Introduction
Since the rolling resistance of tread rubber is directly related to the fuel efficiency of cars, the reduction of rolling resistance has become an important research topic to save on fuel consumption as well as to decrease carbon dioxide emissions.1,2 The composition of tread rubber compounds has been optimized to lower rolling resistance and their filler has also been changed from carbon black to silica that can simultaneously improve the wet traction and rolling resistance of styrene butadiene rubber (SBR) compounds.3 The addition of butadiene rubber (BR) to SBR enhances resistance against wear, and thereby silica-filled SBR/BR compounds have widely been used as tread rubber for high performance of tires with better traction, rolling resistance, and abrasion resistance.4
In addition to the enhancement of silica dispersion, the content of silica in tread rubber has been steadily increased to meet strengthening regulations on the fuel efficiency of cars.5Coupling agents that have two different functional groups combining rubber chains and silica particles through covalent bonds are essential in reinforcing the performance of silica.6 The development of many coupling agents involving bis-[(triethoxysilyl)propyl]-tetrasulfide (TESPT) facilitates the manufacture of green tires with low rolling resistance. Furthermore, the treatment of silica surface with coupling agents,7 accelerator,8 antioxidants,9 or networking materials10-12has been tried to enhance the dispersion of silica and to increase the content of silica. However, the increase of silica content in rubber compounds above 100 phr inevitably leads to several disadvantages such as an increase in viscosity, decrease in silica dispersion, and deterioration of their dynamic and abrasive properties. Heavy silica flocculation with the increase in silica content limits its content in rubber, so the content of silica addressed in most papers has dealt with the role and performance of silica as a re-inforcing filler in SBR, and SBR/BR compounds have remained around 80 phr.13-16 Therefore, papers reporting on the effect of silica content in the preparation and properties of silicafilled rubber compounds on a wide range are very rare.
Although the main role of coupling agents is to form covalent bonds between rubber chains and silica particles, the reaction of their alkoxy groups with the hydroxyl groups of silica reduces the attrition between hydrophobic rubber and hydrophilic silica in rubber compounds, significantly reducing their viscosity.6 Furthermore, the decrease in the polar sites of silica suppresses silica flocculation and reduces the disadvantages related to the aggregation and agglomeration of silica particles. The co-addition of a dispersion agent such as zinc 2-ethyl hexanoate (ZEH) to rubber is also effective in improving the dispersion of silica.18 Zinc cations and carboxylate anions of ZEH are strongly adsorbed on the polar sites of silica and suppress its aggregation, improving the dispersion of silica. The small activation energy of the silica flocculation, about 10 kJ·mol−1, suggests the progress of silica flocculation not only in the cure process, but also in the mixing step.15 Therefore, the addition of both coupling and dispersion agents effectively accomplishes the high dispersion and reinforcing performance of silica.
In this study, we prepared three kinds of silica-filled SBR/BR compounds with a wide range of silica content from 50 to 130 phr to systematically investigate the effect of silica content on their states and properties and to deduce the role of coupling and dispersion agents in their preparation and performance. The compounds were classified according to the additives such as TESPT or ZEH: the first compounds were prepared without TESPT and ZEH, the second only with TESPT, and the third with TESPT and ZEH. Using a conventional internal mixer, the maximum silica content in the compounds without TESPT and ZEH was limited to 80 phr, while that in the compounds with TESPT increased up to 110 phr. The further addition of ZEH increased the maximum content of silica to 120 phr. The increase in silica content also caused significant effects on cure, tensile, dynamic, and abrasive properties, while their dependence on silica content varied according to the characteristics of the properties. In addition, the roles of TESPT and ZEH related to the enhancement of rubber properties are discussed.
Experimental
SBR/BR compounds with different contents of silica were prepared using SBR 5251H and BR KBR-01 manufactured by Kumho Petrochemical Co. Ultrasil 7000GR (Evonik) with easy dispersion and high reinforcement was used as a reinforcing filler. TESPT (Dow Corning) and ZEH (Structol) were also used as coupling and dispersion agents, respectively. The compounds were named according to their additive: Compounds without TESPT and ZEH were denoted as “RS-xx,” those with only TESPT as “RS-xx-T,” and those with TESPT and ZEH as “RS-xx-TZ,” where xx indicated the content of silica as phr. The abbreviations R, S, T, and Z represented rubber, silica, TESPT, and ZEH, respectively. A rubber compound (gum) without silica, TESPT and ZEH was prepared and named R-00. Several additives were added for cure and mixing convenience: Insoluble sulfur (S, Miwon Chemical Co.), zinc oxide (ZnO, Daewon Co.), stearic acid (S/A, Duksan Pure Chemical Co.), N-cyclohexyl-2-benzothiazole sulfenamide (CBS, Miwon Chemical Co.), N,N-diphenylguanidine (DPG, Kumho Petrochemical Co.), and TDAE oil (Hansen & Rosental KG).
The content of silica in rubber was increased to the maximum loading to be unable to prepare rubber sheets. Table 1 lists the compositions of the silica-filled SBR/BR compounds prepared.
The rubber compounds were mixed following the procedure summarized in Table 2. An internal mixer (MiraeSI Co.) with a capacity of 300 cm3 was used at a fill factor of 0.70. The total mixing time in the internal mixer was set to 12.5 min. The initial and final masterbatches were finished by further milling in a two-roll mill (C.W. Brabender Inc. Model PM-300, #138-B) to obtain rubber sheets. The rubber compounds were cured at 160°C for 1 min more than t90 time in a cure press (Daekyung Co., DHP-300).
FE-SEM (Hitachi, S-4700) was used in the examination of silica dispersion in the green (uncured) rubber compounds. The green rubber was cut with a sharp knife and its surface was observed. The compositions of silicon and sulfur were estimated with an electron dispersive X-ray analyzer (EDS, Hitachi, EX-200) attached to the FE-SEM.
Thermogravimetric analysis of the silica-filled rubber compounds was carried out using a thermogravimeter (Shimadzu, DTG-60H) in an air flow of 50 ml·min−1. The temperature increased from ambient to 700°C at 5°C ·min−1.
An oscillating disk rheometer (Daekyung Co., DRM-100) was used in recording the rheocurves of the compounds at 160°C, according to ASTM D2084. The times required for the completion of cure to 40% and 90% were measured and designated as t40 and t90 times, respectively. Torque minimum (τmin), torque maximum (τmax), and delta torque (Δτ) of the rubber compounds built up during cure were determined from the rheocurves.
Mooney viscosities of ML (1+4) 100°C of the rubber compounds were obtained with a Mooney viscometer (Daekyung Co., DMV-200C) following the procedure described in ASTM D1646. Scorch times at 125°C were measured by the same viscometer. The lapsed times for the increases of Mooney units by 5 and 35 were defined as t5 and t35, respectively. The hardness was measured with a Shore A durometer following the procedure described in ASTM D2240.
The tensile properties of the rubber compounds were determined from the strain-stress curves of dumbbell type samples. The curves were recorded using a universal tensile tester (Daekyung Co., DUT-500C) at ambient temperature with a cross-head speed of 500 mm·min−1 following the procedure described in ASTM D412. Moduli were defined by the stresses at 50%, 100%, 200% and 300% elongation, while tensile strength and elongation at break were defined as the stress and strain at the break point, respectively.
The storage moduli of the rubber compounds were measured at a frequency of 1 Hz and room temperature using a dynamic mechanical analyzer (TA Inc., DMA Q800). The Payne effect was defined by the difference in the storage moduli between 0.01% and 20% strains. Temperature scans were also run from 80 to 80°C at a heating rate of 5°C·min−1 with a frequency of 10 Hz, amplitude of 10 μm, and force track of 125% to obtain the loss factor (tan δ) of the compounds.
Results and Discussion
The addition of silica to rubber causes significant changes in rubber compounds in terms of shape and properties, especially when its content is high. Figure 1 shows rubber sheets of silica-filled SBR/BR compounds: The left ones are the sheets of compounds with the maximum silica content that could be prepared with the mixing apparatus used in this study, and the right ones are the powders of the compounds that were unable to prepare rubber sheets, even when milling was repeated with the two-roll mill. The state of the rubber sheet with RS-80 was good, but those of RS-110-T and RS-120-TZ were poor, with much unevenness at their edges. The maximum silica content of RS compounds without TESPT and ZEH was 80 phr, while that of RS-T compounds with TESPT increased to 110 phr, indicating the excellent performance of TESPT in en-hancing the dispersion of silica in rubber.13 The fact that the maximum silica content of RS-TZ compounds with TESPT and ZEH increased to 120 phr suggested that ZEH also contributed to the enhancement of silica dispersion in rubber. Although only the addition of ZEH to the compounds without TESPT was also effective in increasing the content of silica (not shown in this paper), much unevenness observed on the compounds decreased the feasibility of its independent use.
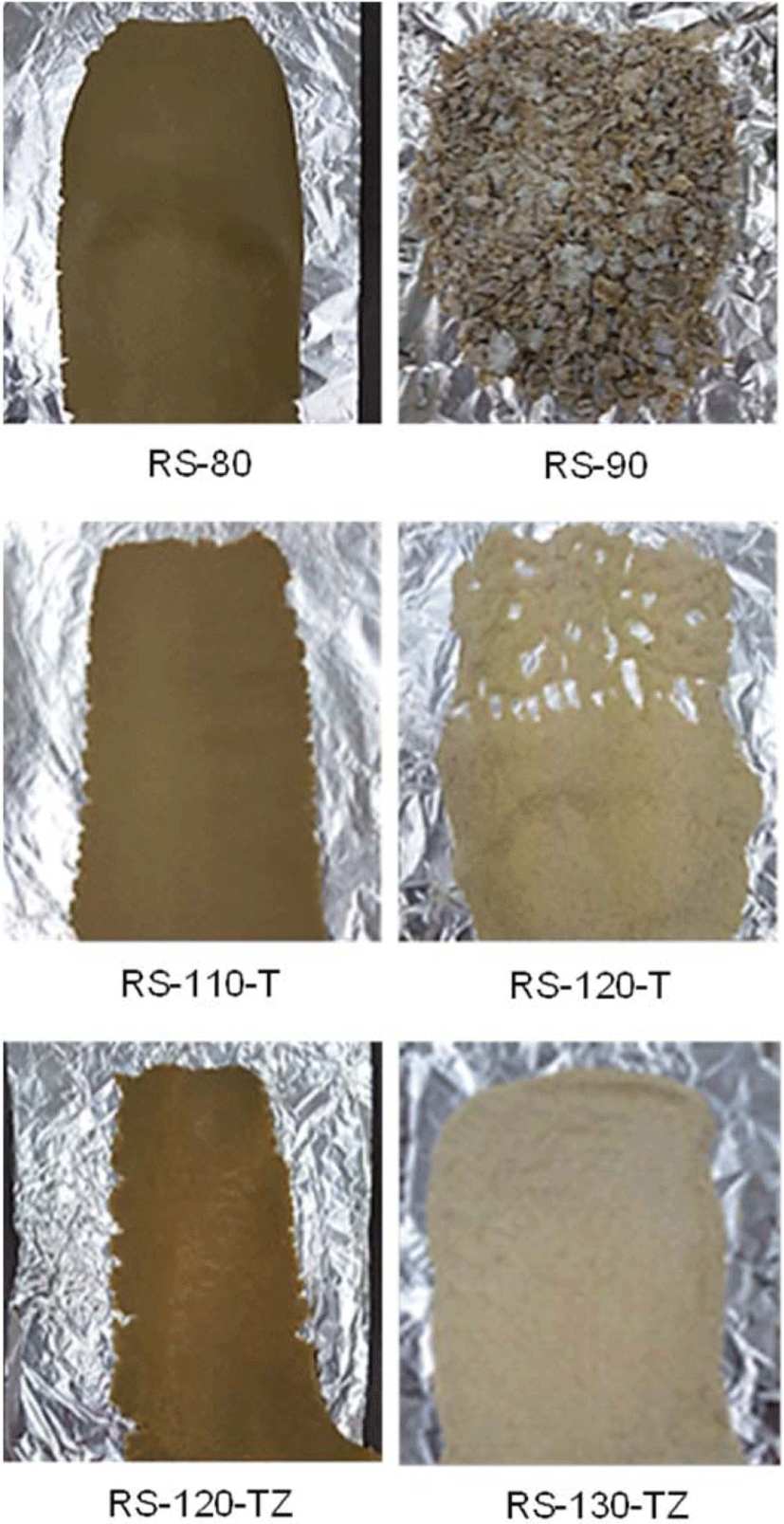
The ethoxy groups of TESPT react with the hydroxyl groups of the silica surface, mask the polar sites of silica, and reduce the attrition between hydrophobic rubber and hydrophilic silica, significantly enhancing the dispersion of silica and increasing the level of silica content in rubber compounds. Since ZEH is a polar material composed of zinc cations and carboxylate anions, ZEH also masks the hydroxyl groups of silica through its adsorption on the polar sites of silica. Furthermore, the hydrophobic moiety of ZEH intrudes into rubber chains and inhibits their strict arrangement or crystallization, which resists the dispersion of silica in rubber. The co-addition of TESPT and ZEH increased the content of silica in silica-filled SBR/BR compounds to 120 phr, but the preparation with extremely high silica content, 130 phr, was not successful with the apparatus used in this study.
Figure 2 shows the SEM images of RS-xx-T samples obtained by cutting with a sharp knife. Due to the severe charging effect of rubber, observation at higher magnification was limited. The moving tracks of rubber due to cutting were observed on RS-60-T, RS-80-T, and RS-100-T, while the surface of RS-120-T was covered with thin rubber layers that were incapable of forming moving tracks. These SEM images indicated the presence of rubber layers with appreciable thickness on the surface of silica particles of the compounds with silica contents less than 100 phr, but the rubber layer of RS-120-T with the highest silica content was very thin. The sulfur content of these samples measured by SEM-EDS decreased with the increase in silica content: 12% for RS-60-T, 9.1% for RS-80-T, 7.0% for RS-100-T, and 5.0% for RS-60-T. Since the content of sulfur corresponded to the amount of rubber, the decrease in sulfur content reflected the decrease in the thickness of the rubber layer that still retained viscoelasticity. The depletion of the rubber layer on silica particles with increasing silica content in rubber weakened the function to form lumps of silica-filled SBR/BR compounds, and thus limited the preparation of rubber sheets.
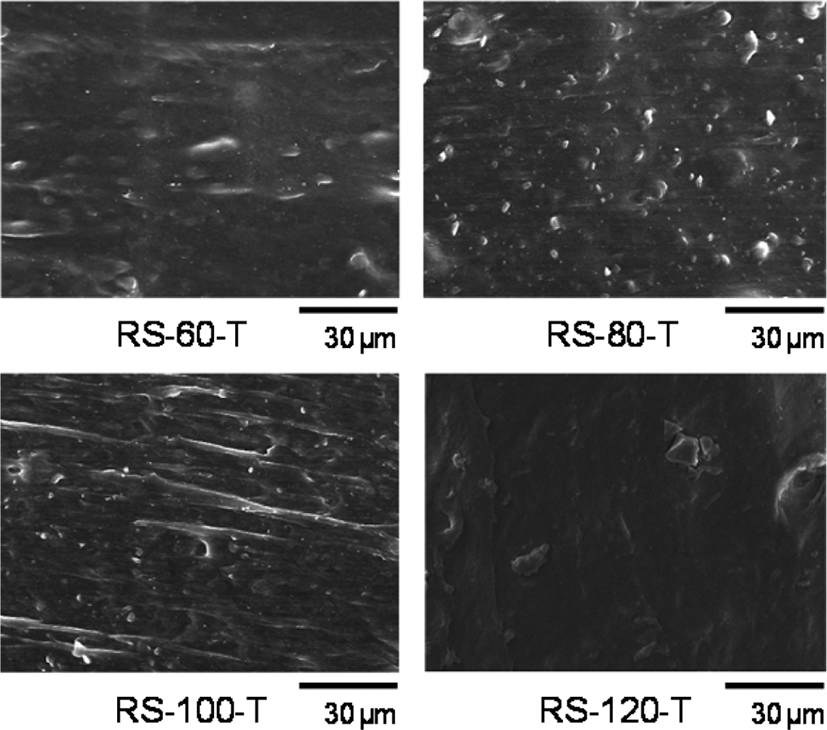
The change in the state of rubber with the addition of silica also caused some differences in TG/DTA curves in terms of the temperature that occurred with weight loss and the heat evolved with the weight loss.19Figure 3 shows TG/DTA curves of RS-xx-T compounds. The weight loss patterns of RS-60-T, RS-80-T, and RS-100-T were very similar to each other. The weight loss below 150°C was attributed to the desorption of water contained in rubber, and the further weight loss at 250-300°C to the removal of organic additives. The combustion of rubber caused a definite weight loss that occurred at 400-520°C and the combustion of rubber followed by its desorption resulted in a very complicated DTA curve. The remain-ing weight above 600°C was assigned to silica and zinc oxide. However, the TG/DTA curve of RS-120-T was considerably different from that of other rubber samples, showing several exothermic peaks at 250-520°C. The sharp exothermic peak observed at 250°C was attributed to the combustion of the organic additives desorbed from thin rubber layers. The depleted rubber layer of RS-120-T could not hold the additives and allowed their rapid desorption, resulting in sharp exothermic peaks at lower temperatures.
The addition of TESPT and ZEH to silica-filled rubber compounds causes a significant effect on their rheocurves because these additives can retard the flocculation of silica by masking the hydroxyl groups of silica. Moreover, the masking of the hydroxyl groups inhibits the adsorption of basic accelerators and the reduction of their actual concentration.20,21Figure 4 shows the rheocurves of R-00 without silica and RS, RS-T, and RS-TZ compounds with silica of 80 phr. The common decreases in torque of these compounds at the beginning of cure were responsible for the increase in temperature, enhancing the mobility of rubber chains. In the rheocurve of R-00, its torque was low in the induction period and increased steeply after 5 min, like an equilibrium rheocurve. However, the addition of silica caused significant changes in the rheocurves in terms of τmin and induction period. The torque of RS-80 without TESPT and ZEH was very high even at the beginning of cure and decreased rapidly. The torque increased inversely after 2 min, so the rapid, continuous increase in torque made it impossible to determine its induction period. Furthermore, the rheocurve of RS-80 was a marching type, being different from the equilibrium type of R-00 due to the steady progress of cure in the rubber intruded in silica agglomerate. The addition of TESPT caused remarkable changes on the rheocurve. The torque of RS-80-T at the beginning of cure was greatly lower than that of RS-80, and the cure was terminated after 20 min. The τmin of RS-80-T was greatly reduced to about half of RS-80 and the maintenance of the low level of torque till 4 min enabled the determination of its induction period. The addition of ZEH accompanied by TESPT also lowered the torque of RS-80-TZ at the beginning of cure and extended the induction period to 7 min. The co-addition of TESPT and ZEH definitely improved the cure properties of the silica-filled SBR/BR compounds by providing lower torque and long induction period to facilitate easy mixing and to ensure high scorch safety.
The considerably high torque of RS-80 at the beginning of cure was due to the silica flocculation that occurred in its mixing stage.15 The steep increase in torque in the early stage of cure also indicated the further flocculation of silica particles in it during cure. In addition to the crosslinking of rubber chains, the aggregation and agglomeration of silica particles also contributed to the increase in torque. The TESPT contained in RS-80-T caused the reaction of its ethoxy groups with the hy-droxyl groups of silica, significantly lowering torque. The addition of ZEH also masked the hydroxyl groups of silica and lowered torque further. Although both TESPT and ZEH commonly improved the cure properties of RS-80-T and RS-80-TZ by suppressing the flocculation of silica particles, the comparison of their performance as the blocking agent of hydroxyl groups may be meaningless because their other functions such as coupling and dispersion contributed to the improvement of cure property in a complicated way.
The presence of silica in rubber additionally causes the formation of new interactions between rubber-silica and silica-silica accompanying the interaction between rubber-rubber, and thus the addition of silica to rubber compounds strongly influ-ences their torques.16Figure 5 shows variations of τmin and τmax of RS, RS-T, and RS-TZ compounds with their silica content. The increase in silica content concomitantly increased the τmin of these compounds, while their degree of increase varied greatly with the added species. The τmin of RS compounds without TESPT and ZEH increased very steeply with the increase in silica content: the τmin of RS-50 was less than 10 dN·m, but that of RS-80 was about 40 dN·m, indicating an increase of τmin by four times as the silica content increased from 50 phr to 80 phr. The τmin of RS-xx-T with TESPT also increased with silica content, while the degree of increase was relatively low when the silica content was less than 90 phr. The degree of increase in the τmin of RS-xx-TZ was lower than that of RS-xx-T, indicating the role of ZEH in preventing silica flocculation in the mixing stage. The fact that the τmin of RS-xx-T increased sharply when silica content was higher than 90 phr indicated that silica flocculation became severe for those with higher silica contents, even though they contained TESPT. On the contrary, the variation of Δτ with silica content was very small compared to those of τmin. Since both the crosslinking of rubber chains and silica flocculation contributed to the increase in torque during cure, the small increase in Δτ for RS-TZ compounds indicated that silica flocculation dependent on silica content was relatively small in them, and thus the increase in Δτ during cure was mainly attributed to the torque increase due to the crosslinking reaction. The relatively high increase in Δτ for RS compounds, on the other hand, reflected the consequence of silica flocculation in them because there was no additive to mask the hydroxyl groups of silica.
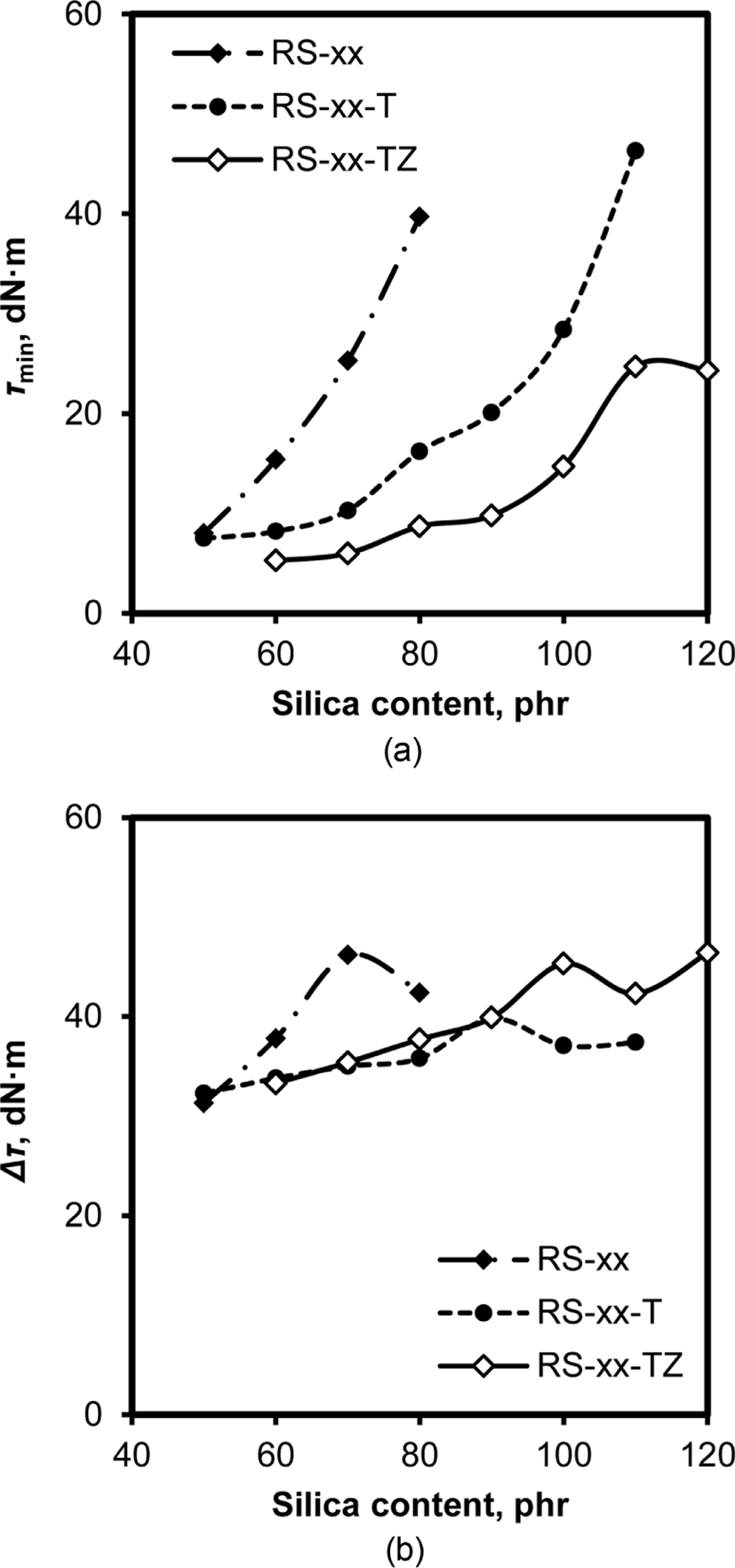
The performance of silica as a reinforcing filler is greatly dependent on its content and dispersion in rubber.22-24 SEM and TEM provide images of silica particles dispersed in rubber, but these techniques are not suitable for the investigation of silica dispersion in rubber compounds with higher silica contents because too closely distributed silica particles obstruct the observation of each particle. In contrast, Lee parameters of rubber compounds determined from their τmin and τmax may be helpful to compare the variation of dispersion with silica content and the effect of the addition of TESPT or ZEH, even though they do not provide the dispersion of silica on a quantitative scale.25,26Figure 6 shows variations of Lee parameter with silica content in RS, RS-T, and RS-TZ compounds. The Lee parameters of these compounds concomitantly increased with their silica content, while the degree of their increases was greatly dependent on the additives. The Lee parameters of RS compounds were higher than those of RS-T and RS-TZ compounds and increased steeply with their silica content. The compounds with TESPT showed relatively small Lee parameters, and the addition of ZEH accompanied by TESPT further lowered Lee parameters. Since a small Lee parameter represents higher dispersion of filler, these results indicated that the dispersion of silica improved by adding TESPT and ZEH. Moreover, the similar variation of Lee parameters of these compounds with silica content to those of τmin also showed that silica flocculation in the mixing stage worked as an important factor determining the dispersion of silica.
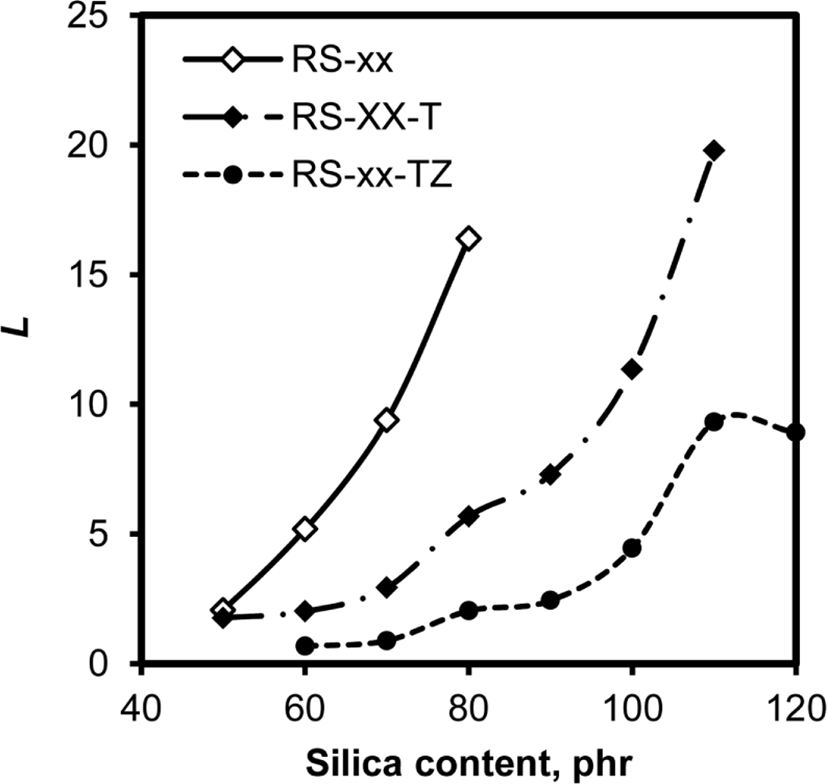
Since TESPT and ZEH can reduce the number of active hydroxyl groups on silica through their reaction or adsorption, they also influence the progress of cure because a part of the basic accelerator, DPG, is inevitably inactivated by adsorption on the hydroxyl groups. Furthermore, the sulfur atoms contained in TESPT increase the actual concentration of sulfur in rubber.21Figure 7 shows the variations of t40 and t90 times with silica content in the cure of RS, RS-T, and RS-TZ compounds. Although the cure rate index is generally used in comparing the effect of curatives or additives on the progress of cure, t40 and t90 times were used in this study because of the steep increase in torque in the early stage of cure and marching type of rhe-ocurve observed for RS compounds. Moreover, the t40 time of these compounds is suitable for a comparison of the induction period, and the t90 time for the total cure rate. The variations of t40 time with silica content for RS, RS-T, and RS-TZ compounds informed two things: The de-crease in t40 time with the increase in silica content in all these compounds and the increase in t40 time following the order of RS < RS-T < RS-TZ. Since the increase in silica content accelerated silica flocculation in the early stage of cure, the increase of t40 time, representing the extension of the induction period, was responsible for the suppression of silica flocculation. The fact that the t40 time of RS-50-T increased to double that of RS-50 with the addition of TESPT indicated that TESPT suppressed the floccu-lation of silica. The further addition of ZEH also extended t40 time, confirming its contribution to the suppression of silica flocculation. The short t40 time for RS compounds without TESPT and ZEH revealed the rapid increase in torque in the early stage of cure due to the severe flocculation of silica particles.
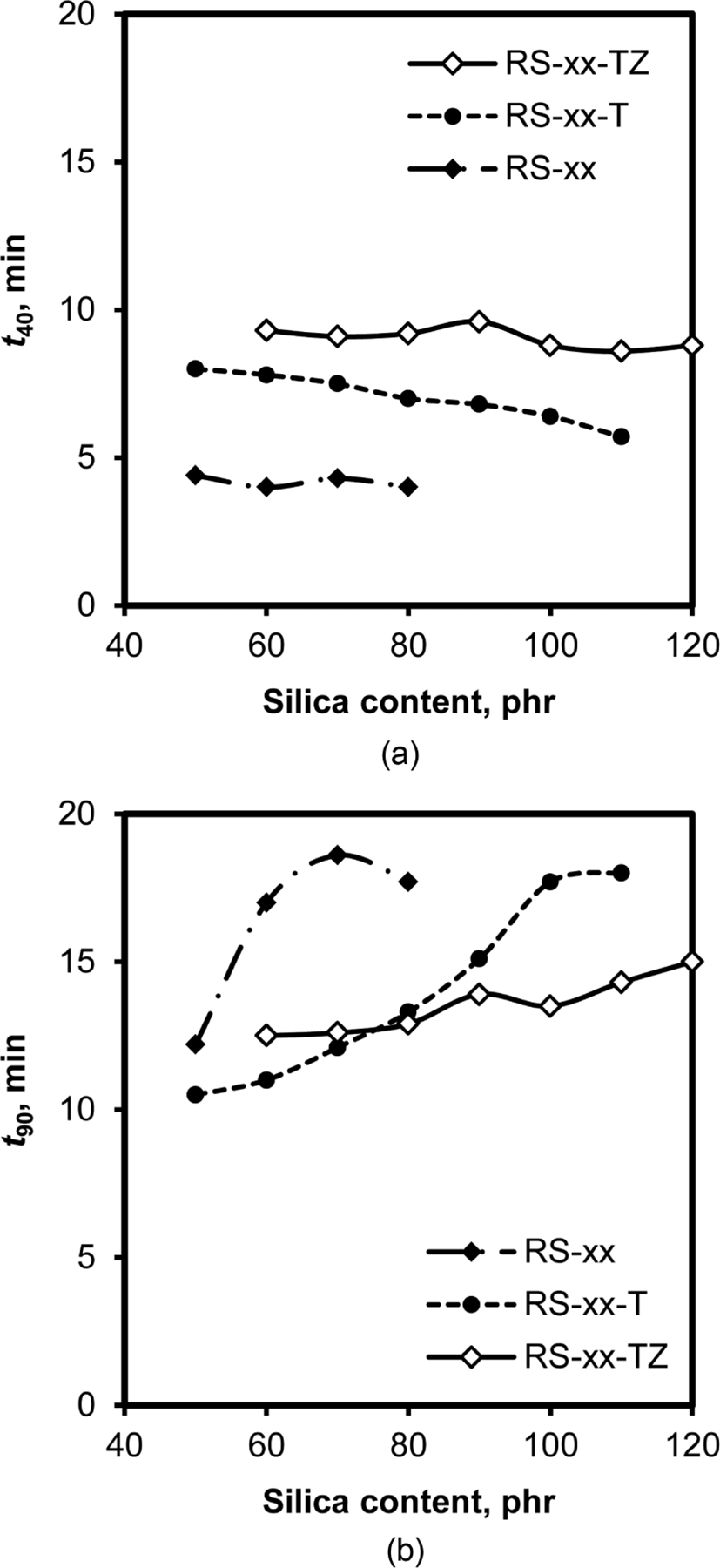
The dosed amount of basic accelerators is usually higher in silica-filled rubber compounds than that essentially required because of their inevitable inactivation through adsorption on silica. As shown in Figure 7(b), the t90 time of RS, RS-T, and RS-TZ compounds increased with the increase in silica content. Since the t90 time corresponds inversely to the cure rate on a total scale, the increase of t90 time of the compounds with the addition of silica reflects a decrease in cure rate, indicating the de-crease of the actual concentration of the basic accelerator, DPG.27 However, the slopes of the increases of t90 time with silica content were considerably different according to the additive. In RS-TZ compounds with TESPT and ZEH, the slope was weak, indicating that the contribution of silica to the inactivation of DPG was negligible because most of the hydroxyl groups located on them were occupied by these additives. On the contrary, the slope of t90 time with silica content was relatively steep for RS compounds without TESPT and ZEH, demon-strating the severe inactivation of DPG by its adsorption on silica.
In order to manufacture perfect tires with a good shape and uniform properties, the scorch time should be ensured to push rubber into the small spaces of molds with complicated shapes.28Figure 8 shows the variations of t5 and t35 times of RS, RS-T, and RS-TZ compounds with silica content. The concomitant decreases in scorch time with the increase in silica content and the increasing order of scorch time following the order of RS < RS-T < RS-TZ clearly confirmed the suppression effect of TESPT and ZEH on silica flocculation in the early stage of cure, as discussed above. Both TESPT and ZEH were effective in enhancing the scorch safety of rubber compounds, and thereby the co-addition of these materials was more effective to guarantee sufficient scorch time. However, higher contents of silica above 100 phr greatly shortened both t5 and t35 scorch times, even though the compounds contained TESPT and ZEH.
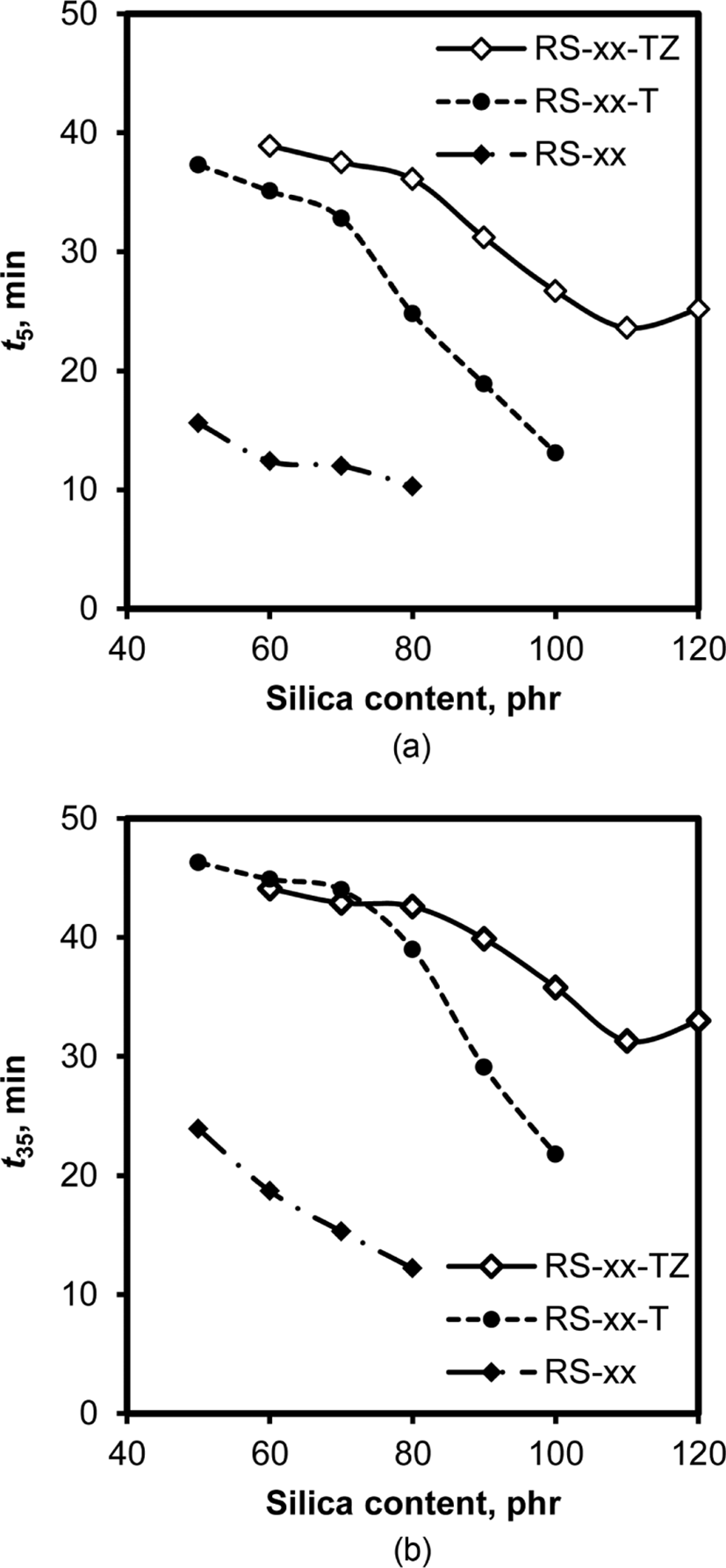
The addition of silica to rubber compounds usually increases their viscosity because the hydrophilic surface of silica can-not be wetted by hydrophobic rubber chains.6Figure 9 shows the variations of Mooney viscosity and Payne effect of RS, RS-T, and RS-TZ compounds with their silica content. Mooney viscosity and Payne effect reflect different properties of rubber, but their similar trends in terms of dependence on silica content and the contribution of TESPT and ZEH to them suggested that these two properties were mainly attributed to the same change that occurred in rubber. As expected, the vis-cosity of all the compounds increased with silica content (Figure 9(a)), because the interfacial area between the hydrophobic rubber and hydrophilic silica must be increased. The effect of the addition of TESPT and ZEH on viscosity was definite: The viscosity of RS-T compounds with TESPT was much lower than that of RS compounds when their silica contents were the same. The addition of ZEH accompanied by TESPT further lowered the viscosity of RS-TZ compounds, but the effect of lowering viscosity by ZEH was greater for RS-TZ with silica content above 90 phr. Since most of the hydroxyl groups of sili-ca were masked by TESPT, the effect of ZEH addition became distinct when the silica content was very high.
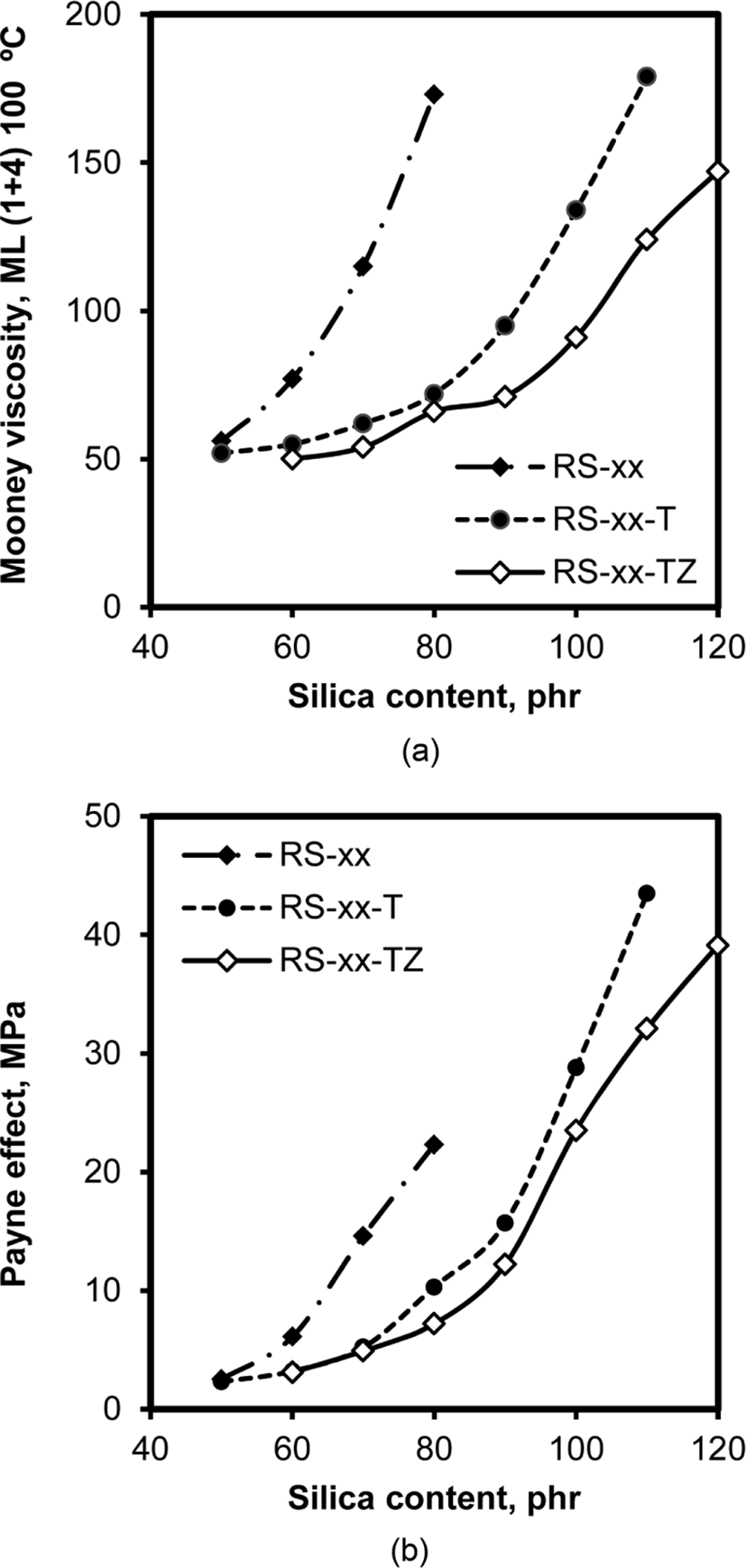
Since the Payne effect is the difference of the storage moduli at low and medium strains, it corresponds to the extent of silica flocculation in rubber.28 The variations of Payne effect of the silica-filled compounds with silica content, shown in Figure 9(b), were astoundingly similar to those of Mooney viscosity, indicating that both viscosity and Payne effect were highly dependent on silica flocculation. The blockage of hydroxyl groups by TESPT suppressed the aggregation of silica particles, resulting in a small Payne effect. Although the further addition of ZEH was effective in reducing the Payne effect for RS-TZ compounds, the small differences in the Payne effect between RS-T and RS-TZ suggested that TESPT was more effective in reducing viscosity and Payne effect than ZEH.
Since the coupling agents including TESPT combine silica particles with rubber chains through covalent bonds, the addition of coupling agents to silica-filled rubber compounds significantly increases their modulus.29 In contrast, the addition of ZEH does not cause any contribution to modulus because it has no function to form chemical bonds. Figure 10 shows the variations of M-300% and hardness of RS, RS-T, and RS-TZ compounds. The M-300% of all the compounds increased proportionally with the increase in silica content, accompanying the increases of moduli at 50%, 100%, and 200% (not shown). Since the modulus is strongly dependent on the interaction between rubber and silica,30 an increase in the interaction due to the increase in silica content should increase the moduli of silicafilled SBR/BR compounds. The lower M-300% of RS compounds than those of RS-T and RS-TZ compounds by about 2 MPa indicated that the formation of coupling bonds between rubber chains and silica particles contributed to the increase in moduli. However, the further addi-tion of ZEH did not cause any change in modulus, confirming that ZEH did not participate in the coupling reaction between rubber chains and silica particles. TESPT contributed to the formation of the covalent bonds between rubber chains and silica particles, resulting in the increase in modulus, while ZEH did not contribute to any enhancement of modulus.
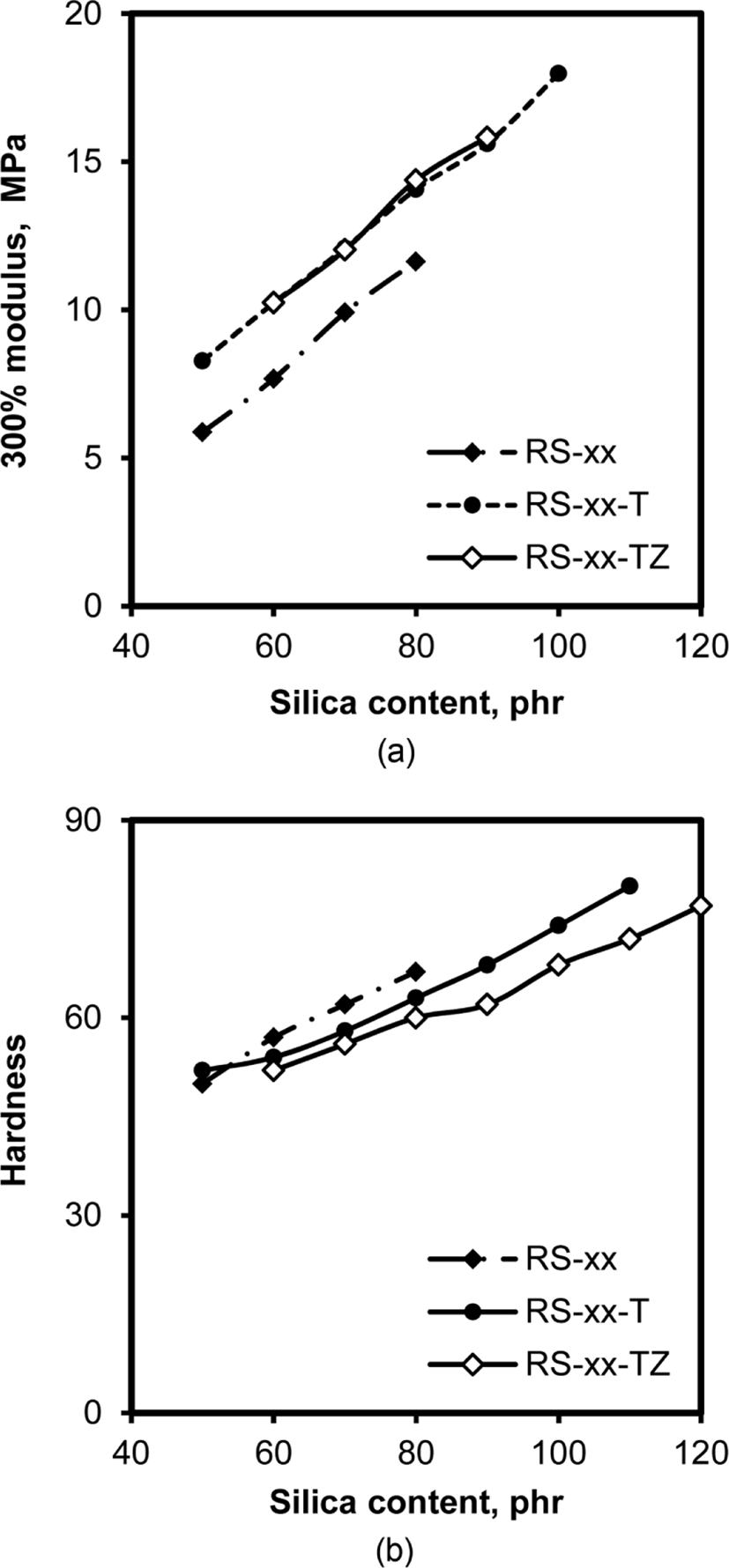
The increase in silica content also proportionally increased the hardness of RS, RS-T, and RS-TZ compounds, indicating that the amount of silica in rubber was important in determining their hardness. The high dispersion of silica without forming large silica aggregates in RS-T and RS-TZ compounds due to the addition to TESPT and ZEH caused slightly low hardness compared to that of RS compounds.
The fatigue of rubber compounds is a complex phenomenon related to many factors such as the generation and propagation of cracks, the deformation due to stress given, and the homogeneity of rubber properties.31 Tensile strength, de-fined as the maximum stress at break point, usually represents the resistance to extension, while DIN abrasion, measured as the loss of rubber under dynamic attrition, is related to both the strength of the rubber itself and its resistance to external force. Figure 11 shows the variations of the tensile strength and DIN abrasion of RS, RS-T, and RS-TZ compounds with their silica content. At lower silica contents of the compounds less than 70 phr, the increase in the content of silica concomitantly increased their tensile strength, but the further increase in silica content caused decreases in the tensile strength of all the compounds, though the degree of decrease varied slightly with the presence of TESPT and ZEH. The increase in the interaction between silica and rubber with the increase in silica content was responsible for the increase in the tensile strength of the compounds, while the high abundance of facile silica aggregates in the compounds with higher silica content lowered their tensile strength. The presence of coupling bonds between silica particles and rubber chains combined by TESPT suppressed the breakage of rubber compounds, and thus the tensile strength of RS-T and RS-TZ compounds remained high even with higher silica contents. On the contrary, the increase in silica content caused opposite trends of DIN abrasion. The increase in the silica content of all the compounds decreased abrasion loss for the compounds with silica content less than 70 phr. However, the further increase in silica content caused an increase in abrasion loss. The opposite trends of DIN abrasion loss with silica content could be explained by the variation of tensile strength with silica content: the increase of the interface between silica and rubber strengthened the resistance to abrasion, while the further increase in facile silica aggregates in rubber weakened the resistance against the fatigue of rubber. The smaller abrasion loss of RS-TZ than that of RS-T compounds with higher silica contents might be due to the enhancement of the homogeneity of rubber with the addition of ZEH.
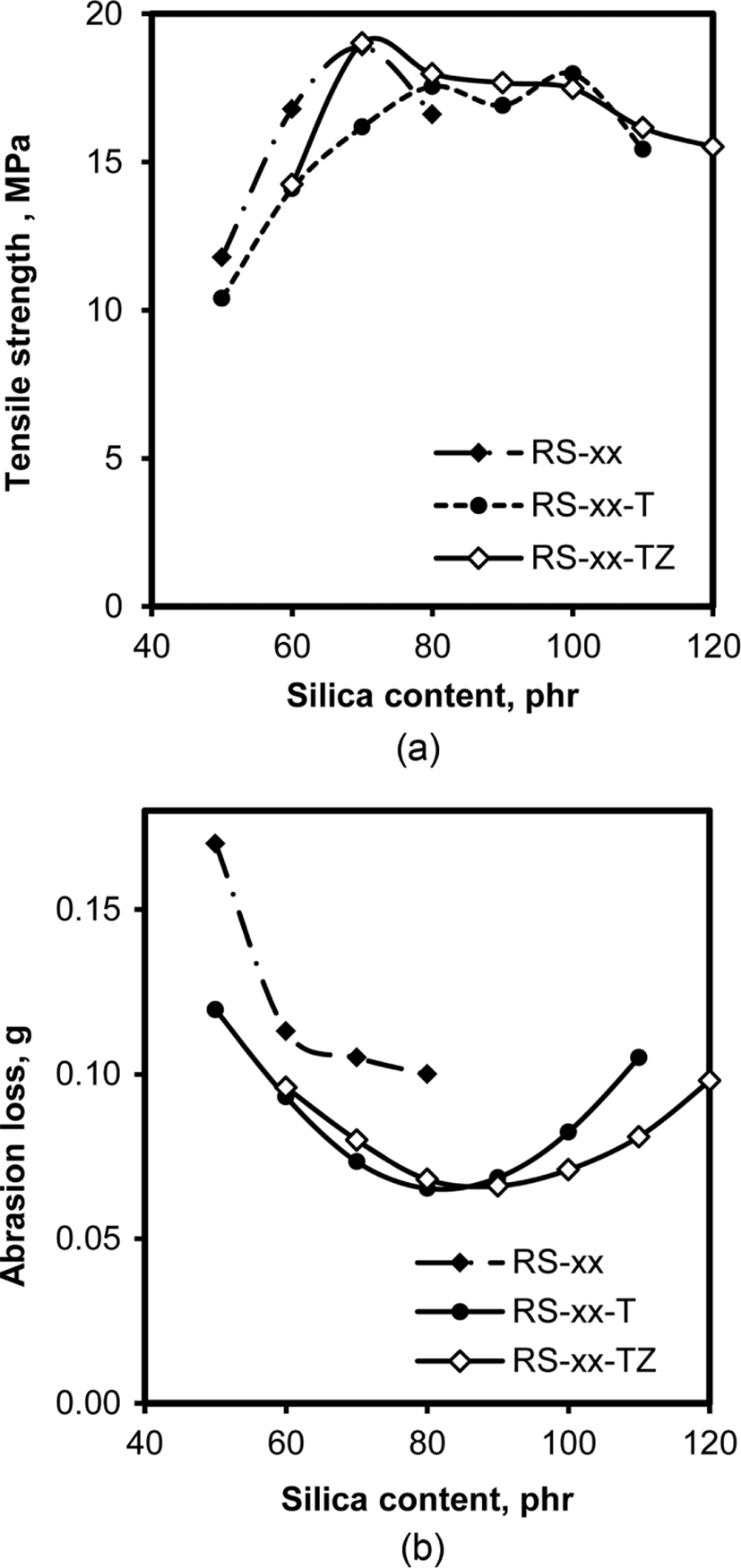
The dynamic properties of rubber compounds such as wet traction and rolling resistance have become the most important properties determining the performance of passenger car tires in a tire labeling system.32 Since the determination of these properties in a laboratory system is not easy, tan δ values at 0°C and 60°C have been conventionally used to represent the wet traction and rolling resistance of rubber compounds, respectively.33Figure 12 shows the variations of tan δ at 0°C and 60°C with the silica content of RS, RS-T, and RS-TZ compounds. The tan δ at 0°C concomitantly decreased with the increase in silica content in all the compounds, which definitely illustrated that the addition of silica was not effective in improving wet traction. The increase in the moduli of these rubber compounds with the increase in silica content usually retarded rapid energy dissipation under dynamic deformation, and heterogeneity due to the presence of silica moieties might weaken the adherence of rubber to the road surface. However, the decreasing degree of tan δ at 0°C with the increase in silica content became lower with the addition of TESPT and ZEH. The RS-T compounds that contained TESPT maintained higher values of tan δ at 0°C than RS compounds without TESPT and ZEH, indicating that the enhancement of resistance to fatigue and the suppression of the formation of facile silica aggregates by TESPT enhanced the wet traction of those compounds. The further addition of ZEH accompanied by TESPT in RS-TZ compounds effectively improved wet traction by improving the homogeneity of the compounds and suppressing silica flocculation.
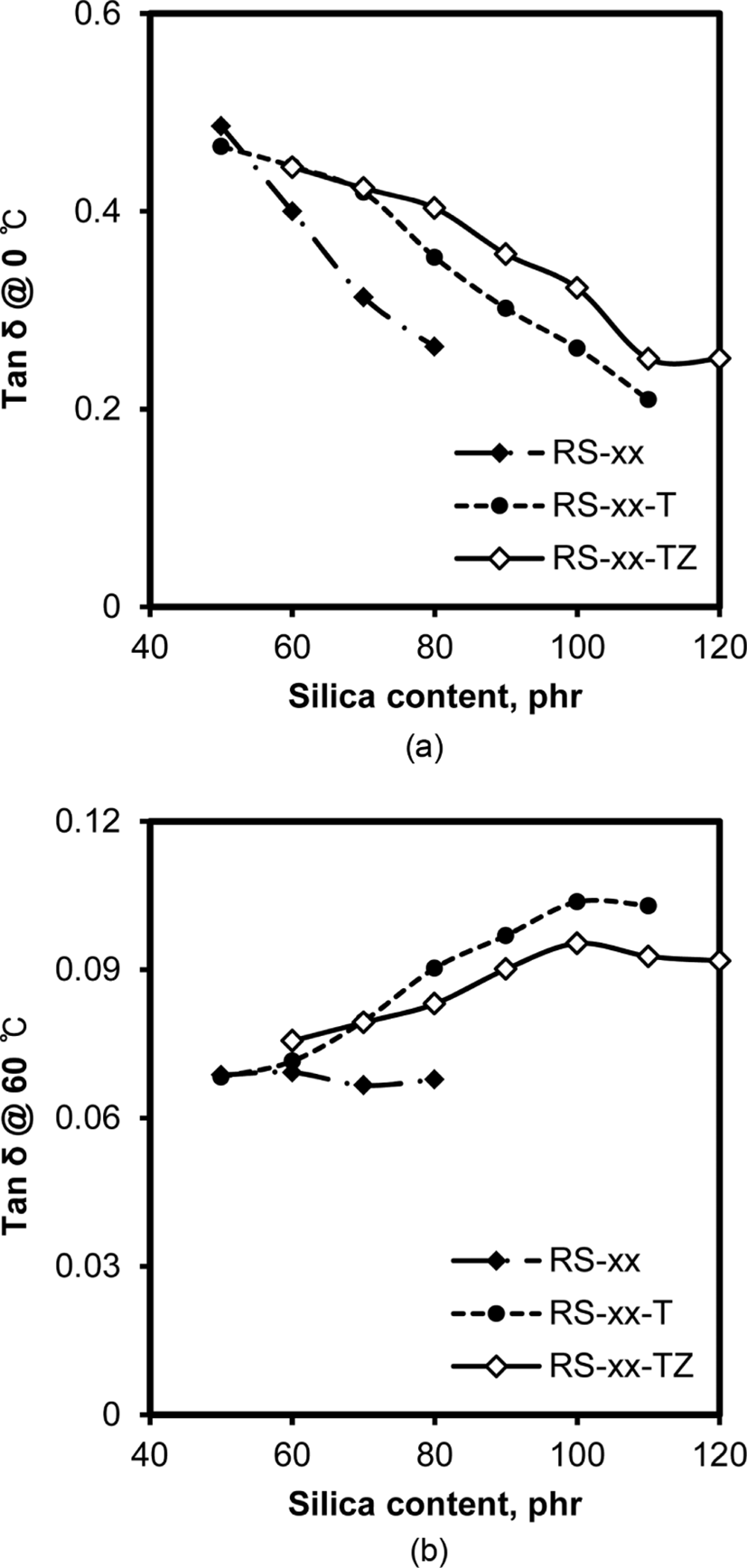
The variations of tan δ at 60°C of RS, RS-T, and RS-TZ compounds with silica content was considerably different from those of tan δ at 0°C. The tan δ at 60°C of RS compounds without TESPT and ZEH were almost constant regardless of their silica content. Since the irreversible deformation of rubber due to the free motion of rubber chains causes rolling resistance, the high attrition between hydrophobic rubber chains and hydrophilic silica particles of RS compounds strictly restricted free motion and maintained low rolling resistance.34 However, tan δ at 60°C of RS-T and RS-TZ compounds increased with their silica content. The blockage of hydroxyl groups of silica with the addition of TESPT and ZEH lowered the attrition between silica and rubber, allowing the free motion of rubber chains and increasing their rolling resistance. The increase in the amount of silica aggregates in rubber with increasing silica content caused their irreversible breakage under dynamic stress, also increasing rolling resistance, so the addition of ZEH accompanied by TESPT was effective in lowering the rolling resistance of RS-TZ compared with RS-T compounds. The enhancement of the homogeneity of rubber compounds and the suppression of silica flocculation by ZEH might contribute to this improvement.
The hysteresis behavior of silica-filled rubber compounds can be deduced from their variation of loss modulus with strain, because the integral value of loss modulus corresponds to the heat evolution during dynamic deformation.35,36Figure 13 shows the loss modulus profiles of RS-, RS-T, and RS-TZ compounds with different silica contents. Generally, the loss modulus of a rubber compound was low in a low strain region, while it increased with the increase in strain in the range from 0.01 to 1% and decreased at higher strains above 1%. The loss modulus of RS compounds with lower silica contents less than 60 phr was low, while that of RS-80 was above 2.5 MPa at 0.01% strain and increased to about 3 MPa at around 1% strain. In constant, the loss modulus of RS-80-T with TESPT was about 1 MPa at 0.01% strain and increased to about 1.5 MPa at around 1% strain, indicating a considerable reduction of the loss modulus for RS-T compared to that of RS compounds. However, the increase in the silica content of RS-T compounds to 100 phr caused high loss modulus of about 5 MPa at 0.8% strain, indicating that the loss modulus of the silica-filled SBR/BR compounds highly increased with the increase in silica content. The RS-TZ compounds with TESPT and ZEH showed lower loss modulus than RS and RS-T compounds with the same silica content, but the loss modulus of RS-120-TZ with extremely high silica content reached 6 MPa at 0.8% strain. These results indicated that the loss modulus that caused rolling resistance was a function of silica content and the addition of TESPT and ZEH was very effective in reducing it. On contrary, higher silica content above 100 phr caused a considerable increase in loss modulus, even if the rubber compounds contained TESPT or ZEH. These additives were very effective in reducing the loss modulus of the SBR/BR compounds with silica contents less than 90 phr, but additives had a certain limit to suppress silica flocculation, and therefore they could not prevent the increase in loss modulus with higher silica contents above 100 phr.
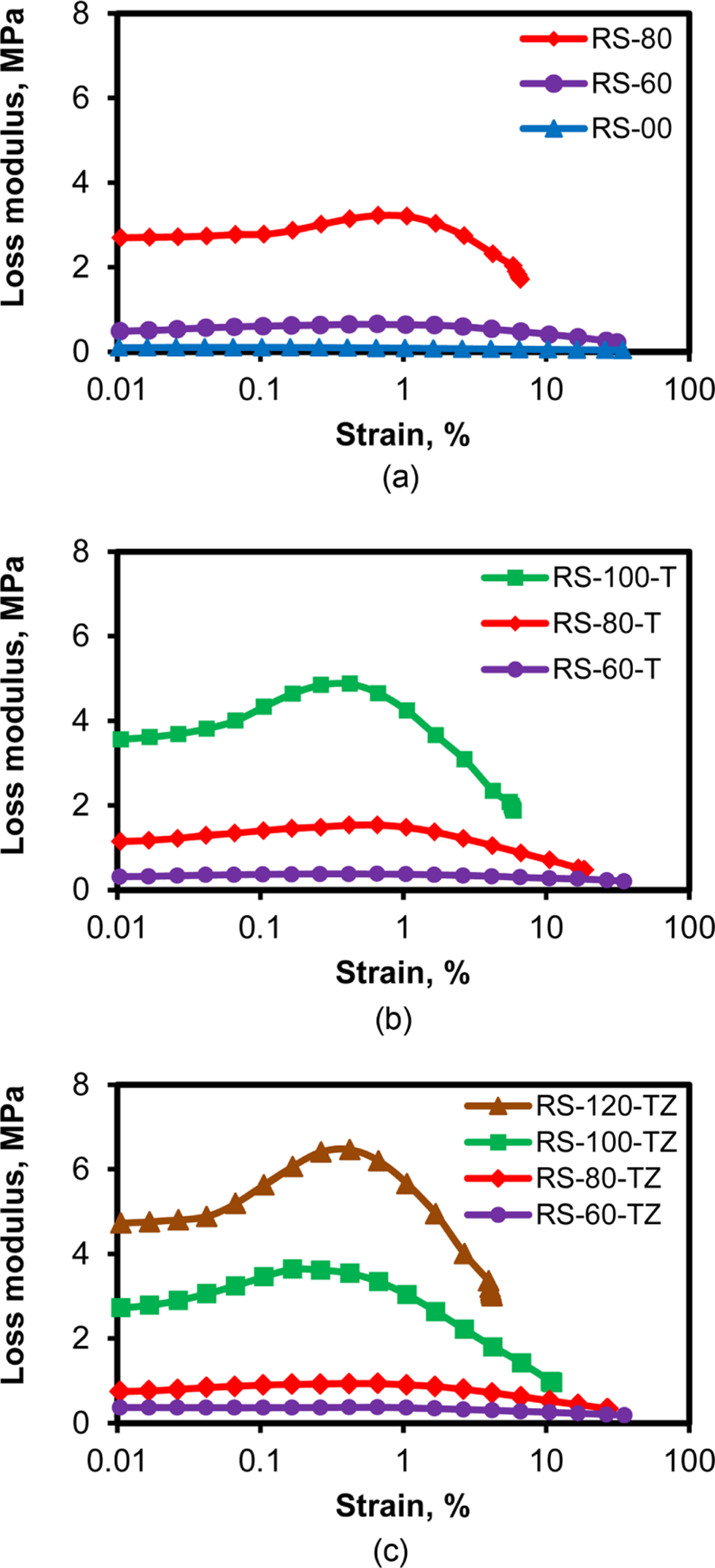
If silica flocculation and its suppression by TESPT and ZEH play the main roles in determining the properties of silica-filled SBR/BR compounds, the dependences of these properties on these causes can be deduced from the relationships. Figure 14 shows four relationships between the properties. The high positive relationship between τmin and Mooney viscosity implied that the viscosity of the compounds was predominantly determined by silica flocculation in the mixing stage. The Payne effect of the compounds increased linearly with the increase in Mooney viscosity, confirming the importance of silica flocculation in the mixing stage in determining τmin, Mooney viscosity, and Payne effect. The slightly weak relationship between Mooney viscosity and Payne effect meant that silica flocculation during cure also contributed to the determination of Payne effect. The weak positive relationship between hardness and M-300% suggested the participation of other factors in addition to modulus in the determination of hardness. Since M-300% increased linearly with the content of silica, the involvement of the fatigue property of the compounds in determining hard-ness weakened the relationship between hardness and modulus. The negative relationship between T.S. and DIN abrasion indicated that high tensile strength was necessary in improving DIN abrasion because high resistance against abrasion loss was primarily attributed to tensile strength. However, the weak relationship inferred that other properties such as the hetero-geneity and intermittence of surface property due to the presence of silica were strongly involved in the determination of abrasion. Although the presence of TESPT and ZEH also influenced the slopes of these relationships, the discussion on them was not tried in this paper. In summary, silica flocculation and its suppression with the addition of TESPT and ZEH work as important factors in determining the properties of the silica-filled SBR/BR compounds, but the contribution of other factors caused by the addition of silica should not be neglected in a discussion of the properties of silica-filled SBR/BR compounds.
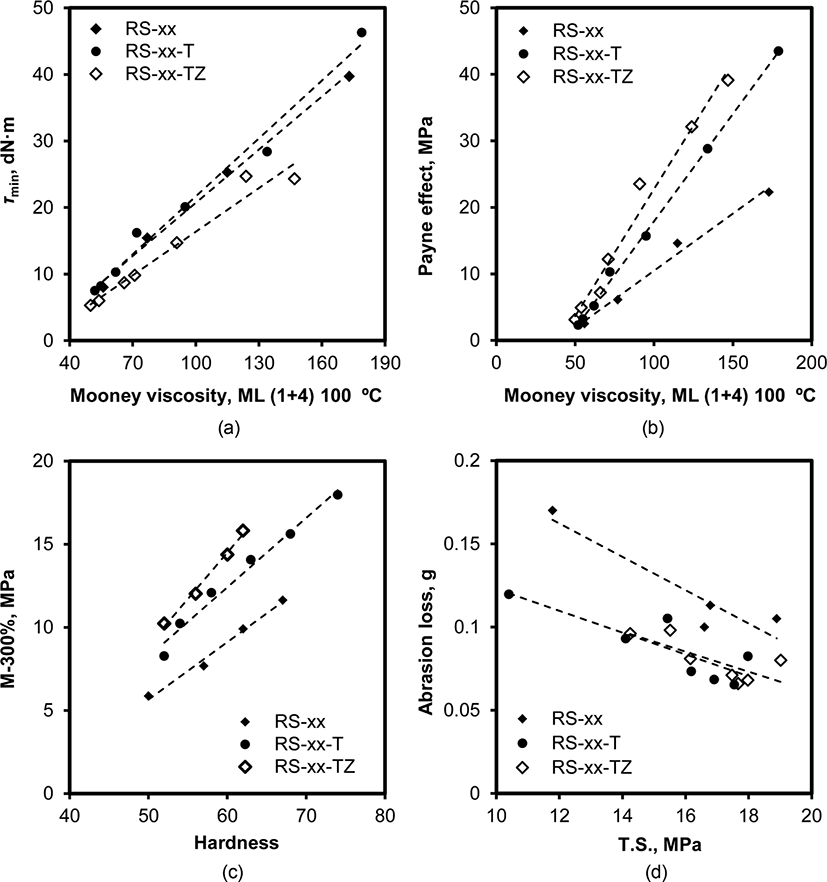
Conclusions
The performance of silica as a reinforcing filler was enhanced by the increase in silica content when its dispersion was preserved sufficiently high. Although the SBR/BR compounds reinforced with silica without any coupling and dispersion agents showed poor cure, viscosity, mechanical strength, and dynamic properties, these properties significantly improved with the addition of TESPT and ZEH: The silica content could be increased to 120 phr, the modulus at 300% doubled, and the DIN abrasion loss reduced to about half for the compounds with TESPT and ZEH. The wet traction of these compounds de-creased with the increase in silica content, while the addition of TESPT and ZEH was helpful in maintaining high wet traction. The deterioration of the rubber properties with increasing silica content was mainly due to the increase of silica flocculation in rubber, and the suppression of silica flocculation with the addition of TESPT and ZEH significantly enhanced these properties. The coupling function of TESPT greatly masked the polar sites of silica and strengthened the interaction between rubber and silica, achieving high performance for silica-filled SBR/BR compounds. Although ZEH had no coupling function, the masking of polar sites through its adsorption and the improvement of homogeneity due to its dispersing function also facilitated the increase in silica content and resulted in better cure and abrasion properties when ZEH was co-added with TESPT. The variations in rubber properties with silica content could be practically explained by the increase in interactions between rubber and silica and by deterioration due to silica flocculation in rubber.