Introduction
Natural rubber latex, extracted from the milky white fluid found beneath the bark of the rubber tree (Hevea brasiliensis), is a complex substance synthesized by the tree in response to environmental stress.1,2 Using photosynthetic products, the tree generates isoprene derivatives, which are polymerized by enzymes and form particulate rubber.3 These particles, consisting of rubber surrounded by proteins and lipids, remain stably dispersed in water as a natural emulsion.4 Through human intervention, natural rubber latex is carefully harvested, purified, and vulcanized to transform it into a highly elastic and resilient material, making it indispensable across numerous industries. However, the increasing global demand for rubber and supply chain instabilities have driven the development of synthetic alternatives. Synthetic rubber not only resolves these supply challenges but also improves durability and performance in extreme environments, thereby promoting the application of rubber products and the advancement of related industries.5-7
Among the various methods developed to manufacture synthetic rubber, emulsion polymerization, which mimics the natural rubber production process, stands out for its numerous advantages.8-10 This approach ensures precise control over polymer viscosity and molecular weight, cost-efficient production, and enhanced overall manufacturing efficiency. Emulsion polymerization achieves these benefits by using dispersed rubber particles stabilized in a water-based system, much like natural latex. These particles provide an expanded surface area for polymerization, enabling consistent molecular structures while avoiding agglomeration, which ensures uniform material quality. Additionally, the use of water as a dispersion medium minimizes costs and reduces the reliance on organic solvents, making the process both economically and environmentally favorable. The emulsified state also simplifies handling and processing, allowing synthetic rubber production to meet the diverse and stringent demands of industries. Through this method, high-performance synthetic rubbers such as nitrile butadiene rubber (NBR), alkyl acrylate copolymer (ACM), styrene-butadiene rubber (SBR), and chloroprene rubber (CR) are efficiently produced, offering enhanced durability and specialized properties for extreme conditions.11
In this study, through the emulsion polymerization technique, we synthesized a matrix polymer that forms the backbone of ACM rubber, which offers exceptional heat resistance, oil resistance, and weatherability.12-14 The material’s properties were precisely tuned by modifying its polymer chain structure and cross-linking system to meet specific performance criteria. To achieve high-temperature resistance, we focused on developing ACM (HT-ACM) using carboxylic cure sites and amine-based cross-linking agents.13,14 HT-ACM is used as a material for components in extreme environments, requiring precise manufacturing techniques. Conventional emulsion polymerization techniques commonly use thermal initiators, and polymerization on fine particles generates significant heat requiring precise control for uniform quality. Effective heat regulation ensures uniform chain growth and prevents micelle size variations that could hinder the control of the polymer’s material properties.8,9 Poor temperature regulation can alter micelle sizes, ultimately making it challenging to achieve consistent polymer quality. To overcome this, we employed a redox radical reaction system to facilitate the reaction at lower temperatures, enabling the synthesis of the matrix polymer effectively.15,16 Using the polymer with a conventional monomer composition typical of ACM, we observed that immediate crosslinking occurred at high temperatures, reducing processability. This phenomenon is attributed to the high reactivity of carboxylic acid-amine cross-linking, which leads to rapid curing. This issue is often addressed by adding processing aids; however, in this study, we incorporated highly polar acrylonitrile into the polymer. The presence of these strongly polar functional groups delayed crosslinking, thereby improving processability, and resulted in enhanced physical properties compared to non-polar polymers.17 This modification not only improved processability but is also expected to enhance durability and chemical resistance. By tailoring the polymer with such highly polar functional groups, we provide an efficient molecular design strategy that enhances both processability and material properties. These advancements are particularly beneficial for industries requiring durability and high functionality in extreme environments, offering foundational strategies for future polymer development.
Experimental
In the emulsion polymerization process, we used ethyl acrylate (SAMCHUN CHEMICALS, Korea), butyl acrylate (SAMCHUN CHEMICALS, Korea), 2-methoxylethyl acrylate (TCI chemical, Japan), 2-ethylhexyl acrylate (SAMCHUN CHEMICALS, Korea), mono-butyl maleate (KUROGANE KASEI, Japan), acrylonitrile (SAMCHUN CHEMICALS, Korea) as monomers. Additives for polymerization included co-surfactants (a mixture of SR-10 and ER-10, Adeka, Japan), a thermal initiator (potassium persulfate, SAMCHUN CHEMICALS, Korea) and a reducing agent (ascorbic acid, SAMCHUN CHEMICALS, Korea).
In compounding process, the synthesized polymer was mixed with various additives, including carbon black (N660, Orion Engineered Carbons, Korea), a plasticizer (PH-100, LG Chem ltd., Korea), a slip agent (MISTRON VAPOR, Imerys, France), a processing agent (Posgen #22, Hwasung Chemical ltd., Korea) and an antioxidant (anox405, Addivant UK ltd., United kingdom). For cross-linking, an amine-based cross-linker (CLP-5050, Unimatec, Japan) and an accelerator (ACT-55, Saficalcan ltd, United kingdom) were used.
In the emulsion polymerization process, deionized (DI) water, referred to as blending water, was mixed with a surfactant and stirred for 30 min to prepare the solution. The total blending water was divided into three portions. First, 20% of the blending water was used for pre-emulsification, where monomers were added and stirred at over 500 rpm for 2 hrs to create the emulsion feed. Separately, 50% of the blending water was set aside in a new reactor for later use. The remaining 30% was used to dissolve acrylic acid (AA), forming a separate solution. Subsequently, the pre-emulsified monomer solution and the AA solution were gradually introduced into the reactor containing the 50% blending water. The reactor atmosphere was purged with nitrogen to remove oxygen, and the temperature was maintained at 30-38°C with continuous stirring at 200 rpm. The prepared emulsion feed was carefully added dropwise over 2 hrs to ensure controlled polymerization. Upon completion of the reaction, the resulting ACM latex was filtered through a 100- mesh screen and washed thoroughly to obtain high-purity latex.
In the carbon black masterbatch (CMB) compounding step, the compounds were prepared using a banbury mixer at 135°C for 4 min, followed by additional mixing on a two-roll mill for 3 min. For the final masterbatch (FMB), a kneader mixer was used to blend the crosslinking agent and accelerator at 110°C for 3 min, with further mixing completed on a two- roll mill for 2 min. To obtain vulcanizates specimens, FMB was vulcanized in a hot press at 160°C for 30 min and post- cured in a dry oven at 180°C for 1 hr.
The synthesized polymers were characterized using FT-IR (Agilent, USA). Curing behavior information was collected by using a rheometer at 190°C for 6min. Mechanical properties of the specimens were evaluated using universal testing machine (UTM, Instron, USA) according to KS M 6518.
Results and Discussion
The fundamental physical properties of ACM rubber can be tailored by designing the polymer matrix, which is why monomer composition technology is critical in constructing this foundational structure and additional reinforcement is achieved during the rubber manufacturing process, particularly in the master batch stage, where additives such as fillers are incorporated. Approximately 95% of the polymer is composed of monomers such as ethyl acrylate, butyl acrylate, and 2-ethylhexyl acrylate, which determine the fundamental behavior of the polymer. The remaining 5% is designed to include specific monomers that form cross- linking points. Depending on the curing method, differences in reactivity, cross-link density, and bond strength arise, enabling the development of products into various grades, such as those with enhanced heat resistance.13,14,18 Herein, the aim was to develop rubber hoses for internal combustion engines requiring excellent heat resistance. To address these needs, 5% of the monomer composition consists of a carboxyl functional group-containing monomer, which acts as the curing site for carboxyl-amine cross-linking, known for achieving the highest heat resistance grade.13,14 The remaining polymer backbone was formulated using butyl acrylate (BA), 2-methoxyethyl acrylate (MEA), ethyl acrylate (EA), and 2-ethylhexyl acrylate (EHA). EA, with its short alkyl chain, significantly increases polymer flexibility and reduces chemical hindrance, allowing for the formation of a denser cross-linked network. This structure provides excellent resistance to polar substances. BA, featuring a longer alkyl chain, enhances flexibility further and contributes to improved cold resistance. MEA enhances oil and chemical resistance due to its polar structure, while EHA, with its branched structure, significantly improves low-temperature performance. These monomers constitute the typical ACM rubber matrix polymer composition. These monomers form the typical components of ACM polymers.19 In this study, we additionally introduced acrylonitrile (ACN) to enhance the processability of ACM rubber. This polar functional group-containing monomer improves chemical resistance and enhances intermolecular interactions, leading to superior mechanical strength, heat resistance, and gas barrier properties. Acrylonitrile is widely used in industries such as rubber (e.g., Nitrile Butadiene Rubber), polymers (e.g., Acrylonitrile-Butadiene-Styrene copolymer, Styrene- Acrylonitrile copolymer, Polyacrylonitrile),20 and liquid crystals (e.g., cyanobiphenyl series)21 in the display industry. It is anticipated to contribute significantly to the durability assessments of ACM rubber in future studies (See Figure 1). The polymerization of the ACM rubber matrix, composed of these monomers as building blocks, was carried out through the emulsion polymerization method. For emulsification, water was used as the dispersion medium, and surfactants were utilized to induce the formation of micelle structures. A combination of anionic and nonionic surfactants was used to stabilize the micelle structure, as the polymer building blocks consisted of monomers with varying polarities.22 To address this polarity difference, the nonionic surfactant, which aids in stabilizing polar monomers (e.g., ACN, MA) within the micelle, was added at a ratio 20% higher than the anionic surfactant, which plays a role in preventing aggregation of nonpolar monomers (e.g., EHA, MEA) through electrostatic repulsion. (See Figure 1) Notably, nonionic surfactants are less sensitive to changes in pH and temperature compared to anionic surfactants, making them highly suitable and widely utilized for large-scale latex production.
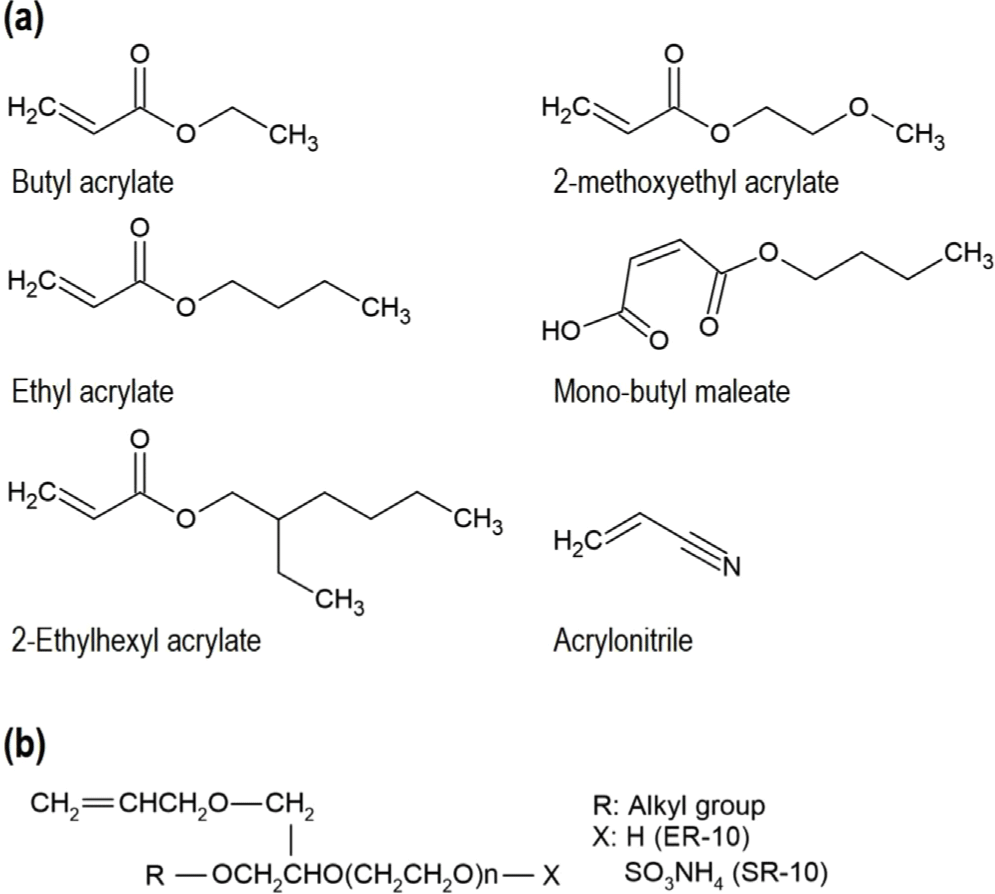
(See Figure 2) Initially, water and co-surfactant were mixed, followed by the addition of monomers and high-speed stirring to produce an emulsion feed with a specific size. Through high-speed stirring, physical collisions between monomers and micelles occur frequently, facilitating the appropriate positioning of monomers with varying polarities. These collisions direct nonpolar monomers into the hydrophobic core of the micelle or separate polar monomers from water to bind them to the micelle surface, which is referred to as the collision-induced micelle stabilization mechanism.23 The polymerization reaction was initiated using a redox radical initiation method, which employs an oxidizing agent (potassium persulfate, KPS) and a reducing agent (ascorbic acid, AA). This method enables the generation of a large quantity of active radicals at relatively low temperatures, making it easier to control the reaction heat. The reaction mechanism is as follows:24
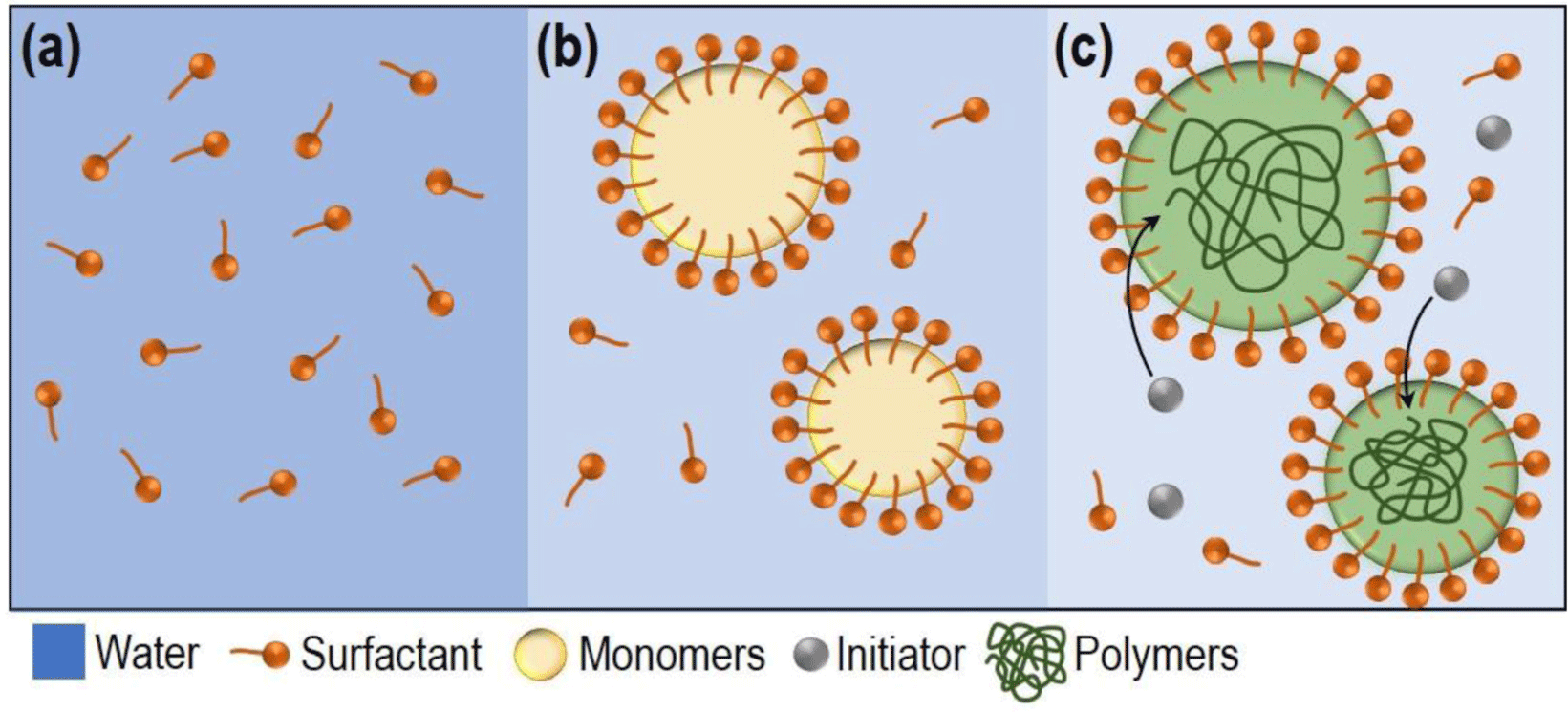
KPS dissociates in water to form persulfate ions, which require an activation temperature of approximately 60°C to independently generate sulfate radicals (SO4o−) (Eq. 1). However, increasing the temperature of the process water to achieve this can lead to excessive heat generation due to the reaction at the large particle surface area, potentially raising the temperature further and causing water evaporation, leading to significant process issues. When AA is used as a reducing agent, it reacts with the dissociated KPS, transferring electrons to generate active radicals. This approach lowers the activation temperature for radical activity to as low as 20-40°C, thereby creating a thermally stable environment. As shown in Eq. (2), the active radical generation through the redox reaction produces both sulfate radicals (SO4o−) derived from KPS and AA radicals (AAo), resulting in a rapid reaction rate and immediate initiation of the polymerization process. The composition and details of the chemicals used for polymer synthesis in each recipe are listed in Table 1. A comparison of Recipes A to C shows that the only difference is the concentration of ACN. Chemical analysis of the latex polymers (A–C) using FT-IR confirmed that, despite ACN’s highly polar structure and high solubility in water, the polymer backbone was successfully formed as designed, as explained by the collision-induced micelle stabilization mechanism. As shown in Figure 3, the CN functional group of ACN is known to exhibit an FT-IR absorption band around 2200 cm−1.25 In Samples B and C, where ACN was incorporated into the polymer chains, a characteristic peak appeared at 2228 cm−1, further confirming its successful integration into the polymer structure. Although nuclear magnetic resonance (NMR) spectroscopy provides precise characterization, the synthesized polymer exhibited extremely dense crosslinking and excellent chemical resistance, making it insoluble in common organic solvents such as tetrahydrofuran, chloroform, dichloromethane, and acetonitrile, thus preventing NMR analysis. Similarly, gel permeation chromatography (GPC), which requires the polymer to be in a dissolved state for molecular weight analysis, could not be conducted for the same reason. Therefore, FT-IR was used to confirm that acrylonitrile successfully penetrated the micelles from the water solution and participated in polymerization via the collision-induced micelle stabilization mechanism.
To produce the final rubber product using the manufactured ACM polymer as the matrix, the process involves the CMB stage for additive mixing and the FMB stage for mixing crosslinking agents, as shown in Table 2. The mixture is then placed into a mold and shaped under high temperature. Optimizing temperature and time in the molding process is essential to achieve the desired properties. To evaluate whether the formulation exhibits the desired crosslinking behavior, the FMB material is analyzed using a rheometer to pre-assess performance and refine formulation conditions. FMB crosslinking behavior is typically evaluated using a rheometer at the actual product crosslinking temperature (as detailed in the experimental section). However, in this study, rheometer testing was conducted under harsher conditions to specifically investigate scorch behavior. Scorch occurs when rubber undergoes premature vulcanization due to rapid crosslinking early in the curing process, leading to unstable properties and poor processability. To determine the presence of scorch in the formulation recipe, the recipes are screened under harsh conditions. Products that pass this stage undergo milder crosslinking, followed by extended post-curing at high temperatures to complete curing. This method is widely used in the industry for the rapid evaluation and screening of multiple formulations using accelerated curing tests. When observing the curing behavior of each FMB prepared using A~C polymers with a rheometer, recipe A exhibited a scorch phenomenon. Typically, the torque behavior shows a decrease in torque after sample loading due to the reduction in material viscosity caused by temperature, followed by an increase in torque as curing progresses after reaching the minimum point.13,14 In the case of recipe A, the viscosity gradually increased after sample loading. This phenomenon occurs because the carboxylic groups, which act as curing sites in the polymer, react rapidly with the amine crosslinker. To address such scorch phenomena, adjustments are commonly made to the formulation by modifying fillers, additives, or crosslinkers. However, since the crosslinker had already been added in a minimal amount (less than 1 wt%) and the filler content had been maximized within the formulation, further adjustments to these two components were limited. An alternative approach involves adding a phenol-based retarder, but this introduces eco-toxicity concerns. Therefore, to achieve typical curing behavior without additional formulation modifications, we incorporated highly polar ACN into the polymer. The high polarity slightly suppressed the reactivity and diffusion of the crosslinker, delaying the initial reaction rate.17 As a result, samples B and C exhibited the typical curing behavior described earlier (See Figure 4). In the rheometer results, the difference between the initial minimum torque value (ML) and the maximum torque value (MH), expressed as ΔTorque = MH ML, indicates the degree of cross-linking, which directly reflects the mechanical properties. A larger ΔTorque corresponds to a higher degree of cross-linking, and the higher the degree of cross-linking, the better the mechanical properties tend to be.13,14 When comparing the ΔTorque values of samples A, B, and C (see Table 3), the order is A < B < C. Similarly, in the tensile test results, sample C showed the highest elongation at break and maximum tensile strength. By incorporating polar functional groups into the polymer, the processability (curing behavior) was improved, resulting in ACM rubber with enhanced mechanical properties (See Figure 5). Although this study did not include additional heat aging behavior analysis, it is anticipated to perform well in this regard as well, based on established results from other rubber fields (such as NBR), where the introduction of ACN improved basic properties and durability compared to BR. Further evaluations related to this are planned.
Recipe code | A | B | C |
---|---|---|---|
MH | 8.90 | 5.73 | 6.27 |
ML | 5.48 | 2.07 | 2.48 |
ΔTorque (MH-ML) | 3.42 | 3.66 | 3.79 |
Conclusions
In this study, we successfully developed an HT-ACM polymer via emulsion polymerization using a redox radical initiation system. By designing the polymer network to include highly polar functional groups, such as acrylonitrile, we achieved significant improvements in processability and mechanical properties compared to conventional ACM polymers. The introduction of polar functional groups played a key role in balancing crosslinking reactivity, delaying early curing, and enabling controlled network formation. This modification led to higher ΔTorque values, indicating improved crosslink density and enhanced mechanical performance. Although this study did not include durability testing, previous findings in related fields suggest that the inclusion of polar functional groups can also improve long- term stability, particularly in heat and chemical resistance. These results lay the groundwork for developing HT-ACM, suitable for use in demanding environments requiring high performance and reliability. Future work will focus on evaluating the durability of these materials under thermal and mechanical stress to further validate their suitability for advanced automotive and industrial applications.