Introduction
일반 승용차는 화물을 적재할 수 있는 트렁크 공간이 별도로 마련되어 있으나 밴(van) 또는 SUV (sport utility vehicle) 차량은 통상 뒷자석 후방에 실내와 연결된 러기지 룸(luggage room)이 있다. 러기지 룸은 부피가 큰 물건을 적재할 경우에는 효과적이지만 소음과 냄새로부터 자유롭지 못하고 외부에서도 쉽게 볼 수 있어 사생활 보호 측면에서 어려움이 있다. 카고스크린은 밴 또는 SUV 차량 내에서 적재 공간을 분리시켜 줌으로써 운전자의 사생활을 보호할 수 있고, 주행 또는 충돌 시 화물의 흔들림을 억제시켜 안전성 측면에도 효과적이다. 최근 들어 가족과 여가시간을 보낼 기회가 많아지면서 실용성이 우수한 밴 또는 SUV를 선호하는 소비자 비중이 점차 늘어나고 있으며 2018년 국내 SUV 신차 등록대수는 전체 시장의 35% 이상을 점유한 것으로 보고되었다. 중국, 미국 등 해외 시장 역시 SUV 판매량이 꾸준히 증가하는 추세에 있다. 밴 또는 SUV 차량 판매량에 비례하여 카고스크린 시장 역시 성장할 것으로 예상된다.
카고스크린은 하우징부 내에 롤 형태로 말려있는 커튼부가 자리하고 있으며 커튼부는 합성섬유(직포)와 폴리염화비닐(Poly vinylchloride, PVC)를 합지하여 제조된다.1-3 PVC는 기계적 강도, 내화학성, 난연성이 우수하고 가격대비 다양한 특성을 쉽게 부여할 수 있는 특성으로 인해 전선, 필름, 파이프, 튜브 등 산업 전반에 걸쳐 광범위하게 사용되고 있다.4-6 자동차 분야에서는 주로 내장, 외장, 전선 부품에 적용되고 있으며 폴리프로필렌, 폴리우레탄, 나일론과 함께 가장 많이 사용되는 플라스틱 소재 중 하나이다. 현재 판매중인 2층구조의 커튼부는 복잡한 마감처리 공정으로 인해 생산비용이 높고 층간 수축률 차이로 발생하는 표면주름 현상을 억제시키기 위해 PVC층이 두꺼워지면서 무게가 증가하는 문제점을 가지고 있다. 원단이 무거울 경우 하중으로 인해 커튼부가 하부로 처치고 연신율과 인장강도가 저하되는 것으로 알려져 있다. 극저온 환경에 노출되는 수출제품의 경우, 유연성이 떨어지면서 연속적인 개폐가 이루어지지 않아 저온유연성 역시 요구되고 있다. 본 고에서는 가소제와 첨가제, 표면처리제를 도입하여 유연성과 내구성이 우수한 PVC 복합소재를 제조하였고, PVC/직포/PVC로 구성된 3층구조의 커튼부를 설계함으로써 경량화와 고강인성을 확보하고자 시도하였다.
Experimental
분말 형태의 순수 PVC (LS100, LG화학)는 160°C 이상의 온도에 노출될 경우 열분해에 의해 다량의 염산가스가 발생되어 자체로는 가공이 어렵다.7-9 가공성과 유연성을 확보하기 위하여 1차 가소제(LGflex DINP, LG화학)와 2차 가소제(LGflex DOA, LG화학)를 각각 선정하였고, 원가절감과 생산성을 고려하여 탄산칼슘 충진제(TL-1000, 대명케미칼)를 25 phr 첨가하였다. 난연성과 열안정성을 부여하기 위하여 삼산화안티몬 무기난연제(대명케미칼)와 Ba-Zn계열의 열안정제(BZ-170T, 송원산업)를 각각 6 phr, 3 phr 첨가하였다.
일정한 비율로 계량된 PVC, 가소제, 첨가제를 반바리믹서(banbury mixer)에서 혼련하여 paste 형태의 혼합물을 제조한 뒤 이축압출기(twin screw extruder, Bautek)를 이용하여 균질화하였다. 압출 온도는 조성비에 따라 차이는 있으나 흐름방향(주입부, 배럴, 다이)으로 160~180°C 범위에서 조절하였고 스크류 회전속도는 110~150 rpm으로 유지되었다. 압출 후 공기 중에 냉각된 혼합물은 커팅기를 이용하여 펠렛화하였고 캘린더링 공정을 통하여 시트 형태로 제조되었다. PVC시트 사이에 직포를 넣고 열압착을 통해 3층구조의 커튼부를 제조하였다. PVC 표면에 처리제를 추가로 도포하여 내마모성과 내구성을 확보하고자 시도하였다. 가소제 함량, 첨가제 및 표면처리제 도입 유무에 따른 시험편의 종류를 Table 1에 요약하여 나타내었다.
가소제와 첨가제가 추가된 PVC 복합체에 대한 상전이 온도를 알아보기 위하여 일정 무게(3~4 mg)의 시료를 셀에 넣고 −50~150°C 온도 범위에서 10°C/min으로 승온시켜 DSC 분석(DSC 4000, Perkinelmer사)을 진행하였다. 또한 시트 형태의 시험편에 대한 점탄 특성을 알아보기 위하여 −90~150°C 온도 범위에서 승온속도 5°C/min, frequency 1 Hz 조건에서 DMA 분석(Q800, TA Instruments사)을 진행하였다. 제조된 시트에 대한 인장강도와 인열강도는 MS300-31 규격에 의거하여 측정하였다. PVC 원단에서 배출되는 총휘발성유기화합물(TVOC, ppbRAE, RAE Systems사)과 포름알데히드(HCHO, Z300XP, Environmental Sensors사) 농도 측정은 MS300-55 규격에 따라 진행되었다. 질소로 충분히 퍼지시킨 polyester 재질의 샘플링백에 시료를 넣고 65°C에서 2시간동안 유지시킨 후 실온으로 냉각한 상태에서 측정하였다. 내마모 특성은 Taber 마모시험기(5135 Abraser, Taber Industries)를 이용하여 일정한 하중(1,000g)을 갖는 마모륜(CS-10)을 72 rpm의 속도로 1,000회 회전시킨 후 마모량과 색변화 정도를 관찰하여 알아보았다. 난연성은 자동차 내장재에 대한 연소성 시험규격(MS 300-08)에 따라 진행하였다. 350 mm 길이의 원단을 시험조(Flammability tester, Limotem)에 넣고 15초간 불꽃이 닿게 한 후 연소 상태를 확인하였다(5회 반복시험). 불꽃이 닿아도 전혀 연소하지 않으면 불연성, 착화는 하지만 80 mm/min 이하 또는 계측점으로부터 50 mm 이상 연소하지 않으면서 60 초 이내에 꺼지면 자기소화성(SE)으로 각각 판정하였다. 외부 환경에 대한 안정성을 알아보기 위하여 MS210-05 (플라스틱성형품 내장재) 규격에 의거하여 내광성 시험을 진행하였다. 시험편 표면이 빛에 조사되도록 환경시험기(Xe-3, Q-Lab) 내에 걸고 규격에 따라 500시간동안 노출시킨 후 색차계(Color i5D, X-rite)를 이용하여 미조사 동일 시험편과 변색 정도를 비교하였다.
Results and Discussion
제조된 PVC 복합소재에 대한 열안정성을 알아보기 위하여 압출된 펠렛을 이용하여 TGA 분석을 수행하였다. 순수 PVC는 160°C 부근에서 열분해가 발생하여 분석이 어려웠으나 가소제와 첨가제를 함유한 복합소재는 조성에 상관없이 200°C 이상에서도 안정한 거동을 보였다(Figure 1a). 열안정제와 가소제 첨가에 의한 안정화 효과뿐만 아니라 탄산칼슘 충진제가 매트릭스 내에 효과적으로 분산됨으로써 PVC의 열분해를 억제시켰기 때문으로 사료된다. 순수 PVC를 이용하여 DSC 분석을 진행해 본 결과, 83°C 부근에서 유리전이온도(Tg)가 관찰되었으나 가소제가 첨가된 복합소재는 조성에 상관없이 상전이가 관찰되지 않았다. 가소제 또는 충진제(탄산칼슘, 25 phr) 첨가에 의해 PVC 유리전이가 넓은 온도 범위에서 발생하였거나 열흐름에 대한 강도가 낮아지면서 육안으로 확인이 어려웠기 때문으로 사료된다.10,11 DSC에 비해 민감도가 우수한 DMA를 이용하여 시트 형태의 복합소재에 대한 저장탄성률(storage modulus, E’) 변화를 살펴보았다. Figure 1b에서 보여주는 바와 같이 가소제 함량에 비례하여 탄성률 감소는 낮은 온도로 이동하는 것을 볼 수 있으며 이는 유리전이온도가 낮아짐을 의미한다. 가소제 함량이 50 phr 이상일 때 상온에서도 유연성을 확보할 수 있음을 확인하였다. 유리전이온도 이하에서는 모든 시험편에서 비슷한 저장탄성률을 보였으나 승온하면서 강성 또는 유연성의 차이가 발생하였다. 가소제 함량이 증가할수록 유연성 측면에서는 유리하지만 기계적 물성 저하를 수반하기 때문에 시트 제조 시 가소제 함량을 50~60 phr 범위에서 조절하였다.12-14
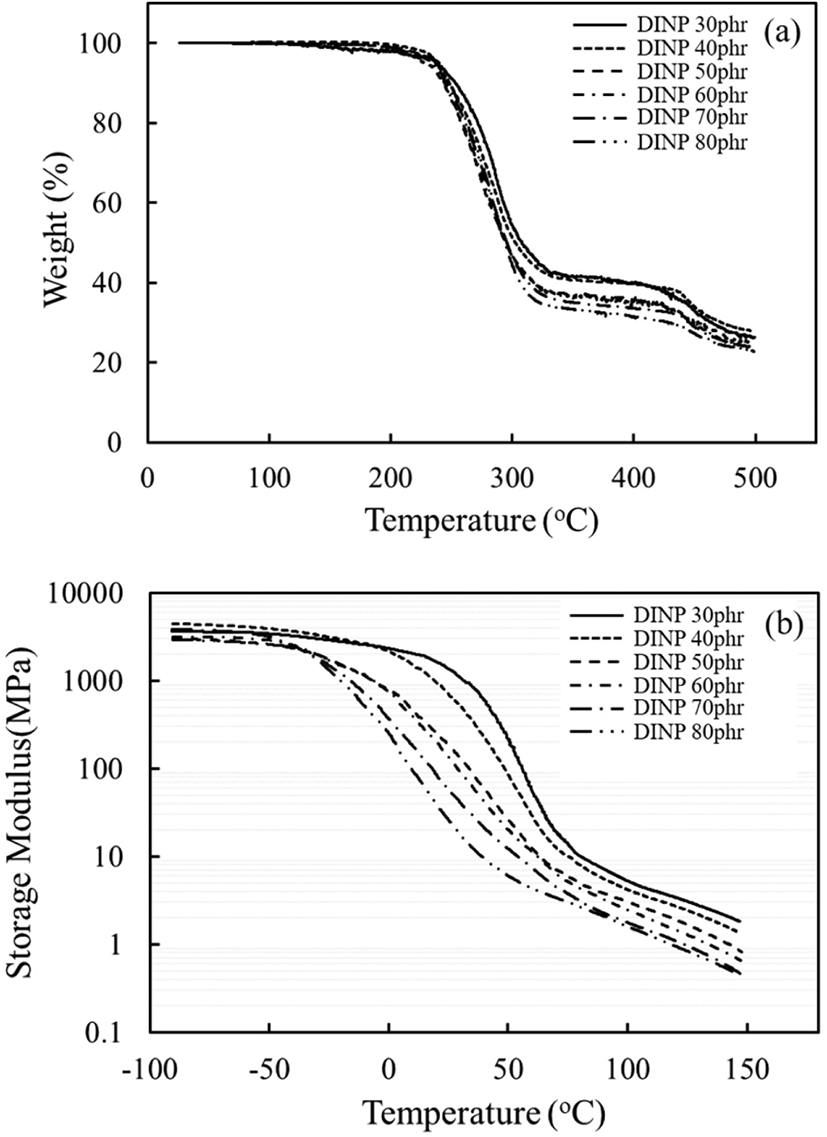
제조된 원단을 일정한 크기(100×100 mm)로 자른 후 두께와 무게를 측정하였다. LG사에서 제조된 양산품은 PVC/직포 2층구조로 되어 있음에도 0.78 mm로 두꺼워 8g의 무게를 보인 반면, PVC/직포/PVC로 구성된 개발원단은 배합비에 따라 차이는 있으나 두께는 0.45~0.59 mm 수준이었고 무게는 양산원단 대비 65~80% 수준을 보였다(Figure 2a). 카고스크린은 내장내의 일부분으로써 커튼부에서 발생한 휘발성유기화합물은 인체에 자극을 주는 원인이 될 수 있다. 총휘발성유기화합물(TVOC) 방출 농도를 측정해 본 결과 1차~4차개발원단은 1.13 ppm~2.38 ppm 수준을 보였고 유성처리제를 사용한 5차개발원단은 양산원단(1.60 ppm)보다 훨씬 낮은 0.5 ppm을 나타내었다. 포름알데히드(HCHO) 농도는 1차개발원단(0.02 ppm)을 제외한 모든 원단에서 0.01 ppm이 측정되어 양산원단과 마찬가지로 거의 방출되지 않았다.
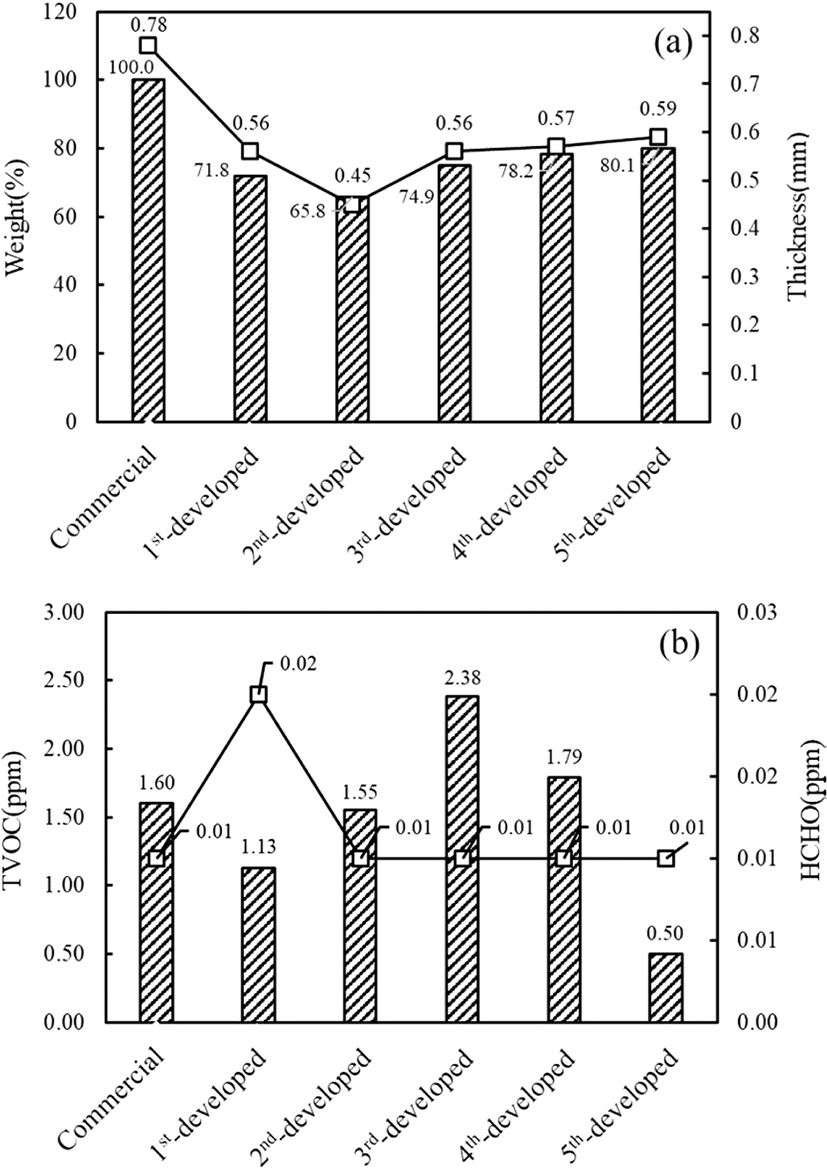
카고스크린용 커튼부 제품에 대한 품질을 보증하기 위하여 완성차 업체에서는 인장강도(수평: 21 kgf/30 mm 이상, 수직: 15 kgf/30 mm 이상)와 인열강도(수평: 1.0 kgf 이상, 수직: 1.0 kgf 이상)를 규격화하고 있다.15,16 양산원단의 인장강도는 수평, 수직방향으로 각각 47.0 kgf/30 mm, 29.6 kgf/30 mm을 보인 반면, 개발원단은 수평방향으로 77~84 kgf/30 mm, 수직방향으로 52~77 kgf/30 mm 수준을 보여 양산원단에 비해 40%이상 높은 강도를 보였다(Figure 3a). 가공 방향과 동일한 수평방향으로 전반적으로 높은 강도를 보였는데 직포는 특정한 방향성이 없는 동일한 제품을 사용하였기 때문에 PVC 분자의 배향성이 물성에 영향을 미친 것으로 보인다. 커튼부와 같은 섬유 제품은 고하중 환경에서 찢어짐이 발생할 수 있으므로 인열특성은 제품의 성능을 평가하는 주요 항목 중 하나이다. Figure 3(b)에서 보여주는 바와 같이 양산원단은 수평, 수직방향으로 각각 3.0 kgf/30 mm, 3.3 kgf/30 mm의 강도를 보였으며 개발원단은 방향에 따라 5.6~16.8 kgf/30 mm(수평), 5.3~15.1 kgf/30 mm(수직) 수준을 보였다. 2차개발원단은 다른 원단에 비해 상대적으로 낮은 인열강도를 보였는데 이는 시트의 두께가 얇아지면서(0.45 mm) 저항성이 떨어진 것으로 보인다. 5차개발원단의 인열강도는 양산품 대비 5배 이상 증가한 15.6 kgf/30 mm, 14.9 kgf/30 mm을 보였다. 인장강도에 비해 방향성에 따른 차이는 크지 않았지만 수평방향으로 전반적으로 높은 수치를 보였다. 양산원단은 개발원단에 비해 0.2 mm 이상 두껍게 제조되었음에도 불구하고 기계적 물성이 떨어지는 이유는 원단에서 큰 비중을 차지하는 PVC층이 직포에 비해 물성이 낮고 층간 계면접착력이 취약하기 때문으로 사료된다.
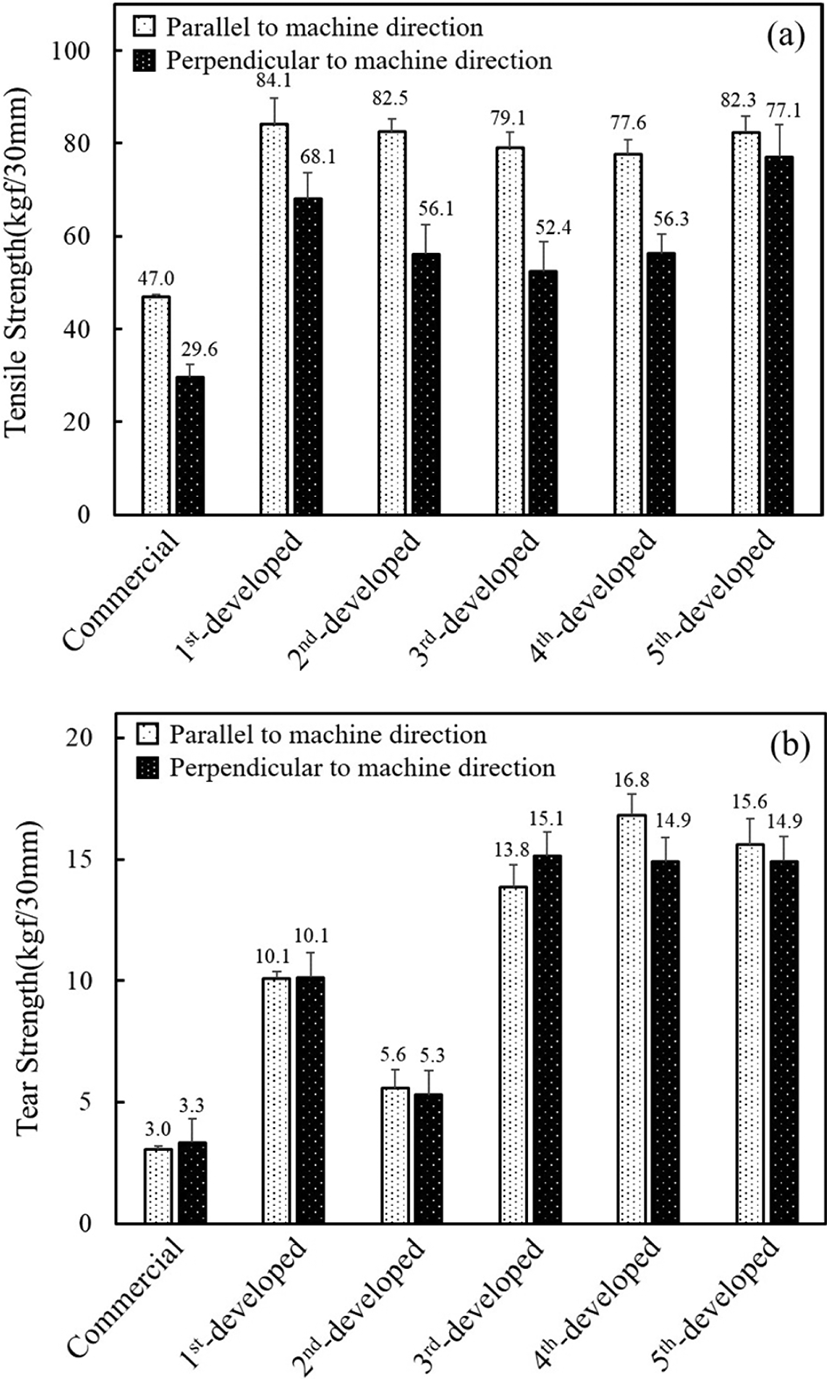
외부 마찰에 대한 표면저항성을 평가하기 위해 Taber 마모시험 후 마모량과 변색 정도를 살펴보았다. 양산원단은 마모시험 후 0.3%(0.0211g) 정도 무게가 감소하였고 색차값 은 0.5, grayscale은 4.5급을 각각 나타내었다(Table 2). 2차~4차개발원단의 마모량은 0.4~0.5%, 색차값은 0.43~0.87, grayscale은 4.5급 수준을 보여 색차값을 제외한 다른 특성은 양산품과 큰 차이가 없었다(Table 2). 1차개발원단은 상대적으로 높은 마모량(0.7%)과 색차값(2.41)을 보였는데 이는 프라이머(primer)층이 도입되지 않아 PVC층과 표면처리층의 접착력이 떨어져 나타난 결과로 사료된다. 5차개발원단의 경우 마모량은 0.4%로 양산원단과 비슷하였으나 색차값과 grayscale값은 각각 0.3, 5급을 보여 우수한 마모 특성을 보였다. 온도 16~21°C, 상대습도 55±5% 환경 하에서 24시간 동안 조절(state)한 상태에서 연소성을 시험해 본 결과 양산, 개발원단 모두 자기소화성(SE)을 나타내었다. 80±3°C로 유지된 항온조에서 168시간 동안 방치시키고 16~21°C, 55±5 %RH 환경에서 24시간 동안 조절한 후 동일한 시험을 진행해 보았는데(heat aging) 여전히 자기소화성을 유지하고 있음을 확인하였다(Table 2).
자동차 내부는 계절에 따라 고온, 저온, 고습 환경에 노출되고 장시간 옥외 주차 시 태양광이 연속적으로 조사됨으로써 PVC의 분해를 초래할 수 있다.17-19 내광성시험 후 색차값(△E)을 살펴보면 1차개발원단은 8.34를 보여 변색이 심하게 발생하였으나 benzophenone계 UV흡수제와 아민계 산화방지제가 각각 첨가된 2차~5차개발원단은 2이하를 보여 UV 안정성이 크게 향상된 것을 알 수 있다(Table 3). UV흡수제는 자외선에 의해 분해되어 생성된 PVC 라디칼을 제거하고 산화방지제는 고온에서 공기와 접촉 시 산화라디칼의 발생을 억제시켜 변색을 차단할 수 있다. 원단의 내광 특성을 양산제품 수준(△E=0.32)까지 향상시키기 위하여 표면처리제를 2액형에서 1액형 urethane 계열로 대체한 후 제조된 5차개발원단의 경우 색차값이 0.35까지 낮아져 안정성이 향상되었음을 확인하였다. 이는 UV흡수제와 산화방지제뿐만 아니라 표면처리제 역시 시트의 내광성과 밀접한 관계를 가지고 있음을 의미한다.
Conclusions
본 연구에서는 가소제, 첨가제, 표면처리제를 도입함으로써 PVC의 가공성과 유연성, 열안정성을 향상시킬 수 있음을 확인하였으며 합성섬유의 양면에 PVC층을 합지시켜 제조된 3층구조의 원단은 양산원단에 비해 25% 이상 가벼우면서 인장강도와 인열강도는 각각 75%, 350% 이상 높은 것으로 나타났다. 총휘발성유기화합물과 포름알데이드 방출량 역시 양산품보다 적게 발생하였고 자기소화성을 보여 자동차용 내장재로 적용이 가능함을 확인하였다. 프라이머층은 PVC층과 표면처리제와의 접착력을 향상시키고 내마모 특성에 영향을 미치는 것으로 판단된다. 자외선에 연속적으로 노출시킨 후 표면 변화를 살펴본 결과 UV흡수제, 산화방지제, 유성 우레탄 계열의 표면처리제로 처리된 원단에서 우수한 내구성을 보였다.