Introduction
As one kind of one-dimensional nanomaterial, carbon nano tube (CNT) is featured with outstanding elasticity modulus and tensile strength, preferable flexibility, small diameter and large aspect ratio, good chemical stability, electrical conductivity and thermostability etc.1,2 Hence, CNT have a bright furture in nanocomposites such as polymers, ceramics, metal and biomaterials etc.2-7 However, due to the strong π-π interaction between CNT, CNT can form a strong aggregation structure in matrix and difficult to disentangle and disperse in the polyolefin matrix.8,9 Currently, lots of methods have been proposed to improve the CNT based nancomposites uniformly, such as solution mixing, emulsion mixing, melt blending and in-situ polymerization blending.10,11 Stemming from polymerization-filling technique (PFT),12,13 in-situ polymerization method seems to be an ideal way to realize the dispersion of fillers in polyolefin, which producing supported catalyst by loading catalyst on the surface of fillers and letting the resultant catalyst react with monomers.14-16 Wang et al. prepared nanocomposite of Nylon-6 by in situ ring-opening polymerization have improved thermal and mechanical properties.17 Zhang et al. applied reduced graphene oxide (rGO) supported MAO catalyst and graphene/MgCl2 supported Ti-based Ziegler-Natta catalysts for vinyl polymerization and got significant improvement in mechanical properties and thermal stability of the nanocomposites.18-20
Various catalysts have been reported for the polymerization of isoprene, but the polymer are mainly cis 1,4-polyisoprene or 3,4-polyisoprene, and rarely have isospecific trans 1,4-selectivity.21,22 Trans 1,4-polyisoprene (TPI) can be crystallized at room temperature because of high a regularity of main molecular chains.23 Due to the unsaturated double bonds, it shows rubbery state after the vulcanization.24,25 Consequently, TPI possess shape memory capability, excellent dynamic fatigue resistance capability, abrasive resistance capability etc. TPI is suitbale to be used in formulation of shape memory materials, damping product, tyre treads, toothpaste, medical splint, golf cover, etc.26,27
However, seldom researches introduce nanomaterials in polyisoprene through in-situ polymerization method. In the present research, CNT/MgCl2 was used as composite support and high energy ball milling method was used to in situ load Ziegler-Natta catalyst, which was further used to synthesize TPI/CNT nanocomposite. Generally speaking, the CNT composite prepared through in situ polymerization, the intermolecular interaction in CNT can be effectively weaken due to the coating effect of the molecular chains of polyisoprene to CNT, which can well prevent CNT from forming strong aggregation structure and realize the good dispersion of CNT. The CNT with the coverage of polyisoprene on the surface can well disperse in polyisoprene rubber matrix. The present research succeeded in synthesizing polyisoprene/single-walled carbon nanotube nanocomposite with CNT/MgCl2 supported Ziegler-Natta catalyst, as well as a preliminary exploration of the polymerization behaviors and thermal stability properties of the nanocomposite.
Experimental
Hydroxylated carbon nanotubes (CNTOH) (outer diameter (OD) around 8 nm, inner diameter (ID): 2-5 nm, length: 10-30 μm) and large inner diameters carbon nanotubes (CNTL) were provided by Chengdu Organic Chemistry Co., Ltd., China. Anhydrous magnesium chloride (purity, 98%), titanium tetrachloride (purity, 99%), and isoprene (purity, 99%) were procured from Sigma-Aldrich, China. Triisobutylaluminum (TIBA) (purity, 98%) was obtained from Akzonobel, USA.
This section was designed to utilize ball milling to prepare the CNTOH/MgCl2/TiCl4 catalyst/CNTL/MgCl2/TiCl4 catalyst with well dispersed CNTOH/CNTL sheets. 30 g MgCl2 and 10 g CNTL (CNTOH) were added into the ball-milling agate jar under nitrogen atmosphere. Keep ball milling at 500 rpm for 1 hour, the mixture turned out to be more uniform. Then, 1.18 mL TiCl4 were directly added into the ball-milling agate jar under nitrogen atmosphere respectively. Hours later, the CNTL/MgCl2/TiCl4 (CNTOH/MgCl2/TiCl4) catalyst was obtained. Then, these two kinds of catalysts were applied in the isoprene polymerization.
The polymerization was implemented in a 250 mL glass reactor filled with nitrogen to remove the moisture oxygen. 180 mL isoprene and the co-catalyst TIBA was added to the reactor then the glass reactor was placed in an ice-water mixture for the pre-polymerization (in the absence of pre-polymerization experiments, this process was abolished). After half an hour the catalyst was poured into the reactor, then pre-polymerization in the ice-water mixture for 10 minutes. After reacting at 20°C for 10 hours the polymerization was terminated by adding 10% HCl-ethanol solution, and then dried under vacuum oven at 40°C until a constant weight was achieved. The polymers obtained by the catalyst of CNTOH/MgCl2/TiCl4 named TPI/CNTOH and obtained by the catalyst of CNTL/MgCl2/TiCl4 named TPICNTL, respectively.
Fourier transform infrared spectroscopy (FTIR) of polyisoprene composites were recorded using a VERTEX 70 infrared spectrometer in the range of 400-4000 cm−1 . Morphologies of the catalyst and composites were examined using a scanning electron microscopy (SEM, JEM-2100F). X-ray diffraction (XRD) patterns were obtained using a Rigaku D/MAX-2500 X-ray diffractometer (Japan). Thermogravimetric analysis (TGA) was conducted using a Q800 thermal analyser (TA, America) under nitrogen atmosphere at a heating rate of 20°C/min. The weight loss was measured from 30 to 800°C.
Results and Discussion
The preparation of CNTL/MgCl2 and CNTOH/MgCl2 supported Ti-based Ziegler–Natta catalyst is illustrated in Scheme 1. In the process of preparation of the catalyst, the CNTL/MgCl2 and CNTOH/MgCl2-supported Ziegler-Natta catalysts were synthesized via high-energy ball milling. During this step, the surfaces of the CNTL and CNTOH were covered with MgCl2-TiCl4 catalyst, which prevented possible aggregation of CNT/CNT layers. The -OH group on the surfaces of CNT can interact with the surfaces of MgCl2 in two distinct ways: by interaction of hydrogen atoms with surface chlorine atoms or via interaction of electron pairs of the oxygen with magnesium.28 To be specific, there were three major factors preventing the aggregation of CNT/CNTOH. Firstly, MgCl2 attached the surface of the CNTL and CNTOH so it can be prevented the Van der Waals force and π-π interaction. Besides, during the high-energy ball milling process, the planetary ball mill possessed greater impact, compression and shearing intensity.29,30 The crashing effect became more intensive and the powders were mixed more uniform, which could turn MgCl2 attached to the surface of CNT will have more active sites exposed to the surface, and this will be beneficial for the catalyst activity. Hence, here we have formulated CNT/MgCl2 supported TiCl4 based Ziegler-Natta catalyst using a solvent-free, ball milling based facile method. Subsequently, the resultant two kinds of catalysts were used during isoprene polymerization to prepare the TPI/CNTL and TPI/CNTOH nanocomposite.
Morphologies of the two catalysts have been compared using SEM analysis and shown in Figure 2. Figure 2(a) shows the dispersed state of CNTOH in CNTOH/MgCl2/TiCl4 catalyst; Figure 2(b) shows the dispersed state of CNTL in TiCl4/CNT/MgCl2 catalyst. As shown in these two figures, CNTOH and CNTL disentangled and dispersed uniformly in the catalysts. In the ball milling process lamella, MgCl2 inserts between CNT or partially cover on the surface of CNT,19,20 which weakens the π-π interaction between CNT and thus makes CNT disentangle and disperse uniformly in the catalyst.
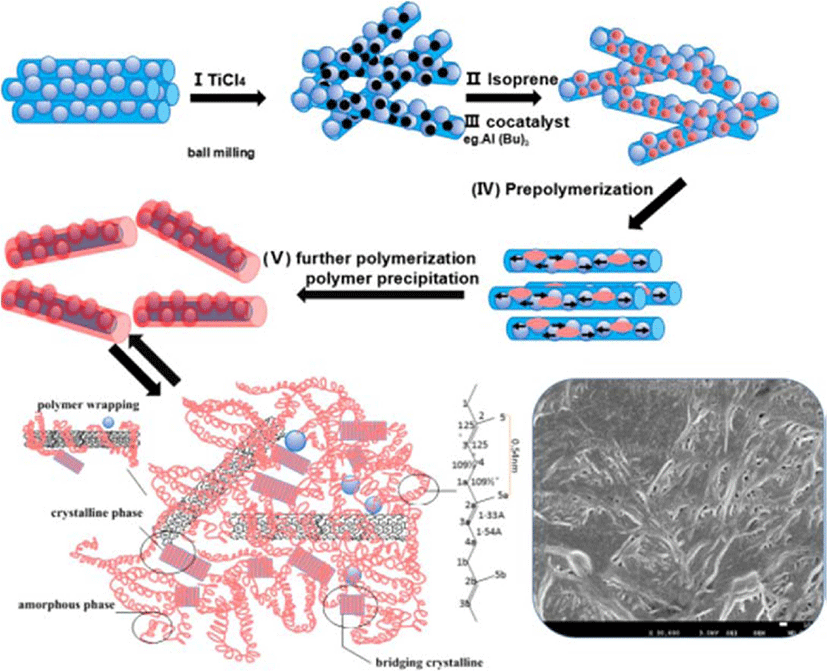
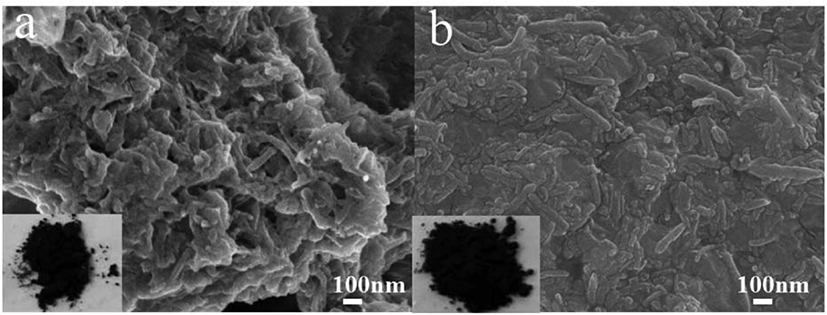
Figure 3 shows the catalytic efficiency of CNTL/MgCl2/TiCl4 and CNTOH/MgCl2/TiCl4 Ziegler-Natta catalysts at different milling time . After the milling time reaches 4 hours with 500 rpm, prolonging the milling time brings minor effects on the catalytic efficiency. Due to the fact that the faster revolving speed and stronger impacting, shearing, milling and compressing effects than traditional mill,31 planetary ball mill presents obvious advantages in breaking and homogenizing powder. After a specific period, the planetary ball mill achieved a kind of balance between smashing and dispersing systems. In consideration of the energy consumption and catalytic activity, the optimum ball-milling time is 4 hours. Hence, the present research sets 4 hours as the milling time for the preparation of catalysts. At the same time, the CNTOH/MgCl2/TiCl4 Ziegler-Natta catalysts shows higher activity than CNTL/MgCl2/TiCl4 Ziegler-Natta catalysts, maybe the -OH group on the surfaces of CNT can interact with the surfaces of MgCl2, so the MgCl2 have higher specific surface area which may cause more titanium tetrachloride active sites to be anchored to the catalyst surface and eventually lead to an increase in catalytic efficiency.
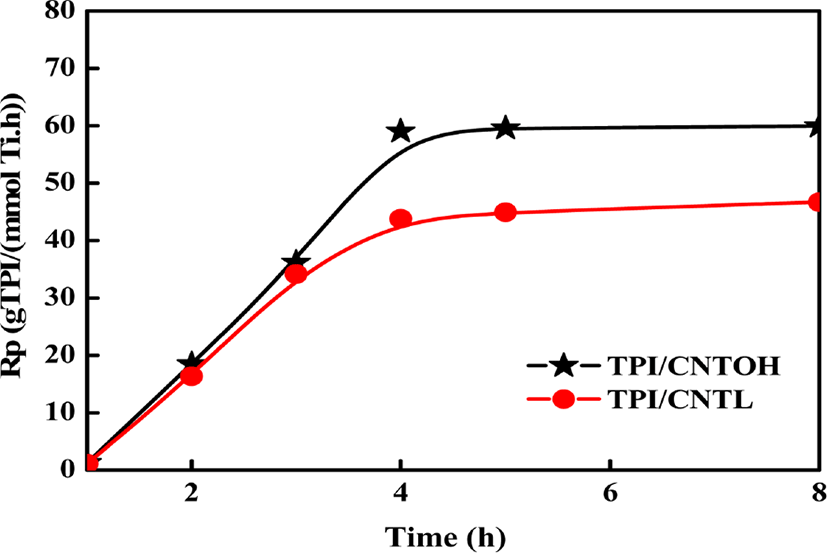
To measure the activity of catalyst and the dispersed state of CNTL and CNTOH, fabrication of more active catalyst has been predicted by comparative XRD analyses of pure MgCl2 carrier, pure CNT carrier, MgCl2/TiCl4 catalyst, CNTL/MgCl2/TiCl4 and CNTOH/MgCl2/TiCl4 catalyst. From Figure 4, in the pure MgCl2 carrier curve it can be seen that high-intensity diffraction peaks are observed when 2θ is 15, 30, and 35. It means MgCl2 carrier is α crystal form. When 2θ is 15, 32 and 50.5, the profile shapes of both MgCl2/TiCl4 catalyst and CNTOH/MgCl2/TiCl4 catalyst are wider at the bottom and lower at the height than the diffraction peaks of α-MgCl2. The WAXD spectrogram of MgCl2/TiCl4 catalyst is basically same with that of CNTOH/MgCl2/TiCl4. It indicates that the magnesium chloride in both the prepared CNTOH/MgCl2/TiCl4 catalyst and TiCl4/MgCl2 catalyst is transferred to δ crystal of activity from the primitive α crystal. The high and steep diffraction peaks in α-MgCl2 become wide and weak in δ-MgCl2 of disordered structure. The reason is that the increase of δ-MgCl2 of disordered structure results in the increase of content of non-crystalline parts, which increases the specific surface area of the above-mentioned Zeiger-Natta carbon nanotube catalyst; besides, the non-crystalline part of the disordered-structure MgCl2 is in favor of the permeation of TiCl4 into the depth. Both the increase of specific surface area and easier permeation of active component effectively increase the Ti content of carriers.
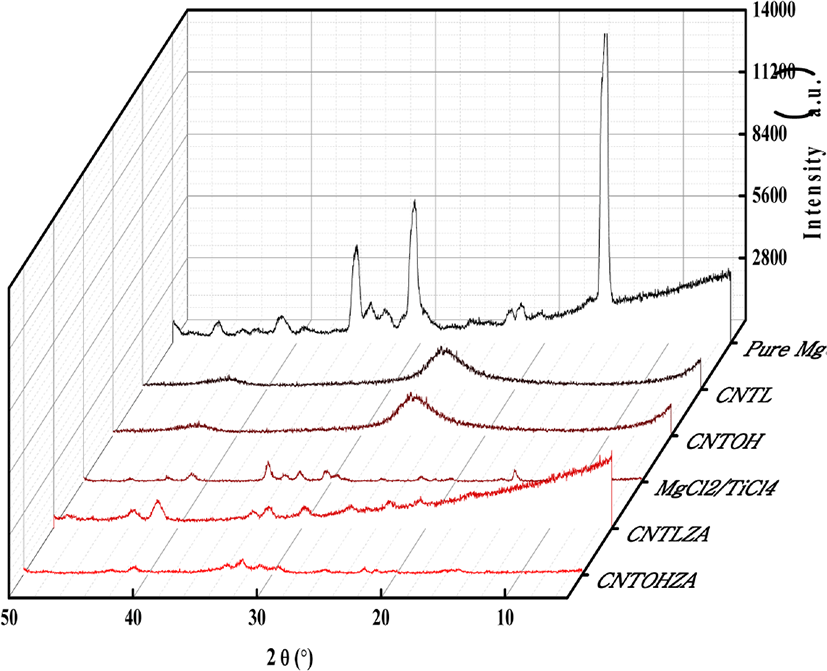
In Figure 5(a), the polymerization reaction starts at 30°C without pre-polymerization. Both the two kinds of catalytic activity rapidly reaches the top and then gradually declines as the reaction goes on. The possible reason is that the power-like catalyst contact monomers at a large-scale at the beginning. However, as the reaction goes on, the catalyst pieces are covered by polymer and monomers become poorer fluidity. The decrease in the catalytic activity can be attributed to the polymer of early formation functions as a physical barrier, retarding the diffusion of the isoprene into the catalyst core. With the increasement of reaction time, the rate of polymerization continuously declines till the isoprene is completely depleted.
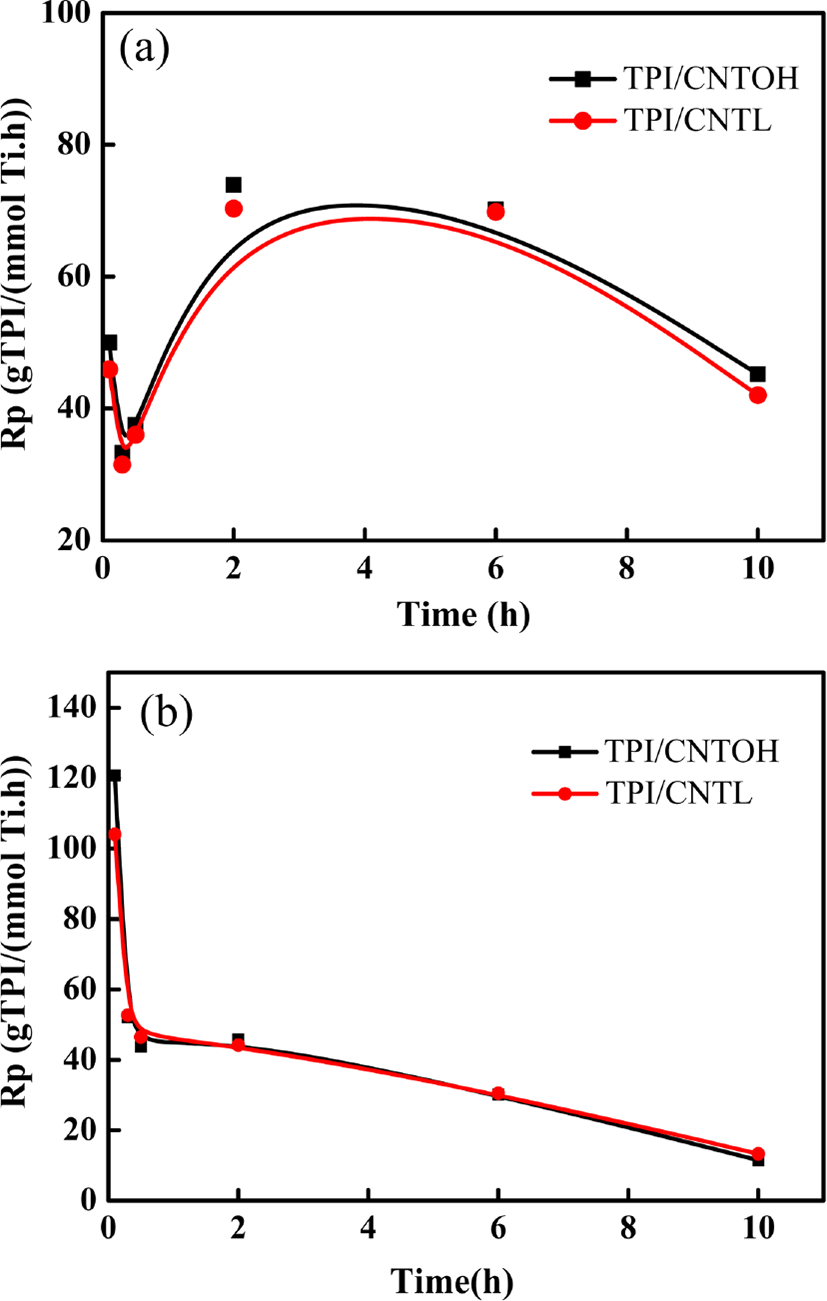
In Figure 5(b), the polymerization reaction includes pre-polymerization in icy water for 0.5 h and then conducting polymerization reactions at 30°C. It can be seen that the catalytic activity rapidly reaches to the peak and then gradually declines during the pre-polymerization process, however, the decreasing trend was much lower than in the direct polymerization process. The possible reason is that during the beginning stage of polymerization reaction, triisobutyl aluminum deoxygenates TiCl4 to TiCl3 and Ti3+ triggers the isoprene polymerization. At the stage, the chain initiation rate and chain conversion rate are both high, so that the polymerization action presents relatively high activity. Without the pre-polymerization at low temperature, the initial polymerization rate of polyisoprene is higher than its crystallization rate (when the trans-1,4-structure is over 95%). The polymerization products possess poor formability and adhere together. While, pre-polymerization at low temperature can stabilize the active centers of catalysts, prolong catalysts' active time and effectively lower the viscidity of the system, which facilitates better morphology of polymers. During the process of polymerization, triisobutyl aluminum further deoxidizes Ti3+ to Ti2+, which has no activity to initiate the isoprene polymerization. The foregoing mentioned reduction reaction consumes the triisobutyl aluminum. Besides, such excessive reduction reaction reduces the concentration of triisobutyl aluminum, which eventually causes the concentration reduction of catalysts active centers initiating isoprene polymerization. The catalysts present declining polymerization activity. Due to the reducing concentration of triisobutyl aluminum, the probability of polymerization active centers transferring to triisobutyl aluminum also reduces, which further reduces the chain transfer rate. As the polymerization reaction goes on for 30 minutes, chain initiation rate and chain transfer rate reach to a balanced state and catalytic active centers tend to stablilize.
Thus, the relationship of the TiCl4/isoprene monomer mole ratio (shorted as n(Ti)/n(IP)) with the monomer conversion rate was studied. As shown in Figure 6, when the n(Ti)/n(IP) is within the range of 1~5×10−5 , the monomer conversion rate increases with the increase of n(Ti)/n(IP). The reason is that when the concentration of the active component TiCl4 is high, the probability that isoprene attacks TiCl4 is also high. As a result, the monomer conversion rate in unit time is high. The catalytic efficiency of catalyst firstly increases and then declines with the increase of n(Ti)/n(IP) as well as reaches to the peak when the n(Ti)/n(IP) is 3.5×10−5 . The reason is that when the catalyst concentration is low and n(Al)/n(Ti) mole ratio reminds unchanged, the relative concentration of the cocatalyst triisobutyl aluminum in monomer is relatively low; besides, due to the active chemical characters, triisobutyl aluminum may react with some residual impurities like water and oxygen in the system, which consumes a certain amount of triisobutyl aluminum. In actual reactions, the n(Al)/n(Ti) declines and the cocatalyst triisobutyl aluminum fails to fully cause complex reaction with active centers, which lead to the declining of polymerization rate (Rp). However, after the n(Ti)/n(IP) reaches to a specific value (3.5×10−5), the numbers that monomer attacks the active center relatively declines as the n(Ti)/n(IP) increases. Then the catalyst's CE calculated with unit mass of catalyst will declines. The result is consistent with relationship of CE and conversion rate gained through theoretical calculation.
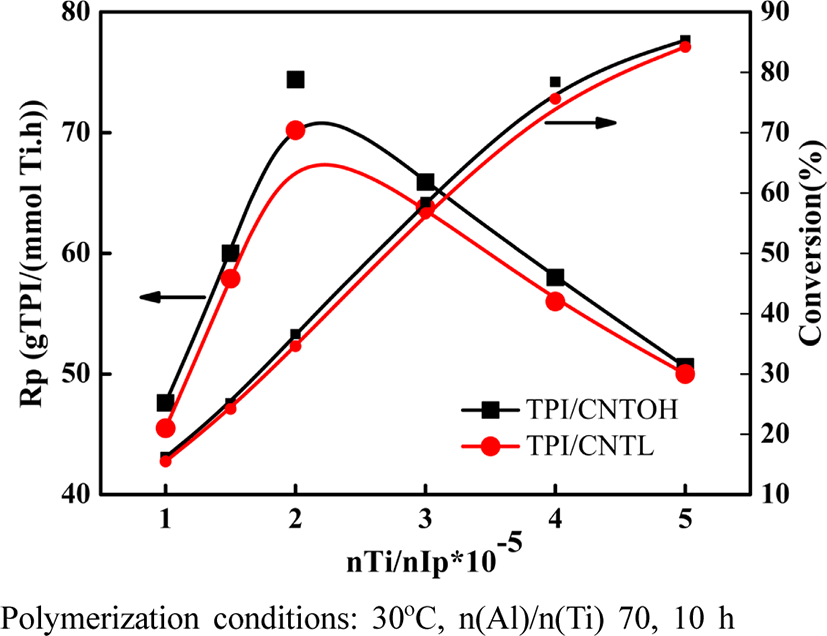
As can be seen from Figure 7, the polymerization efficiency increases with the increase of Al-Ti molar ratio of Al-Ti, and the conversion rate of polymerization decreases with the increase of molar ratio of Al-Ti, which shows that the active component of the main catalyst, tetrachloro Titanium and monomer and cocatalyst triisobutyl aluminum there is the best ratio between. When the molar ratio of Al and Ti is too low, the concentration of triisobutylaluminium is too low, the triisobutylaluminum can not completely remove the impurities in the system, resulting in the loss of activity of some of the active components of the catalyst and the impurities; meanwhile, the co-catalyst The amount of triisobutylaluminium is too small, the main active component of titanium tetrachloride can not be fully coordinated with the reaction and can not form a sufficient number of active reaction centers; and when the the molar ratio of aluminum-titanium molar ratio is too high, the cocatalyst may be the main catalyst Over-reduction of titanium tetrachloride to inactive titanium dichloride will also lead to a decrease in the conversion of isoprene in the polymerized monomer. Meanwhile, an excessive amount of triisobutylaluminium will also be present in the subsequent reaction of the catalytic system Chain transfer, which is equivalent to reducing the number of active centers during the actual reaction, may also result in a decrease in the conversion of the isoprene monomer. In the catalyst system, when the ratio of aluminum to titanium is 80, the catalytic efficiency and the conversion rate achieve the optimal ratio.
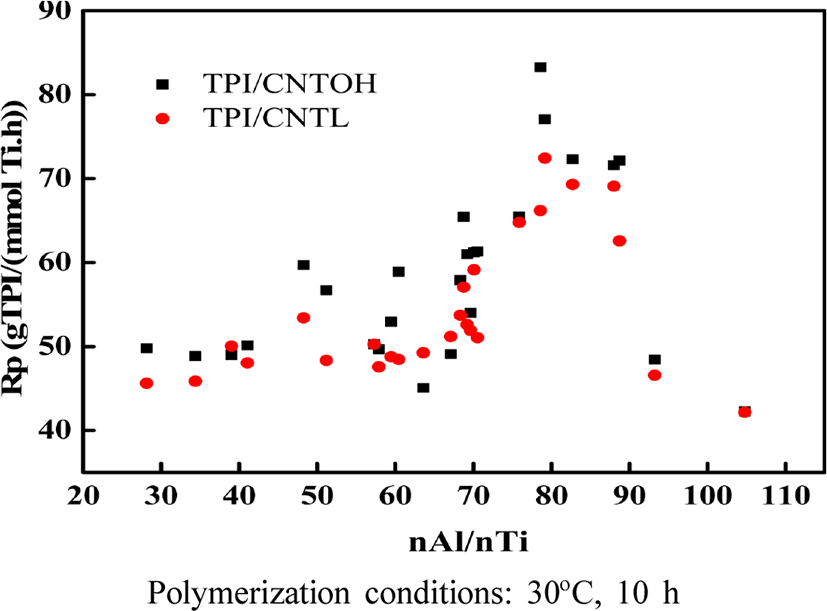
As shown in Figure 8(a) and (b), when n(Al)/n(Ti) increases from 30 to 80, in fingerprint region, no obvious changes is ob-served to the peak shape of polyisoprene carbon nanotube composite. Thus, it can be confirmed that the changes in both n(Al)/n(Ti) and n(Ti)/n(IP) will not lead to structural changes of polyisoprene carbon nanotube composite under catalytic system. At the same time, the structure of these TPI/CNTOH and TPI/CNTL nanocomposites is close to that of natural eucommia rubber, and therefore all of them belong to trans-1,4-polyisoprene, as shown in Figure 8(c). According to the reference (Table 1),32 the signals at 910 cm−1 due to the 1,2-units and the signals at 890 cm−1 due to the 3,4-units, which is not appear in the FTIR spectra. So here there is only contains trans 3,4-units. Then we speculated on the possible mechanism of this reaction, as shown in Figure 9.
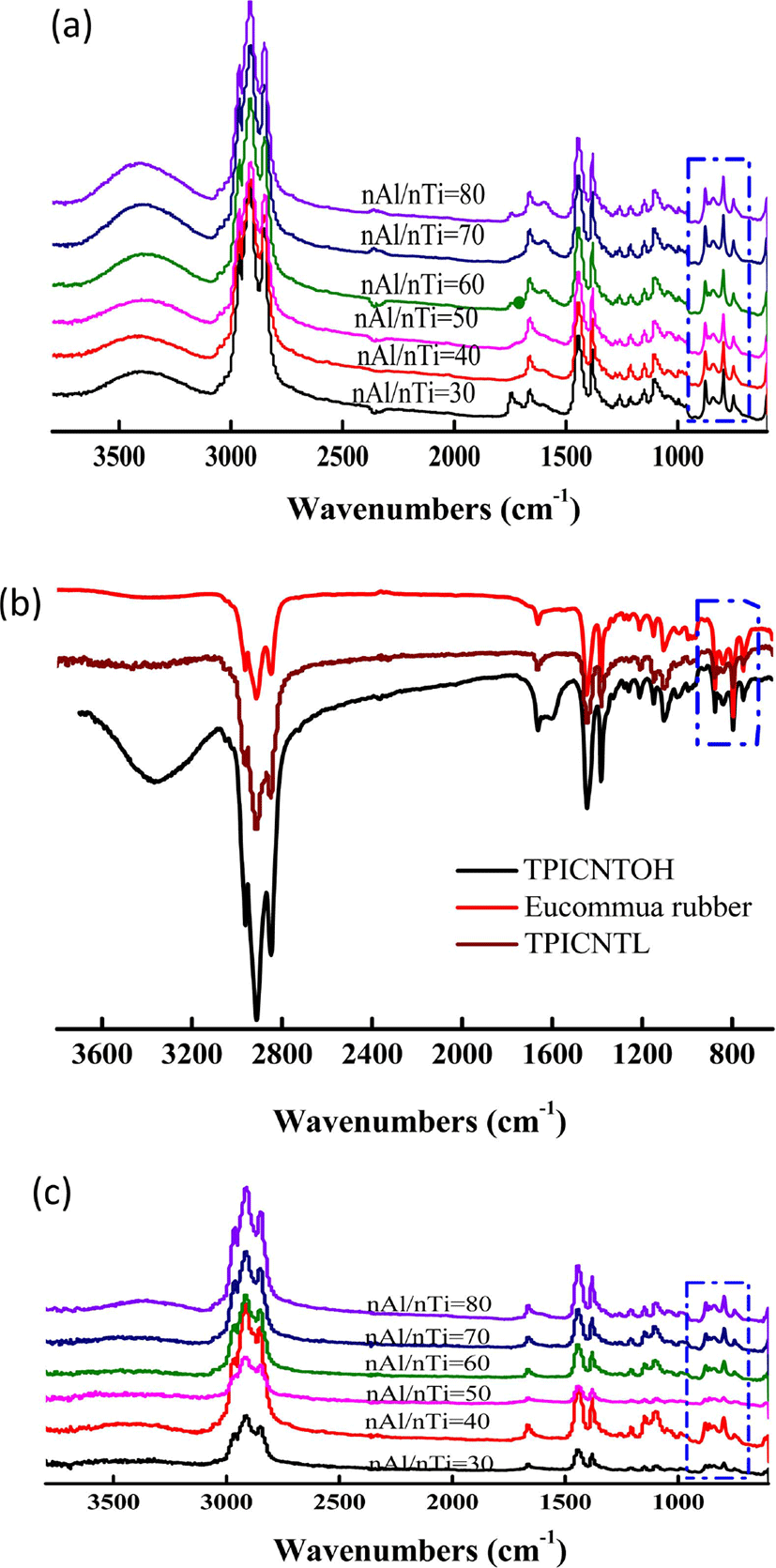
According to the morphology replication characteristics of the supported Ziegler-Natta catalyst, the morphology of the final polymer can be controlled by modifying the morphology of the catalyst.14,16 Therefore, the morphology of the resultant TPI, TPI/CNTOH nanocomposites and TPI/CNTL nanocomposites directly mirror that of the catalyst. As shown in Figure 9, the particles of TPI obtained using the MgCl2/TiCl4 catalyst are white and irregularly shaped, while those of TPI/CNTOH nanocomposites and TPI/CNTL nanocomposites have a flake shape with homogeneous black color. Additionally, no high-contrast black CNTL or CNTOH sheets could be observed. Because the active points of catalysts closely contact CNT, polyisoprene molecular chains densely cover the CNT during the polymerization. Observing the polyisoprene/CNT nanocomposite, as shown in Figure 9(a) and (b), we can see that polyisoprene molecular chains cover on the surface of single-beam CNT. The polyisoprene molecular chains and single-beam CNT form a near core-shell tubular structure. Polyisoprene molecular chains grow during the polymerization process, get rid of active centers and produce crystallization growth near the surface of CNT. Because the active centers disperse uniformly, uniform polyisoprene crystals are formed on the surface of CNT, featuring morphologic reproduction effect and well demonstrating the morphology of CNT.
As shown in Figure 10, Compared with pure polyisoprene, as the nanotube content increases, the highest temperature at thermal weight loss is increased from 380°C to 402°C. The obvious improvement in thermal stability is related to the network structure of the composite and seldom relates to the types of CNT.
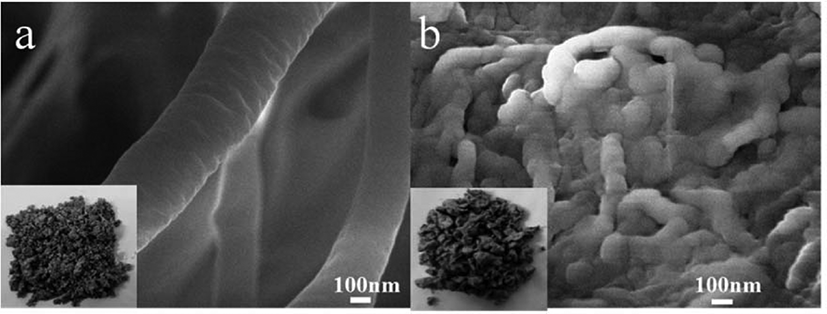
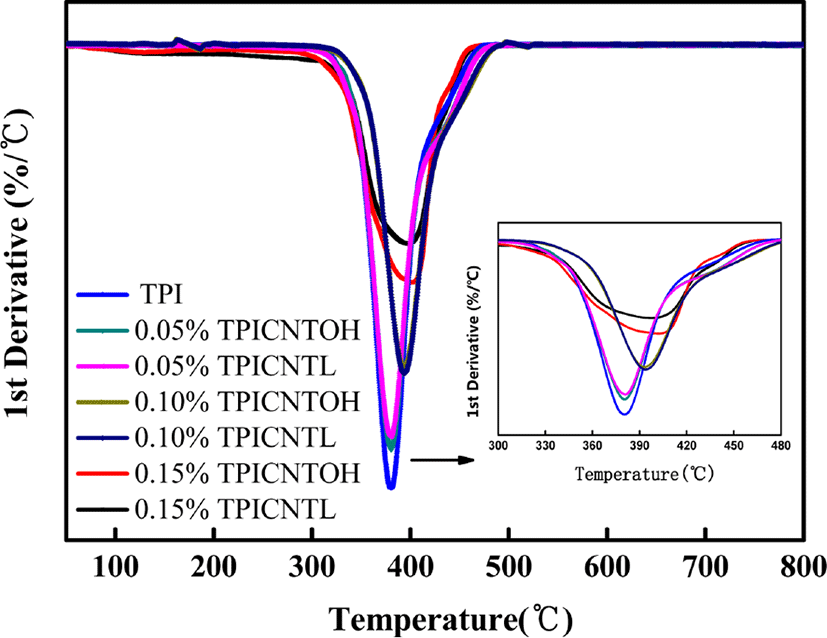
Conclusion
The large inner diameters carbon nanotubes (CNTL), hydroxylated carbon nanotubes (CNTOH) and magnesium chloride (MgCl2) were used as the carriers for the Titanium-based Ziegler-Natta catalyst, which achieved well dispersion by the high-energy ball-milling technique. The optimum ball-milling time for preparing CNT/MgCl2/TiCl4 Ziegler-Natta catalysts was 4 hours. The polymerization rate turned out that CNTOH/MgCl2/TiCl4 Ziegler-Natta catalysts has higher efficiency. Meanwhile, TPI/CNT and TPI/CNTOH nanocomposites was synthesized by in-situ trans-selective polymerization with CNT/MgCl2 supported Ziegler-Natta catalyst. The morphologies of the TPI/CNT and TPI/CNTOH nanocomposites exhibited a tube-like shape and the CNTL and CNTOH fillers were well dispersed in the TPI matrix. In addition, the thermal stability properties of the TPI were significantly enhanced by the CNTL/CNTOH fillers (0.15 wt%).