Introduction
최근 환경문제에 대한 관심의 증가로 인해 생활환경을 침해하는 소음 및 진동 등의 생활 공해에 대한 방지대책의 요구는 점점 높아지고 있다. 자동차 엔진을 비롯하여 산업기계 등 동적인 구조물의 소음 및 진동을 억제 또는 감소시키기 위한 소음저감 및 방진 기술은 더욱 발전되고 있으며 정밀 기기의 발달에 따른 요구 조건의 강화 및 제품의 신뢰성 향상이 요구되어진다. 이런 요구와 상황에서 방진고무에 대한 연구는 국내외적으로 많이 이루어지고 있다. 방진과 같은 진동 제어가 사회적으로 대두되는 이유는 가격절감, 소형화, 경량화 등에 따른 정밀도를 요구하는 새로운 기계 및 장치들이 출현 되고 있기 때문이다. 특히 방진 제품들은 선박, 철도, 항공 시설물 등의 일상에서 활용되고 있는 것 이외에도 반도체 공장, 초미세 가공기술의 진동 제어장치 및 초정밀 검사장비 등에서도 중요성이 더욱 부각되고 있다. 최근 차량의 상품성 향상과 고기능화를 목적으로 차량의 진동을 능동적으로 제어하여 조종성능과 승차감을 동시에 향상시키는 기술은 전 세계적으로 차량 개발의 가장 중요한 흐름이 되어가고 있다. 하지만 기존의 방진고무는 재료 고유의 모듈러스를 가지고 있어 특정 영역의 주파수 진동만을 흡수하는 한계가 있어 능동적인 진동 제어가 어려운 단점을 지니고 있다.1-6
본 연구에서는 기존 방진고무의 한계를 개선하기 위하여 지능 재료의 일종인 가변형 능동제어가 가능한 자기유변탄성체(magneto-rheological elastomer, MRE)에 관한 연구를 진행하였다. MRE란 탄성 매트릭스에 자기응답입자(magnetic responsible particle, MRP)를 충전하여 자기장에 의한 강성이 가역적이고 즉각적으로 변화되는 재료이다. 자성입자를 사용하는 자기유변 물질은 매트릭스의 형태에 따라서 자기유변유체(magneto-rheological fluid, MRF)와 MRE로 구분된다. Figure 1에 나타낸 바와 같이 MRF는 유체로 구성된 매트릭스 내에 자기응답입자가 분산되어 외부에서 자기장이 인가되었을 때 자기장 인가의 방향으로 자기응답입자가 배향되어 가역적인 모듈러스의 변화가 가능한 재료이다. 하지만 MRF는 자기응답입자와 유체 매트릭스 사이의 밀도차로 인해 자기응답입자가 침전이 되는 문제점이 있다.7,8 이와 달리 MRE는 탄성 매트릭스 내에 자기응답입자가 분산되어 고정된 상태로 제조되기 때문에 MRF의 단점을 보완할 수 있다.9-11 이러한 MRE는 외부에서 가해지는 자기장에 의해 강성이 가역적이며 재료의 모듈러스를 즉각적으로 변화시키는 것이 가능하고, 외부의 자기장이 인가되면 매트릭스 내부의 자기응답입자가 자기장이 인가된 방향으로 사슬형상의 클러스터를 형성하게 된다. 이러한 사슬 클러스터가 외부의 압력흐름 또는 전단흐름에 대해 저항하는 것이 기본 메커니즘이다.12
이미 많은 연구를 통해 자기장의 세기가 증가함에 따라 매트릭스의 항복응력이 증가한다는 사실은 밝혀졌다. 자기장 인가에 대한 MRE의 모듈러스 변화율을 MR 효과(magneto-rheological effect)라 한다. 이러한 MR 효과는 사용되는 매트릭스의 종류에 따라 크게 달라질 수 있다. 본 연구에서는 기존에 사용되던 NR계 MRE와 EPDM계 MRE의 블렌드를 통하여 서로의 단점을 보완하면서 MR 효과를 향상시킬 수 있는 방법에 대한 연구를 진행하였다.
본 연구에서 MRE 제조를 위한 매트릭스로 NR과 EPDM을 블렌드 하는 방법을 선정하였다. 기본적으로 NR은 물리적 특성이 우수하며 가공성 측면에서도 우수하다는 장점을 지닌 재료이다. 하지만 NR 매트릭스 내의 불포화 결합으로 인해 열, 산소, 오존 등 외부적인 환경 조건에 취약하다는 단점을 갖는다. 이러한 NR의 장점을 유지하며 단점을 보완하기 위해 사용된 재료가 EPDM이다. EPDM의 경우 내열성, 내오존성, 내산화성, 내후성 등 노화 저항성이 뛰어나 가혹한 환경에서 장시간 사용되어도 재료의 물성을 유지하며 동시에 고온 안정성의 장점을 갖는다. 그리하여 EPDM은 열, 산소, 오존 등 NR의 단점을 보완할 수 있는 재료로 선택 되었다. 두 종류의 엘라스토머를 블렌드 하는 이유는 성능을 만족할만한 새로운 폴리머 재료를 개발하기 위해 사용 되어지는 시간과 비용보다 더 경제적이기 때문이다. 두 엘라스토머의 블렌드는 물리적인 특성과 가공성 향상 그리고 NR의 단점을 보완하기 위함이다. 하지만 단순한 블렌딩을 하였을 때에는 각 엘라스토머가 갖는 기존의 특성보다 오히려 낮은 기계적 특성을 나타낼 수 있다. 이러한 현상은 NR과 EPDM 각각의 불포화 정도와 극성의 차이로 인해 경화속도가 달라지며 상용성이 떨어지기 때문이다. 매트릭스간 불포화 정도의 차이가 생길 경우 상대적으로 불포화 결합이 적은 EPDM의 배합물에 포함된 경화제가 NR의 배합물로 전이되는 현상이 발생할 수 있다.13-15 본 연구의 목적은 상대적으로 경화속도가 느린 EPDM을 전경화 시킨 후 NR과 블렌드 함으로써 상용성이 우수한 NR/EPDM 블렌드를 제조하여 이를 MRE의 매트릭스로 이용하고자 함이다. 따라서 본 연구에서는 NR과 EPDM의 블렌드 비율, EPDM 전경화 온도 및 시간 등에 따라 MRE를 제조하여 이들의 특성을 조사하였다.
Experimental
본 연구에서는 MRE의 제조를 위한 매트릭스로 EPDM (Keltan KEP-960N(F), (주)금호폴리켐)과 NR (STR 5L, PAN STAR)을 사용하였다. 보강제는 카본블랙(N330, Aditya Birla Chemicals)을 사용하였다. 자기응답입자로는 평균 직경이 3~5 μm인 CIP (carbonyl iron particle, CC grade, BASF SE)를 사용하였다. 경화 시스템 구축을 위해 사용한 첨가제는 모두 Puyung Willing Chemical사에서 구입한 zinc oxide (ZnO), stearic acid (SA), N-cyclohexyl-2-benzothiazyl sulfonamide (CZ), dibenzothiazyl disulfide (DM)을 사용하였다.
고무 배합은 open two roll-mill을 사용하여 진행하였다. Open two roll-mill에서 3분간 소련 과정이 진행된 뒤, 충전량이 많은 카본블랙과 CIP는 균질한 분산을 위하여 공정 초반에 투입하여 배합을 진행하였다. 그 이후 다른 첨가제들을 넣어 일정 시간동안 배합을 진행하였다. NR과 EPDM은 같은 방법으로 배합이 진행되었고, NR/EPDM 블렌드 역시 준비된 NR 뱃치와 전경화된 EPDM 뱃치를 open two roll-mill을 사용하여 블렌드 하였다. 고무 배합 과정을 Figure 2에 도식화하여 나타내었다. NR과 전경화된 EPDM의 최종적인 블렌드가 진행된 뒤 안정화가 완료된 고무는 무니점도계(Daekyung Engineering)를 사용하여 100°C에서 배합물의 무니점도를 측정하였고, 고무레오미터(DRM-100, Daekyung Engineering)를 이용하여 170°C의 조건하에서 스코치시간(ts2), 90% 경화시간(t90) 등의 경화 거동을 측정하였다.
NR과 EPDM을 단순 블렌드를 할 경우 EPDM에 비해 상대적으로 불포화 결합이 많은 NR 상으로 경화제가 전이되는 현상이 발생하여 최종적인 매트릭스에서 EPDM 상이 부분적으로 미경화 된 상태로 존재할 수 있다. 이로 인해 기존 NR과 EPDM이 갖는 물성보다 더 낮은 물성을 나타내게 된다. 이러한 단점을 보완하기 위해 EPDM을 전경화 하였다. 본 연구에서는 두 엘라스토머의 블렌드가 진행되기 전에 NR과 EPDM 각각의 뱃치를 만들어 놓은 후 실험을 진행하였다. 1차적으로 open two roll-mill을 사용하여 첨가제들과 배합된 각각의 뱃치는 배합이 끝난 뒤 안정화를 위해 상온에서 24시간 보관하였다. 2차적으로 EPDM은 120°C의 실험실용 air oven에서 각각 12분, 30분, 45분, 60분, 75분, 90분 동안 전경화가 진행되었다.
등방성 MRE는 open two roll-mill로 배합된 배합물을 고무 레오미터로부터 측정된 90% 경화시간에 의거하여 170°C의 온도와 15 MPa의 압력으로 조절된 유압프레스에서 제작되었다. 이방성 MRE는 압력과 열, 자기장을 동시에 인가할 수 있도록 설계된 자기장 인가 장치를 이용하여 고무 배합물 내의 CIP의 배향을 유도하였다. 이방성 MRE의 경우 설계된 전자석 장치를 이용하여 등방성 MRE와 동일한 온도와 압력을 주어 제작되지만 경화 과정에서 추가적으로 자기장을 인가하여 고무 배합물 내의 CIP 배향을 유도하였다. 설계된 전자석장치의 사진을 Figure 3에 나타내었다.
전경화 시간이 다른 EPDM을 블렌드한 MRE의 특성을 비교하였다. MRE의 인장물성은 KS M 6518에 나타난 규격에 따라 시편을 제작하였으며, 만능인장시험기(UTM, Daekyung Engineering)를 이용하여 50 mm의 initial clamp separation과 500 mm/min의 cross-head speed 실험 조건으로 측정하였다. 경도는 Shore A type의 경도계를 사용하여 측정하였다. 노화 시험은 ASTM D573에 의거하여 고무 노화시험기(C-RA1, (주)지시코)를 사용하여 측정하였다. 회전식 열 노화시험기를 사용하여 열 공기 항온조 내에 시험편을 걸어 회전시켜 가열공기와 접촉시키면서 노화시켰다. 실험은 80°C에서 1, 3, 5일 동안 열 노화를 시킨 후 꺼내어 실온에서 24시간 안정화 시킨 후 노화 시간에 따른 기계적 물성의 변화를 측정하였다.
MR 효과는 자기장인가 전후 전단 모듈러스의 변화율을 의미한다. 회전형레오미터(MCR 300)와 외부 자기장인가장치(Physica MDR 180)가 결합된 장치를 이용하여 MR 효과를 측정하였다. 이 장치는 자기장 발생이 계속될 때 전자석 코일의 발열에 의한 전류 감소로 자기장 세기가 점차 감소하는 현상을 제어하기 위해 전류를 동일하게 인가할 수 있도록 디지털 제어방식을 적용하였고, normal force가 증가함에 따라 MR 효과가 감소하는 문제점을 고려하여 오차 범위를 최소화하여 결과 값을 도출할 수 있도록 제작되었다.
Results and Discussion
NR/EPDM의 블렌드 비율과 EPDM의 전경화 시간에 따른 무니 점도와 경화 특성을 Table 1과 2에 나타내었다. Table 1과 2에 나타낸 NE의 N은 NR을 의미하고 E는 EPDM을 의미한다. 숫자는 EPDM의 전경화 시간을 의미한다. 또한 NR과 EPDM 각각의 결과와 NR/EPDM 블렌드 비율 5:5와 7:3의 결과를 나타내었다. NR에 비해 EPDM의 무니점도는 높은 값을 나타내었다. 상대적으로 높은 무니점도를 갖는 EPDM이 낮은 무니점도를 갖는 NR과 블렌드 되었을 때 점도가 감소하였다. 무니점도가 낮은 NR의 비율이 높아질 때 무니점도는 더욱 감소하는 것을 확인하였고 EPDM의 전경화 시간이 증가할수록 블렌드 된 고무의 무니점도는 증가함을 확인하였다. 최대 토크 값과 최소 토크 값 역시 같은 경향을 보였다. Table 1과 2에 나타난 바와 같이 NR, EPDM 매트릭스간의 블렌드와 EPDM의 전경화는 상용성에 크게 문제가 되지 않은 것으로 사료되었다. EPDM의 전경화 시간이 증가함에 따라 토크값이 커지게 되는데 이것은 미리 진행된 EPDM의 전경화 정도가 블렌드 내에서 더욱 진행되어 가교밀도가 증가했기 때문에 나온 결과로 사료된다.
EPDM의 전경화 시간과 블렌드 비율에 따른 인장물성을 Figure 4와 5에 비교하였다. EPDM의 전경화 시간과 NR의 비율이 증가함에 따라 인장물성이 증가 하였다. EPDM의 전경화 시간이 60분인 NR60을 기준으로 전경화가 진행되지 않은 NE0에서 NE60까지는 전경화 시간이 증가할수록 인장물성이 증가 하였고, NE60에서 NE90까지는 감소하는 것을 확인하였다. 이는 EPDM의 전경화 시간이 60분 이전에는 전경화가 충분히 진행되지 않아 NR과의 블렌드를 진행한 매트릭스 내의 EPDM상이 부분적으로 미경화 상태로 존재하기 때문이며, 60분 이후에서 감소하는 현상은 전경화 시간이 길어짐에 따라 EPDM의 과경화로 인해 NR과 충분한 블렌드가 진행되지 않아 나타난 결과로 사료된다. 매트릭스 내 CIP의 배향성에 따라 등방성MRE (Figure 4)와 이방성MRE (Figure 5)를 비교할 경우 등방성MRE의 인장강도가 이방성MRE의 인장강도보다 더 높은 것을 확인하였다. 이는 Figure 6에 나타난 CIP의 배향 특성으로 설명이 가능하다. 등방성MRE는 외부의 자기장인가 없이 열과 압력만으로 제조가 되기 때문에 CIP가 매트릭스 내에 균일하게 분산되어 존재하게 된다. 반면에 이방성MRE는 열과 압력 외에도 외부의 자기장 인가에 의해 제조되기 때문에 매트릭스 내 CIP가 사슬 클러스터와 같이 형성되어 배향을 이루게 된다. Figure 6을 보면 이방성MRE의 매트릭스 내 CIP 배향 방향과 인장시험 방향은 수직을 이루고 있기 때문에 이방성MRE의 인장강도는 매트릭스 내에 CIP가 균일하게 분산된 등방성MRE의 인장강도 보다 더 낮게 나타난 것으로 사료된다.
MRE의 모폴로지는 주사전자현미경을 사용하여 분석하였고 그 결과를 Figure 7에 나타내었다. Figure 7은 EPDM의 전경화가 60분이 진행된 이방성MRE의 자기장 세기에 따른 CIP의 배향성을 비교한 사진이다. Figure 7(a)는 1200 mT, (b)는 1600 mT, (c)는 1980 mT의 자기장을 인가한 시편의 모폴로지이다. 외부에서 가해지는 자기장의 세기가 커질수록 CIP의 배향성은 뚜렷하게 확인이 되었다. 그로 인해 CIP의 배향은 NR과 EPDM을 블렌드한 매트릭스 내에서도 원활하게 이루어지는 것을 확인하였다.
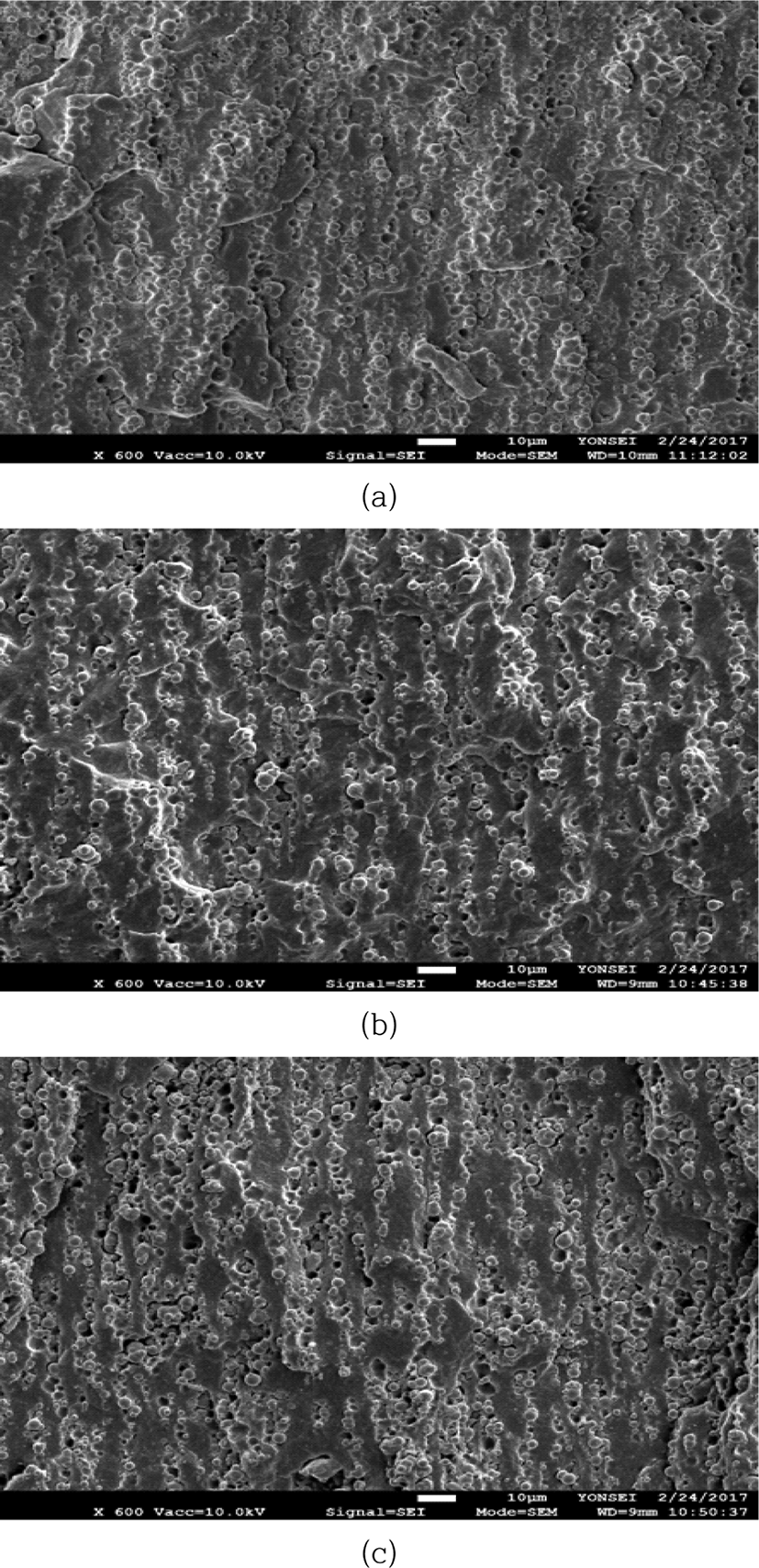
EPDM의 전경화 시간과 블렌드 비율에 따른 등방성 MRE와 이방성 MRE의 Shore A 경도 변화를 Table 3에 나타내었다. Table 3에 나타난 바와 같이 전경화된 EPDM을 블렌딩 할 경우 NR 자체의 매트릭스 보다 경도가 증가하는 경향을 확인하였다. 이러한 현상은 전경화된 EPDM상이 NR상과 전단에 의해 두 상의 입자 크기가 감소하고 균일하게 분산됨으로서 계면영역이 많이 존재하게 됨에 따라 나타나는 현상으로 이해된다. NR과 EPDM 블렌드 비율 및 EPDM의 전경화 시간에 따른 경도의 변화는 크지 않았지만 이방성MRE의 경도는 등방성MRE의 경도보다 높은 값을 나타내었다. 이는 Figure 6에 나타낸 바와 같이 시험 방향과 CIP의 배향특성과 연관 지어 설명할 수 있다. 인장 시험과는 다르게 경도 측정의 경우 매트릭스 내 CIP의 배향 방향으로 측정이 이루어지기 때문에 경도가 증가하는 것으로 사료된다. 따라서 CIP의 배향성은 MRE 인장물성의 감소와 경도 증가로 확인할 수 있었다.
Shore A hardness | i-MRE | a-MRE | ||
---|---|---|---|---|
5:5 | 7:3 | 5:5 | 7:3 | |
NR | 52 | 58 | ||
NE0 | 56 | 58 | 59 | 61 |
NE15 | 56 | 57 | 59 | 60 |
NE30 | 57 | 57 | 61 | 61 |
NE45 | 57 | 55 | 61 | 61 |
NE60 | 58 | 56 | 62 | 61 |
NE75 | 58 | 55 | 62 | 62 |
NE90 | 61 | 57 | 63 | 62 |
EPDM | 55 | 61 |
EPDM의 전경화 시간과 NR과 EPDM의 블렌드 비율에 따른 MRE의 노화 특성을 비교하기 위하여 노화 시간을 다르게 하여 실험을 진행하였다. 각 해당하는 인장시편을 24 h, 72 h, 120 h 동안 80°C의 노화 오븐에서 노화를 진행한 뒤 인장 강도를 측정하여 노화가 진행되기 전의 값에 대비하여 감소하는 비율을 비교하였다. 각 조건에 따른 결과를 Figures 8과 9에 나타내었다. NR과 EPDM의 블렌드 비율이 5:5인 MRE의 노화 시간에 따른 인장 물성의 변화를 나타낸 Figure 8을 보면 NR의 경우 모든 노화 시간에서 가장 높은 감소율을 보여 열에 의한 노화 저항성이 가장 낮음을 확인하였다. 이와 반대로 EPDM의 경우는 모든 노화 시간에서 가장 낮은 감소율을 보였기 때문에 열에 의한 노화 저항성이 우수함을 확인하였다. 노화 저항성이 낮은 NR 매트릭스와 노화 저항성이 우수한 EPDM 매트릭스를 블렌드 할 경우 기존 NR 매트릭스가 갖는 노화 저항성 보다 우수한 노화 저항성을 갖는 것을 확인하였다. 더불어 EPDM의 전경화 시간이 증가할수록 블렌드된 매트릭스의 노화 저항성 역시 동시에 증가함을 확인하였다. NR과 EPDM의 블렌드 비율에 따른 MRE의 노화 저항성을 비교하면 상대적으로 노화 저항성이 우수한 EPDM의 블렌드 비율이 높은 5:5의 감소율이 Figure 9에 나타낸 NR/EPDM 비율이 7:3 보다 더 낮음을 확인하였다.
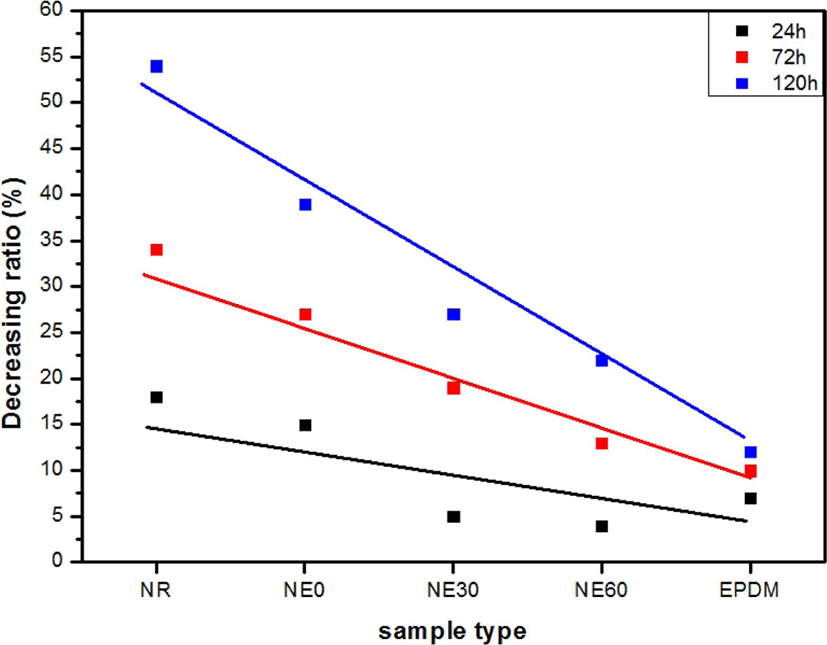
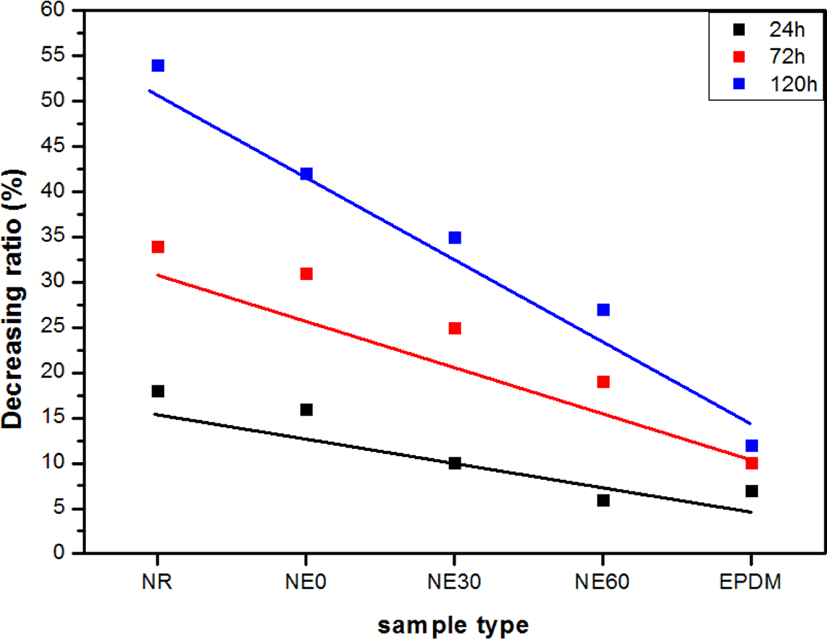
EPDM의 전경화 시간이 MR 효과에 미치는 영향에 관한 연구를 위해 EPDM의 전경화 시간에 따른 NR/EPDM이 5:5인 등방성MRE와 이방성MRE의 전단 저장 모듈러스를 측정하였고 그 결과를 Figure 10에 나타내었다. 전경화가 진행됨에 따라 초기 모듈러스(G0′)와 모듈러스의 변화량(ΔG′)이 모두 상승했는데 이는 전경화를 진행함으로써 매트릭스 내의 가교도가 상승하여 나타난 결과로 사료되며 이러한 모듈러스의 변화는 MR 효과에 큰 영향을 미치게 된다. Figure 10에 나타난 바와 같이 초기 모듈러스의 상승 비율이 모듈러스의 변화량 보다 높기 때문에 EPDM의 전경화 시간이 증가할 경우 MR 효과가 다소 감소하는 경향을 나타내었다. NR과 EPDM의 블렌드 비율이 5:5인 매트릭스의 MR 효과는 Figure 10에 나타낸 바와 같이 전경화가 진행되지 않은 NE0의 등방성MRE와 이방성MRE는 각각 140%와 174%의 MR 효과를 나타내었다. EPDM의 전경화가 진행됨에 따라 MR 효과는 감소하여 60분의 전경화가 진행된 NE60에서는 등방성MRE와 이방성MRE의 MR 효과가 120%와 133%로 감소되었다. 이는 앞서 설명한 매트릭스 내의 가교도 상승으로 설명할 수 있다. 등방성MRE와 이방성MRE의 MR 효과의 차이를 보면 이방성MRE의 MR 효과가 높음을 확인할 수 있다. 이방성MRE는 매트릭스 내 CIP 입자가 외부의 자기장에 의해 배열이 된 상태로 제조가 되었기 때문에 등방성에 비해 자기장에 민감하게 반응하여 MR 효과가 더 우수한 것으로 사료되었다. 매트릭스 내 CIP의 배향이 이루어지면 외부의 자기장을 인가할 경우 사슬구조 내 인접한 CIP는 효율적으로 자기력을 전달하기 때문에 효과적인 MR 효과를 나타내는 것으로 사료된다.
Conclusion
EPDM의 전경화 시간에 따른 NR/EPDM계 MRE의 특성을 조사하기 위해 EPDM의 전경화 시간을 다르게 하여 블렌드 한 이들의 물성을 비교하여 다음과 같은 결론을 얻었다.
-
불포화 정도가 다른 NR과 EPDM을 블렌드 할 경우 상대적으로 불포화 결합이 적게 포함된 EPDM 상의 경화제가 NR 상으로 전이되는 현상을 나타내기 때문에 블렌드 하기 전 EPDM의 전경화가 필요하였다.
-
NR/EPDM계 MRE에서 EPDM의 전경화 시간이 매트릭스의 기계적 물성에 영향을 주었다. EPDM의 전경화 시간이 증가할수록 MRE의 기계적 물성이 향상되었으며 이는 EPDM의 전경화로 인해 최종적인 매트릭스 내 EPDM상의 경화가 충분히 진행되어 최종적인 매트릭스의 기계적 물성이 향상되는 것으로 판단된다.
-
기존의 NR계 MRE와 EPDM이 블렌드 된 NR/EPDM계 MRE를 비교하였을 때 EPDM이 블렌드됨으로써 MRE의 노화저항성이 향상되었고 또한 EPDM의 전경화 시간이 증가할수록 노화저항성이 향상됨을 확인하였다.
-
등방성MRE와 이방성MRE의 기계적 물성을 비교하였을 때 등방성MRE에 비해 이방성MRE의 인장 물성이 낮았는데 이는 이방성MRE의 매트릭스 내에 분산된 CIP의 배향이 인장강도를 측정하는 방향과 수직을 이루고 있기 때문에 나타난 결과로 판단된다. 하지만 경도의 경우 반대 결과로 이방성MRE가 더 높았다. 이는 인장강도와는 반대로 경도의 측정 방향과 CIP의 배향 방향이 같기 때문에 나타난 결과로 사료된다.
-
MR 효과를 비교하였을 때 등방성MRE에 비해 이방성MRE가 더 우수하였다. 이방성MRE의 경우 CIP의 사슬 클러스터 구조가 형성되지 않은 등방성MRE에 비해 밀집된 자성입자 간 자기력이 용이하게 전달될 수 있어 보다 우수한 MR 효과가 나타난 것으로 사료된다. EPDM의 전경화 시간에 따른 MR 효과를 비교하면 전경화 시간의 증가에 따라 MR 효과가 감소하였다. EPDM의 전경화가 진행되면서 매트릭스 내 가교도가 증가하여 초기 모듈러스와 모듈러스의 변화량이 모두 상승하였고 초기 모듈러스의 상승 비율이 모듈러스의 변화량 보다 높기 때문에 나타난 결과로 사료된다.