Introduction
Since particulate matter has emerged as a major contribution to air pollution, many industries are implementing various policies to reduce particulate matter. In particular, the automotive industry is significantly reducing the amount of particulate matter generated from exhaust gas by reinforcing emission regulations and promoting the shift toward the use of electric vehicles.1,2 As the amount of particulate matter from the exhaust system has decreased, the proportion of particulate matter from the non-exhaust system has increased; therefore, interest in reducing particulate matter from the non-exhaust system is increasing. Particulate matter from the non-exhaust system is mainly composed of brake pad wear particles, tire wear particles, road surface wear, and road dust.3 Michelin in France reported that only 0.17% and 2.20% of tire wear particles become particulate matters PM2.5 and PM10, respectively.4 Despite the particulate matter generation from tires being low, research has been continuously conducted to reduce particulate matter generation by improving tire performance to counteract the increase in particulate matter generation due to increased vehicle load.5,6
Tires have more than 10 components, including tread, belt, carcass, sidewall, and inner liner. Of these components, tread occupies the largest volume fraction,7 and is the most important component affecting tire performance because it is in direct contact with the road surface.8 Tires are broadly classified into passenger car radial (PCR), light truck radial (LTR), and truck bus radial (TBR) tires. In particular, research is needed to reduce particulate matter from TBR tires, which require high loads and long driving times.
Due to the harsh driving conditions they are exposed to, TBR tire treads are subjected to many cut & chip phenomena that are rarely observed in PCR tire treads. Thus, NR, which has excellent mechanical properties, is used as a base rubber in TBR.9 Moreover, high cis-BR is blended to improve wear resistance of compound.10 As a filler, CB, which has a good affinity with NR and excellent reinforcement properties, is mainly used. However, using CB as a filler has the disadvantage in fuel efficiency due to heat generation.9 Therefore, research is being conducted to improve fuel efficiency by replacing CB with a silica/silane system.11,12 Applying this silica/silane system in TBR tire treads can interrupt the silanization and the coupling reaction of silica due to the proteins and phospholipids contained in NR and the large molecular structure of NR.13 Consequently, research has been conducted on the epoxidized NR (ENR), which has a good affinity with silica, in applying the silica/silane system to TBR tire treads.5,6,14
In a polymer blending system, filler distribution in each phase is a major factor determining the reinforcement of the com-pound.15 For a compound blended with more than one type of base rubber, filler distribution in the rubber matrix may be uneven due to the differences in the affinity of the base rubber for the filler. This issue have to solve because NR and BR are only partially compatible.16 In particular, since ENR with a functional group has a good affinity for silica, solving the uneven filler distribution in ENR/BR blend compounds is crucial.
In this study, conventional blending method, in which the base rubber, filler, and additives are mixed simultaneously, was compared with the Y-blending method,17 in which masterbatches (MBs) are prepared according to the type of base rubber, and the MBs are blended afterward. CB-filled NR/BR blend compound and silica-filled ENR/BR blend compound were prepared according to the blending method to evaluate the physical properties of the compound and the amount of particulate matter generated. Through this, we examined the effect of the blending method on filler dispersion, the performance of the TBR tire tread compound, and the amount of particulate matter generated.
Materials and Experimental Methods
NR (Standard Vietnamese Rubber SVR-10, dirty contents 0.1 wt%), ENR-25 (Epoxyprene 25, Muang Mai Guthrie Public Co., Ltd., Muang Phuket, Thailand), and BR (NdBR-60, Kumho Petrochemical Co., Daejeon, Korea) were used as the base rubber. Silica (Ultrasil 7000 GR, Evonik Industries AG, Essen, Germany, Brunauer–Emmett–Teller (BET) surface area: 160 175 m2/g) and CB (N234, IA: 119 g/kg, OAN: 125 cm3/100 g, OCI Co. Ltd., Seoul, Korea) were used as filler. Additionally, bis-[3-(triethoxysilyl)propyl]-tetrasulfide (TESPT, Si-69, Evonik Korea Ltd., Seoul, Korea) was used as the silane coupling agent. TDAE oil (Kukdong Oil & Chemicals Co., Yangsan, Korea) was used as a processing aid. Zinc oxide (Sigma-Aldrich Corp., Seoul, Korea) and stearic acid (Sigma-Aldrich Corp., Seoul, Korea) were used as crosslinking activators. N-(1,3-Dimethylbutyl)-N′-phenyl-phenylenediamine (6PPD, Kumho Petrochemical Co., Daejeon, Korea) and 2,2,4-trimethyl-1,2-dihydroquinoline (TMQ, Sinopec corp., Beijing, China) were used as antioxidants. Sulfur (Daejung Chemicals & Metals Co., Siheung, Korea) was used as a crosslinking agent and N-tert-butyl-2-benzothiazyl sulfonamide (TBBS, Shandong Yanggu Huatai Chemical Co., Ltd., Liaocheng, China) and 1,3-diphenylguanidine (DPG, 98%, Tokyo Chemical Industry Co. Ltd, Tokyo, Japan) were used as vulcanization accelerators. Furthermore, N-cyclohexylthio phthalimide (PVI, Shandong Yanggu Huatai Chemical Co., Ltd., Liaocheng, China) was used as a pre-vulcanization inhibitor.
Proton nuclear magnetic resonance (1H NMR) spectroscopy (Varian, Unity Plus 300 spectrometer, Garden State Scientific, Morristown, NJ, USA) was used to determine the epoxide contents of ENR as well as the composition of the bound rubber. Samples were dissolved in deuterated chloroform (CDCl3, Cambridge Isotope Laboratories, Inc., Andover, MA, USA), adjusted to a concentration of 15 mg/mL, and placed in a 5 mm NMR tube, and their NMR spectra were recorded.
The glass transition temperatures (Tg) of NR and ENR were measured using a differential scanning calorimeter (DSC-Q10, TA instruments, DE, USA). In this process, the rubber sample was heated from 80°C to 100°C at a heating rate of 10°C/min.
To measure the bound rubber content, 0.2 ± 0.01 g of the compound after the first-stage mixing was placed in a filter paper, which was then immersed in 100 mL of toluene at 25°C for 6 days to extract unbound rubber. Then, toluene was washed with acetone, and compound remaining in the filter was dried. Bound rubber content was calculated by weighing it before and after the experiment. 1H NMR analysis was performed using the extracted unbound rubber to analyze the composition of the bound rubber.
wfg: weight of the filler and gel
wt: weight of the specimen
mf: weight fraction of the filler in the compounds
mr: weight fraction of the polymer in the compounds
To examine the degree of filler network formation in the uncured compound, a strain sweep test (0.28% 40%) was performed at 60°C using a rubber process analyzer (RPA 2000, Alpha Technologies, Hudson, Ohio, USA). As the strain increases, the filler network is destroyed and the storage modulus (G′) decreases. Thus, ΔG′ (G′ at 0.28% − G′ at 40%) which is the difference between G′ at the initial strain and G′ at the final strain measures the degree of filler filler interaction, which is called the Payne effect.18
Mooney viscosity, an evaluation for the processability of compound, was measured using a Mooney rotational viscometer (Vluchem IND Co., Seoul, Korea). It was measured by operating a large rotor (diameter 38.10 ± 0.03 mm, thickness 5.54 ± 0.03 mm) at 100°C for 4 min after preheating for 1 min at 2 rpm according to the conditions specified by the ASTM D1646 conditions.
Cure characteristics of the compound were measured using a moving die rheometer (RLR-3-rotorless rheometer, Toyoseiki, Tokyo, Japan) at a temperature of 150°C and a vibration angle of 1 for 30 min. The minimum torque (Tmin), maximum torque (Tmax), and optimum cure time (t90) of the compound can be determined by this experiment. Subsequently, vulcanizates were prepared by vulcanization in a heating press at 150°C using the optimum vulcanization time.
Vulcanizates were cut into pieces of dimensions 10 mm (length) 10 mm (width) 2 mm (thickness), which were then weighed and stored in tetrahydrofuran (THF, 99%, Samchun Chemical Co., Seoul, Korea) and n-hexane (95%, Samchun Chemical Co., Seoul, Korea) at 25°C for 2 days each to remove organic additives inside the specimens. Next, the specimens were dried at 25°C for 1 day and weighed. Then, the mass fraction of extracted organic additives was calculated. This specimen was then swollen in toluene at 25°C for 1 day and weighed again. Finally, crosslink density was calculated from the measured weight of the specimen using the Flory-Rehner equation (2), as follows:19
v: Crosslink density of vulcanizate (mol/g)
Mc: Average molecular weight between crosslink points (g/mol)
Vr: The volume fraction of rubber in the swollen gel at equilibrium
Vs: The molar volume of solvent (cm3/mol)
ρr: The density of the rubber sample (g/cm3)
χ: The polymer solvent interaction parameter
Mechanical properties (tensile strength, modulus, elongation at break) of the vulcanizates were measured using a universal testing machine (UTM, KSU-05 M-C, KSU Co., Ansan, Korea) at a speed of 500 mm/min on dumbbell-shaped specimens of dimensions 100 mm (length) × 25 mm (width) made according to ATSM D 412.
Abrasion resistance was measured according to ISO 4649 using a Deutsche Industrie Normen (DIN) abrasion tester. The specimens were prepared in a cylindrical shape with a diameter of 16 mm and a thickness of 8 mm. A load of 5 N was applied to the surface of the abrasive sheet attached to a cylindrical drum rotating at 40 rpm, and the reduced mass was measured after running it for 40 s.
To determine viscoelastic properties of vulcanizates, tan δ was measured using a dynamic mechanical analyzer (DMA Q800, TA Instrument, DE, USA) at a strain of 0.2% and a temperature sweep from 80°C to 100°C at a frequency of 10 Hz. In addition, a dynamic mechanical thermal spectrometer (DMTS, EPLEXOR 500 N, GABO, Ahlden, Germany) was used to measure tan δ by strain sweeping from 0.5% to 10% strain at a temperature of 60°C and a frequency of 10 Hz.
Particulate matter in tire tread specimens was determined using an aerodynamic particle sizer (APS, TSI 3321, MN, USA) by measuring the mass concentration of particulate matter generated during the wear of the specimen. A schematic of the test is illustrated in Figure 1. A load of 20 N was applied vertically to the specimen that was in contact with the sandpaper belt, and the specimen was abrased by rotating the sandpaper belt (80 grit) at a speed of 20 m/min. In this study, clean, dry, moisture-free air was supplied to the chamber at 5 L/min (flow meter, TSI 5300, MN, USA) using an air filter (filtered air supply, TSI 3074B, MN, USA). Finally, particles in the size range of 0.37 μm 20 μm generated during specimen wear were measured.
In this evaluation, formulations were designed for CB-filled NR/BR compounds and silica-filled ENR/BR compounds to determine the effect of the blending method on compound properties and the amount of particulate matter generated. Conventional blending compounds were prepared by simultaneously mixing the base rubber, filler, and additives. For Y-blending compounds, MB was pre-mixed according to the base rubber and filler type, and then MBs were blended. Furthermore, NR/BR/CB-C (11:00, min:s) and ENR/BR/silica-C (15:00, min:s) with the same mixing time as Y-blending compounds were also prepared to consider the effect of increasing mixing time on the compound.
Compounds were manufactured using an internal kneader (300 cc, MIRAESI Company, Gwangju, Korea). Formulation of compounds is shown in Table 1, and mixing procedure is shown in Table 24. Fill factor was set at 80% of the mixer capacity and unit was parts per hundred rubber (phr) which was based on rubber. First, in the pre-mixing stage, MBs were manufactured according to the base rubber and filler type at the same dump temperature as the 1st mixing stage. Then, kneading was started at 80°C 100°C, and the dump temperature was controlled at 140°C 155°C. Unlike conventional blending, Y-blending compounds were manufactured using the Y-blending method which is a process of blending MB. Subsequently, in the 2nd mixing stage, kneading was started at 50°C, and the dump temperature was controlled to 80°C 90°C. After each mixing stage, the compound was sheeted using a two-roll mill. The optimum cure time of compounds was confirmed at 150°C using a moving die rheometer (MDR). Then, vulcanizates were prepared by curing the compounds for the optimum cure time in a hydraulic press at 150°C.
Results and Discussion
1H NMR spectrum of NR, ENR-25 is shown in Figure 2, and the epoxide contents and Tg of rubber are shown in Table 5. NR and ENR-25 showed methine proton signals at 5.1 ppm, and only ENR-25 showed signals from epoxide protons at 2.7 ppm. At 3.6 ppm, the signals were generated by cyclic ether structures created by ring opening of adjacent epoxide groups.20 The epoxide contents were calculated by using two peak areas (A2.7, A5.1) at 2.7 ppm and 5.1 ppm.21
Rubber | 1H NMR results | DSC results |
---|---|---|
Epoxide contents (%) | Tg (°C) | |
NR | 0 | 62 |
ENR-25 | 25 | 42 |
The result confirmed that NR has 0% epoxide content because no epoxide group was present. For ENR-25, the presence of 25% epoxide groups was confirmed. As the polarity of chain increases, Tg has a higher value as chain mobility is limited by intermolecular interactions.22,23 Thus, ENR-25 exhibited a higher Tg (−42°C) than NR (−62°C).
The results of analyzing the bound rubber content and composition are summarized in Table 6. Bound rubber formation is evidence of filler–rubber interaction, which includes both physical and chemical adsorption and mechanical interaction.24 Bound rubber content analysis revealed that the increase in mixing time in the conventional blending process resulted in minimal change because the effect of chain scission of rubber was offset by the improved filler dispersion. In contrast, the Y-blending compounds showed increased bound rubber content upon improving the uneven filler distribution in the heterogeneous rubber matrix.
In CB-filled NR/BR blend compounds, CB is preferentially distributed in the BR phase.15,25 In silica-filled ENR/BR blend compounds, silica is preferentially distributed in the ENR phase. To confirm this distribution, the composition was analyzed using unbound rubber obtained from the bound rubber extracts. The result showed that in conventional blending compounds, the filler was biased toward the BR and ENR phases, which have an excellent affinity with the filler, leading to a different composition than the base rubber ratio used in compound manufacturing. However, when Y-blending method was applied, the composition of the base rubber was relatively similar to the base rubber ratio used in compound manufacturing. This suggests that the uneven filler distribution in the heterogeneous rubber matrix can be improved by using the Y-blending method.
The results of Payne effect measurements of the compounds are shown in Figure 3 and Table 7. Silica is hydrophilic filler and is difficult to disperse within a hydrophobic rubber matrix. In addition, proteins and phospholipids in the NR interfere with the silanization and coupling reaction of silica and rubber. However, silica-filled ENR/BR blend compound exhibited much better filler dispersion than CB-filled NR/BR blend compound due to the ring opening of the epoxide group, which formed chemical interaction with the silanol group on the silica surface. Furthermore, compounds prepared using the Y-blending method exhibited the lowest ΔG′ due to the improvement of filler dispersion with the increase of mixing time and the uniform filler distribution in the heterogeneous rubber matrix.
The cure characteristics obtained using MDR and Mooney viscosity, a measure of compound processability, are shown in Figure 4 and Table 8. Y-blending compounds exhibited better filler dispersion and uniform filler distribution than conventional blending compounds, accordingly, they exhibited lower Mooney viscosity.
In MDR curves, the value of ΔT (Tmax−Tmin) is closely correlated with the crosslink density of the compound.26 Tmin is lower for less filler flocculation within the com-pound.27 Introduction of Y-blending resulted in a lower ΔT due to the increased chain scission of the base rubber. Moreover, uniform filler distribution reduced filler flocculation, resulting in a lower Tmin. Particularly, ENR/BR/silica-Y compound exhibited a lower ΔT as less chemical interaction occurred between silica and ENR due to decreased silica in the ENR phase. Silica can adsorb vulcanization accelerators because it is a hydrophilic filler.5 Furthermore, ENR causes a competing reaction with silane due to its polar characteristics.28 However, ENR/BR/silica-Y compound separates the MB manufacturing process, so the silane used to manufacture BR/silica MB does not participate in a competing reaction with ENR. As a result, ENR/BR/silica-Y compound showed faster t90 due to a decrease in the adsorption of vulcanization accelerator by silica.
Crosslink density, mechanical properties, and DIN abrasion loss of the compounds are shown in Figure 5 and Table 8. In the conventional blending compounds, the difference in crosslink density was not significantly affected by mixing time because the chain scission of the base rubber was offset by the improvement in filler dispersion. However, when Y-blending method was introduced, silica-filled ENR/BR blend compound exhibited lower crosslink density due to reduced chemical interaction between silica and ENR, unlike the CB-filled NR/BR blend compound, which has no functional groups in the base rubber.
In mechanical properties, the tensile modulus determines rubber stiffness, which is higher for compounds with high bound rubber contents and excellent filler-rubber interaction.29 The Y-blending compounds showed higher M300 (modulus at 300% elongation) values than the conventional blending compounds. This is attributed to the improved filler distribution within the heterogeneous rubber matrix, which increased the bound rubber content and thus improved the reinforcement by the filler.17
Abrasion loss observed in the DIN abrasion test is strongly correlated with filler distribution in the rubber ma-trix.30 In particular, abrasion resistance is significantly reduced when phase separation occurs due to the affinity difference between filler and base rubber.17 Uniform filler distribution obtained by applying the Y-blending method reduced the effect of the affinity difference, thus increasing the bound rubber content. As a result, the Y-blending compound exhibited better abrasion resistance.
When a tire rotates under the load of a vehicle, all parts of the tire lose energy as they undergo repeated deformation and recovery. This phenomenon is called hysteresis loss. In the low-temperature region, where the motion of filler is restricted, micro-brownian motion of the polymer within the network is the main source of energy dissipation. Thus, in the vicinity of Tg, the hysteresis loss of the compound increases with increasing volume fraction of the polymer.31 Tan δ at 60°C is a measure related to the hysteresis loss that occurs during the destruction and reformation of the filler network. Its higher value is more unfavorable for the rolling resistance of the compound.32 Tan δ at 0°C is a measure related to the wet grip performance of the tire, and the higher its value, the better wet grip performance.33
Tan δ values as a function of the temperature change under 0.2% strain, obtained using dynamic mechanical analysis, are shown in Figure 6 and Table 10. NR and BR are partially compatible with each other but in the NR(70)/BR(30) compound, Tg peaks due to base rubber appear respectively.16 Furthermore, as ENR is more polar than NR, it is less compatible with the non-polar BR. However, the Y-blending method increases the compatibility of heterogeneous rubbers by uniform filler distribution.17 With the introduction of the Y-blending method, polymer volume fraction of NR phase decreased in the CB-filled NR/BR blend compound, resulting in lower tan δ at a Tg around −60°C. In contrast, in the silica-filled ENR/BR blend compound, polymer volume fraction of ENR phase increased, resulting in higher tan δ at a Tg around −35°C.
DMA measurements showed the hysteresis loss is mainly due to the filler distribution in the heterogeneous rubber matrix. When Y-blending method was applied, CB-filled NR/BR blend compound showed high tan δ at 0°C due to decreased polymer volume fraction in the NR phase. In contrast, silica-filled ENR/BR blend compound showed low tan δ at 0°C due to increased polymer volume fraction in the ENR phase.
Improved filler dispersion of compound reduces hysteresis loss caused by destruction and reformation of filler network, leading to a low tan δ at 60°C value.34 Tan δ values as a function of strain at 60°C using DMTS are shown in Figure 7 and Table 10. Unlike the low strain region, the filler network is mostly destroyed in the high strain region (above 5% strain). So the effect of hysteresis due to filler network destruction and reformation is more prominent.35,36 Y-blending compounds formed less filler networks by improved filler dispersion and uniform filler distribution in the heterogeneous rubber matrix. Accordingly, they exhibited a low tan δ at 60°C in the high strain region.
The measurement results of particulate matter generated by abrasion of compound are shown in Figure 8 and Table 11. It has been demonstrated that the amount of particulate matter generated by compound is highly correlated with wear resistance and filler rubber interaction.5,37 In the experimental results, silica-filled ENR/BR blend compound showed high bound rubber contents due to strong filler rubber interaction and a significantly lower particulate matter generation than the CB-filled NR/BR blend compound. Furthermore, Y-blending compounds exhibited a lower particulate matter generation than conventional blending compounds due to uniform filler distribution in the heterogeneous rubber matrix and improved filler rubber interaction. Consequently, the application of the Y-blending method can reduced PM2.5 particulate matter generation from the CB-filled and silica-filled compounds by 38% and 60%, and that of PM10 by 29% and 67%, respectively. This confirmed that Y-blending is an effective blending method that can significantly reduce particulate matter generation. This experiment is the result of a laboratory wear test, and the wear mechanism is different from that of in-service wear test, so the tendency can be different. Therefore, it is a good idea to compare the generation of particulate matter by the in-service wear test by referring to the results of this evaluation.
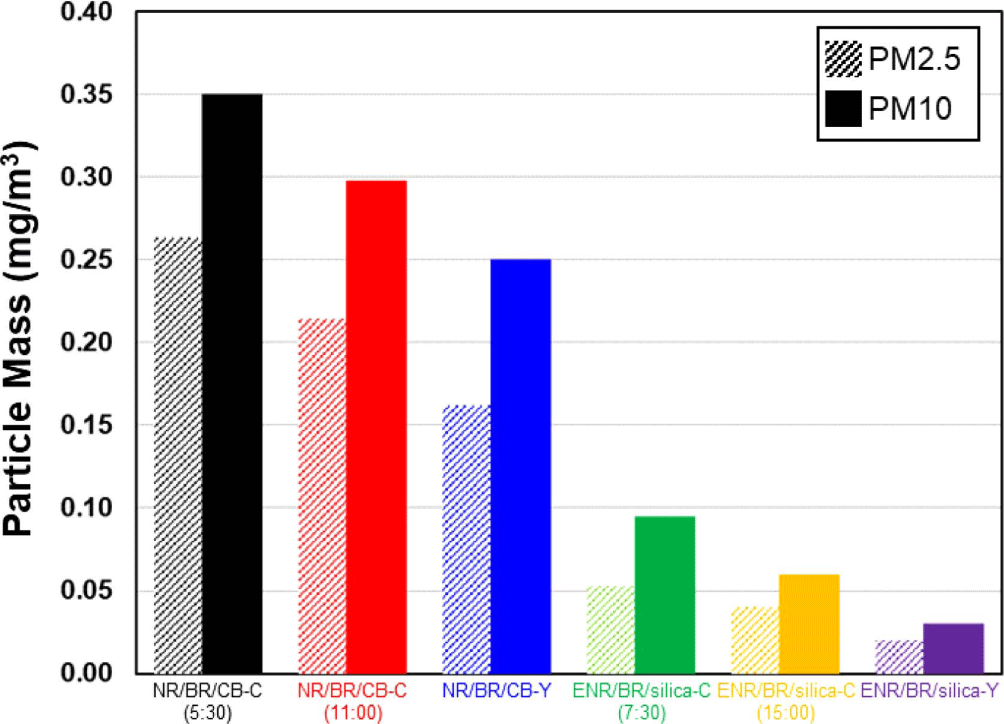
Conclusions
In this study, CB-filled NR/BR blend and silica-filled ENR/BR blend compounds were manufactured according to the blending method to determine the physical properties of the compounds and the amount of particulate matter generation. The experimental results showed that introducing Y-blending improved the uneven filler distribution originating from the difference in affinity between rubber and filler, thus enhancing processability. Furthermore, Y-blending compounds with strong filler rubber interaction exhibited superior mech- anical properties and abrasion resistance relative to the conventional blending compounds. Uniform filler distribution resulting from introducing the Y-blending method also showed improvements in rolling resistance, and improved filler rubber interaction was also highly effective in reducing particulate matter generation. The findings of this study present a guideline for the Y-blending method, a manufacturing technology that can improve filler distribution and properties in TBR tire tread compounds while reducing the amount of particulate matter.