Introduction
Recent advancements in the field of flexible and stretchable electronic devices have driven active research in the development of electronic skin. Electronic skin, also known as e-skin, plays an important role in human-machine interaction, particularly in the fields of robotics and healthcare. It enables the detection and monitoring of a wide range of stimuli, including pressure, proximity, deformation and temperature. Differing from conventional sensors relying on rigid substrates and materials, electronic skin necessitates the use of flexible or stretchable materials to achieve its distinctive flexibility.1-3
Extensive research is currently underway in the realm of electronic skin, employing various mechanisms including capaci-tance, piezoresistance, piezoelectricity, and triboelectricity. Electronic skin sensors utilizing a piezoresistive mechanism operate on the principle that external pressure changes manifest as corresponding variations in resistance values. These sensors have been widely investigated due to their relatively simple structure and operational principles. However, they exhibit sensitivity to ambient temperature change and suffer from poor hysteresis, primarily attributed to the extensive use of conductive fillers to ensure conductivity. In contrast, electronic skin sensors employing piezoelectric and triboelectric mechanisms offer the advantage of not requiring an external power source. Nevertheless, they exhibit reduced sensitivity and precision in pressure measurements compared to other methods. Conversely, capacitance mechanism-based electronic skin sensors feature a relatively uncomplicated structure, facilitating sensor production, and excel in sensitivity.2,3
This study aimed to produce an electronic skin sensor employing a capacitance mechanism through a straightforward method using natural rubber and nitrile butadiene rubber (NBR), both commonly utilized materials in the rubber industry, to create a flexible sensor. Natural rubber, renowned for its remarkable elasticity, was selected for its expected excellent sensor repeatability and resilience to pressure. Meanwhile, NBR, a synthetic rubber composed of polar molecules, was chosen for its superior dielectric constant in comparison to other rubber types, making it an ideal dielectric material for the electronic skin sensor. The rubber compound, serving as the dielectric, was formulated by blending foaming agents and other mixing materials using a mixer commonly employed in the rubber industry. During the cross-linking process, this compounded rubber was transformed into a sponge-like structure with uniformly distributed pores through the foaming process. Subsequently, an electronic skin with a capacitance mechanism was manufactured using the resulting foam rubber, and the sensor’s characteristics were analyzed.
Experimental
The dielectric material used in this study consisted of Malaysian natural rubber (CV50) and Kumho Petrochemical’s nitrile butadiene rubber (KNB-35L). Details regarding the ingredients and formulations of the rubber compound can be found in Table 1. The electrode material for the tactile sensor was created using conductive tape composed of nickel and copper fibers. To protect the electrodes, the outermost layer of the electronic skin was made from silicone rubber (Ecoflex 003).
The dielectric rubber employed in the tactile sensor for electronic skin was prepared through compounding using a Banbury mixer (BR-1600, FAREL) and a two-roll mill. To reduce the stress experienced by the rubber molecules during the mixing process, the compounded rubber was stored at room temperature for 24 hours. Subsequently, the compounded rubber was processed through a cross-linking and foaming procedure, conducted at a temperature of 155°C for an appropriate duration, determined using a rheometer (MDR-2000, Monsanto). Utilizing the manufactured dielectric rubber, an electronic skin sensor employing a capacitance mechanism was constructed, as illustrated in Figure 1. The compounded rubber served as the dielectric material, with electrodes positioned both above and below it. To shield the electrodes, the electronic skin sensor was coated with silicone rubber.
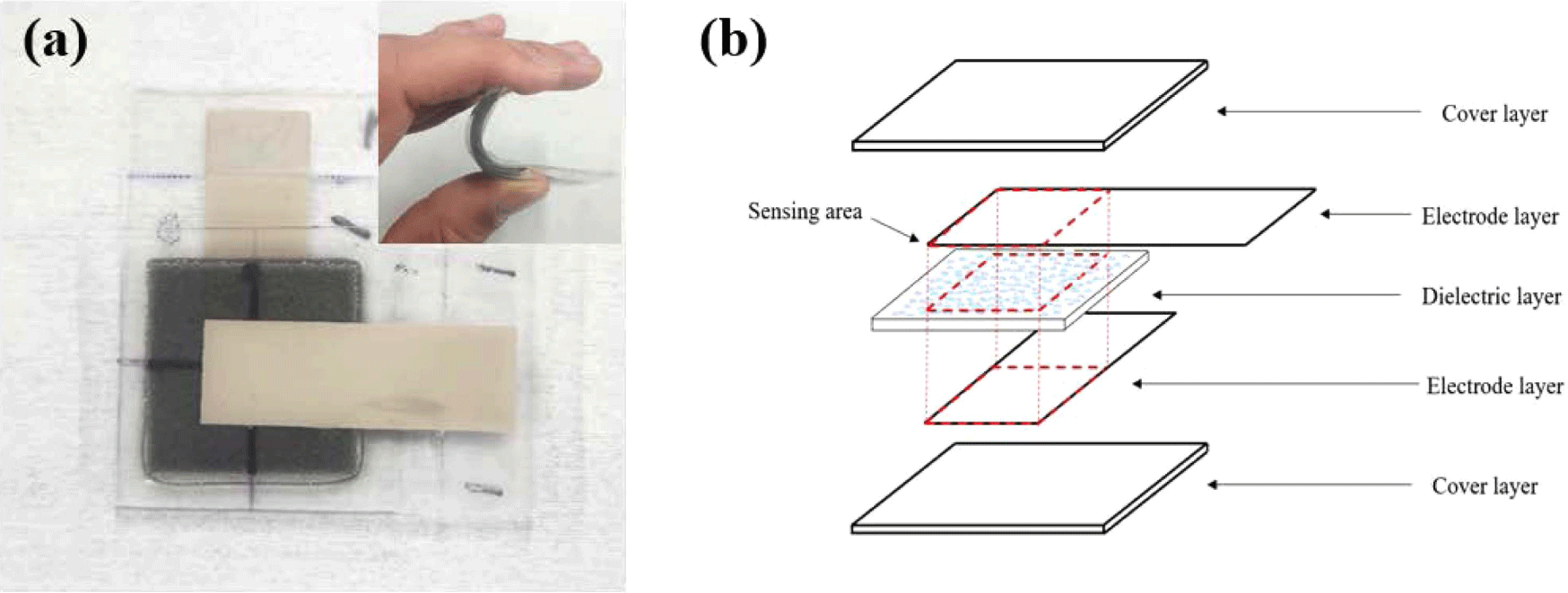
The compressive modulus of the produced dielectric rubber was assessed using a push-pull gage (JSV-H1000, JISC). The microstructure of the foamed dielectric rubber was examined through an optical microscope (AM41132ZT, Dino-lite). To assess the signal generation in response to applied pressure levels, the variation in voltage upon exerting a specific pressure on the sensor was observed and measured using a push-pull gage and a digital multimeter (DMM6500, KEITHLEY). Typically, capacitance sensors are evaluated by monitoring changes in capacitance. However, as capacitance measurements are derived from voltage changes, this study employed alternating current power to observe voltage alterations.
Results and Discussion
The results of observing the microstructure of the rubber manufactured for use as the dielectric material in the electronic skin sensor are presented in Figure 2. It is evident that the dielectric rubber made from natural rubber (NR) exhibits a uniform structure with a pore size of approximately 50 μm. Conversely, the dielectric rubber produced from nitrile butadiene rubber (NBR) displays smaller pores, around 20 μm in size, in contrast to NR. Upon comparing the ts1 values, which represent scorch time as presented in Table 2, it is apparent that the ts1 value for NBR is shorter than that of NR. This observation suggests that NBR, with its shorter scorch time, did not foam adequately due to a faster cross-linking initiation compared to NR.4 In Figure 2(c), the pressure-compression distance curve of the manufactured rubber is depicted. Notably, NBR demonstrates a higher compressive modulus (slope) in comparison to NR. This outcome is attributed to the elevated maximum torque value in Table 2 and the smaller size of the foam cells.
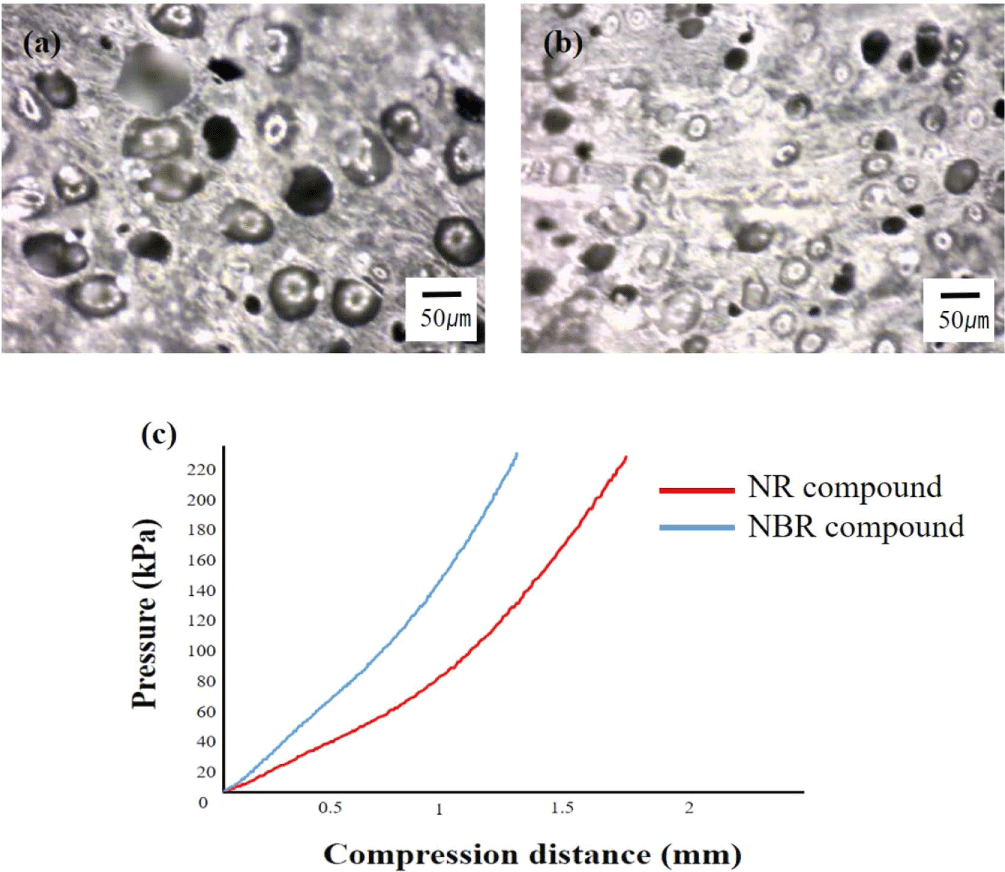
Rubber compounds | Time (min) | Torque(N·m) | |||
---|---|---|---|---|---|
t10 | t90 | ts1 | Min. | Max. | |
NR | 1.37 | 19.45 | 7.17 | 0.5 | 2.2 |
NBR | 1.73 | 21.08 | 4.87 | 0.5 | 3.3 |
The signal generation principle of the capacitance mechanism tactile sensor can be explained by the equation below.5,6
In equation (1), C represents the capacitance value, while ε stands for the permittivity of the dielectric. A denotes the area of the electrodes that overlap, facing both the top and bottom, and d signifies the distance between the bottom and top electrodes. the distance (d) between electrodes and the capacitance (C) are inversely proportional. In equation (2), Xc represents the reactance value, representing the resistance effect in the AC power circuit, with ω being a function of the AC power supply frequency. According to equation (2), there exists an inverse relationship between capacitance and reactance, whereby higher capacitance values correspond to lower reactance. As reactance functions as resistance in an AC power circuit, its reduction leads to changes in voltage values. These altered voltage values are then detected as signals. In simpler terms, when pressure is applied, the d in equation (1) decreases, subsequently increasing the capacitance value. The augmented capacitance value results in lowered reactance within the AC power circuit, leading to an increase in voltage values. This increase in voltage values can be utilized to measure the magnitude of pressure.
Figure 3 shows the results of signal generation evaluation based on the pressure levels applied to the manufactured electronic skin sensor. Both sensors exhibit noticeable voltage changes, extending up to a pressure of 212 kPa. The NR-based electronic skin sensor displayed a voltage change of approximately 35% at 14 kPa, while the NBR-based sensor showed a voltage change of about 20%. In the high-pressure range of 212 kPa, the NR-based sensor exhibited a voltage change of around 110%, while the NBR-based sensor demonstrated a voltage change of about 90%. These findings can be attributed to the microstructure of the rubber used as the dielectric. NR-based dielectrics with larger pore sizes are considered to yield higher signal due to the relatively greater compression distance of the dielectric, even at low pressures. Figure 4 shows a graph of the relative voltage change of the electronic skin sensor according to pressure in the range of 15-212 kPa. The NR dielectric-based sensor showed excellent sensitivity of 1.05 %/kPa at pressures below 63 kPa, and 0.13 %/kPa at pressures above 106 kPa. The NBR dielectric-based sensor showed a linear sensitivity of 0.5 %/kPa in the pressure range below 106 kPa and 0.15 %/kPa above 104 kPa. This result is considered to be because the pores of the NBR-based dielectric are relatively small and the solid portion occupies a relatively large portion, so a relatively high pressure is required to completely compress the pores. It can be seen that in order to exhibit excellent sensitivity, the compression modulus is low, so there must be a large compression deformation even at a small pressure. It can be seen that the NBR-based sensor has better sensitivity at high pressures of 104 kPa or higher for the NR-based sensor and the NBR-based sensor. At high pressure, since the pores are completely compressed, it is believed that the higher the dielectric constant of the dielectric material, the higher the sensitivity.7
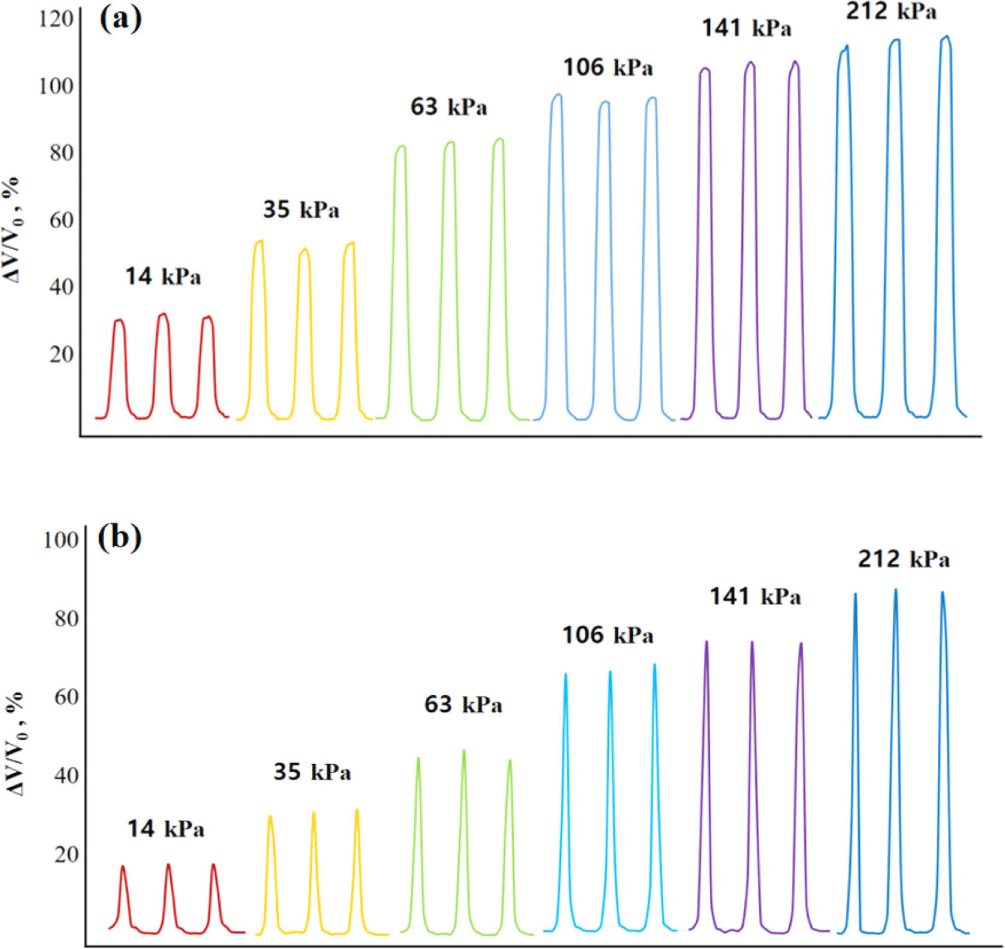
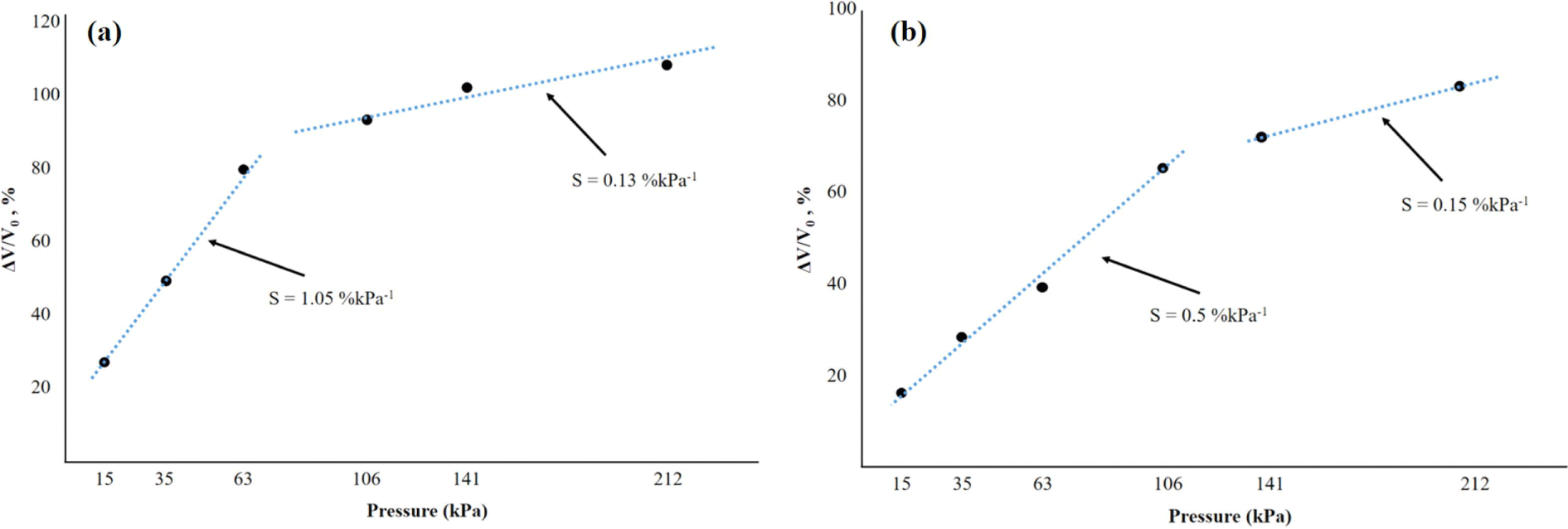
Figure 5 shows the response time of the manufactured sensor. It can be seen that both NR- and NBR-based sensors exhibit good response and recovery times of approximately 100 ms. The results of testing the durability of the sensor by repeatedly applying pressure for 5000 cycles are shown in Figure 6. The test pressure was evaluated as a section where the signal increases linearly in the low pressure area. The NR-based sensor was tested at a pressure of 63 kPa, and the NBR-based sensor was evaluated at a pressure of 106 kPa. NR-based sensors maintain relative voltage changes of approximately 80% for 5000 cycles without performance degradation. On the other hand, NBR initially had a relative voltage change value of 70%, but as the cycle was repeated, the base line and peak of the signal were observed to increase. It is considered that this is because NR is superior to NBR in terms of hysteresis, which recovers as pressure is repeated.
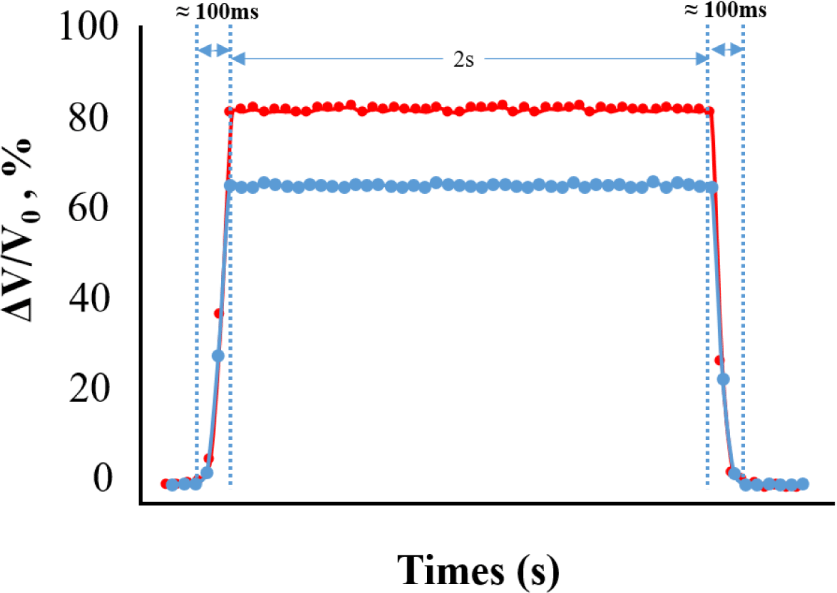
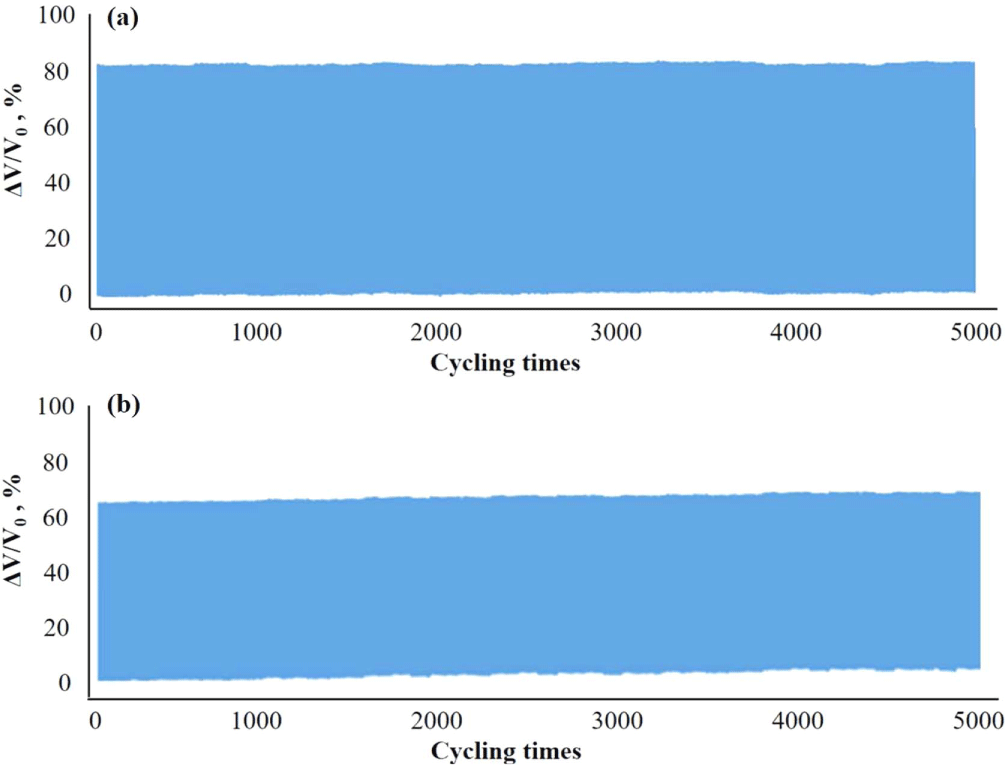
Table 3 shows a comparison of the performance of capacitive tactile sensors reported by previous researchers. Zhu et al. al. produced a capacitive tactile sensor with a sensing range similar to that of this study and reported its characteristics. A composite was manufactured by dispersing carbon black in PDMS and used as a dielectric, and the sensitivity of the capacitive tactile sensor is reported to have a sensitivity of 1.9 %/kPa. This result shows a slightly higher sensitivity compared to the results of this study, but the sensitivity decreases sharply in the cycling test. PDMS is known as a material with excellent dielectric constant and is widely used as a dielectric material for capacitive sensors. When carbon black is dispersed in PDMS to make a composite and used as a dielectric, the electrical properties change when the dispersed carbon black is connected by deformation, which can increase the sensitivity of the sensor. However, due to poor compatibility between silicone rubber and carbon black, hysteresis occurs during repetitive fatigue, resulting in a rapid deterioration in sensor performance in cycling tests.10 In comparison, the natural rubber used in this study is believed to have shown excellent performance in the cycling test due to its higher affinity with carbon black than silicone rubber.
References | Dielectric materials | Sensitivity | Sensing range |
---|---|---|---|
Kai Ke8 | TPU / CNS*/GNP** | 0.2 %/kPa | 100~1300 kPa |
Yinlong Zhu9 | PDMS / CB*** | 1.96 %/Kpa | 10~200 kPa |
This work | NR or NBR / CB | 1.05 %kPa | 10~200 kPa |
Conclusions
An electronic skin tactile sensor was manufactured in a relatively simple method using NR, which has excellent elasticity, and NBR, which has excellent dielectric constant. The characteristics of the manufactured electronic skin sensor were analyzed. It was confirmed that the NR-based electronic skin sensor generates sufficient signals as a sensor in the pressure range of 14 kPa to 212 kPa. NR-based electronic skin sensors have excellent sensitivity with a sensitivity of approximately 1%/kPa in the low pressure range (<64 kPa). The sensitivity and sensing range of the sensor were found to be greatly affected by the microstructure (pore size, density, etc.) of the manufactured dielectric and the elasticity of the rubber. It can be manufactured in a relatively simple way using rubber that is commonly used in the rubber industry, and it is considered that it will be possible to manufacture an electronic skin with sufficient performance.