Introduction
Polyurethane (PU) discovered by Bayer et al.1 are considered to be a fascinating material which is capable to display wide range characteristic properties of thermoplastic, thermoset, and elastomers. Polyurethane foams, polyurethane adhesives, and polyurethane elastomers are the important commercial class of products available, which are highly sustainable and extremely adaptable with prominent industrial importance.2-6 PU shall be considered as prime material among polymers that could be ranked 5 in overall polymer usage. The global market for polyurethane in 2015 amounted to USD 53.94 billion.7 This indicates the high demand and importance of polyurethane in end-use indus-tries.
Polyurethane elastomers with high hardness, prominent chemical resistance, excellent mechanical strength, extreme resistant towards abrasion and promising elastic properties comprise of hard segment chains and a low glass transition - soft segment chains.8 The highly reactive isocyanate group quantitatively react with great variability of nucleophiles such as polyols and amines which results in the fascinating properties of PU.9 The properties of PUs depend on the choice and composition of the reactant and method of synthesis. The pot lives of most of these PUs are in a range of 2-10 min and possess a demolding time of 20-60 min.
The major area of polyurethane elastomer utilization is the production of large, small and multi volume roller products. These are used as industrial rubber roll in wheels and steel manufacturing industries. The production of these systems requires special casting methods instead of conventional mold casting. The mold casting is not appropriate for the molding and demolding of polyurethane systems with short pot life. The major hurdle created by this conventional method is the huge cost of mold making with different dimensions to suit the industrial needs.
For the casting of PU resins as rolls, the most appropriate method is ribbon flow method in which a continuous casting of the resin occurs on the surface of a rotating iron core. In this method, there is no need to develop molds with different dimensions, and the wastage of time and raw materials is minimum.
The major requirement of ribbon flow method is the fast curing polyurethane with suitable working time. Different classes of curatives and catalysts are added to the reaction mixture to ensure the complete fast curing of the system.10-14 The prominent curing agent is an aromatic diamine (e.g. MOCA). There exist many strict regulations on the MOCA containing materials since it is a IARC (International Agency for Research on Cancer) group 1 carcinogen, the carcinogenic effect of MOCA have been described in literatures.15
Development of a curative – prepolymer system with improved health protection, environmental compatibility, fast curing rate is our ongoing work. The most adverse effect of the very fast rate of curing is the inefficiency of the system for casting and handling at room temperature or even at cooling temperature.16 Therefore, a complete understanding of the rheology of the developed prepolymer system is required. In this work, a complete characterization of the MOCA free fast curing polyurethane is done by assessing pot life and physical properties.
Experimental
The isocyanate prepolymer (RF-90A), curative (RF-90B), and catalyst (RFUCT-2) for the preparation of MOCA free fast curing polyurethane were supplied by Daesung Ewha Ltd., South Korea.
The fast curing polyurethane is fabricated by the intermixing of a multi-component system, component A and component B. Component A is a mixture of polyol and catalyst and component B is isocyanate prepolymer. Throughout these studies, the weight of component B is kept constant and the weight of Component A is varied. The feed ratios are summarized in Table 1. According to the designed experiment, a homogenous mixture (component A) of polyol and catalyst was initially prepared. The obtained component A is blended uniformly with component B using a high shear mixer at 2000 rpm for 5 sec. The resulting mixture is quickly poured to a mold and the samples for the property assessment were prepared by molding in a hydraulic press at a temperature 45°C for 5 min.
NCO index | Weight of prepolymer (g) | Weight of curative (g) | Weight of catalyst (g) |
---|---|---|---|
100 | 100 | 81.3 | 1.69 |
105 | 100 | 77.2 | 1.61 |
110 | 100 | 73.9 | 1.54 |
115 | 100 | 70.7 | 1.47 |
120 | 100 | 67.7 | 1.41 |
The usable time available to perform the processing of polyurethane before it loses the possessed fluid nature is defined as the pot life.17 The pot life of the PU resin was determined by a correlation study of viscosity and physical flowability of the blend. The viscosity of the PU was measured at 25°C with a Brookfield, DV2T RV digital viscometer with Gel timer spindle at a spin rate 1 rpm. The polyol, catalyst and isocyanate prepolymer were mixed uniformly in a high-speed mixer at an 3000 rpm for 3 sec before being subjected to viscosity studies. The flowability of the polymer mixed at different mixing times is studied visually and the trend of flowability is compared with the viscosity results.
Gel fraction was measured by the solvent extraction method using tetrahydrofuran (THF) for 24 hrs. Thereafter the swollen samples were dried at 60°C for 24 hrs to measure the dried weight. The gel percentage was calculated from the ratio of the dried sample to the initial polymer weight. The crosslink density at different NCO index was determined by using the Flory−Rehner equation.18
where Mc = molecular weight between the crosslinks, Vs = molar volume of the swelling liquid, ρ = density of the vulcanized samples, and χ = Flory-Huggins solvent rubber interaction parameter. The equilibrium swelling data provides the quantitative value of volume fraction of rubber (νr).
The tensile test was executed as per KS M 6518 method in the universal testing machine (Tensometer 2000, Myungjitech). Tensile and tear specimens were punched out using Dumbel type 2 and Type B test specimens respectively, from the molded sheets. The tensile tests were carried out until a failure occur in the sample with a crosshead speed of 500 mm/min and it also provide characteristic information about the elongation at break and final strength of the polymer. KS M 6518 was used to perform tear strength analysis, Crosshead speed: 500 mm/min. All the tests were carried out at room temperature.
The sample size, the rotation displacement of the platform, and load for abrasion testing were selected according to ASTM D3389. A load of 10 N and a uniform displacement of 70 rpm was maintained. The measurement was taken using 500 cycle abrasion tester (COAD 101, Ocean Science) with H-18 abrasion wheel. In each testing, the weight of the sample before the test and after the test is keenly measured and the difference is considered to be the abrasion loss.
The hardness of prepared PU samples was measured using durometer. In this method, the depth up to which the indenter penetrated to the sample surface is correlated with the hardness of the test specimen.
The measurement of the force required for an object to move over another is studied by the coefficient of friction (COF). COF is measured using the tactile meter (HEIDON Type 33, SHINTO Scientific) at room temperature (RT) of 25±1°C, and 50 ± 5% relative humidity (RH). There are research papers in which the tactile meter has been utilized to determine the friction coefficient.19 The tests were performed by sliding mode on a 63 × 63 mm specimen under a normal load of 1 N and a sliding speed of 5 mm/s. A jig is utilized to maintain uniform test conditions.
Results and Discussion
For most of the fast curing resins like polyurethane, pot life is the most important parameter. Pot life is an important factor affecting the processability of a targeted composition. The analysis of the viscosity build-up with time helps to understand the cure kinetics of polyurethane. In a polyurethane curing system as the formation of urethane advances, the overall viscosity of the system exhibits a tremendous increase.20Figure 1(a) depicts the rapid upturn of rheo – kinetic viscosity with time and with rise in the NCO index. The cure characteristic at each NCO index shows similar behavior.
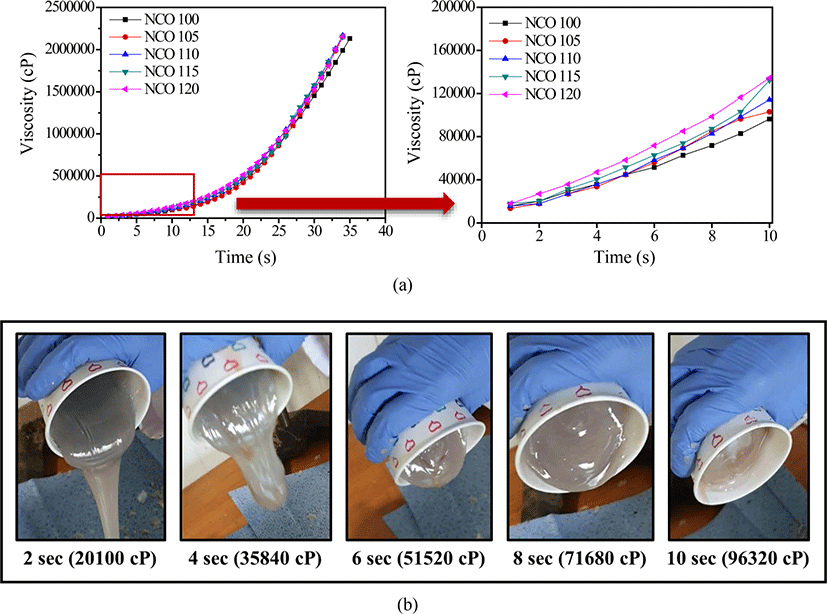
The confirmation on pot life was made from the investigation of flowability attained by polyurethane curing system with NCO index 100 and it is shown in the Figure 1(b). The flowability test is a piece of strong evidence to precisely determine the pot life of a fast curing system. At 2 sec the curing system flows freely which indicates the feeble crosslinking attained in the system. A moderate flowable stage of polyurethane elastomer is observed at 4 and 6 sec. A completely cured system highly resistant to flow and mold is observed at a mixing time of 10 sec. The system shows a complete resistance to free flow yet a highly viscous fluid nature between 6-8 sec, indicating the limiting time of processability. Thus it could be inferred that the pot life of the system is between 6-8 sec. The obtained result of flowability test is correlated with viscosity data. This further confirms that the pot life of this fast curing polyurethane system is around 6-8 sec.
The gel fraction and crosslink density of the cured polymer is a tool to measure the effective interaction among the polymer chains, therefore, these properties indicate a direct correlation with the overall mechanical reinforcement. The variation of the gel fraction and crosslink density at different NCO indexes are depicted in Figure 2(a, b). The polyurethane with NCO index 120 possesses superior crosslink density and gel fraction, whereas the polyurethane with NCO index 100 possesses the least value. The increase in the NCO index resulted in an increase in the crosslink density and gel fraction, which indicates the denser crosslinking of the polymer network at higher NCO index. The percentage of gel fraction at higher NCO indexes are comparable.
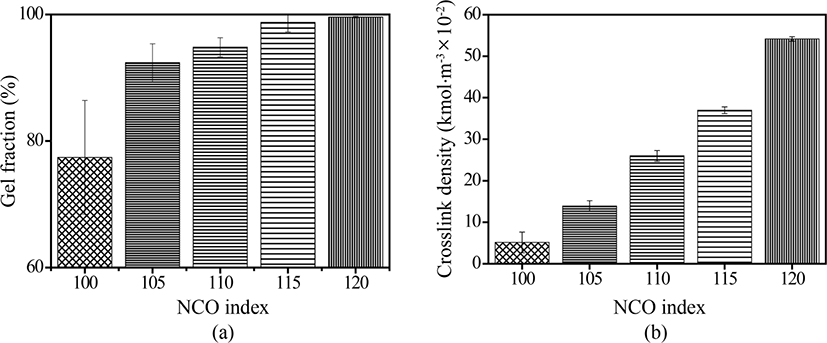
Figure 3 shows the dependence of tensile strength on isocyanate content in the polyurethane sample. The results support the direct dependence of tensile strength and the ratio of isocyanate. The PU elastomer with the highest NCO index (120) possess the best tensile strength and the least tensile strength is possessed by sample with lowest NCO index. The increment in the concentration of hard segment in the polymer matrix with the increase in the NCO index could be attributed as the reason for enhanced tensile strength. The hard segments in the PU act as physical cross-links which play the role of active fillers.21 This resists the deformations when the samples are subjected to the applied strain. These studies indicate that the hard domain is very effective in strengthening the elastomer. The hard segment region also plays a subordinate role in increased energy dissipation and domains of plastic deformation which leads to delayed microcrack formation and thus increases the toughness and strength of the elastomer.
The tear strength of samples indicates the resistance of a material to tear apart and is shown in Figure 4. Tear strength follows the same trend of tensile strength it increases with the rise in the NCO index. The deflection and bifurcation of cracks by the hard prepolymer domain could be the major cause for increased tear strength of the sample. In comparison to the base NCO index 100, the final composition of isocyanate index 120 shows a 30% increment in tear strength. The tear strength approaches a limiting increment on reaching 20% increment in the hard segment which is clearly observed from the comparable tear strength value of NCO index 115 and NCO index 120.
It is a general observation that elongation decreases as there is a rise in the concentration of the hard segment. The variation of elongation at break with increment in the NCO index is shown in the Figure 5. The elongation at break of target material exhibits a downturn trend as the isocyanate index shows an upsurge trend from 105 to 120.
Figure 6 indicates the hardness of PU samples. The hardness of the PU elastomer increases with the increase in the NCO index. This is because of the increment of the hard segment in the matrix. The hard segments resist the deformation in the sample. The increased cross-links induced by higher NCO/OH content could also be considered as a prominent reason for the overall increment in the hardness of the sample. The high NCO content leads to the formation of chemical intermediate such as allophanate, which improves the hardness of the elastomer.22
The coefficient of friction (COF) and abrasion resistance at different NCO index is given in Figure 7(a, b). These two properties are considered to be the most important for the applications such as rolls, wheels and so on. In this investigation Figure 7(a) indicates that the PU with higher NCO index possesses the lowest COF as it is discussed in the literature.23 The COF of hard PU is comparatively lower than that of the soft PU and it has a higher load-bearing capacity. A slight discrepancy is shown by the sample with NCO index 115.
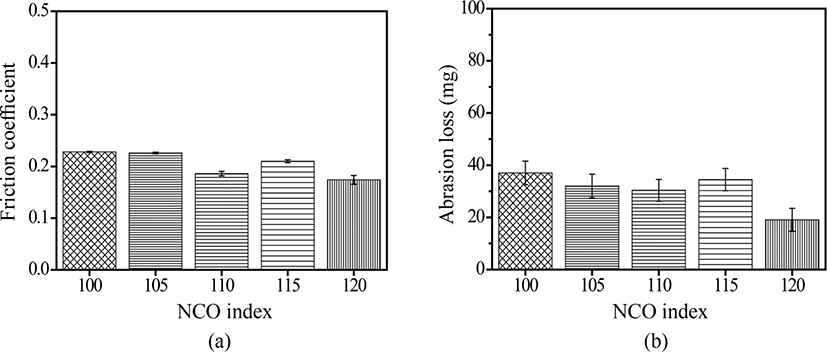
Figure 7(b) depicts the abrasion loss of PU at different NCO index. The sample with NCO index 120 shows the highest resistant to the wear mechanism and thus shows the least weight loss. In this investigation, the PU sample with the least hardness (NCO 100) shows the highest weight loss. This could be explained by the ease of erodent particle to press against the softer surface of the material which leads to the fast generation of cut in the sample surface.
Conclusions
In this study, a series of MOCA free fast curing polyurethanes with different isocyanate index have been successfully prepared from the developed pair of polyol and isocyanate prepolymer. The pot life of the fast curing system was determined by viscosity and fluid flow method. The results obtained from both methods shows great correlation, which ensures the accuracy of the data obtained. The time period at which the polyurethane retains its fluid nature and is fit for processing shall be considered to be the pot life. By this study, we conclude that the pot life of the criterion composite with NCO index 100 is between 6-8 sec. The gel fraction and crosslink density of polyurethane exhibit a direct correlation with the NCO index.The mechanical properties of the system such as tensile strength, tear strength, and hardness show an upsurge behavior with the increment in NCO index, while the coefficient of friction, elongation at break, and abrasion loss exhibit reduction in magnitude. The obtained mechanical property results and short pot life pinpoint the satisfactory utilization of this polyol-prepolymer system for processes requiring short processing time such as ribbon flow processing and so on.