Introduction
일반적으로 겔코트(Gel-coat)는 마블(Marble) 또는 FRP (Fiber-Reinforced Plastics) 제품의 표면을 보호하고 유리섬유 보강재 패턴을 감추어 최종 제품의 외관을 미려하게 유지시켜줄 뿐만 아니라 성형품의 수명과 성능을 향상시킬 목적으로 사용되는 도료형 코팅소재를 지칭한다.1,2 최근 들어서 해양 레저, 파이프, 건축용 외장재, 자동차 경량부품 등 다양한 산업 분야에서 경량복합소재에 대한 수요가 꾸준히 증가하고 있다. 그러나 적용되고 있는 복합소재들은 태양광, 해수, 수분, 화학적 침식 등 가혹한 열화환경에 장기간 노출되기 때문에 경량복합소재를 보호하고 제품의 내구성 및 신뢰성 등을 확보하기 위한 고기능화된 겔코트 기술개발도 다양하게 진행되고 있다.3
레저(leisure) 선박용 경량복합소재 제조 현장에서, 주로 사용되는 겔코트 소재는 스티렌 모노머를 포함하고 있는 불포화 폴리에스테르, 비닐 에스터 수지 또는 에폭시 수지 기반으로 적용되고 있다. 그러나 불포화 폴리에스테르 계열 겔코트인 경우, 사용되는 많은 양의 스티렌 모노머에 의한 VOC의 환경적인 유해성 관점에서 문제점이 있으며 반면에, 에폭시 계열 겔코트는 고온에서 내구성 저하가 빈번하게 발생하고 있는 실정이다.4-7 이러한 단점을 보완할 뿐만 아니라 친환경적인 작업환경을 기대할 수 있는 새로운 겔코트 소재가 필수적이며, 이에 대하여 폴리우레탄계 겔코트가 대안소재로서 개발이 진행되고 있으며 관련시장도 확대되고 있다.8,9
폴리우레탄은 일반적으로 다양한 이소시아네이트, 다양한 폴리올 그리고 사슬연장쇄(chain extender)의 부가반응에 의해 쉽게 제조할 수 있으며 내후성, 내마모성 그리고 크랙 저항성도 개선되어 결과적으로 탈 몰드 시 부품의 손상을 최소화 할 수 있는 장점이 있다. 또한 다양한 조합에 의해 각각의 응용에 필요한 경화속도를 맞춤형 화학으로 조절할 수 있는 장점도 있다.10-14
본 연구에서는 불포화 폴리에스터계 겔코트의 단점을 극복하고 다양한 부가기능을 부여하기 위해 기초적인 폴리우레탄 기반의 겔코트를 설계하였다. 폴리우레탄계 겔코드에 사용된 이관능성 이소시아네이트의 화학구조에 따른 겔코트 코팅막의 표면강도와 인장강도 등을 측정하여 폴리우레탄계 겔코트의 내구성 뿐만 아니라 자외선 촉진 내후성 테스트를 통한 폴리우레탄 겔코트의 내후성 특성을 비교 고찰하였다.
Experimental
본 실험에 사용한 시약은 polyether polyol (GY-420, Mw = 420, 국도화학), isophorone diisocyanate (IPDI; 삼전화학), hexamethylene diisocyanate (HDI; Fluka), dicyclohexylmethane-4,4'-diisocyanate (HMDI; TCI), m-xylylene diisocyanate (XDI; TCI)이며 정제과정 없이 그대로 사용하였다. 우레탄 반응 촉매로는 bismuth octoate (A9, 진양화성)을 사용하였으며, 불포화 폴리에스터 수지(POLYSTAR R110, 세원화성) 경화촉매는 methyl ethyl ketone peroxide (MEKPO; Sigma-Aldrich)와 cobalt octoate (Sigma-Aldrich)를 사용하였다.
Diisocyanate와 polyether polyol을 NCO/OH Index 값을 1.05로 일정하게 맞추고 일정량(0.03 wt.%)의 우레탄 반응촉매와 함께 겔코트 코팅액을 제조하였다. 코팅액을 honey wax로 이형 처리한 소다라임 유리판 위에 닥터블레이드(Doctor blade)을 이용하여 일정한 두께로 도포한 뒤, 상온에서 약 24 시간 우레탄 반응을 시킨 다음, 60°C의 순환식 건조 오븐에서 24 시간 동안 추가 반응을 수행하여 약 1.0 mm 두께의 겔코트 코팅막을 제조하였다.
경질유리판 위에 겔코트 코팅막을 형성한 다음, 혼합 속경화제(MEKPO/cobalt octoate)가 함유된 불포화 폴리에스터 수지에 glass-fiber woven roving mat를 함침시켜 3겹으로 적층한 후 로울러를 이용하여 겔코트/FRP 복합소재를 제조한 다음, 상온에서 24시간 동안 경화시킨 후 겔코트 접착력 테스트를 위한 시편을 제조하였다.
겔코트의 지촉건조 시간은 KS M 5000 방법에 따라 측정되었다. 형성된 겔코트 코팅막에 손끝을 살며시 접촉하여 손가락 끝에 겔코트가 묻지 않고, 지문이 남지 않은 상태까지의 시간을 5분 단위로 측정하였다. 겔코트 표면경도를 측정하기 위해, GS-702N durometer (TECLOCK Co.)를 이용하였다. 두께 4 mm 이상 되는 시편에 4 kg의 힘을 가했을 때의 표면경도를 측정하였다. 겔코트의 기계적 물성을 측정하기 위해, LR30K-Plus universal testing machine (AMETEK Ltd.)을 이용하였다. 겔코트 샘플을 폭 10 × 70 mm로 절단하고 5 mm/min의 테스트 속도로 기계적 물성을 측정하였다. 겔코트 코팅막과 FRP 복합소재 층간 접착력은 Pull-off strength test로 측정하였다. PosiTest AT-A Automatic (DeFelsko Inspection Instruments)를 이용하여 에폭시 접착제로 겔코트 도막에 circular steel disc (dolly)를 접착하는 near-to-surface method를 사용하였다. 겔코트 코팅막의 내후성을 측정하기 위하여 Weather-O-meter, Ci4000 (Atlas Co.)를 사용하였다. 시료에 Xenon Arc 광을 100 시간 조사한 후 변색 정도를 색차계, CM-3600d (Konica Minolta)로 측정하였다.
Results and Discussion
본 연구에 사용한 이관능성 이소시아네이트의 화학구조를 아래 Figure 1에 나타내었다. 사용된 이관능성 이소시아네이트의 화학구조에 따른 폴리우레탄계 겔코트 특성을 확인하기 위해 동일한 polyether polyol을 NCO/OH Index 값이 1.05가 되는 조성비로 겔코트 조성액을 제조하였다. 산업적으로 레저용 선박을 건조하기 위한 경량복합소재 제조할때 표면층을 형성하는 겔코트는 충분한 지촉건조 시간(Set-to-touch time)이 요구된다. 그 이유는 넓은 면적의 선박 목업(mockup)에 일정한 두께로 도포해야 하고, 반건조 상태에서 복합소재가 적층되어 두 계면간 접착력을 향상시키기 위한 충분한 시간이 필요하기 때문이다. 실제 현장 작업자들은 약 20~30분 이상의 지촉건조 시간을 요구하는 경우가 일반적이다. Figure 2는 상온촉매인 bismuth계 촉매하에서 이관능성 이소시아네이트 화학구조 변화에 따른 겔코트의 지촉건조 시간을 보여주고 있다. 지촉건조 시간 측정은 KS M 5000 방법에 따라 진행하였다. HDI를 사용할 때 가장 긴 지촉건조 시간(약 40분)이 걸린 반면, XDI를 사용할 때 가장 짧은 지촉건조 시간(약 15분)을 보여주고 있다. 지방족 고리구조를 가진 IPDI와 HDMI인 경우, 중간정도의 지촉건조 시간(약 25~30분)을 보여주고 있다. 이러한 결과는 HDI의 낮은 반응성으로 인해 상대적으로 우레탄 반응이 느려져 지촉건조 시간이 지연된 것이며,15 이소시아네이트 작용기 이웃에 있는 방향족 고리는 이소시아네이트 작용기의 반응성을 촉진시켜 XDI의 우레탄 반응을 촉진시켜 짧은 지촉건조 시간을 보여준 것으로 판단된다. 이에 따라 방향족 고리를 포함하는 이소시아네이트는 폴리우레탄계 겔코트에 적절하기 않으며, 상대적으로 반응성이 낮은 지방족 또는 지방족 고리 이관능성 이소시아네이트가 폴리우레탄계 겔코트 제조에 적절한 것을 확인하였다.
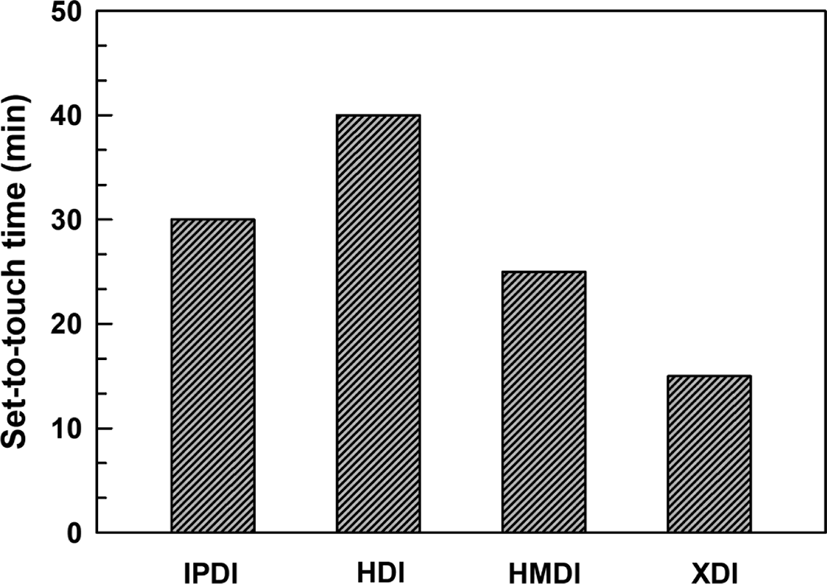
Figure 3은 이관능성 이소시아네이트의 화학구조 변화에 따른 폴리우레탄계 겔코트의 표면 경도변화를 나타내었다. 전체적으로 HDI 기반 폴리우레탄 겔코트를 제외하고 겔코트의 표면경도는 거의 일정한 표면 경도값을 보여주고 있다. 고리형 화학구조를 가진 이관능성 이소시아네이트인 경우 대부분 높은 표면 경도값을 유지하였지만, 지방족 선형 이관능성 이소시아네이트는 낮은 표면 경도값을 보여주었다. 이러한 결과는 상대적으로 유연한 폴리우레탄 주쇄를 구성하는 지방족 선형 이관능성 이소시아네이트가 겔코트의 표면 경도를 낮추는 요인으로 작용한 것으로 판단된다.
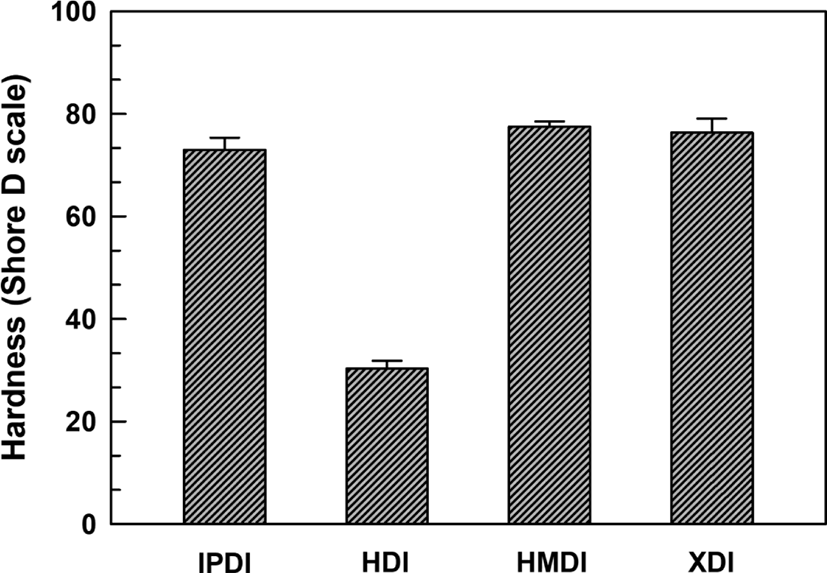
이관능성 이소시아네이트의 화학구조 변화에 따른 폴리우레탄계 겔코트의 인장강도 변화를 Figure 4에 나타내었다. 가장 우수한 인장강도는 IPDI 기반 폴리우레탄 겔코트이었으며, 가장 낮은 인장강도값을 보여준 것은 HDI 기반 폴리우레탄 겔코트이었다. HMDI와 XDI 기반 폴리우레탄 겔코트의 인장강도는 큰 차이는 없지만 HMDI 기반 폴리우레탄 겔코트의 인장강도가 약간 증가한 것을 보여주고 있다. 비록 IPDI가 지방족 고리화합물이지만, 폴리우레탄의 반복구간이 다른 이소시아네이트에 의한 우레탄 반복구조에 비해 짧기 때문에 고분자 주쇄의 강직도를 향상시킨 것으로 판단된다. HDI의 상대적으로 긴 지방족 탄화수소 사슬이 폴리우레탄 주쇄의 유연성을 증가시켜 낮은 인장강도 결과가 도출된 것으로 판단된다. 방향족 고리화합물인 XDI 기반 폴리우레탄 겔코트는 벤젠고리 이웃에 위치한 methylene 그룹으로 인해 벤젠고리에 의한 고분자 주쇄의 강직도 향상을 감쇄한 것으로 판단된다. 이소시아네이트 화학구조 차이에 의한 인장강도 결과는 IPDI가 제안된 이관능성 이소시아네이트들 중에 폴리우레탄 겔코트의 인장강도 향상에 더 효과적임을 보여 주고 있다.
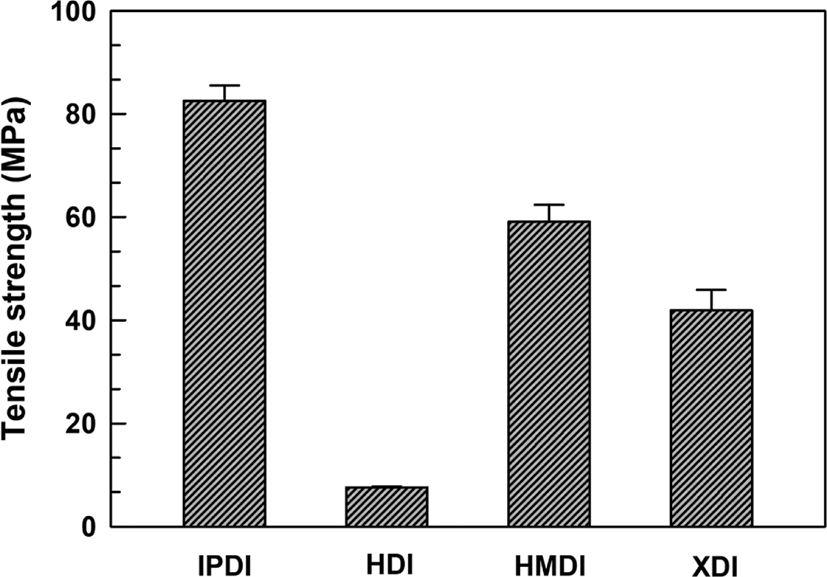
Figure 5에서 실제 FRP 경량복합소재 표면에 폴리우레탄 겔코트를 도포한 후 두 계면사이의 접착력을 측정한 결과를 보여주고 있다. 가장 좋은 접착력은 HMDI 기반 폴리우레탄 겔코트에서 나타났으며, 반면에 XDI 기반 폴리우레탄 겔코트가 가장 낮은 접착력을 보여주었다. IPDI와 HDI 기반 폴리우레탄 겔코트는 XDI 기반 폴리우레탄 겔코트의 접착력에 가까운 경향을 보여주었다. 극성관능기인 우레탄 그룹이 경량복합내의 불포화 폴리에스터층과 물리적인 결합력이 두 계면간 접착력에 밀접한 관계가 있다. 그러나 레저용 선박제조 과정중 선박 목업에 도포된 겔코트의 경화도가 그 다음 공정으로 진행되는 FRP 경량복합층과의 접착력에 영향을 줄 수 있다. Figure 2에서 보는 바와 같이 HDI 기반 폴리우레탄 겔코트가 가장 느린 지촉건조시간을 보이며 XDI 기반 폴리우레탄 겔코트가 가장 빠른 지촉건조시간을 보여주고 있다. XDI기반 폴리우레탄의 경우, 빠른 지촉건조로 인해 FRP 경량복합층 형성시 이미 우레탄반응이 진행되어 불포화 폴리에스터층과의 계면접착력이 감소된 것으로 판단된다. HDI 기반 폴리우레탄 겔코트인 경우, 충분한 지촉건조로 인해 두 계면간 접착력이 증가하지만, 폴리우레탄 주쇄의 유연성으로 인해 단단한 불포화 폴리에스터층과의 계면접착력이 낮아진 것으로 판단된다. 상대적으로 적절한 지촉건조시간을 가진 IPDI와 HMDI 기반 폴리우레탄 겔코트는 불포화 폴리에스터층과 적절한 계면접착력을 유지할 수 있고 고리형 화학구조로 인해 폴리우레탄 주쇄의 강직도를 증가시켜 전체적인 계면접착력을 향상시키는 것으로 판단된다.
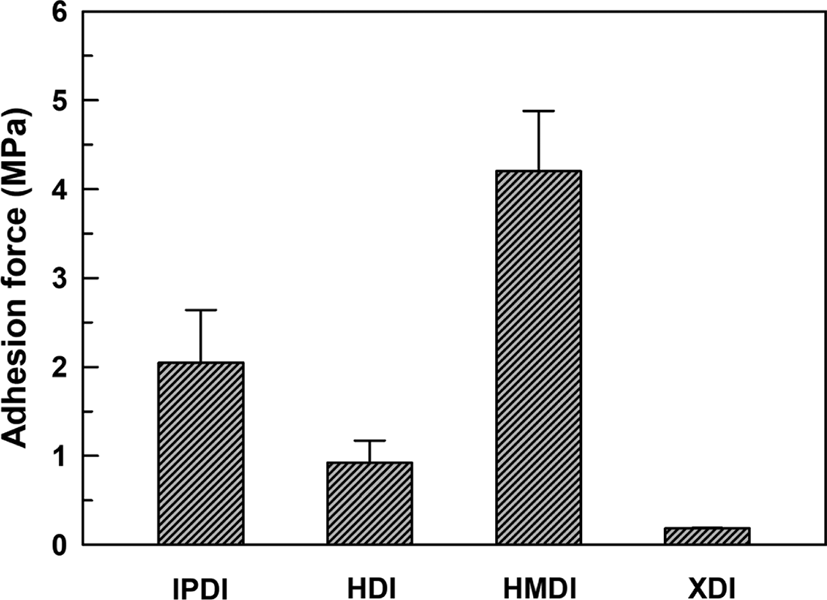
겔코트의 내후성 평가를 위하여, Xenon Arc 광에 100 시간 노출시킨 시편을 노출 전과 후의 베르거 백색도 차이를 CIELAB방법 1976 (DIN 6174)에 따라 색차계를 이용하여 측정한 결과를 Table 1에 정리하였다. 폴리우레탄 겔코트의 황변지수는 Δb*값이 대변하며, 양의값이 나타나는 의미는 외부환경에 의해 시편이 더욱 황변되었음을 나타낸다.16 본 실험에서 사용한 이관능성 이소시아네이트로 구성된 폴리우레탄 겔코트는 Table 1에서 보는 바와 같이 낮은 Δb*값을 보이며 이는 레저선박용 경량복합소재의 겔코트에 모두 적용가능함을 나타내고 있다.
Sample code | ΔL* | Δa* | Δb* | ΔE* |
---|---|---|---|---|
IPDI | -0.04 | -0.07 | 0.28 | 0.29 |
HDI | -1.89 | -0.03 | 1.27 | 2.28 |
HMDI | -0.04 | -0.11 | 0.41 | 0.43 |
XDI | -0.58 | -0.13 | 0.86 | 1.05 |
Conclusion
본 연구에서는 다양한 이관능성 이소시아네이트를 사용하여 폴리우레탄 겔코트를 제조하여 이소시아네이트의 화학구조에 따른 겔코트 코팅막의 표면강도와 인장강도 등을 측정하여 폴리우레탄계 겔코트의 내구성 및 내후성 특성을 비교 고찰하였다. 내후성 측면에서 사용한 모든 이관능성 이소시아네이트는 폴리우레탄 겔코트 제조에 적합하였다. 하지만, 지촉건조시간과 겔코트의 물리적 특성(표면경도와 인장강도)을 고려한 결과, 고리형 지방족 화학구조를 지닌 IPDI와 HMDI 기반 폴리우레탄 겔코트가 적합한 결론을 도출하였다. 이러한 결과들을 바탕으로 폴리우레탄 겔코트의 기능성 향상을 위한 연구개발에 적용할 수 있는 기본적인 데이터로 사용될 수 있을 것으로 기대한다.