Introduction
The electronic skin (e-skin) is the next form factor of electronic devices constructed with various functional components such as displays, integrated circuits, sensors, and power supplies with skin-like mechanical properties. It can be applied to the artificial skin of smart robotics for imparting bimodal sensing to robots, which leads to high energy consumption and requires energy harvesting/storage devices with high energy densities and capacities.1-3 For the power source of electronic devices, thermoelectric (TE) energy has been rising as a renewable and sustainable energy source.4,5 The TE devices enable directly convert from various heat sources to renewable energy. Moreover, harvesting the heat energy emitted from the human body is the most efficient method to obtain continuous electrical power for the e-skin.6-9
The e-skin devices need skin-like mechanical properties, including conformal adherence to the human body, stretchability, and softness. Furthermore, the e-skin power sources require skin adaptability to endure tensile and compressive strains under dynamic movements (folding, twisting, and stretching). Due to these properties, power sources should be mechanically durable against unexpected damages without performance degradation.10-12 The skin-adaptable TE materials are introduced with intrinsic or extrinsic stretchability and physically reconfigurable properties to withstand at least 30% strain and have a low Young’s modulus (≤ 10−1 MPa).13-16
Carbon nanotubes (CNTs) are highly nominated for stretchable TE materials due to various excellent properties, including good TE performance and the one-dimensional electrical pathway for stretchability.17,18 In our previous work, we introduced the blending of CNT clays with non-ionic liquid surfactants (Triton X-100) as viscous additives.19 Through the blending of CNTs powder with a viscous additive, the mixture had a flour dough-like clay texture with reconfigurable properties. In this result, the skin-adaptable p-n paired TE energy harvesting patches consisting of the reconfigurable and stretchable CNT clays were introduced. The TE e-skin patches preserved electrical performance up to 100% strain and 50 times re-molding due to clay texture properties. Moreover, using tetracyanoquinodimethane (TCNQ) as a p-dopant and triphenylphosphine (TPP) as an n-dopant for chemical doping with CNT:Triton X-100 enhanced TE performance such as electrical conductivity, Seebeck coefficient, and power factor. The doped CNT clays exhibited 58.5 S/cm, 48.1 S/cm as electrical conductivity, and 43.6 μV/K, -53.9 μV/K as the Seebeck coefficient for p-type and n-type, respectively. For higher thermoelectric energy harvesting, thermoelectric CNT clays need to be further developed.
In this work, we improved the thermoelectric CNT clay using thermoelectric enhancers for wearable energy harvesting e-skin patches. We introduced the physical and chemical doping for the thermoelectric CNT clays. The inserting of poly(3,4-ethylenedioxythiophene):polystyrene sulfonate (PEDOT:PSS) and dimethyl sulfoxide (DMSO) increased p-type TE performance. In addition, the insertion of liquid metal into CNT clays improved n-type TE performance. Finally, the TE energy harvesting patches laminated with biocompatible elastic film with three p-n junctions of CNT clays stably worked up to 50% elongation strain and their elastic modulus was similar to human skins.
Experimental
Single-wall CNTs (SWCNTs; TUBALLTM, ≥ 80%) were purchased from OCSiAl. Triton X-100 as a non-ionic surfactant was purchased from Sigma-Aldrich. Tetracyanoquinodimethane (TCNQ), triphenylphosphine (TPP) and eutectic gallium indium (EGaIn) were purchased from Sigma-Aldrich. Poly(3,4-ethylenedioxythiophene):polystyrene sulfonate (PEDOT:PSS) (Clevious P) was purchased from Heraeus. Dimethyl sulfoxide (DMSO; 99.8%) was purchased from SAMCHUN. All materials were used without any purification.
To fabricate p-type CNT clays, SWCNTs and Triton X-100 were mixed at 1:5 weight percent after dissolving TCNQ at 5 wt% in Triton X-100 by using a vortex mixer (VM-10, Daihan Scientific) for 1 minute and then sonicated for 10 minutes (Ultra-sonic Cleaner, Daihan Scientific). After blending the above chemicals, PEDOT:PSS and DMSO were added to CNT clays following each ratio. Blending materials were mixed using a centrifugal mixer (ARE-310, THINKY) at 1000 rpm for 10 minutes. After mixing, the p-type clays were annealed at 80 °C for 1 day to remove the residual solvent.
To fabricate n-type CNT clays, SWCNTs and Triton X-100 were mixed with the same ratio as p-type CNT clays. Single-doped n-type CNT clays were fabricated by adding EGaIn following each ratio. In the case of dual-doped n-type CNT clays, 0.1 wt% TPP was added into Triton X-100 and mixed with other components. After using a centrifuged mixer, the clays were directly measured without annealing.
The Seebeck coefficient was measured using customized TE equipment which is connected to two copper plates with Peltier devices controlled by the source meter (Keithley 2400) and the multimeter (Keithley 2700) with the K-type thermocouple.19 The electrical conductivity of CNT clays was measured using a four-probe meter (MCP-T610, MITSUBISHI). The electrical conductivity under strain was calculated after measuring by using Cu wire connected to CNT clay, which is contained in an elastic sponge encapsulated by biocompatible TegadermTM film (3 M, 1624 W). The strain stress curves were obtained using fully encapsulated Tegaderm film, which contained three-pair modules, by using the force tester (AND MCT-2150, elongation rate: 10 mm/min).
Results and Discussion
Figure 1(a) exhibits an image of the reconfigurable TE e-skin patches with three p-n paired CNT clays. Following our previous work, CNT clays were fabricated by the SWCNTs and non-ionic liquid surfactants (Triton X-100) as viscous additives with 1:5 weight ratio. As a result, the CNT clays were kneaded together with the viscous additive to form the whole clay-like texture. To achieve p-n module structure and enhance the TE properties of the CNT clays, p-type and n-type chemical doping and physical blending of the CNT clays were developed. Figure 1(b) shows the schematic illustration of the p-type and n-type doped CNT clays. The TCNQ was used as a p-type dopant in the CNT clays to further increase their positive Seebeck coefficient, positive charge carriers, and electrical conductivity. Moreover, PEDOT:PSS, known as the p-type enhancer, was used to increase electrical conductivity.20 To further increase electrical performance, DMSO was introduced to remove PSS. On the other hand, Eutectic Gallium Indium (EGaIn) was used as the typical n-type enhancer to increase the negative Seebeck value, negative charge carriers as well as the electrical conductivity of the CNT clays.
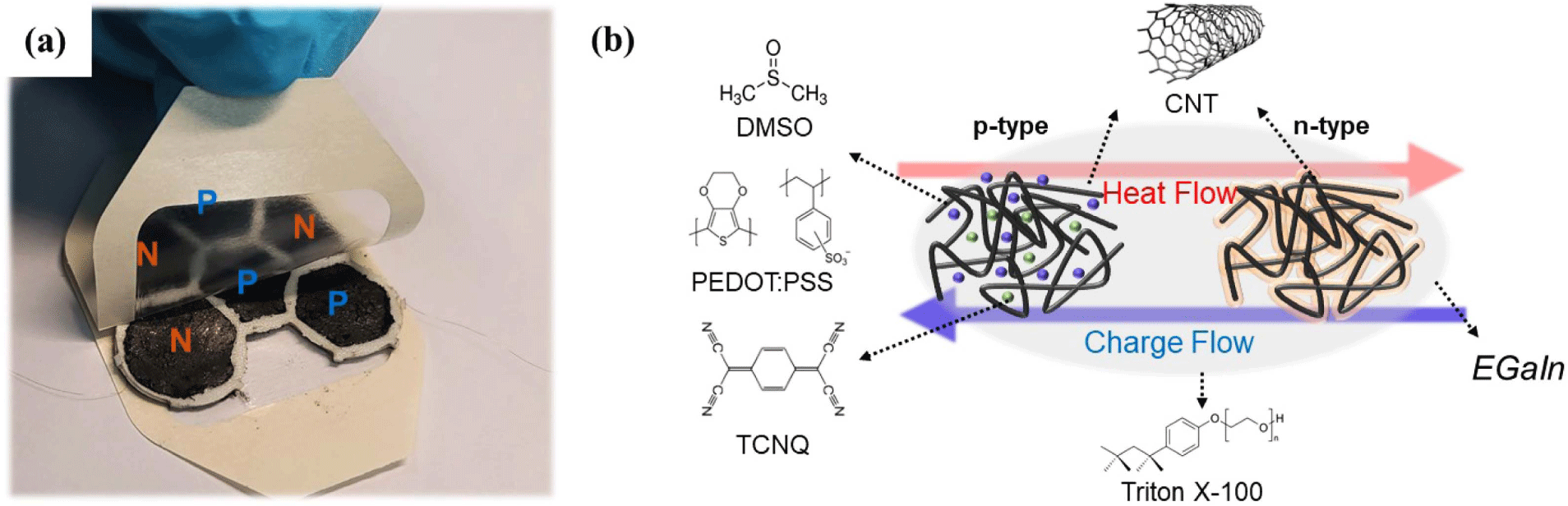
Figure 2 shows the TE performance of the p-type doped CNT clays. With the previously optimized 5% weight ratio of TCNQ dopant, the p-type CNT clays showed a positive Seebeck coefficient (43.6 μV/K) and an electrical conductivity of 58.5 S/cm. After that, PEDOT:PSS was introduced as a physical enhancer to improve the performance of TCNQ-doped CNT clays. The electrical conductivity of the CNT clays was maximized at 100 wt% PEDOT:PSS (70.5 S/cm) and slightly decreased at over 100 wt% PEDOT:PSS contents, as shown in Figure 2(a). PSS is the solubilizer to be soluble PEDOT; however, PSS can decrease electrical conductivity due to the sulfonic acid groups of the PSS chains.21 To overcome that limitation, some reports22,23 incorporate additives such as ethylene glycol (EG) and DMSO to increase electrical conductivity and Seebeck coefficient by removing the PSS chain. In Figure 2(b), the electrical conductivity of CNT clays linearly increased and reached a maximum value (103.76 S/cm) at 5 wt% DMSO due to the selective removal of excess insulating PSS within the CNT clays. However, exceeding the 5 wt% condition, the decrease in electrical conductivity occurred upon further increasing the contents of DMSO due to the inducing agglomeration of the PEDOT molecule with the surrounding PSS chain.24Figure 2(c) exhibited electrical conductivity (σ), Seebeck coefficient (S), and calculated power factor from equation (1). The results clearly indicated that the combination of 5 wt% TCNQ, 100 wt% PEDOT:PSS, and 5 wt% DMSO is the optimal blend condition for the p-type dopant in the TE generator.
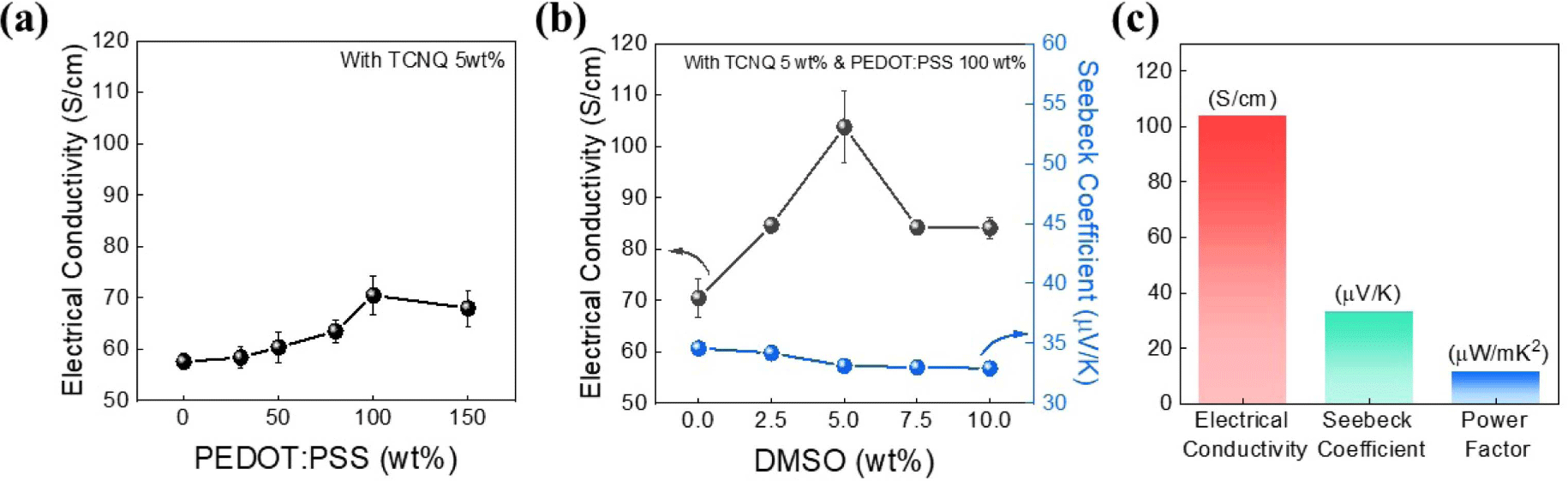
Moreover, the n-type doping of the CNT clays is an essential component for achieving TE modules. Figure 3 shows the TE performance of the n-type CNT clays with TPP for chemical doping and EGaIn for physical blending systems. The TPP can generate better chemical bonding to enhance the free charge carrier for n-type doped CNT clays. Liquid metal (EGaIn) is well known as an n-type material that can interconnect with each CNT to improve the TE properties without the reduction of performance under strain.25 In Figure 3(a), with optimized 1 wt% TPP, the electrical conductivity of doped CNT clays (48.08 S/cm) is higher than that of pristine clay (27.67 S/cm). For further increasing n-type performance, EGaIn is used as the n-type enhancer. The electrical conductivity linearly increases with higher content of EGaIn up to 98.27 S/cm at 200 wt% EGaIn. Moreover, only EGaIn-blended clay showed a similar trend and value of increasing the electrical conductivity compared to that without using the TPP dopant. However, CNT clays cannot maintain mechanical properties like clay texture exceeding EGaIn 200 wt% blending ratio. To compare the TE performance of dual-doped (chemically doped and physically blended) CNT clay and single-doped (only physically blended) CNT clay, Figure 3(b) exhibited the Seebeck coefficient of each CNT clay. The single-doped CNT clay showed a higher Seebeck coefficient (39.04 μV/K) than that of the dual-doped CNT clay (31.08 μV/K). From this result, the power factor of singled-doped CNT clay reached 14.6 μV/mK2 with 200 wt% EGaIn (Figure 3(c)).
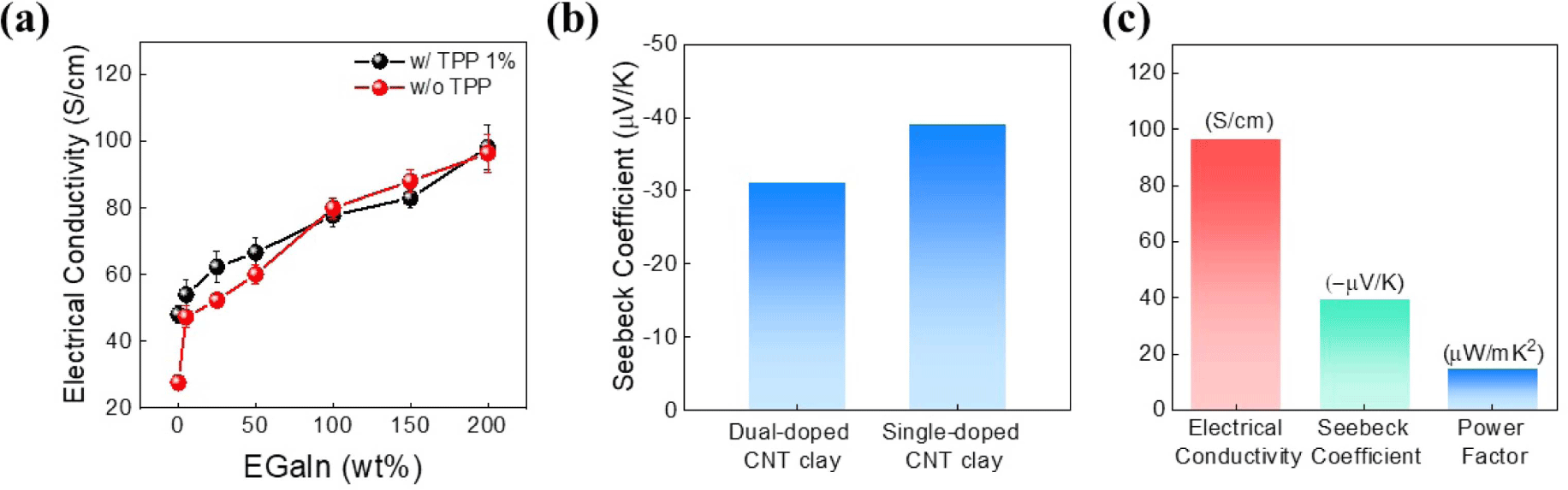
To demonstrate the application of the reconfigurable TE CNT clays with thermoelectric enhancers, a TE module of an energy-harvesting e-skin patch was designed and fabricated, as shown in Figure 1(a). The e-skin path consisted of three p-n paired CNT clays and was filled in hexagonal sponge walls, which were encapsulated by biocompatible elastic Tegaderm films. The stretchability of wearable TE materials is an essential mechanical property to effectively adapt the human body. The reconfigurable ability of the CNT clays can satisfy that elongation for stretchability. The TE e-skin patch was highly stretchable up to 50% strain without plastic deformation due to the elastic sponge frame and biocompatible elastic encapsulation film, as shown in Figure 4(a), (b). The p-type and n-type CNT clays maintained electrical conductivities and power factor values upon stretching up to 50% tensile strain (Figure 4(d)). Moreover, the cyclic strain and stress curves were shown to measure the quantitative mechanical stress during the stretching cycle from 10% strain up to 50% strain (with a 10% strain step), which is a higher strain than the stretchability of human skin (around 30% strain). In hysteresis loops, Young’s modulus of the TE e-skin patch exhibited a lower value (0.04-0.07 MPa) than the human skin value (10-1 MPa). These results indicate that the TE e-skin patch with CNT clays minimizes the foreign-body sensation with skin adaptability (Figure 4(c)). All results highlight the improved TE performance of e-skin patches with high durability and stability against large external strain.
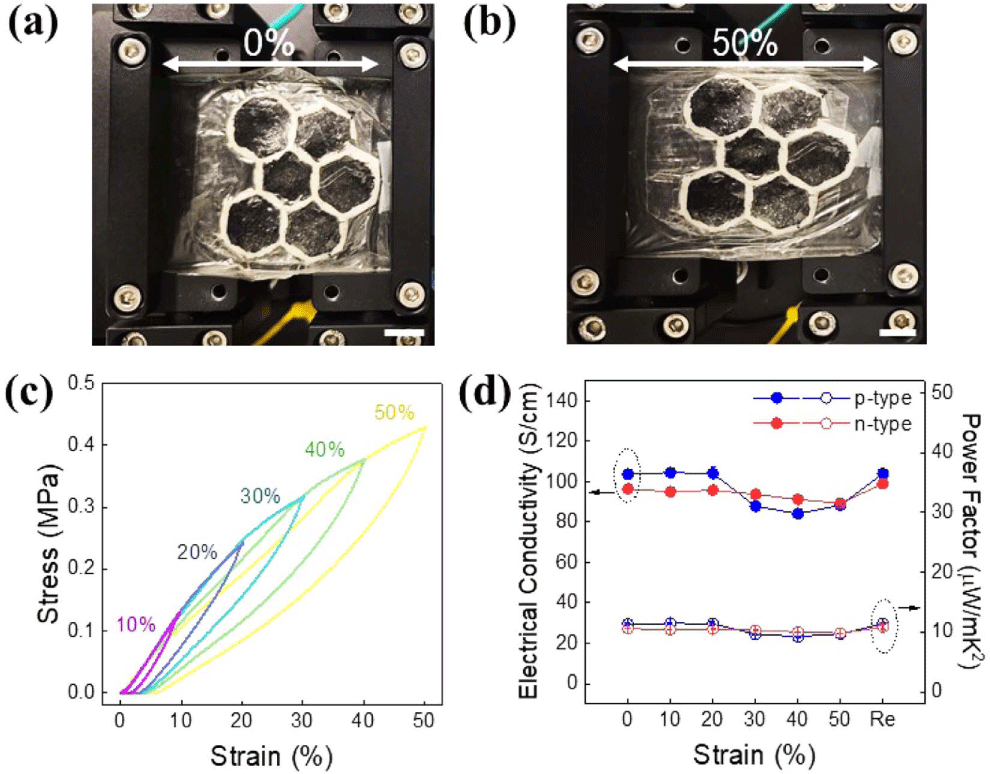
Conclusions
In summary, we presented thermoelectrically improved CNT clays with thermoelectric enhancers with high stretchability and re-moldability properties for application to stretchable and repairable TE devices. By optimizing the materials and the contents of thermoelectric enhancers, the reconfigurable thermoelectric CNT clays were afforded better characteristics and higher performance uniformity in both p-type and n-type devices. Finally, the stretchable TE e-skin patch consisting of three serially connected p-n pairs of CNT clays was manufactured, and its thermoelectric performances were evaluated under mechanical strain. The achieved e-skin patch with reconfigurability and low elastic modulus can be expected to fabricate skin-adaptable devices under the human skin’s strain range with uniform performance.