Introduction
The rubber indicates a viscoelastic polymer with hyperelasticity, high stretchability, and high energy storage capability, in which its deformation under an external force would be recovered to its original state after removing the applied external force.1-3 During several decades of industrial advancement, rubber has undergone drastic development, resulting in wide diversity of rubber types, each tailored to specific functions demanded by various industries. Among them, Acrylic rubber (ACM) is a saturated co-polymer, composing mainly of acrylic acid ester monomers and small portion of cure site monomers. Ethyl acrylate and n-butyl acrylate, which are mainly composed of highly polar repeating units, are primarily used, and there have been some attempts to show new functions by incorporating other acrylic monomers with specific alkoxy alkyl groups, such as methoxyethyl acrylate and ethoxyethyl acrylate.4-6 This combination of a saturated carbon chain backbone and high polarity gives rise to high-performance elastomers that exhibit excellent resistance to heat, oil and oxidation. In comparison of styrene butadiene rubber, this synergy enables their successful utilization in a range of applications in automotive industry including seal, hoses, O-ring, gaskets, and more.7-9
However, the evolving automotive industry, coupled with the increasingly stringent environmental regulations, a notable demand has arisen for the advancement of high-performance engines and enhanced energy efficiency.10,11 For this reason, it began to be necessary to expand the service temperature of organic automobile engine parts. In response, many studies have been conducted to expand the service temperature of ACM, which includes the design of primary polar repeating units, the formulation of additives such as pillars, emulsifiers, surfactants, alongside the alteration of the crosslinking system.5,12,13 Among these approaches, the crosslink density is one of the most effective factors for adjusting ACM performance. The cure site monomer, a minor component within ACM units, transforms into a crosslinking point in the entangled structure of the network of long chain polymers through a process referred to as vulcanization.11 Through this study, ACM with a special high-temperature ACM (HT-ACM) named carboxyl type cure site that can be used at extreme environmental condition has recently been developed from epoxy, active halogen type, and chlorine type. Some HT-ACM products provide service temperature of -40 to +185°C, showing short-term performance up to +200°C.5,14 However, the need for further research remains to meet the rapidly changing and harsh climate change and the demand for extended product lifecycles aimed at resource circulation.10
Herein, we have conducted a fundamental study on HT-ACM with high weather resistance and heat resistance used in hose materials for automobile engine components. We used a carboxyl-diamine cure system, wherein diamine molecules function as a crosslinkers and react with carboxylic cure sites in polymer chains, results in three-dimensional network structure. The diamine crosslinkers with distinct molecular structures were used to induce variations in kinetics. Moreover, we applied the two different guanidine accelerators to make the gap in the crosslink density more. This approach was conducted to evaluate the effect of the degree of crosslinking, which is a major determinant of the resulting physical properties of the ACM, which was supported by experiments both the rubber process analyzer (RPA) and tensile test.6,15,16 Differences in process methods and durations can cause to significant variations in product qualities, even with the same composition.17 This phenomenon reflects the role of storage stability as a prominent factor, which also was observed in each crosslinking system.
Experimental
We used PA-526 (Unimatec, Germany) and AR-930 (ZEON, Japan) as a main copolymer with carboxylic cure site. For the prototype, various additives, including a carbon black particle (N-330, OCI, Korea), an antioxidant (NAUGARD-445, Dupont, USA), and a stearic acid (PH-100, LG H&H, Korea), were mixed with the polymer, as shown in Table 1. To control the crosslink density, we used two crosslinking agents, 3,4’-diaminodipienyl ether (CLP-5050) from Unimex, Germany, and hexamethylenediamine carbamate (HMDAC) from Dupont, USA, respectively. And two accelators, 1,3-di-O-tolylguanidine (DOTG) and 1,3-diphenylguanidine (DPG), were supplied by Sigma Aldrich, Germany (see Table 1).
In the carbon black masterbatch (CMB) compounding step, we prepared the compounds using a mixer (Brabender Technologie GmbH & Co. KG, 300 cc) for 10 min, at 60°C. And then, we stabilized the CMB compounds under room temperature for 1 day. For the final masterbatch (FMB), we used a 2-roll mill to mix the crosslinking agent and the accelerator, and sheeted. To obtain vulcanizates specimens, FMB was vulcanized in a hot press at 180°C for 10 minutes and post-cured in a dry oven at 170°C for 4 hours.
Results and Discussion
Crosslinking refers to a chemical bonding process that establishes a connection between polymer chains, significantly influencing physiochemical performance of products. Therefore, it is important to study this process as a variable. To this end, a compound was prepared by mixing additives without the addition of a crosslinking agent to CMB. And then, the correlation between the prototype’s performance and the crosslink density was analyzed during further compounding process in FMB. The main polymer used possesses carboxyl cure sites, and the carboxylic side chains in the linear entangled chains of this polymer chemically bind with a diamine based crosslinker, resulting in amide bonds. In this crosslinking, we used two crosslinkers with different molecular structures. CLP-5050 is bulky and rigid due to its diphenyl linkage, whereas HMDAC, featuring an alkyl chain composition, exhibits flexibility and thin profile, as shown in Figure 1. Considering kinetics occurring between densely and viscously entangled polymers, it is expected that the relatively flexible and linear HMDAC will undergo more reactions compared to CLP-5050. This was verified using a RPA, a rheometer that measures viscosity in real time at curing temperature. In Figure 2, upon heating the compound, there is an initial drop (ML: minimum torque) of viscosity, and then gradually rises to saturation. (MH: maximum torque) By using the ΔTorque (=MH-ML), we can easily evaluate the difference of crosslink density varying compound recipes, wherein the crosslink density is proportion to ΔTorque. The compounds based on HMDAC exhibit higher ΔTorque values compared to those with CLP-5050, indicating that HMDAC promotes higher crosslink density as shown in Table 2. Furthermore, we investigated the effect of accelerators that enhance crosslinking while establishing basic environment at high temperature.18 Although it was confirmed that there was a difference in the degree of crosslinking by the accelerator, the main factor in the degree of crosslinking of the rubber is considered a crosslinker because there was no reversal of crosslinking between the two crosslinker groups by the accelerator (See Table 2).
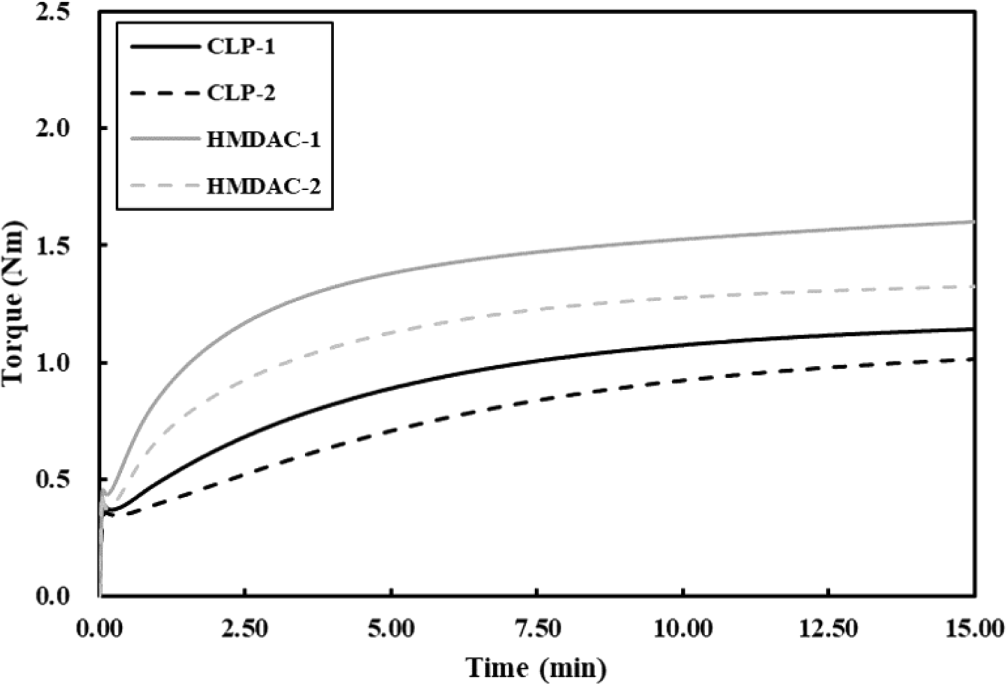
Recipe code | CLP-1 | CLP-2 | HMDAC-1 | HMDAC-2 | |
---|---|---|---|---|---|
RPA (180°C) |
MH | 1.14 | 1.02 | 1.60 | 1.33 |
ML | 0.37 | 0.35 | 0.44 | 0.38 | |
Δtorque =MH-ML | 0.77 | 0.67 | 1.17 | 0.95 |
As the degree of crosslinking increases, the chemical bonding between polymer chains also increases, wherein the internal force in the material increases to resist deformation caused by loads or external forces. Therefore, when measuring the tensile strength, we can see that the deformation of the material is suppressed and stress increases. In a strain-stress diagram, the tensile strength is determined by dividing the maximum stress the material can withstand before breaking. In Table 3 and Figure 3, the tensile strength of the groups using HMDAC was higher than that of the CLP-5050. And the CLP-5050 group exhibited a higher elongation rate, indicating a greater degree of deformation under external forces compared to the HMDAC group. Furthermore, when measuring the modulus at 300% deformation, the HMDAC-based samples showed higher values.19 This difference in crosslink density between the two characteristic crosslinking agents is believed to be the underlying cause. Even within the same crosslinker groups, variations were observed based on the accelerator used. Considering the comparatively lower tensile strength and elongation and the higher 300% modulus observed with DOTG, it can be inferred that DOTG promotes crosslinking more actively in comparison to DPG. Based on this, families of various physical properties can be created by adjusting the degree of crosslinking in one compound, making it important and possible to design the optimal crosslinking system for the purpose.
Recipe code | CLP-1 | CLP-2 | HMDAC-1 | HMDAC-2 |
---|---|---|---|---|
Tensile Strength (kgf/cm2) | 136 | 139 | 154 | 155 |
Elongation (%) | 363 | 497 | 248 | 339 |
Modulus of 300% (kgf/cm2) | 104 | 83 | - | 137 |
It takes a lot of steps and time to make desired rubber products from raw materials. There are some high-temperature and high-pressure processes such as extrusion and injection molding, often involving the incorporation of additives and crosslinking agents into the raw rubber material, and problems in any process can lead to prolonged production delays. If partial curing takes place under undesirable conditions, it can lead to significant issues in both product quality and processing. Ideally, curing should be accomplished within an appropriate timeframe under designed temperature condition that facilitates the curing process. If the curing time is too short, the reaction’s activation energy remains low, resulting in scorch, which is pre-crosslinking due to energy caused by pressure or friction in a pre-process environment lower than the optimal reaction temperature. Conversely, excessively long curing times extend the overall process duration, leading to productivity issues. In the case of the crosslinking system we studied, when observing the change in torque with RPA, it was confirmed that the reaction was completed around 10 minutes at the set temperature of 180°C, as shown in Figure 2.20 However, given the variation in crosslinking degree attributable to different crosslinking agents, a significant divergence in storage stability at room temperature is expected. Hence, we evaluated room temperature storage stability. In the FMB process, Δtorque was measured using RPA with same process as in Figure 2 every specific period while storing the compounds at room temperature. The larger reduction in Δtorque corresponds to increased occurrence of scorch, indicating evidence of partial crosslinking-a metric used to assess storage stability. As shown in Figure 4, when the Δtorque was observed for 60 days, it was shown that the aging stability was highly dependent on the accelerator regardless of the crosslinkers. DPG, which had a low degree of promotion of crosslinking, showed a lower Δtorque change compared to DOTG, and thus had excellent stability over time. Additionally, to determine if this phenomenon is exclusive to the polymer, we evaluated the substitution of PA-526 with AR-930 using the same crosslinker, CLP-5050. The storage stability results revealed that DPG was better than DOTG in both systems (See Figure 5).
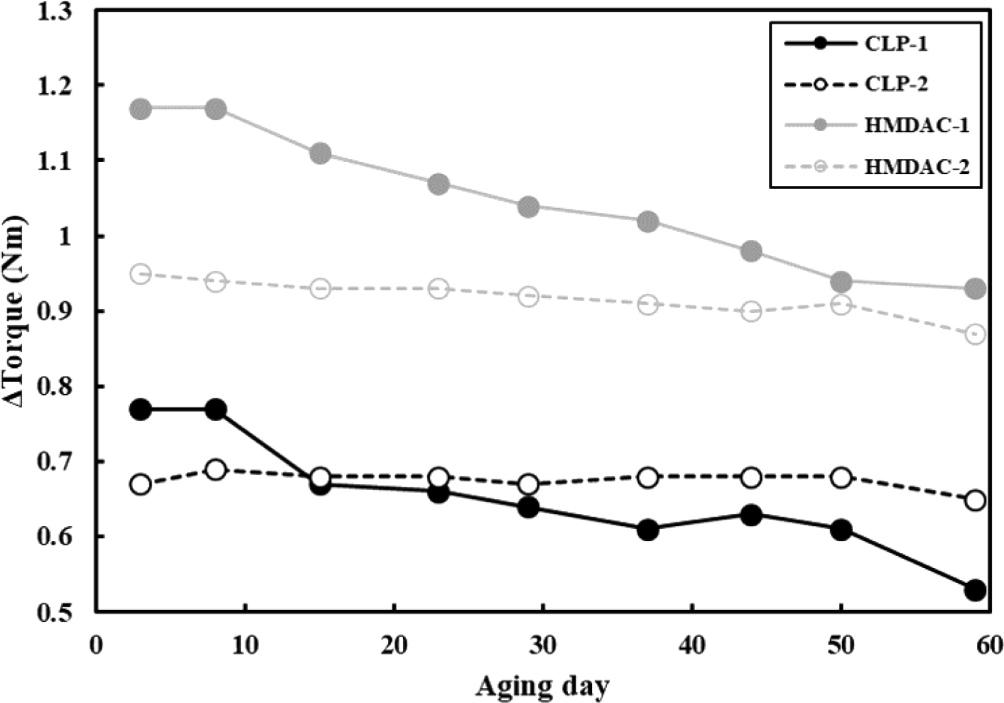
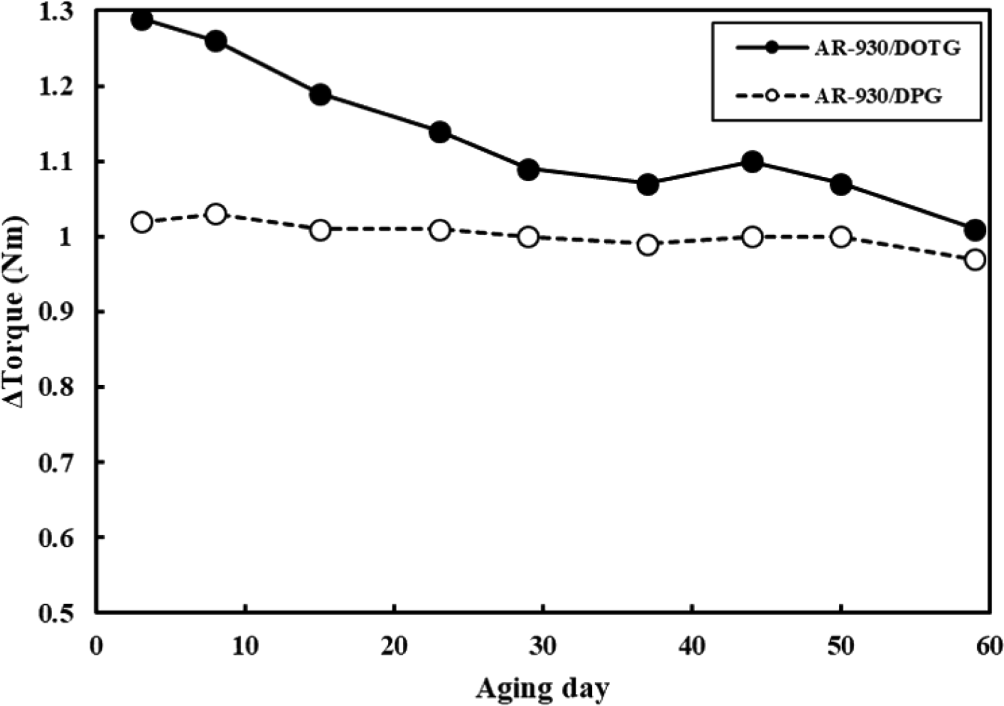
Conclusions
The degree of crosslinking, which has a significant effect on rubber properties, was controlled from in terms of a kinetic according to the chemical structure of the molecule, and the correlation between the degree of crosslinking and mechanical properties was studied. For crosslinking, we utilized a system consisting of ACM rubber with carboxylic cure sites and crosslinkers having diamine groups. Our findings indicate a direct correlation between the degree of crosslinking and molecular structure in terms of mobility. Through tensile experiments, it was conformed that the crosslinker, which is relatively advantageous for improving mobility, exhibited a high degree of crosslinking. This, in turn, resulted in lower elongation and a higher 300% modulus. In addition, we evaluated the effect of accelerators on the crosslinking process, and it was observed that the accelerators did not alter physical properties, thereby confirming the dominant role of the crosslinker. Instead, it was found that the accelerator acted as a variable in the manufacturing process, and storage stability significantly differed depending on the type of accelerator used. Conversely, it was revealed that the crosslinking agent served as an independent variable for storage stability. These findings are believed to form the basis for developing an optimal formulation strategy in the compounding process for high-performance products.