Introduction
지방족 폴리케톤(Aliphatic polyketone)은 최근 상용화가 이루어지고 있는 고분자 신소재이다. 이는 대략 15°C의 유리전이온도와 225°C의 용융온도를 갖는 반결정성 고분자로 그 특성은 폴리프로필렌과 매우 유사하다고 알려져 있다.1 지방족 폴리케톤 재료에는 상대적으로 저렴한 일산화탄소, 에틸렌 및 프로필렌을 사용한다.2 이러한 재료는 기계적 강도, 내화학성, 내마모성, 기체 차단성 및 내충격성 등의 우수한 물리-화학적 특성이 있어 섬유, 엔지니어링 플라스틱 또는 복합재료에 응용 가능성이 높은 고분자 물질로서 연구되어 왔다.3
복합재료는 서로 다른 성질을 가지는 두 가지 이상의 재료를 혼합하여 상호 결점을 보완할 수 있도록 인위적으로 만든 재료이다. 고분자의 경우 수지 자체만의 성질로는 응용에 한계가 있기 때문에 이를 극복하기 위해서는 섬유, 금속 또는 세라믹 등의 유/무기 첨가제를 사용하여 물성을 향상시켜야 한다.
섬유 강화 복합재료는 섬유를 이용하여 고분자의 물성을 보완한 것으로 섬유의 길이에 따라 단 섬유 및 장 섬유가 사용된 섬유 강화 복합 소재와 연속상의 fiber fabric에 고분자를 함침시킨 섬유 강화 복합 재료로 구분된다.4 대표적으로 사용되는 섬유상의 보강소재로는 유리섬유,3,5-7 아라미드 섬유,8,9 천연섬유10,11및 탄소섬유6,12,13가 있으며 이를 활용한 연구가 다양하게 이루어지고 있다. 이 중 탄소섬유는 높은 비탄성률, 강도, 강성, 전기적 특성 및 낮은 밀도 등 우수한 특성으로 섬유 강화 복합재료의 제조에 널리 사용되며14 그 뛰어난 특성이 필요한 항공 우주, 스포츠 및 자동차 분야 등 다양한 곳에서 응용되고 있다.
본 연구에서는 엔지니어링 플라스틱으로 높은 활용 가능성을 가지는 지방족 폴리케톤의 특성을 향상시키기 위하여 PAN계 짧은 탄소섬유를 이용한 섬유강화 복합재료를 제조하였다. 복합체는 압출공정을 통하여 제조되었으며, 섬유를 50 wt%까지 첨가하였다. 제조된 PK/CCF 복합체의 함량 변화에 따른 인장, 굴곡 및 충격 시험을 통한 기계적 특성 및 열변형 온도와 열전도도를 측정하여, 열적 특성 변화를 확인하였으며 주사전자현미경을 통하여 복합체의 모폴로지를 관찰하였다.
Experimental
섬유 강화 복합재료의 제조를 위해 사용된 고분자 매트릭스는 융점이 220°C이며, 용융지수가 60 g/10 min인 폴리케톤(polyketone, PK)으로 ㈜효성에서 구입하였다. 보강섬유는 PAN계 짧은 탄소섬유(chopped carbon fiber, CCF)를 사용하였으며 에이스씨엔텍㈜에서 구입하였다. 탄소섬유는 12000 개의 필라멘트로 구성되어 있으며, 직경이 약 7 μm, 길이가 6 mm이며 약 1 wt%의 에폭시 사이징 처리되어 있다. 본 연구에서는 가공 공정 중 점도 상승에 의한 체류시간 증가 에 따른 PK 고분자 수지의 열적 분해를 줄이기 위해 1, 2차 산화방지제를 사용하였다. 페놀계 1차 산화방지제로 tetrakis-[methylene-(3,5-di-tert-butyl-4-hydroxyphenyl)prop- ionate methane](TPM)을, 인계 2차 산화방지제로 triphenyl phosphate (TCP)를 각각 송원산업㈜과 Sigma-aldrich에서 구입하였다.
본 연구에서는 스크류의 L/D가 42, 지름이 30 mm인 모듈라 치합형 동방향 회전 이축 스크류식 압출기(LG Machinary, BT-30-S2-42C)를 사용하여 짧은 탄소섬유 강화 폴리케톤 복합체를 제조하였으며, 수냉 공정을 거쳐 펠렛타이저를 통해 펠렛으로 제조되었다. 압출 온도 조건은 Table 1과 같으며, 스크류 회전 속도는 150 rpm으로 설정하였고, 스크류 조합은 Figure 1과 같이 3-kneading-1-reverse block을 사용하였다. 복합체 제조에 사용된 재료들의 조성은 Table 2에 나타내었다.
Barrel Temperature (°C) | ||||||||
---|---|---|---|---|---|---|---|---|
Cy 1 | Cy 2 | Cy 3 | Cy 4 | Cy 5 | Cy 6 | Cy 7 | Head | Die |
180 | 220 | 225 | 230 | 230 | 230 | 230 | 230 | 230 |
1 | 2 | 3 | 4 | 5 | 6 | |
---|---|---|---|---|---|---|
PK (wt%) | 100 | 90 | 80 | 70 | 60 | 50 |
CCF (wt%) | - | 10 | 20 | 30 | 40 | 50 |
Songnox 1010 (phr) | 0.2 | 0.2 | 0.2 | 0.2 | 0.2 | 0.2 |
3. 특성분석
제조된 짧은 탄소섬유 강화 PK 복합체의 인장 특성 및 굴곡특성은 만능재료 시험기(Universal testing machine, UTM, Shimadzu, AG-50Knx Plus)를 통해 측정되었다. 복합체의 인장 특성은 ASTM (American Society for Testing and Materials) D638 규격을 따라 50 kN의 load cell과 50 mm/min의 크로스헤드 속도(cross head speed) 조건에서 시편의 인장탄성률, 인장강도 및 신장률을 측정하여 평균값을 취하였다. 굴곡특성은 3점 굴곡 시험으로 길이대 폭의 비율이 32:1인 시편을 이용하여 ASTM D790 규격에 따라 50 kN의 load cell과 5.1 mm/min의 크로스헤드 속도(cross head speed) 조건에서 측정되었다. 제조된 복합체의 충격강도는 아이조드 충격시험기(Izod impact tester, Tinius Olsen, Model 892)를 이용하여 측정되었다. 충격강도의 측정은 ASTM D256 규격에 따라 충격시험용 시편을 사용하여 중앙부분의 두께가 10.16 ± 0.5 mm가 되도록 노치한 후, 평균값을 얻었다.
짧은 탄소섬유의 함량에 따른 PK 복합체의 열 변형온도의 변화를 관찰하기 위하여 열 변형온도 측정기(Heat deflection temperature analyzer, HDT, Tinius olsen, Model 603)를 이용하였다. 3-point bending mode에서 두께가 약 3.2 mm인 굴곡시험용 시험 시편을 사용하여 0.455 MPa의 하중 및 2°C/min의 승온속도의 조건에서 시편이 0.254 mm (0.1 inch) 변형이 이루어질 때의 온도를 측정하였다.
제조된 PK/CCF 복합체의 열전도도를 측정하기 위하여 열전도도 측정기(레이저 플래시법, Lazer flash analyzer, LFA, NETZSCH, LFA 447)를 이용하였다. 열전도도 측정 시편은 지름 12.7 mm, 두께 3 mm의 치수를 가지는 원판 디스크 형태이며, 25°C 온도에서 열전도도를 측정하였다. 열전도도 측정하기 전 시편은 흑연 파우더(graphite powder)로 표면을 코팅 처리하였다. 열전도도 시편을 이용하여 열 확산도를 5회 측정하여 평균값을 취하였으며, 여기에 복합체의 밀도 및 비열을 곱하여 열전도도를 얻었다.
Results and Discussion
짧은 탄소섬유의 함량에 따른 PK 복합체의 인장시험을 통해 얻어진 응력-변형률 곡선을 Figure 2에 나타내었다. 그림과 같이 PK은 인장 시험 시 인장응력이 최대가 되는 지점에서 시편의 단면이 급격히 줄어드는 네킹(necking)이 발생하면서 최대의 인장강도 값을 나타내는 항복점(yield point)을 보이며, 이후 소성 변형을 일으켜 약 230%의 신장된 지점에서 파괴를 보이는 전형적인 연성재료의 인장거동을 보인다. CCF를 50 wt%까지 첨가한 PK 복합체의 경우 섬유의 함량이 증가함에 따라 인장탄성률(tensile modulus)을 나타내는 그래프의 초기 기울기가 급격히 증가하는 것을 관찰할 수 있다. Figure 3은 CCF가 50 wt%까지 첨가된 PK 복합체의 인장강도 및 인장탄성률을 나타내는 그래프이다. 순수한 PK의 인장강도는 62.3 MPa이며, CCF의 함량을 10~50 wt%까지 증가시키면 79.0~157.9 MPa로 크게 증가하는 것을 볼 수 있다. 이는 CCF가 가지는 높은 인장강도의 영향 및 압출 공정을 통한 PK 매트릭스 내 고른 분산과 더불어, 강한 전단력에 의한 섬유의 결함이 발생함에도 불구하고 CCF의 표면에 사이징 처리된 에폭시의 영향에 의하여 일부 섬유가 PK와의 계면에서 접착을 형성하였기 때문으로 사료된다. 인장탄성률도 CCF의 함량 증가로 증가하였다. CCF가 첨가되기 전, 즉 순수한 PK의 인장탄성률은 약 1.2 GPa의 값을 가지는데 비하여 CCF를 10 wt% 첨가하면 3.0 GPa의 값을 나타내며, 50 wt% 첨가한 경우 10.0 GPa의 값을 나타냈다. 이러한 이유는 연성(ductile)을 지니는 PK 고분자 수지에 비하여 높은 탄성률을 갖는 CCF가 첨가됨에 따라 함량이 증가할수록 PK 복합체의 인장 탄성률을 증가시키기 때문으로 사료된다. 또한 사출 공정 시 CCF의 함량 증가에 따른 사출 압력의 증가로 인해 금형에 채워지면서 금형 벽면 쪽의 전단응력에 의해 시편의 표면층 (skin layer)에서 용융물이 흐르는 방향으로 배향이 이루어짐에 따라 인장시험 측정 방향으로 복합체의 강성(stiffness)을 증가시키는 것도 인장탄성률 증가의 원인으로 사료된다.
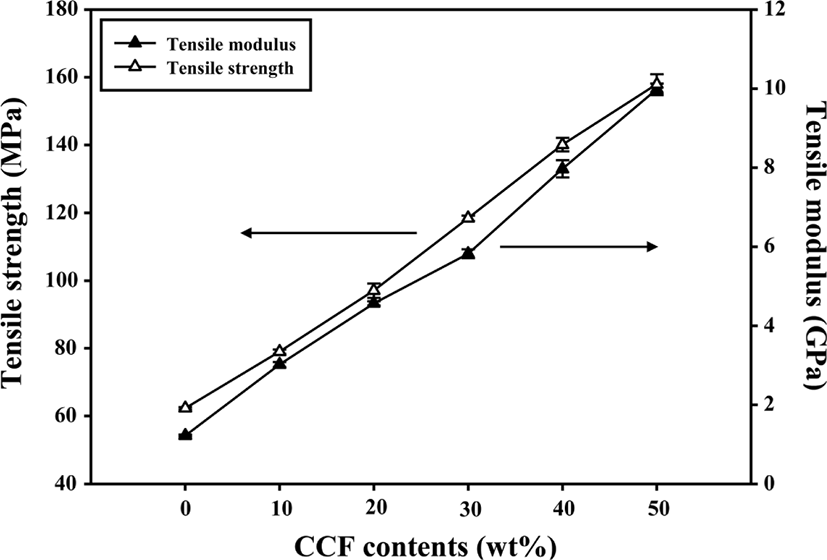
CCF 함량 증가에 따른 PK 복합체의 인장신율은 Figure 4에 나타낸 바와 같이, 섬유의 함량이 증가할수록 지속적으로 감소하는 경향을 보이며 이는 연성인 PK에 CCF의 첨가 함량 증가에 따라 복합체가 더욱 취성(brittleness)의 특성을 나타내기 때문인 것으로 보인다.
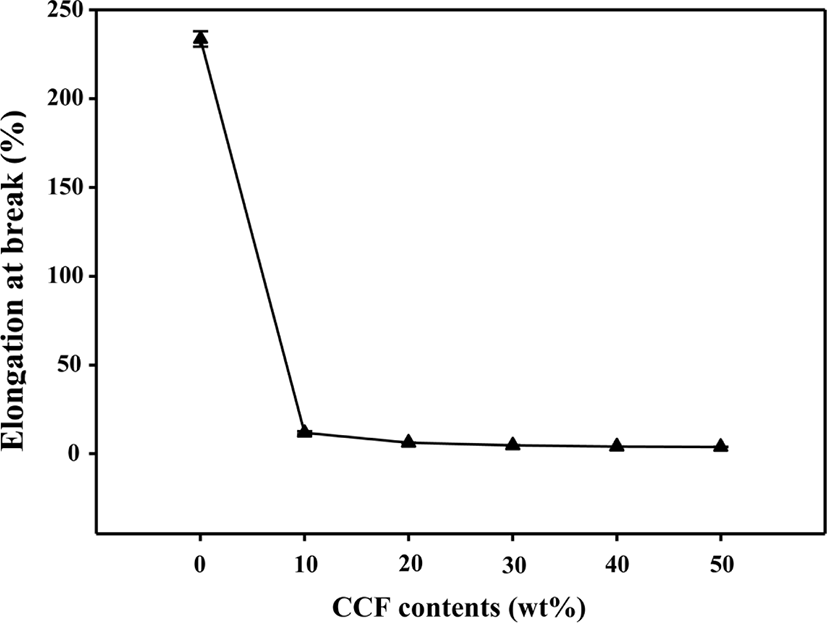
제조된 PK/CCF 복합체의 굴곡강도와 굴곡 탄성률을 Figure 5에 나타내었다. PK의 굴곡강도는 32.4 MPa인데 CCF의 함량이 증가될수록 증가하여 50 wt%에서 241 MPa의 값을 보였다. 이와 같은 굴곡강도의 향상은 시편 중심(core)에서의 섬유의 무질서한 배향과 표면부에서 길이 방향으로의 섬유의 배향과 섬유와 매트릭스간의 약간의 계면의 형성을 통해 굽힘에 의한 응력이 매트릭스 내부로 효과적으로 분산할 것이다. 그리고 시편의 파단 경로의 형성 방해와 같은 보강효과에 의해 굽힘에 의한 파괴에 대하여 저항성이 증대되었기 때문으로 사료된다. 굴곡탄성률에서는 인장탄성률의 결과와 마찬가지로 CCF의 첨가 함량의 증가는 굴곡탄성률의 증가를 유발시켜, CCF가 첨가되기 전인 순수한 PK 고분자의 경우 굴곡탄성률이 1.2 GPa에서 첨가 함량이 50 wt%인 경우 30.4 GPa의 값을 나타낸다. 이와 같은 결과는 인장탄성률과 마찬가지로 시편 중심부의 무질서한 CCF의 배향과 표면에서 CCF의 길이 방향으로의 배향에 의하여 강성이 증대되며 함량 증가에 따라 길이 및 두께 방향으로의 많은 섬유 함량에 따라 탄성률 증가에 영향을 주었기 때문으로 해석된다.
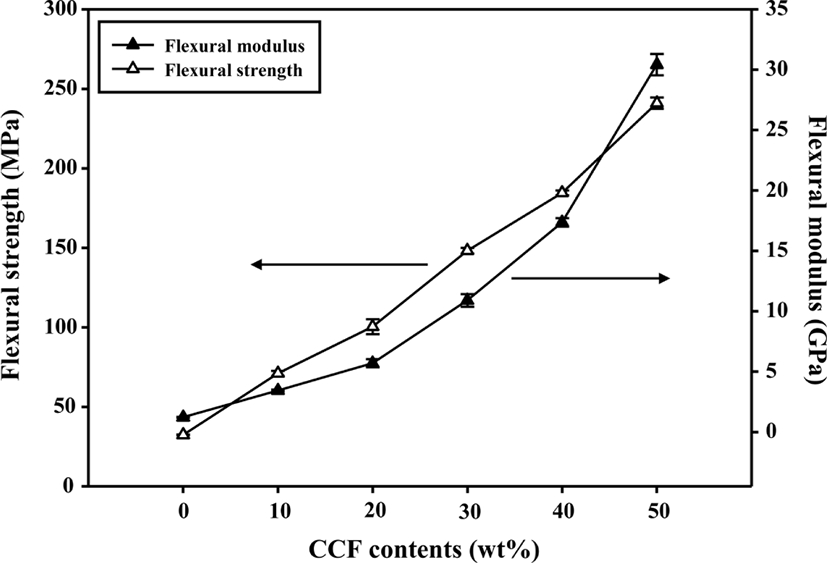
Figure 6은 PK/CCF의 충격강도 변화를 나타내는 그래프로 PK의 경우 약 7.9 kJ/m2의 충격강도 값을 보인다. CCF의 함량이 증가할수록 감소하는 경향을 보여 30 wt%의 경우 4.3 kJ/m2의 충격강도 값을 보인다. 그러나 이후 40 wt%부터는 증가하며 50 wt%에서는 5.3 kJ/m2의 충격 강도 값을 보였다. 이와 같은 충격강도의 변화는 30 wt%까지는 고탄성의 강직한 CCF의 첨가 함량 증가에 따라 취성(brittleness)의 증가로 인해 감소하는 것으로 보이며, 이후 40 wt%부터는 섬유에 의하여 외부에서 전달되는 하중의 이동경로가 길어지게 되어 크랙의 성장이 지연되기 때문에 충격강도가 증가한 것으로 사료된다.
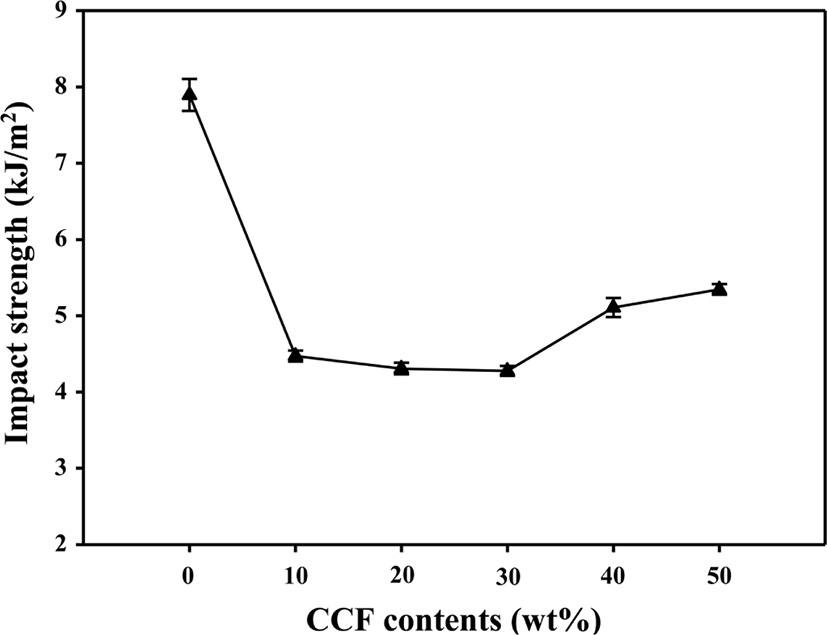
CCF의 함량 변화에 따른 PK 복합체의 열변형 온도 변화를 Figure 7에 나타내었다. 이는 앞에서 기술한 굴곡탄성률의 결과와 일치하는 경향을 보였다. 그림과 같이 순수한 PK 고분자의 경우 0.254 mm 변형되었을 때의 온도는 약 168.0°C이며, CCF의 함량이 50 wt%일 때는 207.5°C로 첨가대비 23.5% 증가하였다. 이와 같이 CCF 첨가 함량에 따른 열변형 온도의 증가는 PK 매트릭스에 도입된 상대적으로 큰 탄성률과, 열 안정성을 가지는 CCF에 의해 실리콘 오일 내에서 온도 증가에 따른 3점 굴곡하중이 시편에 가해질 때, 굴곡특성의 변화에서 기술한 바와 같이, 복합재료 시편의 두께 및 길이 방향에 분포하고 있는 섬유에 의하여 일정한 하중에서 열에 의한 변형을 억제 시켜주어 매트릭스 수지의 열에 의한 변형 저항성을 높여주기 때문으로 사료된다. 그러나 20 wt% 이상의 CCF 함량에서는 눈에 띄는 증가를 보이지는 않았다.
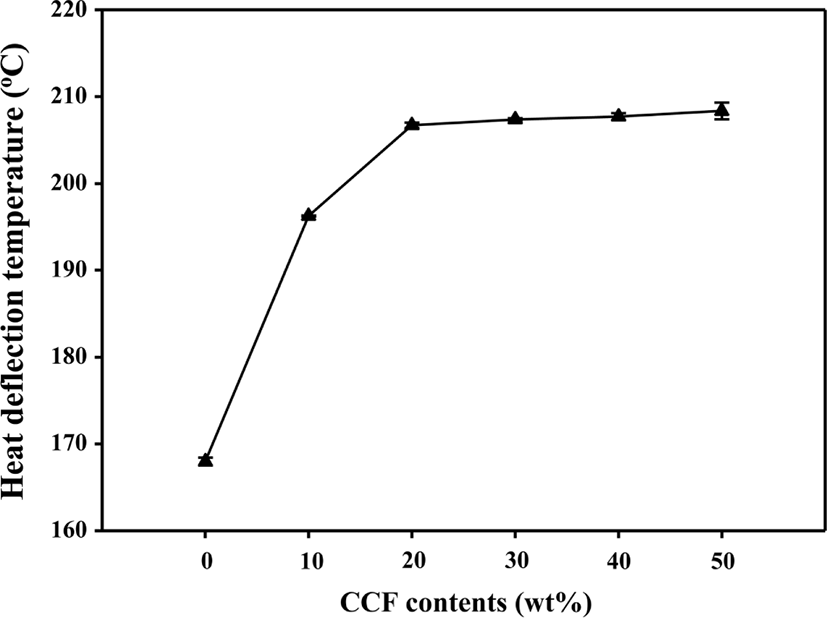
Figure 8은 CCF 함량 변화에 따른 PK 복합체의 수직 열전도도를 보여주는 결과이다. 일반적인 고분자는 0.2~0.5 W/m.K의 열전도도를 갖는 것으로 알려져 있다.14 순수한 PK의 경우 수직 열전도도는 0.36 W/m.K 이며, 이는 다른 고분자들에 비해 비교적 높은 열전도도 수치로 분자간의 강한 인력으로 인한 결정성이 높기 때문이다. CCF의 함량 증가에 따라 열전도도가 상승하여 10~50 wt% 첨가함량에서 0.41~0.67 W/m.K의 열전도도 향상을 가져왔다. 이는 PK 매트릭스 내의 필러의 분산을 통해 섬유 간 접촉을 통한 열이 이동할 수 있는 통로의 형성을 생성하기 때문으로 사료된다.
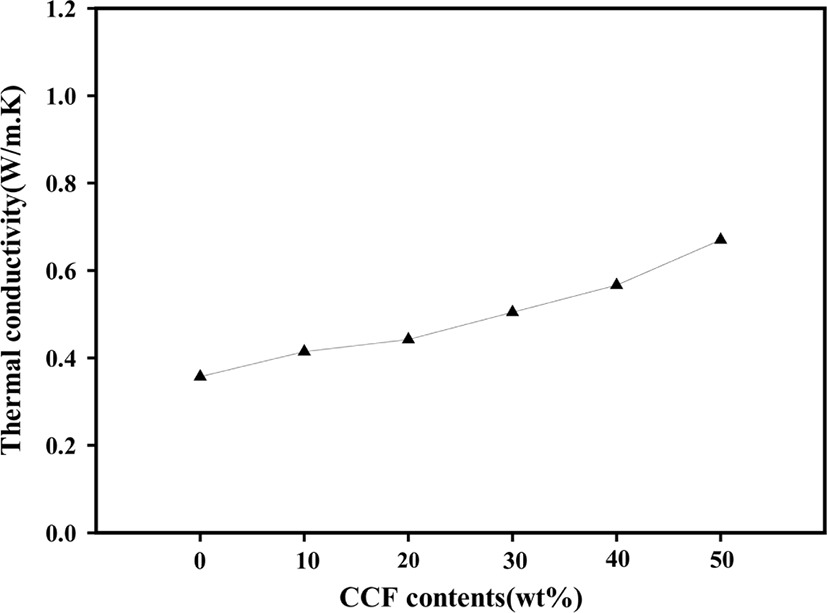
CCF 함량에 따른 PK 복합체의 파단면을 Figure 9에 나타내었다. PK의 경우 일반적인 연성 고분자와 유사한 파단 표면을 보여준다. CCF 함량증가에 따라 매트릭스 내 섬유상이 많이 관찰되며, 일부 섬유는 PK와의 계면 형성으로 인해 고분자 수지에 감싸여 거친 표면을 보이며, 나머지 일부 섬유는 파단시 섬유 표면에서 PK가 깨끗하게 떨어져 계면결합을 형성하지 못하거나 pull out 되어 있는 것을 관찰할 수 있다. 40 wt% 첨가된 복합체의 이미지는 시편의 중심 부근으로 무질서한 배향을 보여주며, 50 wt%의 이미지는 사출에 의한 영향으로 시편의 skin 부근에서 사출 방향으로 섬유의 배향이 이루어진 모습을 보인다. 이러한 파단면 관찰을 통해 필러의 함량 증가는 서로간의 접촉을 통한 열의 이동 통로의 형성과 더불어 복합체 내에 고루 분산되어 보강효과에 의하여 기계적 특성 및 열변형 온도의 증가를 가져온 것으로 판단된다.
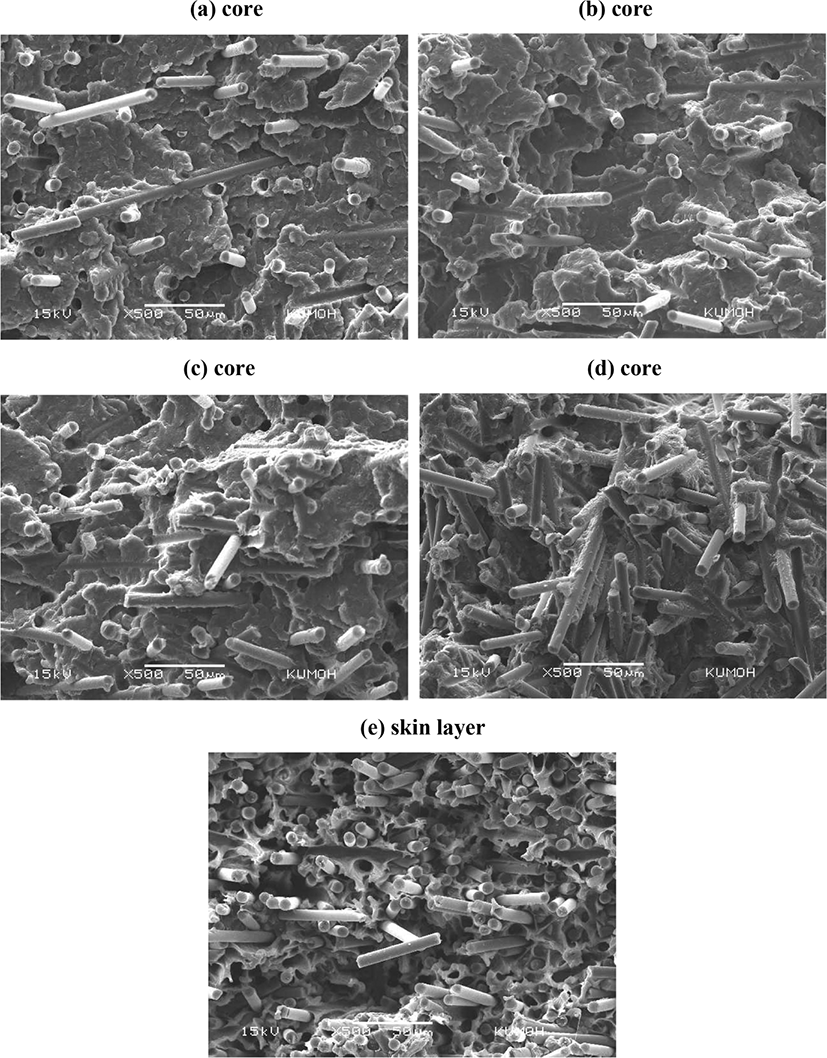
Conclusions
본 연구에서는 고분자 신소재인 PK에 PAN계 짧은 탄소섬유를 첨가하여 기계적 특성 및 열적 특성의 변화를 관찰하였으며, 이에 따른 결과는 다음과 같다.
기계적 특성에서 탄소섬유의 함량 증가는 섬유 배향 효과에 의하여 인장 및 굴곡 탄성률을 향상시켰다. 또한 압출 공정을 통한 섬유의 매트릭스 내 분산과 PK 매트릭스와의 일부 계면의 형성을 통해 인장 및 굴곡 강도가 증가하였다. 반면 파단신율의 경우 CCF의 함량 증가에 따라 지속적인 감소의 경향을 보였다. 충격강도의 경우 일정 함량까지는 섬유 함량 증가에 따라 취성(brittleness)에 의해 감소하였으나. 이후 함량에서는 섬유 보강효과에 의하여 크랙의 성장 지연에 의하여 충격강도가 향상하였다.
복합체의 열적 특성에서 CCF의 첨가는 높은 탄성률과 섬유의 배향, 일부 폴리머와의 계면 결합을 통해 온도가 상승함에 따라 3점 굴곡에서 열에 의한 변형이 억제되어 열변형온도가 증가하였다. 그러나 특정 함량 이상에서는 눈에 띄는 증가를 가져오지는 않았다. 열전도도 특성에서는 섬유의 매트릭스 내 분산에 의하여 함량 증가에 따라 섬유간 접촉 수 증가에 따른 열의 이동 통로의 형성으로 인하여 열전도도가 상승하였다.