Introduction
Chloroprene rubber (CR) has chlorine atoms in its skeletal form and a tendency to crystallize, and thus it shows particular characteristics such as high resistance to heat, ozone, chemical materials, and combustion, accompanied by high tensile properties.1-4 Due to its high resistance and stability, CR has been widely used in the preparation of cable and pipe coatings, tubing, O-rings, and seals and in the construction of marine structures requiring long-term stability and high resistance to corrosion by sea water.1-7 CR compounds, therefore, should preserve high mechanical properties and low deformation by external force as well as high weatherability to endure the attack of oxygen and ozone.8
In order to enhance the mechanical properties and stability of CR compounds, various fillers such as carbon black,9 silica,10 graphene oxide,11 montmorillonite,12,13 and magnesia14 have been added to them. Silica has become an important filler due to its low compression set and high stability against combustion. The particular interaction between the chlorine atoms of CR and the hydroxyl groups of silica through hydrogen bonds exempts the use of coupling agents in the preparation of silica-filled CR compounds, contrary to the preparation of silica-filled SBR and NR compounds.15,16 Although the amount of silica added to CR compounds is limited from 20 to 40 phr, the co-addition of 3-mercaptopropyltriethoxysilane of 0.7 phr significantly improves the compression set of silica-filled NSM neoprene.10 The addition of coupling agents is not essentially required for the reinforcement of CR compounds by silica, but the presence of 3-aminopropyltriethoxy silane (APTES) in them considerably enhances their hardness and modulus and lowers compression set and heat build-up.17 Bis-[triethoxysilylpropyl]tetrasulfide (TESPT), which is conventionally and widely used in the preparation of SBR tread compounds as an effective coupling agent, is also helpful to improve the mechanical properties of silica-filled CR compounds.2 In addition, the increase in silica content increases the interface between CR and silica, resulting in high modulus and tensile strength, but the silica flocculation among silica particles is also preferable with increasing silica content that causes serious deterioration of the reinforcement performance of silica.18,19 Therefore, APTES and chloropropyltriethoxysilane added along with silica partially mask the hydroxyl groups of silica particles and suppresses the flocculation, resulting in high performance silica-filled CR compounds.20
Networked silicas prepared by introducing organic connecting bonds among silica particles are very effective in reinforcing SBR compounds because of their high feasibility for entanglement of rubber chains with the connecting bonds.21-23 The entanglement induces considerable improvement of mechanical and dynamic properties even without coupling and prevents the excessive increase in stiffness caused by thermal and oxidative aging. The SBR compounds reinforced with networked silicas have lower hysteresis in dynamic deformation and exhibit better performance for the tread rubber of passenger car tires. These results suggest that the application of networked silica to CR compounds promises not only higher dimensional stability due to highly entangled rubber chains allowing reversible deformation, but also better resistance to aging treatment.
CR compounds are generally cured with sulfur and xanthogen disulfide to obtain high performance and stability.24 The cure also enhances the tear strength of CR compounds and adhesion to fiber, while their storage stability and aging properties are relatively deteriorated. In the cure of CR compounds with sulfur, zinc chloride formed by the reaction between zinc oxide and hydrogen chloride acts as an activator. The addition of magnesia accompanied by zinc oxide stably captures the hydrogen chloride formed and retards the generation of zinc chloride, maintaining the proper cure rate.25
Although the use of silica as reinforcing filler in CR compounds is a prominent research topic in developing aseismatic materials with high mechanical stability and low deformation, reports addressing the effect of silica content on their mechanical and aging properties are rare. Furthermore, the contribution of silica’s nature to their properties has not been systematically studied. In this paper, we prepared various silica-filled CR compounds reinforced with networked silicas and conventional precipitated silica. The reinforcement performance of networked silicas compared to conventional silica was discussed in the aspects of the maximum content, the dispersion of silica and the interaction between rubber and silica. In addition, their resistances to combustion, heat, oil, and ozone were also examined.
Experimental
The CR used in this study was Baypren® 210 rubber manufactured by Lanxess (Germany) with viscosity [ML (1+4) @ 100°C] of 43 ± 4 and density of 1.23 g·cm−3.
Three kinds of silica were used in preparing silica-filled CR compounds: the first (NS1) and second (NS2) ones were networked silicas prepared by MiraeSI and the third one was highly dispersive precipitated silica provided by Evonik (Ultrasil 7000GR; abbreviated as GR). NS1 networked silica contained only organic connection materials, while NS2 one contained 4 wt% TESPT accompanied by the connection materials.
Several additives such as zinc oxide (ZnO, Daewon Co.), magnesium oxide (MgO, Kyowamag, Kyowa Chemical Industry), stearic acid (S/A, Duksan Pure Chemical Co.), sulfur (S, Miwon Chemical Co.), N-cyclohexyl-2-benzothiazol sulfenamide (CBS, Miwon Chemical Co.), 1,3-ethylene thiourea (ETU, TCI), N′-phenyl-p-phenylenediamine (6-PPD, Kumho Petrochemical Co.), 3-mercaptopropyltrimethoxy silane (MPTMS, Momentive), and paraffin oil (P-2, Michang) were also added in the preparation of the silica-filled CR compounds.
The chemical compositions of prepared silica-filled CR compounds are listed in Table 1. The compounds were named by classifying the nature of silica as MS1, MS2, MS3, and GR according to the nature of silicas: MS1 indicated that the CR compounds contained NS1 networked silica with low sulfur content (0.5 phr), MS2 compounds contained NS1 networked silica with high sulfur content (2.0 phr), MS3 compounds contained NS2 networked silica with high sulfur content (2.0 phr), and GR compounds contained 7000GR silica with high sulfur content (2.0 phr). The names of the compounds, for instance, CR-MS1-xx, denoted their silica content as “xx.” The contents of other ingredients except S and TESPT were the same in phr: ZnO; 5, MgO; 4, S/A; 1.0, S; 2.0, CBS; 1.0, ETU; 0.5, 6-PPD; 1.0, MPTMS; 0.3, and paraffin oil, 10.
The silica-filled CR compounds were mixed following the procedure described in our previous paper.21 In the first step, CR, silica, paraffin oil, ZnO, and S/A were put into an internal mixer (300 cm3, MiraeSI) to prepare the initial masterbatch and mixed at a fill factor of 0.70 for 12 min. Sub- sequently, S, CBS, and ETU were added to the initial masterbatch and mixed for 2.5 min to obtain the final masterbatch. Both the initial and final masterbatches were milled for 11 cycles with a two-roll mill (C.W. Brabender Inc. Model PM-300, #138-B).
Rheocurves of the silica-filled CR compounds were recorded on an oscillating disk rheometer (Daekyung Co., DRM-100) at 155°C according to ASTM D2084. Since the rheocurves were marching types with continuously and slightly increasing torque, the cure times for 40% (t40) and 90% (t90) were calculated under an assumption that the torque of a CR compound observed at 30 min of cure was considered to its maximum torque (τmax). Minimum torque (τmin) and delta torque (Δτ) were defined by the torque minimum of its rheocurve and the difference between τmax and τmin, respectively.
The rubber compounds were obtained by curing at 155°C for t90 time with an additional 1 min in a cure press (Daekyung Co., DHP-300).
FE-SEM (Zeiss, Gemini 500) was used in the examination of silica dispersion in cured rubber compounds. The samples were sputtered with a plasma treatment system (MiraeSI) at 200 V for 75 min to selectively remove rubber.
Thermogravimetric analysis of the silica-filled CR rubber compounds was carried out using a thermogravimeter (Shimadzu, DTG-60H) in an air or nitrogen flow of 50 ml∙min−1. The temperature increased from ambient to 700°C at 5°C∙min-1.
Mooney viscosities of ML (1+4) @ 100°C of the rubber compounds were obtained with a Mooney viscometer (Dae-kyung Co., DMV-200C) following the procedure described in ASTM D1646. Scorch times at 125°C were measured by the same viscometer. The lapsed times for the increases of Mooney units by 5 and 35 were defined as t5 and t35, respectively.
The tensile properties of the rubber compounds were determined from the strain-stress curves of dumbbell type samples. The curves were recorded using a universal tensile tester (Daekyung Co., DUT-500C) at ambient temperature with a crosshead speed of 500 mm∙min−1 following the procedure described in ASTM D412. Moduli were defined by the stresses at 50%, 100%, and 200% elongation, while tensile strength and elongation at break were defined as the stress and strain at the break point, respectively. Four samples were used to obtain an average value of each tensile test. Tearing strength was also measured using the same apparatus with samples of the dimension described as ASTM D624 die C specimen by extending with a crosshead speed of 500 mm∙min−1 until its breaking. The tear strength of the sample was determined from its maximum force for breaking and three samples were used to obtain each tear strength.
A dynamic mechanical analyzer (DMA, TA Inc., Q800) was used in the measurement of dynamic properties of the compounds. The storage modulus was measured from 0.01% to 20% strain at a frequency of 1 Hz and room temperature. The Payne effect was determined from the variation of storage modulus with strain and defined as its difference between the storage modulus at 0.01% strain and that at 10% strain.
The heat build-up (HBU) of a sample with repeated strokes was measured using GABO® 200 (BF Goodrich) following the procedure described in ASTM D623. The static loaded pressure was 1.0 MPa. A stroke of 4.45 mm was repeatedly added to a sample with 30 Hz at 50°C for 25 min and measured the increase in temperature as its HBU. Compression set was also measured using the same apparatus following the procedure described in ASTM D623. Cylindrical rubber samples with a diameter of 17.8 ± 0.1 mm and a height of 25.0 ± 0.15 mm were compressed under a static force of 11 kg for 25 min at 50°C. The samples were then allowed to recover for 24 h at room temperature and their compression sets were calculated using the method described in the literature.26
The samples were thermally aged at 100°C for 72 h in an oven.27,28 For oil aging, the samples were put in a paraffin oil bath at room temperature for 7 days. The samples were exposed to ozone of 100 pphm at 50°C for 72 h in an ozone test chamber.29 The degree of enhancement of modulus or strength was defined as the changes in percentages of modulus and strengths compared to the original values before aging.
Results and Discussion
The TG curves of networked silicas show the amount of organic materials incorporated by them as well as the amount of water adsorbed on them. Figure 1 shows the TG curves of the silicas used in this study. The weight loss of GR silica without any organic materials was simple. The removal of adsorbed water caused the weight loss below 150°C, while the slightly gradual weight loss above 400°C was attributed to the removal of hydroxyl groups dispersed on its surface. The presence of organic materials in networked silicas reduced water desorption due to the consumption of their hydroxyl groups in the reaction with silane, while the presence of organic materials originated the weight loss at 200-600°C. The slightly small weight loss of NS2 networked silica below 200°C compared to that of NS1 informed the further reduction of hydroxyl groups by the incorporation of TESPT.
The presence of silica in CR compounds considerably influences the state of rubber sheets. Figure 2 shows photos of the rubber sheets of the CR compounds reinforced with silicas of different natures. The CR-GR-20 compound reinforced with GR silica of 20 phr slightly contracted after milling, while the increase in silica content to 60 phr suppressed the contraction and resulted in a good flat surface. However, a rubber sheet of CR-GR-80 could not be prepared because the rubber scattered into tiny particles. The black-gray color of CR-GR-60 might be due to the presence of stabilizers, although the cause was not certain. On the contrary, the CR compounds reinforced with networked silicas were less contractive than those reinforced with GR silica. Moreover, the content of networked silica increased to 80 phr without applying any special mixing apparatuses or methods. The rubber sheets of CR-MS2-80 and CR-MS3-80 were very good, without any unevenness at their edges, even though their silica contents were considerably high, indicating that networked silicas were more appropriate as reinforcing filler for CR compounds with higher silica contents.
The increase in silica content may cause silica aggregation during mixing and cure. Figure 3 shows SEM images of silica-filled CR-MS1 compounds with different contents of silica after plasma sputtering to remove soft rubber.30 Voids previously filled with rubber were spread among silica aggregates of less than 50 nm. The decrease in voids with increasing silica content indicated that the increase in silica content increased the surface occupied by silica. The slight increase in the size of aggregates of CR-MS1-80 indicated that silica flocculation occurred on the rubber compound with extremely high silica content. Figure 4 shows SEM images of CR-GR compounds obtained after plasma sputtering. The silica aggregation was obvious on CR-GR-20 with a low silica content, 20 phr. The weak interaction between silica and rubber chains allowed the segregation of silica particles, while the entanglement of rubber chains with the connection bonds of networked silica suppressed the aggregation on CR-MS1-20 compound (Figure 3). Similar SEM images of CR-MS1-40 and CR-GR-40 indicated that the effect of the nature of silica on its dispersion was appreciable when silica content was low or high.
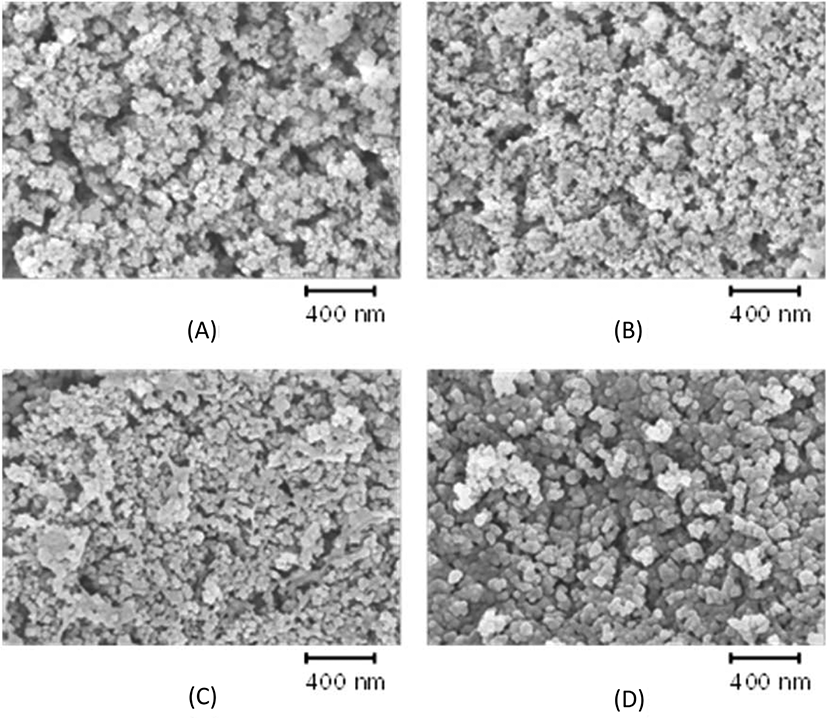
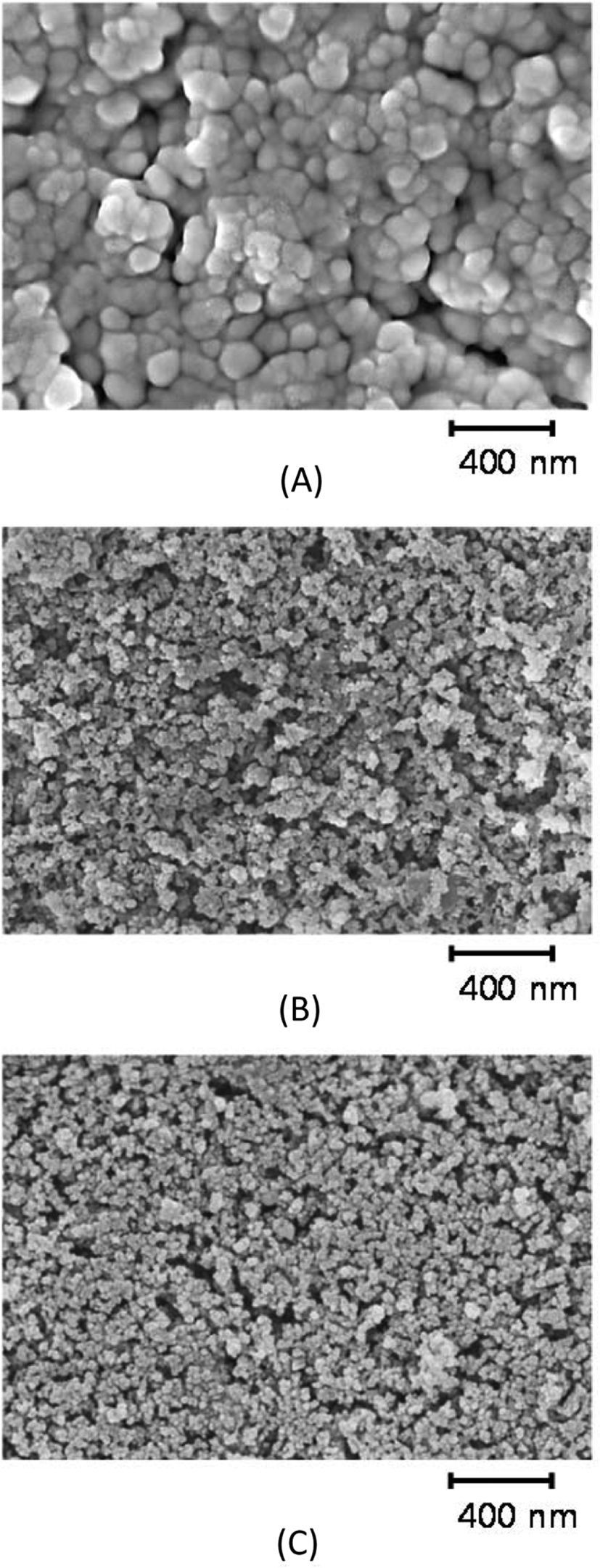
Figure 5 shows TG and DTA curves of the CR compounds recorded in nitrogen. The weight loss of CR compounds occurred through several steps, while their general patterns of weight loss were very similar, regardless of silica nature. The first weight loss proceeded at 250-320°C, the second one at 380-450°C, and the third one above 580°C. Since the first and second pyrolysis temperatures of CR (Baypren 210) without any filler were reported at 378.3 and 448.9°C, respectively,31 the first weight loss observed at around 310°C was attributed to the vaporization of remaining monomers and oligomers of dichlorobutadiene, and the additives freely remaining in rubber.32 Since the pyrolysis eliminating hydrogen chloride begins at 380°C with CR, the second weight loss was attributed to this elimination. The gradual weight loss above 550°C might be due to the decomposition of residual rubber, including the second pyrolysis of CR. The similar TG and DTA curves of the silica-filled CR compounds represented no significant difference in the elimination and pyrolysis of CR compounds, regardless of the nature of silica. However, the first endothermic peaks of CR-GR-60 were observed at 309°C, while those of CR-MS2-60 and CR-MS3-60 were observed at 325°C, indicating that the removal of monomer and additives occurred at higher temperatures with CR-MS2-60 and CR-MS3-60 than that of CR-GR-60. The weight loss occurred at higher temperature with CR compounds reinforced with NS1 and NS2 networked silicas than that reinforced with conventional silica, suggesting that networked silica was more effective in preserving the monomer and additives in them and in increasing their stability.
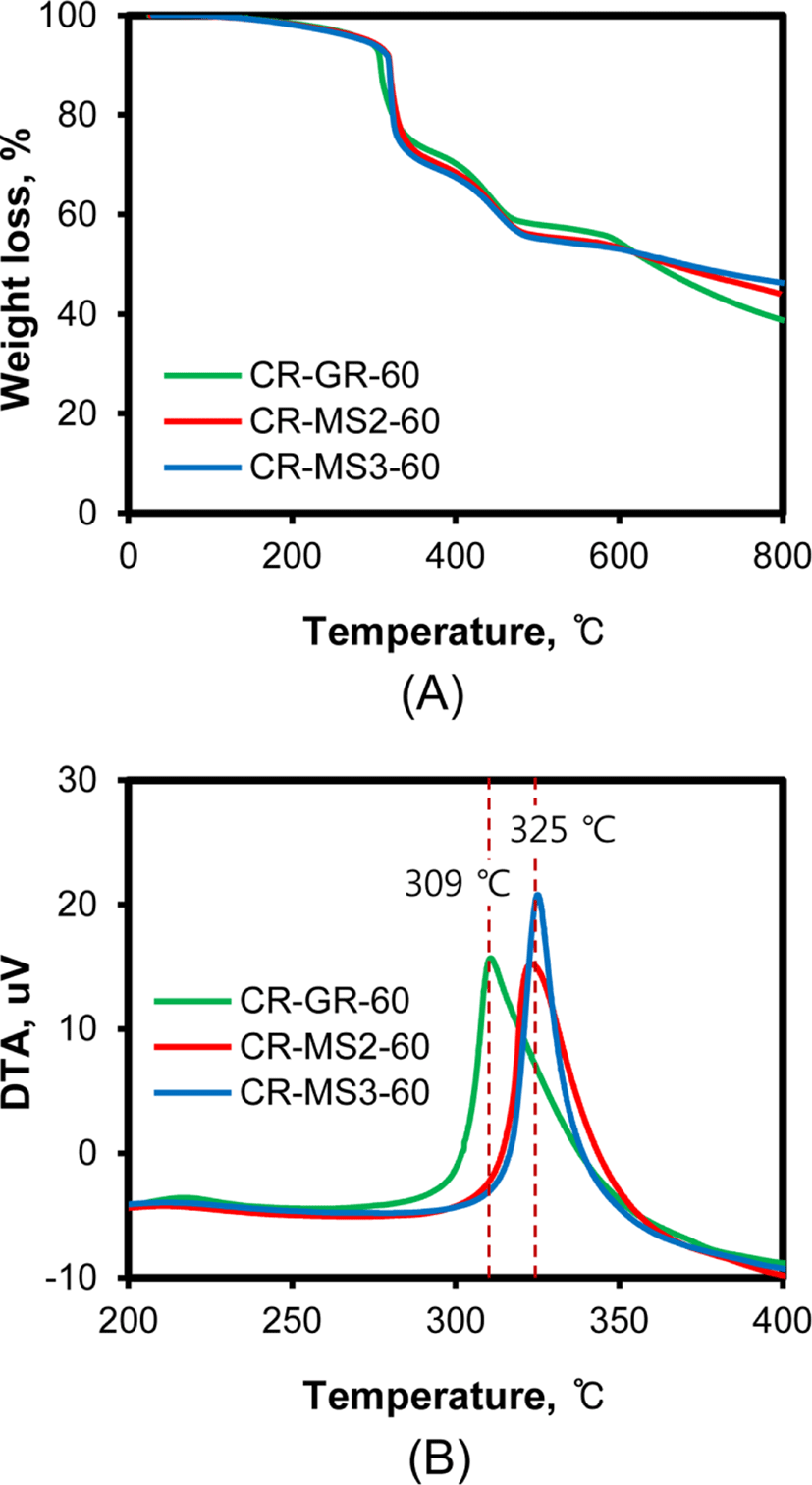
The presence of silica in CR compounds increases their resistance to combustion because silica is an inherently noncombustible material.32Figure 6 shows the TG and DTA curves of CR compounds reinforced with conventional silica and networked silica recorded in air. The stepwise weight loss with temperature was very similar, regardless of silica nature, and the increase in silica content gradually reduced weight loss. The weight losses below 450°C were similar to those observed on TG curves recorded in nitrogen (Figure 5). The large weight loss above 450°C was attributed to the combustion of rubber, so the remaining weight above 700°C was directly proportional to the content of silica. Although the general patterns of TG curves were very similar, the temperatures for the first weight loss of silica-filled CR compounds were considerably different according to the nature of silica, as shown in Figure 6(C) and 6(D). The peak maximum temperature of CR-GR compounds was 314°C, while that of CR-MS3 compounds shifted to a higher temperature of 322°C. These results demonstrated the strengthened preservation of the monomer and additives in CR compounds reinforced with networked silica, because the entangled rubber chains with the connection bonds of networked silica prevented their desorption from CR compounds followed by combustion.
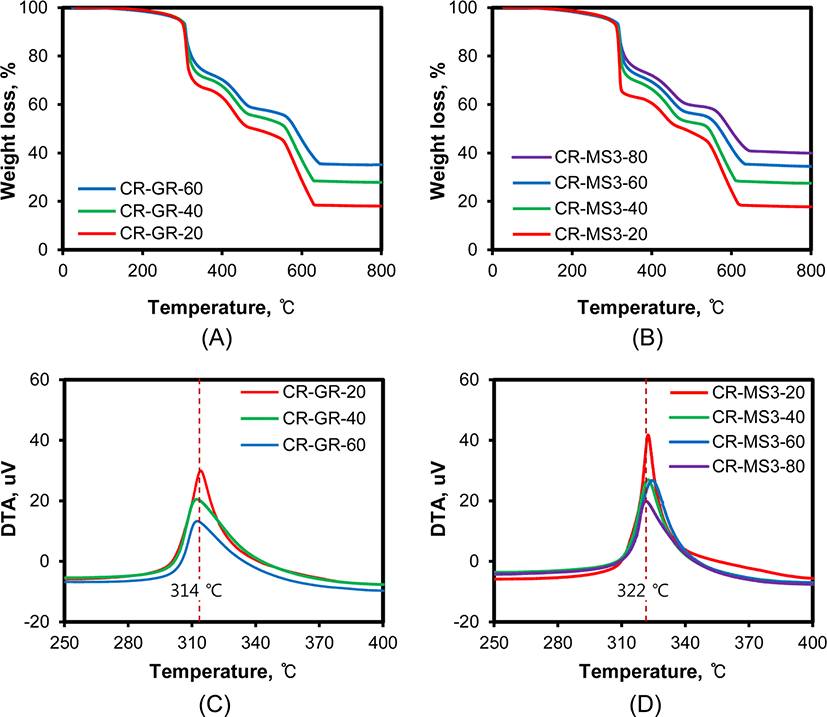
Since the increase in torque during cure directly corresponds to the formation of crosslinks, the coupling between rubber and silica, and silica flocculation, the effect of silica addition on the rheocurves of CR compounds must be great. Figure 7 shows the rheocurves of the silica-filled CR compounds with different silica contents. The rheocurve of CR-Si-00 compound without silica was a marching type, and the very slow increase in torque around 30 min indicated the approach to cure equilibrium.15 The CR compounds reinforced with silica also exhibited marching rheocurves, with a continuous increase in torque even after 30 min. However, the level of torque varied considerably with the nature and content of silica. The torque of CR-GR compounds reinforced with GR silica of 20 and 40 phr remained very low at the beginning of cure, slowly increased after an induction period, and steadily increased without accomplishing the end of cure. In contrast, the torque of CR-GR-60 was very high even in the early stage of cure and steadily increased with cure time. The rheocurves of the silica-filled CR compounds reinforced with silica of 20 and 40 phr were very similar in terms of low τmin and slow increase in torque regardless of the nature of silica, while those of CR compounds reinforced with silica of 60 and 80 phr were considerably different according to the nature of silica added. The τmin of CR-GR-60 was very high compared to that of CR-GR-40, indicating that the increase in the content of silica from 40 phr to 60 phr induced significant silica flocculation in the early stage of cure. In contrast, the τmin of CR-MS3-60 reinforced with MS3 networked silica containing TESPT in it was much lower than those of CR-GR-60 and CR-MS2-60. Although the increase in silica content of CR-MS3 compounds from 60 to 80 phr caused a considerable increase in τmin, τmin of CR-MS3-80 was still low compared to that of CR-GR-60, CR-MS1-80, and CR-MS2-80. These results indicated that the suppression of silica floccu-lation by TESPT involved in CR-MS3 compounds effectively maintained both their low τmin and τmax.19 The CR-MS3 compounds also retained their low τmin, while the absence of TESPT induced silica flocculation and high torque in the early stage of cure. The continuous increase in torque with cure time for all silica-filled CR compounds suggested the slow formation of the interaction between the chlorine atoms of CR and the hydroxyl groups of silica.15 The intrusion of rubber chains into the voids formed among silica particles during cure resulted in the formation of the new interaction that caused the increase in torque.
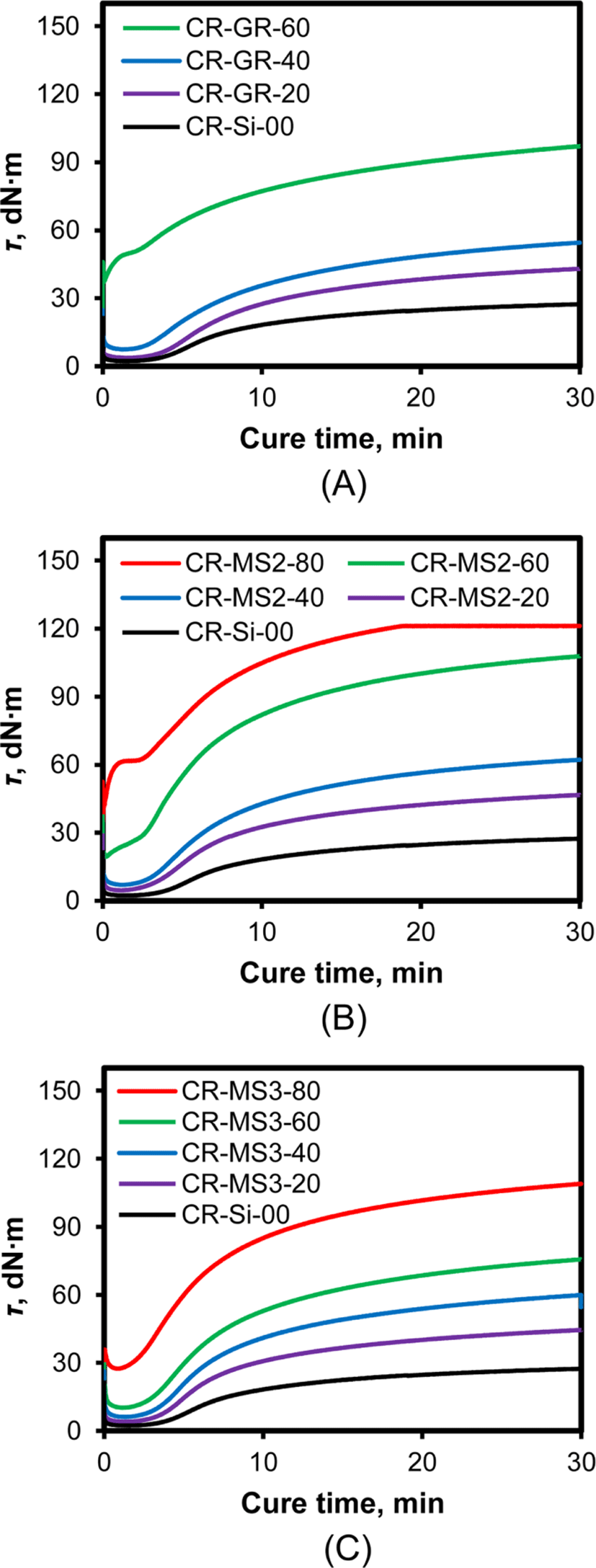
The silica added to CR causes the interaction between the chlorine atoms and the hydroxyl groups of silica, and the interaction strongly influences the level of torque during cure. Figure 8 shows the variations of τmin and Δτ of the silica-filled CR compounds with their silica content. τmin and Δτ of CR-MS1-80 were not shown because of their high fluctuation. The increases in silica content commonly increase their τmin, regardless of the nature of silica, but the degree of the increase in τmin above silica content of 40 phr varied considerably with the nature of silica. Since the value of τmin usually represents the extent of silica flocculation during mixing,33 concomitantly low τmin of CR compounds with silica content of less than 40 phr indicated their low extent of silica flocculation. However, the increase in silica content above 40 phr causes a difference in the extent of silica flocculation during cure, and thus, τmin of CR-GR-60 was much higher than those of CR-MS1-60, CR-MS2-60, and CR-MS3-60. The extremely high τmin of CR-GR-60 indicated a high extent of silica flocculation during mixing, but the low τmin of CR-MS3-60 implied that the organic connection materials dispersed on networked silica suppressed its silica flocculation. The absence of TESPT in CR-MS2-60 caused a considerably higher τmin than that of CR-MS3-60, indicating that TESPT was important in the suppression of silica flocculation.34 The higher τmin of CR-MS3-80 and CR-MS2-80 indicated that silica flocculation became severe when silica content was too high, even though they were reinforced with networked silicas.
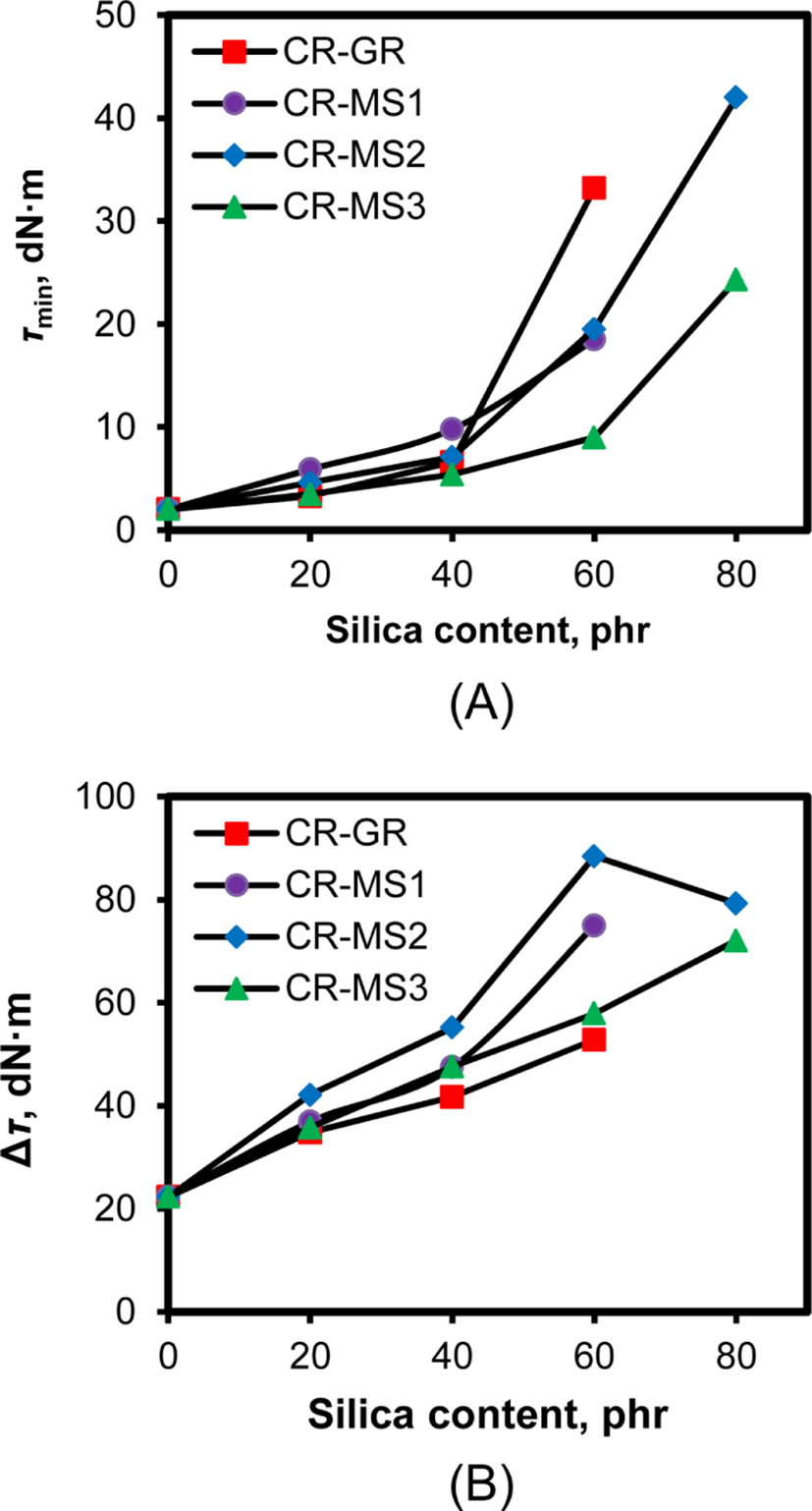
The increase in torque of silica-filled CR compounds during cure results from several causes such as the crosslinking of rubber, silica flocculation, the coupling between rubber and silica, and the interaction between chlorine atoms and hydroxyl groups, and thus their Δτ generally increased with increasing silica content (Figure 8B). However, the degree of the increase in Δτ was different according to the nature of silica used for the reinforcement of CR compounds. CR-MS2 compounds reinforced with NS1 silica that contained a sufficient amount of sulfur showed the highest Δτ throughout the range of silica content from 20 to 80 phr, while CR-GR compounds reinforced with conventional silica exhibited the lowest Δτ. This meant that the presence of the networks among silica particles and sufficient cure achieved high Δτ. In contrast, the relatively low Δτ of CR-MS3 compounds compared to those of CR-MS2 suggested that the low Δτ of the former might be responsible for the suppression of silica flocculation by TESPT, not for low interaction between rubber and silica. Therefore, a quantitative explanation of the differences between Δτ according to the nature of silica could not derived because many causes were involved in determining Δτ, as mentioned before. However, the high Δτ of CR-MS2 compounds showed their high likelihood to be enhanced mechanical properties with prolonged cure.
The specific interaction between the chlorine atoms of CR and the hydroxyl groups of silica in silica-filled CR compounds reduces the mobility of rubber chains in them, so the increase in silica content inevitably increases their viscosity. Figure 9 shows the variations of Mooney viscosity and Payne effect of the silica-filled CR compounds with their silica content. The viscosity gradually increased with the increase in silica content, regardless of the nature of silica, indicating that viscosity was actually determined by the specific interaction. The slightly low viscosity of CR-MS3 compounds might be due to the reduction of hydroxyl groups in reacting with the TESPT contained in them. The Payne effect of the silica-filled CR compounds also increased with silica content, like their viscosity, confirming that the silica flocculation-inducing Payne effect was mainly dependent on silica content.
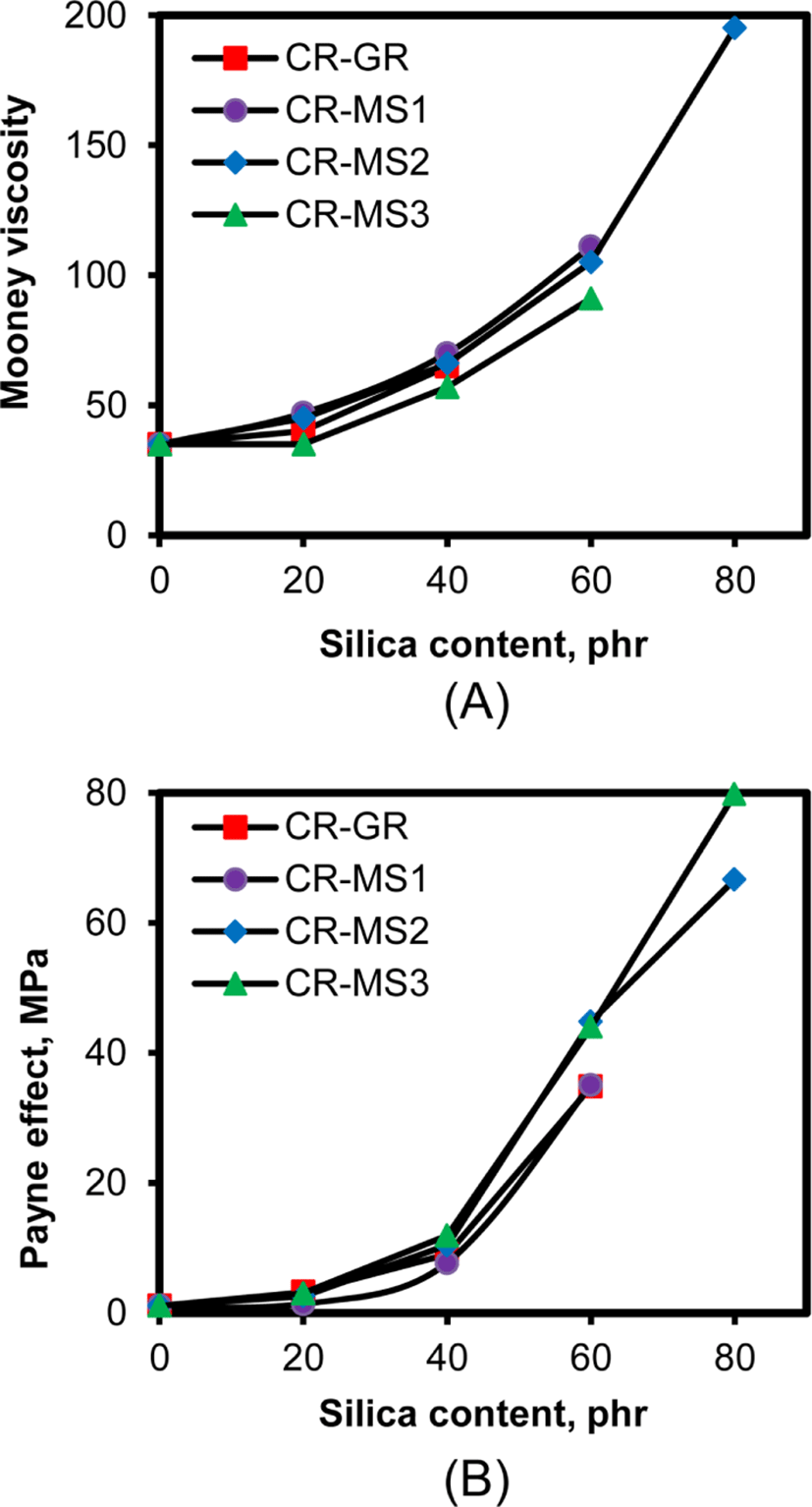
The tear and tensile strengths at break of rubber compounds reflect their fatigue properties determined by the initiation and propagation of cracks in rubber. Figure 10 shows the variations of tear and tensile strengths of the silica-filled CR compounds with their silica content. The tear and tensile strengths of the compounds concomitantly increased with silica content when their silica content was less than 40%, regardless of the nature of silicas, indicating that the increase in the interaction between CR and silica contributed to the increase in these strengths. However, the breakage of silica aggregates formed through silica flocculation on the compounds with higher silica contents caused a decrease in these strengths. The decrease in these strengths became distinct when their silica content was higher than 60 phr.
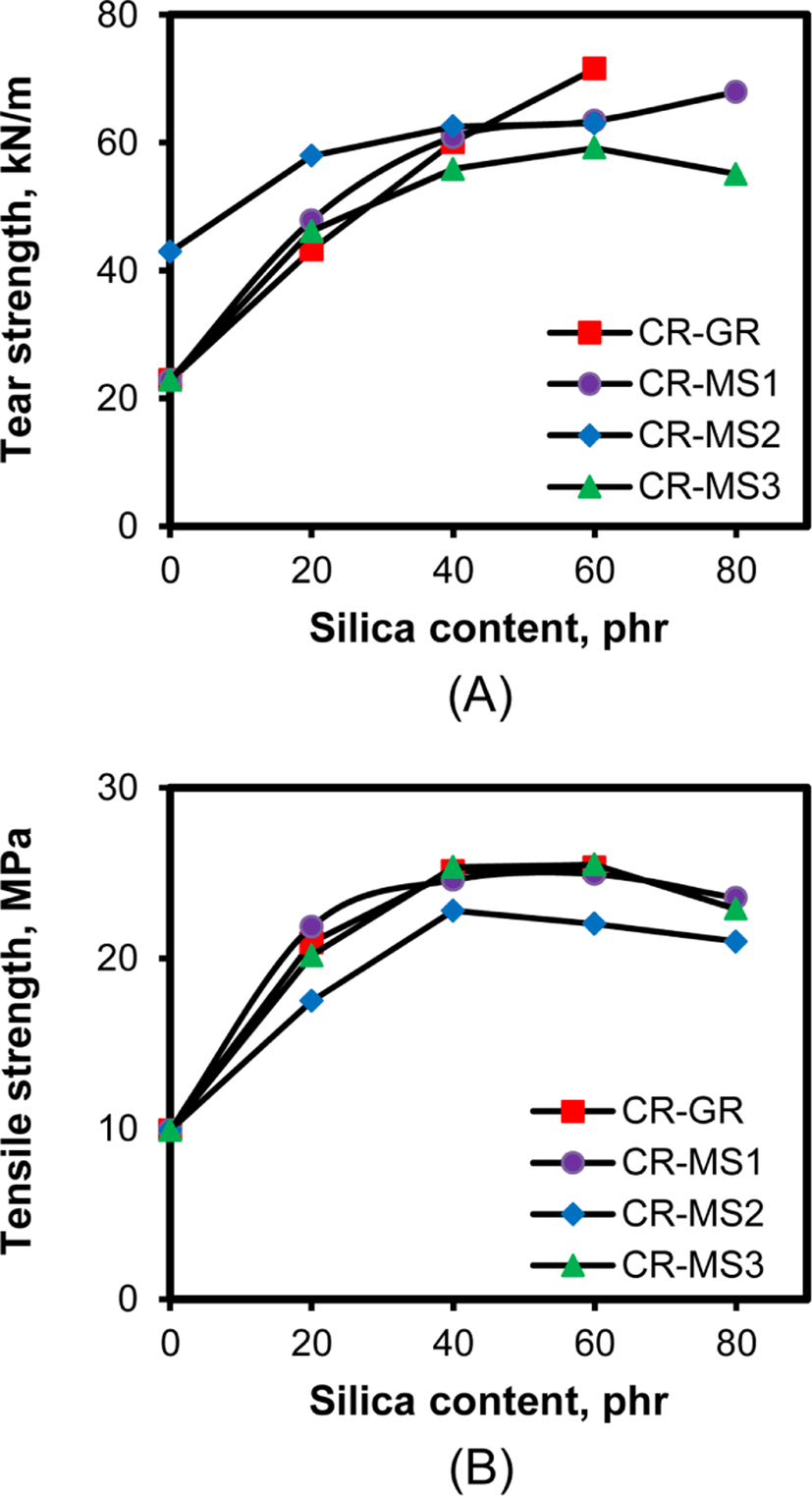
The interaction between the chlorine atoms of CR and the hydroxyl groups of silica also enhances the modulus of the silica-filled CR compounds.15Figure 11 shows the variations of M-200% and E.B. of the silica-filled CR compounds with their silica content. As expected, the increase in silica content proportionally increased M-200% regardless of the nature of silica added as reinforcing filler. The M-200% of CR-Si-00 was 1.6 MPa, but that of CR-MS3-80 was 20.6 MPa, increasing by more than 10 times. Their values of M-50% and M-100% similarly increased with increasing silica content to those of M-200%, but are not shown here for clarity. The similar increase in modulus with silica content suggested that modulus was mainly dependent on the interaction. The higher moduli of CR-MS3 than those of CR-MS2 compounds, when their silica contents were above 60 phr, indicated the contribution of TESPT to the increase in modulus. The elongation at break of the compounds gradually decreased with the increase in silica content due to the increase in their modulus.
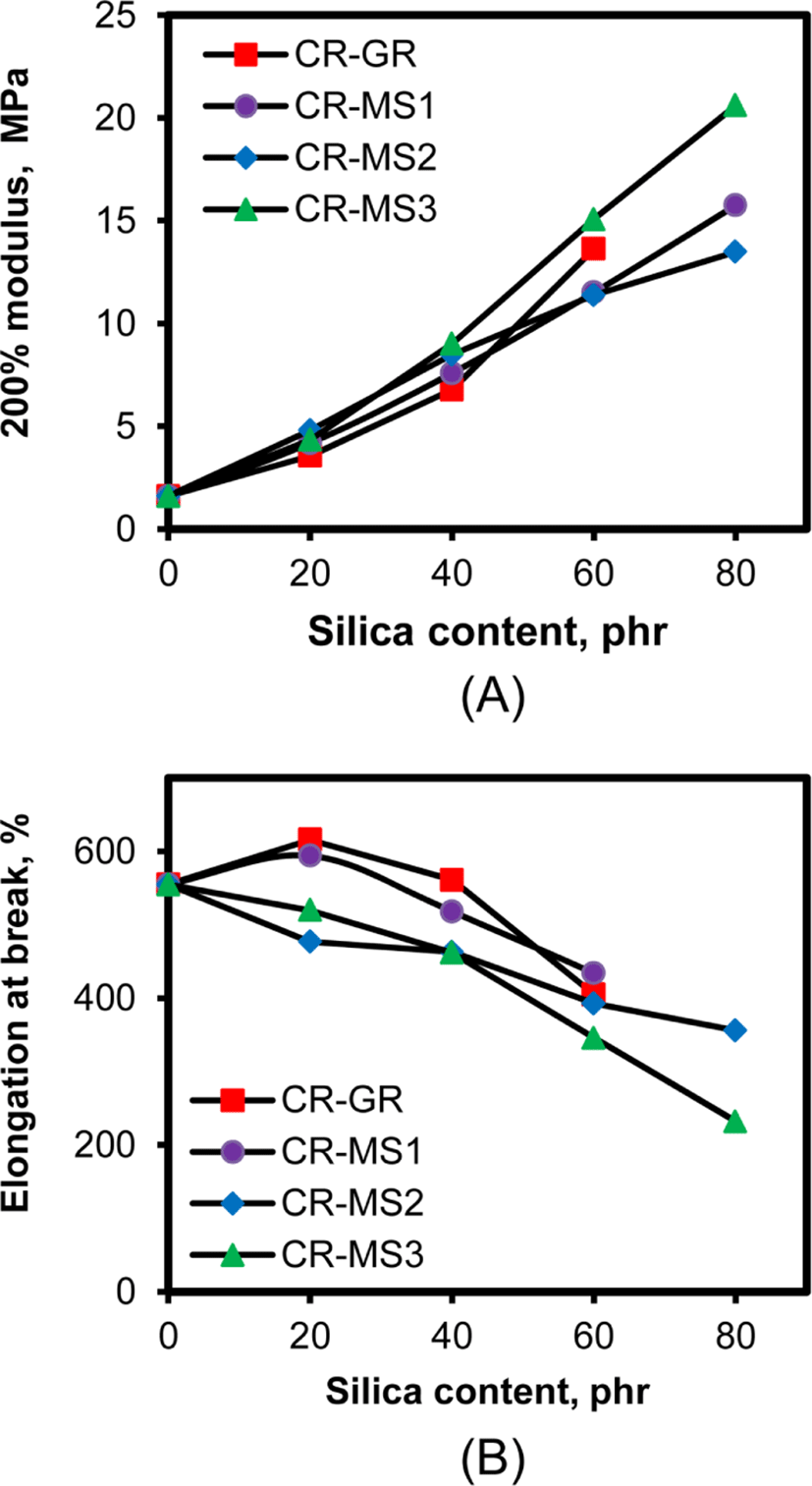
For the application of CR compounds as seals or O-rings,35 low HBU and compression set are required for the stable preservation of their dimensions under a repeatedly applied external force. Figure 12 shows the variations of HBU and compression set of the silica-filled CR compounds with their silica content. The increase in silica content gradually increased the HBU of the compounds. No appreciable difference in HBU value was observed for the rubber compounds when their silica content was less than 40 phr, regardless of the silica nature. However, the HBU of the CR compounds reinforced with networked silicas of 60 phr were slightly low compared to that of CR-GR-60 compound, and the further increase in silica content to 80 phr did not cause significant increases in HBU. The slightly low HBU of the CR compounds indicated that the physically entangled rubber chains with their connection bonds were beneficial for reducing heat generation leading to irreversible deformation.
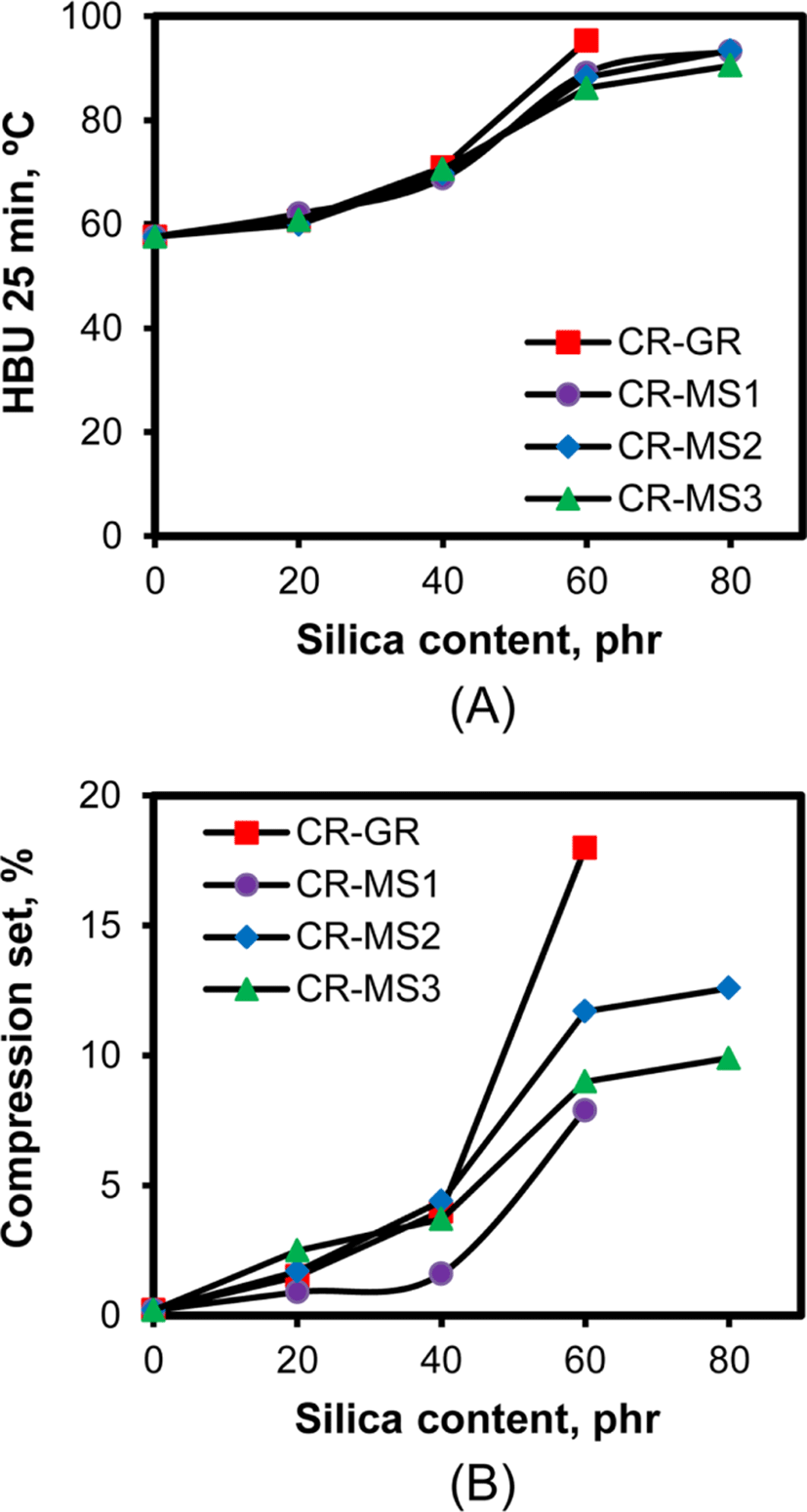
The compression set of the silica-filled CR compounds also increased with the increase in silica content, like HBU, because the presence of silica restricted the reversible deformation of rubber chains. The interesting thing was the considerably lower compression sets of CR-MS compounds reinforced with networked silicas of 60 phr than that of CR-GR-60, preserving their dimensions against external force. The small increases in compression set with the increase in silica content from 60 to 80 phr of CR-MS compounds exhibited the high feasibility of the application of networked silicas in the preparation of CR compounds for sealing products.
High resistance to aging from heat, oil, and ozone is necessary for the use of CR compounds in seals, O-rings, and impact-proof materials.36Figure 13 shows changes in the moduli of silica-filled CR compounds with 60 phr silica after thermal, oil, and ozone aging. Most moduli of the CR compounds were enhanced with the aging treatment, while the degree of enhancement varied considerably with the nature of silica and the type of aging. The degree of modulus enhancement with aging treatments was the highest with CR-MS2-60 compounds, especially after oil aging treatment. The CR compounds reinforced with MS1 networked silica with a low content of sulfur and with MS3 networked silica containing TESPT showed similar aging behavior to those reinforced with GR silica. The high preservation of CR-MS2-60 might be related to its high Δτ, as mentioned before. Simple networks among silica particles without TESPT, but with a sufficient content of sulfur, were beneficial for the preservation of modulus of CR-MS2 compounds under thermal, oil, and ozone aging.
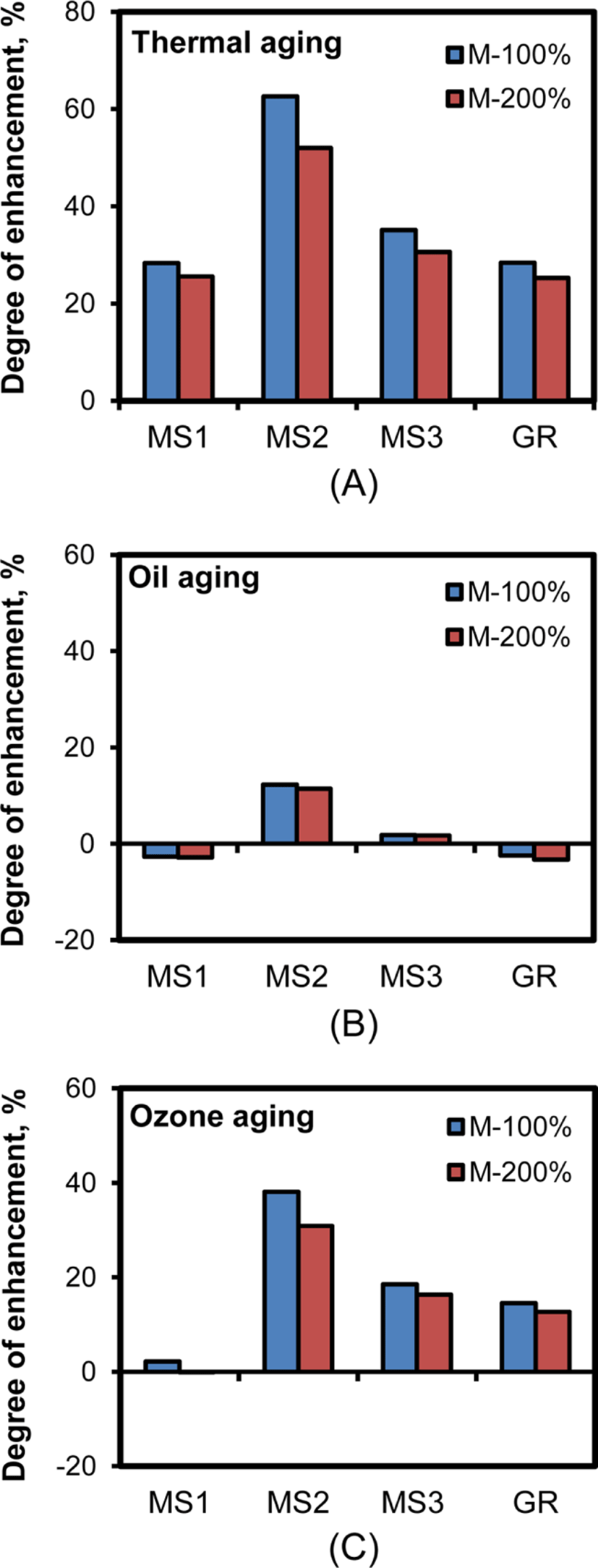
Contrary to the moduli of the silica-filled CR compounds, their tear and tensile strengths decreased with thermal, oil, and ozone aging, as shown in Figure 14. Only CR-MS2-60 consistently maintained enhanced tensile strength after thermal, oil, and ozone aging, while its tear strength decreased after the aging treatments. These results meant that the CR compounds reinforced with networked silica were effective in preserving their moduli and tensile strength during aging treatment. Furthermore, the higher resistance of CR-MS2-60 to aging properties than that of CR-MS1-60 indicated that the appropriate content of sulfur was important to achieve strong preservation of the physical properties of silica-filled CR compounds.
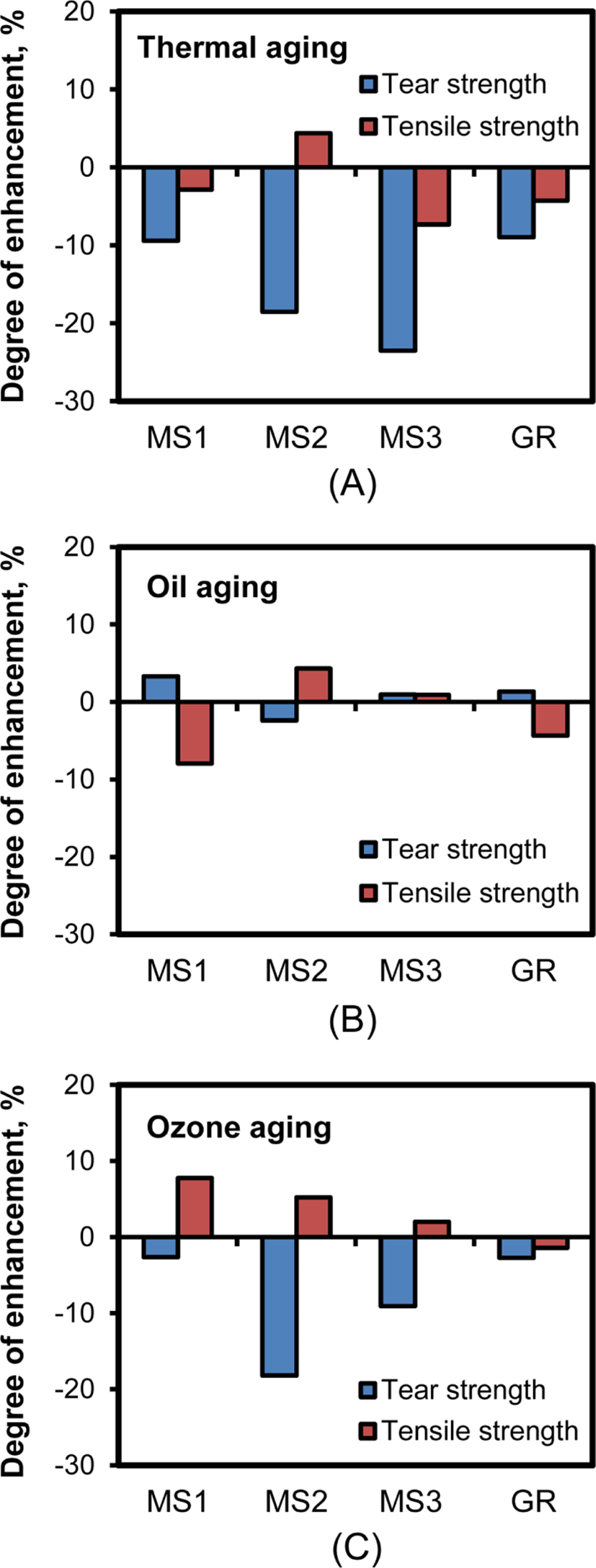
Conclusions
Since the particular interaction between the chlorine atoms of CR and the hydroxyl groups of silica mainly determines the behavior of silica-filled CR compounds, the increase in silica content results in the increases of their viscosity, modulus, tear and tensile strengths, and Payne effect. The increase in silica content to 80 phr for the CR compounds reinforced with networked silicas allowed the achievement of their high moduli. The application of networked silica to CR compounds, enabling the physical entanglement of rubber chains with the connection bonds of silica particles, has some advantages to suppress irreversible deformation under external force, resulting in a low compression set and HBU. The entanglement also retarded the weight loss of the CR compounds and improved their thermal stability. The CR compounds reinforced with networked silica and cured with a sufficient content of silica maintained a high level of modulus even after thermal, oil, and ozone aging compared to those reinforced with GR silica.