Introduction
세계 각국의 환경과 연비에 대한 관심, 그리고 불안정한 유가 상승 등으로 인하여 저연비 타이어 트레드에 대한 수요가 지속적으로 증가하고 있어 자동차 산업에서 저연비 타이어의 개발이 가속화되고 있다. 특히 환경에 관심이 큰 유럽을 필두로 하여 전 세계적으로 다방면의 환경 규제 정책이 시행되고 있다. 자동차 업계에서 친환경적인 기술은 2 가지로 생각된다. 첫 번째로 타이어의 회전저항의 감소로 연비를 개선하여 배기가스 배출량을 감소시키는 것, 두 번째는 타이어의 내마모성을 증가시켜 오래 쓰도록 하여, 타이어 생산 시 발생하는 이산화탄소를 줄이고 재활용이 곤란한 폐타이어의 양을 줄이는 것이다. 그 예로 트레드용 고무 보강제로 오래간 쓰였던 카본블랙을 실리카로 대체하는 연구가 활발히 진행되고 있다. 카본블랙은 실리카에 비해 값이 싸고 고무와 상용성이 우수한 특성으로 널리 사용되었으나, 보강제로 사용 시 타이어의 히스테리시스 손실이 실리카 보강 타이어보다 불리하다는 단점이 있다. 실리카로 보강된 타이어는 고무와 혼화성과 분산성이 좋지 않으나, 이를 극복하기 위한 커플링제의 개발로 연비 절감형 타이어용로서 실리카 보강 SBR 고무복합체는 최고등급으로 인정받고 있다.1-3,7 Solution styrene-butadiene rubber (SSBR)은 회전저항이 낮으면서 기존의 유화중합으로 중합된 SBR보다 실리카와의 상용성이 좋고 더욱 우수한 점탄성 특징을 가지고 있다.4,5 또한 타이어용 SBR은 접지력이 우수하나 이와 반대급부로 따라오는 불량한 내마모성을 보강하기 위하여 butadiene rubber (BR)을 혼합하여 사용한다.6 타이어용 고무복합체에서 BR의 함량 증가는 butadiene에 존재하는 이중결합의 증가로, 이는 고무 가교의 가장 일반적인 방법인 유황 가황을 위한 가교점을 제공한다. 또한 최근에는 다양한 기후조건 하에서 대외적인 활동을 활발히 하고 있기 때문에 고무복합체의 내한성에 대한 관심이 크다. 특히 고무가 상온에서는 탄성을 나타내더라도 저온이 되면 점차 단단해져 고화되고 탄성을 잃어 고무의 특성을 잃게 된다. 이는 고무복합체의 Tg와 밀접한 관련이 있다. NdBR (ultra high-cis polybutadiene rubber)은 분자 내에 butadiene이 cis-ontent가 97% 이상인 고무를 말하는데 90~−100℃까지 상용이 가능하여 SSBR과 혼용 시 상용온도는 –70℃까지 기대할 수 있고, 점성이 뛰어나 내마모성에 대한 보강효과 또한 뛰어나다. 이는 극지방이나 고산지대에서 상용 가능한 타이어나 신발 밑창, 트레드용 고무복합체에 대한 좋은 방안으로 적용될 수 있다. 본 연구에서는 실리카와 기타 충전제 비율은 동일하게 고정하고, SSBR과 NdBR의 함량 변화에 따른 고무복합체의 물성 연구를 통하여 결합고무의 가교특성, 경도, 인장강도, 내마모성, 내한성에서 경향성을 보고자 하였다.
Experimental
본 연구에서 사용한 원료 고무는 solution styrene-butadiene rubber (SSBR, Kumho Petrochemical, SOL-5270H, styrene content; 21 wt%, vinyl content; 65 wt%, Mooney viscosity (100℃); 63, Tg; −26℃)와 ultra high-cis polybutadiene rubber (NdBR, Kumho Petrochemical, NdBR-40, cis content; >97 wt%, Mooney viscosity (100℃); 43, Tg; −100℃)를 사용하였고, 보강제로 실리카(Ultrasil 7000GR, Evonik Korea; BET 175 m2/g)와 커플링제는 bis(triethoxysilylpropyl)tetrasulfide (TESPT)로 표면을 개질한 카본블랙(X-50s, Evonik carbon black Korea)을 사용하였다. 가교제로는 sulfur (Daejung Reagents Chemicals)를 사용하였고 실리카 배합 시 실라놀 그룹의 작용으로 인한 가교속도 지연을 방지하기 위하여 1, 2차 가교촉진제로 N-cyclohexyl-2-benzothiazole sulfonamide (CBS, Tokyo Chemical Industry)와 di-phenyl guanidine (DPG, Tokyo Chemical Industry)를 사용하였고, 이외에 zinc oxide (ZnO, Samchun Pure Chemical Co.), stearic acid (SA, Daejung Reagents Chemicals)는 상용화된 재료를 사용하였다.
SSBR과 NdBR을 오픈 롤밀(open rollmill)을 이용하여 5 분간 소련한 후 ZnO, SA, silica, carbon black (CB)을 첨가하여 10 분간 혼합하였다. 그 후에 sulfur, CBS, DPG를 넣고 3분간 혼련하여 배합고무를 제조하였다. 배합과정에서 컴파운드 내부의 온도는 60℃를 유지하였다. Rubber process analyzer (RPA)를 이용하여 최적의 가황시간(t90)을 측정한 후 2 mm 두께의 몰드를 이용하여 160℃, 10 MPa의 조건에서 t90 동안 가황하였다. 배합처방은 Table 1에 나타내었다.
고무복합체의 유변학적 성질 및 가교특성, 적정가교 시간을 측정하기 위하여 RPA-V1 (U-can Inc., Taiwan)을 이용하여 160℃, 30 분 동안 측정하였다. 실험은 ASTM 6204 시험 방법을 따랐다. 가교속도 CRI(cure rate index)는 식 (1)로 계산하였다.
고무복합체의 모폴로지를 조사하기 위해 제조된 2 mm 두께의 시편을 액체질소로 급속 냉동 후 파단하여 2 분간 백금 코팅 후 SEM (scanning electron microscopy, EM-30, Coxem)을 이용하여 파단면을 관찰하였다.
경도는 ASTM D2240의 시험방법을 따랐다. Shore A 경도계(Time, TH200)를 사용하여 총 5 개의 가황고무를 6 mm 두께로 제작하여 5 번 측정한 후 최대 값 및 최소 값을 제외한 3 개의 시편의 평균을 구하였다.
인장시험은 ASTM D 412의 규격에 맞추어 시편을 제작하였다. 제작된 시편을 만능재료시험기(H5KT, Tinius Olsen)를 이용하여 인장속도 500 mm/min으로 각 배합당 5 개의 시편을 측정하여 최대값 및 최소값을 제외한 나머지 값들의 평균값을 구하였다.
ASTM D 1630에 의거 시험을 실시하였다. 25.4 mm × 25.4 mm × 6.3 mm 크기의 시편을 제작 후 드럼 위에 고정한다. 드럼을 회전시켜 시험편의 두께가 2.54 mm 마모되었을 때 그 회전 수를 기록하였다. 내마모율(AI)은 기준 시험편의 마모 평균 값(R1)으로 시험편의 마모 평균 값(R2)을 나눈 값으로 식 (2)로 계산하였다.
Results and Discussion
SSBR/NdBR 블렌드의 조성에 따른 가교특성, 최저토크(ML), 최대토크(MH), 가교도(∆M), 스코치 시간(ts2), 적정 가교시간(t90), 가교속도지수(CRI)를 Table 2에 정리하였다. 가교도의 경우 NdBR의 함량이 증가할수록 증가하는 모습을 볼 수 있었다. NdBR의 함량의 증가는 분자 내의 이중결합의 증가로 가교 지점이 증가함으로 가교도가 증가되었다고 판단되 었다.
SEM은 충전제의 분산도를 보기 위해 사용되었다. Figure 1은 고무복합체의 조성에 따른 파단면의 SEM 이미지이다. SSBR과 NdBR의 배합비율에 따른 분산성은 큰 차이를 보이지 않았다. NdBR의 함량이 증가할수록 고분자 주쇄의 소수성이 커지게 되므로 충전제-충전제 상호작용이 커지므로 응집현상으로 인하여 미세하게 충전제의 분산성이 낮아지는 모습을 관찰할 수 있었다.
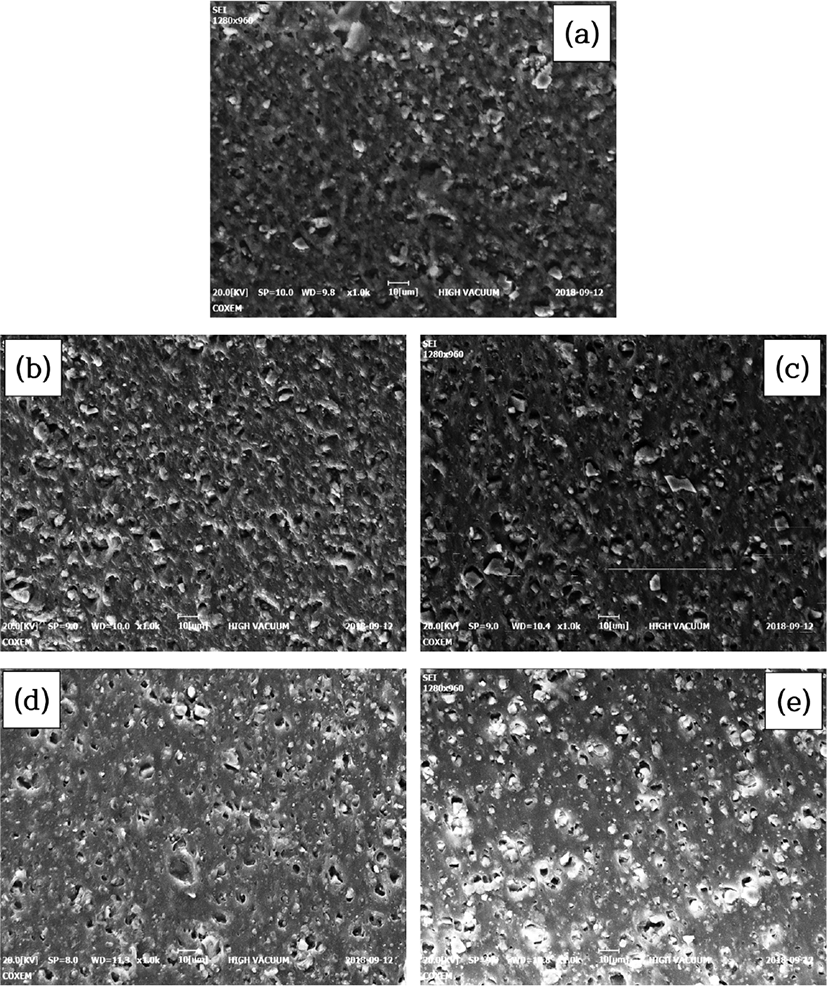
SSBR/NdBR 블렌드의 경도 측정 결과를 Figure 2에 나타내었다. 일반적으로 경도는 고무의 가교도에 비례하는데, NdBR의 함량이 증가할수록 경도는 증가하였다. NdBR의 함량 증가는 고분자 주쇄 내에 적은 팬던트 그룹을 가지게 되므로 보다 조밀한 구조를 가지게 되고, 또 가교 지점의 증가로 더 높은 가교도를 가지게 된다.13 따라서 이는 경도의 증가를 가져오는 것으로 판단되었다.
SSBR/NdBR 블렌드의 인장강도 측정 결과를 Figure 3에 나타내었다. 일반적으로 인장강도의 경향성은 경도를 따라간다. NdBR의 함량증가는 가교밀도의 증가와 조밀한 구조의 블렌드를 형성하고 이는 인장강도의 증가로 나타났다.
SSBR/NdBR 블렌드의 마모현상은 두 가지로 나누어 해석할 수 있다. 우선 SSBR의 함량 증가로 엉성한 매트릭스를 가지는 조성에서 다른 면과 접촉 면적이 좁아지므로 거친 마모 면을 가지게 되고, 이는 피로마모를 일으키게 된다. 피로마모는 거친 표면이 고무의 표면에서 연속적으로 변형을 하게 됨으로써 고무의 일부가 표면으로부터 분리되는 현상를 말한다. 다른 하나의 요인으로는 SSBR의 경우 마모가 일어나 분자의 주쇄가 끊어졌을 때 공명에 의해 라디칼이 안정화가 되어 파괴가 영구히 지속되는 반면 NdBR의 경우 라디칼이 높은 반응성을 가지고 있어 파괴 후에도 가교되려는 성질을 가지게 된다.8 따라서 NdBR을 증량시킨 조성에서 큰 폭으로 내마모성을 증가하는 것을 확인할 수 있었다. 이는 Figure 3에 나타내었다.
고무가 실온에서는 탄성을 나타내더라도 저온으로 되면 점차 단단해져 고화되고 탄성을 잃어 고무의 특성을 잃게 된다. 고무가 점차 저온으로 가게 되면 고무의 열운동 단위인 주사슬 세그먼트와 마이크로 브라운 운동, 회전 운동 등이 활발성을 잃게 되어 결국 일정온도에 달하면 점탄성적 성질이 없는 고체가 된다. 이는 고무복합체의 Tg와 밀접한 관련이 있는데, 대부분의 고분자물질은 Tg가 낮을수록 내한성이 양호하다.11 NdBR의 Tg값이 SSBR보다 낮으므로 NdBR의 함량 증가는 내한성이 증가하는 결과를 초래하였다. 내한성 측정 결과는 Table 3에 나타내었다.
S100 | S90 | S80 | S70 | S60 | |
---|---|---|---|---|---|
Hardness(Shore A) | 80 | 80 | 82 | 83 | 84 |
S100 | S90 | S80 | S70 | S60 | |
---|---|---|---|---|---|
No. of broken speci-men(−50℃) | 3 | 2 | 1 | 0 | 0 |
Conclusions
자동차 타이어 트레드용으로 사용되는 SSBR의 물성 향상과 silica와의 분산성을 확인하기 위해 NdBR과 silica로 보강하여 실험을 실시하였다. NdBR의 함량이 증가할수록 가교속도가 빨라지고 가교도가 증가하는 경향을 보였다. NdBR의 함량 증가는 분자 내의 이중결합의 증가로 가교 지점이 증가하는 것으로 판단되었다. 또한 고분자 주쇄에 styrene 그룹의 비율이 감소하므로 조금 더 선형적인 구조가 되어 가교 거리가 줄어들게 되는 것도 가교속도와 가교도의 증가 이유로 생각된다. 모폴로지 관찰 결과는 실리카 입자가 비교적 균일하게 잘 분산된 것으로 확인되었다. 경도와 인장강도 측정결과는 가교도와 비슷한 경향을 보였다. 분자 내 이중결합의 증가와 조밀한 구조는 경도와 인장강도의 증가로 나타났다. 내마모성 측정 결과도 NdBR의 함량 증가가 수치 증가로 나타났다. 주 요인으로는 가교도의 증가로 조밀한 매트릭스를 가지는 조성이 내마모성이 높고, SSBR의 경우 마모 진행 중에서 분자 주쇄가 끊어질 때 styrene과 공명구조를 이루기 때문에 안정되어 끊어짐이 영구히 지속되는 반면, NdBR의 경우 분자 주쇄가 끊어지고 생성된 라디칼의 높은 반응성으로 또 다른 가교를 형성하기 때문에 내마모성에서 우수하다.8 내한성 측정 결과는 NdBR의 함량이 증가할수록 좋은 결과를 보였다. 이는 NdBR의 Tg가 –100℃로 낮기 때문에 고무복합체의 Tg가 낮아져서 내한성이 향상된 것으로 판단되었다.11