Introduction
Asphalt is the most commonly used material for road pavement.1-3 According to the researches on highways and paved roads, more than 90% of them are asphalt pavements in both Europe and the United States.2,3 When driving a vehicle, friction occurs between the tire and the asphalt road surface, and various wear particles are generated.4 Since aged and rough asphalt road surfaces can affect tire tread wear, regular maintenance is required.5 A typical asphalt pavement consists of a foundation subgrade followed by an aggregate base layer and an asphalt layer.6 The surface of asphalt is a mixture of various materials. On average, 95% of them are stone aggregates and 5% are binders (bitumen).7
Since bitumen is a petroleum material processed from crude oil, it contains various types of hydrocarbons, including polycyclic aromatic hydrocarbons (PAHs).8,9 Softeners derived from automobile engine oil and crumb rubber from scrap tires can also be added to the asphalt process.10,11 In addition, asphalt pavement adsorbs traffic-related substances produced on the road.6 When asphalt road wear particles (APWPs) are produced and introduced into the environmnet, PAHs and some metal components can cause environmental toxicity.11-13 Properties of asphalt pavement vary depending on the type and composition of fillers and additives.7,14,15 Asphalt pavement is a difficult material to analyze because it is highly inhomogeneous and has complex chemistry. Although there are many studies evaluating the quality of different asphalt additives,16-19 there is a lack of standard data on asphalt. Since APWPs exist in the environment, it is also necessary to analyze them.
Several methods are used to analyze asphalt components. Legret et al. analyzed PAHs and heavy metals present in asphalt pavement using gas chromatography (GC) and inductively coupled plasma-atomic emission spectroscopy (ICP-AES).11 Yin et al. analyzed the chemical composition of limestone and granite aggregate used in asphalt pavement through X-ray diffraction (XRD).20 Thermogravimetric analysis (TGA) is useful for analysis of the composition and thermal behavior of asphalt, and it is a simple and effective method.21-23 Among the saturates, aromatics, resins, and asphaltenes (SARA) in asphalt, asphaltene showed the highest thermal stability and had more aromatic and resin components.21,22
In this study, model asphalt pavement was prepared and it was broken into powder to obtain APWPs. A single APWP was analyzed using TGA, and the composition was determined. Raw materials used for manufacturing the model asphalt pavement were also analyzed to build the reference thermogram. Difference in the comppositions of APWPs was investigated, and the inhomogeneity depending on the particle size was examined.
Experimental
Model asphalt pavement was prepared by mixing bitumen, coarse aggregate, fine aggregate, calcium carbonate, and modifier. The formulation was presented in Table 1. The model asphalt pavement was supplied from Hansoo Road Industry Co. (Republic of Korea). The model asphalt pavement was crushed with a hammer to create APWPs. The APWPs were classified by size using a sieve shaker (Octagon 200, Endecotts Co., UK) and then APWPs of 212-500 μm (S-series, S-APWPs) and 500-1000 μm (L-series, L-APWPs) were used for analysis. Each ten APWPs were randomly selected, and their sizes and weights were listed in Table 2. Magnified images of the APWPs were obtained with an image analyzer (EGVM 35B, EG Tech., Republic of Korea).
Raw material | Weight percentage (wt%) |
---|---|
Bitumen | 5.5 |
Coarse aggregate | 66.0 |
Fine aggregate | 20.0 |
Calcium carbonate | 8.0 |
Modifier | 0.5 |
The raw materials and model APWPs were analyzed using TGA (Mettler Toledo Co., USA). The temperature was heated from 50 to 700°C in N2 atmosphere, and then from 700 to 900°C under air atmosphere. The heating rate was 20°C/min. The five raw materials were analyzed by about 10 mg. For the model APWPs, a single APWP was analyzed. Since a single particle is too small to obtain a good thermogram, an alumina ball (Korea Material Scientific Co., Republic of Korea) was put together into the crucible and analyzed to obtain a stable TGA thermogram. The three alumina balls (approximately 6 mg) with a diameter of 1 mm were used for each analysis.
In the case of analysis of the single APWP, additional data processing was performed. The values of alumina balls were excluded from the original thermogram. After peak smoothing, the final thermogram of each APWP was obtained.
Results and Discussion
Magnified images of the 20 APWPs used in this study were shown in Figure 1. TGA analysis of the five raw materials used for manufacturing the model asphalt pavement was performed, and their TGA thermograms were shown in Figure 2. Principal weight losses of the raw materials were summarized in Table 2. For the bitumen and modifier, there were four weight loss regions. The ash contents for the bitumen and modifier were 0.4 and 4.4%, respectively. For the modifier, almost organic components in the sample were vaporized or decomposed before introduction of air at 700°C, but the bitumen was remained 8.1% before the atmosphere change from nitrogen to air. Ash content of the calcium carbonate (CaCO3) was 70.2%, which is larger value than expected as pure CaCO3. When CaCO3 is heated, it is changed to CaO by loss of CO2 and the weight ratio of CaO/CO2 is 56/44=1.27. If the calcium carbonate used in this study is pure, the ash content should be 56%. The TGA thermograms of the stone components of coarse and fine aggregates were different from each other. The TGA thermogram of the coarse aggregate was similar to that of the calcium carbonate. The ash contents of coarse and fine aggregates were 74.8 and 98.8%, respectively.
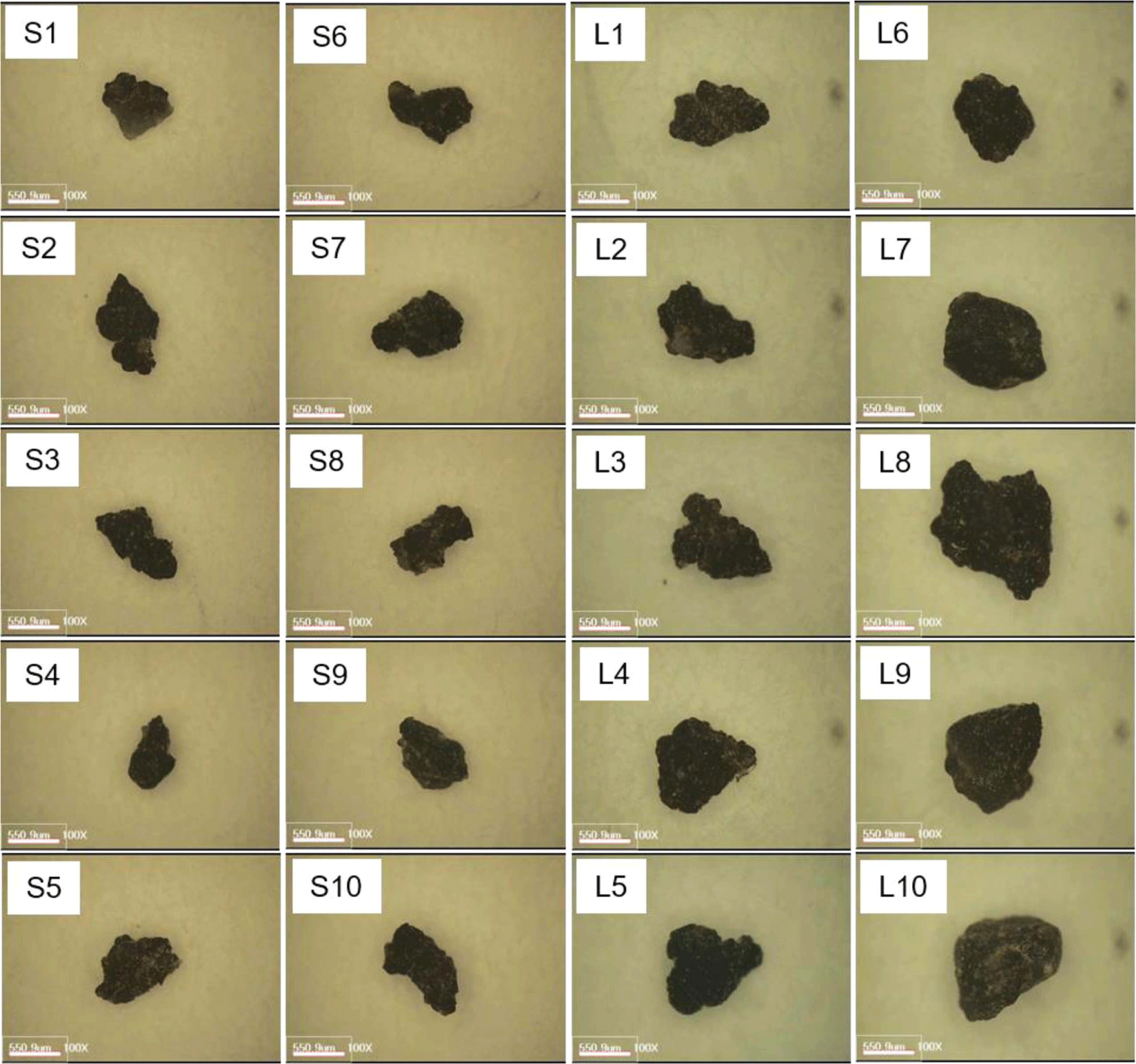
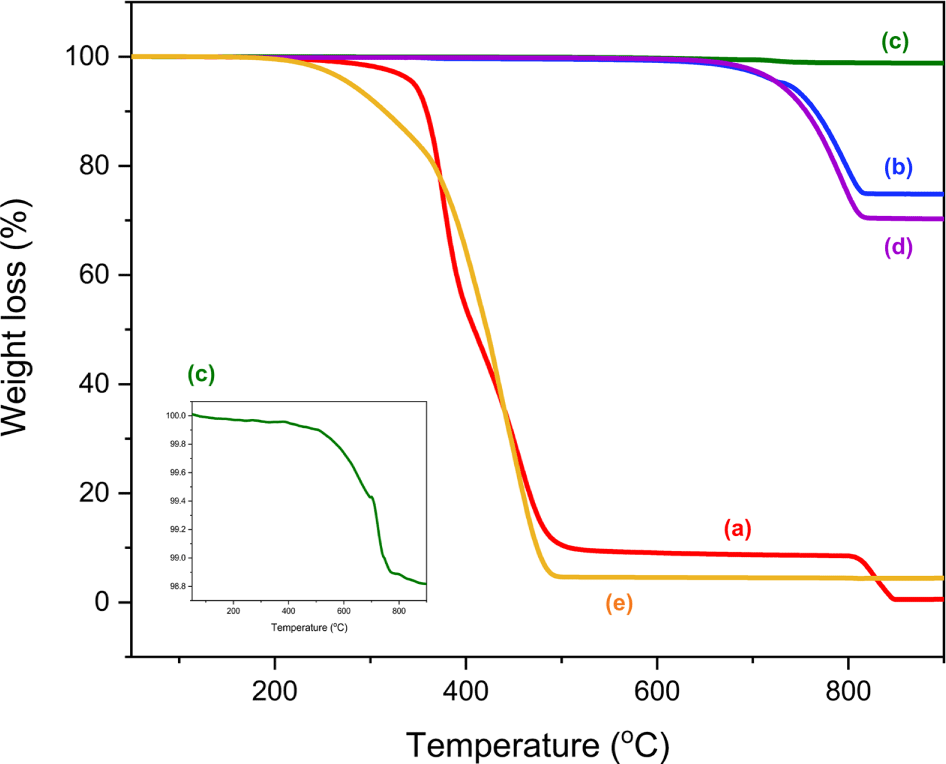
Reference TGA thermogram of the model asphalt pavement was built using the TGA thermograms obtained from the five raw materials used for manufacturing the model asphalt pavement and their ratios in the formulation (Figure 3). There were four weight loss regions at 50-345, 345-492, 492-850, and > 850°C in the reference TGA thermogram, corresponding to the volatile organics (VO), polymeric materials (PM), decomposed components in inorganic matter (DI), and ash, respectively (Table 4).
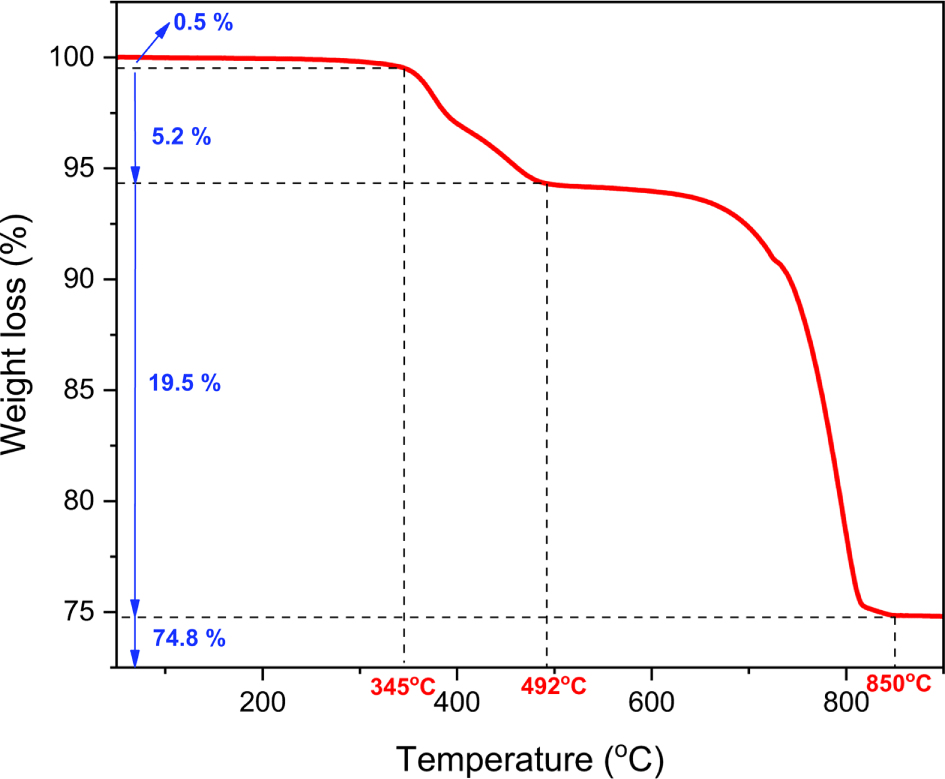
Temperature range (°C) | Component | Weight loss (%) |
---|---|---|
50-345 | Volatile organics (VO) | 0.5 |
345-492 | Polymeric materials (PM) | 5.2 |
492-850 | Decomposed components in inorganic matter (DI) | 19.5 |
> 850 | Ash | 74.8 |
Of the S-APWPs, three TGA thermograms were shown in Figure 4. The TGA thermograms were different from each other, though they were prepared from the same asphalt pavement. The detailed component ratios of the ten S-APWPs were summarized in Table 5. Ranges of the component ratios were VO : PM : DI : ash = 0.5-3.1 : 0.7-22.8 : 10.8-34.1 : 50.2-77.8. The component ratios of the S-APWPs varied depending on the samples. APWPs with higher DI content implies that they had larger content of the coarse aggregate, while those with higher ash content means that they had larger content of the fine aggregate. The S2, S4, and S10 samples had lower DI content than the reference (19.5% of DI). Especially, the DI content of the S10 sample (10.8%) was about half of the reference. The ash contents of all the S-APWPs were greater than 50%, but most samples had lower ash contents than the reference (74.8% of ash). Only the S9 and S10 samples had higher ash content than the reference. Lower ash contents of the APWPs compared to the reference may be due to production of tiny inorganic particles generated from the fine and coarse aggregates during preparation of model APWPs. APWPs with higher content of VO and PM denotes that they had larger content of the bitumen and modifier. The S8 and S9 samples had lower total content of VO and PM than the reference (5.7%).
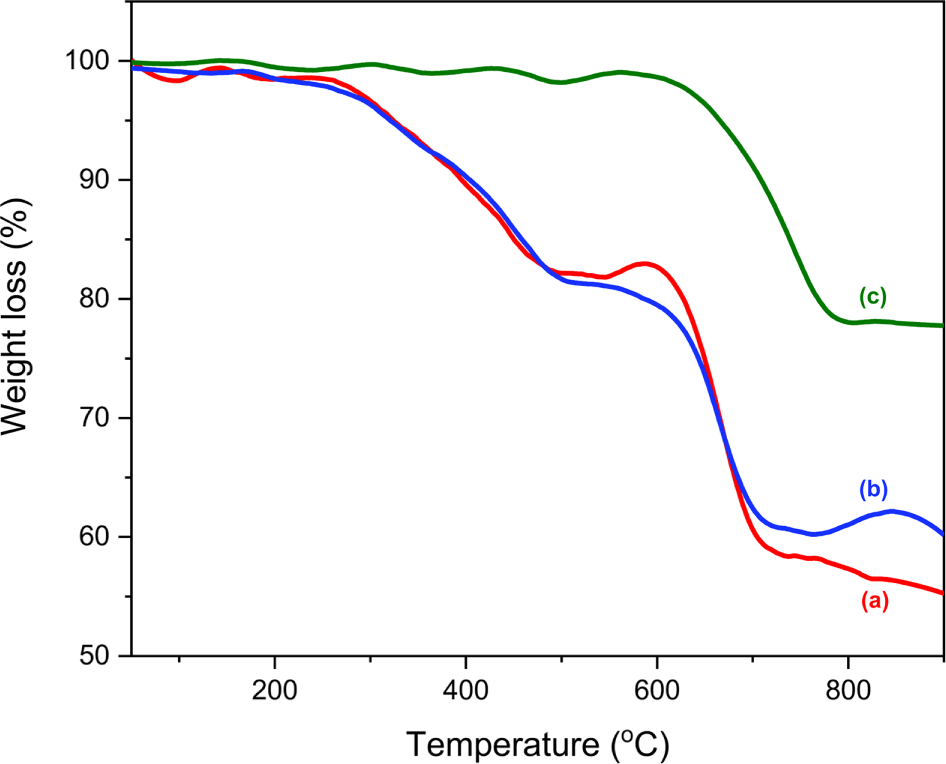
The total content of PM and VO of the S9 sample was very small (1.8%), whereas those of the S3, S6, and S7 samples were very large (over 20.0%). This implies that the S9 sample contained very small amount of the bitumen and modifier, whereas the S3, S6, and S7 samples had a large amount of them. Ratios of PM/VO for the bitumen and modifier can be calculated using the weight losses before the air introduction. Assuming the volatile organics in the bitumen and modifier are totally vaporized until 335 and 364°C, respectively, the PM/VO ratios would be approximately 26 and 4 for the bitumen and modifier, respectively. The PM/VO ratio of the reference thermogram was 10.2. The ratios of the S8 and S9 samples were very small (below 3.0), whereas those of the S2 and S4 samples were very large (over 30.0). Thus, it can say that the S9 sample had very low bitumen content.
Of the L-APWPs, four TGA thermograms were shown in Figure 5. The TGA thermograms were also different from each other. The detailed component ratios of the ten L-APWPs were summarized in Table 6. Ranges of the component ratios of VO : PM : DI : ash were 0.5-1.8 : 0-21.2 : 17.5-35.3 : 53.1-74.9. The DI contents of the L5 and L8 samples were slightly lower than that of the reference, whereas those of the L9 and L10 samples were much higher than that of the reference by about twice. The ash contents of the L-APWPs were greater than 50%. Total contents of VO and PM of the L7 and L10 samples were much lower than that of the reference, whereas those of L2, L3, L4, and L5 were much greater than that of the reference. The PM/VO ratios of the L7 and L10 samples were very small (below 3.0), whereas those of the L2, L3, and L4 samples were relatively large over 16.0 (L2 34.8, L3 16.3, L4 21.2). Thus, it can say that the L2 sample had very high bitumen content.
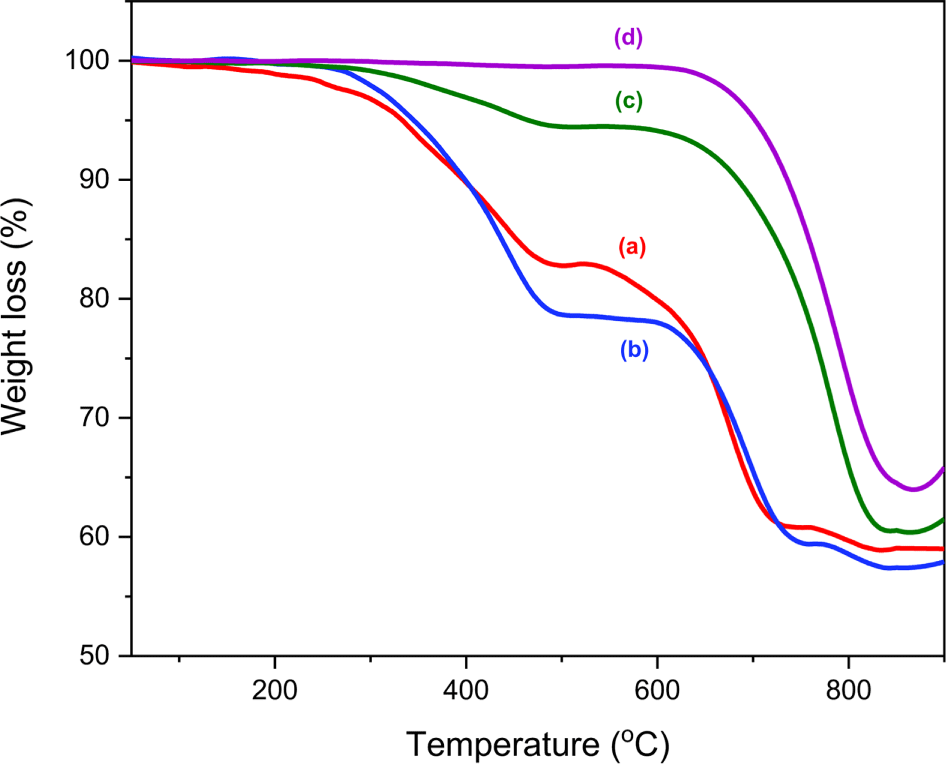
The component ratios and ranges of the S- and L-APWPs were summarized in Table 7. The ash contents of all the APWPs were much lower than that of the reference, but the other components of the APWPs were higher than the reference. The VO contents of the S-APWPs were much higher than those of the L-APWPs, but differences in the other components were small or negligible. The wider range means the larger inhomogeneity. The inhomogeneity of the S-APWPs was relatively larger than that of L-APWPs.
Component | S-APWP | L-APWP | Reference |
---|---|---|---|
VO | 1.6±0.9 | 0.9±0.4 | 0.5 |
PM | 14.7±7.1 | 13.2±8.0 | 5.2 |
DI | 22.4±6.7 | 24.2±6.0 | 19.5 |
Ash | 61.4±9.6 | 61.7±6.2 | 74.8 |
Conclusions
APWPs were prepared using the model asphalt pavement, and the single APWP was analyzed through TGA to examine difference in the their compositions. Reference TGA thermogram of the model asphalt pavement was built using the TGA thermograms of the five raw materials and their ratios. The reference TGA thermogram showed four weight loss regions at 50-345, 345-492, 492-850, and > 850°C corresponding to the VO, PM, DI, and ash, respectively. The TGA thermograms of the APWPs were different from each other, though they were obtained from the same asphalt pavement. The ash contents of the APWPs were much lower than that of the reference, but the other components of the APWPs were higher than the reference. Lower ash contents of the APWPs compared to the reference can be explained by tiny inorganic particles generated from the aggregates during preparation of the model APWPs. The VO contents of the S-APWPs were much higher than those of the L-APWPs, but differences in the other components were small or negligible. The experimental results can lead to a conclusion that degree of the inhomogeneity will be increased as size of the APWP decreases.