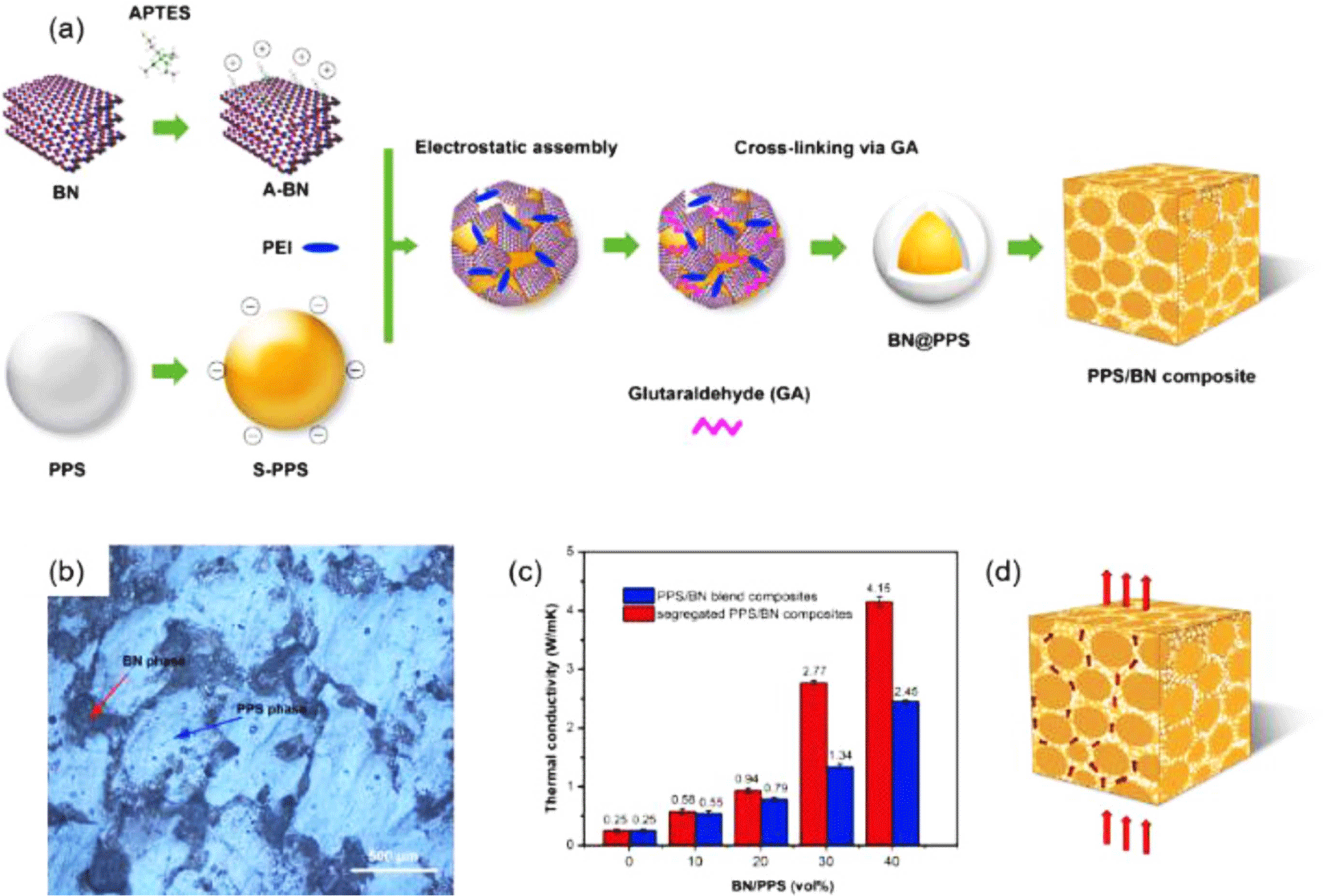
탄소 보강재도 PPS의 열 전도도를 향상시킬 수 있는 좋은 후보이다. 이에 PPS의 열전도도, 전기 전도도 및 기계적 물성을 보완하기 위해 판상형 그래핀(graphene nanoplatelet, GNP), 탄소섬유(CF) 및 탄소 나노튜브(carbon nanotube, CNT) 등이 사용된다. Zou 연구팀은 열전도도를 향상시키기 위해 PPS@PDA-CNTs-SiC 복합재료를 제조하였다. 개발된 복합재료는 PPS 표면을 폴리도파민(polydopamine, PDA)과 폴리에틸렌이민(polyethyleneimine, PEI)으로 개질한 후, CNT와 탄화 규소(silicon carbide, SiC) 입자를 개질된 PPS 표면에 침착(deposit)시켜 제조되었다(Figure 5(a)). 그 결과 PDA와 PEI는 PPS와 강한 계면 접착력을 형성하는 역할을 하였으며, 나노 크기의 보강재는 PPS와 분리되어 국부적으로 네트워크를 형성한 것을 관찰할 수 있다(Figure 6(d)). 이렇게 형성된 네트워크가 열 전달 통로를 제공하여 복합재료의 열전도도를 향상시켰다. PPS@PDA-CNTs-SiC 복합재료의 열전도도는 약 0.97 W/m‧K으로 PDA로 표면 처리되지 않은 PPS/CNTs/SiC 복합재료보다 120% 증가하였다. 또한, Figure 5(d)의 시간에 따른 시편의 온도 변화 그래프에서 볼 수 있듯이, 열전도도가 가장 높은 PPS@PDA-CNTs-SiC 복합재료의 표면 온도가 가장 빠르게 증가하는 것으로 보고되었다.18
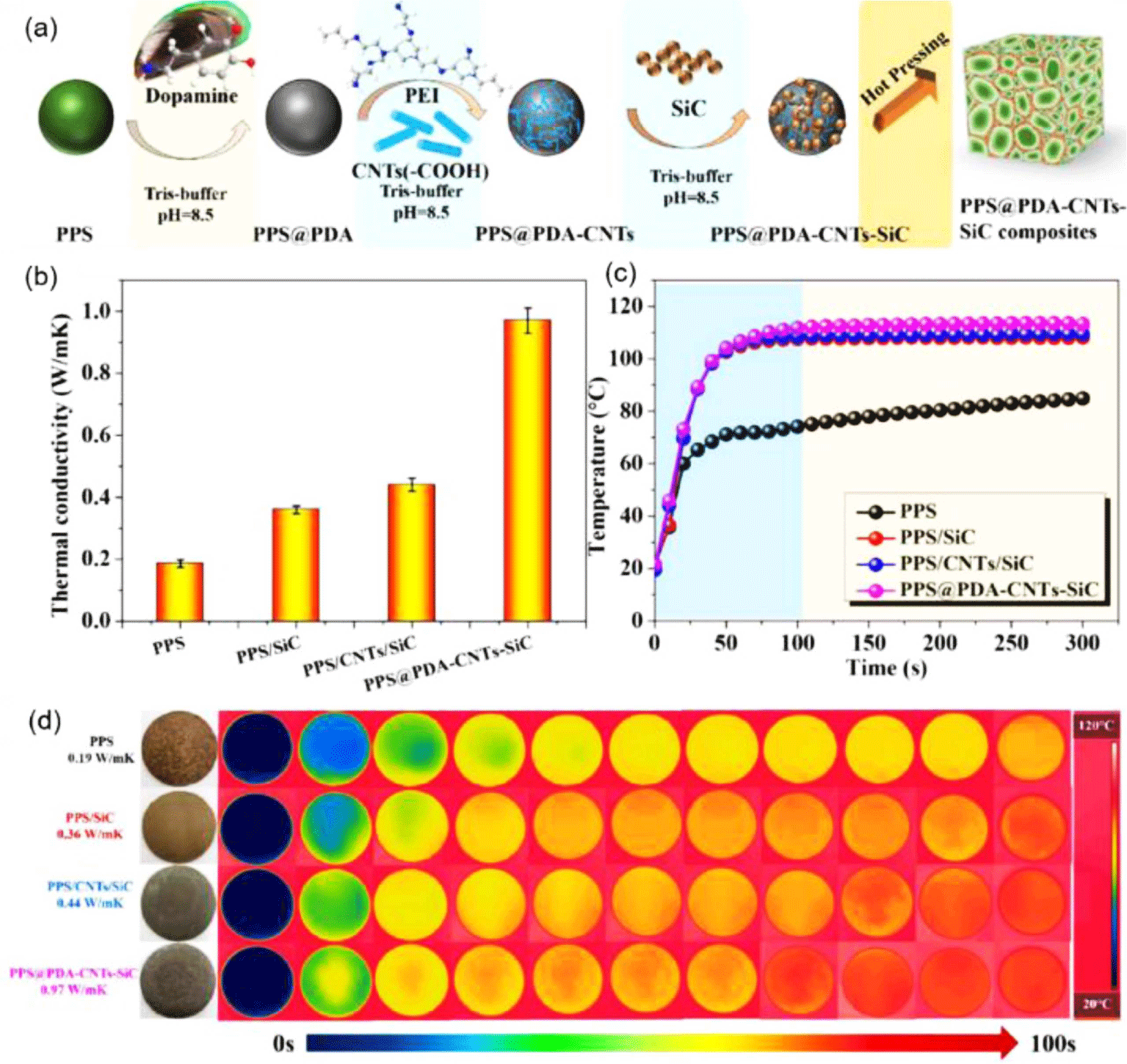
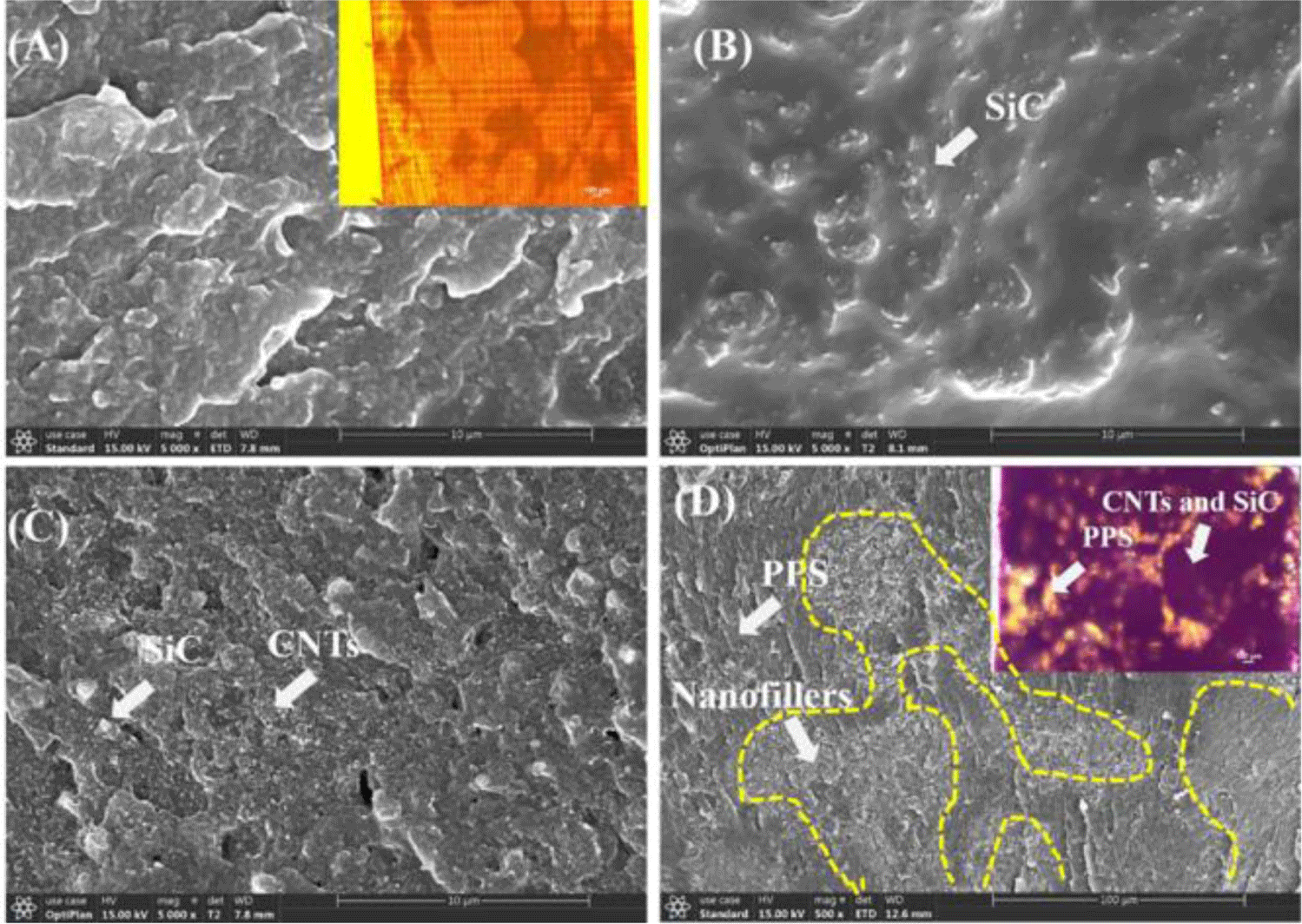
Zhang 연구팀은19 methanesulfonic acid (MSA)와 isopropyl-trioleictitanate (NDZ-105)을 사용하여 GNP의 표면을 개질(fGNP)한 후, 열전도도가 개선된 PPS/fGNP 복합 재료를 보고하였다(Figure 7(a)). 그 결과 40 wt%의 fGNP를 사용하였을 때, 약 4.41 W/m‧K의 높은 열전도도를 나타내었다(Figure 7(b)). 이는 표면에 개질된 MSA와 NDZ-105가 PPS/fGNP의 계면 열 저항을 최소화하여 개선된 것으로 보여진다. 이를 통해 탄소 재료를 활용하여 열전도도를 개선하기 위해서는 보강재 사이의 네트워크와 계면 접착력이 열전도도 향상에 영향을 주는 것을 확인할 수 있다.
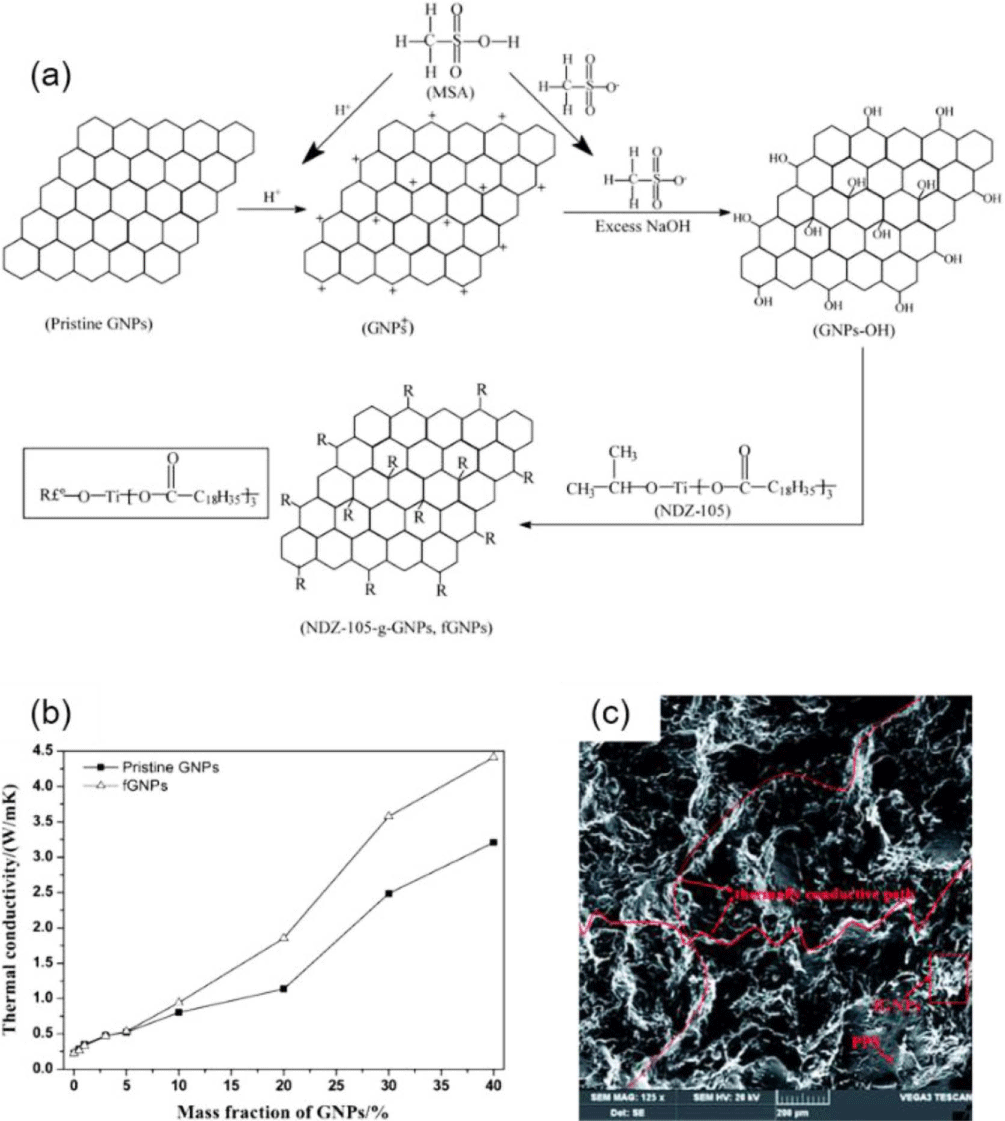
최근에는 열전도도를 개선하고 기계적 및 유전적 특성의 저하를 최소화하기 위하여 탄소 재료와 세라믹 재료와 같은 두 가지 이상의 보강재를 동시에 사용하는 연구들이 수행되고 있다. 대표적으로 붕화 질소와 같은 세라믹 재료는 전기 절연성이 우수한 물질로 알려져 있으며, 탄소 재료는 높은 열전도도를 가지는 재료로 알려져 있다. 이러한 보강재의 장점을 활용하기 위한 하이브리드 시스템 복합 재료가 연구되고 있다.
송영석 교수팀은20 1D MWCNT (one-dimensional multi- walled carbon nanotube)와 2D (two-dimensional) BN을 사용하여 PPS/hybrid filler 복합재료의 계면 열 저항과 열전도도를 예측하여 하이브리드 시스템이 열전도성 향상에 효과적임을 입증했다. 복합재료 조합은 Figure 8(a)에 나타냈고, 계면 열 저항 시뮬레이션 결과에 따르면 PPS/BN에 MWCNT를 첨가하면 계면 저항이 낮아진 것을 확인할 수 있다(Figure 8(b)). 또한, MWCNT의 표면을 염기 처리를 한 경우에 계면 저항이 더 낮아지는데, 이는 MWCNT 표면의 –OH가 포논(phonon)이 효과적으로 이동할 수 있도록 돕기 때문이다. 복합재료의 열전도도를 확인하기 위하여 실험 값과 FE (finite element) 시뮬레이션 결과들을 Figure 8(c)에 나타내었다. MWCNT의 표면을 H2O2 처리한 PBHM-501의 경우, 열 계면 저항이 낮은 이상적인 계면 조건을 가정하면 매우 우수한 열전도도 결과를 얻을 수 있지만, 계면에서 발생하는 열 저항(thermal barrier resistance)을 가정하면 실험값과 유사한 결과를 얻을 수 있는 것으로 보고되었다. 이 연구는 FE 시뮬레이션을 활용하여 하이브리드 시스템을 이용한 복합재료의 열전도도 결과를 예측하고 이상적인 복합재료를 설계할 수 있음을 보여주었다.
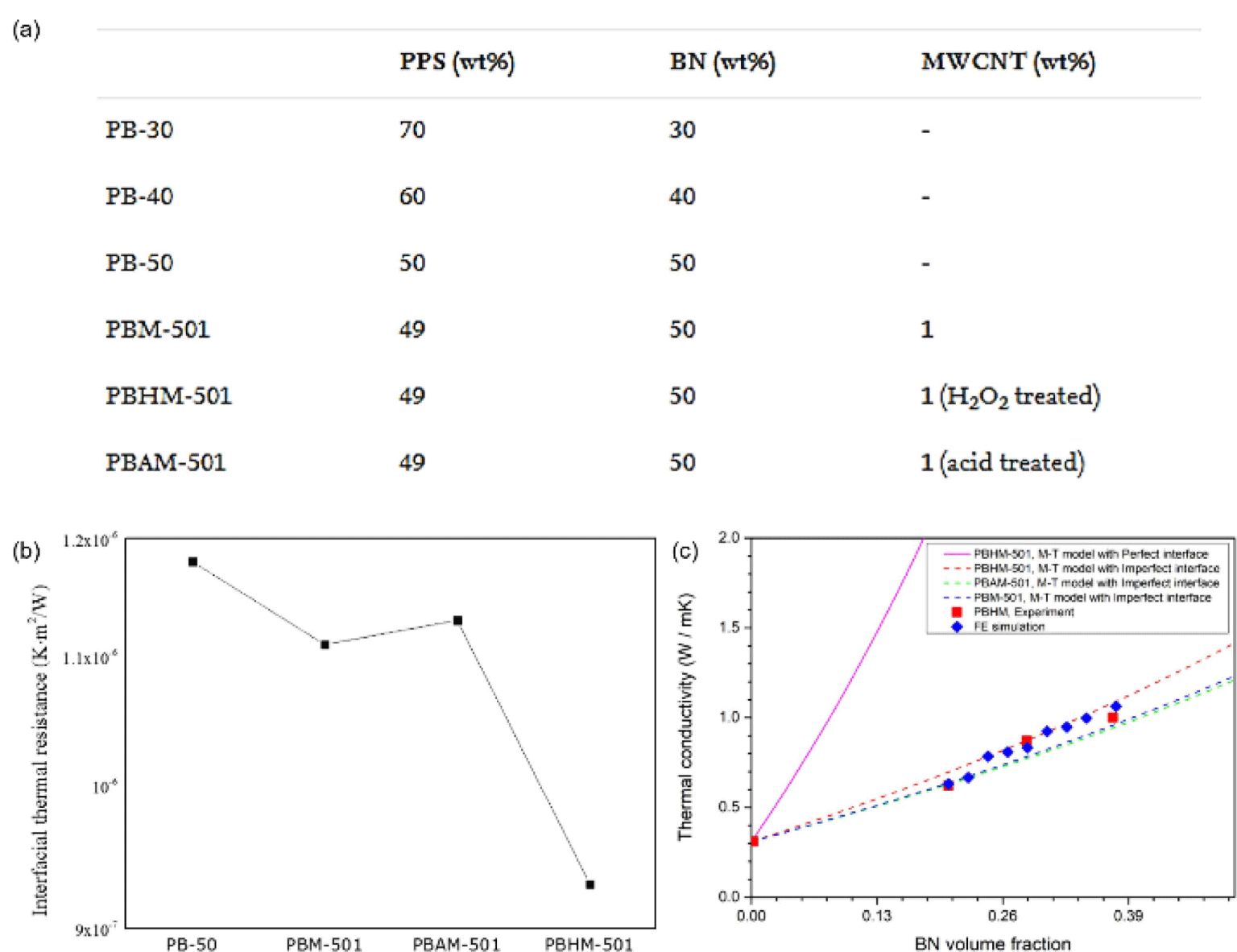
기계적 물성 개선
PPS는 잘 부러지는 성질(brittle)을 가지기 때문에 단독으로 사용하기에는 다소 제한이 있다. 이에 기계적 물성을 보완하기 위하여 다양한 보강재가 사용되는데, 주로 유리섬유(GF), 탄소섬유(CF) 또는 아라미드 섬유(aramide fiber, e.g. Kevlar)가 주로 사용된다.
유리섬유는 높은 인장강도와 저렴한 가격으로 인해 많이 사용되는 보강재 중 하나이다. 이에 다양한 그레이드의 제품이 상용화되어 있으며, 고함량 PPS/GF 복합 재료를 제조하는 것이 주된 관심사 중 하나이다. 이와 관련하여, Wang 연구팀은21 유리섬유 직물(glass fiber fabric, GFF)와 PPS 부직포(nonwoven)를 사용하여 GFF의 함량이 최대 85 wt%인 PPS/GF 복합 재료를 제조하였다. 이는 melt-blow 압출을 통해 PPS 부직포를 제조하고, GFF의 표면을 에폭시로 개질하여 320°C, 30 MPa에서 30분간 열 압착하여 제조하였다. 에폭시 처리는 PPS와 GFF의 계면 특성을 향상시켜 높은 함량의 GFF 도입을 가능하게 했고, PPS/GFF 복합재료의 기계적 물성 측정 결과, 80 wt%의 GFF 함량 조건에서 가장 우수한 인장 강도 및 굴곡 강도를 가지는 것으로 보고되었다(Figure 9(a), (b)). 해당 연구는 우수한 기계적 강도를 가지는 고함량 PPS/GF 복합 재료의 개발 가능성을 제시하였다.
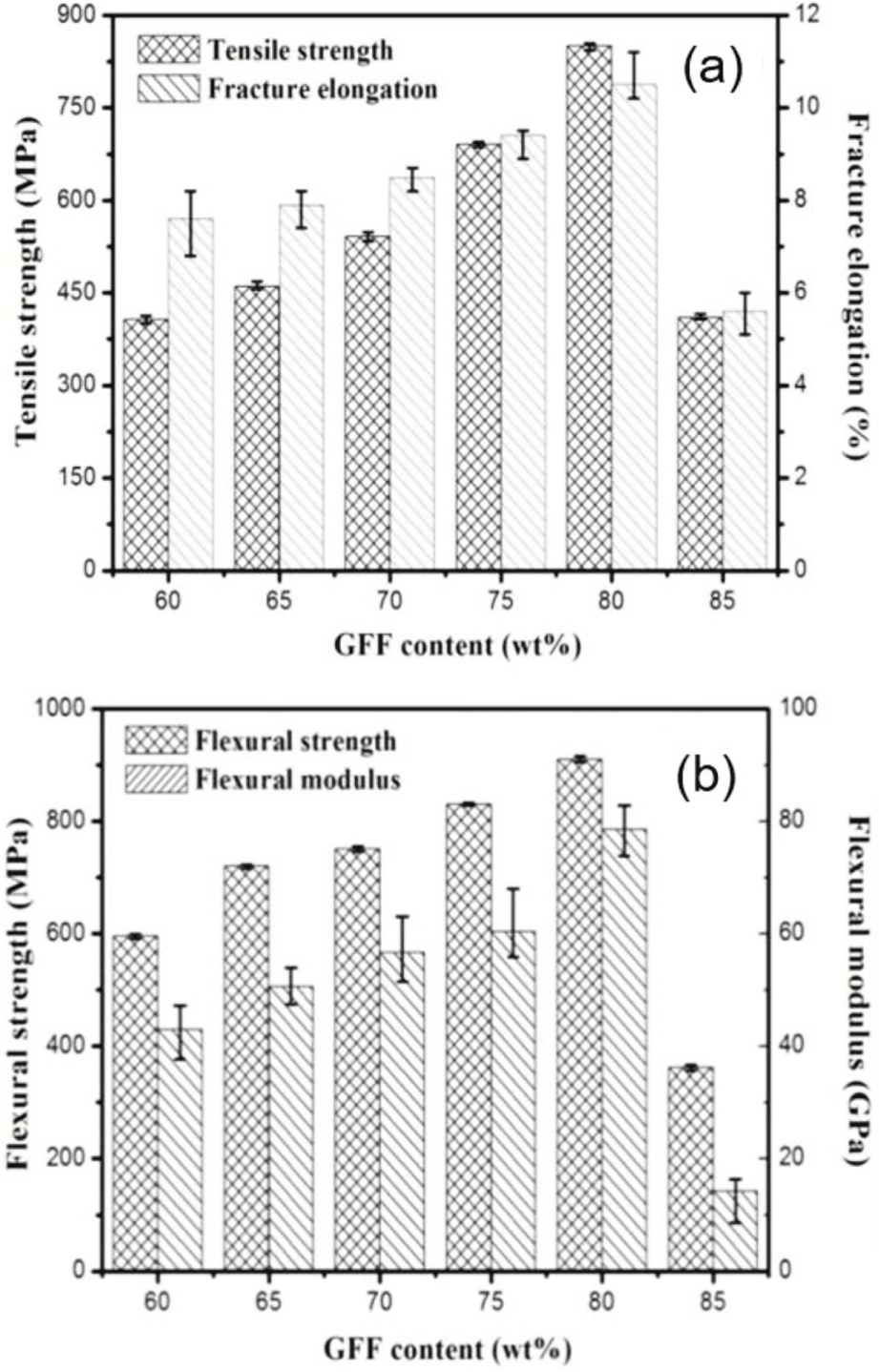
탄소섬유는 높은 강성 및 인성의 장점이 있어 섬유 강화 플라스틱의 보강재로 많이 사용된다. 특히 65 vol% 이하의 탄소섬유를 함유하는 PPS 적층 소재의 경우 우수한 기계적 물성을 달성할 수 있는 것으로 알려져 있다. 하지만, PPS/CF 복합 재료에서 불연속적인 탄소섬유의 함량이 60 wt% 이하의 조건에서만 가공되는 한계가 있는데, 이는 열가소성 플라스틱의 높은 점도로 인해 고함량의 탄소섬유가 PPS에 함침되지 않아 기계적 특성에 부정적인 영향을 미치기 때문이다. 따라서 우수한 기계적 물성을 갖는 PPS/CF 복합 재료를 위해서 고분자 내에 고함량의 보강재를 복합화하기 위한 노력이 필요했다.
이러한 한계를 극복하기 위해 Wang 연구진은22 고함량 PPS/CF 복합 재료를 만들기 위한 방안을 제시하였다. 앞서 고함량 PPS/GF 복합 재료 제조 방식과 동일하게 탄소섬유 직물(carbon fiber fabrics, CFFs)와 PPS 부직포를 사용하여 탄소섬유 함량이 85 wt%인 복합 재료를 제조하고, 기계적 물성을 측정하였다. 그 결과, 탄소섬유의 함량이 80 wt%일 때 인장강도 및 굴곡 강도가 348.6 KJ/m2, 1200.3 MPa, 1305.6 MPa로 측정되었다(Figure 10). 이는 고분자와 보강재를 부직포 형태로 제조하여 열 압착하는 방식을 사용하여 고함량 유리 및 탄소섬유 PPS 복합재료를 제조할 수 있음을 보여주는 연구이다.
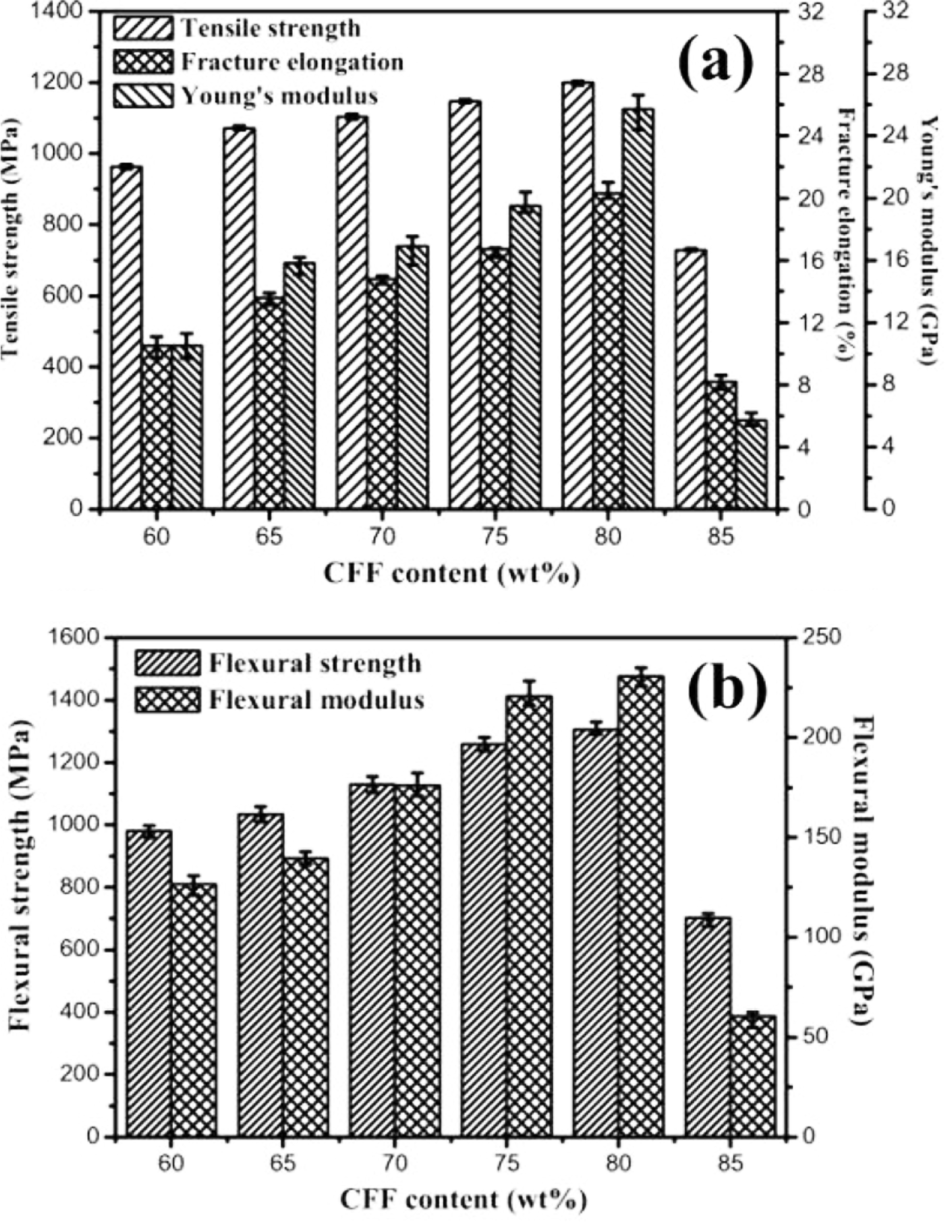
내마모성 향상
PPS는 마찰 및 마모 특성이 낮아 장시간 사용이 어렵다. 따라서 마찰 특성을 향상시키기 위해 다양한 연구들이 수행되고 있다. Chen 연구팀은 마찰 특성을 개선하기 위해서 PPS/PA66/PTFE (polyphenylene sulfide/polyamide 66/polytetra- fluoroethylene) 복합소재를 제조하여 PTFE 함량 및 열처리(annealing) 온도에 따른 마찰 특성에 대해 연구하였다. PPS는 잘 부러지며 높은 마찰 계수를 갖지만, PA66와 PTFE는 높은 고유 윤활성(self-lubrication)을 가지고 때문에 PPS의 마찰 특성을 개선하기 위해 세 가지 소재를 복합화 하였다. 그 결과 PPS/PA66/PTFE의 함량이 각각 56, 24, 20 wt%이고, 열처리 온도가 150°C일 때 가장 낮은 마찰계수(0.139) 및 마모율 (4.327×10-6 mm3/N)을 나타내었다. 하지만 180°C 이상에서 열처리를 진행하면 미세 섬유의 구조가 파괴되어 마찰 특성이 저하된다고 보고되었다(Figure 11).23 한편, Zou 연구팀은24 CF/PTFE/PPS 삼원 복합 재료에서, 매트릭스 내 탄소섬유와 PTFE가 interlocking network structure (INS)를 구축하여 마찰 계수 감소 및 내마모성을 개선한다고 보고했다. 이때 탄소섬유의 길이에 따른 영향을 비교하기 위하여 micrometer carbon fiber (MCF, 40 μm)와 short carbon fiber (SCF, 4 mm)를 사용하였다. 그 결과 PPS/PTFE/SCF20의 마찰 계수가 약 0.103으로 가장 낮은 연구 결과를 보였다(Figure 12(a)). 또한, 복합재료의 마모 표면 및 friction pair를 분석한 결과, MCF/PTFE 보다 SCF/PTFE 섬유가 우수한 하이브리드 네트워크를 형성하여 SCF가 깨지지 않도록 돕는 것을 확인하였다. 또한 PPS/PTFE/SCF 복합 재료의 주요 마모 메커니즘이 연마 마모가 동반되는 접착성 마모임을 보고하였다(Figure 12(b)).
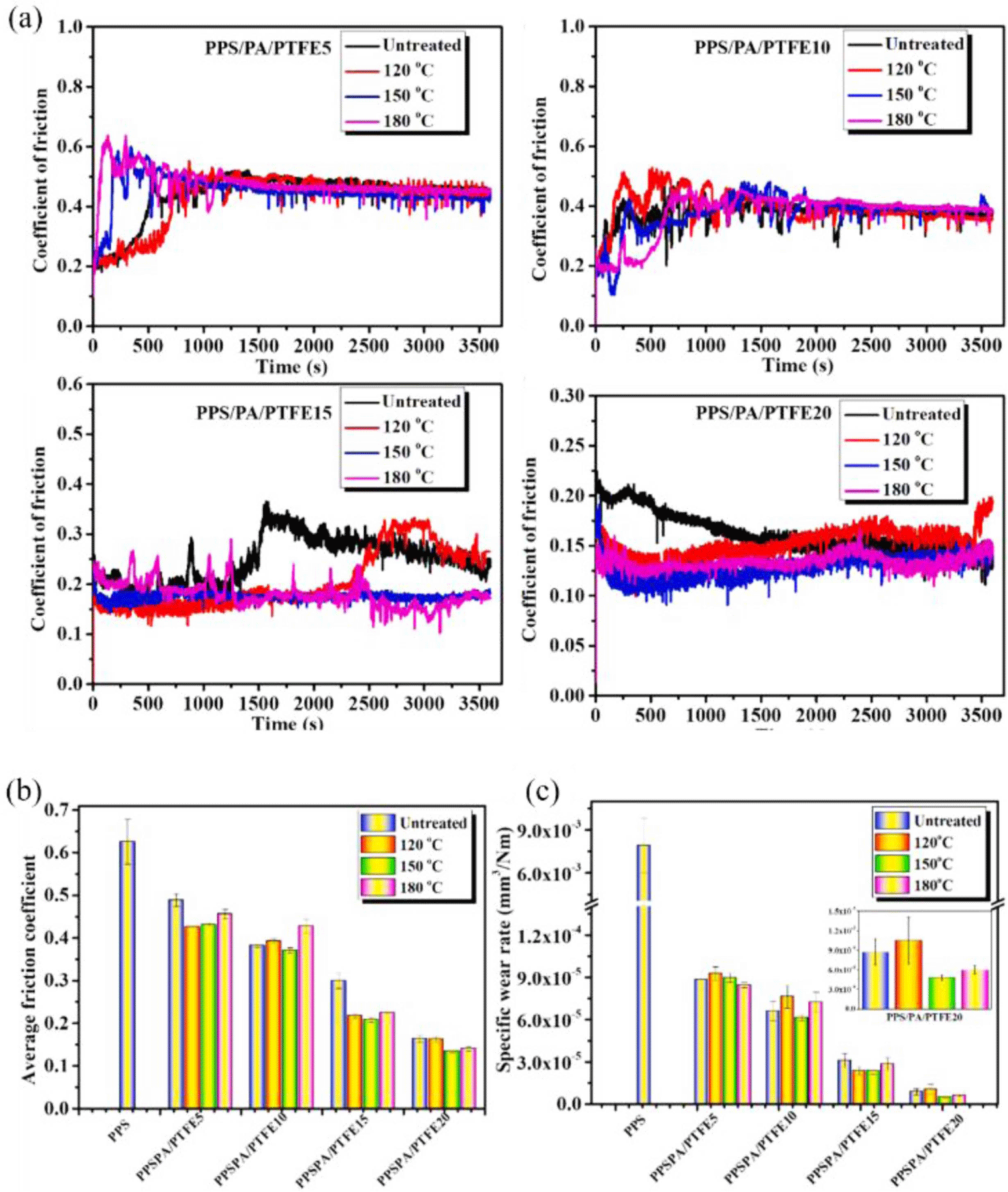
계면 접착력 개선
고분자와 보강재 사이의 계면 접착력은 복합재료의 응력을 전달하는 역할을 하기 때문에 중요한 요소 중 하나이다. 따라서 고분자와 보강재의 계면 접착력을 개선하는 것은 우수한 물성의 복합재료를 구현하기 위해서는 필수적이다. 이에 보강재와 고분자의 계면 접착력을 향상시키는 방법으로 첨가제 사용, 표면 개질, 그래프팅(grafting) 등 다양한 방법이 연구되고 있다.
Wu 연구팀은25 PPS와 탄소섬유의 계면 접착력을 향상시키기 위해 short carbon fiber (SCF) 표면을 산화 그래핀(graphene oxide, GO)으로 개질하여 복합재료를 제조하였다. 산화 그래핀의 표면은 에폭시기, 하이드시기, 카르보닐기와 같은 화학 작용기가 많기 때문에 SCF를 산화 그래핀으로 코팅하여 사용하면 계면 특성을 향상시켜 PPS에서 탄소섬유로 응력을 효과적으로 전달할 수 있다. PPS와 탄소섬유의 계면 접착력을 확인하기 위하여 촬영한 SEM 사진을 보면, 산화 그래핀으로 처리하지 않은 경우, PPS와 탄소섬유 사이에 공극이 관찰되지만 산화 그래핀 처리를 한 탄소섬유를 사용한 경우, 고분자와 섬유 사이의 계면 접착력이 개선되어 공극이 사라진 것을 확인할 수 있다(Figure 13(a)). 또한 인장 강도도 151 MPa에서 170 MPa까지 향상된 것을 확인할 수 있다(Figure 13(b)).
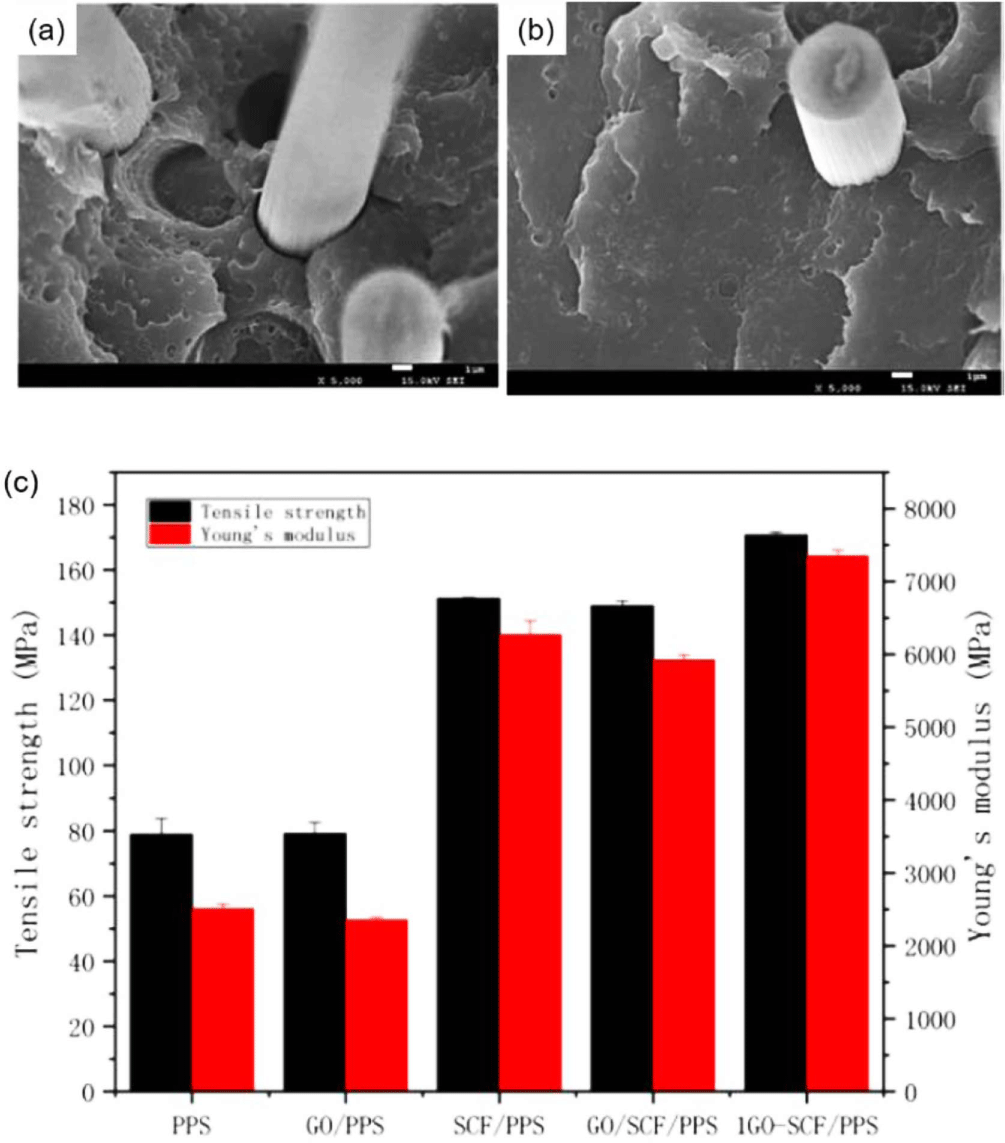
또한, 첨가제를 사용하여 계면 접착력 및 혼화성을 높이기 위한 연구도 수행되고 있다. Yang 연구진은26 카르복실 그룹을 포함하는 modified PPS (PPS-COOH)를 합성하여 적용하였다(Figure 14(a)). 이를 사용하여 PPS-CF의 interfacial shear strength (IFSS) 시험 결과 PPS-COOH를 사용하였을 때 IFSS의 값이 36.1 MPa에서 49.1 MPa까지 상승하는 결과를 얻을 수 있었다(Figure 14(b)). 이는 PPS-COOH가 CF표면에 있는 –OH 또는 에폭시 같은 작용기와 화학 반응 및 분자간 인력을 형성하기 때문으로 보인다(Figure 14(c)). 이와 유사한 방법으로, –COOH를 -NH2로 변경하여 연구한 결과도 보고되었다.27
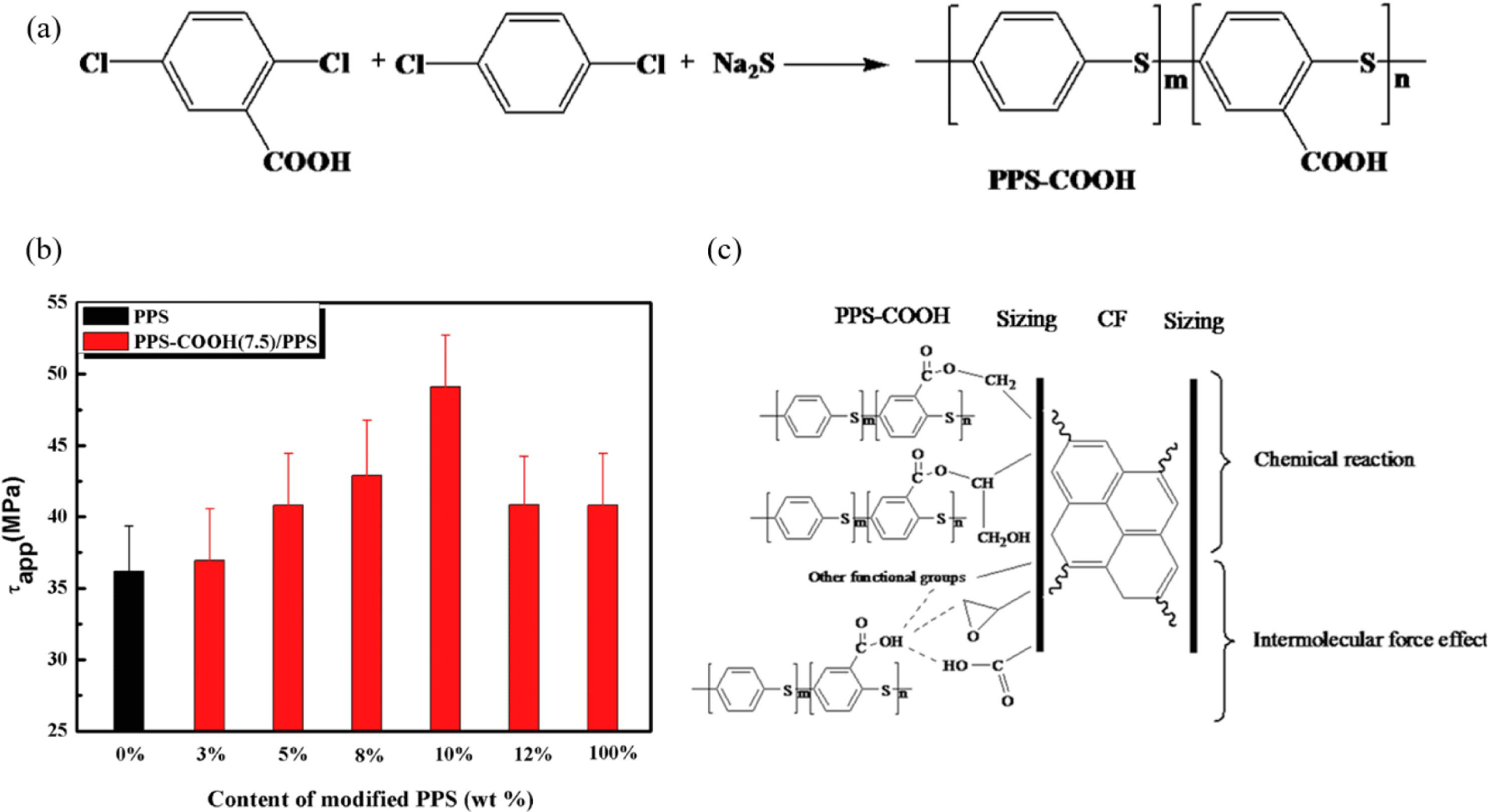
Durmaz 연구팀은28 Joncryl (ADR-4300F, BASF), amino-propyl polyhedral oligomeric silsesquioxane (APOSS), 2,2'-(1,4-Phenylene)bis(4-oxazoline) (PBO)를 첨가제로 사용하여 계면 접착력을 향상 시킨 연구결과를 보고하였다. 세 종류의 첨가제 모두 인장강도를 향상시키는 결과를 얻을 수 있었다(Figure 15(a)). 위 첨가제는 탄소섬유 표면의 작용기와 반응하거나 PPS의 말단기인 –SH와 반응하여 계면 접착력을 개선하고 (Figure 15(b)), 이로 인해 인장 강도도 증가하였다.
이처럼 PPS와 탄소섬유 사이의 계면 접착력은 우수한 기계적 물성을 구현하는데 필수적이고, PPS/CF 복합재료를 통해 우수한 물성을 구현할 수 있을 것으로 기대된다.
Conclusions
PPS는 구조적 특징으로 인해 자체 난연성, 내화학성 및 우수한 기계적 물성을 가지고 있다. 이에 항공우주, 자동차 경량화 소재 및 분리막 등의 소재로 사용하기 위해 목적에 맞는 기능성을 부여하기 위한 다양한 PPS 복합재료의 연구가 진행되고 있다. 하지만, 실제 PPS 복합재료를 적용할 경우 기대한 만큼의 최적의 물성을 구현하지 못하는 경우가 있는데, 이는 PPS와 보강재의 낮은 계면 접착력 때문이다. 본 논문에서는 PPS의 내충격, 내마모 및 방열 특성을 향상시키기 위한 복합재료 연구동향에 대해 소개하고, PPS와 보강재 사이의 낮은 계면 접착력에 의한 문제를 해결하기 위해 보강재와 PPS의 혼화성을 향상시킬 수 있는 첨가제 및 표면 개질 방법에 대한 연구도 함께 소개하였다. 최근에 금속을 대체할 수 있는 경량화 소재에 대한 수요가 지속적으로 증가하고 있다. 슈퍼엔지니어링 플라스틱 중 하나인 PPS를 활용한 복합재료는 이러한 수요를 충분히 만족시킬 미래소재로서 잠재력을 갖고 있으며, PPS의 단점을 보완하고 보강재의 장점을 적극적으로 활용하여 다양한 분야에서 활용할 수 있기를 기대한다.