Introduction
Seals include O-rings and gaskets, used to a wide range of industries and became more demanding. The reliability of seals was determined by the ability of the seals to restrict the flow of fluid in the service environment.1,2 Nowadays, seals are applied to more expensive engineered systems, like nuclear plants, ships, aerospace, etc. The selection process of seals would follow steps; 1) operating temperature, 2) chemical resistance, 3) mechanical properties requirements.3 In case of the application to expansive engineered system, wide range of operating temperature include extreme low temperature was demanded. While many people researched to operating characteristics and degradation mechanism at high temperature, low temperature sealing capability of seals was less studied. Low temperature sealing capability was usually investigated for developing the new improved seals. At normal operating temperatures, the molecules in O-rings would be free to rotate, and the individual chain segments would remain flexible. With decreasing temperature, the ability of molecules to rotate would be reduced. At glass transition temperature (Tg), the mobility of molecules and chain segments was minimized. At below glass transition temperature, the O-ring couldn’t perform sealing. Degradation of elastomers affected the mobility of the molecules and chain segments. And it induced to low temperature sealing capabilities of O-ring.4-6
Elastomers would start the degradation after it was made. Many variables affect the elastomer’s degradation, like temperature, light, ionizing radiation, humidity, fluids, etc. In these available, oxygen directly affects elastomer degradation. These effects were significantly interesting on analyzing the degradation mechanism and predicting the life-time. The many techniques used to analyze elastomer degradation and predict the life-time includes modulus profile, oxygen permeability, NMR, TGA, and DTA.7-9 In previous study, we studied life-time prediction of a CR O-ring using intermittent CSR (Compression stress relaxation) and TTS (Time temperature superposition) principle, and was introduced to previous paper.10
In this study, we investigated the thermal degradation effects on low temperature sealing capability. A large sized CR O-ring of 90.0 mm inner diameter and 7.0 mm cross-sectional diameter was used. We prepared aged CR O-rings and specimens by thermal aging test. We analyzed FT-IR and modulus profiles to observe the degradation mechanism. DMA and temperature retraction (TR) tests were used to observe the dynamic and visco-elastic properties. Finally, low temperature sealing capability was tested by low temperature sealing tester.
Experimental
CR O-rings and specimens were supplied from Sam Jung Industrial Co. (South Korea). They had 90.0 mm inner diameter and 7.0 mm cross-sectional diameter. CR S40V (DENKA, Japan) was used as the main matrix of CR O-rings. Table 1 shows the formulation of CR O-rings.
In previous study, we analyzed thermal degradation behavior of CR O-ring with intermittent CSR test. Table 2 shows the thermal aging time for preparing thermally aged CR O-rings, which aged to a controlled state of degradation at 120°C. Controlled state of degradation was 70%, 50%, and 10%RSF (Retained sealing force). Thermally aged CR O-rings prepared by aging each scheduled time in 120°C convection oven. A convection oven, AS-F0-05 model of A-Sung Tester Co. (South Korea), was used for the thermal aging test and preparation of thermally aged CR O-rings which was aged to controlled state of degradation.
Code | CR-I | CR-70 | CR-50 | CR-30 | CR-10 |
---|---|---|---|---|---|
%RSF (%) | 100 | 70 | 50 | 30 | 10 |
Aging time at 120°C (hrs) | 0 | 98 | 196 | 284 | 436 |
Figure 1 showed how the intermittent CSR test jig was designed and manufactured with consideration of how O-rings see service. The groove of the intermittent CSR jig was designed according to KS B 2799(O-ring housing design criteria; Korea Standard). Compression ratio was 15% when CR O-ring was fitted to intermittent CSR test jig. Intermittent CSR tests followed this procedure: 1) CR O-ring was fitted to the jig; 2) the assembled jig was placed to UTM (Universal test machine); 3) Sealing force of CR O-ring was measured by UTM. In intermittent CSR tests an Instron (U.S.A) UTM, 3345(Q3776) model, was used. The indenter was cylindrical of dimensions 25 mm×180 mm (diameter ×height). The test speed was 1.0 mm/min.
Modulus profile was measured as followed steps: 1) Cylinder type specimen (20 mm in diameter and 10 mm in thickness) was used. 2) After the thermal aging test, slice the specimen into five pieces with 2 mm thickness. 3) For each sliced piece, 10% compressive modulus was measured. The test speed was 1.0 mm/min
The JASCO 6100 FT-IR spectrophotometer was used to analysis chemical structure e change of CR O-ring by thermal aging. Resolution was 4 cm-1 and 32 scans with ATR mode.
Q800 (TA instruments, U.S.A.) was used to analysis the dynamic mechanical properties with a constant frequency of 1 Hz and the temperature range from -60°C to +80°C. The samples were analyzed by tensile mode with a static load of 1% and dynamic load was 0.5%. The sample size was 60 mm × 12 mm × 2.5 mm.
For observing the visco-elastic properties of each CR, temperature retraction test (TR test) was carried out according to ASTM D1329. EKT-TR100 (Ektron Tek Co., Ltd, U.S.A) was used to TR test at low temperature. TR test was carried out as followed steps. 1) Specimen strained for 50%, 2) cooled down below freezing, 3) measured recovery percentage with increasing temperature.
Lastly, low temperature sealing capabilities were observed by low temperature sealing tester. Figure 2 shows low temperature sealing tester, which was made by us. Low temperature sealing test was progressed by followed procedures: 1) Thermally aged CR O-ring was fitted to groove in sealing test jig (Part 1). 2) Pressurized gas was supplied to line 1. When there was no leak, gas passed to line 2. The gas pressure was 70 bar, and the flow rate was 40 lbs/hr. 3) The temperature of the test jig was continuously decreased. Decreasing velocity of temperature was 2°C/min. Test temperature could be controlled to -60°C. 4) When gas leak occurred, it was detected and recorded by the mass flow meter.
Results and Discussion
Sealing force of thermally aged CR O-rings was measured by intermittent SCR test. Figure 3 shows the measured sealing force and %RSF. With increasing thermal aging degradation, sealing force was decreased. In Table 3, we arranged the relationship between aging time, sealing force and %RSF of CR O-rings. Each CR O-ring showed suitable sealing force to control the state of degradation under ±1% deviation. We confirmed and successfully prepared thermally aged CR O-rings
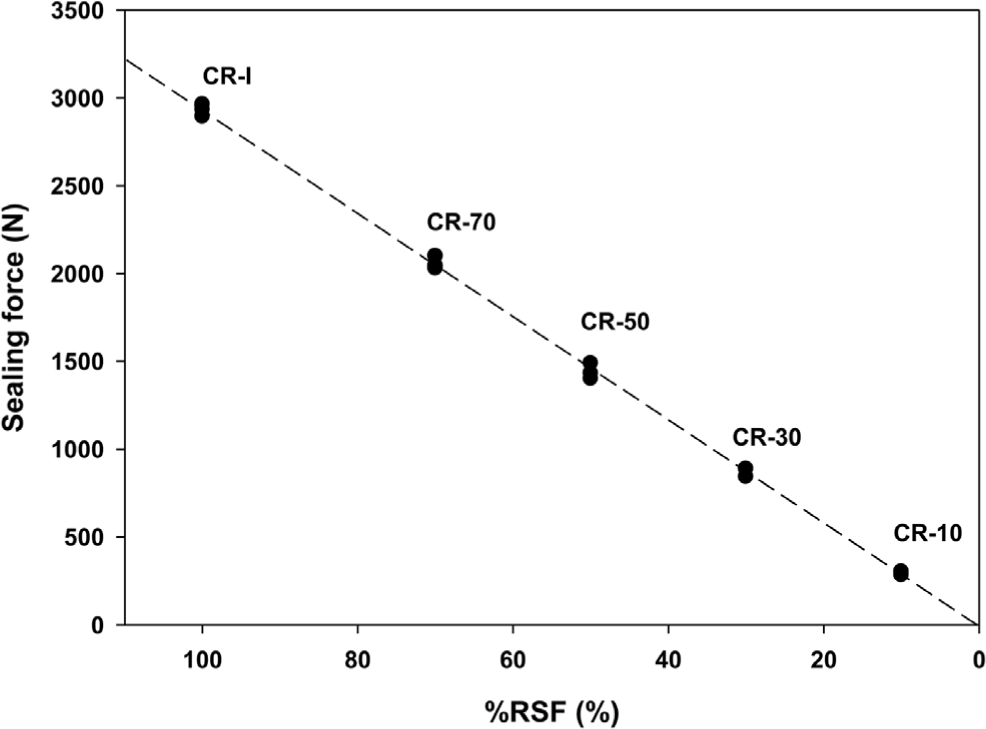
CR-I | CR-70 | CR-50 | CR-30 | CR-10 | |
---|---|---|---|---|---|
%RSF (%) | 100 | 70 | 50 | 30 | 10 |
Sealing force (N) | 2931 | 2058 | 1441 | 873 | 295 |
Real %RSF (%) | 100 | 70.2 | 49.1 | 29.8 | 10.1 |
Deviation (%) | 0 | +0.2 | -0.9 | -0.2 | +0.1 |
Figure 4 showed FT-IR analysis result. From IR spectrum of CR-I, unaged CR O-ring showed some of characteristic features expected for CR. Spectrum of CR-I shows C-Cl stretching and bending band at 825 cm-1, -CH2 band at 1450 cm-1, C=C band at 1660 cm-1, CH2 symmetric band at 2848 cm-1, CH2 asymmetric band at 2917 cm-1, and OH band at 3450 cm-1. In the spectrum of CR-10, hydroxyl (3450 cm-1) was broadly increased, and conjugated carbonyl (1660 cm-1) was increased.11 It was caused by oxidation of CR. In thermal aging, oxygen diffused to CR inside, and oxidation reaction occurred in CR backbone. Caused by this oxidation, sealing force was decreased with increasing thermal aging time.
For observing the interface change by degradation, we measured the modulus profile of CR-I, CR-50, and CR-10, as shown in Figure 5. The outside of the specimen, 0% and 100% positions showed the highest 10% compressive modulus. Whereas the inside of the specimen, 40~60% position showed the lowest 10% compressive modulus.12 Because of degradation of the CR was dependent on oxygen diffusion. Therefore, the level of oxygen diffusion differed according to the position, and the specimen surface showed a faster degradation rate than the center of the specimen. CR-I showed an 88 N deviation in modulus according to the position, but CR-10 showed a 196 N deviation. At the 40% and 60% positions, CR-I showed a 10% lower compressive modulus than CR-10 because CR-I had a lower degree of degradation than CR-10.
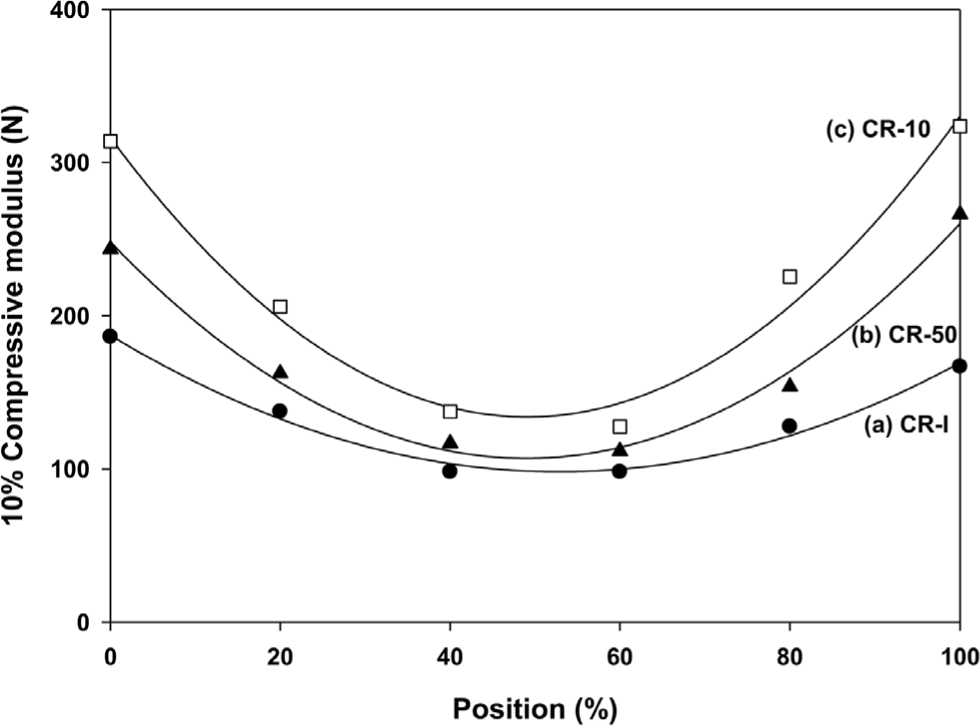
We analyzed DMA and results were shown in Figure 6. All the samples showed different Tg and tan δ. With increasing the degree of degradation, Tg was increased, and tan δ was decreased. By thermal degradation, oxidation occurred to the CR backbone. With increasing the degree of degradation by oxidation, mobility was decreased, and stiffness was increased.13 These influenced to change of tan δ and Tg.
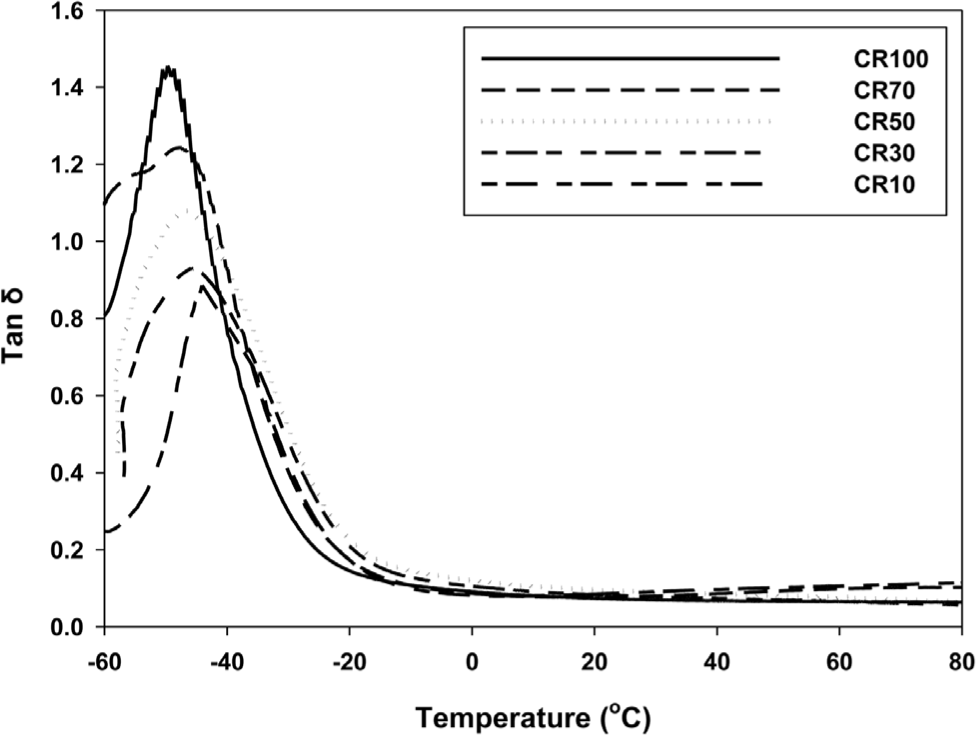
CR-I showed 49.7°C of Tg and 1.45 of tan δ. CR-10 showed -44.0°C of Tg and 0.89 of tan δ. Compared with CR-I, Tg of CR-10 was increased about 5.7°C of Tg and decreased 38.6% of tan δ.
The visco-elastic property was observed by the TR test, and the results are shown in Figure 7. TR10 of CR-I was -52.16°C, 2.4°C lower than Tg. TR10 increased with the degree of degradation. With increasing the degree of degradation, the mobility of CR decreased and showed a slow recovery rate at low temperatures. All specimens showed lower TR10 than Tg with 2.0~2.5°C difference. We confirmed that CR could still have mobility under Tg. Also, the TR70-TR10 values of all specimens were approximately 7.5°C. It seems that the degree of degradation affected mobility, but the recovery rate would be similar at low temperatures.
Sealing capability of CR O-rings was tested by low temperature sealing tester, and the results were shown in Figure 8. Gas leakage temperature increased with increasing the degree of degradation. It coincided with Tg and TR10 tendency. Mobility of CR directly affected to low temperature sealing capability. Gas leakage temperature was lower than TR10 about 5.2~6.4°C, and lower than Tg about 7.6~9.0°C. Under Tg and TR10, CR could still have visco-elastic property and performed as the seal. At the gas leakage temperature, CR changed to a glassy state, and a leak occurred. Gas leakage temperature and %RSF showed the following relationship: y= -5.43x-52.35.
According to Tg changing, the relationship with TR10 and gas leakage temperature is depicted in Figure 9. With the increase of the degree of degradation, mobility decreased but could still be maintained at a lower temperature than Tg. Tg and TR10 showed the following relationship: y = 1.01x-2.07. Also, Tg and gas leakage showed the following relationship: y=1.06x-7.25.
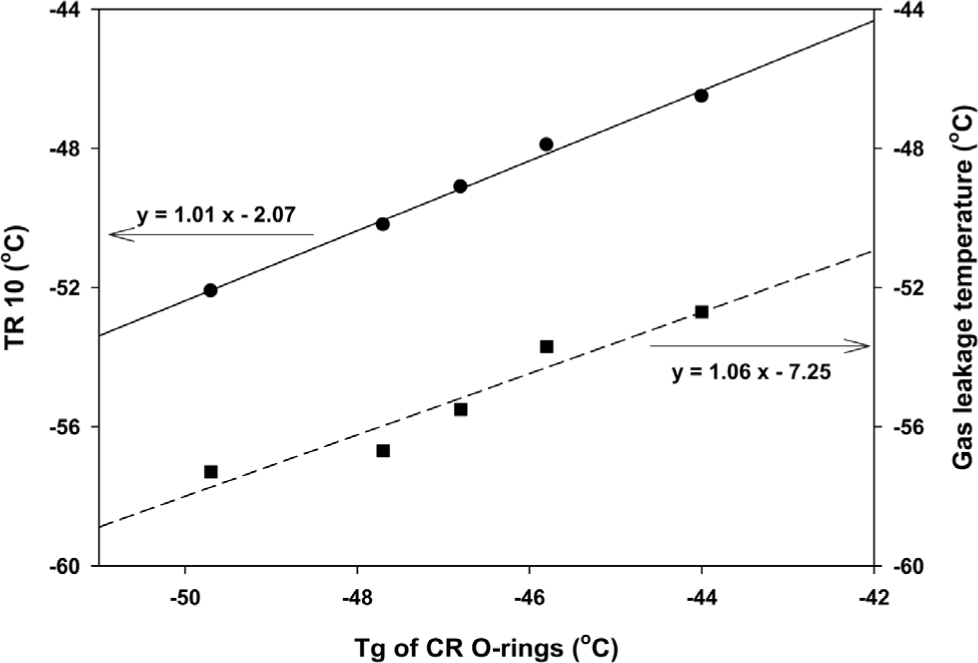
Conclusions
In this study, we observed the thermal degradation effect on low temperature sealing capability. We successfully prepared CR O-rings and specimens with controlled degree of degradation. In FT-IR spectroscopy, aged CR O-ring; CR-10, showed carboxyl group by oxidation. By oxidation of the CR backbone, the sealing force of aged CR O-rings decreased with increasing the degree of degradation. With increasing the degree of degradation, 10% compressive modulus had higher values at each relative position. It was caused by oxidation caused by oxygen diffusion, and the modulus of the inside position increased with the degree of degradation. As the degradation degree increased, Tg was increased while tan δ decreased. Because of oxidation degradation, mobility decreased, and stiffness increased. CR-10 showed -44.0°C of Tg and 0.89 of tan δ. With increasing the degree of degradation, the mobility of CR decreased and showed a slow recovery rate at low temperatures. All specimens showed lower TR10 than Tg with 2.0~2.5°C difference. Gas leakage temperature increases with the degree of degradation. It coincided with Tg and TR10 tendency. Gas leakage temperature was lower than TR10, about 5.2~6.4°C, and lower than Tg, about 7.6~9.0°C. Under Tg and TR10, CR could still have visco-elastic properties and perform as the seal. At the gas leakage temperature, CR changed to a glass state, and a leak occurred.