Introduction
Submarines play an important role in modern warfare and national defense and their effectiveness relies heavily on underwater stealth performance. As sound waves are the primary means of long-distance communication and detection in seawater, a submarine’s ability to absorb underwater sound is a key factor in its stealth capabilities.1 The main method for achieving underwater acoustic stealth is applying sound-absorbing materials to the interior and exterior surfaces of submarines.2,3 Rubber-based materials are widely used for underwater sound absorption due to their ability to dissipate acoustic energy into heat through their viscoelastic properties.4 To enhance their strength to withstand the hydrostatic pressure and damping performance across various frequency ranges, additives such as ceramics and fibers can be incorporated.5 Additionally, the porosity and microstructure of these materials are carefully controlled to optimize their mechanical and acoustic properties.6
Among the rubber-based materials, polyurethane is a highly adaptable polymer with a block copolymer structure. It is composed of soft segments formed by flexible long-chain oligo-polyols and hard segments made from diisocyanates and chain extenders, arranged in alternating repeating units.7,8 The properties of polyurethane can be tailored extensively by modifying the monomer structure, adjusting the hard segment content, or varying the molecular weight to meet specific properties such as elasticity, density, and loss factor.9,10 The microphase separation structure of polyurethane11,12 contributes to its energy loss performance, making it suitable for sound absorption applications. In previous studies on polyurethane (PU), the effects of crosslinking agents were often overlooked, and detailed analyses of changes in loss factor with temperature variations were rarely conducted.
In this study, the influence of TMP concentration on the mechanical and sound absorption properties of PU was systematically investigated. The results demonstrated a significant increase in Young’s modulus with increasing TMP concentration, indicating that the enhanced crosslink density due to higher TMP content strengthens the structural integrity of the PU. The loss factor (tan δ), a key indicator of sound absorption performance, showed a 27.19% increase at the highest TMP concentration (TMP 100). Notably, as the temperature decreased from 30°C to 10°C, the loss factor increased by up to 13.68%, highlighting that both TMP content and temperature are critical factors affecting the sound absorption performance of PU.
Experimental
The following chemicals (Sigma-Aldrich, St. Louis, MO, USA) were used in the study: dimethylolpropionic acid (DMPA), trimethylolpropane (TMP), polyethylene glycol (PEG, Mn = 3350 g/mol), dibutyltindilaurate (DBTDL), 4,4′-methylenebis(cyclohexyl isocyanate) (H12MDI). H12MDI was dried with 4-Å molecular sieves prior to use. PEG was melted at 60°C before mixing.
PU membranes were synthesized following the method described in a previously reported study.7 PEG, DMPA, and TMP were placed into a four-necked round-bottom flask equipped with inlets for an external thermometer, a stirrer, nitrogen gas purging, and a heating jacket. The mixture was degassed under vacuum at 85°C for 1 hour and then cooled to 55°C. Next, a solution of H12MDI and DBTDL was added dropwise into the flask. The reaction was carried out at 85°C for 3.5 hours. The PU underwent an additional forming process to fabricate into 0.1 mm-thick films using a mini hot press (QM900S, QMESYS, Uiwang, South Korea) under a pressure of 25 MPa and a temperature of 50°C. The prepared samples were cut into a desired size for the mechanical and thermal tests.
The functional groups of the PUA prepolymers were analyzed using FTIR spectroscopy (Frontier, PerkinElmer, Waltham, MA, USA). The IR spectra were obtained via the attenuated total reflectance (ATR) technique by coating the PUA prepolymers onto a zinc selenide crystal. Spectral data were collected over the wavelength range of 500 to 4000 cm-1 with a resolution of 4 cm-1.
The tensile properties of the PUA membranes were evaluated according to ASTM D882 standards, as described in a previously reported procedure.7 A tensile tester (Instron Corp, Norwood, MA, USA) with rubber-coated grips and a 100-kgf load cell was used for testing. Samples were elongated at a constant rate of 5 mm/min to measure their tensile characteristics.
The viscoelastic properties of the PU membranes were investigated using a dynamic mechanical analyzer (DMA, TA Instruments DMA 850). Samples were prepared in a rectangular shape with a width of 5 mm, a length of 30 mm, and a thickness of 300-500 μm. The tests were performed in film tension mode over a frequency range of 1-100 Hz and conducted in a multifrequency (temperature sweep) mode from 0°C to 50°C, with a heating rate of 5°C/min. To ensure linear viscoelastic behavior, the amplitude was maintained at 10 μm, and the initial preload force was set to 0.01 N. Each sample was analyzed to measure the storage modulus (E’), loss modulus (E’’), and loss factor (tan δ). These measurements were used to evaluate the sound absorption performance and thermal stability of the PU. The storage modulus represents the elastic portion of stored energy, while the loss modulus indicates the energy dissipated within the material. The loss factor, defined as the ratio of the viscous to the elastic component, depends on the storage and loss moduli (Table 2).
The thermal properties of the PU membranes were analyzed using a differential scanning calorimeter (DSC, TA Instruments Q2000). Samples were prepared in a square shape with dimensions of 1 cm × 1 cm and a weight of 5.5 mg. The temperature range was programmed to increase from -90°C to 100°C and then decrease back to -90°C, with a heating and cooling rate of 19.98°C/ min. To minimize noise caused by initial impurities, each measurement was repeated three times, and the data were collected accordingly.
Results and Discussion
Figure 1(a) and (b) show the components used to synthesize the PU polymers and the images of the molded samples in film form for characterization, respectively. The names of each sample and the quantities of materials used for their production are listed in Table 1. In general, an increase in the amount of TMP resulted in higher viscosity of the premixture during synthesis, making agitation challenging. Conversely, a decrease in TMP led to insufficient crosslinking after synthesis, resulting in unstable shapes. Visually, the PU samples appear opaque, with no significant differences observed based on the amount of TMP used and they were rigid at room temperature.
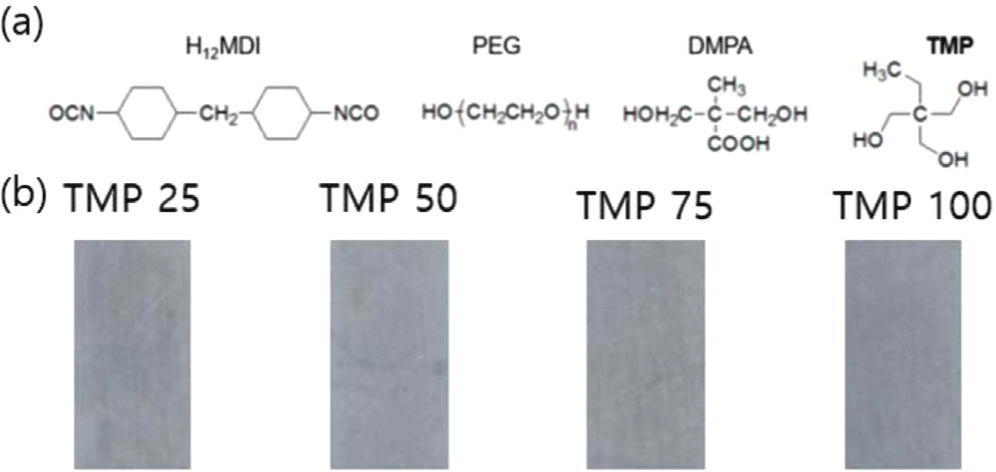
Figure 2(a) shows the overall spectra corresponding to the PU sample with different TMP content. All the spectra look similar and show the peaks at 2882-2886 and 1150 cm−1, corresponding to the CH2–CH2 and C–O–C bonds for PEG.7 Characteristics peaks of CO, and NH were observed at 1740-1790, and 3300-3600 cm−1 confirm the formation of urethane bonds. The urethane peak at 1715 cm−1 decreased as the TMP content increased, indicating a greater formation of urethane bonds as shown in Figure 2(b).
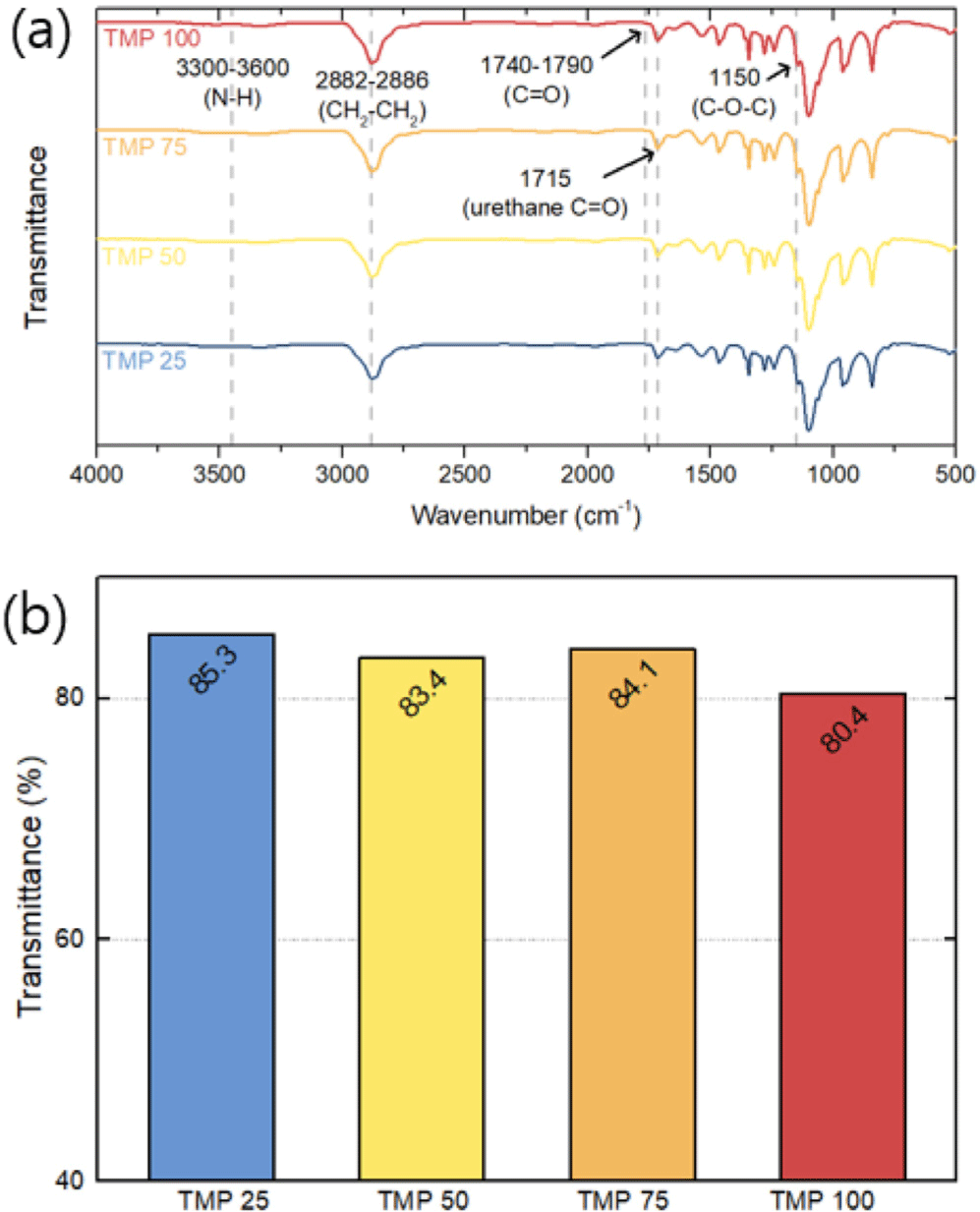
Figure 3(a) shows the slope of the initial tensile curve, indicating a significant increase in the elastic modulus of the polyurethane (PU) material with increasing TMP concentration. As shown in Figure 3(b), the elastic modulus was 144.72 MPa at TMP 25, but increased to 294.96 MPa at TMP 100, representing a rise of approximately 103.8%. This is attributed to the tripling of TMP content, which enhances the crosslinking density and strengthens the polyurethane structure. The increase in elastic modulus can have a positive effect on improving pressure resistance in underwater environments
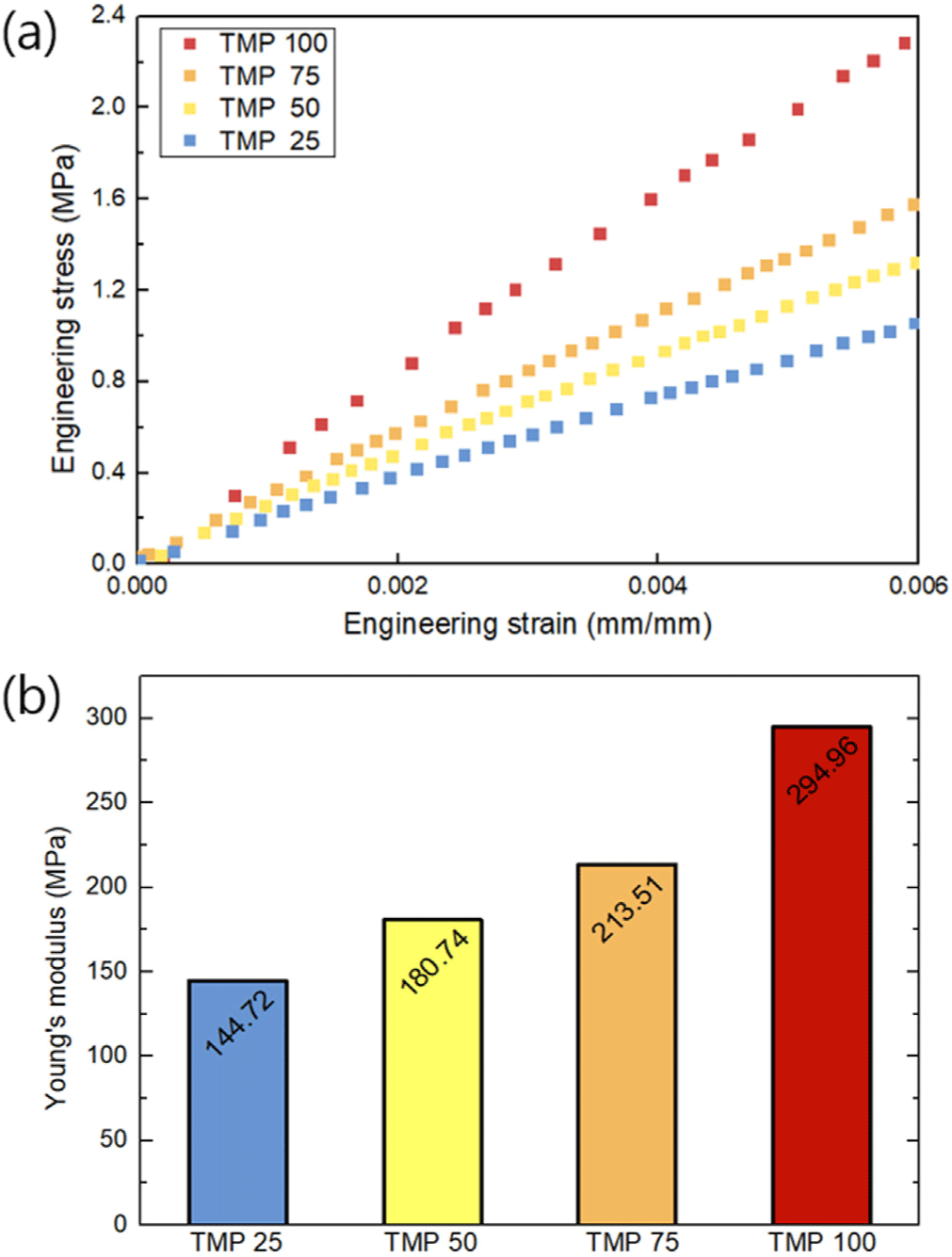
Melting temperature (Tm) and crystallization temperature (Tc) of the PU specimens were identified from DSC curves shown in Figure 4(a). Tm represents the temperature at which the crystalline structure completely melts and corresponds to the highest point of the endothermic peak. Tc indicates the temperature at which the amorphous regions begin to transform into crystalline structures and is represented by the highest point of the exothermic peak. Regardless of the TMP content, all the samples exhibited sharp Tm and Tc peaks. These distinct peaks are likely attributed to the high PEG content in the PU samples (>85 wt.%), as PEG is a semicrystalline polymer. Although the PU samples were crosslinked with TMP, the thermal properties of semicrystalline PEG appear to have a significant influence.13Figure 4(b) shows that Tm ranges from 40 to 42 °C, while Tc ranges from 15 to 16 °C. These temperatures remain relatively consistent regardless of the TMP content.
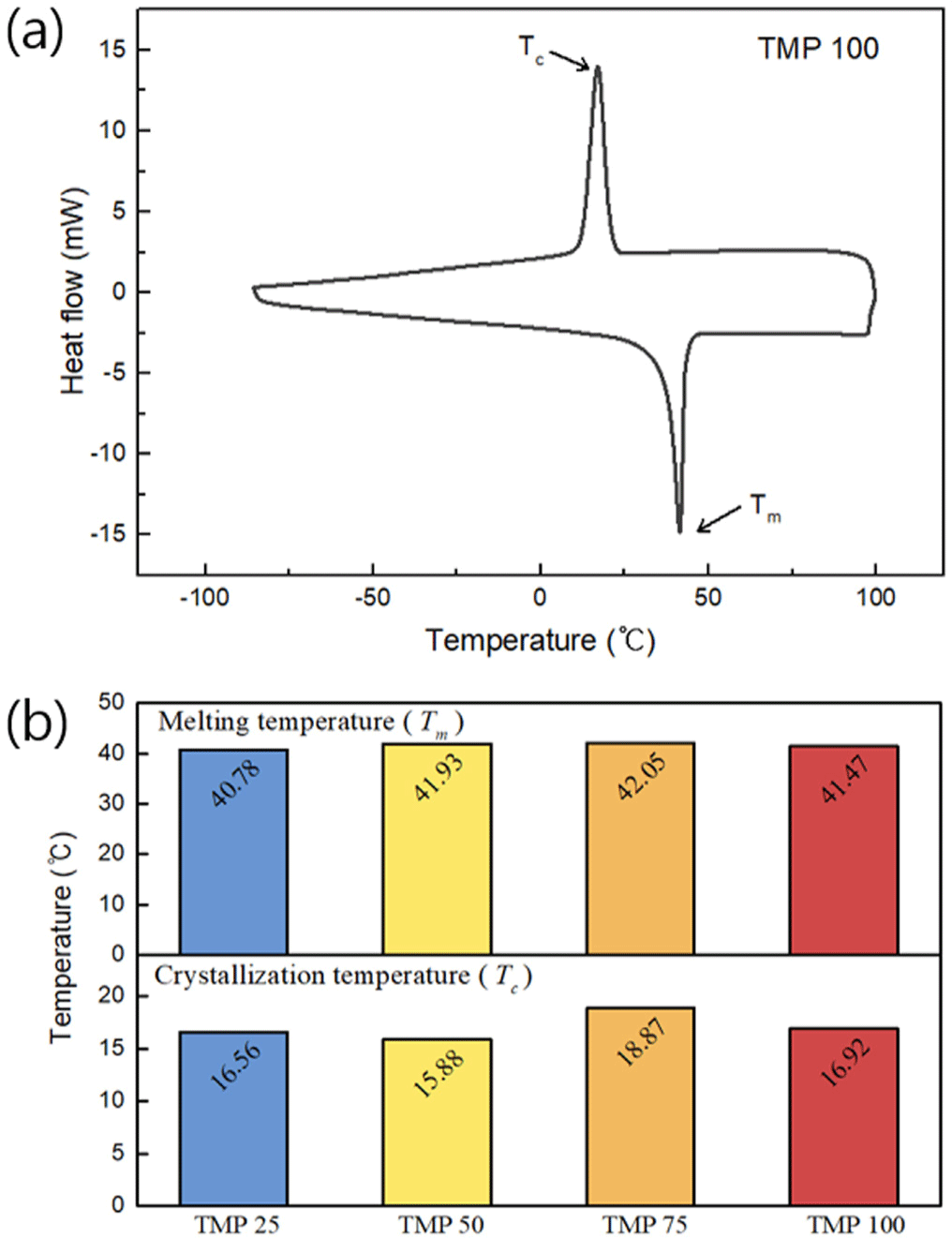
Figure 5(a) illustrates the change in loss factor with varying TMP content. As the TMP content increases, the loss factor also rises. For instance, the loss factor of the TMP100 sample is 27.19% higher compared to the TMP25 sample at 30°C. This indicates that the higher TMP content leads to more crosslinking, thereby enhancing the viscoelastic properties of the material and increasing energy dissipation.
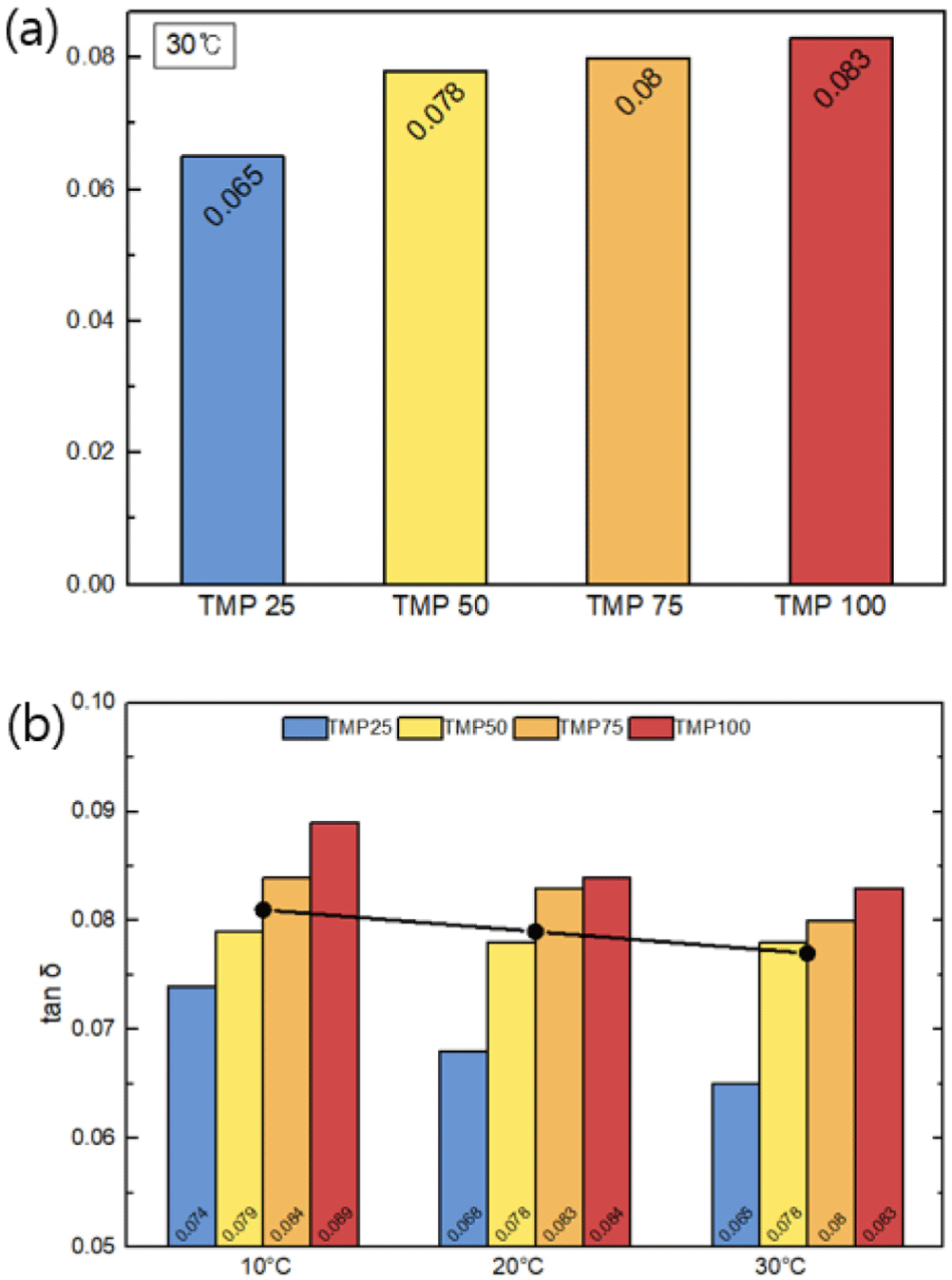
As shown in Figure 5(b), the trend of increasing loss factor with higher TMP content remains consistent even when the temperature varies between 10°C and 30°C. Furthermore, it is observed that the loss factor tends to increase at lower temperatures. Generally, as water depth increases, seawater temperature decreases, typically ranging from 200°C to 1500°C, which causes the loss factor to drop to approximately 5-15. This trend suggests that the material exhibits advantageous behavior under such conditions. Considering the previously discussed shape stability and elastic modulus trends, the higher TMP content in crosslinked PU not only increases the loss factor but also demonstrates suitable properties for underwater acoustic absorption materials.
Conclusions
This study investigates the effect of TMP content on the mechanical and viscoelastic properties of polyurethane (PU) membranes. The results reveal that increasing TMP content significantly enhances both Young’s modulus and the loss factor (tan δ), indicating that higher TMP content improves the crosslink density and mechanical strength of PU materials. Specifically, Young’s modulus increased from 144.72 MPa at TMP 25 to 294.96 MPa at TMP 100, demonstrating improved structural reinforcement. Similarly, the loss factor (tan δ) at 30°C rose from 0.06536 at TMP 25 to 0.08313 at TMP 100, indicating enhanced acoustic absorption performance. Regarding the temperature-dependent changes in the loss factor (tan δ), the results show that temperature has a significant effect. The tan δ value at 10°C was approximately up to 13.68% higher than that at 30°C. These findings suggest that increasing TMP content in PU materials improves the mechanical strength, damping performance, and thermal stability required for underwater acoustic applications. The increased crosslinking agent contributes to these enhanced properties. This study provides foundational data for the design and application of PU-based acoustic absorption materials. Future research should explore the interaction of TMP with other additives and investigate the long-term thermal stability of these materials.