Introduction
Blending various polymers is widely adopted as an important approach to improve the properties of materials and expand their application range. Among them, the combination of polypropylene (PP) and low-density polyethylene (LDPE) has garnered significant attention due to their complementary characteristics. The PP has high stiffness, good chemical resistance and excellent processability, while the LDPE offers excellent flexibility and impact resistance. This combination of properties has the potential to create materials with balanced mechanical, thermal and barrier properties suitable for a variety of industrial applications.
However, blends of PP and LDPE pose great challenges in achieving homogeneous and stable blending due to their inherent incompatibility and different melting points.1 To solve this problem, we aim to improve the kneading effect in the melt blending process. The kneading effect plays an important role in improving the dispersion of the polymer, promoting interfacial adhesion, and enhancing the overall homogeneity of the blend.2 The improved kneading effect not only enhances the mechanical properties of the blend, but also reduces phase separation, which directly affects the thermal stability and barrier properties of the blend. Additionally, uniform distribution of additives, fillers and compatibilizers helps tailor the properties of the blend to suit the application.
In this study, optimal conditions for improving the kneading effect of the PP/LDPE blend were set through a simulation program.3 In particular, the change in kneading effect according to the screw profile was analyzed and the kneading effect was analyzed by adjusting the screw profile, including the number and angle of kneading elements. This modification improved shear distribution and residence time, leading to better dispersion of the minor phase and enhanced interfacial adhesion.4 In addition, a simulation program was used to optimize variables such as temperature, pressure, screw rotation speed, and feeding rate. These optimized conditions were then applied to actual experiments to investigate the uniform dispersion of the blend and the strengthening of the phase interface.3,5 There was a rheological difference indicating that the dispersion of PP/LDPE had better dispersion via kneading effect. This can be used to manufacture automobile parts to achieve weight reduction and fuel efficiency simultaneously. Additionally, The excellent dispersibility, excellent durability, and eco-friendly characteristics were achieved through process optimization by adjusting the screw configuration rather than relying on chemical compatibilizers. This environmentally friendly approach enhanced phase dispersion and interfacial adhesion while maintaining mechanical performance, making it applicable to the development of sustainable packaging materials.
Experimental
The polymer LDPE 737 (low-density polyethylene(LDPE), 147,500 g/mol, PDI = 10.46) was purchased from Hanwha Solution, Korea with a melt flow rate (MFR) of 2.2 g/10 min (190°C, 2.16 kg by ASTM D1238). J-150 PP (polyprolylene, 288,610 g/mol, PDI = 5.21) was purchased from Lotte chemical, Korea with a melt flow rate (MFR) of 10 g/10 min (230°C, 2.16 kg by ASTM D1238).
Information on the used extruder was set through a simulation program (Ludovic v7.0.7, France). The screw profile of the twin-screw extruder (BA-11, Bautek), the world’s smallest modular intermeshing coating twin-screw extruder with an L/D ratio of 40, was directly measured. Additionally, other basic specifications were obtained from the information provided by Bautek. The extruder used is the world’s smallest modular intermeshing coating twin screw extruder with L/D=40. In the Ludovic program, the diameter/centerline mode was set to implement the screw of the BA-11 extruder. The barrel diameter was specified as 11 mm, the barrel centerline as 9 mm, and the screw/barrel leakage as 0.1 mm. The total length of the screw profile was set to 500 mm. The screw profile consists of five 100 mm barrels, forward conveying blocks of 17 mm and 11 mm, a reverse conveying block of 11 mm, and a forward kneading block of 2.75 mm.
In the product part, the thermal characteristics and viscosity of LDPE and PP were measured, and information was entered. Heat capacity (J/kg·°C), density (kg/m3), thermal conductivity (W/m·K), melting temperature (°C), and melting enthalpy (KJ/kg) are determined by DSC (DSC 204 F1 Phoenix, NETZSCH), He gas pycnometer (AccuPyc II 1340, Micromeritics), and Laser Flash Analysis (LFA 467, NETZSCH). In addition, the viscosity of PP and LDPE was measured by shear rate/viscosity at three temperatures above the melting temperature (Tm) of each material using a rotational rheometer (MCR 102e, Anton Paar).
In the process part, the user must enter variables that directly manipulate the conditions, so that the values were set according to the specifications of the extruder being used. The temperatures of the barrels were set at 110°C, 130°C, 160°C, 190°C, and 210°C, and the output temperature was set at 210°C.4 The screw rotation speed was set to 300 rpm, and the feeding rate was adjusted to 0.18 kg/h.3,5,7
Before the twin screw extruder process, PP and LDPE polymers were dried in a vacuum oven at 80°C for 24 hours. The PP and LDPE polymers mixed in a 5:5 volume ratio was placed in the matrix hopper, and the temperature of each region of the barrels was set to 110°C, 130°C, 160°C, 190°C, and 210°C. The temperature of barrel 1 was set low to prevent PP and LDPE polymers from sticking to the hopper and blocking the inlet. In addition, the temperature of barrel 3 was set higher than the Tm of the two materials to ensure that both polymers melted and flowed well toward the die without being affected by the torque surge caused by the kneading block and reverse conveying block. The temperatures of barrel 4 and barrel 5 were gradually raised to allow the materials to move smoothly towards the die, avoiding blockage from the rapidly increased torque due to long-term blending by the kneading zone and reverse conveying block.6 The extruded material that came out of the die was immediately water-cooled in a bath and then fragmented using a pelletizer. When using a screw that can quickly increase torque, such as a new screw consisting of a reverse conveying block, it is important to frequently monitor the screw torque value displayed on the extruder during the extrusion process. If the screw torque is too high, problems may occur in the process, such as the screw stopping rotating.
Results and Discussion
To understand the role of blocks in a screw, we created three types of screws (CB is a screw composed of only one type of conveying block, KB is a screw composed of one type of conveying block and two types of kneading blocks, and Original is a screw composed of two types of conveying blocks and one type of kneading block.) using the Ludovic program. We performed extrusion simulations with all process conditions except for the screw profile set identically. As a result of comparing the Specific Mechanical Energy (SME, represents the mechanical energy input per unit mass), Residence Time Distribution (RTD, indicates the distribution of residence time within the extruder, torque, temperature, and cumulated strain of the three screws, all the values were highest in the KB screw set, which consists of two types of kneading blocks and one type of forward conveying block. The CB screw consisting of only forward conveying blocks showed the lowest results. This indicates that the kneading blocks in the KB screw and the reverse conveying block in the original screw significantly contribute to the degree of kneading.8 Therefore, we studied the effective use of kneading blocks and reverse conveying blocks to design screws with excellent kneading effects (Figures 1, 2).
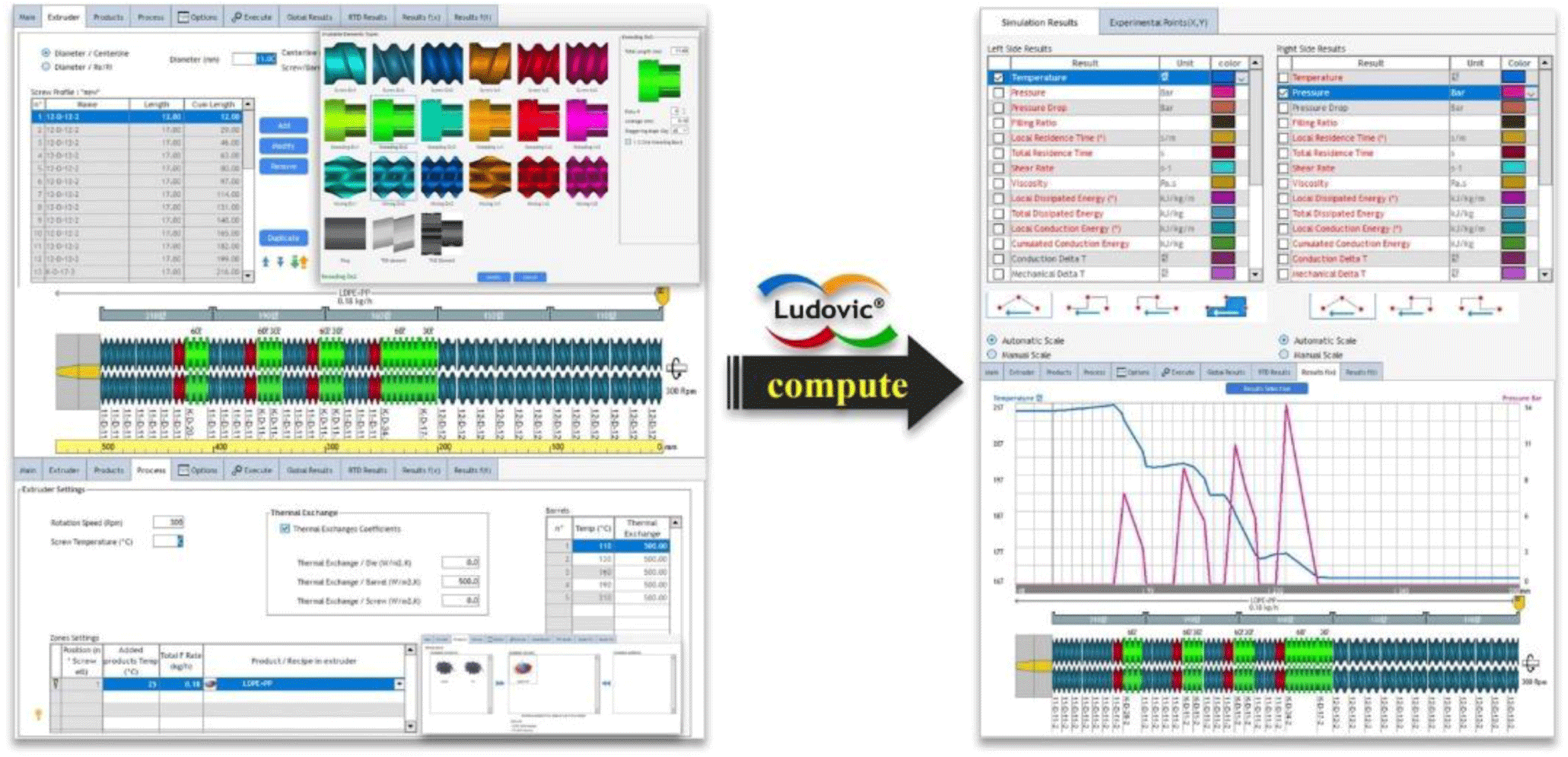
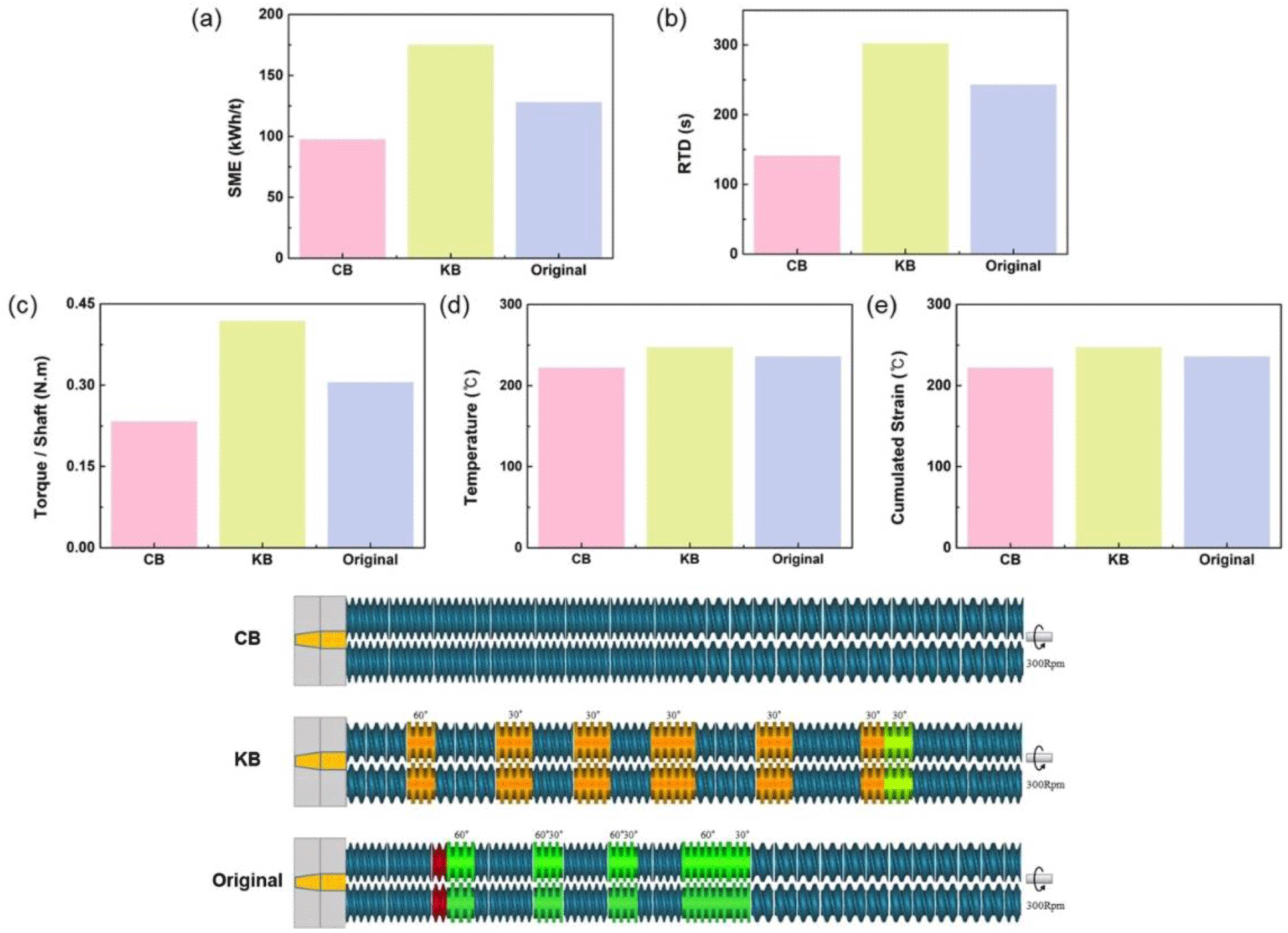
Based on the role of the blocks analyzed with the Ludovic program, a new screw with improved kneading effect compared to the original screw was designed. To further improve the kneading effect compared to the original screw, the three forward conveying blocks located right after the kneading block zone (green zone) of the original screw were replaced with kneading blocks or reverse conveying blocks at 30°, 60°, and 90° angles, respectively, in the Ludovic simulation. Additionally, simulations were performed for all screw profiles created by replacing them with a reverse conveying block. In this experiment, to increase the kneading effect of PP/LDPE blends, the screw profile with the greatest increase in SME value relative to the RTD was investigated through simulation. As a result, a new screw with a reverse conveying block located right after the kneading zone was selected. In the actual process, a total of three forward conveying blocks located immediately after the kneading zones starting from barrel 3 were replaced with reverse conveying blocks.8,9,10,11 In the process of designing the new screw, not only the location of adding blocks but also the length (number of blocks in the actual process) was considered important (Figure 3).
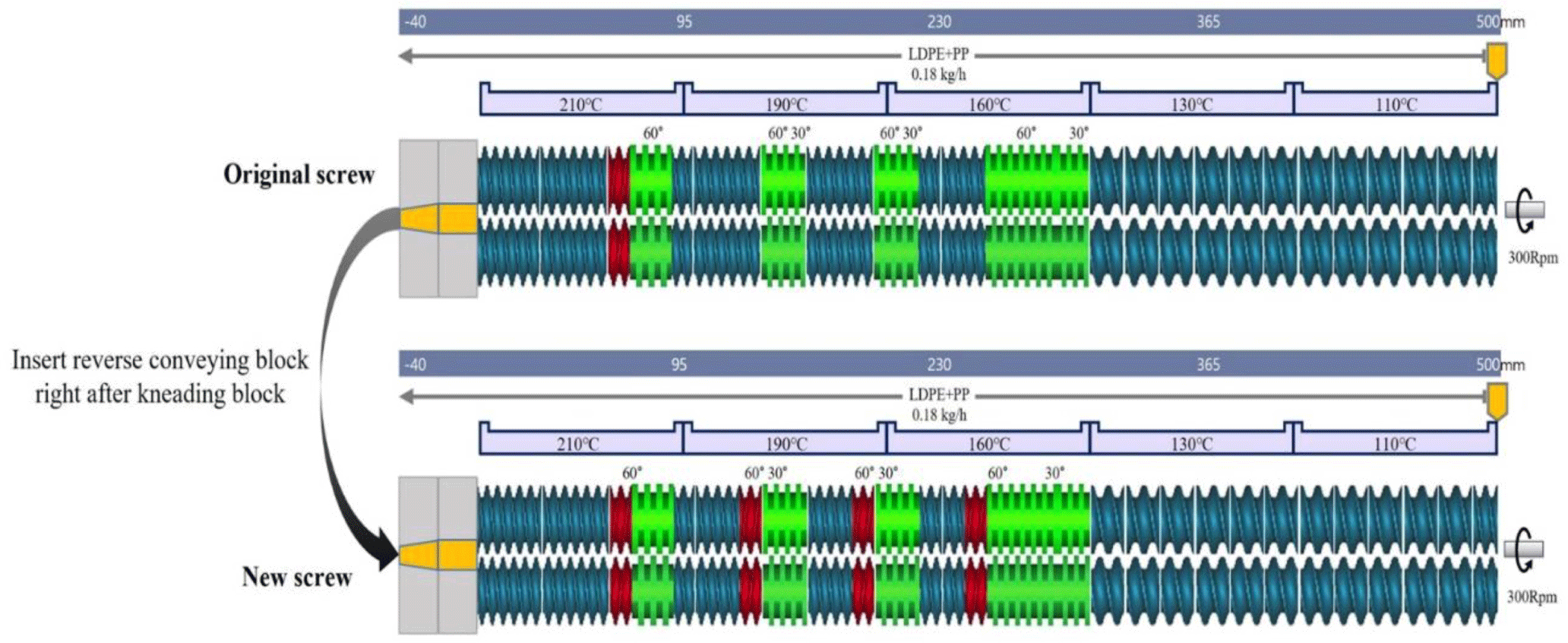
The blend extruded from each screw set was pelletized, treated with liquid nitrogen, and the surface was observed through FE-SEM (CLARA, TESCAN). In Figure 4, it can be observed that the blending of the PP/LDPE blend was more uniform in the new screw than in the original screw. This is confirmed by the decrease in the matrix spacing from 2312.31 nm to 1699.04 nm in the pelletized sample (Figure 4(a), (c)).6 The matrix spacing refers to the average distance between dispersed PP and LDPE phases, indicating the degree of phase distribution. A reduced matrix spacing suggests that the two polymers are more finely and uniformly dispersed, leading to improved blend homogeneity. As a result of observing the surface of the sample destroyed by liquid nitrogen treatment, the improved kneading effect of the blends extruded from the new screw was observed more clearly than in the original screw (Figure 4(b), (d)). In the case of PP/LDPE blends extruded from the new screw, it appears that a different matrix is embedded in the matrix, whereas in the case of PP/LDPE blends extruded from the original screw, the two matrices were not mixed well and appeared to be pushed out as is. This means that the kneading effect has been further improved in blends extruded from the new screw and shows that the kneading effect changes depending on the screw profile.
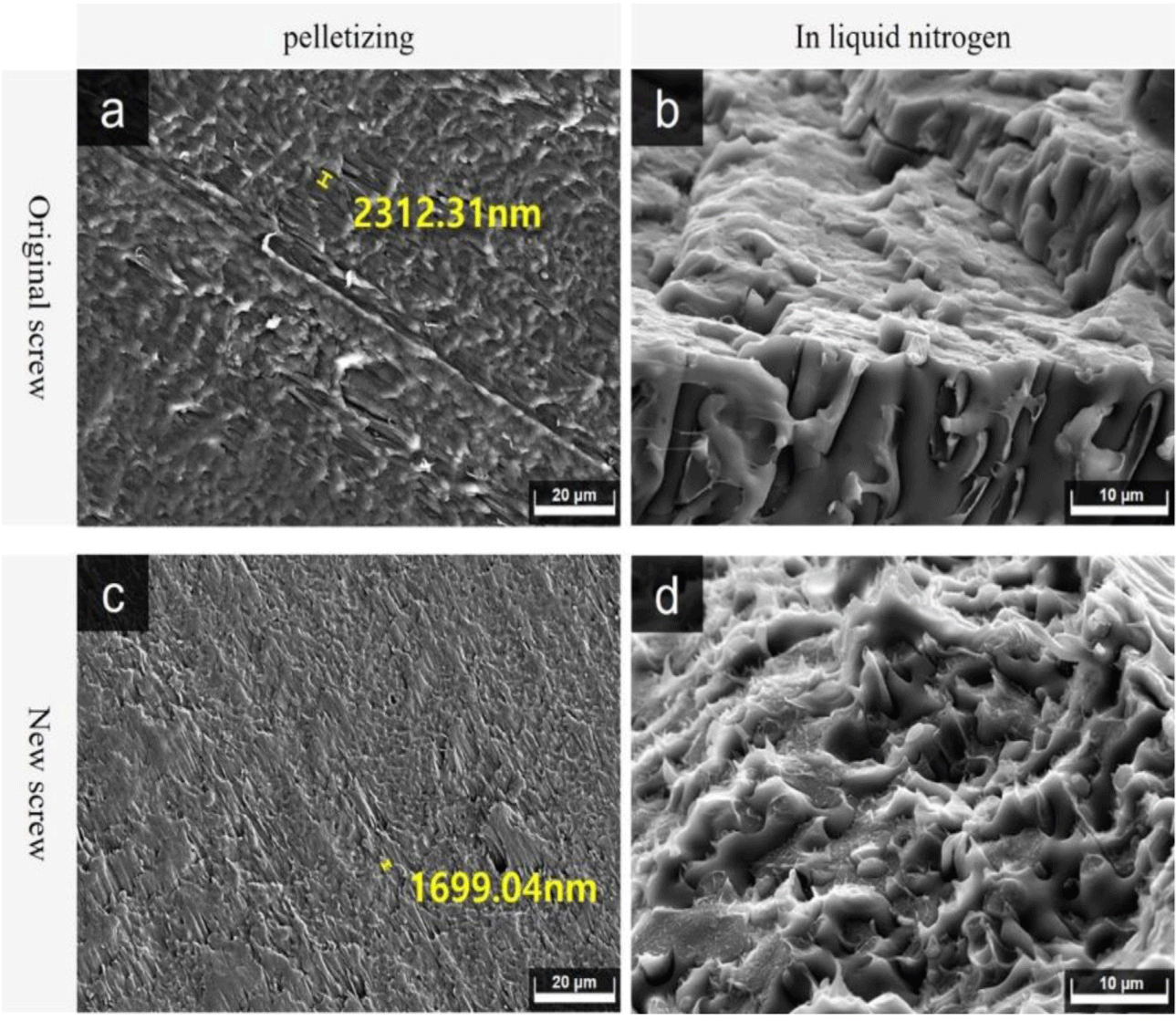
To determine whether the change in screw profile affects the rheological properties during blending, the rheological properties were measured using a rheometer. Figure 5 shows the rheometer measurement results of PP/LDPE blends extruded through the original screw and new screw. Measurements were made using a Rotational Rheometer (MCR 102e, Anton Paar), and when measuring strain sweep, the angular frequency was set to 100 rad/s (constant), and the shear strain range was set to 0.01~1000%. Based on the strain sweep measurement results, the frequency sweep was measured by adjusting the angular frequency to 100~0.1 rad/s and the shear strain was set to 0.1%. Viscosity measurement was performed by setting the shear strain to 0.001~100 1/s and at a temperature of 250°C with a gap of 1.0 mm. In Figure 5(a), it was observed that the material experienced more shear as it was extruded from the new screw with the reverse conveying block added, and the viscosity decreased from 782.1 Pa·s to 643.4 Pa·s. The results of the storage modulus (G’) and loss modulus (G’’) in Figure 5(c), (d), measured by frequency sweep, also decreased further because the mechanical properties changed due to shear and thermal degradation as it was extruded from the new screw. The complex viscosity was measured to be higher for the blends extruded from the original screw than the blends extruded from the new screw, with 8.67×105 mPa·s and 7.23×105 mPa·s, respectively, due to the effect of the compatibility effect (Figure 5(e)). Interactions between phases favor good interfacial adhesion and enable long chain entanglements that can withstand higher frequencies, thereby increasing complex viscosity.12,13,14,15 In other words, in PP/LDPE blends without additives such as fillers or compatibilizers, the complex viscosity decreases due to larger shear in the new screw.
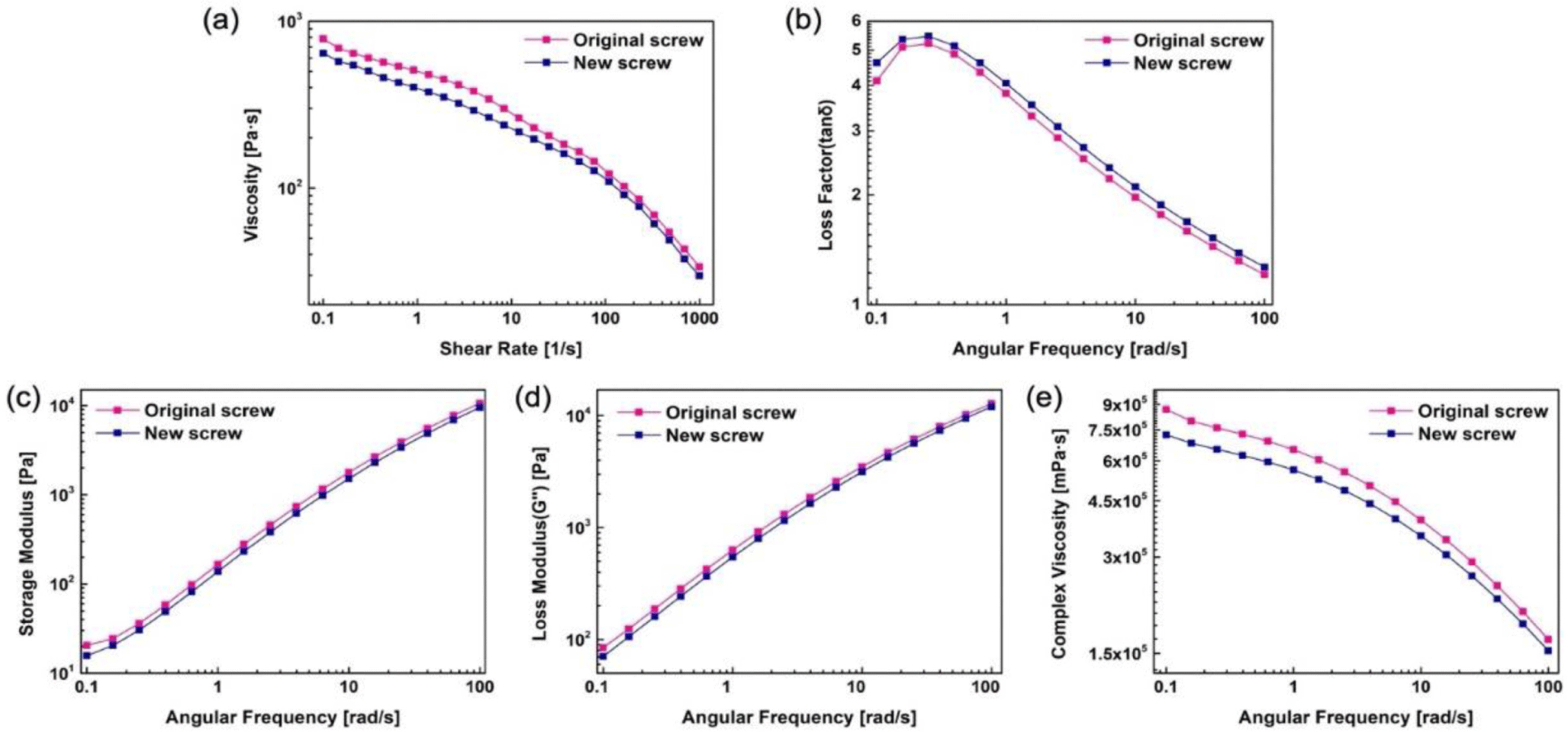
Conclusions
In this study, the kneading effect of PP/LDPE blends according to differences in screw profile was analyzed using an extrusion simulation program. We designed a new screw with an improved kneading effect by replacing the forward conveying block of the original screw with a reverse conveying block. By setting the optimal extrusion process conditions through a simulation program, waste of materials and time was minimized, and an eco-friendly process was realized. The simulation results were compared with actual extrusion process outcomes to evaluate the superior kneading effect of the new screw, confirm changes in material properties, and verify the accuracy of the simulation program. This laid the foundation for the study into the possibility of developing high-performance polymer composites and recycling through efficient blending of polymer materials.