Introduction
Urgent demands by society for both the reduction of carbon dioxide emissions and saving of fossil oil resources have steadily strengthened the regulation of fuel efficiency of cars. Although carbon black has been a powerful reinforcing filler of SBR compounds traditionally used in the preparation of the tread rubber of passenger car tires for a long time, it has been replaced by silica to improve fuel efficiency.1 The coupling of silica particles with rubber chains by forming covalent bonds through coupling agents significantly improves the mechanical properties of silica-filled SBR compounds and reduces their rolling resistance applicable to commercial tires.2 The synthesis of SBR with an appropriate functional group,3,4 the development of effective coupling agents with high reinforcing performance,2,5 and the use of a dual filler system composed of carbon black and silica,6,7 have been studied to improve the performance of tires.
Since hydrophilic silica has totally conflicting surface properties to hydrophobic rubber, SBR is generally mixed with silica in an internal mixer under high shear stress accompanied with coupling agents, cure accelerators, activators, and expansion oil.8 The mixing of rubber compounds in a dried state, called the dry masterbatch (DMB) method, is carefully operated to minimize the deterioration of rubber due to the elevation of temperature induced by attrition. However, the direct mixing of carbon black with emulsion SBR in liquid phase facilitates the preparation of carbon black-filled emulsion SBR compounds with the wet masterbatch (WMB) method.9 The hydrophobicity of carbon black promotes its coagulation with rubber and mixing them in liquid phase strengthens their interfacial interaction without deteriorating rubber. Water stripping using hot water easily separates WMB from organic solvent and water layers, recovering carbon black-SBR WMB. Fully functionalized and dispersed silica also facilitates the preparation of silica-SBR WMB by mixing hydrophobated silica and emulsion SBR, simplifying the compounding process for tire application.10 In contrast to emulsion SBR, solution SBR used in the manufacture of passenger car tires is dissolved in an organic solvent, and thus the hydrophobation of silica is a prerequisite to enhance the interaction between rubber and silica and to prevent silica aggregation during the mixing and recovery of silica-SBR WMB.11
Since the interaction between silica and rubber greatly affects the mechanical and dynamic properties of silica-filled SBR compounds, high dispersion of silica is essential to obtain improved physical properties because of the necessity for a sufficient interface between rubber and silica.12 The surface treatment of silica with alkoxysilanes such as 3-mercapto-propyltriethoxy silane and octyltriethoxy silane enhances its hydrophobicity and results in better reinforcing performance by improving the dispersion of silica in rubber.13,14 The organic moieties incorporated in the silica surface suppress silica flocculation during mixing and cure and lower rolling resistance by reducing the irreversible breakage of silica aggregates. Furthermore, the hydrophobated silica particles do not tend to aggregate in organic solvent, minimizing silica loss during the recovery process of WMB. The silane-treated silica prepared by Behn Meyer Europe GmbH showed high feasibility for the preparation of silica-filled SBR compounds applicable to the tread rubber of passenger car tires.15 The silica-NR WMB prepared using silicas treated with Si-747 silane with long arms facilitated the preparation of silica-filled NR compounds with low rolling resistance due to appropriate interaction between rubber and silica.16
Bis-(triethoxysilylpropyl) tetrasulfide (TESPT) is a typical coupling agent that has been successfully used in silica-filled rubber compounds.17 Its ethoxy groups react with the hydroxyl groups of silica and its sulfide groups with the double bonds of rubber, respectively, producing covalent bonds that combine silica and rubber and improve their tensile properties. The incorporation of TESPT into silica also makes its surface hydrophobic, so TESPT-treated silica shows high feasibility for application as a raw material for the preparation of silica-SBR WMB. However, the surface treatment of silica by TESPT in the preparation of silica-SBR WMB should be carefully optimized to obtain adequate hydrophobicity of silica and proper mobility of TESPT, because the TESPT added to rubber works as a lubricant as well as coupling agent.18
Instead of the addition of TESPT to rubber during mixing, SBR compounds reinforced with silica pretreated by TESPT exhibited improved properties, especially both wet traction and rolling resistance.19 TESPT incorporated in silica connects silica particles and produces organic networks on their surfaces. The physical entanglement of rubber chains with the networks dispersed on the silica surface reduces irreversible deformation under dynamics stress, resulting in better dynamic properties. The reaction of 3-aminopropyltriethoxy silane (AP)-incorporated silica with bisphenol A diglycidyl ether (BG) also forms organic networks composed of amine groups of AP and glycidyl group of BG (APBG).20 The change in the molar ratio of BG to AP in the surface treatment alters the surface state of silica in terms of the exposed functional groups and the concentration of APBG connecting bonds. The reduction of surface hydroxyl groups of APBG silica suppresses silica flocculation in SBR compounds and the entanglement of rubber chains with the connecting bonds improves both tensile and dynamic properties. Methylene diphenyl diisocyanate forms organic networks among neighboring silica particles with urethane linkage and the organic networks provide adequate hydrophobicity and rein-forcement of SBR by entanglement.21
The silica-SBR WMB preparation method can be classified by the way silica is treated in the aspects of the species and amount of modifier incorporated and recovery method of WMB. Scheme 1 shows the classification of WMB preparation methods. In the treatment methods classified by types I and II, TESPT reacts with silica in liquid phase, followed by mixing with SBR solution. WMB particles are recovered by water stripping in type I, and by evaporation in type II. In the treatment of type III, silica-SBR WMB is prepared by direct mixing of pretreated silica with SBR solution followed by evaporation of solvent from a dense dough of WMB. The temperature of silica treatment and the amount of modifiers influence the state of silica-SBR WMB. The exposure of silica to water in water stripping or the stirring of silica suspension in organic solvent may induce the aggregation of silica particles. In addition, the species and type of organic material incorporated in silica greatly influence the interaction between rubber and silica and the dispersion of silica in rubber. Therefore, the method of treating silica with organic material in the preparation of silica-SBR WMB is very important to obtain high performance silica-filled SBR compounds.
In this study, we prepared several silica-SBR WMBs by varying the species and amounts of organic modifier in the silica treatment method, and the recovery methods of WMB. Silica was modified with TESPT in liquid phase by stirring at ambient temperature and refluxing in toluene, while the treatment of silica in gas phase was also tried. The successive reaction of AP-incorporated silica with BG in toluene provided pretreated silicas containing APBG connecting bonds on their surface and the successive reaction of amine groups of diaminohexane (AM) with glycidyloxy groups of (3-glycidyl-oxypropyl)trimethoxysilane (GP) and amine groups in gas phase produced GPAM connecting bonds. The state and amount of organic material incorporated in silica and silica-SBR WMB were investigated from their TG/DTA curves. The partial extraction of rubber from silica-SBR WMB using a Soxhlet apparatus enabled the comparison of incorporated states of TESPT in silica according to their preparation methods.22 The treatment of silica with TESPT in liquid phase following by mixing facilitated the preparation of silica-SBR WMB, but a considerable amount of silica loss was inevitable. In contrast, the treatment of silica either in gas or liquid phase followed by mixing with SBR solution and evaporation effectively produced silica-SBR WMB with high silica yield. The silica treatment method with organic materials greatly affected the physical properties of silica-filled SBR compounds (WSBR) prepared using silica-SBR WMB because the state and amount of organic material dispersed in silica determined the interaction between rubber and silica. The silica-SBR WMB prepared with pretreated silicas containing either APBG or GPAM connecting bonds might enhance the entanglement of rubber with the bonds and suppress irreversible deformation, resulting in low rolling resistance without sacrificing mechanical properties.
Experimental
Various silica-SBR WMB were prepared by varying the silica treatment method, the species and amount of organic material incorporated in silica, and their recovery method. Table 1 summarizes the preparation methods of silica-SBR WMB. The silicas prepared by consecutive mixing with TESPT were named CSilx, while those prepared by pretreatment with various organic material named PSilx, where x denoted the serial number of silicas. In a consecutive mixing process precipitated silica (Oriental Silica Co., Tokusil 195) was added to n-heptane (SK Global Chemical Co., Ltd.) solution of TESPT (Dow Corning) charged in a 5000 mL continuous stirred tank reactor (CSTR) and subsequently stirred at 1000 rpm for 2 h. CSil1 was treated at ambient temperature, and CSil2-CSil4 were heated at 110°C for refluxing. After the treatment of silica with TESPT, SBR (Kumho Petrochemical Co., 5251H) solution dissolved in n-heptane was added and stirred further for 1 h. The water stripping method was used in the recovery of WMB1, WMB2, and WMB4 from the suspension of CSil1, CSil2, and CSil4 silicas, respectively. Boiled water was poured into the suspension and collected particles of WMB settled at the bottom. In contrast, WMB-3 was recovered by evaporation of solvent from the dense suspension of SBR and CSil3. Since sampling of CSil1-CSil4 from the CSTR was very difficult, their samples for characterization were prepared separately in a round-bottomed flask with a condenser attached.
PSil5 was prepared by injection of TESPT solution dissolved in ethanol (Daejung Chemical & Metals Co.) in a fluidized bed reactor at 90°C followed by drying at 130°C for 8 h in an oven. The organic material incorporated in PSil6 was AP and BG. In the preparation of APBG50 silica with equivalent moles of amine and glycidyl groups, the incorporation of AP (Dow Corning) to silica and subsequent reaction with BG (KER 828, Kumho P&B Chemical Inc.) were carried out in toluene by refluxing. On the other hand, PSil7 was a commercial networked silica manufactured by Mirae Scientific Instruments Inc. using a fluidized bed reactor. The organic materials used in the formation of networks on it were GP (Dow Corning) and AM (Invista), but it also contained small amounts of undisclosed promotors. The total amount of organic materials incorporated in it was 13.5%. Pretreated silicas, PSil5-PSil7, were directly added to SBR solution dissolved in n-heptane and stirred at ambient temperature for 1 h. Their WMBs were recovered by evaporation. The recovered silica-SBR WMB, regardless of preparation method, was dried in an oven at 60°C for 12 h.
Silica-filled SBR (WSBR) compounds were prepared by mixing silica-SBR WMB with additives such as sulfur, accelerators, activators, and expansion oil following the procedure described in Table 2. In the first step of initial mixing, WMB was charged in an internal mixer (Mirae Scientific Instruments Inc., 300 cm3) set at 110°C accompanied with TDAE expansion oil (Kukdong Oil & Chemial Co.). After 5 min mixing, activators such as zinc oxide (ZnO, Daewon Co.) and stearic acid (S/A, Duksan Pure Chemical Co.) were added. Initial mixing products were dumped after 10 min mixing. The initial mixing product was charged in the internal mixer set at 70°C for final mixing. After 0.5 min mixing, insoluble sulfur (S, Miwon Chemical Co.) and accelerators such as N-cyclobenzyl sulfenamide (CBS, Miwon Chemical Co.) and diphenylguanidine (DPG, Kumho Petrochemical Co.) were added. The final mixing was completed after further mixing for 2.5 min. Final compounds were milled for 11 cycles with a two-roll mill at 20 rpm (C.W. Brabender Inc.; Model PM-300, #138-B).
Step | Time, min | Procedure | Temperature, °C1) |
---|---|---|---|
Initial | 0 | charge WMB with TDAE oil | 110 |
5 | add ZnO and S/A | ||
10 | dump | ||
Final | 0 | charge initial masterbatch | 70 |
0.5 | add sulfur, CBS, and DPG | ||
2.5 | mixing completed |
The silica content of WSBR compounds was adjusted to 85.3 ± 0.3 phr with a specific gravity of 1.201 ± 0.003. Since the silica loss of CSil1, CSil2, and CSil4 was considerable, high reinforcing silica Ultrasil 7000GR (Evonik, abbreviated as GR herewith) was supplemented by being accompanied with an appropriate amount of TESPT in the preparation of WSBR1, WSBR2 and WSBR4. The silica loss in the preparation of silica-SBR WMB from CSil3 was too high, and thus the preparation of corresponding WSBR was abandoned. Table 3 lists the composition of prepared WSBR compounds. A reference SBR compound reinforced with GR silica, called DSBR-GR, was also prepared with the DMB method for comparison.
Rheocurves of silica-filled SBR compounds were obtained by an oscillating disk rheometer (Daekyung Co., DRM-100) at 160°C following the procedure described in ASTM D 2084. t40 and t90 cure times were defined as the times required for the cure for 40% and 90%, respectively and obtained from the rheocurves. τmin, τmax, and Δτ were also determined from the rheocurves as the minimum torque, maximum torque, and difference between minimum and maximum torques, respectively. The rubber compounds were cured at 160°C for t90 and 1 minute more in a cure press (Daekyung Co., DHP-300).
TG/DTA curves of WMB and WSBR compounds were recorded on a thermogravimetric analyzer (Shimadzu, DTG-60H) with increasing temperature from ambient to 800°C at 10°C/min in an air flow of 50 ml/min. SEM images of WMB and WSBR compounds were observed using a scanning electron microscope (Zeiss, Gemini 500). The samples were sputtered with plasma in a plasma sputter (Mirae Scientific Instruments Inc.) at 200 W for 120 min to remove rubber.
Mooney viscosity of silica-filled SBR compounds denoted by ML (1+4) @ 100°C were obtained using a Mooney visco-meter (Daekyung Co., DMV-200C). t5 and t35 scorch times were defined by the time required for the increase in Mooney viscosity by 5 and 35 units at 135°C, respectively.
The strain-stress curves of rubber compounds were recorded using a universal tensile tester (Daekyung Co., DUT-500C) at ambient temperature with a crosshead speed of 500 mm/min according to ASTM D 412. Four dumbbell-type samples were used for each measurement. M-200% was defined by the modulus at 200% elongation and tensile strength by the stress at break point.
The variation of tanδ of silica-filled rubber compounds with temperature was recorded on a dynamic mechanical analyzer (DMA, TA Inc., DMA Q800). Temperature increased from −80°C to 80°C at a heating rate of 3°C/min with a frequency of 10 Hz, amplitude of 30 μm, and force track of 125%. The variation of storage modulus with strain was also measured using the DMA from a strain of 0.01-20% with frequency of 1 Hz at ambient temperature. The Payne effect was defined by the difference in storage moduli at 0.01 and 20% strain.
A DIN abrasion apparatus (Daekyung Co., DRA-460D) was used in the measurement of the average loss in weight of a cylindrical sample with a diameter of 16 mm and thickness of 13 mm at a rotating speed of 4061 rpm following DIN 53516.
Results and Discussion
The silica treatment method influences the state of organic material incorporated in it. Figure 1 shows TG/DTA curves of silicas treated with TESPT. The TG curves of CSil1, CSil2, CSil4 and PSil5 were generally composed of three weight losses: a steep weight loss below 100°C, slow weight loss at 100-250°C and further weight loss above 220°C. The first weight loss was attributed to the desorption of physically adsorbed water and the second one to the gradual removal of the surface hydroxyl group.23,24 The combustion of organic material incorporated in silica caused appreciable weight loss around 250°C. Although the TG curves of the silicas treated with TESPT were very similar to each other, remarkable differences were observed in the weight losses attributed to desorption of water and to the combustion of organic material according to their treatment method. The first weight loss of CSil1 treated by stirring at ambient temperature with TESPT was larger by 0.5% than that of CSil2 treated by refluxing, indicating that treatment at elevated temperature removed more hydroxyl groups at the incorporation of TESPT. The smallest first weight loss of PSil5 treated in gas phase reflected the high removal of hydroxyl groups and the increase in the incorporated amount of TESPT. The high dosing of TESPT in the preparation of CSil4 with 16% induced a large third weight loss above 250°C, and revealed the presence of plentiful TESPT incorporated in silica with different chemical states. The removal of hydroxyl groups and large amount of TESPT incorporated in PSil5 confirmed the effectiveness of the gas phase treatment to achieve high and stable incorporation of TESPT.
The treatment method of the silicas treated with TESPT also caused appreciable differences in their DTA curves, as shown in Figure 1(B). The endothermic peaks observed below 100°C were attributed to the desorption of water, while the exothermic peaks observed around 180°C and above 320°C to the combustion of organic material incorporated in silica. The general shapes of the first and second peaks were similar, regardless of their preparation method, while the third exothermic peaks were different in terms of their peak height and maximum temperature. The large and broad peaks of CSil4 compared to those of other silicas reflected its high incorporated amount of TESPT due to its high dosed amount of 16%. The presence of a side peak of PSil5 at 350°C indicated a stably incorporated state of TESPT compared to that incorporated in CSil1 and CSil2.
The treatment and recovery methods of silica determine the shape of WMB produced. Figure 2 shows photos of WMB prepared using CSil and PSil silicas. WMB1, WMB2 and WMB4 were composed of discrete particles with diameters of 0.4-10 mm, but most of them were in the range of 4-6 mm. WMB3 was divided by two parts: one was rubber-rich sheet and the other was composed of fine silica particles. In contrast, WMB5 and WMB6 were white dough. Although the modifier of WMB1 and WMB5 was commonly TESPT, their shapes were definitely different according to their preparation method. In the preparation of WMB using the silicas treated in liquid phase followed by mixing with SBR solution, the mechanical power employed for stirring produced fine silica aggregates covered with rubber. The recovery of WMB by water stripping resulted in the phase separation of the silica-rubber suspension into a solid phase composed of WMB and two liquid phases of n-heptane and water. Insufficiently treated silica particles were sedimented in the water phase. However, pretreated silicas, PSil5 and PSil6, were already coated with organic material and easily clumped with rubber, shaping dough without segregating into fine WMB particles. Silica particles were not observed on the surface and bulk of dough after evaporation of heptane from recovered WMB. Although WMB3 was recovered by evaporation, not by water stripping, the insufficiently treated silica particles aggregated and caused a heterogeneous distribution of silica. Some parts of WMB were recovered as dough, while silica-rich domains segregated into silica particles. These results meant that the insufficiently treated silica particles was responsible for the silica loss observed in the preparation of WMB in liquid phase, and the silicas treated in gas phase with stably incorporated organic material caused negligible silica loss.
Since WMB contains plenty of rubber, it may be better to study the incorporated state of rubber to the silica in it after partial removal of rubber using the Soxhlet apparatus with toluene.25Figure 3 shows TG/DTA curves of WMB5 after extraction with toluene for different times. The change in the slopes of TG curves of WMB5 at 300-500°C indicated mixed states of rubber with different physical and chemical states. The silica content of WMB5 before extraction was 42%, but the extraction of rubber for 4 h increased it to 60%. The increase in silica content was very small even after further extraction for 12 h confirming that extraction for 4 h was sufficient to remove the easily removable bulk rubber contained in WMB5. The content of removable rubber in WMB5 was about 18%, reflecting that most rubber was stably incorporated in silica. The DTA curve of WMB5 suggested the presence of four different kinds of rubber in it. The extraction removed only the rubber combusted at 450°C, while the other three kinds of rubber remained stably even after extraction. Further study on the characteristics of rubber contained in WMB would provide a profound understanding of the physical and chemical states of the rubber.
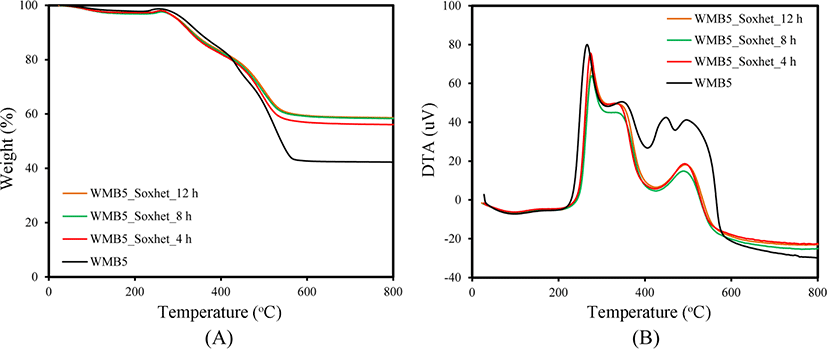
The amounts of rubber contained in WMB remaining after extraction varies with the treatment method. Figure 4 compares TG/DTA curves of WMB1 and WMB5 prepared using silicas treated with TESPT in liquid and gas phases, respectively, after Soxhlet extraction of rubber with toluene for 12 h. Their general shapes were very similar to each other in terms of weight loss temperature and combustion pattern. However, the large remaining weight of WMB5 compared to that of WMB1 implied that the portion of stably incorporated rubber in the former was higher than that of the latter because their rubber contents were almost the same. The difference in the incorporated amounts of TESPT between CSil1 and PSil5 was around 1 wt%, but the difference in amounts of extractable bulk rubber of WMB1 and WMB5 was about 11 wt%, indicating that the gas phase treatment increased the portion of rubber stably incorporated in silica in WMB.
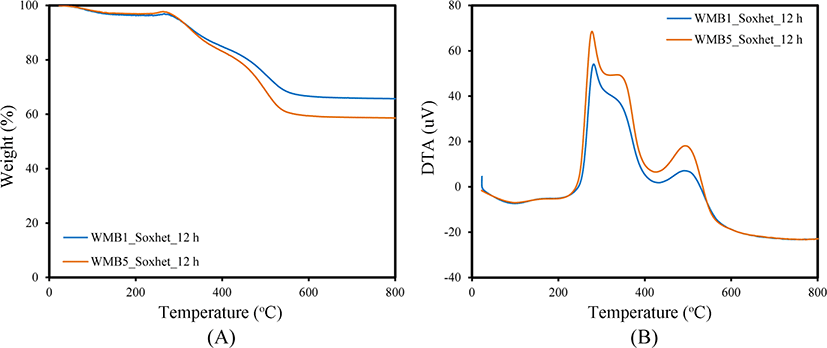
Although the amount of rubber incorporated stably in silica in WMB varied considerably with the treatment method, no definite difference was observed between the SEM images of WMB1 and WMB5 extracted with toluene, as shown in Figure 5. Most silica particles aggregated while maintaining their primary particle shapes, and did not produce a fused state. Since WMB was prepared below 150°C with mixing in liquid phase in the absence a strong shear force, severe aggregation and breakage of silica particles did not occur. The absence of appreciable cracks and grooves in the surface of silica-SBR WMB extracted with toluene suggested that the rubber incorporated in silica would be mainly dispersed on its surface.
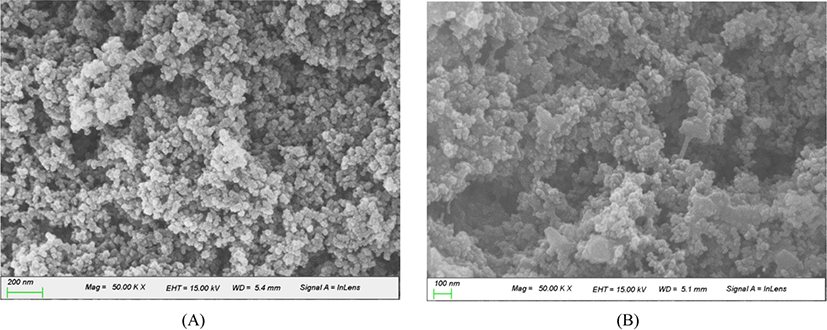
The content of silica in rubber compounds plays a significant role in determining the physical properties of silica-filled rubber compounds,18 and therefore the confirmation of their silica content is required prior to discussion on the effect of the silica treatment method on their reinforcement performance. Figure 6 compares the specific gravities of WSBR compounds. Their specific gravities, except WSBR3, were in the range of 1.201 ± 0.003, indicating highly adjusted silica content in them. The regression of specific gravity data obtained from many silica-filled SBR compounds in our laboratory provided a relationship between the specific gravity (ρ) and silica content (sc) of silica-filled SBR compounds where ρ = 0.0023sc + 1.005 with high R2 of 0.9933. Based on the relationship the prepared WSBR and DSBR compounds except for WSBR3 had silica content of 85.3 ± 0.2 phr, regardless of the silica treatment method and rubber compound mixing method. Since the silica content of WSBR3 was estimated to be 60.4 phr, it was excluded from the discussion of the properties of WSBR compounds.
The content of silica in silica-filled SBR compounds can be confirmed from their TG curves. Figure 7 shows TG/DTA curves of WSBR compounds with almost identical shapes. Weight loss below 350°C might be attributed to the desorption of volatile additives, while that at 400-420°C to the combustion of rubber.26 The combustion of rubber that was stably incorporated in silica might induce weight loss at 420-500°C. The same residual weight of all WSBR compounds verified their same content of silica. The DTA curves were composed of four peaks, while their characteristics varied with the silica treatment method used in the preparation of WSBR compounds. The first and second common endothermic peaks, which started around 350°C revealed the desorption of volatile additives. The combustion of rubber incorporated in silica might cause the last weight loss at 450-550°C, but further study is needed to clarify the physical and chemical characteristics of these peaks.
The cure rates of WSBR compounds vary with the silica treatment method and the organic material used in the treatment of silica, as shown in Figure 8. The high dosing amount of TESPT, 16% per g silica, in the treatment of the silica used for the preparation of WSBR4 caused both short t40 and t90 times. The shortest t40 times of WSBR6 prepared using APBG50 silica-SBR WMB might be due to the exposed amine groups of AP that accelerated the cure of SBR.20 Since the treatment of silica with TESPT or other alkoxysilanes removed hydroxyl groups and lowered their surface concentration, the suppression of the inactivation of basic accelerator DPG via its adsorption on them in WSBR compounds reduced their t40 times compared to DNR-GR.27 However, the t90 times of WSBR5 and WSBR6 were slightly longer than that of DNR-GR. The treatment of silica with TESPT or APBG removed some hydroxyl groups of silica and reduced the amount of DPG inactivated through adsorption, resulting in shortened t40 times, while the small amount of DPG added to WSBR compounds (0.55 phr) compared to that of DNR-GR (1.1 phr) lowered the total cure rate and extended t90 time.
Figure 9 shows τmin and Δτ of WSBR compounds. τmin varied widely from 11.9 to 26.5 dN·m, while most Δτ were in a narrow range of 33.5 ± 2.5 dN·m, except WSBR5. Although the same amount of TESPT (8 wt%) was dosed to the treatment of silica that was used in the preparation of WSBR1, WSBR2, and WSBR5 compounds, their τmin was considerably higher than DSBR-GR. The silica flocculation that occurred at mixing in silica-filled SBR compounds usually increased their τmin,28 but too high τmin of WSBR compounds reflected the high contribution of viscosity to τmin due to the attrition between rubber and silica (discussed later relating to viscosity). In contrast, Δτ representing the extent of cure of WSBR compounds was similar, indicating a weak contribution of the silica treatment method to the progress of cure, because crosslinking of rubber and coupling between rubber and silica mainly determined the increase in torque during cure. The relatively small Δτ of WSBR5 implied the partial exclusion of the sulfur contained in incorporated TESPT from cure because of its stably incorporated state.
The SEM images of silica-filled rubber compounds after plasma sputtering are beneficial to clarify their silica dispersion when their silica content is too high to observe separated primary silica particles i.e. 80 phr. Figure 10 shows SEM images of WSBR compounds obtained after plasma sputtering and their simplified schematic diagrams. The silica particles made large agglomerates on WSBR1, but the presence of cracks and grooves formed by the removal of rubber reflected the entangled state of rubber and silica. The fused state of silica particles and negligible cracks and grooves in WSBR2 implied a low probability of entanglement of rubber with silica. The size of silica agglomerates reduced on WSBR4 compared to that on WSBR1 and the increase in the probability of grooves in it compared to that on WSBR2 indicated an enhancement of the entanglement of rubber with silica. The high frequency of small cracks and grooves in WSBR5 and WSBR7 reflected the highly entangled state of rubber and silica. In contrast, the large and deep grooves observed in DSBR-GR suggested a mixed state of rubber and silica with their large domains, indicating poor dispersion of silica in rubber. The SEM images of WSBR5 and WSBR7 with fine grooves distributed evenly among remaining silica particles showed a highly entangled state of rubber with silica, resulting in high dispersion of silica and high interfacial area between rubber and silica.
The presence of organic materials on silica affects the viscosity and scorch time of WSBR compounds, as shown in Figure 11. The Mooney viscosities of WSBR1, WSBR2, and WSBR4 were high compared to that of DSBR-GR, while those of WSBR4, WSBR7, and DSBR-GR were relatively low. The surface treatment of silica with organic material considerably suppresses the aggregation of silica particles29 and the addition of TESPT usually reduces viscosity because small TESPT molecules work as a masking agent for hydroxyl groups and a lubricant.18 The WSBR1, WSBR2, and WSBR4 reinforced by silicas with incorporated TESPT exhibited high viscosity, revealing that the incorporated TESPT did not work as a lubricant. The highest viscosity of WSBR6 might be due to the reaction between AP and BG that produced stably incorporated organic networks without having capability to reduce viscosity. The low viscosity of WSBR4 was responsible for high dosing of TESPT, so non-incorporated TESPT could work as a lubricant. On the other hand, the small molecular promotors of PSil7 worked as a lubricant and the lowered the viscosity of WSBR7 comparable to DSBR-GR in which the addition of free TESPT during mixing caused low viscosity. The silica flocculation of WSBR compounds should be suppressed because the silica surface was covered with organic material, so the high τmin and the viscosity of WSBR compounds was mainly responsible for the attrition between rubber and silica.
Since the rapid increase in torque during cure induces the shortening of scorch time, the t35 scorch time of WSBR1, WSBR2. WSBR3 and WSBR4 varied with a similar trend to their t90 cure time (Figure 8), except for WSBR6 and WSBR7. The negligible inactivation of DPG on WSBR6 due to compact masking of the silica surface by organic networks caused the shortest t35 scorch time. The promotor included in PSil7 retarded cure and extended t35 scorch time on WSBR7. The longest t35 scorch time of DSBR-GR was responsible for the partial inactivation of DPG by its adsorption on hydroxyl groups on silica, because DPG definitely shortened the induction period of silica-filled SBR compounds.30
The species and amount of organic materials incorporated in silica affect the tensile properties of silica-filled rubber compounds. Figure 12 shows M-200% and tensile strength and WSBR compounds. Since the brittleness of WSBR4 made it impossible to measure M-300%, M-200% was employed in the comparison of their moduli. The modulus of WSBR4 was extraordinarily high because of the excessive amount of TESPT dosed in the treatment of silica. On the contrary, the absence of TESPT on PSil6 and PSil7 lowered modulus. The tensile strength of WSBR compounds showed an opposite trend to modulus, while their relationship was weak. The high modulus limited extension, and thus tensile strength was generally low. As expected, the elongation at break of WSBR compounds varied similarly with their tensile strength (not shown).
The interaction between rubber and silica determines the wet traction and rolling resistance of silica-filled rubber compounds. Since the direct measurement of these properties is not easy, tanδ values at 0°C and 70°C are usually used to reflect wet traction and rolling resistance, respectively.31Figure 13 shows tanδ values of WSBR compounds at 0°C and 70°C. The tanδ values at 0°C of WSBR compounds corresponding to wet traction were smaller than that of DSBR-GR, except for WSBR7. The higher tensile strength and low modulus of WSBR compounds weakened energy dissipation, lowering the tanδ value at 0°C.32 The exceptionally high tanδ @ 0°C of WSBR7 was attributed to the physical entanglement of rubber chains with silica particles and to maintain low viscosity and modulus, while the high viscosity of WSBR6 suppressed the entanglement and resulted in low wet traction performance. The tanδ value @ 70°C of WSBR compounds exhibited a considerably different trend form their tanδ @ 0°C. WSBR1-WSBR4 compounds reinforced with TESPT-incorporated silica showed higher values of tanδ @ 70°C, indicating poor rolling resistance. On the contrary, WSBR6 and WSBR7 reinforced by silicas with organic networks dispersed on their surface exhibited lower tanδ @ 70°C than DSBR-GR, confirming the improvement of rolling resistance by physical entanglement of rubber chains with silica particles. The lowest viscosity of WSBR7 due to its promotors further reduced tanδ @ 70°C, achieving very small rolling resistance.
Figure 14 shows DIN abrasion and the Payne effect of WSBR compounds. The variance of DIN abrasion according to silica treatment was small except for WSBR6. The high viscosity of WSBR6 caused high DIN abrasion. The Payne effect also exhibited a similar trend as DIN abrasion. The presence of small molecular promotors in WSBR7 induced an extremely low Payne effect. The lowest Payne effect of WSBR7 represented the smallest formation of silica aggregates and provided persuasive reasons for its low τmin, low viscosity, high wet traction and low rolling resistance.
Although the low rolling resistance of silica-filled SBR compounds is an important issue in manufacturing passenger car tires, it is not easy to achieve rolling resistance with maintaining sufficient mechanical properties because these properties are intricately correlated. Silicas with organic networks composed of connecting bonds on their surface showed a greater inclination to lower rolling resistance when the compounds prepared using them preserved both Mooney viscosity and a small Payne effect. The low viscosity allowed the elastic movement of rubber chains to entangle with the connecting bonds and the small Payne effect reflected the negligible formation of silica aggregates, inducing irreversible deformation under dynamic stress. Furthermore, the presence of organic networks on the silica surface and mixing in liquid phase in the preparation of WMB enhanced the dispersion of silica in rubber. Reinforcement by silica through entanglement in silica-filled SBR compounds, not by chemical bonds, resulted in low rolling resistance without causing the deterioration of rubber properties.
Conclusions
The preparation methods of silica-SBR WMB in terms of silica treatment with organic material, mixing of treated silica with SBR solution, and recovery method of WMB greatly influenced the amount and stability of organic material incorporated in them, and determined the physical properties of silica-filled SBR compounds produced using the WMB. The treatment of silica with TESPT in liquid phase followed by mixing with SBR solution and recovery by water stripping produced silica-SBR WMB composed of small particles, while considerable losses of silica and TESPT were inevitable. The mixing of pretreated silica with SBR solution followed by evaporation of solvent from a dense silica-SBR suspension formed dough type silica-SBR WMB with high silica yields above 99%. The pretreatment of silica with TESPT or other organic material was beneficial for silica yield and stable incorporation of organic material, but stably incorporated organic material increased the viscosity of WSBR compounds because of the loss of organic molecules workable as lubricant. However, the presence of organic networks formed on silicas treated with APBG and GPAM significantly lowered the tanδ @ 70°C of corresponding WSBR compounds by maintaining low viscosity and suppressing silica flocculation. The WSBR compounds prepared using silica-SBR WMB based on the silica treated with GPAM and small molecular promotors showed both improved wet traction and rolling resistance without sacrificing mechanical properties due to reinforcement based on the entanglement of rubber chains with GPAM connecting bonds. In addition to the presence of organic networks on the surface of PSil7 silica, the high dispersion of silica, the maintenance of low τmin and Mooney viscosity, and small Payne effect of WSBR7 achieved low rolling resistance of silica-filled SBR compounds.