Introduction
In the past few years, there has been a growing interest in natural substances that can be used as a component in the synthesis of polyurethanes.1 This is due to the environmental problems with disposing of waste materials and the harmful effects on non-renewable resources that are being heavily used.2 It should be noted that the renewable resources can potentially replace their synthetic counterparts without worsening the properties of the final products.3 Thermoplastic polyurethanes (TPUs) possess excellent properties such as high tensile strength, high flexibility, high abrasion resistance, good adhesion, transparency, etc.4 Furthermore, these materials are characterized by higher tensile modulus, and better abrasion resistance and oil/solvent resistance compared to rubber. TPUs can be synthesized by a “one-shot” or “two shot” method as a result of the reaction between di-isocyanate, polyol and glycol.5 TPUs are composed of hard and soft segments. Soft segments are built of polyol (long chain diols), and their glass transition temperature is much lower than room temperature.6 Hard segments are derived from diisocyanate and short chain diols. The glass transition temperature of hard segments is higher than that of soft segments, and it is above the temperature at which these materials are usually used.7
In this research, Bio-based polyester polyol had been synthesized by esterification method with azelaic acid and isosorbide. After esterification reaction, the bio-based polyurethanes were synthesized by polyester polyol, 1,3-propanediol as chain extender, and isocyanate (4,4’-diphenylmethane diisocyanate) with mixing ratios of 1:1:1.5, 1:1:1.8, 1:1:2, and 1:1:2.3. They were investigated the influence for different isocyanate contents in the synthesis process on chemical structure, mechanical properties, and dynamic viscoelastic properties of thermoplastic polyurethanes. Moreover, the chemical resistance was also determined.
Experimental
1,3-propanediol (1,3-PD, 99%, Daejung Co.), bio-azelaic acid (Emerox 1144, 89%, Emery Olechemicals), Isosorbide (90%, Covestro Chemical), and 4,4’-methylenebis phenyl isocyanate (MDI, 99%, Dongyang Chemical) were shown in Table 1, and the nitrogen gas which used as protect gas in polyester synthesis process was from Daesung Co.
The mechanism for polymerization of bio based-polyester polyol was shown in Scheme 1. A typical polymerization reaction was carried out as following: azelaic acid powder and isosorbide were poured into the reaction system with a molar ratio of 1:1.2, The mixture was stirred by a magnetic stirrer at 400 rpm. And first 4 h, it was controlled below 200°C with atmosphere of nitrogen, and next 4 h, raised the temperature of 230°C and dropped stannous octoate9,10 as catalyst, and last 4 h, removed the nitrogen atmosphere and set the vacuum system (2 torr) with the temperature of 160~180 °C, then cooled down the system temperature below 60°C, and the polyester polyol in this research had been synthesized.
The polyurethane polymerization raw materials ratios were shown in Table 2. Polyols, diisocyanates and chain extender had been poured into reaction system, stirred with 200 rpm at room temperature, and got the products.
Sample | Amount | Unit: mol ratio | |
---|---|---|---|
PE | 1,3-PD | MDI | |
![]() |
![]() |
![]() |
|
TPU 1 | 1 | 1 | 1.5 |
TPU 2 | 1 | 1 | 1.8 |
TPU 3 | 1 | 1 | 2 |
TPU 4 | 1 | 1 | 2.3 |
The chemical structure of the obtained bio-based polyester polyol and thermoplastic polyurethanes was investigated by means of Fourier transform infrared spectroscopy. The infrared spectra were recorded with a Perkin Elmer Spectrum 100®, with 64 scans and a resolution of 4 cm−1. The spectra was registered at room temperature for the wavenumbers between 650 and 4000 cm−1.
Thermal Gravimetric Analysis (TGA) results of the bio TPUs was performed using a TA Instruments TGA Q500 V20 from 30 up to 800°C, at a heating rate of 10°C/min and under nitrogen flux (200 mL/min).
Differential Scanning calorimetry (DSC) results were characterized by TA Instruments DSC Q20 V24 from −50 to 150°C at a heating rate of 10°C min−1 under nitrogen atmosphere with 2 round cooling and heating processes.
The molecular weights of bio-based polyurethanes were determined by gel permeation chromatography analysis (Waters, USA, ACQUITY APC Core System) using THF/DMF (1:9) as the mixture solvent.
Tensile testing was carried out at room temperature with a Tinius Olsen H5KT-0401 universal testing machine with cross-head speed 500 mm/min, in accordance with ASTM D412. The tensile strength, elongation at break, modulus at 100% and 300% elongation, and the Young’s modulus of the prepared materials were determined. The recorded results were averages of five independent measurements.
The hardness of the bio-based thermoplastic polyurethane samples was measured by using a Shore type A Durometer at room temperature, in accordance with the ASTM D22-40 standard. The presented results were averages of ten random points per one type of sample.
The viscoelastic properties were determined with a rubber process analyzer (RPA-V1, U-Can Dynatex Inc., Taiwan. The strain sweep test from 0.01 degree to 20 degrees was operated at 60°C and 1 Hz, and the frequency sweep mode was hold on from 1 to 120 cpm, at the temperature of 60°C and at the strain amplitude of 1 drgree according to ASTM D 6204-97.
Results and Discussion
The FT-IR spectra of bio-based polyester polyol and bio TPUs were shown in Figure 1. Compared to the curve of PE, the typical peaks of polyurethane had appeared at about 1735 cm−1 for amide I, >C=O stretching vibrations, 1550 cm−1 for amide II, >C-N stretching and -N-H bending character, 3440 cm−1 for -NH stretching vibrations,11 and 1050 cm−1 for -O-C=O stretching of ester/urethane groups into the curves of TPU 1, 2. 3 and 4, but with the ratio of isocyanate increased, the peak of -C=O stretching frequency showed a gradual shifting from 1735 cm−1 to 1710 cm−1,12 the probable reason could be explained as: with the increased of isocyanate ratio, the hard segment had been also increasing, and resulted the improvement of H-bonding effect, which could cause the wavenumber of -C=O group decreased.13
Figure 2 and Figure 3 showed the results of TGA test, from these figures, it could be found with the increasing of isocyanate ratio, there were more and more inflexion in curves of Weight (%) vs Temperature (°C), and the thermal decomposition temperature had been decreased before 400°C, but after 400°C, the third thermal decomposition peak had been raised, but the deriv. weight value decreased, which meant under the high temperature (> 400°C), the TPU 4 showed the best thermal decomposition resistance in this test.
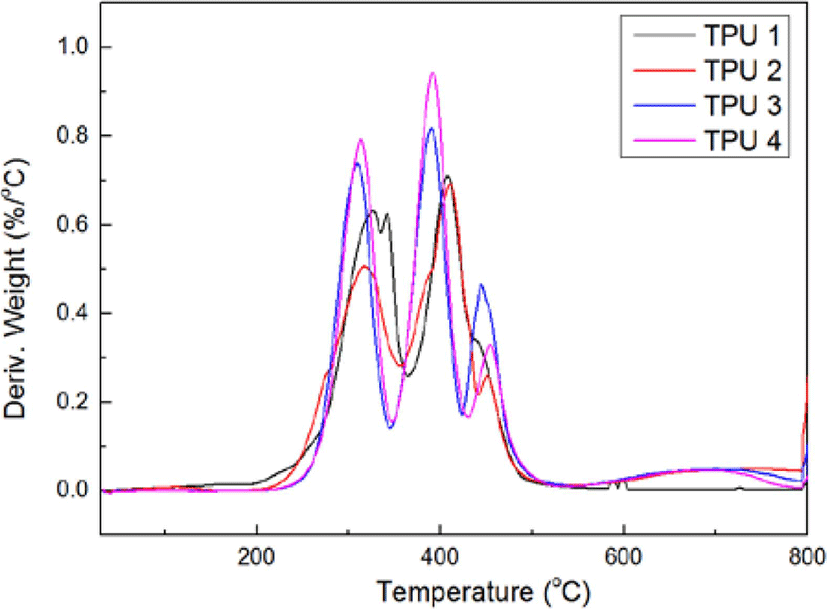
Figure 4 presented the results of DSC, the curves were the results of 2nd round heating process, with the ratio of isocyanate increasing, the inflexions had been turned to the right, which meant the Tg of bio TPUs increased, the probable reason is due to the ratio of hard segment of TPU molecular which synthesized by polyester polyol, the more ratio of hard segment (MDI-BD) in the molecular of bio TPU, the more hardness value, the higher Tg; and the more ratio of soft segment (PE), the less hardness value, the lower Tg.14
Table 3 showed the GPC results of all the bio TPU samples, from this table, it could be found with the ratio of isocyanate increasing, the Mn, Mw, Mz and Mz+1 also increased, because with the hard segment ratio increased, the molecular also became larger, so the molecular weight also turned to larger. And PDI decreased with the increasing of isocyanate ratio, which meant high isocyanate ratio could cause uniform and narrow molecular weight distribution.15
Sample | TPU 1 | TPU 2 | TPU 3 | TPU 4 |
---|---|---|---|---|
Mn (Daltons) | 29740 | 34150 | 42946 | 46597 |
Mw (Daltons) | 39820 | 48400 | 69725 | 71052 |
PDI | 1.62 | 1.42 | 1.33 | 1.21 |
Figure 5 showed the results of hardness, it could be found TPU 4 had the largest hardness value, it could be interpreted as the more content of hard segment, the larger hardness value, TPU 4 had the most hard-segment (MDI-BD) ratio, thus, it showed the largest value of hardness in this research, and with the ratio of isocyanate decreased, the hardness value also turned to less.
Figure 6 and Figure 7 showed the results of dynamic strain sweep (storage modulus and loss factor), it could be found with the increasing of isocyanate ratio, the storage modulus also increased, and the loss factor decreased.
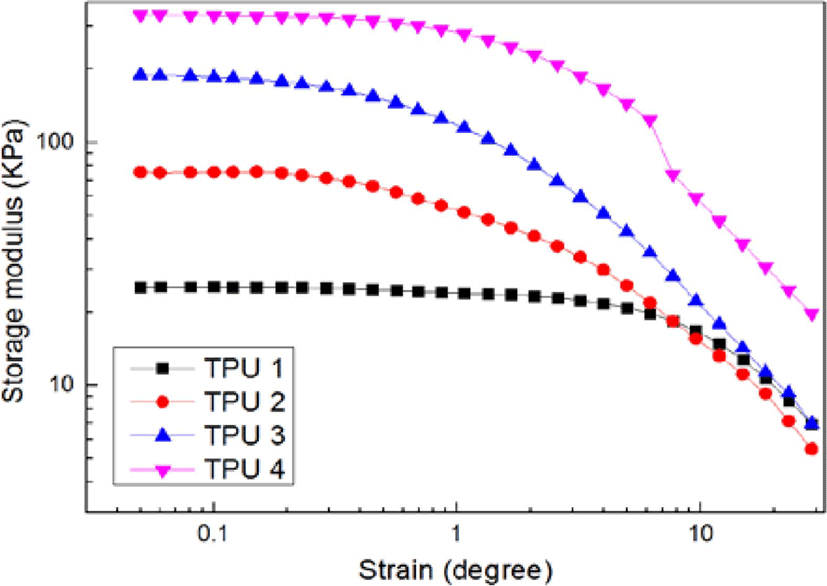
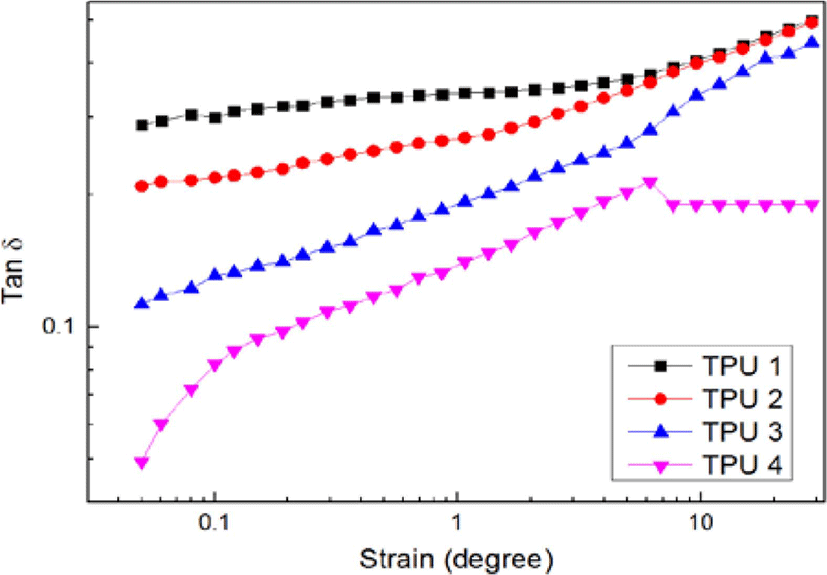
Figure 8, Figure 9 and Figure 10 showed the results of dynamic frequency sweep (storage modulus, complex viscosity and Cole-Cole polts of η* vs. η′), from the results of storage modulus, it could be found TPU 1, TPU 2 and TPU 3 showed a downward trend from low frequency range to high frequency range, but as TPU 4, it still showed a upward trend during all the test process, it was due to the high ratio of isocyanate increased the hardness of bio TPU material, which also could increase the stability of structure, and caused higher destruction resistance in this test.16
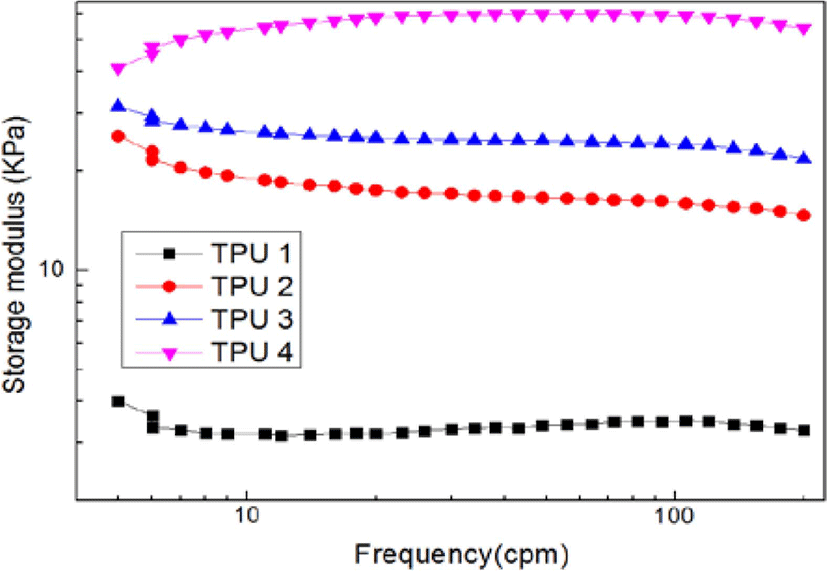
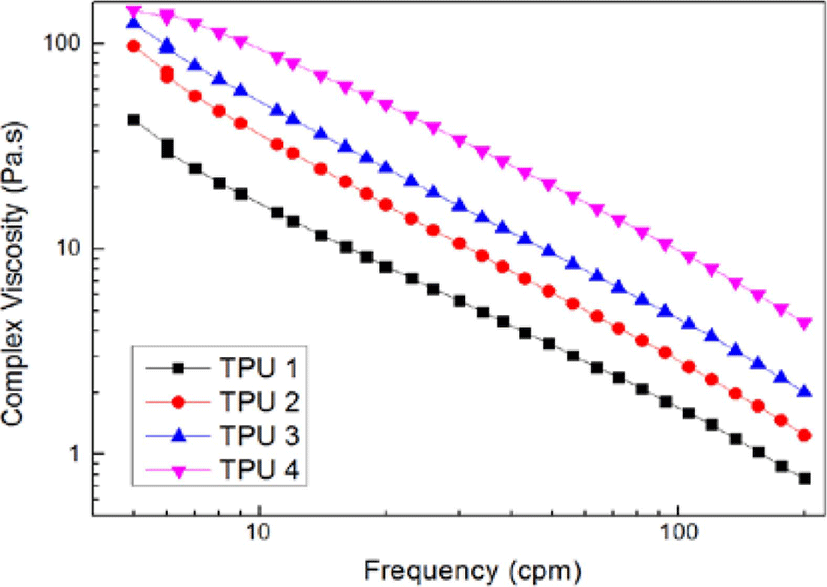
It was observed from Figure 9 that the complex viscosity (η*) decreased with the increasing in frequency. This was due to the strong shear thinning behavior of the bio TPU materials and their pure equivalent with the lower shearing rate. The dynamic viscosity of bio TPU’s with higher isocyanate ratio in the high frequency region was appreciably higher, which meant high ratio of hard segment could improve the complex viscosity, and hinder the molecular slippage during shearing.17
Cole-Cole plots were shown in Figure 10, which described the relationship between complex viscosity and real viscosity. It described the structure of heterogeneous materials. All the Cole-Cole plots in linear shape, which meant the solid like18 viscoelastic response at test temperature (60°C). With the ratio of isocyanate increasing, the initial slope of curves decreases gradually during the low frequency range, which meant hard segment could decrease the real viscosity of bio TPU, but at high frequency range, in order to resist the destruction of the test mode, the bio TPU showed great recovery ability and presented larger slope on the curves.19,20
Table 4 showed the results of tensile strength. It could be found TPU 4 showed the highest tensile stress and elongation rate in this research, which meant it had the best mechanical properties in this research, the probable reason is isosorbide structure in PE could provide more −OH groups during the reaction process, and these newly generated groups also would consume MDI, thus, when the mixing ratio (PE: chain extender: MDI) is 1:1:2, due to the more rest −OH groups, the MDI could be insufficient. But when the ratio is 1:1:2.3, the amount of MDI could be enough to react with the newly generated −OH groups and produce the most compact matrix structure. So the TPU 4 with largest MDI amount ratio showed the best tensile strength and elongation with a fuller reaction process.
Samples | 100% modulus (MPa) | 300% modulus (MPa) | Final modulus (MPa) | Strain (%) |
---|---|---|---|---|
TPU 1 | 1.45 | X | 1.97 | 127 |
TPU 2 | 2.72 | 7.25 | 16.98 | 698 |
TPU 3 | 3.06 | 14.72 | 29.16 | 927 |
TPU 4 | 4.23 | 17.25 | 35.59 | 1015 |
Figure 11 showed the results of chemical resistance test (swelling test in methanol), due to the hydrogen bonding effect in both solvent and samples, the weight of sample had been lost during the 24 h, from this figure, it could be found TPU 1 and TPU 2 showed larger weight loss during this test, which meant the structure and chemical bonding of these two sample were loose, but as TPU 3 and TPU 4, showed less weight loss, which meant these two sample had better chemical resistance. TPU 4 showed the best chemical resistance in this research. The probable reason for this phenomenon was: in TPU 1 and TPU 2, due to the lack of isocyanate, the amount of hard segment was less than soft segment, thus, the reaction of bio TPU synthesis was not complete, so the structure of TPUs were not compact, and existed excessive −OH end groups, thus, during the swelling process in methanol, the end groups would combine the solvent by hydrogen bonds, and gradually disengage from the matrix of bio TPUs.21
But as TPU 3 and TPU 4, due to the enough and excessive isocyanate at the synthesis process, the −OH end groups had been completely reacted. Also, the complete synthesis could improve the density of bio TPU, and make matrix compact, which also could increase the chemical resistance.22
Conclusions
In this research, bio-based polyester polyol had been synthesized by esterification method with azelaic acid and isosorbide. After esterification reaction, the bio-based polyurethanes were synthesized by polyester polyol, 1,3-propanediol as chain extender, and isocyanate (4,4’-diphenylmethane diisocyanate) with mixing ratios of 1:1:1.5, 1:1:1.8, 1:1:2, and 1:1:2.3. The synthesis analysis of bio TPUs were characterized by FT-IR, TGA, DSC, GPC. The mechanical properties (tensile stress, hardness) had been presented by UTM, Shore A tester and taber abrasion tester. The viscoelastic properties had been tested by an RPA-V1 with dynamic strain sweep and dynamic frequency test modes. The chemical resistance had been tested with methanol by swelling test method. The bio TPU which synthesis ratio was 1:1:2.3 showed the highest thermal decomposition temperature, the largest hardness value, the best tensile property, the best viscoelastic properties and the best chemical resistance during the characterization, the probable reason for that is due to the increasing of hard segment ratio in the molecular structure, which caused the better combination and compact matrix.