Introduction
Fluorosilicone rubber (FVMQ) is a versatile elastomer with exceptional performance. Its high impact resistance and mold-ability allow it to be used in automobiles, aerospace, and electronics. Furthermore, the fluorine groups of the side chains of FVMQ results in superior barrier properties against a variety of media (e.g., gas, oils, fuels, acids), qualifying it for use in sensitive environments and other specific situations.1-8 However, such special applications require high temperature resistance (above 250 °C) and, as is known, the working temperature of FVMQ is -60 °C to 200 °C.9
Thermal-oxygen aging of rubber elastomers was an inescapable engineering challenge in normal application environments.10 In addition, the study of the aging and degradation of silicone rubber under heat and oxygen impact has become a hot topic.11-14 The aging mechanism of silicone rubber in the thermal oxidative environment was primarily comprised of two situations: the degradation or reversion of the main chain to produce low molecular weight cyclo-siloxanes; the oxidation of silicone rubber’s side groups which changes the molecular chain structure.15,16 How to prevent silicone rubber molecular chain damage in high temperature environments is the key to improving silicone rubber thermal stability.
The most common way to prevent this type of degradation is to use antioxidants like metal oxides as free radical stabilizers.14-17,18 However, some elastomers may be delayed or even prevented from being vulcanized as a result of adding these antioxidants, which could easily affect the performance of materials.19 In contrast, inorganic nano-particles such as fumed silica, quartz, and carbon black could improve the mechanical and thermal properties of rubber-matrix composites.20-23 Silica is one of the most widely used fillers in the rubber industry. When silica interacts with silicone rubber, it forms a high level of specific hydrogen bonding between the surface silanol groups of the silica and the polyorganosiloxane chain which is called “crepe hardening”.24 This formation can decrease the mobility of molecules that affects the degradation of the main chain of silicone rubber as it mentioned above.25 Kang et al. reported that adding silica to silicone rubber has increased the initial decomposition temperature, the char of composites at 800 °C, and the temperature of the maximum rate of degradation.26 Nazir et al. reported the thermal stability characteristics of the composites at the temperature of 5, 25, and 50 % weight loss of filled composites have improved by adding silica to silicone rubber.27
With the above considerations in mind, different amounts of silica-loaded FVMQ/Silica composites were prepared and investigated in terms of dispersibility, mechanical properties, thermal stability, and vulcanization.
Experimental
Fluorosilicone rubber (FE 271U) as a raw rubber was purchased from Shin-Etsu Chemical Co., Ltd., Tokyo, Japan. Fumed Silica (Aerosil-300, BET area: 270-330 m2/g) was purchased from Evonik Industries, Germany. Di(tertbutyl-peroxyisopropyl)benzene (Perkadox 14S-FL) as a curing agent was purchased from Nouryon, Amsterdam, Netherlands.
After 1.5 min of mastication FVMQ, fumed silica was added and mixed for an additional 5 min. When the torque value of the composite became stable, the curing agent was added and mixed for another 1.5 min, and the compounding was completed. Composites were prepared using an internal mixer (300 ml kneader, Brabender Gmbh & Co. KG, Duisburg, Germany) based on the formulation shown in Table 1 with 50 °C initial temperature and using rotor speed of 60 rpm for 8 min. The filler factor was set at 75% of the mixer capacity and the input unit was administered on a rubber basis with the parts per hundred rubber (phr). The resulting composites were vulcanized using a heat press at 170 °C and 10 MPa for 10 min, and then post-cured in an oven at 200 °C for 4h.
Sample | T0 | T1 | T2 | T3 |
---|---|---|---|---|
FVMQ | 100 | 100 | 100 | 100 |
Silica | 0 | 1 | 3 | 5 |
Perkadox 14S-FL1 | 0.5 | 0.5 | 0.5 | 0.5 |
The morphology of the fumed silica in the polymer matrix was investigated by field-emission scanning electron microscopy (FE-SEM; JSM-6701F, JEOL Ltd., Tokyo, Japan) at an accelerating voltage of 15 kV under an N2 atmosphere. Before the observation, the specimens were cryogenically broken after immersion in liquid nitrogen and then coated with gold.
Cure characteristics of composites were analyzed using RPA (RPA Elite, TA Instruments Inc., New Castle, DE, USA) under 170 °C for 10 min at an oscillation angle of ± 1°.
The mechanical properties of vulcanizates were measured using a universal testing machine (UTM, DUT-500 CM, Dae Kyung Engineering Co., Ltd., Bucheon-si, Gyeonggi-do, South Korea) according to the test method A in ASTM D 412 at room temperature. The dimension of the test specimens was 100 mm × 25 mm × 2 mm in size. The crosshead speed was 500 mm/min, and at least 5 samples were used to measure the mechanical properties.
Vulcanizates samples were prepared in 10 mm × 10 mm × 2 mm sizes and immersed in 30 mL THF for three days to evaluate the crosslink density of composites. Crosslink density was calculated by using Flory – Rehner equation (1).
V: Crosslink density (mol/g)
Mc: average molecular weight between crosslink points (g/mol)
Vr: the volume fraction of rubber in the swollen gel at equilibrium
Vs: the molar volume of solvent (cm3/mol)
ρ: the density of the rubber sample (g/cm3)
χ: the polymer-solvent interaction parameter
Vr value at the Flory - Rehner Equation was obtained from the equation (2)
Wd: Weight of dried sample after swelling
Wf: Weight of filler in sample
Ws: Weight of sample after swelling
ρs: Solvent density
ρr: Rubber density
Thermogravimetric analysis (TGA) was conducted by (Universal V4.5A, TA Instruments Inc., New Castle, DE, USA) under the nitrogen atmosphere from room temperature to 800 °C at a heating rate of 10 °C min-1.
To investigate the interactions between fumed silica and FVMQ, a simulation experiment was carried out. First, 100 g of fluorosilicone oil (FVMQ-O) was mixed with 0.5 g of fumed silica. The suspension was then aged by a sun lamp tester (Daesung Tester Co., Ltd., South Korea) for three days at 40 °C. The resulting fumed silica after separation, washing by ethyl acetate, and drying was characterized by Fourier transform infrared spectroscopy (FTIR) (Jasco Inc., Easton, MD, USA).
The thermal oxidative aging treatment was performed at 200 °C in a convection oven (OF3-15W, Jeio Tech Co., Ltd., Daejeon, South Korea) for 70 h. Then, the mechanical properties of composites were measured under the same conditions as previously described.
Storage modulus was measured by the strain-controlled rheometer (ARES-G2, TA Instruments Inc., New Castle, DE, USA) at 25 °C, frequency of 10 Hz, 0.01% to 10% strain, and torsion mode.
Results and Discussion
The morphology of fumed silica-filled FVMQ composites analyzed by SEM is shown in Figure 1. The neat rubber composite (T0) has a smooth texture, as can be seen. The small white line-like structures in image T0 are the result of quenching. In the T1 which is filled with 1phr fumed silica, the silica particles are well dispersed and shown as white dots (agglomeration size of silica: 13.6-16.2 μm) and T1 shows a similar texture to the T0 image. It can be easily observed that silicas begin to aggregate and converge in the T2 composite, and the silica aggregate size are also increased (20.6-25.9 μm). These agglomerations are even larger (31.0-48.5 μm) when we look at the 5phr fumed silica-filled T3 composite. The interaction of hydroxyl groups on the silica surface causes this aggregation.24 This filler-filler interaction is called Payne effect, and it indicates the network is formed between fillers.30
Cure characteristics that were measured by RPA and mechanical properties that were measured by UTM are shown in Figure 2 and Figure 3, respectively. Delta torque (ΔT) has described as the difference between maximum torque and minimum torque, and ΔT is very commonly related to crosslink density, which also affects the mechanical properties of composites such as tensile strength and modulus. Moreover, the crosslink density of vulcanized rubber is affected by two factors: filler-rubber interactions and chemical crosslinks.28-31
Table 2 shows that increasing the silica loading increases the ΔT, tensile strength, modulus at 100%, and hardness of FVMQ/silica composites. It is caused by a silica-fluorosilicone rubber system called “crepe hard-ening”. As previously stated, silica aggregates interact with one another via hydrogen bonding via the surface hydroxyl group and Van der Waals attraction. However, in the silica-fluorosilicone rubber system; the silica-polymer interaction can be formed due to hydrogen bonding between the hydroxyl groups on the silica surface with few residual terminal hydroxyl groups on the polymer chains and also possibly with the oxygen atoms in the fluorosilicone polymer molecule.24,31 It can increase the filler rubber interaction between silica and fluorosilicone rubber as well as the crosslink density. The mechanism of the silica-fluorosilicone rubber system can be seen in Figure 4.24
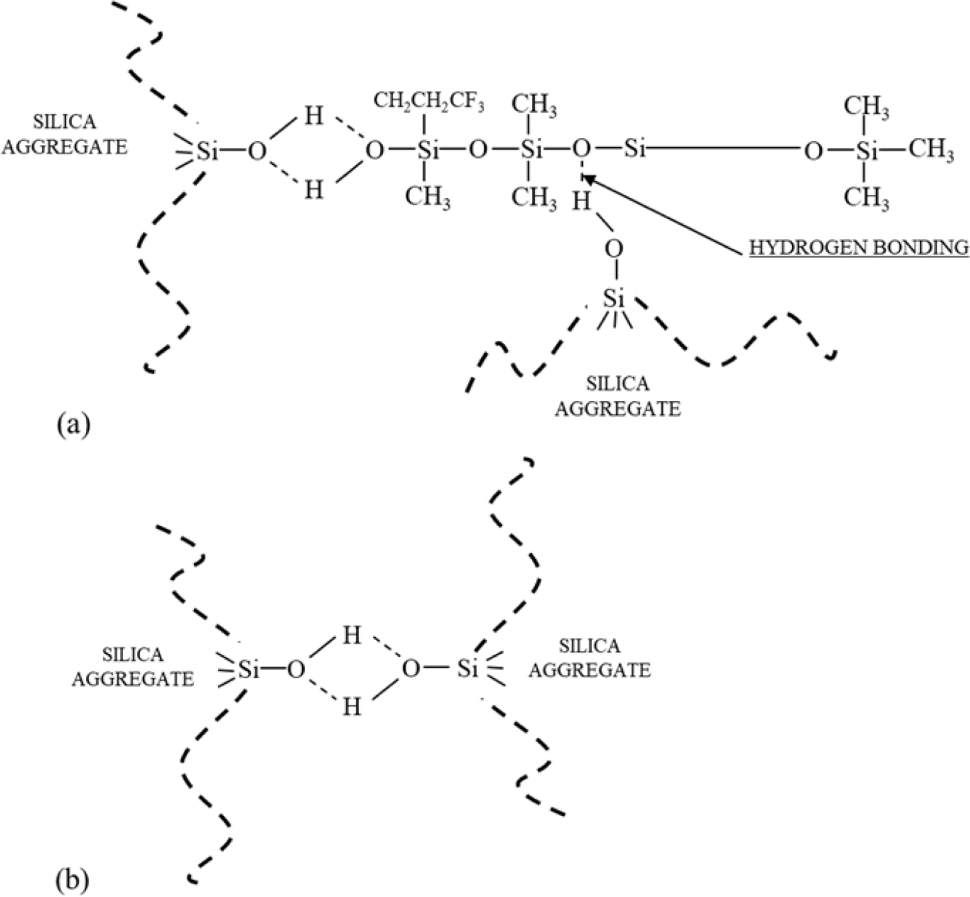
To confirm the silica-fluorosilicone rubber system, a crosslink density test was performed. As seen in Figure 5, the crosslink density of the composite increased as the amount of silica added to the composite increased. In addition, it is also seen that the crosslink density of the composite after thermal aging increases compared to before aging. This suggests that in the aging process, new crosslink formation outnumbers main chain degradation.

As mentioned before, the aging mechanism of silicone rubber in the thermal oxidative environment was primarily comprised of two situations: the degradation or reversion of the main chain to produce low molecular weight cyclo-siloxanes (Figure 6(a)); the oxidation of silicone rubber’s side groups which changes the molecular chain structure (Figure 6(b)).15,16
In order to investigate the principle of fumed silica improves the thermal stability of FVMQ, TGA was conducted to detect the degradation of composites in the nitrogen atmosphere. Figure 7 represents the TG, while Figure 8 represents the DTG curves. The details of mass loss data include the onset degradation temperature Td (defined as the temperature at 2% mass loss), characteristic temperatures T5, T20, and T50 (defined as the temperature at 5,20 and 50% mass loss, respectively) and the final residue (defined as the mass remaining at 800 °C) are listed in Table 3.
Sample | Td/°C | T5/°C | T20/°C | T50/°C | Final residue/% |
---|---|---|---|---|---|
T0 | 400.7 | 443.7 | 504.6 | 538.2 | 34.5 |
T1 | 405.4 | 447.8 | 504.9 | 539.9 | 35.0 |
T2 | 408.9 | 450.5 | 505.9 | 539.5 | 36.4 |
T3 | 409.3 | 449.9 | 505.4 | 539.7 | 37.6 |
Sample | Td/°C | T5/°C | T20/°C | T50/°C | Final residue/% |
---|---|---|---|---|---|
T0 | 384.3 | 403.1 | 431.6 | 476.0 | 40.8 |
T1 | 387.7 | 405.7 | 435.9 | 478.7 | 41.6 |
T2 | 388.6 | 407.4 | 436.3 | 475.6 | 43.1 |
T3 | 392.4 | 410.4 | 436.5 | 473.6 | 45.4 |
Considering the TGA analysis, it turns out that only main chain degradation can be observed the under the nitrogen atmosphere since there is not much difference between the curves. And the depolymerization of FVMQ is just dominated by the random main chain scission mechanism.32-34 FVMQ thermally decomposes to cyclic oligomers during depolymerization via Si-O bond scission in a chain folded cyclic conformation energetically favored by the overlapping of empty silicone d-orbitals with oxygen and carbon atom orbitals.35 Furthermore, the formation of an intermolecular cyclic transition state, which is influenced by molecule mobility, is the rate-determining step in the depolymerization process.25
In the nitrogen atmosphere, the pristine FVMQ was relatively stable till the temperature reached 400.7 °C. In contrast, adding only 1phr of fumed silica increases the degradation starting temperature of the composite to 405.4 °C, while it is seen that the degradation starting temperature increases with the increasing amount of fumed silica. Furthermore, when the residual mass data is examined, it is clear that increasing the amount of silica increases not only the degradation temperature but also the final residue of composites at 800 °C. In addition, the presence of a single peak in the DTG analysis composites represents the volatilization of cyclic oligomers formed by siloxane rearrangement (Figure 6(a)). The flexibility of the polymer chain segments and the high polarity of the Si-O bonds influence this degradation mechanism.33 As it explained before, in the silica-fluorosilicone rubber system; the hydrogen bonding can be formed between the hydroxyl group on the silica surface with the terminal hydroxyl groups on the polymer chain and also with the oxygen atoms in the silicone polymer molecule. It is believed that such bonding interaction reduces the mobility of the FVMQ chain, which can improve barrier resistance and thermal stability.25,27
Figures 9 and 10 represent the TGA analysis in the air atmosphere. With the presence of oxygen, the side groups of FVMQ (-CH3 and -C2H4CF3) can be easily oxidized to generate reactive oxygen species (Figure 6(b)) that could hasten the deterioration of FVMQ by initiating circular chain cleaving reactions, so the Td for the composites drop. Furthermore, as in the nitrogen atmosphere, in the TG analysis performed in the air atmosphere, the degradation starting temperature (Td) of the composites increased with the increase of the silica content. At the DTG graph of the air analysis, we can see that a second peak, indicated by the arrow, has appeared in the T0 composite. With the addition of silica to the composites, it is seen that this peak decreases in T1 and completely disappears in T2 and T3 composites. This can indicate that silica has a high antioxidant ability and can protect FVMQ against oxidative degradation.
FTIR spectroscopy peak analysis was carried out to examine silica silicone system. UV irradiation was replaced thermal aging as a method of decomposition. Figure 11 represents the FTIR spectra of fumed silica before and after interaction with the FVMQ-O. The FTIR spectrums show that similar peaks of FVMQ-O, attributed to the Si-C bond, appear on the silica surface after UV aging at 1210 cm-1 and 1266 cm-1. This verifies Si-C bond cleavage from the polymer along with a new Si-C formation on the fumed silica. Moreover, the C-F number 1332 cm-1 peak observed on FVMQ-O does not appear on silica, demonstrating that the Si-C bond on silica does not result from a possible bond rubber interaction.
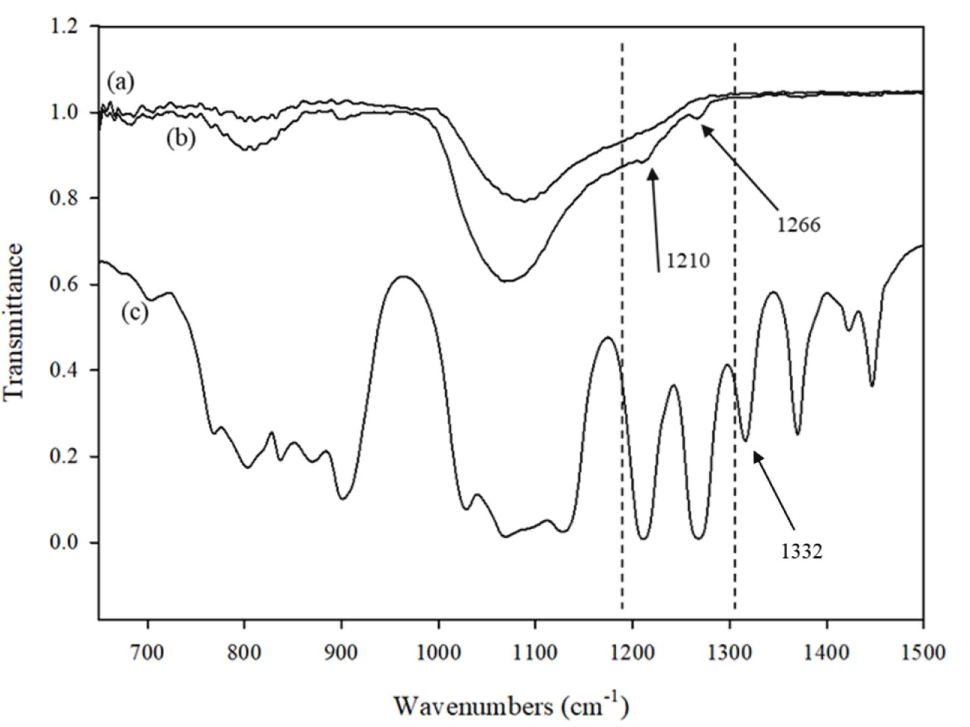
The aging performance of FVMQ/silica composites is evaluated by the change ratio of the tensile strength (TS), change ratio of elongation break (EB), and change ratio of modulus at 100% (MD), which are shown in Figure 12-14, respectively. After the thermal aging of the pristine T0 composite, its TS, EB, and MD changed by -8.83%, -13.27%, and 9.5%, respectively. In contrasts, the rates of change in TS, EB, and MD of filled composites after thermal aging were as follows: -7.38%, -8.27%, and 2.88% for composite T1; -10.20%, -4.38%, and -2.07% for composite T2; and -19.65%, -15.95%, and -7.41% for composite T3. Considering changes in tensile strength, elongation at break, and modulus at 100% after thermal aging, composites T1 and T2 outperformed composite T0 in terms of thermal oxidative performance. However, the T3 composite showed a much worse thermal oxidative performance than the pristine T0 composite. This may be due to the deterioration of the filler dispersion of the T3 composite after thermal aging. When the main polymer chain degrades during heat aging, the silica may form hydrogen bonds between the silica surfaces instead of forming hydrogen bonds with the silica polymer chain, which increases the filler-filler interaction.
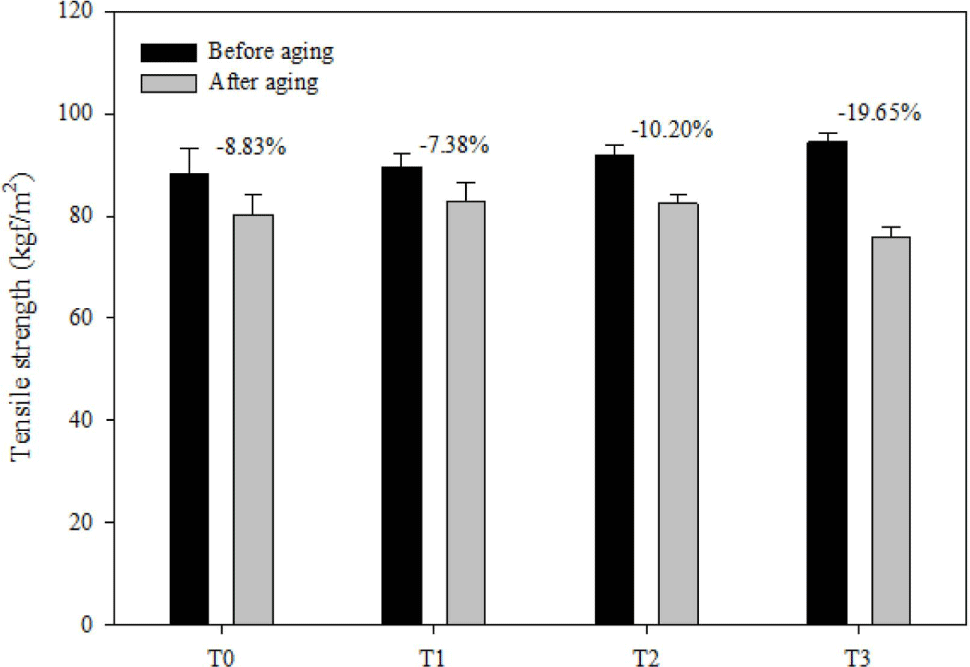
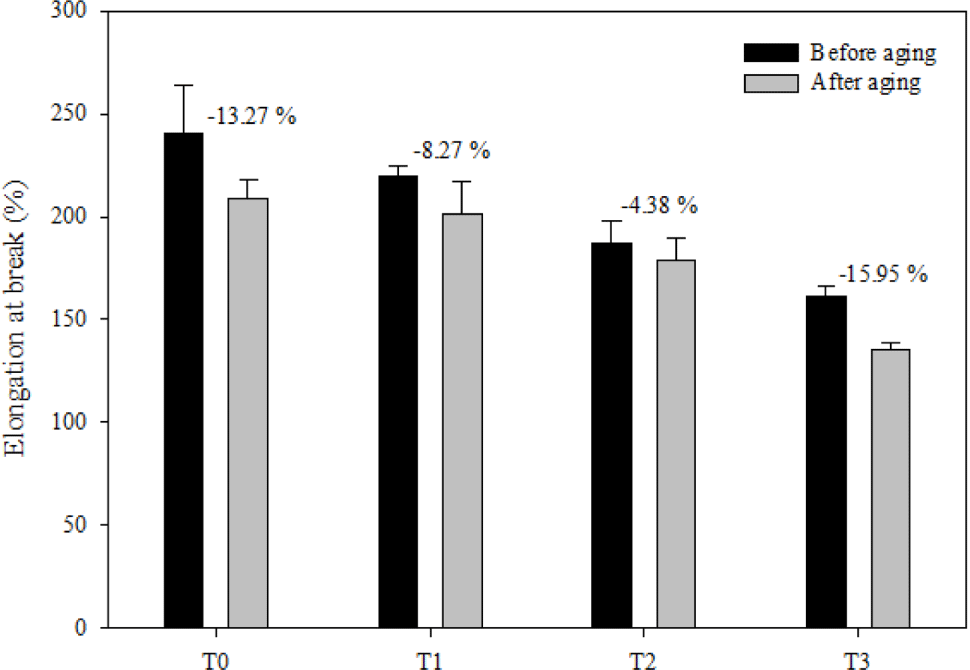
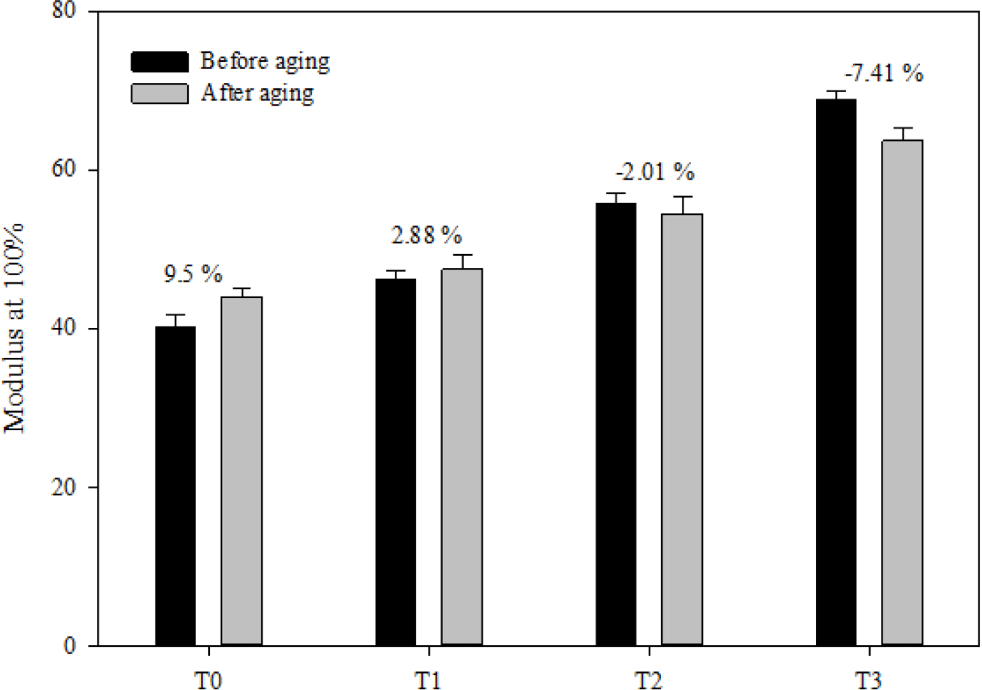
Figure 15 demonstrates the SEM analysis of the filler dispersion of silica-filled composites after thermal aging. When the SEM analysis pictures are examined, it is seen that the silica dispersion of the T1 and T2 composites do not change or show a little change after thermal aging; However, it was observed that the silica dispersion of the T3 composite changed drastically, and the silica aggregation increased.
The Payne effect of the T3 composite was measured by ARES in order to analyze its silica dispersion, which is shown in Figure 16. Payne effect can describe as the difference of storage modulus (G′) at low and high strains which represents dispersion of filler in rubber composites. A decrease in the storage modulus with increasing strain amplitude is result of the destruction of the filler network. The larger ΔG′ value, the strong filler-filler interaction.30
The ΔG value of T3 composite before aging was 4.49 MPa. After the aging, it has increased to 6.39 MPa. That means the filler-filler network in the T3 composite has increased 29.12%. That means interaction of hydroxyl groups on the silica surfaces increase while the interaction between silica and polymer decreases. Thus, thermal oxidative stability of T3 composite decreases.
Conclusions
The effect of fumed silica loading on the thermal stability and mechanical properties of FVMQ rubber has been investigated. FTIR, TG analysis, and tensile testing before and after thermal aging were used to investigate the effect of silica-fluorosilicone rubber system on the thermal stability of FVMQ rubber. The results exhibited that the hydrogen bonding between silica and FVMQ increased with the increasing of the amount of silica loading. Additionally, due to this interaction, crosslink density and mechanical properties of composites increased. Finally, the hydrogen bonding between silica and FVMQ rubber limits the flexibility of the FVMQ chain, making ring-forming degradation of FVMQ difficult. As a result, the thermal stability of FVMQ rubber is enhanced.