Introduction
작은 생활용품 및 부품에서부터 자동차, 항공기의 큰 파트까지 다양한 분야에서 플라스틱이 사용되고 있다. 이러한 플라스틱 제품은 대부분 사출성형을 통해 생산된다.1 사출 성형은 복잡한 형태라도 성형이 가능할 뿐만 아니라 동일한 형상을 안정적이고 빠르게 대량 생산 할 수 있다는 장점이 있다.
사출성형은 충전, 보압, 그리고 냉각 단계 등 일련의 과정으로 구성되어 있는데 충전단계에서는 속도와 시간이 중요한 요소이고 보압 단계에서는 압력의 크기와 시간이, 그리고 냉각에서는 온도와 시간이 중요하게 작용한다.2
플라스틱 사출성형 제품은 성형 조건뿐 만 아니라 재료의 특성 및 제품 형상 등 다양한 요인으로 성형결함이 발생하게 된다.3 성형결함 중 특히 휨이나 뒤틀림은 치수 정밀도를 저하시켜 조립이 필요한 제품에서 조립 불량을 야기할 뿐만 아니라 제품의 구조적 안정성에 문제를 일으킨다. 이러한 문제 해결을 위해 과거에는 숙련된 경험에만 의존되었던 것을 성형해석 CAE (Computer Aided Engineering)을 활용한 과학적인 접근 방법이 활용되고 있다.
본 연구에서는 성형품의 치수 정밀도에 가장 크게 영향을 미치는 사출성형 수축을 관찰하였다. 연구에 사용된 재료는 보강재로 사용되는 유리섬유(Glass Fiber) 및 Calcium Carbonate (CaCO3)를 함유한 다른 두 그레이드의 PPS이다. 성형 조건 중 사출 온도와 사출 속도, 쿠션량을 변화하며 두 수지에서 성형수축을 관찰하였다. 실험과 해석을 통하여 성형수축을 측정하고 비교하였다.
Experimental and CAE analysis
본 연구에서 사용한 수지는 SK Chemical사의 PPS로 보강재 함유량이 다른 2개의 Grade로 선정하였다. 본 연구에서 사용한 PPS1은 E1040G, PPS2는 E5060G이다. Table 1은 두 수지의 보강재 함유 정보를 보여주고 있다. Figure 1은 두 재료의 전단전도를 보여준다. 유리섬유와 Calcium Carbonate를 함유한 PPS2가 유리섬유만 함유한 PPS1에 비해 점도가 큰 것을 알 수 있다.
Resin | Grade | Supplier | Composition |
---|---|---|---|
PPS1 | E1040G | SK Chemical |
PPS + Glass Fiber 40% |
PPS2 | E5060G | SK Chemical |
PPS + Glass Fiber 35% + Calcium Carbonate 30% |
본 연구는 실제 사출 실험과 CAE해석을 수행하였는데 총 2가지의 연구모델을 사용하였다. 원형 형상의 수축시편은 ASTM D955규격의 시편으로 지름 99.90 mm, 두께 3.20 mm이다. 사각 형상의 수축시편은 ASTM D 955 규격의 시편으로 한 변의 길이가 59.93 mm, 두께 2.00 mm이다. Figure 2에 두 가지의 시편형상 및 스프루, 게이트를 나타내었다. Figure 3은 원형 시편과 사각 시편을 성형하기 위한 금형을 보여주고 있다. 한 금형에서 로터리 방식으로 한쪽의 유동을 막아 원하는 시편만 사출하도록 하였다.
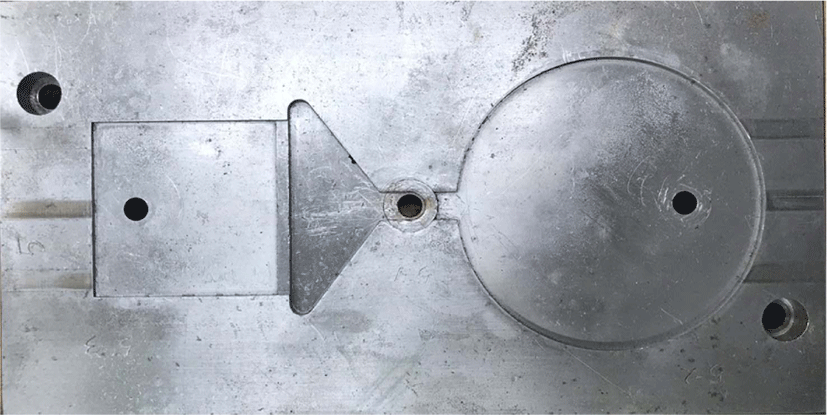
성형 조건은 사출 온도와 사출 속도, 사출유닛의 쿠션량으로 선정하였으며 각 인자의 수준을 세 개로 선정하였다. Table 2는 본 연구의 성형 조건들을 보여주고 있다. 쿠션량은 사출이 완료된 후 배럴 앞쪽에 남아 있는 스트로크의 양을 칭한다. 충분한 보압을 주기 위해서는 적당한 양의 쿠션이 필수적이다. 보압 전환 위치는 공통으로 전체 캐비티의 90%를 충전한 위치로 결정하였다. 실험과 해석은 Table 2에 나와 있는 조건으로 동일하게 수행하였다.
Mold Temp. (°C) | Nozzle Temp. (°C) | Injection Speed (mm/s) | Cushion (mm) | Packing Time (sec) | Packing Pressure (MPa) |
---|---|---|---|---|---|
130 |
300 310 320 |
80 | 5 | 10 | 80 |
310 |
50 80 110 |
5 | |||
310 | 80 |
2 5 10 |
사출성형 실험을 수행하기 위해 Figure 4의 우진 플라임의 전동식 사출 성형기(TE 110-IE2)를 사용하였다. 사출기의 형체력은 110 ton이고, 스크루 직경은 32 Ø이다. 최대 사출압은 154 MPa이며 최대 사출률은 322 cm3/s, 최대 사출속도는 400 mm/s이다.
각 조건별 실험에서 초기 10회의 사출시편을 버린 후 안정된 공정에서 5개의 시편을 사출하여 분석하였다. 분석은 각 조건당 5개 시편 측정값의 평균을 이용하였다. 시편의 치수 측정은 Mitutoyo사의 디지털 버니어 캘리퍼스(CD-20APX)를 이용하였다. Figure 5는 시편에서 측정 위치를 보여주고 있다. 수지의 흐름 방향과 흐름 직각 방향의 수축을 측정하였다.
사출성형 해석의 지배방정식은 Cauchy의 운동법칙이며, 이 방정식을 식 (1)에 나타내었다.4
사출성형해석S/W는 Moldflow Insight 2019이다. 3차원 유동과 관성을 고려하여 해석하였다.5
Moldflow에서 생성한 모든 메시는 3D 타입으로 Table 3에 메시의 수와 최대 종횡비를 나타냈다.
Model | Elements | Max. Aspect Ratio |
---|---|---|
Circular Shape | 474,487 | 26.90 |
Rectangular Shape | 565,822 | 25.55 |
성형해석 후 변형해석 결과를 이용하여 최종 예측된 치수를 측정하였다.
Result and Discussion
해석으로 예측한 충전 패턴과 사출성형의 숏샷(short shot) 결과를 Figure 6과 Figure 7에 비교하여 나타냈다. 성형 조건은 사출 온도 310°C, 사출 속도 80 mm/s, 쿠션량 5 mm이다. PPS2는 PPS1에 비해 재료의 점도가 높아 흐름성이 낮게 나타났다. 원형 시편의 PPS1 결과를 살펴보면 대체로 해석과 실험에서의 충전 패턴 결과가 일치하는 것으로 보인다. 원형시편의 PPS2는 실험에서는 젯팅을 보이며 해석과 다른 충전 패턴을 보였다. 사각 시편의 PPS1와 PPS2 결과는 실험과 해석의 충전 패턴 양상이 일치하는 것으로 나타났다. 사각 시편은 팬 게이트(fan gate)를 사용하고 있는데 젯팅이 발생하지 않았다.
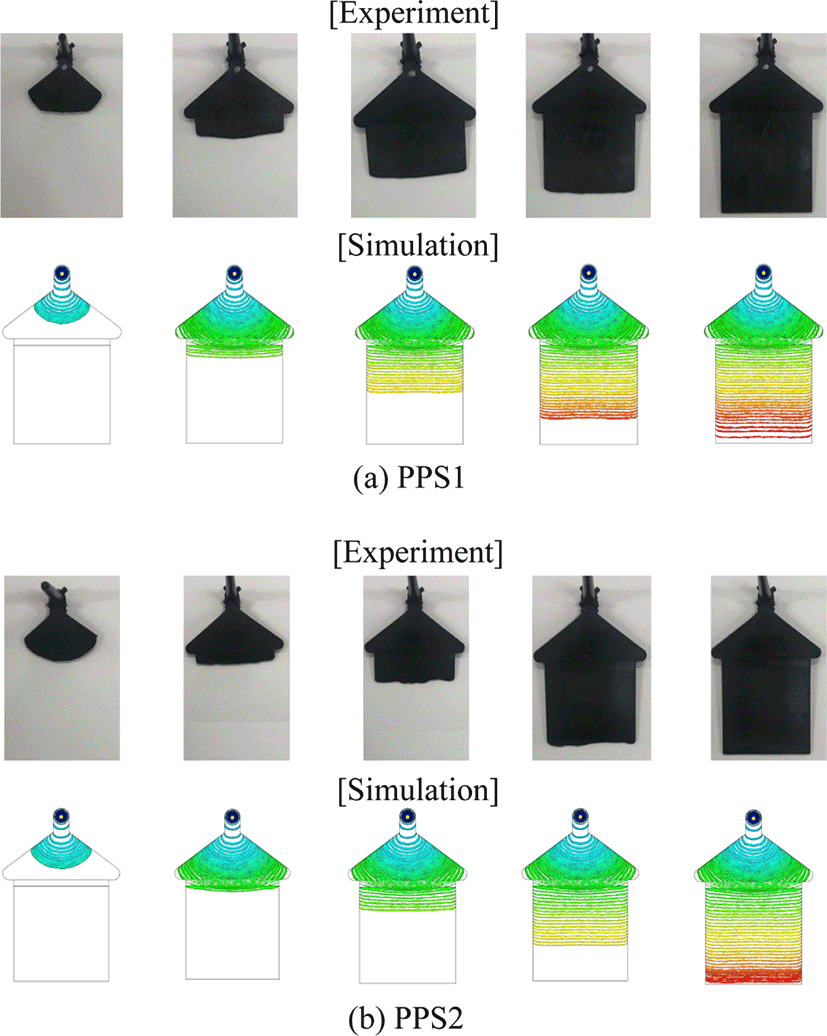
사출 온도 310°C, 쿠션량 5 mm를 고정 조건으로 유지하고, 사출 속도를 변수로 유동 선단의 온도를 해석으로 예측하였다. Figure 8과 Figure 9는 유동 선단의 온도 변화를 나타내고 있다. 사출 속도가 50, 80, 110 mm/s로 증가할수록 최대 온도가 증가하는 경향이 나타났다. 시편의 종류와는 무관하게 사출 속도 증가에 따른 PPS1의 온도 상승 폭은 평균 5.2°C PPS2의 온도 상승 폭은 평균 8.75°C를 보였다. 이러한 현상은 PPS2의 점도가 높아 전단열을 더 크게 발생시키는 것으로 판단된다. 그리고 다른 부분에 비하여 성형품 벽면의 온도가 높은 것을 확인할 수 있는데 이는 벽면에서 전단변형률 속도가 커서 온도의 상승이 크게 나타나기 때문이다.6
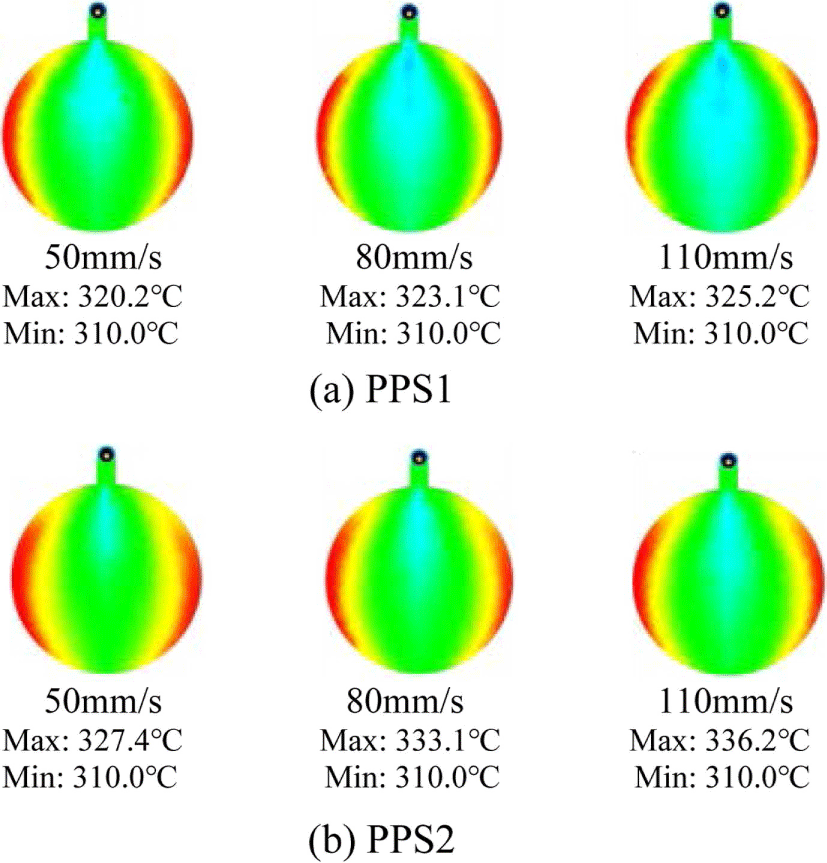
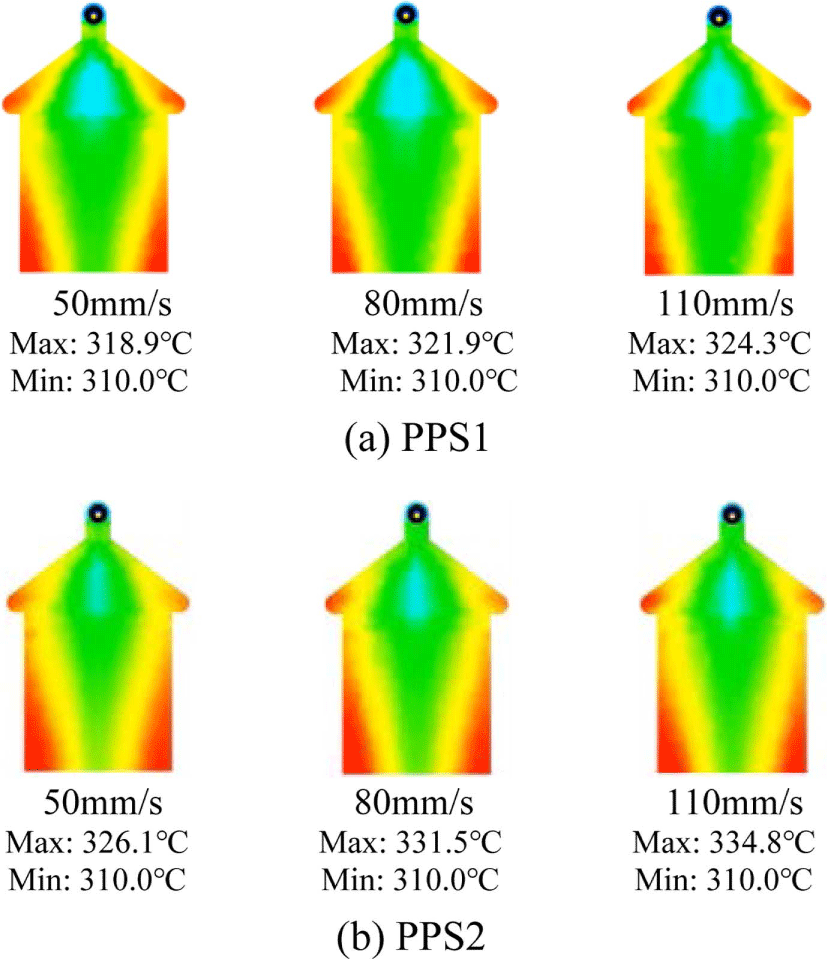
해석으로 예측한 사출품의 최종 형상, 그리고 실험으로 측정한 형상을 금형의 치수와 비교하여 수축률을 계산하였다.
PPS1과 PPS2에서 각 해석의 수축률과 실험의 수축률 그리고 해석과 실험의 차이를 Table 4에 정리하였다.
해석과 실험의 결과 모두 PPS2의 수축이 PPS1에 비해 적게 발생한 것을 확인할 수 있다. 실험과 해석에서 모두 흐름방향보다 흐름 직각 방향에서 수축률이 크게 나타났다. 특히 PPS1의 경우에 그 차이가 PPS2에 비해 더 컸다. PPS2의 경우 첨가제가 더 많이 포함되어 있어서 수축이 작았으며 또한 흐름 방향과 흐름 직각 방향의 수축차이도 작았다. 대체로 해석에서 실험의 수축률 보다 평균 0.24% 더 크게 예측하였다.
사각 시편의 경우에도 원형 시편과 같이 흐름 방향과 흐름직각방향의 수축을 측정하였다. PPS1과 PPS2 각 해석에서의 수축률과 실험에서의 수축률 그리고 해석과 실험의 차이를 아래 Table 5에 나타내었다.
해석과 실험의 결과에서 대체로 PPS2의 수축이 PPS1에 비해 적게 발생한 것을 확인할 수 있다. 이는 보강재의 높은 함량 및 사용된 Calcium Carbonate 때문으로 판단된다. 특히 중질 탄산칼슘은 엔지니어링 플라스틱의 보강재로서 강성 및 열 변형온도의 향상, 수축 방지를 향상할 목적으로 사용되고 있다.7
흐름 방향 수축이 흐름 직각 방향 수축에 비해 적게 나타났다. 흐름 직각 방향에서는 게이트 부분이 게이트에서 먼 부분보다 수축이 크게 나타났다. 해석에서 수축률은 사출품의 실제 수축률보다 평균 0.43% 더 높게 수축을 예측하였다.
보압 전환 시점인 캐비티 충전 체적의 90% 지점에서 사출압을 실험과 해석으로 비교 분석하였다.
성형 조건 변화에 따른 사출압 경향이 Figure 10에 나타나 있다. 원형 시편과 사각 시편을 사출 온도 310°C, 쿠션량 5 mm 조건에서 사출 속도를 50, 80, 110 mm/s로 변경할 때의 사출압의 변화이다. PPS2가 PPS1보다 사출압이 크게 나타났으며, 사출속도 증가에 따라 사출압도 함께 증가하는 경향을 확인할 수 있었다.
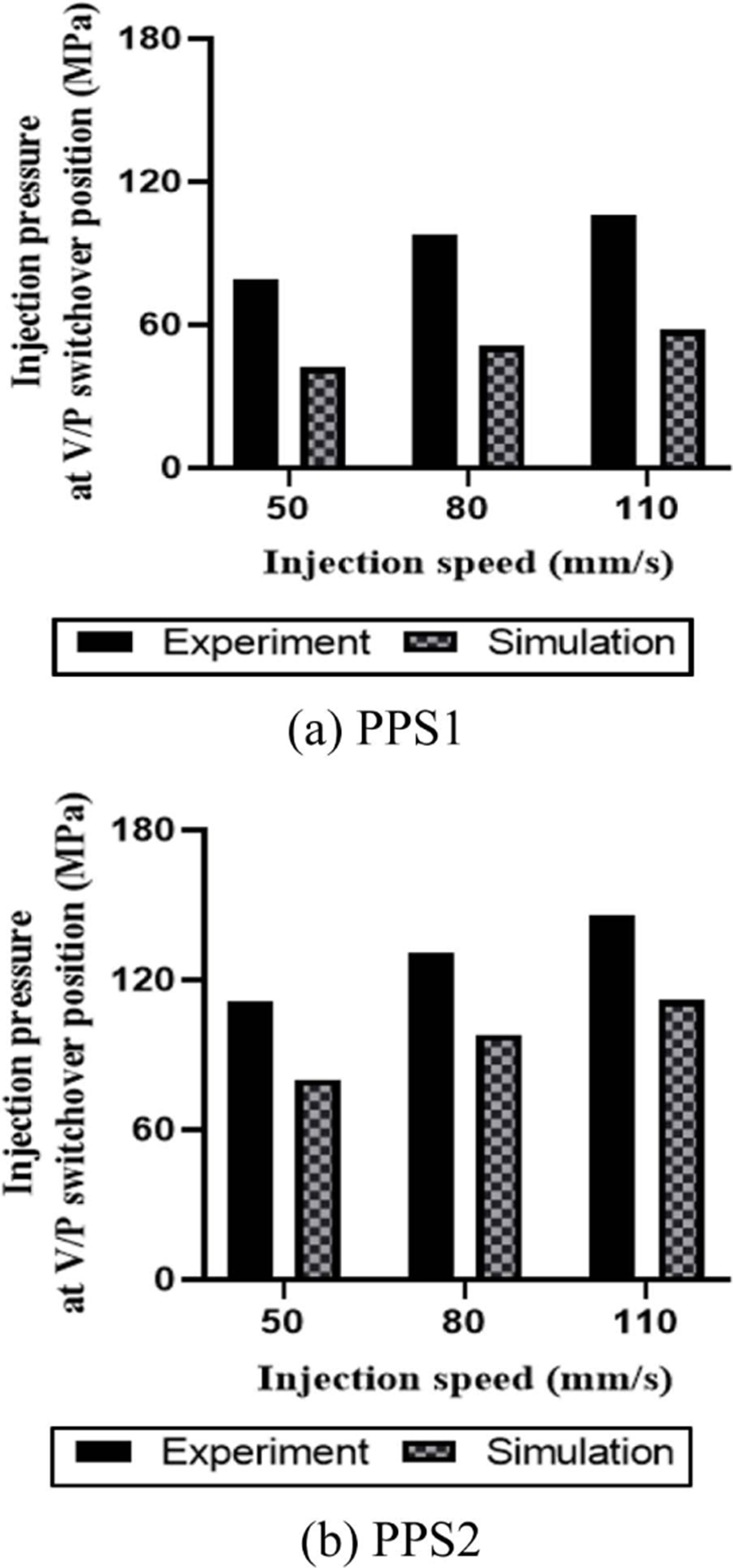
이는 PPS2가 PPS1에 비하여 점도가 크기 때문에 PPS2가 PPS1에 비하여 사출압이 크게 나타나는 것으로 판단된다. 그리고 높은 사출속도를 위해서 큰 사출 압력이 요구됨을 알 수 있다. 해석에서는 사출성형 실험 결과 보다 약 34.9% 낮게 사출압을 예측하였다.
Figure 11은 원형 시편에서 사출 속도 80 mm/s, 쿠션량 5 mm 에서 사출 온도변화에 따른 수축률을 보여주고 있다. 모든 조건에서 흐름 방향보다 흐름 직각 방향의 수축률이 높은 것으로 나타났다. Figure 12는 사각 시편의 결과이다. 흐름 직각방향에서 하단부 보다 게이트와 가까운 상단부가 수축률이 높은 것으로 나타났다. A는 게이트로부터 가까운 위치이고, B는 게이트로부터 먼 위치다. 일반적으로 게이트에서 가까운 위치는 충분한 보압을 받을 수 있으므로 수축이 적게 발생한다. 그러나 본 실험에서는 게이트에서 먼 곳이 수축이 적게 발생하였다. 본 연구에서 사용한 수지는 많은 첨가제를 포함하고 있는데 게이트 부근에서 충전 속도가 커 첨가제의 배향이 커서 나타난 현상이라 판단된다.8
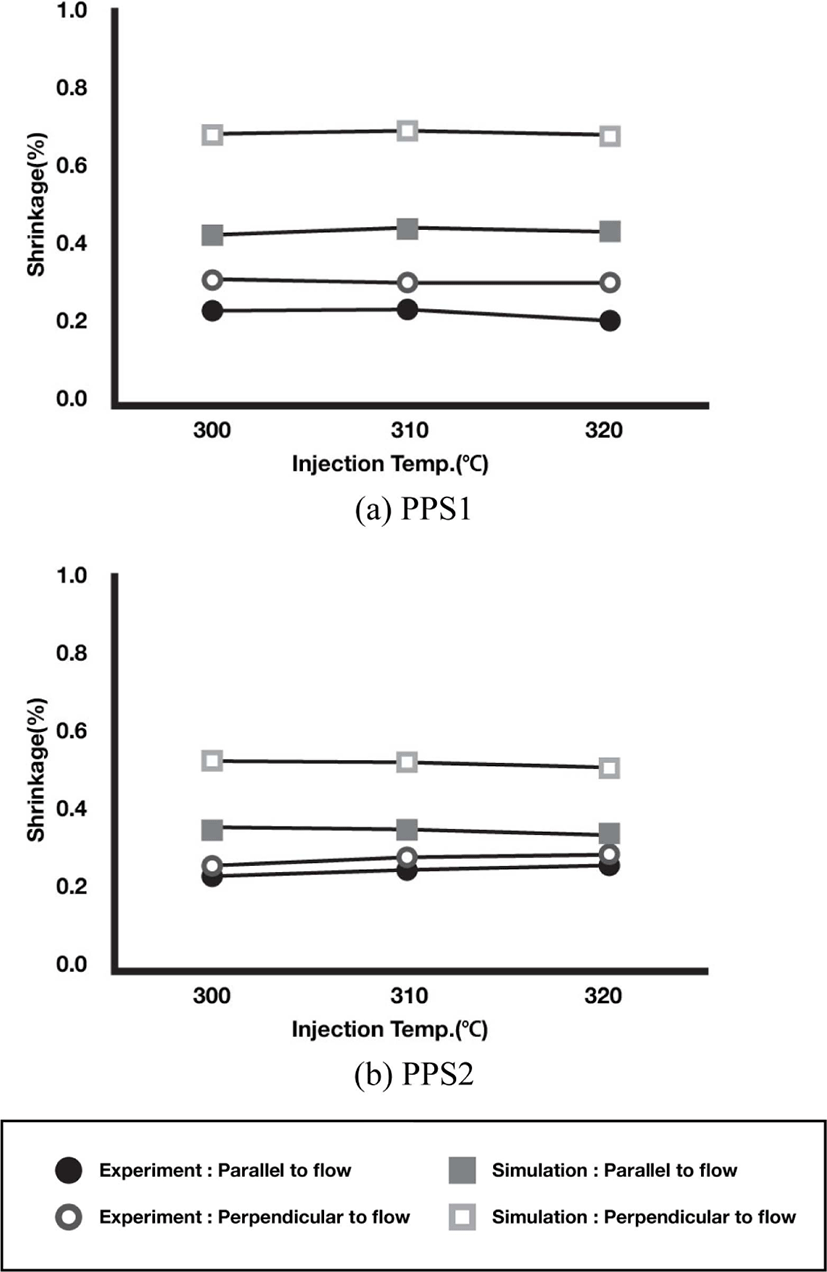
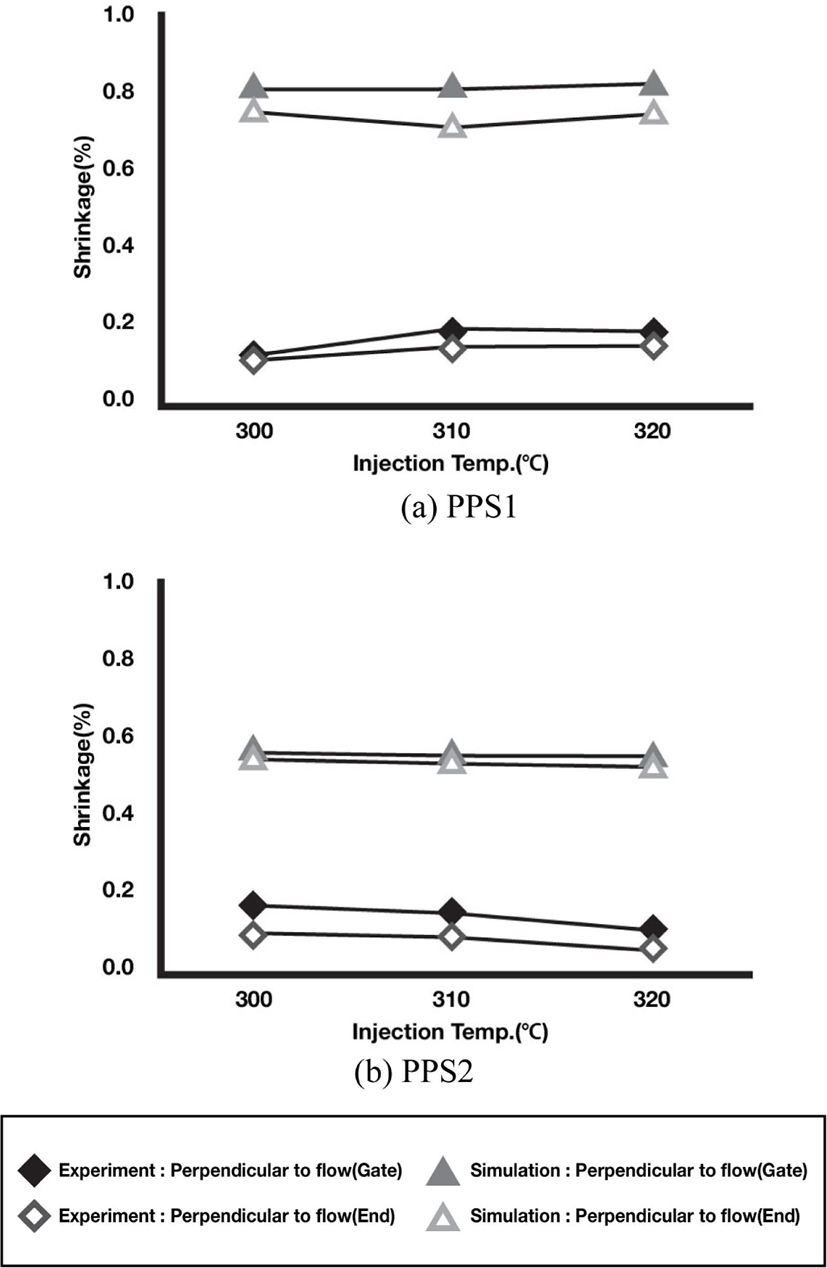
사각 시편에서 흐름 방향으로 첨가제의 배향이 잘 되어 흐름 방향과 흐름 직각 방향의 수축률이 확연히 다르게 나타났다. 온도에 따른 수축률은 큰 차이가 없었다.
Figure 13은 원형 시편을 사출 온도 310°C, 쿠션량 5 mm에서 사출속도 변화에 따른 수축률을 보여주고 있다. 모든 조건에서 흐름 방향에 비하여 흐름 직각 방향의 수축률이 높은 것으로 나타났다. Figure 14는 사각 시편을 보여준다. 흐름 직각방향에서 하단부에 비하여 상단부가 수축률이 높은 것으로 나타났다. 시편 종류에 관계없이 PPS2에서 수축률이 낮게 나타났다.
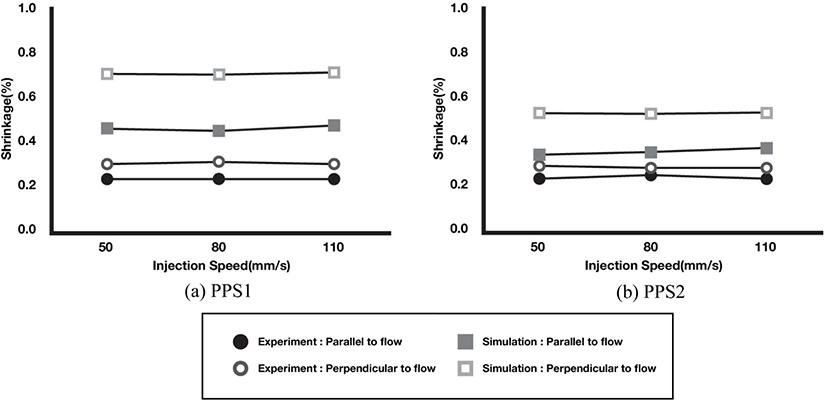
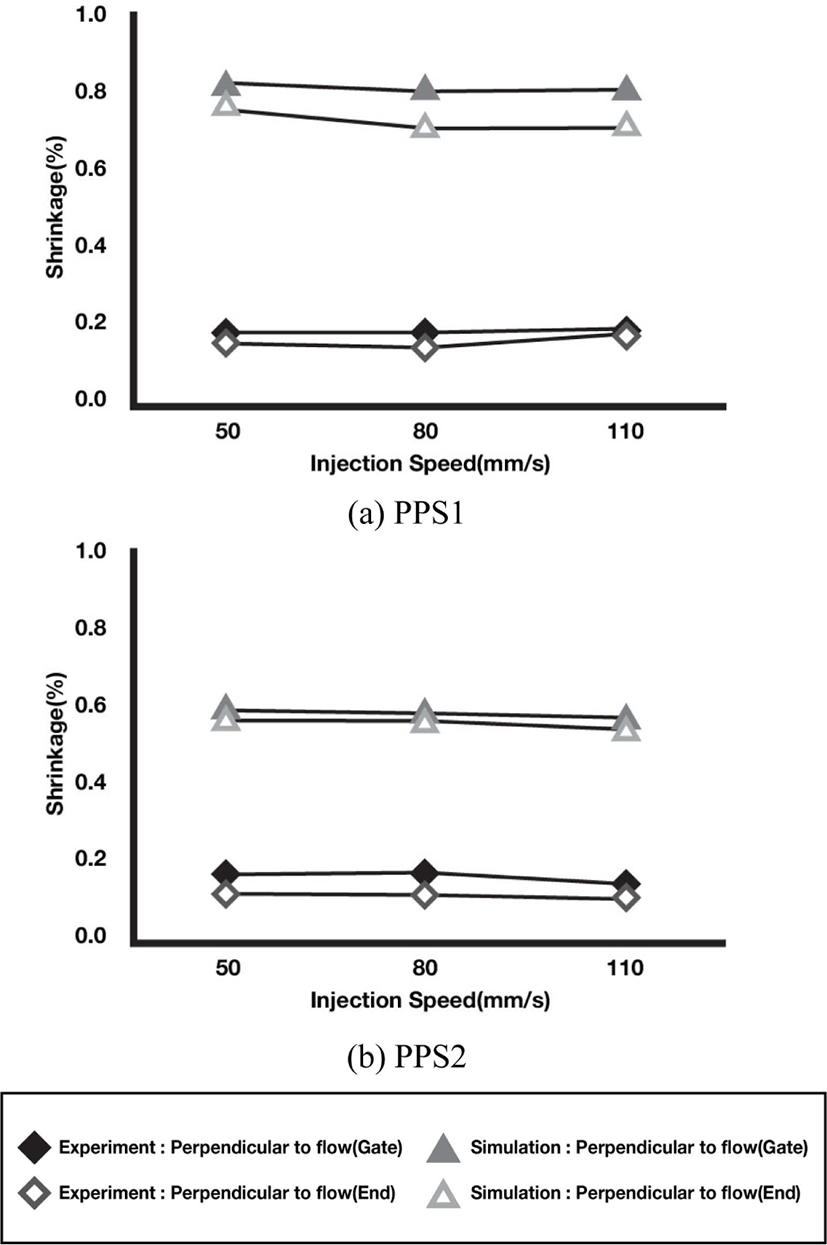
해석에서 예측한 성형 조건에 따른 수축 경향은 사출성형 실험의 결과와 부합하며 모두 흐름 직각 방향 수축이 흐름 방향의 수축보다 더 크게 나타난 것으로 확인되었다. 다만 PPS1의 해석 결과는 실제 사출 결과보다 더 높게 수축률을 예측하였다. 사출 성형 해석과 실제 사출실험을 비교한 결과 그 차이가 1% 내의 오차 범위로 신뢰 수준이 높다고 판단되었다. 따라서 정밀한 플라스틱 제품의 사출 성형 전 해석 프로그램을 이용하여 사출 성형 조건에 따른 수축률을 예상하고 적절한 조건을 검토하는 방법을 활용하는 것이 적합하다고 판단된다.
Figure 15는 원형 시편을 사출 온도 310°C, 사출속도 80 mm/s 에서 쿠션량 변화에 따른 수축률을 보여주고 있다. 모든 조건에서 흐름 방향보다 흐름 직각 방향의 수축률이 높은 것으로 나타났다. Figure 16는 사각 시편을 보여준다. 흐름 직각방향에서 하단부보다 상단부가 수축률이 높은 것으로 나타났다. Figure 15, 16에 표시된 쿠션량에 따른 수축률의 경향 차이는 크게 나타나지 않았으며 게이트에서 먼 곳의 흐름 직각 방향의 수축률이 게이트에서 가까운 위치에 비해 낮게 나타나는 경향은 온도 및 속도 변경 실험에서 동일하게 나타났다.
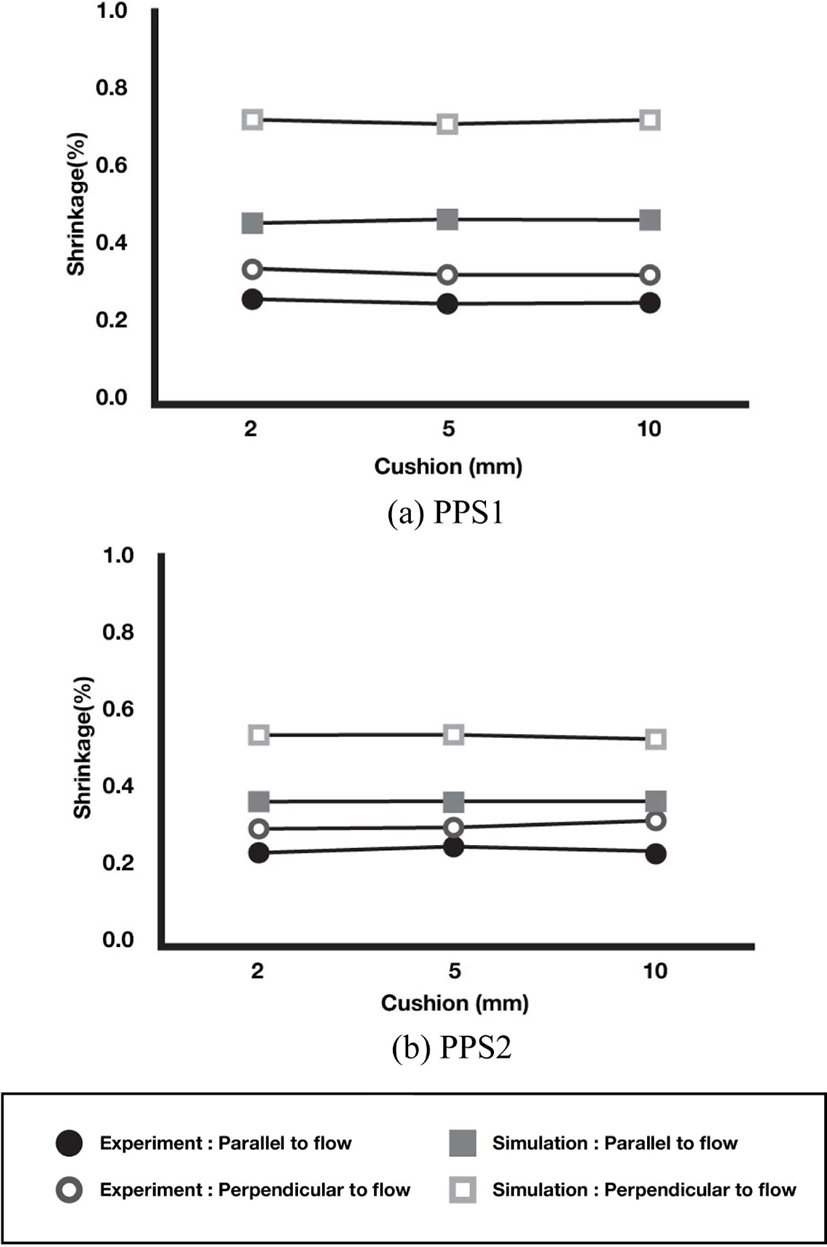
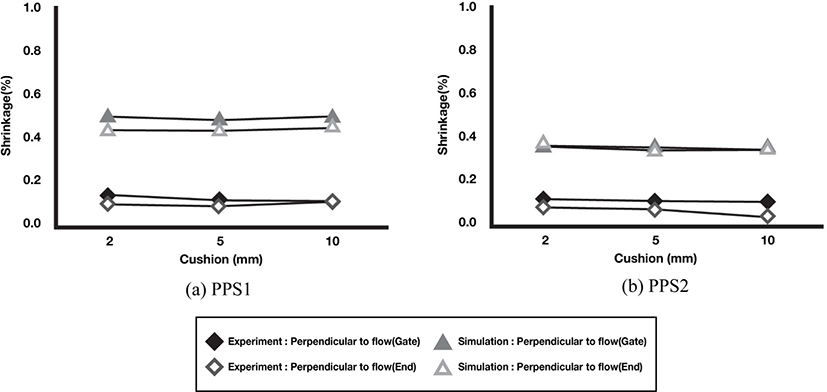
Conclusions
본 연구에서는 첨가제의 함량 및 종류가 다른 두 가지 PPS 수지에 대해 성형수축을 관찰하고 분석하였다. PPS1의 충전 패턴은 성형해석 결과와 실험 결과가 대체로 일치하였다. 그러나 첨가제의 함량이 많은 PPS2에서는 젯팅이 발생하여 충전 패턴은 성형해석 결과와 실험 결과에서 큰 차이를 보였다. 두 수지의 수축률은 원형 시편과 사각 시편에서 모두 흐름 직각 방향이 흐름 방향보다 높게 나타났다. 흐름 직각 방향 수축의 경우 사각 시편에서 게이트에 가까운 부분이 게이트에서 먼 부분보다 수축률이 높게 나타났다. 그리고 PPS2 수지는 PPS1에 비하여 수축률이 낮아 높은 치수 안정성을 보였다. 성형수축의 해석 결과와 실험 결과의 차이가 1% 미만으로 신뢰 수준이 높았다.