Introduction
Cellulose is the most abundant biopolymer in the biosphere, which is a linear condensation polymer composed of repeating D-glu-copyranose residues linked by β-1,4-glucosidic bonds.1 Cellulose exhibits a high degree of polymerization, the individual glycan chains can reach lengths of greater than 25,000 glucose residues. The adjacent anhy-droglucose molecules are rotated 1808 with respect to their neighbors, coupling with adjacent cellulose molecules by extensive hydrogen bonds and van der waals forces2 which produces a straight, stable heterogeneous supra-molecular structure.3 It is the main reason that cellulose shows high strength properties. Cellulose also presents biodegradability, renewability, low density, and is potential for chemical modification. Thus, cellulose is potential as reinforcing biomaterial.4
Starch is a natural carbohydrate, which is composed of a mixture of amylose, a linear polysaccharide and amylopectin, a highly branched polysaccharide.5 The particle size of starch ranges from 5 to 50 μm depending on its original resources.
In general, the particle size of starch increases as the following order: rice starch < corn starch < wheat starch < potato starch.6 It is well known that fillers with particle size from 1 to 10 µm primarily act as diluents and have no reinforcing capability in rubber matrix, fillers with particle size greater than 10 µm generally deteriorate the physical properties rather than reinforcing.7 Therefore, one of the major bottlenecks for starch used as reinforcing filler in the rubber compounds is its large particle size. Another one of the major bottlenecks is its hydrophilic surface, which lead to poor interfacial adhesion with the hydrophobic rubber matrix, especially for the non-polar rubber, such as SBR.8 Therefore, various surface modification methods, such as grafting of poly(butyl-acrylate), esterification with xanthate, crosslinking with resorcinol-formaldehyde and isocyanate have been reported to enhance the interfacial bonding.9
A gel is a solid jelly-like material that can have properties ranging from soft and weak to hard and tough.10 Gels are defined as a substantially dilute cross-linked system, which exhibits no flow when in the steady-state. By weight, gels are mostly liquid, yet they behave like solids due to a three-dimensional cross-linked network within the liquid.11 It is the crosslinking within the fluid that gives a gel its structure (hardness) and contributes to the adhesive stick (tack).12 In this way gels are a dispersion of molecules of a liquid within a solid in which the solid is the continuous phase and the liquid is the discontinuous phase. The word ‘gel’ was coined by 19th-century Scottish chemist Thomas Graham by clipping from gelatin.13
In this research, cellulose and starch were made into gel state at first, and then incorporated with silica powder to get the hybrids (cellulose-silica hybrid which was called into Cell. hybrid and starch-silica hybrid which was called into Star. hybrid in this paper) as fillers with gel-adsorption method which filled into SBR 1502 used as reinforcing agents. After the compounding and curing processes, abrasion resistance, friction coefficient, tensile strength, storage modulus in different temperatures, oxygen transmission, and swelling test of compounds filled with different fillers were characterized.
Experimental
Styrene-butadiene rubber latex 1502 (effective mass 61 ± 1%, styrene 23.5%) was obtained from Korea Kemho Petrochemical Company (KKPC), Korea; cellulose powder (microcrystalline) was obtained from DaeJung Company, Korea; starch (corn) was provided by Duksan Pure Chemical Company, Korea; sodium hydroxide (NaOH), extra pure (above 95%); sulfur, powder, extra pure (above 99%), were purchased from Dae Jung Company, Korea; methanol, extra pure (99.5%); zinc oxide, extra pure (99%); stearic acid, extra pure (95%); dodecyl-benzene-sulfonic acid, sodium salt, (DBS-Na) (50%), ethanol, extra pure (above 98%) were purchased from Samchun Pure Chemical Company, Korea; sodium hydroxide, extra pure (above 95%), was purchased from Dae Jung Company, Korea; urea, extra pure (above 99%); epichlorohydrin, extra pure (99.5%); N-cyclohexyl-2-benzothiazolylsulfenamide, extra pure (above 95%); 2,2’-dibenzothiazolyl disulfide, extra pure (above 95%), were purchased from Tokyo Chemical Industry Company, Japan.
Synthesis of starch-silica hybrid and cellulose-silica hybrid mechanisms were shown in Figure 1 and Figure 2. The step for starch-silica hybrid was shown in Figure 1: first, 5 g starch was added into the water, then heat at 80°C, stirring for about 30 min, then put 10 g silica powder into the system, stirring for 10 min under the temperature of 80°C. After that, cooling the system at room temperature.
The gel hybrid for starch-silica hybrid was produced. And the step for cellulose-silica hybrid was shown in Figure 2: 5 g cel-lulose was poured into a NaOH/urea solution14 with a ratio of 6 wt%/4 wt% in water, then put 10 g silica powder into the reaction system. After that, dropped the epichlorohydrin (which used as crosslinking agent) slowly into the system, stirring for 30 min under a temperature of 5°C,15 then cooled at room temperature, then the gel-silica hybrid for cellulose-silica hybrid was produced.
The mechanism of composite process was shown in Figure 3. The SBR latex which has been stabilized by DBS-Na was poured into the reaction system under high temperature (80°C in starch-silica hybrid system and 50°C in cellulose-silica hybrid system), stirred for 4h, then cooling down in static state. After that, the mixtures were dried in vacuum at 70°C for 48 h, and the neat SBR was fabricated by directly precipitating SBR latex into calcium chloride aqueous solution and then dried in vacuum at 70°C.
During the process, the gel-silica hybrid adsorbed the rubber chain under the high temperature, then cooling down under the room temperature, the gel-silica hybrid will form the block state, and filled into the space of the rubber crosslinking layers, and occurred the dislocation effect,16 to provide physical crosslinking for rubber chain, and make the composite more compact than neat rubber material. As for silica, it would be filled into the space of gel structure by the adsorption effect due to the –OH groups which can form the hydrogen bonds with gel, it will improve the mechanical properties of rubber materials.
The composites and neat SBR were blended with other ingredients on a two-roll mill at 40°C. The formulations for synthesis and compounding process are summarized in Table 1. At the last step, the vulcanized composites with a thickness of 1 mm were achieved at 150°C under a pressure of 15 MPa with a heating press machine (Auto hydraulic press type, Ocean Science). Finally, the vulcanizates were cut into specimens for mechanical characterizations and other tests.
The morphology of the samples after the tensile test was carried out on a FE-SEM (JSM-7500F, JEOL Ltd. Japan). The cure/vulcanization characteristic of as-prepared samples were measured by a rubber process analyzer (RPA-V1, U-CAN DYNATEX INC.). The minimum torque (ML), maximum torque (MH), scorch time (ts2), and optimum cure time (t90) were determined by the above RPA. The cure rate index (CRI) was used to evaluate the cure rate of the rubber, and it was calculated by the following equation:17
Tensile strength was performed on a Tinius Olsen H5KT-0401 testing machine at a speed of 500 mm min−1 according to ASTM D412 with the average of three measurements. Specimens on standard dumb- bell shape were cut from the vulcanizate sheet with dimensions 25 mm × 6 mm × 1 mm (length × width × thickness). Strain sweep was performed with an RPA. It was carried at 60°C with a 1.67 Hz frequency. Shear storage modulus was recorded at each strain according the ASTM D 6204-97. Shore A hardness of the specimens was obtained with Shore Durometer Type A according to ASTM D22-40.
Friction factor test was performed at room temperature by friction test machine. And swelling ratio tests were carried out in toluene18 for 1, 2, 4, 8, 12 and 24 h according to ASTM D71-79.
Results and Discussion
Figure 4 showed the FE-SEM micrographs of (a) compound filled with cellulose hybrid before vulcanization; (b) compound filled with starch hybrid before vulcanization; (c) compound filled with cellulose hybrid after vulcanization; (d) compound filled with starch hybrid after vulcanization. From graph (a) and (b), it can be found that the structures of cellulose-silica hybrid and starch-silica hybrid in SBR compounds, and the structure of cellulose-silica hybrid compound looked like a whole.19 But as (b) showed, it can be found the structure of starch-silica hybrid compound looked relatively loose. And large, individual blocks of gel could be seen in the graph (b). It could prove that after drying process,20 the network structure of starch gel had been partially destroyed, but as cellulose gel, it didn’t seem to get influence due to the drying process. The possible reason of that may be the network structure of cellulose gel is stronger than starch gel, and after drying, the cellulose-silica hybrid composite can maintain a more completed network structure. (c) and (d) showed the graph of cellulose-silica hybrid compound and starch-silica hybrid compound. From these graph, it can be found that the structure of cellulose-silica hybrid compound looked more compact than starch-silica hybrid compound. And the particle size of cellulose-silica hybrid is also smaller than starch-silica hybrid. The smaller filler particle size may provide better mechanical properties of rubber com-pounds.21
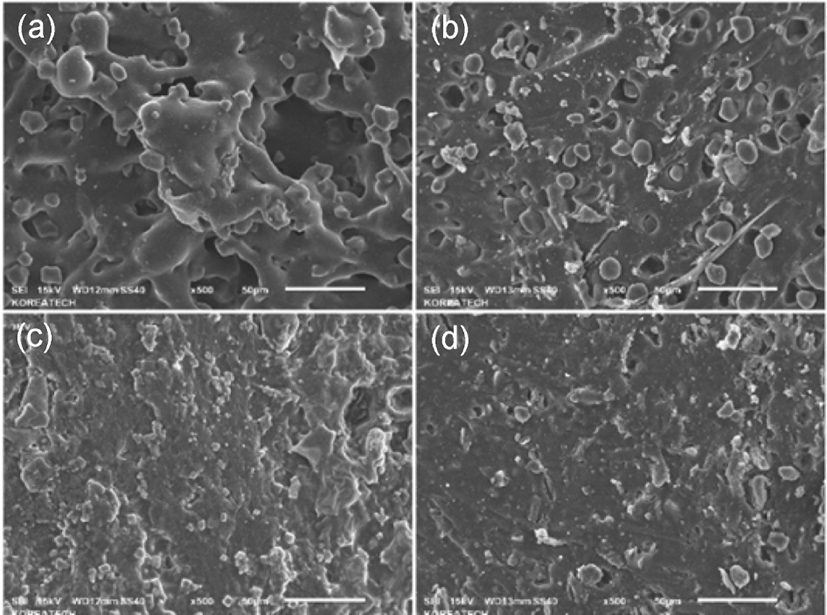
It can be found the difference for compounds filled with starch gel, cellulose gel, starch-silica hybrid and cellulose-silica hy-brid from Figure 5, which showed the FT-IR curves. From this graph, it can be seen the main difference peak is about 1100 cm−1, which would be the typical peak of silica.22 And in the curve of cellulose-silica hybrid, it also showed the peak about 3500 cm−1, which meant cellulose-silica hybrid had more –OH groups than others.
Figure 6 showed the TGA data of samples. From these curves, it can be found the more ratio of filler increase, the higher initial decomposition temperature. The possible reason is due to the structure of matrix would be more compact with the filling ratio increasing. And the more compact structure of matrix, the better thermal stability.23 Due to this reason, cellulose-silica hybrid compounds showed better thermal stability than starch-silica hybrid compounds under the same ratio. Figure 7 showed the different samples’ friction coefficient, it can be found that the friction coefficients (both static and dynamic) of cellulose-silica hybrid compounds decreased with the filling ratio increased. But as starch-silica hybrid compounds, the situation was completely opposite. It can be interpreted cellulose-silica hybrid would provide more compact structure when constitute matrix with SBR rubber chain, so the surface of samples would be more smooth than others, but as starch-silica hybrid, due to the destruction by drying process, it would also destroy the smooth surface for compounds, so the friction coefficient value is higher than others.
Figure 8 showed the tensile strength results of compounds. From these curves, it can be observed all the gel fillers had in-creased modulus and tensile strength of compounds compared to the neat SBR, especially at the strain value of 300%. The reinforcing effect of cellulose-silica hybrid 10 phr is the best, which curve has the largest 300% modulus value. The reason for this result is that cellulose-silica hybrid not only has compact network structure which will provide physical crosslinking for rubber chain, but also has more –OH groups, they will provide more hydrogen bonds between cellulose-silica hybrid and vulcanizing agent sulfur which provide single sulfur bonds for crosslinking.24 It could make better combination with SBR matrix. And compared to the curve of cellulose-silica hybrid 5 phr, it also can be seen the curve of cellulose-silica hybrid 10 phr always on the top, which meant it would provide better reinforcement effect with the filling ratio increased. Thus, the cellulose-silica hybrid 10 phr has the best tensile strength reinforcement effect.
Figure 9 displayed the results of storage modulus with strain (or Payne effect25) at the constant pressure of 15 MPa for SBR compounds filled with different fillers. The storage stress decreased with the increasing of the strain amplitude for all the above samples. This result can be explained by the breakdown of the aggregated secondary network among filler particles or the aggregates formed by van de Waals-London attraction forces, and as illustrated by Payne. From the curves, it can be found the curves of cellulose-silica hybrid filled compounds were always on the top, which meant they had more storage stress than others. And the cellulose-silica hybrid 10 phr also showed better storage modulus compared to the cellulose-silica hybrid 5 phr, it proved with the filling ratio of cellulose-silica hybrid increased, the storage modulus also increased. The possible reason is due to the compact structure of cellulose-silica hybrid which can form more stable matrix, and form physical crosslinking with rubber chain by adsorption method, which could provide more storage stress. But as starch-silica hybrid, the more filling ratio, after drying process, the worse crosslinking state and less physical crosslink, thus, the lower storage modulus of that.
Figure 10 showed the swelling ratio of fillers/SBR vulcanizates in toluene solvent, the swelling ratio is calculated using the following equation:26
Where w1 is the original weight of specimens and w2 is the weight of specimens after swelling, ρr is the density of rubber (ρSBR = 0.933 g/cm3), and ρs is the density of solvent (ρtoluene = 0.867 g/cm3).
It can be seen that the swelling ratio increased very fast at the early 4 h and then changed little from 8 to 12 h, indicating the adsorption saturated. The saturated swelling ratio of neat SBR was 396.5%. When the starch-silica hybrid incorporated, the swelling ratio decreased (282.5% for starch-silica hybrid 5 phr, and 295.5% for starch-silica hybrid 10 phr), but the swelling ratio of compound filled with pure silica had decreased into 201.3%. This may be attributed to the pure silica could occur better dislocation effect with rubber matrix than starch-silica hybrid after the drying process. And for cellulose-silica hybrid compounds, due to the best adsorption property and more compact matrix structure, they showed great swelling resistance in toluene solvent (165.2% for cellulose-silica hybrid 5 phr, and 157.6% for cellulose-silica hybrid 10 phr), it meant the compounds filled with cellulose-silica hybrid have higher crosslinking density value, which is a very important data to describe the mechanical properties for rubber materials.
Conclusion
Starch-silica hybrid and cellulose-silica hybrid were synthesized by gel-adsorption method, then compounded with SBR rubber latex by physical crosslink with adsorption force. The results of FE-SEM graphs showed the states of composites and compounds filled with different fillers (cellulose-silica hybrid and starch-silica hybrid), it can be seen that cellulose-silica hybrid can form more compact matrix structure with rubber material, just like a whole, but as starch-silica hybrid composite, it showed individual gel blocks in the matrix. So cellulose-silica hybrid would improve better mechanical properties during the graphs.
The results of tensile strength and strain sweep showed cellulose-silica hybrid 10 phr could improve the mechanical properties of SBR rubber, and the swelling test results also showed this filler could form a more compact matrix with SBR rubber compared to others in this research.
In addition, it could be found from the results of friction coefficient test that cellulose-silica hybrid would reduce the friction coefficient of SBR rubber compounds, which would extend the service life of some rubber products like rubber roller and conveyor belt.27-29 Above all, cellulose-silica hybrid will become a potential filler for rubber industry in the future.