Introduction
The number of earthquakes in Korea has steadily increased since 1978, when analog observations were made in Korea. According to the 2022 Seismological Annual Report published by the Korea Meteorological Administration, an average of 70.6 earthquakes occurred annually during the digital observation period from 1999 to 2021. In 2022, a total of 77 earthquakes of magnitude 2.0 or greater occurred 10% (7 times) from the previous year. In particular, a total of 10 earthquakes with a magnitude of 5.0 or greater occurred from 1978 to 2022.1 When a large-scale earthquake occurs, many earthquake-resistant designs are applied to prevent damage to urban structures, internal facilities, and power facilities, resulting in human and economic damage. As shown in Figure 1, seismic design structures are largely divided into earthquake resistance, vibration control, and seismic isolation structures. Seismic isolation structure is a technology that has been applied worldwide to protect building structures, non-structural components, and contents from earthquake-induced damage. The seismic isolation damper used in the seismic isolation structure is composed of a laminated structure of steel plate and rubber as shown in Figure 2.2 Therefore, the adhesive strength between different materials is an important factor.
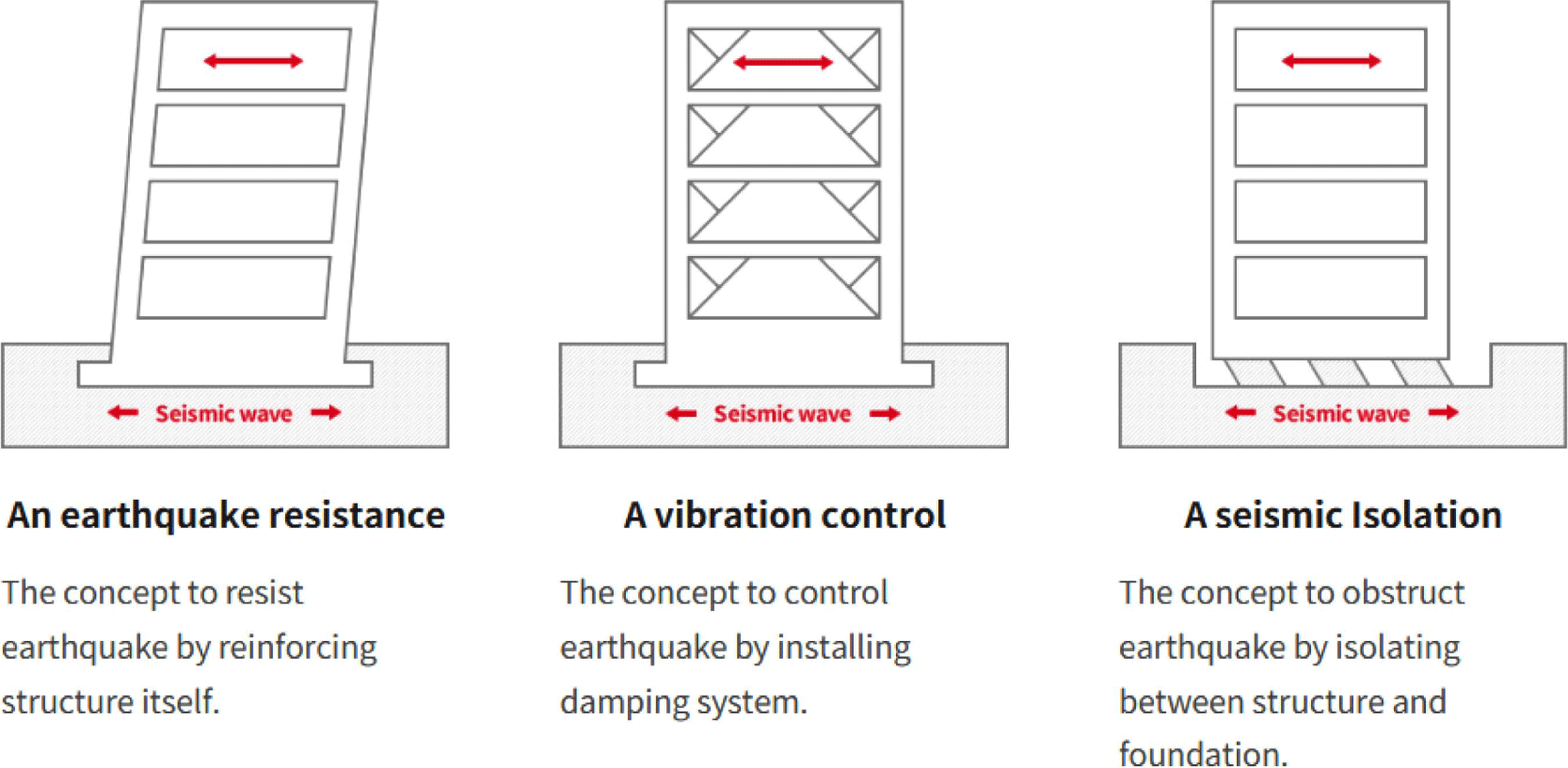
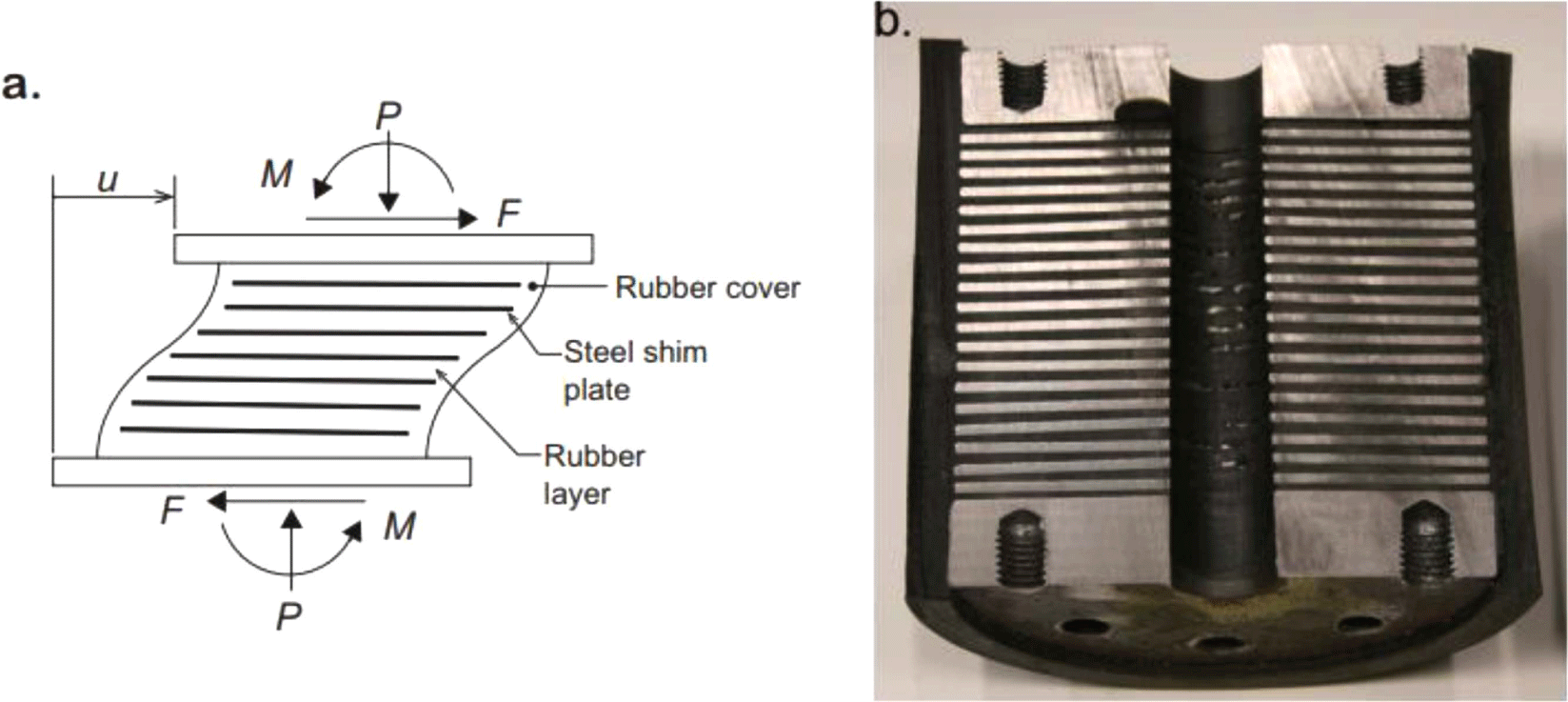
Natural rubber (NR) is an excellent elastomer with a well-balanced set of properties. For this reason, it is used in a wide range of applications, including seismic isolation structures, but NR is non-polar, and has poor adhesion to rubber-metal or rubber-fiber, therefore many modification studies are being conducted to improve the adhesive strength. Many types of polymers have been studied for modification by various methods depending on their use, and modified polymers can supplement the physical properties of existing polymers by imparting new properties while maintaining basic intrinsic properties.3,4 Polymer modification methods can be largely divided into three types: first, a method of introducing a functional group into a polymer chain; second, a method of crosslinking polymer chains; and, finally, a method of mixing and bonding with heterogeneous polymers.5
In this study, NR/citraconic acid-g-natural rubber (CCA-g-NR) compounds applied to seismic isolation damper rubber, we provide data as basic research to obtain the optimal ratio of adhesive strength and mechanical properties, and processability characteristics.
Experimental
Natural rubber (NR, SVR-3L, VAN NANG ST, Vietnam), reactive monomer citraconic acid (CCA, ACROS), initiator azobisisobutyronitrile (AIBN, Sigma-Aldrich) were used without further purification. vulcanization activator zinc oxide (ZnO, KS-1, Hanil Chemical Ind Co., Korea), processing aid for rubber aromatic process oil (A-2, Michang Petroleum Co., Korea), filler Carbon Black ISAF (N220, Orion Engineered Carbons GmbH), other additive stearic acid, antioxidant, cross-linking agent sulfur (S, Siam Chemical Industry, Thailand), vulcanization accelerator n-cyclohexyl-2-benzothiazole sulfonamide (CBS, Yaoduo Industrial, China) were used as received.
CCA-g-NR was prepared by melt grafting from CCA/NR/initiator AIBN using an inter mixer (Brabender GmbH & Co. KG, Germany) with a chamber volume of 300 cc. In order to prevent the thermal aging of natural rubber, kneading at a kneading temperature of 100°C for (1) 5 minutes, and (2) reacting at 30 rpm for 15 minutes by adding a reactive monomer and an initiator to prepare CCA-g-NR. The reaction mechanism of CCA-g-NR is shown in Figure 3.
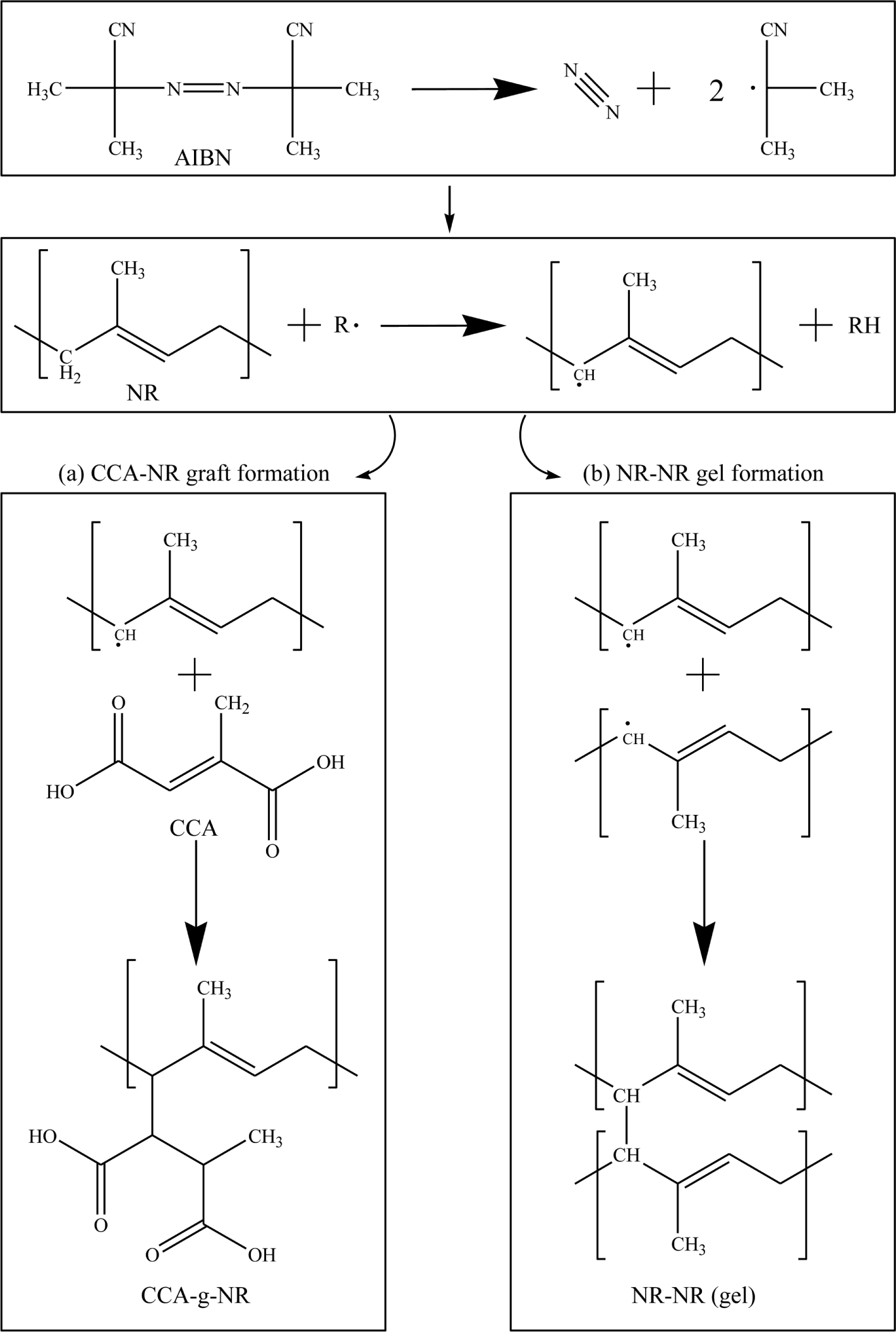
The formulation of the seismic isolation damper rubber compounds with sample designations is displayed in Table 1. All the compounds were prepared using an inter mixer (Brabender GmbH & Co. KG, Germany) with a chamber volume of 300 cc. Carbon masterbatch was prepared, after, the final masterbatch (FMB) was prepared by mixing sulfur and accelerator for 5 minutes using an 8 inch two roll mill, and the seismic isolation damper rubber compounds were prepared at the optimal vulcanization time (T90) derived through analysis of cure characteristics at 160°C.
Sample Designation | NR | CCA-g-NR | ZnO | Addactives | ISAF | A-2 | Sulfur | CBS |
---|---|---|---|---|---|---|---|---|
NgC-0 | 100 | 0 | 5 | 9 | 70 | 5 | 2 | 1 |
NgC-20 | 80 | 20 | 5 | 9 | 70 | 5 | 2 | 1 |
NgC-40 | 60 | 40 | 5 | 9 | 70 | 5 | 2 | 1 |
NgC-60 | 40 | 60 | 5 | 9 | 70 | 5 | 2 | 1 |
Attenuated total reflectance (ATR)-Fourier transform infrared (FTIR 6200, Jasco, Japan) spectroscopy was used to confirm the chemical components of the pristine NR, CCA, and CCA-g-NR. For each sample, 32 scans at a 4 cm-1 resolution were collected in transmittance mode and recorded in the 2000-600 cm-1 range.
The graft ratio G/R (%) is the mass of grafted CCA per unit mass of backbone polymer (NR). The grafting efficiency G/E (%) is readily defined as the mass of the grafted CCA divided by the total CCA produced. G/R (%) and G/E (%) were calculated from the following equations:
Mechanical properties (tensile strength, elongation, modulus at 300%) were measured using dumbbell-shaped specimen number 3 according to KS M6518 using a universal testing machine (UTM, UTM 3345, Instron, USA) at a crosshead speed of 500 mm/min.
The adhesive strength was measured using the universal testing machine (UTM, UTM 3345, Instron, USA) according to ASTM D1876 operated at a crosshead speed of 254 mm/min.
Seismic isolation damper rubber compounds rheology was measured using a rubber process analyzer (RPA, RPA elite Rubber Process Analyzer, TA Instruments, USA) according to ISO 6502-1, ISO 6502-3 at 160°C for 20 min with ±1°. The curing characteristics such as maximum torque MH, minimum torque ML, the difference between maximum and minimum torque △M, scorch time (the time to incipient cure) TS2, optimum cure time: T90 (the time required for the torque to reach 90% of the maximum torque), and cure rate index (CRI) can be determined. The CRI, a measure of the rate of curing, was calculated from the following equation:
where T90 is the time required for the torque to reach 90% of the maximum torque and TS2 is scorch time, respectively.
Results and Discussion
Figure 4 shows the FTIR spectra of pristine NR, CCA, and CCA-g-NR. The CCA-g-NR sample had two characteristic peaks for NR (Trisub. C=C stretch peak at 1664 cm-1, Trisub. C-H Wag at 830 cm-1)6,7 and citraconic acid (the C=O stretch peak at 1704 cm-1, C-O stretch peak at 1270 cm-1)8,9 for the carboxylic acid group of citraconic acid component), indicating the presence of citraconic acid in NR.
Table 2 shows the G/R (%) and G/E (%) of CCA-g-NR according to CCA and AIBN content (phr). As the content of reactive monomer CCA increased, G/R (%) of CCA-g-NR increased, G/E (%) of CCA-g-NR decreased. As the reactive monomer CCA content increases, the CCA concentration increases and more reactions proceed, therefore, G/R (%) improves, but G/E (%) decreases because the initiator content is the same as 0.10 phr. As the content of initiator AIBN increased, G/R (%) and G/E (%) of CCA-g-NR increased. It was shown that a critical point exists based on specific content. These results are thought to be the result of the reactive monomer CCA acting as a limiting reactant by fixing the content of the reactive monomer CCA. Therefore, the excess initiator AIBN proceeds with a crosslinking reaction between natural rubber chains, which is a side reaction of the CCA-g-NR production reaction, to form a gel. In order to improve both G/R (%) and G/E (%), it is determined that the optimal G/R (%) and G/E (%) can be derived only when the contents of the reactive monomer and the initiator are simultaneously controlled. In the scope of this study, sample NC7A0.13 (CCA: 7 phr, AIBN: 0.13 phr) was determined to be the optimal condition to apply for seismic isolation rubber.
In the rubber industry is of elementary importance to know the way of crosslinking of rubber, in order to define its processability, curing time, and final characteristics. The rheometric curve obtained is a fingerprint of the vulcanizing process and its processability characteristics. The torque (force) plot against the actual cure time is called the rheometric curve, all vulcanization characteristics of rubber compound can be determined directly. In general, this rheometric curve is divided into 3 stages. Phase 1, gives an indication of the processing behavior of rubber compound. The next phase 2, describes the curing characteristics of the rubber compound. The next phase 3 gives a good indication of the physical properties of the rubber compound. There are three types of rheometric curves, curve to equilibrium torque, cure to a maximum torque with reversion, and cure to no equilibrium in maximum torque. Depending on the type of compounds, the slope of increasing torsion varies. After a while, the pair normally reaches the maximum value. If the test continues for sufficient time, curing reversal occurs and the torque tends to decrease. This type of reversal curve is called the reversion curve.10-12
Figure 5 shows the rheometric curves of NgC-0, NgC-20, NgC-40, and NgC-60 samples. It was found that NgC-0, NgC-20, NgC-40, and NgC-60 samples showed the reversion cure curve. Cure characteristics, as well as maximum torque MH, minimum torque ML, the difference between maximum and minimum torque △M, incipient cure time scorch time TS2, optimum cure time T90 (the time required for the torque to reach 90% of the maximum torque), and cure rate index (CRI) of the seismic isolation damper rubber compounds, are shown Table 3. The cure rate index (curing speed ratio or cure rate) is essentially a measure of the linear slope of the upward cure curve. Curing speed is an important vulcanization parameter, since it determines the time required to create the crosslink, that is, cure time. As shown in Table 3 the scorch time (Ts2) and optimum time (T90) of compounds increased, however, the maximum elastic torque (MH) and cure rate index (CRI) of compounds decreased, with increasing CCA-g-NR content. These results mean that as the content of CCA-g-NR increases, the optimal vulcanization time increases. It means as the CCA-g-NR content increases, the maximum torque value decreases, and the scorch time is delayed equal to the optimal vulcanization time.
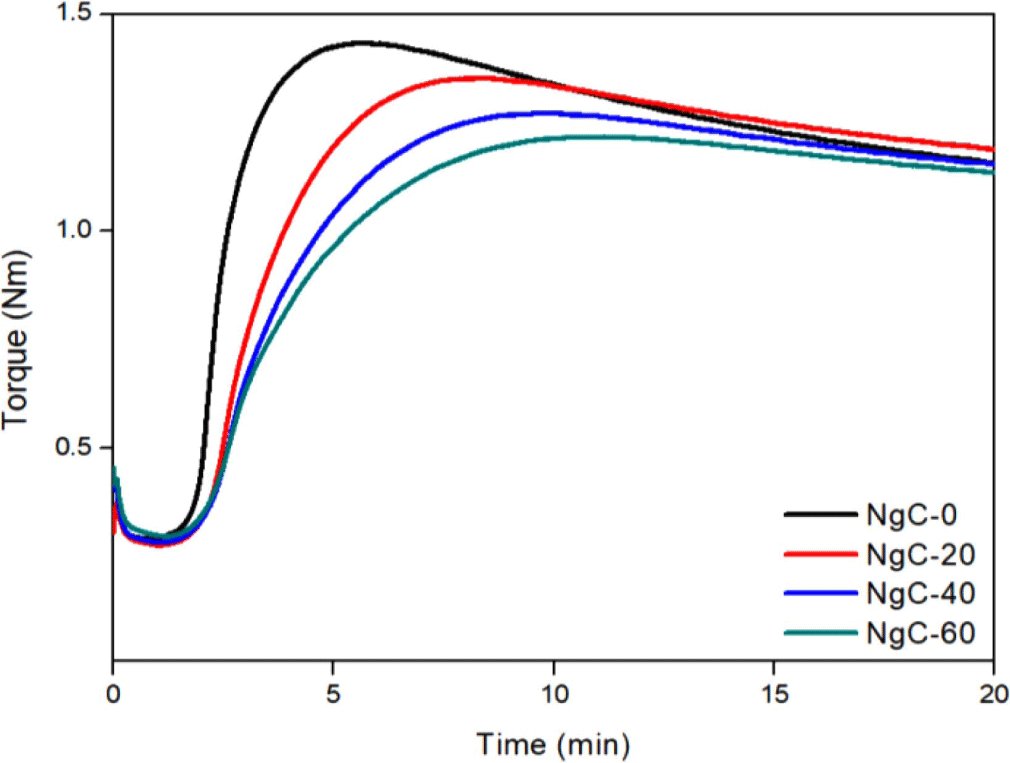
Figure 6 shows the stress-strain curves of NgC-0, NgC-20, NgC-40, and NgC-60 samples. The tensile strength, elongation at break, modulus at 300%, and adhesive strength of NgC-0, NgC-20, NgC-40, and NgC-60 samples are shown in Table 4. As the content of CCA-g-NR increased, the elongation at break of seismic isolation rubber compounds increased, and tensile strength and modulus at 300% of seismic isolation rubber compounds decreased. Generally, modulus at 300% is known to have a high correlation with crosslinking density.13 This shows the same tendency as the results of cure characteristics (see Table 3). The crosslinking rate and crosslinking density decreased, it should be attributed to the acid-base reaction between the carboxylic acid of CCA-g-NR and CBS as an accelerator.14 In addition, the adhesive strength of NgC-0, NgC-20, NgC-40, and NgC-60 samples were 3.31, 3.54, 3.88, and 3.93 kgf/2 cm, respectively. As the content of CCA-g-NR increased, and the adhesive strength of the seismic isolation rubber compound increased. Adhesive strength is known to be affected by surface irregularities, tangles in polymer chains, chemical bonds, and secondary bonds such as van der Waals forces or hydrogen bonds.15 Because the natural rubber used in this study had already been crosslinked, the effect of chain tangling or chemical bonding was insignificant. However, as the CCA-g-NR content increased, the hydrogen bond by the carboxyl group of CCA increased. Hydrogen bonds are about 10 times stronger than van der Waals forces and are known to exhibit strong bonds similar to weak primary bonds.16 Therefore, as the CCA-g-NR content increased, the concentration of hydrogen bonds increased, therefore, the adhesive strength was improved by 18.7% of the NgC-60 sample compared to the NgC-0 sample.
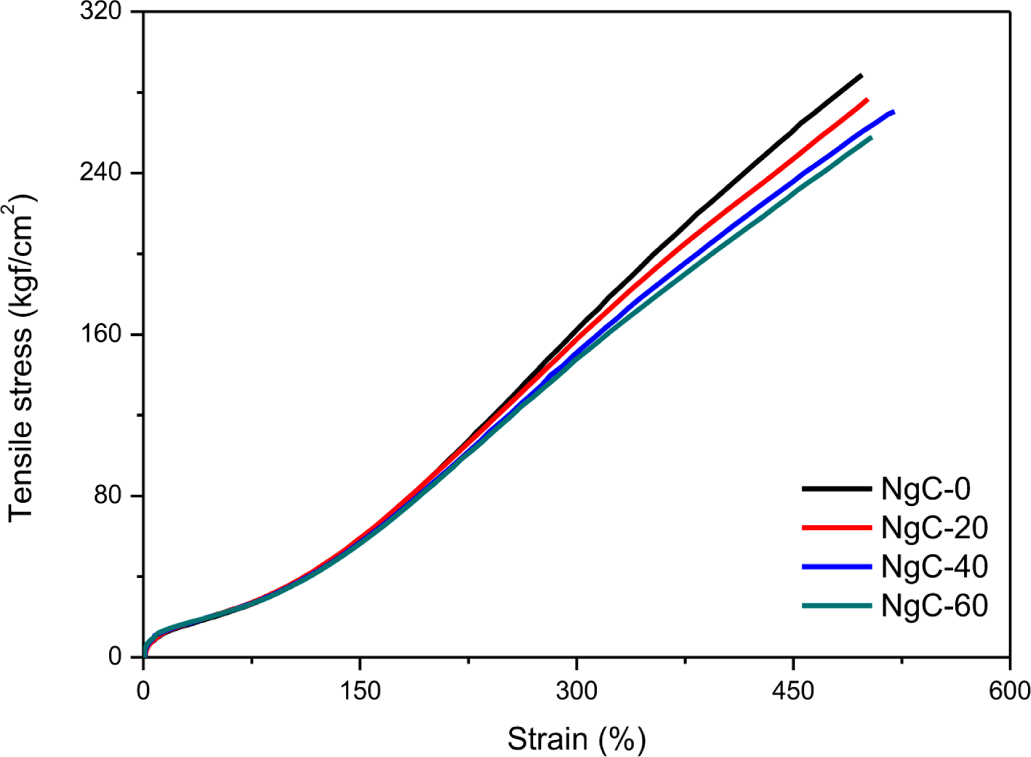
Of course, it would be necessary, in order to apply it for seismic isolation damp rubber, the optimal content of CCA-g-NR should be applied by considering the processability characteristics, adhesive strength, and mechanical properties of the compounds.
Conclusions
CCA-g-NR was prepared from reactive monomer CCA, NR, initiator AIBN using melt graft technique to modify natural rubber. Moreover, graft ratio G/R (%) and grafting efficiency G/E (%) were investigated according to reactive monomer CCA, and initiator AIBN content. It was found that the sample NC7A0.13 (CCA: 7 phr, AIBN: 0.13 phr) was determined to be the optimal G/R (3.49%) and G/E (49.8 %) applying it to seismic isolation rubber compounds. In addition, the effect of CCA-g-NR content on the mechanical properties (tensile strength, elongation at break, 300% modulus), adhesive strength, and curing characteristics of the seismic isolation damper rubber compound was studied. It was found that elongation at break of seismic isolation rubber compounds increased, however, tensile strength and modulus at 300% of seismic isolation rubber compounds decreased, with increasing the content of CCA-g-NR. As CCA-g-NR content increased, the adhesive strength of seismic isolation rubber compounds was increased. From the cure characteristic, the scorch time (Ts2) and optimum time (T90) of compounds increased, however, the maximum elastic torque (MH) and cure rate index (CRI) of compounds decreased, with increasing CCA-g-NR content. As CCA-g-NR is applied for seismic isolation rubber, the adhesive strength improves, the crosslinking density decreases, and the mechanical properties decrease. Therefore, the optimal content of CCA-g-NR should be applied by considering the processability characteristics, adhesive strength, and mechanical properties of the compounds.