Introduction
고무는 엔지니어링, 가정용, 스포츠 및 기타 분야 등에 응용되는 바람직한 특징을 갖는다. 엔지니어링 소재로서 고무의 사용은 새로운 것이 아니지만 그 응용은 관련 분야에서 새로운 개발의 도래와 함께 최근에 중요성이 증대하고 있다. 1,2 엔지니어링 응용을 위한 고무물성의 요구는 현실적으로 변하며 물성의 강화는 왕겨재,3 유기물 친화성 clay, 카본블랙, 탄소나노섬유, 나노튜브 등의 첨가에 의하여 성취될 수 있다.2,4 한편 산처리 나노-함수 규산염으로 충진된 PTFE는 베어링과 seal에 고체 윤활제를 적용하는 동안 마모저항이 개선되었 다.5 고무클레이 나노복합재료의 배합과 응용에 있어서 고무의 특성이 향상되는 결과가 보고되었다.6
고무부품의 적정성 여부는 몇 가지 요인들에 의하여 좌우되는데 마찰과 마모는 그 가운데 가장 현저한 요인이며 마모는 다른 범주로 분류된다. 접착과 히스테리시스는 고무마찰의 두가지 주요한 성분인데 접착은 고무와 부드러운 대응부 표면 사이의 고착-미끌림 작용을 책임지며 반면에 히스테리시스는 고무소재의 내부 댐핑 물성과 관련된 현상이다.3,7히스테리시스 또는 내부마찰은 반복된 하중 주기 동안 고무소재 내에서 발생된다. 즉 압축하중의 적용과 뒤이은 하중완화는 반복적으로 계속해서 일어난다.8-10
수송 산업의 성장 및 개발도상국의 경제 발전에 따라 최근 타이어 생산이 기록적으로 증가하였다. 년 생산 기준으로 대략 14억개의 타이어가 전 세계적으로 제조되었다.11 사용기간이 끝나면 대부분의 타이어는 매립지에 폐기되는 데 전 세계적으로 매립지내에 약 40억개의 타이어가 버려지는 것으로 추정된다.12 타이어는 열화에 의한 영향을 받지 않기 때문에 매립지에 폐기된 타이어는 사회경제적 및 환경적인 관심으로 연결된다. 타이어 폐기물의 비상용성의 결과로서 타이어는 큰 용적의 매립지 공간이 요구된다. 게다가 타이어 폐기물은 모기와 설치류의 번식처를 제공한다.13,14 또한 타이어는 화학적으로 가교된 상이한 여러 종류의 고무들과 steel cord, 고분자 섬유, 카본블랙, 기타 유기 및 무기충진재들의 혼련물이다.15
염화부틸고무는 단독으로 또는 천연고무와의 블렌드에 의하여 tubeless 타이어의 inner liner, 타이어 사이드휠 등의 타이어 산업에 널리 이용되고 있다.16,17 부틸고무와 마찬가지로 염화부틸고무는 allylic chloride 성분의 형태로 제한된 수준의 반응성 관능기를 포함하는 포화도가 높은 고분자이다.16 천연고무와 비교하여 염화부틸고무의 낮은 반응성은 가황공정 동안 보다 많은 관리가 요구된다. 그럼에도 불구하고 관능성의 수준은 높은 강도의 가교 망상구조를 제공하기에는 충분하다. 염화부틸고무는 또한 생체의학 응용에 널리 사용되고 있다.18 염화부틸고무로부터 만들어진 물품은 약 150°C에서 압축성형에 의하여 제조된다. 압축몰드에 공급된 재료는 혼련고무, 가교제 및 충진재, 가소제, 가황촉진제 등과 같은 다른 성분들로 이루어지는 데 이 계는 실온에서는 가황하지 않으므로 가교가 일어나기 위해서는 100°C 이상의 온도로 가열해야 한다. 가황하는 동안 재료는 엉켜진 거대분자 사슬로 이루어진 분자량이 큰 중합체로부터 분자량이 무한히 큰 분지형 가교구조로 바뀐다.
Ethylene propylene diene rubber (EPDM)는 다른 범용고무와 비교하여 우수한 내오존성 및 내열성을 갖는 고무로서 주로 알려져 있다. 그리고 우수한 성능에 기인하여 EPDM고무는 자동차, 빌딩 및 건축, 케이블, 와이어, 시트 및 실링재 등에 응용되고 있다.19 비록 EPDM고무는 산소, 오존 및 열 등에 대하여 높은 저항성을 갖지만 미충진된 EPDM고무는 실제로 매우 열악한 성질을 나타내므로 강도를 높이기 위하여 충진재의 도입이 요구된다. 충진재는 보통 생산단가를 낮추고 고무의 성질을 보강하거나 가공을 용이하게 하기 위하여 고무상에 가해진다. 사용되는 모든 충진재 가운데 카본블랙은 높은 보강능력 때문에 보다 많이 알려져 있다. 하지만 다양한 색상의 사용이 제한되고 환경을 오염시킬 가능성이 있어 연구자들로 하여금 보다 친환경적인 다른 흰색 충진재를 발견하도록 촉구한 결과 벤토나이트 및 montmorillonite (MMT) 등의 silicate layer clay가 소개되었다.
본 실험에서는 EPDM고무 함량을 달리하여 CIIR/EPDM blend에 의한 고무가황체를 제조한 후 기계적 물성, 인장 영구변형율, 열전도도, 반발탄성 및 열적 안정성 등의 여러가지 물성을 측정함으로써 가해지는 EPDM고무 함량이 블렌드 가황체의 특성에 미치는 영향에 대하여 검토하였다.
Experimental
CIIR은 Exxon 제품의 CIIR1066 grade 를 사용하였다. EPDM은 디엔 함량이 2.5%인 금호폴리켐 제품의 KEP435 grade를 사용하였다. 활성제로는 산화아연을 사용하였으며, 가교 시스템은 황을 이용한 semi-EV cure system을 사용하였다. 가교촉진제는 N-tert-butyl-2-benzothiazoyl sulfenamide (TBBS)와 dibenzothazyl disulfide (DM)을 함께 사용하였다. 윤활제로서는 스테아린산이 사용되었으며 충진제로는 high abrasion furnace (HAF)와 silica #175를 함께 사용하였으며, silica와 고무결합력 향상을 위하여 가장 널리 사용되는 coupling agent로 silane si69를 사용하였다. 그리고 가소제로는 napthanic oil #3 grade 를 사용하였다.
본 실험에서 이용된 시편은 1차 혼련과 2차 혼련으로 나누어 배합하였다. 1차 혼련에서는 용량 1.6 L Banbury Mixer를 이용하여 초기온도 60°C, 최종온도 90°C를 유지하면서 40 rpm의 속도 조건으로 실험하였다. 고무 소련(mastication)은 1분 동안 행하였으며, 이후 충진제와 약품을 함께 투입하여 5분 간 더 혼련(mixing)한 후, 1차 혼련물은 상온에서 24시간 방치하였다. 2차 혼련은 6″×9″인 open roll 에서 1차 혼련물과 함께 황과 가황촉진제를 넣어 45°C에서 5분간 균일하게 혼련하여 최종 혼련물을 제조하였다. CIIR/EPDM 혼련물의 조성비를 Table 1에 나타내었다. T-1는 CIIR 단독으로 하고 T-2, T-3, T-4 및 T-5는 각각 CIIR/EPDM의 비를 75/25, 50/50, 25/75 및 0/100 wt% 로 하여 혼련시킨 CIIR/EPDM 블렌드계이다. 최종 배합 시편은 rheometer (Monsanto ODR 2000)를 이용하여 ASTM D 20849 에 준하여 180°C에서 가황계를 실험하였으며, Mooney Viscometer (Monsanto MV100)를 이용하여 100°C에서 무니 점도를 조사하였다. 180°C에서 적정 가황시간을 산출하여 hot press 에서 압축성형법으로 시험시편을 제조하여 물성을 측정하였다.
경도는 스프링식 경도계(Shore-A)를 사용하여 측정하였으 며, 노화 전과 노화 후 인장특성은 ASTM D 412에 따라 dumbbell die C 를 사용하여 측정하였다. 노화조건은 125°C 온도하에서 노화시간을 6 시간, 12 시간, 24 시간 동안 행한 후에 실험을 하였다. 실험에서 사용된 tensometer (Instron 3312) 는 25°C 하에서 500 mm/min 의 crosshead 속도와 100 kgf load cell 조건에서 측정하였다.
인장 영구 변형율 시험은 ASTM D 395에 따라 행하였으며, 정적 인장이나 전단력을 받는 부분에서 가황고무의 가열인장에 의하여 잔류줄음율을 측정하였다. 시험편의 두께는 2.0± 0.2 mm, 인장강도 시험용 dumbbell no. 3 시편을 사용하였다. 표선간 거리는 20 mm이며 한쪽을 고정한 후 다른 쪽을 5 mm/sec 속도로 50% 변형을 주고 열처리를 하였다. 열처리는 노화시험기 중에서 70°C에서 24시간과 100°C에서 24시간을 행하고 열처리가 끝난 후 곧 압축장치에서 시험편을 꺼내어 30분간 실온에 방치하여 냉각시켰다. 계산은 다음 식에 따랐다.
여기서 Ls는 인장 영구 변형율(%), l0는 인장 전 표선간 거리(mm), l1은 노화(가열) 후 인장 장치에서 꺼낸 후 30분 경과시의 시험편의 표선간 거리(mm)를 나타낸다.
본 연구에서는 열전도도 측정에 널리 이용되는 비정상 열선법(transient hot wire method)을 이용하여 가황체의 열전도도를 측정하였다. 열전도도 시험기는 Kyoto Electronics 의 QTM-500 model 을 사용하였으며 이 시험기는 0.023~12 W/mK의 측정범위를 가지며, 측정된 값은 다음과 같은 식에 의해 구할 수 있다. 측정의 정확성을 검증하기 위해 표준물질을 대상으로 열전도도를 측정한 후 블렌드 가황체 열전도도 측정을 하였다.
λ=[q·ln(t2/t1)]/[4π(T2-T1)] λ : 열전도도 (W/mK)
q : 열선의 단위 길이당 발열량 (W/m)
t : 측정시간 (sec)
T : t 시간에서의 온도 (K).
Results and Discussion
고무의 경도는 규정 하중하에서 표면이 규정된 크기의 압침(indentor) 또는 침입(penetration)에 저항하는 정도로 정의된다. 경도계는 시험과 동시에 곧장 그 값을 읽을 수 있는 일정한 눈금 값을 가지고 있다. 눈금은 0(아주 부드러운 경우)에서 100(딱딱한 경우)까지 구분되어 있으며 하중은 정하중 및 스프링 형태로 가해진다.
본 실험에서는 CIIR/EPDM 고무 블렌드의 가황체로부터 제작된 시편에 대하여 노화시키지 않은 것과 노화시험을 행한 것들의 물성치를 Table 2에 나타내었다. Figure 1에는 CIIR/EPDM 블렌드계에 있어서 공기중에서의 노화시험을 거치지 않은 시편 및 125°C의 오븐 내에서 노화시간을 달리하여 노화시킨 시편의 경도변화를 나타내었다. 그림으로부터 알 수 있는 것처럼 EPDM 고무의 첨가량이 증가할수록 경도가 증가하는 경향을 보임을 알 수 있다. 여기서 산화는 고온에 의하여 촉진되기 때문에 공기 중의 가열 노화시험에 있어서 온도는 고무의 분해요인(degradation factor) 중의 하나로서 경도에도 영향을 미치게 된다. 한편 고무 혼련물을 성형한 후에 다시 가열하여 고무의 가황반응을 충분하게 완료시키는 후경화(post cure) 공정에 의하여 공기 중의 노화시험에 있어서는 오븐 내에서의 가열 노화시간이 증가할수록 충분한 후경화가 진행되고 결과적으로 고무 시료의 경도가 증가하게 된다.
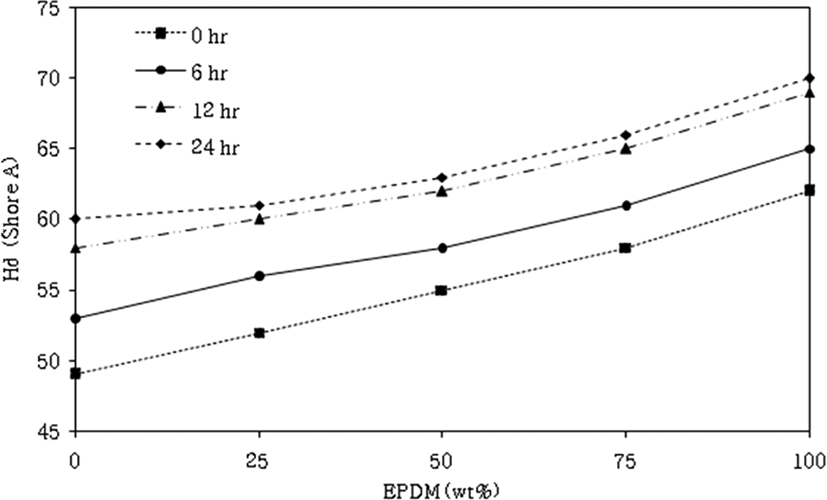
Figure 2에는 노화시키지 않은 혼련물 및 125°C의 오븐에서 6시간, 12시간, 24시간 동안 각각 가열 노화시킨 CIIR/EPDM 블렌드 가황체의 조성비율에 따른 인장강도 변화를 보여주고 있으며, 측정값은 4회 시험한 평균값이다. 첫번째로 가열 노화시키지 않은 CIIR/EPDM 의 조성비율애 따른 인장강도 변화를 보면 CIIR 단독일 때 가장 낮은 값을 보이며 EPDM 함량이 증가함에 따라 인장강도는 증가하는 경향을 보인다. 이러한 특성은 EPDM이 부분적으로 비결정성 구조를 가지기 때문에 상대적으로 결정화가 잘 일어나는 CIIR보다 충진제에 의한 보강효과가 크기 때문으로 판단된다. 전반적으로 노화시간을 달리하여 가열 노화시킨 경우는 가열 노화시키지 않은 시료의 경우와 비슷한 경향을 나타내고 있다. 또한 노화시간이 길어짐에 따라 인장강도 값이 감소함을 알 수 있다.
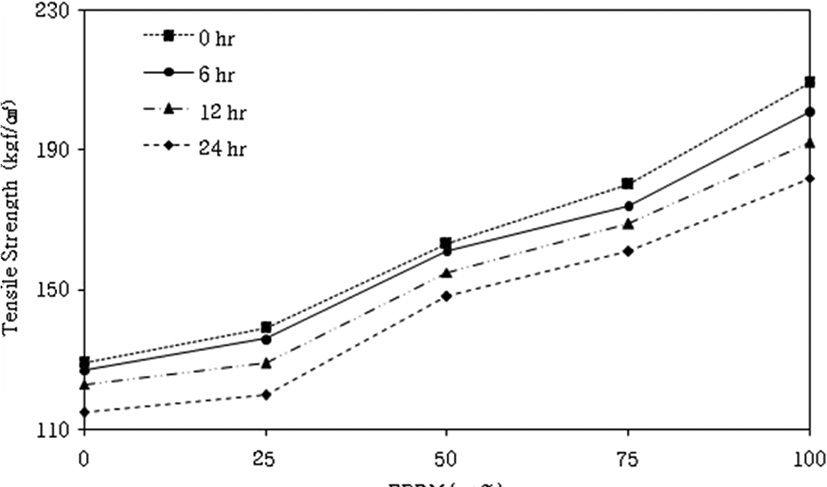
고무는 점탄성 재료로서 지속적인 변형은 어느 정도의 영구변형(set)을 일으키는 데 이것은 변형의 일부는 회복되고 일부는 영구히 유지된다는 의미이다. 영구변형은 변형하중을 제거한 후에 남아있는 변형량으로 정의한다. 본 실험은 CIIR/EPDM 블렌드계에 있어서 EPDM 고무량의 변화에 따른 인장영구변형율의 변화를 Figure 3에 나타내었다. 고무 시편을 정해진 시간동안 인장변형을 주고 고정 시킨 후에 일정한 조건(노화 및 상온)이 지난 다음 시편이 최초의 길이로 회복되지 않는 양을 측정하여 인장 영구 변형율로 표시하고 있다. 공기 중에서의 가열온도가 높아짐에 따라 인장 영구 변형율은 전반적으로 높아지는 경향을 보이는데 이것은 후경화(post-cure)에 따른 경도의 증가 및 탄성의 감소에 기인한 것으로 판단되어진다. 그리고 블렌드 조성비에 있어서 EPDM고무의 함량이 증가함에 따라 인장 영구변형율 또한 증가하고 있음을 알 수 있다. 여기서 이러한 경향을 보이는 이유는 분자의 자유로운 운동의 제한에 따른 탄성의 감소로 인하여 나타나는 현상으로서 CIIR고무 분자 간의 정전기적 인력과 EPDM고무 분자 간의 강한 상호작용에 기인한 것으로 판단된다.
각종 고무의 열전도도는 배합시 투입되는 각각의 배합제에 따라 다르지만 일반적으로 고무는 불량한 열전도체이다. 따라서 이 특성은 진동, 굽힘 또는 마찰 등에 의하여 열이 발생하는 고무부품인 경우 설계자들에게 실제적으로 중요하다. 즉 열을 발산시키도록 설계하는 것이 중요하다. 한편 고무배합물의 열전도도는 미가황 상태로는 두께가 균일하지 않아 측정오차가 크기 때문에 일반적으로 가황한 시편을 사용한다. 본 실험에서는 180°C에서 최적가황시간(t90) 동안 가황 후 실험하였으며, 블렌드 비율 변화에 따른 열전도도 측정결과를 Figure 4에 나타내었다. EPDM 함량 증가에 따른 열전도도는 지속적으로 상승되고 있지만, 그 차이는 아주 근소한 것으로 관찰되었다. 이는 고무가 전기 또는 열에 대한 저항이 매우 커서 전기나 열을 잘 전달하지 못하는 부도체이고, 가황체의 열전달은 가황체내에 존재하는 카본블랙에 의해서 이루어지기 때문이다. 즉 각각의 블렌드 가황체에 들어가는 카본블랙의 양이 동일하므로 열전도도 차이가 거의 나타나지 않았다. 또한 상대적으로 EPDM 고무의 열전도도가 CIIR에 비하여 좋은 것으로 판단된다.
Figure 5에 EPDM 고무량의 증가에 따른 반발탄성 특성을 나타내었다. 고무에 있어서 반발탄성은 일시적으로 고무제품이 변형된 후 빠르게 원래의 형태로 되돌아가는 능력을 뜻하며, 회복정도를 나타내는 압축줄음율과는 달리 회복속력을 의미한다. 고무가 변형을 일으킬 때는 에너지가 가해지게 되고 일부는 고무가 거의 원래의 형태로 되돌아와도 회복되지 못한다. 회복되지 못한 에너지 일부는 고무내에서 열의 형태로 사라진다. 변형이 일어날 때 가해진 초기 에너지 대비 회복에너지의 비율을 그 재료의 탄성이라고 한다. 한번의 충격에 의하여 변형이 일어날 때 회복에너지와 투입에너지 사이의 비율을 반발탄성이라고 일컫는다. 대부분의 고무에서의 반발탄성은 온도에 따라 크게 다르다. 상온에서 각각 다른 고무의 반발탄성은 원료고무와 배합제에 따라 5% 이하로부터 75% 이상까지 다르게 나타난다. 본 실험의 CIIR/EPDM 블렌드에서는 EPDM 함량이 증가함에 따라 반발탄성이 증가하는 경향을 보이고 있다. CIIR 고무는 일반적으로 저반발 탄성체로서 구조상 댐핑 효과가 다른 고무보다 높기 때문에 CIIR 함량 증가에 따라 반발탄성이 낮아지는 것으로 보여진다. CIIR의 낮은 반발탄성은 이소부틸렌에 붙어있는 메틸기의 구조적 입체작용에 따른 것으로, 측쇄에 많은 메틸기들이 전달된 에너지를 많이 흡수하기 때문으로 판단된다. 이러한 반발탄성 저하는 고무자체의 성질로서는 나쁜 성질이지만, 반대로 내진제, 충격흡수제 용도로 적합할 것으로 보여진다.
TGA는 온도변화에 따른 시료의 무게 변화를 측정하여 분석하는 방법으로서 온도-무게 변화량의 곡선으로부터 시료의 열변화 상태를 알고 정성 및 정량분석을 가능하게 한다. 온도-무게 변화량의 곡선은 사용한 시료의 열안정성(thermal stability) 및 물질의 구성비 등을 나타내고, 가열 중에 생긴 중간체의 열적성질도 나타내주며 가열 종료시 남은 잔류체(residue)의 무게비도 알 수 있게 한다. 본 실험에서는 CIIR/EPDM 블렌드 가황체의 열적안정성을 알아보기 위하여 TGA를 이용하여 열분해 온도를 측정하고 그 결과를 Figure 6에 나타내었다. 한편 폴리머의 분해, 주요 사슬의 파괴 및 잔여탄소의 연소에 의해 무게 감량이 발생하며 내열성 측정시 분해가 진행됨에 따라 5%의 무게 감량이 일어나는 온도를 내열성 척도로 간주한다. 그림에서 보여지는 것처럼 300°C 이하에서의 초기 분해온도의 변화는 유기물 영역에서는 일어나지 않았으며, EPDM 양이 증가할수록 분해온도가 증가하고 결과적으로 블렌드 가황체의 고무영역에서의 분해속도가 감소되어 열적안정성이 향상됨을 알 수 있었다. 또한 Figure 7에 나타낸바와 같이 TGA 그래프를 온도에 대한 미분으로 표시한 DTG 그래프에서 EPDM 고무함량이 증가할수록 최대피이크 온도가 높아지는 경향이 보여진다.
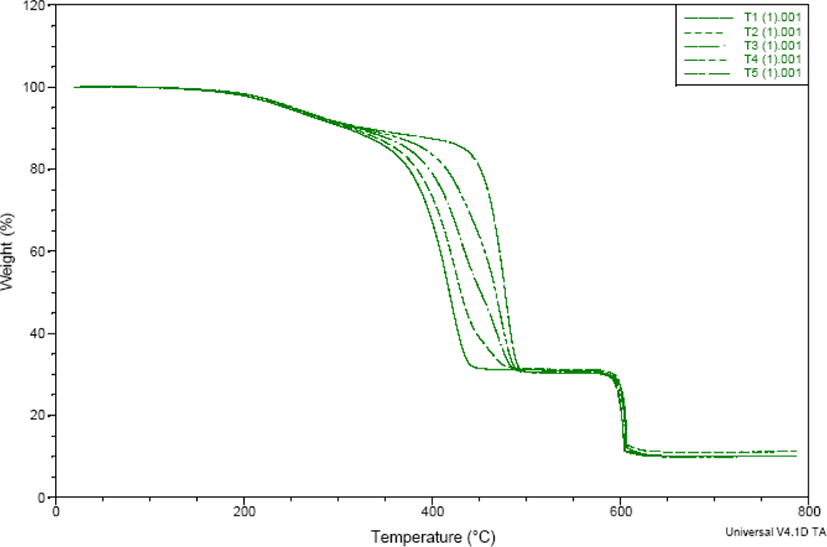
Conclusion
먼저 기계적 혼련방법으로 CIIR과 EPDM을 다른 배합약품들을 함께 polymer blend법에 따라 혼련하였다. Rheometer 등을 이용하여 미가황고무의 경화거동을 분석하였으며, hot press에 의한 압축성형법으로 고무가황체를 제조하여 기계적 물성 등의 여러가지 물성을 측정하였다. 즉 CIIR과 EPDM의 blend에 의한 가황체의 물성을 측정하여 다음과 같은 결과를 얻었다.
-
EPDM 고무의 첨가량이 증가할수록 경도가 증가하는 경향을 보였다.
-
인장강도 변화를 보면 CIIR 단독일때 가장 낮은 값을 보이며 EPDM 함량이 증가함에 따라 인장강도는 증가하였다.
-
EPDM 고무의 함량이 증가함에 따라 인장 영구 변형율 또한 증가하였다.
-
열전도도 특성은 EPDM 함량이 증가함에 따라 선형적으로 증가하였으나 그 차이는 아주 작게 나타났다.
-
CIIR고무는 일반적으로 저반발 탄성체로서 댐핑효과가 높은 데 기인하여 EPDM 함량이 증가함에 따라 반발탄성은 증가하는 경향을 보였다.
-
EPDM 양이 증가할수록 블렌드 가황체의 고무영역에서의 분해속도가 감소되어 열적 안정성이 향상됨을 알 수 있었다.