Introduction
In 1839, Charles Goodyear discovered by chance that adding sulfur to natural rubber and applying heat transformed it into a stronger and more durable material, a process now known as vulcanization.1,2 Sulfur cross-linking breaks the double bonds in rubber and forms connections between the polymer chains, creating a network of cross-linked molecules. This significantly increased the durability and elasticity of rubber, making it a crucial material for applications such as hoses, belts, and seals. Over time, this material became essential to both civilian and military industries, leading to a rise in global demand.1,3,4
As the demand for rubber increased across various industries, the production and supply of natural rubber remained limited and heavily dependent on specific regions. In the 20th century, political instability led to disruptions in rubber supply chains, which resulted in the development of synthetic rubbers aimed at enhancing productivity and stabilizing supply.5,6 Beyond addressing supply issues, decades of technological advancements led to the creation of various synthetic rubbers with superior chemical resistance, heat resistance, and oil resistance compared to natural rubber. These synthetic rubbers overcame the limitations of natural rubber and contributed significantly as key component technologies to the rapid development of related industrial fields.6
Among the various synthetic rubbers developed to meet industrial needs, acrylic rubber (ACM), a synthetic rubber composed of acrylic monomers such as ethyl acrylate or butyl acrylate, features a saturated backbone that provides excellent resistance to oxidative and UV degradation, allowing it to perform well under prolonged high-temperature conditions.7-9 The polar side chains contribute to its high chemical stability, protecting it from deformation or damage caused by oils and chemicals. This combination of thermal and chemical resistance makes ACM rubber ideal for use in industries that require materials capable of withstanding harsh environments, particularly in automotive and industrial sectors. Common applications include seals, gaskets, and hoses in engine compartments, where exposure to high temperatures, oils, and chemicals is frequent.10-12 Additionally, its stability in ozone-rich environments extends its lifespan in outdoor applications. In addition to its inherent chemical and thermal stability, ACM rubber’s performance can be optimized through precise control of the cross-linking system, which plays a crucial role in determining its physical properties. Different grades of ACM are determined by the cross-linking method used, with systems primarily categorized into epoxy, active chlorine-sulfur, and carboxylic acid-amine chemistries, with carboxylic acid-amine cross-linking offering the highest heat resistance due to its rapid cross-linking speed and strong bond strength.13,14 Therefore, designing an optimal cross-linking system is the most effective approach to expanding the range of properties derived from the base polymer and enhancing the overall performance limits of rubber materials. Herein, we investigated how different cross-linking agent molecular structures affect the properties and durability of acrylic rubber, as an extension of our previous study.14 Specifically, diamine molecules with aliphatic, aromatic, and alicyclic structures were employed, and variations in cross-link density were observed based on the volume, shape, and polarity of these molecules. Notably, the elasticity of rubber, as measured by its ability to recover after exposure to repeated tensile or heat stress, was found to vary significantly depending on the linkage structure of the diamine cross-linking agent. The microstructural control approach proposed in this study, particularly through variation in cross-linking agent structures, offers potential to overcome the limitations of existing general-purpose materials and, ultimately, provides a strategic direction for the design of next-generation rubber materials in the chemical industry.
Experimental
We used PA-526 (Unimatec, Germany), a copolymer with carboxylic cure sites, as the main polymer. For the prototype, various additives were mixed with the polymer, including carbon black particles (N-660, OCI, Korea), an antioxidant (NAUGARD-445, Dupont, USA), a plasticizer (RS-735, Adeka), processing agents (Prosgen #22, Hwasung Chem.), and stearic acid (PH-100, LG H&H, Korea), as listed in Table 1. To control the cross-linking density, 1,3-di-O-tolylguanidine (DOTG, Sigma Aldrich) was used as an accelerator, and eight different cross-linking agents, procured from TCI (Tokyo Chemical Industry Co., Ltd., Japan), were employed, as shown in Table 1.
In the carbon black masterbatch (CMB) compounding step, we prepared the compounds using a mixer (Brabender Technologie GmbH & Co. KG, 300 cc) for 10 min, at 60°C. And then, we stabilized the CMB compounds under room temperature for 1 day. For the final masterbatch (FMB), we used an 8-inch 2-roll mill made of SUS material to mix the crosslinking agent and the accelerator at 40°C for 5 min at a roll speed of 30 rpm, and sheeted. To obtain vulcanizates specimens, FMB was vulcanized in a hot press at 180°C for 10 minutes and post-cured in a dry oven at 180°C for 4 hours.
Results and Discussion
The performance and durability of rubber materials are fundamentally determined by cross-links that form reversible bridges, which facilitate the highly entangled chains to deform under external forces and subsequently return to their original state. Given the critical role of cross-linking in rubber properties, in this study, we focused on the cross-linking behavior, basic mechanical properties, and durability of ACM rubber with carboxylic acid cure sites on the side chains. Various diamine structures were employed, differentiated by their molecular characteristics, as an extension of our previous work on cross-linking behavior.14 The diamine cross-linkers in this study are terminated with diamine groups at both ends and are categorized based on the type of linkage: aliphatic, aromatic, and alicyclic. Specifically, aliphatic linkages include molecules with 6, 8, and 12-carbon alkyl chains, while aromatic structures comprise phenyl, diphenylmethane, and diphenyl ether linkages. For alicyclic linkages, cyclohexyl and diphenylmethane structures were examined (See Figure 1).
To process rubber into the final product, it must under-go the Carbon black master batch (CMB) and Final master batch (FMB) stages. In the CMB process, the rubber raw material, carbon black, stearic acid, and an antioxidant were combined and mixed at 60°C for 10 minutes, as specified in the recipe shown in Table 1. This preliminary mixing step aids in dispersing the carbon black evenly within the rubber matrix, contributing to the desired mechanical properties. In the subsequent FMB process, a cross-linking agent and accelerator were added to complete the formulation, enabling the necessary cross-linking reactions during curing to achieve the final material properties. In each ACM formulation, the CMB conditions were kept consistent, while, as shown in Table 1, different types of cross-linking agents were used in the FMB process. As shown in Figure 2, we investigated the curing characteristics of rubber compounds in each formulation using an RPA and determined the optimal cure time under conditions of 180°C for 20 minutes. The FMB temperature was adjusted according to manufacturer guidelines to match the cure temperature of the cross-linking agent. If the temperature is too low, there is insufficient activation energy for the reaction, while excessively high temperatures can cause scorch before adequate processing occurs.15 Based on prior experiments confirming that 180°C is sufficient for reactions across varying cross-linking systems with distinct molecular structures, this experiment also employed a temperature of 180°C.14 The increase in torque (viscosity) over time at this fixed temperature indicates the progression of cross-linking. Despite the same additive concentrations, the curing behavior differed significantly according to the cross-linker’s molecular shape. While the initial torque across formulations was similar, approximately 0.2 Nm, the maximum torque and TC90 values varied. TC90, defined as the time required for the material to achieve 90% of its total cure, is a critical parameter that reflects the curing rate under given test conditions. It provides insight into the progression of cross-linking by marking the point at which 90% of the overall torque increase, indicative of stiffness due to cross-linking, is reached. As a standardized measure of curing progress, TC90 ensures consistency across production batches and serves as a benchmark for evaluating the alignment of material properties during the scale-up process. By referencing TC90, manufacturers can assess material and process compatibility, ensuring stable cross-linked properties and reliable mechanical performance. Additionally, TC90 enables precise fine-tuning of material properties to meet specific application requirements, making it indispensable for process optimization and material design. That’s why TC90 was used as the basis for setting the MH value, ensuring that the curing process aligns with the desired material properties and application requirements, in this work. To calculate TC90 during RPA testing, the minimum torque (ML) and maximum torque (MH) are first identified, followed by calculating the 90% torque level using the equation TC90 = ML + 0.9 × (MH - ML); the time at which this torque value is reached represents the TC90 time.16
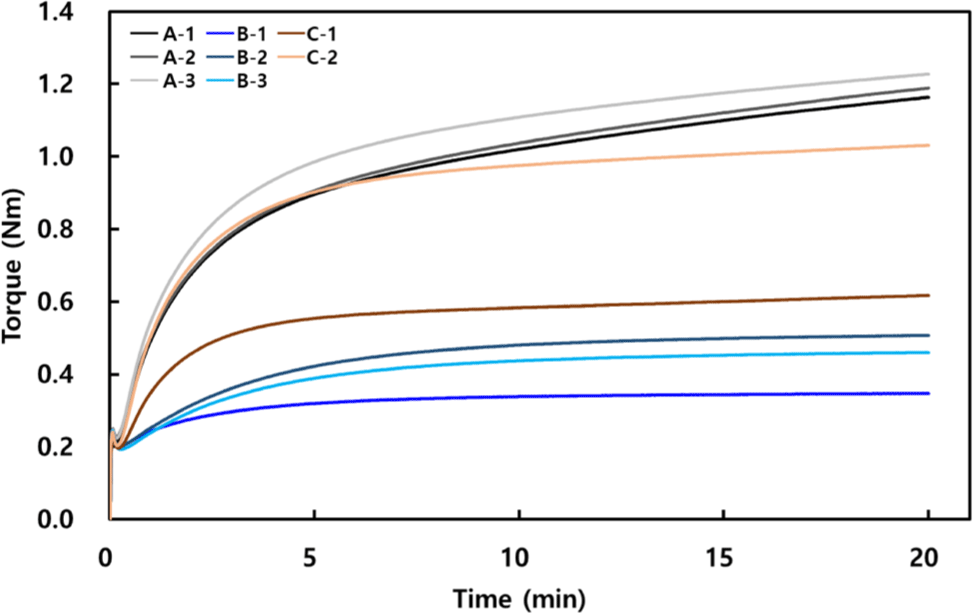
The difference between the initial minimum torque value and the maximum torque value over 20 minutes, expressed as ΔTorque=MH−ML, indicates the degree of cross-linking, with a higher ΔTorque signifying a greater degree of cross-linking. Aliphatic molecules exhibited a higher ΔTorque compared to other types of molecules. Because aliphatic molecules are flexible, small in volume, and linear, they move easily, which helps the reaction sites to meet and react. On the other hand, aromatic linkages are planar and bulky, making it hard for reaction sites to meet, so they have the lowest cross-linking. Alicyclic structures, which also have closed rings like aromatics, showed better reactivity than aromatics. In aromatics, electrons are spread across the ring, making a conjugated system. This makes the ring flatter, which blocks the molecules from approaching due to steric hindrance. Also, the electron cloud around the aromatic ring creates repulsion, adding more bulk. Meanwhile, alicyclic structures do not have conjugation. Even though they are a bit bulky, they have non-planar or 3D shapes, giving more flexibility than aromatic rings. So, for reactivity, alicyclic molecules are better than aromatic ones.17,18 In conclusion, comparing cross-linker groups, the aliphatic group had the highest ΔTorque because of its flexibility, good mobility, and low steric hindrance. The aromatic group, being rigid and bulky with high steric hindrance, had the lowest ΔTorque, and the alicyclic group was in between. To examine the cross-linking density in each group more closely, in the aliphatic group, the longer the chain length, the greater the ΔTorque, indicating that more cross-linking occurred. Although shorter chain lengths might be expected to favor more cross-linking due to higher molecular mobility, the cross-linker needs to interact with side chains between long, entangled chains on both ends. If the cross-linking molecule is too short, the polymer chains would need to be closer for the chemical reaction, increasing the physical stress on the chains. Thus, when the polymer chains are at an optimal distance, reactions occur more easily, and a longer molecular length of the cross-linker can lead to increased cross-linking. In the aromatic group, where cross-linking was the lowest, the ΔTorque of a single phenyl linkage (B-1) was the lowest, while cross-linking was higher with diphenyl molecules. Among diphenyl structures, B-2, which includes a flexible -CH2- linkage, showed higher cross-linking than -O-. Similarly, in the alicyclic group, the cross-linking density of C-2, which has cyclohexane groups connected by a central -CH2- structure, was higher than that of a single cyclohexane ring. A comparison between B-1 and C-1, as well as B-2 and C-2, which differ only in having either phenyl or cyclohexane groups, shows that cross-linking with cyclohexane was approximately 1.5 times higher than with phenyl rings (See Figure 2).
Since interchain cross-linking significantly impacts the mechanical properties of elastomers, the cross-linking behavior can be evaluated through tensile testing (See Figure 3). The aromatic group was excluded from tensile testing because its ΔTorque was too low to maintain a stable sample form. Comparing the aliphatic group, A-1 showed the lowest cross-linking degree but exhibited the highest tensile strength. Generally, a higher cross-linking density increases resistance to chain deformation under external forces. The high tensile strength in the formulation with the lowest cross-linking suggests an influence from the molecular structure. This can be attributed to the inductive effect19, where electrons are more effectively localized around the central bond in short chains, potentially increasing bond strength and, consequently, tensile strength. In contrast, A-3, with a longer chain length, has a more dispersed electron distribution, leading to weaker bonds that may break more easily under external forces, resulting in lower tensile strength. From this perspective, the alicyclic group likely has a bond strength between that of the aliphatic and aromatic groups due to its ring structure. The aromatic group, with strong electron sharing due to its conjugated structure, has the highest bond strength but was excluded from property testing due to insufficient cross-linking. In the alicyclic group, C-2 demonstrated significantly higher tensile strength than C-1, which is attributed to the cross-linking density difference between the two. Additionally, although C-2 showed a lower cross-linking density than the aliphatic group, it exhibited excellent tensile strength and elongation at break, indicating high mechanical performance despite lower cross-linking due to its unique molecular structure.
Further, specimens were thermally aged at 180°C for 24 hours to observe changes in mechanical properties (See Table 2 and Figure 4). Thermal degradation, where cross-links between chains break under high temperatures, results in decreased physical properties of the rubber as chains break.20,21 In the aliphatic group, both tensile strength and elongation at break showed similar changes before and after aging. Although cross-linking density increased with molecular chain length, the degree of property change was similar across all aliphatic samples. As cross-links break, the deterioration in properties is proportional; however, samples with higher cross-linking density maintained their properties to some extent despite breakage. The fact that A-1, with the lowest cross-linking density, showed a similar level of performance to other molecules can be concluded to be due to A-1’s higher bond strength, resulting in fewer broken cross-links. In the alicyclic group, a notable difference was observed between C-1 and C-2, as previously explained. C-1, with very low cross-linking, showed a marked decrease in properties when cross-links broke. In contrast, C-2 showed similar levels of property retention to the aliphatic group, which is likely due to the ring structure of the cross-linking molecule. Comparing the aliphatic and alicyclic groups under thermal aging, tensile strength decreased in both, but elongation at break increased in the alicyclic group. When cross-links are broken by heat, the ring structures in the alicyclic group act as side chains. These ring-shaped side chains interact with the main polymer chain, providing flexibility and distributing tensile forces, which can increase elongation.22 This distinction illustrates how aliphatic and alicyclic molecules can play differing roles in durability, flexibility, and physical properties.
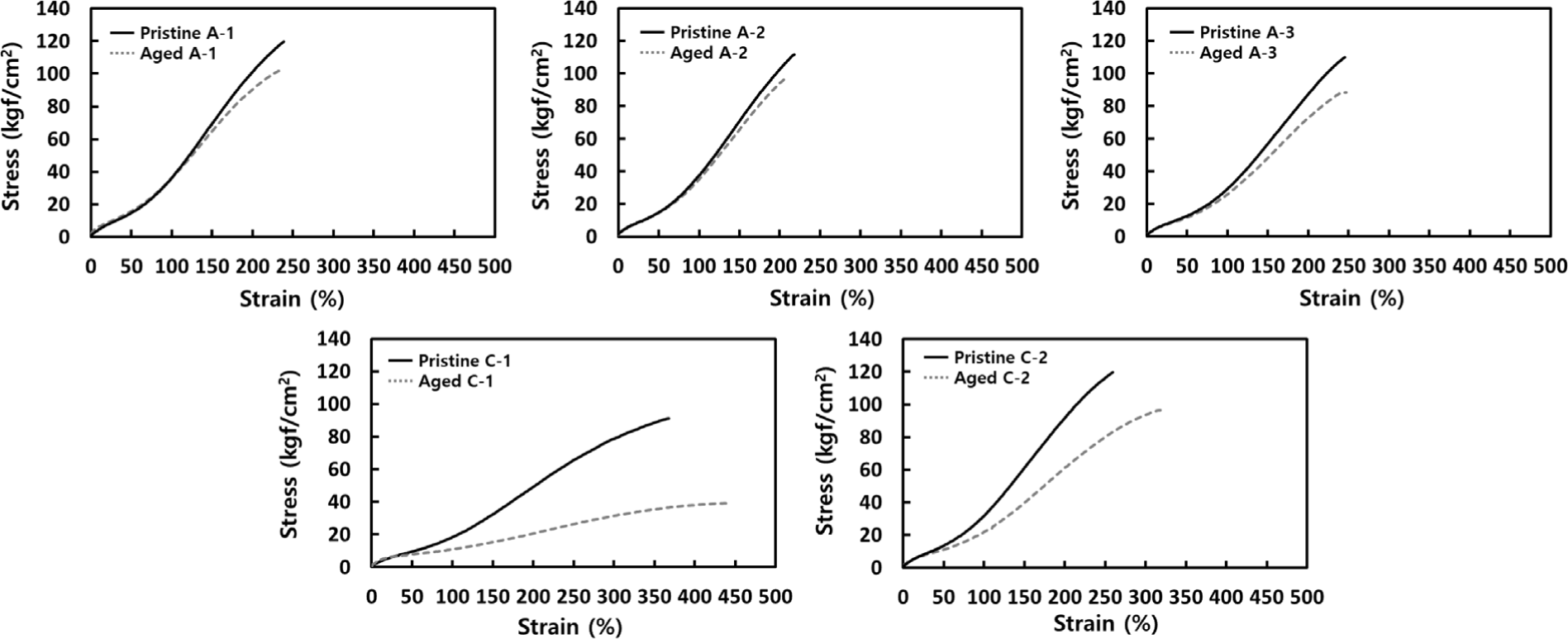
Conclusions
This study investigated the cross-linking behavior, mechanical properties, and thermal aging durability of ACM rubber with carboxylic acid cure sites, focusing on how different diamine structures affect these characteristics. Through a comparison of aliphatic, aromatic, and alicyclic linkages, we demonstrated that molecular structure plays a critical role in determining cross-link density and material properties. Our findings reveal that aliphatic molecules, with their flexible, low-bulk structures, exhibit the highest ΔTorque values, indicating superior cross-linking density. This high degree of cross-linking correlates with improved resistance to chain deformation, yet interestingly, the shortest aliphatic chains also demonstrated the highest tensile strength due to an inductive effect that enhances bond strength. In contrast, the bulkier, planar structure of aromatic linkages resulted in the lowest ΔTorque and hindered cross-link formation, leading to poor sample stability and thus excluding them from tensile testing. Alicyclic linkages, with their 3D ring structures, offered intermediate performance. Despite slightly lower cross-linking density compared to aliphatic linkages, alicyclic structures provided excellent tensile strength and elongation, particularly in 4,4’-Methylenebis(cyclohexylami ne) (C-2), which exhibited superior mechanical properties even at lower cross-linking levels. The thermal aging tests conducted at 180°C over 24 hours further highlighted the differences between the groups. Aliphatic linkages showed consistent performance across varying chain lengths, with higher cross-linking density samples retaining better properties post-aging. However, even 1,6-Hexanediamine (A-1), with its lower cross-linking density, demonstrated comparable durability due to the intrinsic bond strength of its short chain structure. Alicyclic samples, particularly 4,4’-Me thylenebis(cyclohexylamine)(C-2), retained substantial mechanical properties under thermal stress, with their ring structures contributing to property retention by acting as side chains that increase elongation under tensile forces.