Introduction
Solution styrene-butadiene rubber (S-SBR) and silica have been used to improve the wet grip and rolling resistance properties of tire tread compounds.1-4 S-SBRs generally have a higher 1,2-unit content than emulsion SBR, and their high vinyl content can improve traction and fuel economy.5 However, recent special S-SBR grade for electric vehicle tire shows low vinyl content. In addition to the microstructures of SBR, the modification, filler type, and silica content also influence the properties of SBR compounds.6-11 Dynamic mechanical analysis (DMA) is usually used to predict the wet grip and rolling resistance properties; the tangent delta (tanδ) at 0°C and 60°C of a rubber composite are used for predictors of the wet grip and rolling resistance, respectively. A higher 0°C tanδ correlates to a better wet grip, while a lower 60°C tanδ correlates to better rolling resistance; the two properties are generally tradeoffs.12,13
Two or three types of SBRs can be blended to improve the physical properties of tire tread compounds. In this study, four types of SBRs with different microstructures were employed to prepare SBR/SBR biblend compounds, and their dynamic mechanical properties were investigated by obtaining the tanδ at 0°C, tanδ at 60°C, and glass transition temperature (Tg) values from DMA results. These results were then compared with the expected values obtained from the DMA results of the single SBR samples. The findings aided in understanding which blends and ratios can improve the wet grip and rolling resistance properties as well as the glass transition temperature.
Experimental
Four types of SBRs (SBR1, SBR2, SBR3, and SBR4) with different microstructures were used (Table 1). Three combinations of SBR1/SBR2, SBR2/SBR3, and SBR3/SBR4 were designed, and four blend ratios of 80/20, 60/40, 40/60, and 20/80 were applied (Table 2). Mixing for master batch (MB) was performed using a Kneader type mixer and final mixing (FM) was performed using a two-roll mill. The vulcanizates were prepared by curing the compounds in a compression mold at 170°C for 30 min.
SBR | Styrene content (wt%) | 1,2-Unit content (wt%) |
---|---|---|
SBR1 | 23.5 | 17 |
SBR2 | 38 | 24 |
SBR3 | 25 | 61 |
SBR4 | 34 | 48 |
Dynamic mechanical properties were measured using a Qualimeter Eplexor 500N of Gabo Co. (Germany) according to ASTM D2231-87. The sample thickness was about 3 mm. The instrument was operated by setting the frequency of 11 Hz with 0.25% strain. The measurement temperature was - 50 to +80°C at a heating rate of 2°C/min.
Tetrahydrofuran (THF), n-hexane, and toluene were purchased from Daejung Chemicals & Metals Co. (Republic of Korea). The sample was cut with dimention of 0.5 × 0.5 cm2 and its thickness was approximately 3 mm. Organic additives in the sample were removed by extracting with THF and n-hexane for 3 and 2 days, respectively, and it was dried for 2 days at room temperature. The weight of the organic materials-extracted sample was measured, and then the sample was soaked in toluene for 2 days at room temperature. The weight of the swollen sample was measured. The swelling ratio (Q) was calculated by equation (1).
where Ws and Wu are weights of the swollen and unswollen samples, respectively. Experiments were carried out three times and they were averaged. The reciprocal of the swelling ratio (1/Q) is generally used as apparent crosslink density.
Results and Discussion
In this study, we measured the apparent crosslink densities of the samples (Table 3), instead of calculating the crosslink density using the Flory–Rehner equation,14 to avoid errors caused by differences in the microstructures of the SBRs. The order of 1/Q for the single rubber samples was SBR2 > SBR1 > SBR4 > SBR3. The three microstructures in SBR, the styrene unit, 1,2-unit, and 1,4-unit, have 0, 1, and 2 sulfur-crosslinking sites, respectively. Thus, it can be expected that the SBR vulcanizate with a higher 1,4-unit content will exhibit a higher crosslinking density. The 1,4-unit contents of the SBRs were in the order of SBR1 > SBR2 > SBR4 > SBR3, exhibiting values of 59.5, 38, 16, and 14 wt%, respectively. For SBR1 and SBR2, the orders of 1/Q and 1,4-unit content were reversed; that is, SBR1 had a greater 1,4-unit content than SBR2, but a lower 1/Q value. We found that the 1/Q values of the single rubber vulcanizates with a high 1,2-unit content (SBR3 and SBR4) were much lower than those of the single rubber vulcanizates with a low 1,2-unit content (SBR1 and SBR2). Meanwhile, for the SBR/SBR biblend samples, the order of 1/Q was A series (SBR1/SBR2) > B series (SBR2/SBR3) > C series (SBR3/SBR4). The measured 1/Q values were lower than the expected 1/Q values, except for the samples of SBR1/SBR2 = 20/80 and SBR3/SBR4. This indicates that mixing two SBRs can reduce the crosslink density compared to the expectation.
Figure 1 shows variations of the tan values at 0°C and 60°C of the SBR1/SBR2 biblend composites with the blend ratio. The 0°C tanδ value increased as the SBR2 content increased, while the 60°C tanδ value decreased. This implies that both the wet grip and rolling resistance properties of the SBR1/SBR2 blend composites improved with increasing SBR2 content. However, these values were inferior to those of the SBR2 single sample. Furthermore, the tanδ values at 0°C and 60°C deviated from the expected values. The 0°C tanδ values were lower than the expected values, except for the SBR1/SBR2 = 80/20 sample; the 0°C tanδ of the SBR1/ SBR2 = 40/60 sample was lower than the expectation by 16%, but that of the SBR1/SBR2 = 80/20 sample was higher than the expectation by 1.4%. The 60°C tanδ value of the SBR1/SBR2 = 80/20 sample was higher than that of the SBR1 single sample, and higher than the expectation by 20%. The 60°C tanδ value approached the expected value with increasing SBR2 content, with the SBR1/SBR2 = 20/ 80 sample exhibiting nearly the same value as the expectation.
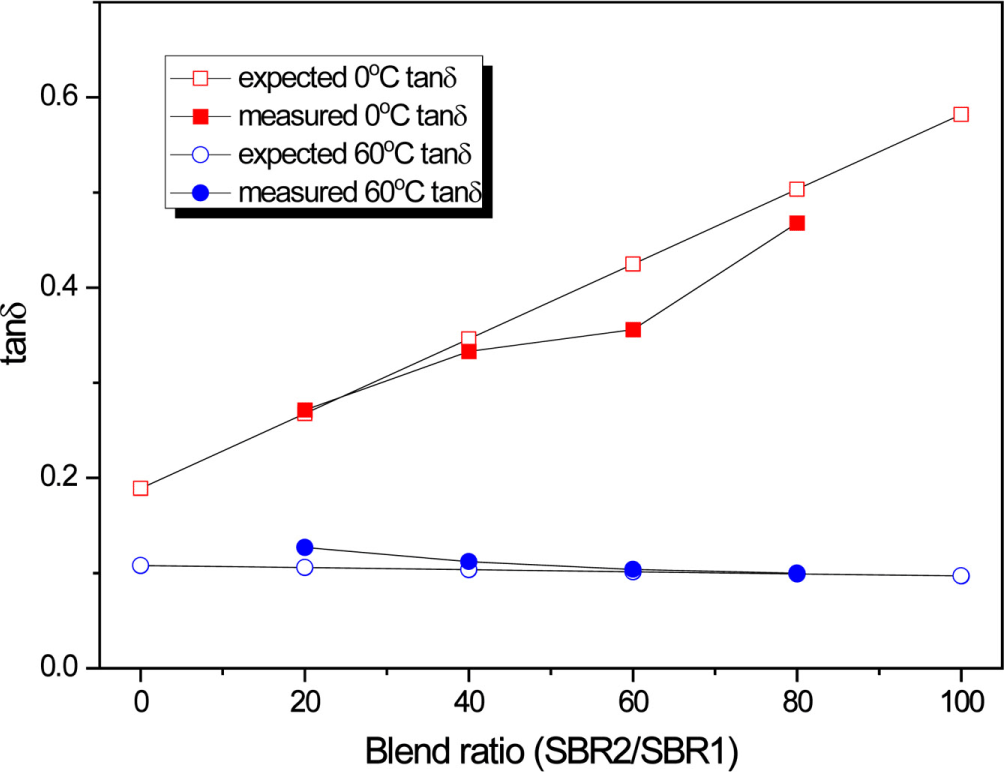
Figure 2 shows variations of the tan values at 0°C and 60°C of the SBR2/SBR3 blend composites with the blend ratio. For SBR2 and SBR3, the 0°C and 60°C tanδ values did not significantly change with the blend ratio, only improving slightly as the SBR2 content decreased and increased, respectively. The measured tanδ values at 0°C of the SBR2/SBR3 = 20/80 and 80/20 samples were notably higher than the expected values by 3.8 and 5.0%, respectively. The tanδ values at 0°C of the SBR2/SBR3 = 80/20 and 20/80 composites were also higher than that of the SBR2 single sample. This shows that the combination of SBR2 and SBR3 can improve the wet grip properties. As there was a large difference in the 1,2-unit contents of SBR2 and SBR3, it can be concluded that the combination of two SBRs with a large difference in 1,2-unit content results in the improvement of wet grip property. However, the rolling resistance property did not improve upon mixing the two SBRs; the 60°C tanδ values were higher than the expectation by approximately 10%.
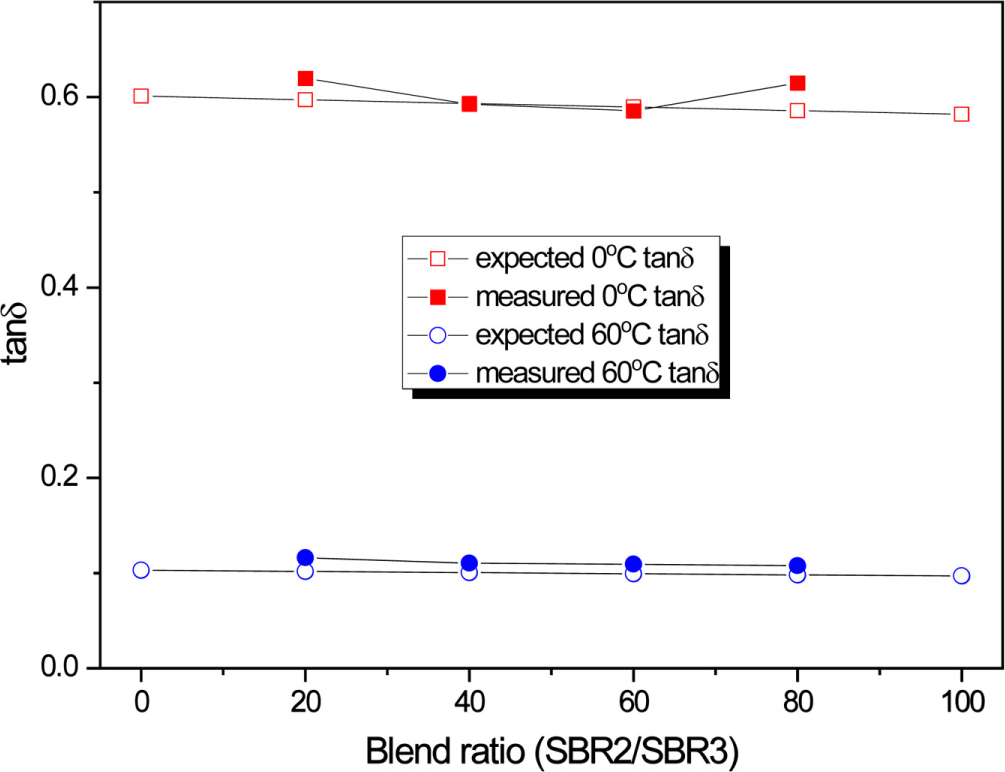
Figure 3 shows variations of the tan values at 0°C and 60°C of the SBR3/SBR4 blend composites with the blend ratio. The expected tanδ values at 0°C and 60°C did not significantly change with the blend ratio of SBR3 and SBR4. It was expected that both the wet grip and rolling resistance properties would improve as the blend ratio changed. There were two notable cases for the improvement of wet grip property like the SBR3/SBR4 = 80/20 and 60/40 composites; the 0°C tanδ values were higher by 4.8 and 8.2%, respectively, compared to the expected values. These values were higher than the 0°C tanδ value of pure SBR3 as well by 3.9 and 6.5%, respectively. This implies that the combination of SBR3 and SBR4 can improve the wet grip property. However, their rolling resistance properties did not improve; the 60°C tanδ values of the SBR3/SBR4 = 80/20 and 60/40 samples were higher by 10.0 and 6.1%, respectively, compared to the expected values. Note that there was one significant case for improvement in the rolling resistance property, the SBR3/SBR4 = 20/80 composite; the 60°C tanδ value was lower than the expected value by 16.7% and was even lower than the 60°C tanδ of pure SBR3 by 4.2%. This implies that the combination of SBR3 and SBR4 can have a positive effect on the rolling resistance depending on the composition of the biblend. However, at this composition, the wet grip property did not improve; the 0°C tanδ of the SBR3/SBR4 = 20/80 increased by 4.2%. For the SBR3/SBR4 = 40/60 composite, both the wet grip and rolling resistance properties improved, compared to the expectation; the 0°C tanδ was higher by 0.3% and the 60°C tan was lower by 3.6%. However, comparing with the SBR3 single composite, both the wet grip and rolling resistance properties did not improve. Figure 4 shows the variations in the glass transition temperature (Tg) of the SBR/SBR blend composites with the blend ratio. For the SBR1/SBR2 blend composites, all Tgs values were higher than the expected values, irrespective of the blend ratio. For the SBR2/SBR3 blend composites, the Tg values were lower than the expected values, with the exception of the SBR2/SBR3 = 40/60 sample. There was a specific trend in the Tg variation of the SBR2/SBR3 = 40/ 60, 60/40, and 80/20 composites: the expected Tg increased with increasing SBR2 content, but the measured Tg decreased. The Tg values of the SBR2/SBR3 = 20/80, 60/40, and 80/20 samples were 7.7, 5.1, and 15.7% lower than the expected values, respectively. The Tg of the SBR2/SBR3 = 20/80 sample was the same as that of pure SBR2. For the SBR3/SBR4 blend composites, the Tg values were higher than the expected values, with the exception of the SBR3/ SBR4 = 40/60 sample, the Tg of which was lower than the expected value by 11.0%, and was even lower than the Tg of pure SBR4 by 0.8°C.
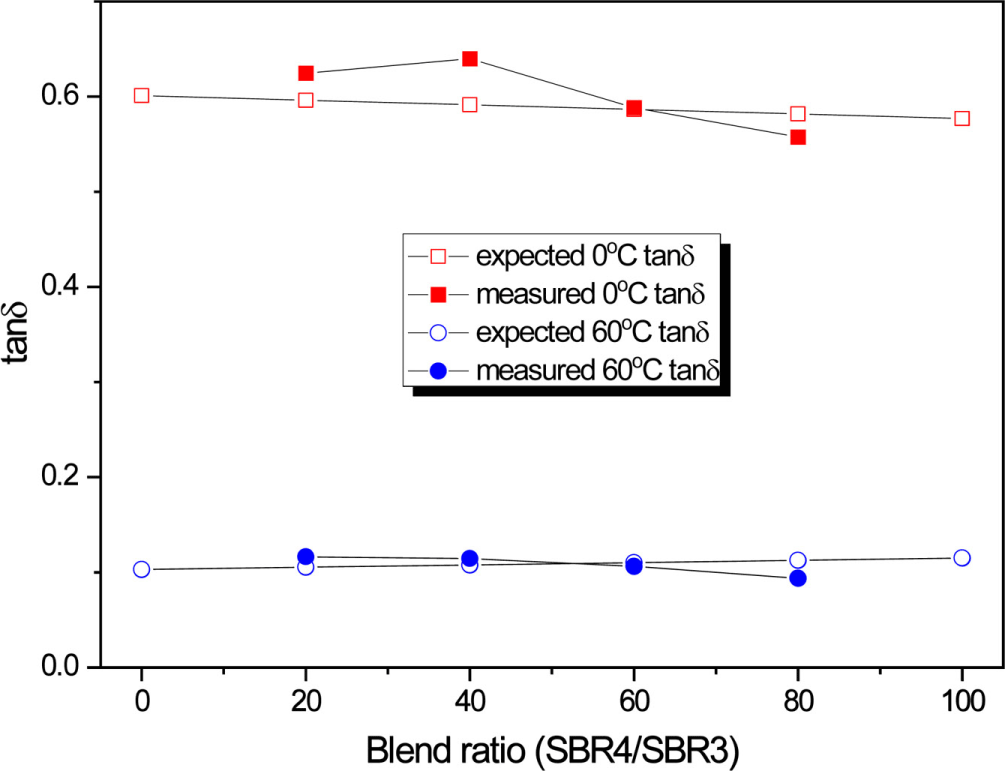
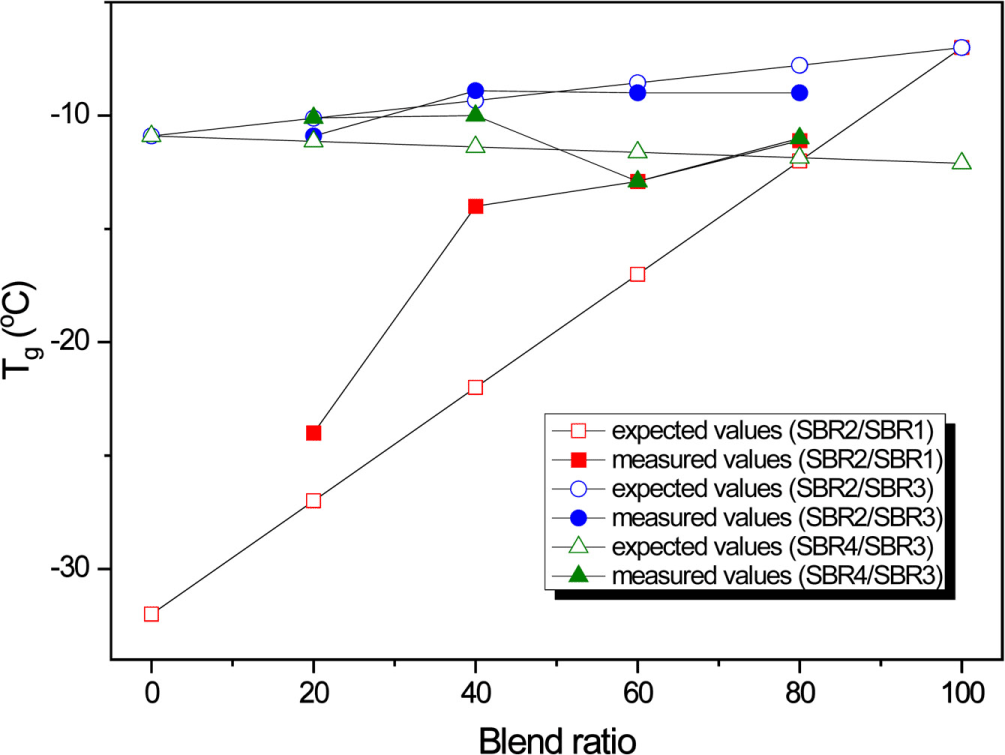
Conclusions
In this study, we evaluated the crosslink densities, wet grip and rolling resistance properties, and Tg values of SBR/SBR biblend composites to understand how they were affected by the SBR type and blend ratio. Many samples had lower crosslink densities than the expected values, indicating that the mixing of two SBRs did not enhance the crosslink density. The order of 1/Q was A series (SBR1/SBR2) > B series (SBR2/SBR3) > C series (SBR3/SBR4). The 0°C and 60°C tanδ values of the SBR/SBR blend composites deviated from the expected values, and some of them were not desirable. The wet grip property of the SBR1/SBR2 = 80/20 sample was slightly higher than the expected value. The 0°C tanδ values of the SBR2/SBR3 = 80/20 and 20/80 samples were higher than the expected values by 3.8 and 5.0%, respectively, and were also higher than that of pure SBR2. The 0°C tanδ values of the SBR3/SBR4 = 80/20 and 60/40 samples were higher than the expected values by 4.8 and 8.2%, respectively, and were also higher than that of pure SBR3 by 3.9 and 6.5%, respectively. The 60°C tanδ of the SBR3/ SBR4 = 20/80 composite was lower than the expected value by 16.7%, and was also lower than that of pure SBR3 by 4.2%. Both the wet grip and rolling resistance properties of the SBR3/SBR4 = 40/60 composite improved; however, the values were inferior to those of pure SBR3. The Tg values of the SBR2/SBR3 = 20/80, 60/40, and 80/20 samples were lower than the expected values by 7.7, 5.1, and 15.7%, respectively, while the Tg of the SBR2/SBR3 = 20/80 sample was the same as that of SBR2. The Tg of the SBR3/SBR4 = 40/60 composite was lower than the expected value by 11.0%, and was lower than that of pure SBR4 by 0.8°C.