Introduction
산업이 발전함에 따라 고무제품의 작동 환경 또한 점점 가혹화되고 있는 실정이다. 이러한 가혹 조건을 견디기 위해 고무의 물리적, 화학적 물성 보강이 필요하다. 그 대표적인 예가 보강제의 첨가와 가교시스템의 변경이다. 대표적 가교시스템에는 황(sulfur) 가교 시스템, 과산화물(peroxide) 가교 시스템 및 황/과산화물 복합 가교시스템이 있으며, 제품의 용도, 사용되는 고무의 종류 및 가교 후 요구되는 기계적 물성에 따라 적용하는 가교시스템이 결정된다. 이 중 과산화물 가교시스템은 포화고무, 불포화고무, 불소고무 및 실리콘고무를 포함한 대부분의 고무를 가교시킬 수 있으며, 고무 체인(chain)간 탄소-탄소 공유결합으로 고무의 탄성을 발현시키는 3차원 망상구조를 형성시킨다. 탄소-탄소 결합 에너지(343.2 kJ/mol)는 황 가교시스템으로 형성되는 탄소-황 결합에너지(276.2 kJ/mol) 및 황-황 결합에너지(205.1 kJ/mol)에 비해 높은 결합에너지를 가지기 때문에 황 가교시스템에 비해 열 안정성 및 열 산화 안정성이 필요한 고무복합소재에 과산화물 가교시스템이 사용된다. 하지만 과산화물 가교시스템은 황 가교시스템에 비해 가교효율이 낮고 가교시간이 많이 걸리는 단점들을 가지고 있다.1-5
과산화물 가교시스템은 과산화물의 열 분해로 생성된 라디칼(radical)에 의해 고무복합소재의 가교가 개시된다. 하지만 생성된 라디칼은 재배열 반응(rearrangement reaction)에 의해 일부 새로운 라디칼로 변환되고, 변환된 라디칼은 과산화물 분해에 의해 생성된 라디칼에 비해 낮은 반응성을 가져서 과산화물 가교효율을 저하시키는 것으로 알려져 있다. 또한 생성된 라디칼이 다른 고분자와 결합하여 가교되는 효과적 가교결합 이외에 고분자 사슬을 절단하거나 분해하는 비효과적 가교반응의 발생으로 고무복합소재의 가교효율을 저하시키는 것으로 알려져 있다.6,7
공가교제(co-agent)는 과산화물 가교시스템에서 수소추출(hydrogen abstraction)반응에 의해 라디칼을 형성시켜 가교 반응 동안 발생하는 망상을 형성하지 않는 부 반응(non-network forming side reaction)을 막거나 고분자 체인에 접목(graft)되어 추가 가교를 형성시켜 과산화물 가교 효율을 향상시킨다. 과산화물 가교에서 가교 효율 향상을 위해 상용화된 많은 물질이 공가교제로 사용되고 있으며, 형성되는 가교구조는 공가교제의 화학적 미세 구조와 라디칼 반응성에 따라 달라진다. 공가교제는 과산화물 가교시스템의 가교속도와 가교밀도를 동시에 향상시킬 수 있는 type I 공가교제와 가교밀도에만 영향을 미치는 type II 공가교제로 분류된다. Type I 공가교제는 일반적으로 극성을 가지는 저 분자물질로 부가반응을 통하여 반응성 높은 라디칼을 형성하는 화합물이다. 다 관능성 아크릴레이트(multi-functional acrylate), 메타크릴레이트 에스테르(methacrylate esters) 및 디말레이미드(dimaleimides)가 type I 공가교제에 속한다. Type II 공가교제는 type I 공가교제에 비해 상대적으로 낮은 반응성을 가지는 라디칼을 형성시킨다. 낮은 극성을 가져 대부분의 고무와 상용성을 가지며, 시아누레이트(cyanurates), 이소시아누레이트(isocyanurates), 1,2-폴리부타디엔(1,2-polybutadiene)이 type II 공가교제에 속한다.7-10
수소첨가 아크릴로니트릴-부타디엔고무(HNBR)는 아크릴로니트릴-부타디엔고무(NBR)의 부타디엔 세그먼트(segment)에 존재하는 이중결합부를 수소첨가 반응을 통하여 포화시킨 고무로 NBR보다 높은 내열성 및 내오존성이 요구되는 환경에 사용된다. 하지만 수소첨가 반응으로 부타디엔에 존재하는 반응성이 높은 알릴기 함량이 줄어 가교효율이 떨어지게 된다.
본 연구에서는 과산화물 가교시스템이 적용된 HNBR 복합소재에 공가교제를 첨가시켜 공가교제의 미세화학구조와 함량이 HNBR 복합소재의 가교특성 및 기계적 물성에 미치는 영향을 연구하였다. 공가교제로는 trimethylolpropane trimeth- acrylate (TMPTMA)와 high vinyl 1,2-polybutadiene (HVPBD)를 사용하고 함량은 5 phr씩 증량하여 20 phr까지 첨가하였다. HNBR 복합소재의 가교특성은 ODR (Oscillating Disk Rheometer)를 이용하여 스코치시간(TS1), 가교속도를 나타내는 CRI (curing rate index) 및 화학적 가교밀도를 나타내는 ΔM (MH-ML)을 측정하였다. 기계적물성은 Shore A 경도, 10% 모듈러스 및 파단신율을 확인하였다. 또한 HNBR 복합소재의 내열성을 확인하기 위하여 135℃에서 70 시간 내열노화 후의 기계적 물성 변화를 측정하였다.
Experimental
실험에 사용한 HNBR은 Lanxess사의 acrylonitrile (ACN) 함량 21%인 LT 2157을 사용하였다. LT2157은 잔류 이중결합 함량이 5.5%인 HNBR로 저온특성 향상을 위해 에스테르-카르보닐기(ester-carbonyl group)가 도입된 등급이다. 충전제는 OCI사의 카본블랙(FEF, particle size: 39~55 nm)를 사용하였다. 가공조제는 스테아르산(stearic acid)를 사용하였으며, 가교제는 NOF corporation사의 dialkyl peroxide type의 DCP (dicumyl peroxide, 98%)를 사용하였다. SARTOMER사의 trimethylolpropane trimethacrylate (TMPTMA)인 SR-350과 CRAY VALLEY사의 high vinyl 1,2-polybutadiene (HVPBD)인 Ricon 153D를 각각 공가교제로 사용하였다. 사용된 공가교제들의 화학구조는 Figure 1에 나타내었다.
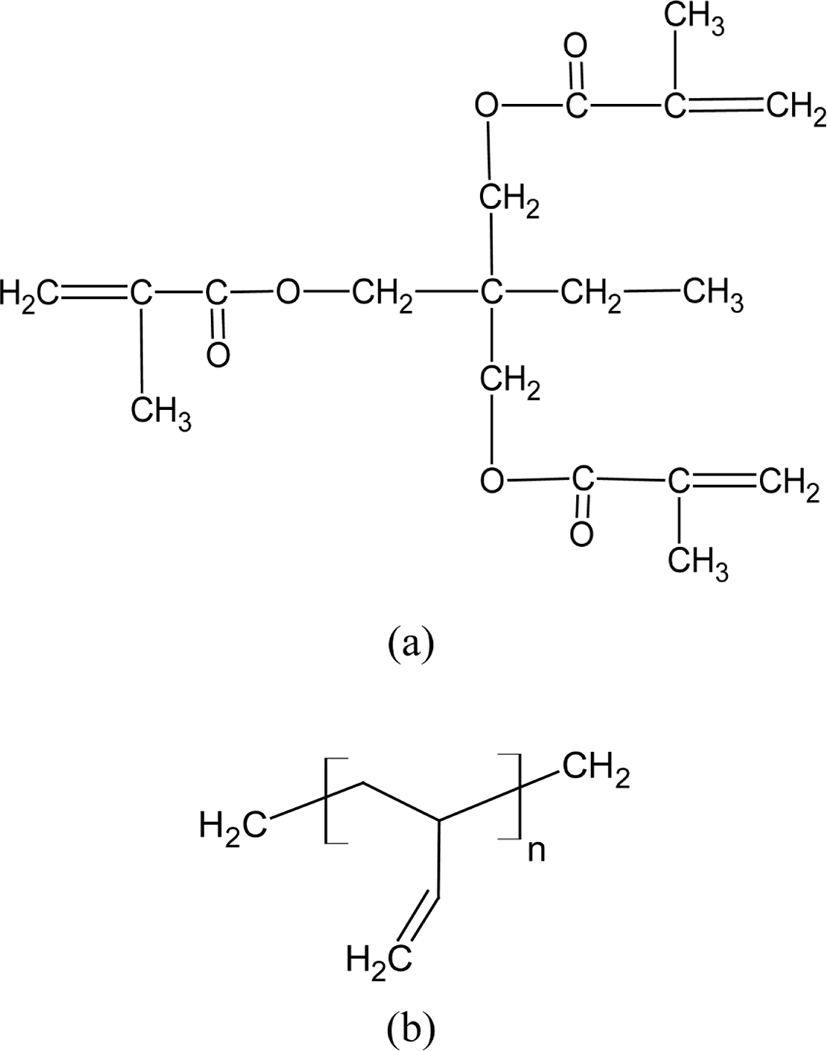
HNBR 복합소재의 제조는 Mirae Rubber & Plastic Machinery사의 3 ℓ kneader를 사용하여 HNBR 고분자를 2분간 혼합(mixing)하고 카본블랙 충전제를 투입하여 3분간 혼합하였다. 그 후 가공조제 및 공가교제를 투입하여 3분간 혼합하여 CMB (carbon master batch) 상태의 HNBR 복합소재를 제조하였다. 배합 시 충전율(fill factor) 및 로터 속도(rotor speed)는 0.7 및 30 rpm으로 모두 동일하게 적용하여, 배합조건에 따른 영향을 최소화하였다. FMB (final master batch) 상태의 HNBR 복합소재는 CMB 상태의 HNBR 복합소재에 과산화물 가교제를 첨가하고 봉신사의 8 inch open mill (속도비 1.2:1.0)로 6분간 분산시켜 제조하였다. HNBR 복합소재에 대한 공가교제의 영향을 검토하기 위해 공가교제의 종류 및 함량 별로 배합조성을 설정하였다. HNBR 복합소재의 명칭은 공가교제를 함유하지 않은 HNBR 복합소재는 HNBR/co-agent 0로 명명하고 HNBR 복합소재에 첨가된 공가교제의 종류 및 함량에 따라 명명하였다. 공가교제의 첨가는 5 phr (parts per hundred rubber)씩 증량시켜 20 phr 함량까지 첨가하였다. Table 1에 배합조성을 나타내었다.
Ingredients | HNBR/co-agent 0 | HNBR/TMPTMA 5~20 | HNBR/HVPBD 5~20 |
---|---|---|---|
LT 2157 | 100 | 100 | 100 |
Carbon black (FEF) | 20 | 20 | 20 |
Stearic acid | 1 | 1 | 1 |
TMPTMA | 0 | 5~20 | 0 |
HVPBD | 0 | 0 | 5~20 |
DCP | 3 | 3 | 3 |
기계적 물성 측정을 위한 HNBR 복합소재의 가교 시험편은 80 ton 유압프레스를 사용하여 170℃에서 ODR (Kunhaw engineering, Model; KHR-200) 측정을 통하여 얻어진 적정 가황시간(TC90)으로 2 mm 두께의 가교 시트를 제작하였다.
공가교제의 종류와 함량에 따른 HNBR 복합소재의 가교특성 변화는 ODR을 이용하여 170℃에서 최대 토크(MH), 최저토크(ML), ΔM (MH-ML), 스코치시간(TS1) 및 적정가황시간(TC90)을 측정하고 가교속도를 나타내는 CRI을 아래의 식 (1)에 따라 계산하였다.
ODR 측정은 ASTM D 2084에 따라 측정하였으며, 측정시간은 6분으로 측정하였다. ΔM은 화학적 가교밀도를 나타내는 척도이며, ΔM 값이 높을수록 가교밀도가 높음을 의미한다.
Thermo Fisher Scientific사의 Nicolet 5700 FTIR (Fourier transform infrared) 기기를 사용하여 HNBR 복합소재의 가교 반응 전, 후의 스펙트럼 변화를 ATR-FTIR (Attenuated total reflection-Fourier transform infrared) spectroscopy법으로 측정하였다. Germanium (Ge) 결정을 사용하여 4,000 cm−1~400 cm−1 범위의 파수(wave number)에서 32회 측정하여 스펙트럼을 측정하였다.
HNBR 복합소재의 경도 측정은 Shore A 경도 측정 방법인 ASTM D676에 따라 진행하였으며, 각 시편당 5개를 측정하여 산술 평균값을 나타내었다. 10% 신장되었을 때의 응력을 나타내는 10% 모듈러스(modulus) 및 파단신율은 UTM (Universal testing machine, Kunhaw engineering)을 이용하여 cross head speed 500 mm/min으로 ASTM D412에 따라 측정하고, 배합물 당 3개의 시편을 사용하여 산술 평균값을 구하였다. 또한, 가교고무의 내열노화 전 후의 물성변화를 측정하기 위해 공기순환식 오븐에 시편을 135℃에서 70시간 노화시킨 후, 시편의 Shore A 경도, 10% 모듈러스 및 파단신율을 측정하였다. 10% 모듈러스 및 파단신율은 ASTM D 412 Die C형 시편을 제작하여 측정하였다.
HNBR 복합소재의 압축영구줄음율을 측정하기 위해 원통형 시편(지름: 29.0±0.5 mm, 두께: 12.5±0.5 mm)을 제조하였다. 시험은 ASTM D 395 시험방법 B에 따라 시편을 25% 압축시키고, 공기순환식 오븐을 사용하여 135℃에서 70시간 노화 시켰다. 노화 종료 후에 시편을 압축영구줄음 장치로부터 분리시키고 상온에서 30분간 방치 후 시편의 두께를 측정하였다. 압축영구줄음율은 아래의 식 (2)에 따라 계산하였다.
여기서 t0 는 시험편의 시험 전 두께(mm), t1은 시험 후의 시편의 두께, t2는 spacer의 두께이다. 3개 시편의 측정결과의 산술 평균값으로 결과를 나타내었다.
Results and Discussion
공가교제의 종류와 함량에 따른 HNBR 복합소재의 가교특성 변화 그래프를 Figure 2에 나타내었다. Figure 2의 왼편에는 0~720 second 사이의 Rheo-curve를 나타내고, 오른편에는 초기에 나타나는 torque 변화 관찰을 용이하게 하기 위하여 0~100 second 부분을 확대하여 나타내었다. Figure 2(a) 그래프는 TMPTMA가 첨가된 HNBR 복합소재의 가교특성 변화그래프를 보여준다. HNBR/TMPTMA 5의 경우 HNBR/co-agent 0 복합소재에 비하여 스코치시간(TS1)이 22초 감소하는 결과를 나타내었으며, TMPTMA 함량 증가에 따른 추가적 TS1 단축현상은 나타나지 않았다. 하지만 TS1 이후 급격한 토크(torque)증가는 TMPTMA 함량이 증가 할수록 높아지는 결과를 나타내었다. MH는 HNBR/co-agent 0이 4.09 Nm를 나타내었으며, HNBR/TMPTMA 20은 6.57 Nm를 나타내었다. ΔM (cross-link density) 또한 MH 증가로 인하여 2.95에서 5.67로 증가하였다. 이러한 현상은 공가교제인 TMPTMA가 가교반응에 관여하여 나타난 결과로 라디칼의 반응성 및 접목반응으로 설명될 수 있다. 과산화물에 의한 HNBR 가교반응은 열에 의해 생성된 과산화물의 라디칼이 HNBR 고분자 체인의 수소를 추출시켜 라디칼을 형성시키고, 형성된 HNBR 고분자 체인의 라디칼 상호 간의 반응으로 가교가 이루어지게 된다. 가교반응 속도에 영향을 미치는 수소추출 반응은 고분자를 구성하는 미세구조의 C-H 결합에너지와 함량에 따라 달라지며, C-H 결합에너지가 작고 함량이 높을 수록 수소 추출반응이 빨리 일어나게 된다. TMPTMA 분자는 말단에 알릴기(allylic group)를 가지고 있으며, 말단의 이중결합부는 고분자 내에 존재하는 이중결합부보다 반응 시 입체장애를 적게 받기 때문에 더 빠르게 반응 하는 것으로 알려져 있다.11 즉 HNBR 가교반응 시 HNBR 고분자 내의 알릴기보다 첨가된 TMPTMA 말단의 알릴기에서 수소추출 반응이 우선적으로 일어나게 된다. 또한, TMPTMA 말단에 형성된 라디칼과 HNBR 체인에 형성된 라디칼이 반응하면 접목 반응을 일으켜 가교밀도(cross-link density)를 증가시킨다. 따라서 TMPTMA의 첨가에 따른 TS1의 감소 및 ΔM의 증가는 말단에 위치한 알릴기 함량이 증대되어 나타난 결과로 추측 할 수 있다. Figure 3에 분자 구조에 따른 C-H 결합에너지와 수소 안정화 순서를 나타내었다.6
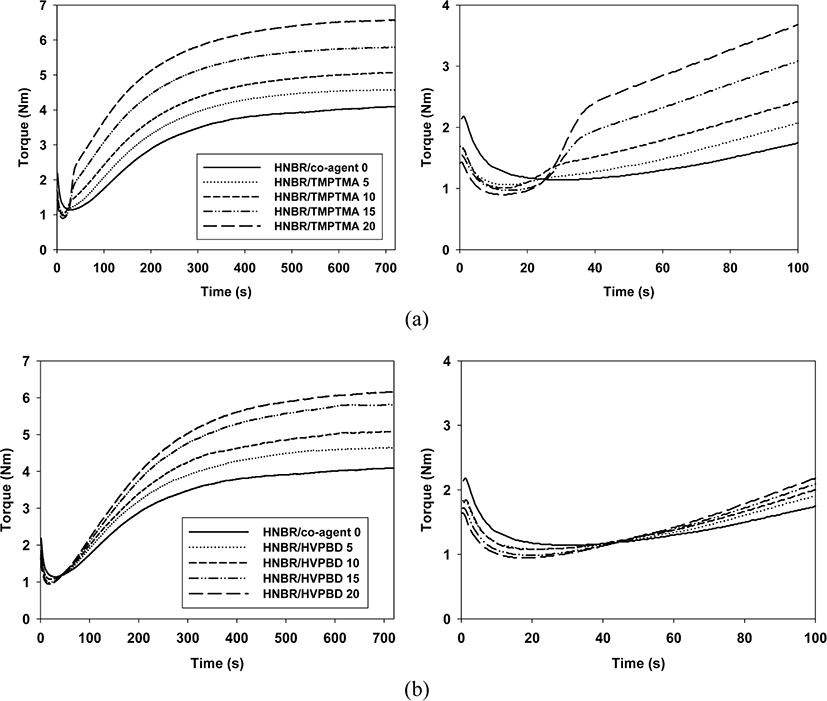

Figure 2(b)에 HVPBD의 함량에 따른 HNBR 복합소재의 가교특성변화를 나타내었다. HNBR/HVPBD 5의 TS1는 33초를 나타내어 HNBR/co-agent 0 복합소재에 비해 TS1이 9초 감소하는 결과를 나타내었다. 이는 HNBR/TMPTMA 5의 TS1과 비교하였을 시 13초 느린 결과로 HVPBD의 측쇄(side chain)에 위치한 비닐기(vinyl group)에 의한 라디칼 형성보다 TMPTMA 말단에 위치한 알릴기에 의한 라디칼 형성이 우선적으로 발생되어 나타난 현상으로 판단된다. 비닐기의 C-H 결합에너지는 464 kJ/mol이며, 알릴기의 결합에너지는 368 kJ/mol이다. 따라서 TMPTMA가 HVPBD에 비하여 과산화물 가교시스템에서 가교반응을 더 빠르게 개시시킴을 알 수 있다. MH의 경우 TMPTMA가 첨가된 HNBR 복합소재와 다르게 TS1 이후 급격한 토크 상승 구간은 나타나지 않았으나, HVPBD 함량이 증가함에 따라 지속적으로 증가하는 경향을 나타내어, HNBR/HVPBD 20의 경우 6.15 Nm을 나타내었다. ΔM 또한 MH 증가로 인하여 2.95에서 5.67로 증가하였다. 가교속도를 나타내는 CRI의 경우 HVPBD 함량 증가에 따른 HNBR/HVPBD 복합소재의 CRI 값 변화는 나타나지 않았다. 하지만 HNBR/TMPTMA 복합소재의 경우 TMPTMA 함량 10 phr 이후부터 증가하는 결과를 나타내었다. Table 2에 가교 특성 결과 값을 정리하여 나타내었다.
공가교제 첨가에 따른 HNBR 복합소재의 가교반응으로 발생되는 화학적 변화를 관찰하기 위하여 FTIR-ATR 스펙트럼을 측정하고 측정 결과를 Figure 4에 나타내었다. Figure 4(a)는 HNBR/co-agent 0 복합소재의 가교 전과 가교 후의 FTIR-ATR 스펙트럼을 보여준다. 가교 전의 스펙트럼을 보면 2919, 2851, 2235, 1727, 1461, 1169, 965 및 725 cm−1 에서 피크(peak)들이 나타났다. 2919 및 2851 cm−1피크는 -CH2의 비대칭 연신(asymmetric stretching) 변형에 기인하고 1461 cm−1는 –CH2의 굽힘(bending) 변형에 기인한다. 725 cm−1는 -CH2의 긴 체인의 좌우흔듬진동(rocking) 변형에 기인한다. 2235 cm−1는 -C≡N 삼중 결합의 연신 변형에서 기인한다. 또한 965 cm−1은 trans -CH=CH의 앞뒤흔듬진동(wagging) 변형에 기인한다. 본 실험에 사용된 HNBR 고분자의 경우 저온 특성 향상을 위해 에스테르-카르보닐기가 도입된 등급이다. 1727 및 1169 cm−1의 경우 각 -C=O 및 -C-O의 연신 변형에서 기인한다. HNBR/co-agent 0의 경우 가교 전 후에 측정한 스펙트럼에서 피크 변화는 거의 나타나지 않았다. Figure 4(b)는 HNBR/TMPTMA 20 복합소재의 가교 전 후 FTIR-ATR 스펙트럼 변화를 보여 준다. HNBR/TMPTMA 20의 경우 1637 및 812 cm−1의 피크를 가교 후 관찰 할 수 없었다. 1637 cm−1의 피크는 TMPTMA의 C=C 연신 변형에 기인한 것이며, 812 cm−1은 말단 =CH2에서 기인한다.1 따라서 TMPTMA 말단의 =CH2가 과산화물에 의한 가교 반응에 관여하여 변환되었다고 판단된다. Figure 4(c)는 HNBR/HVPBD 20의 가교 전 후의 스펙트럼 변화를 보여주며, HNBR/co-agent 0과 같이 FTIR-ATR 측정에서 가교에 따른 변화를 관찰하기는 어려웠다.
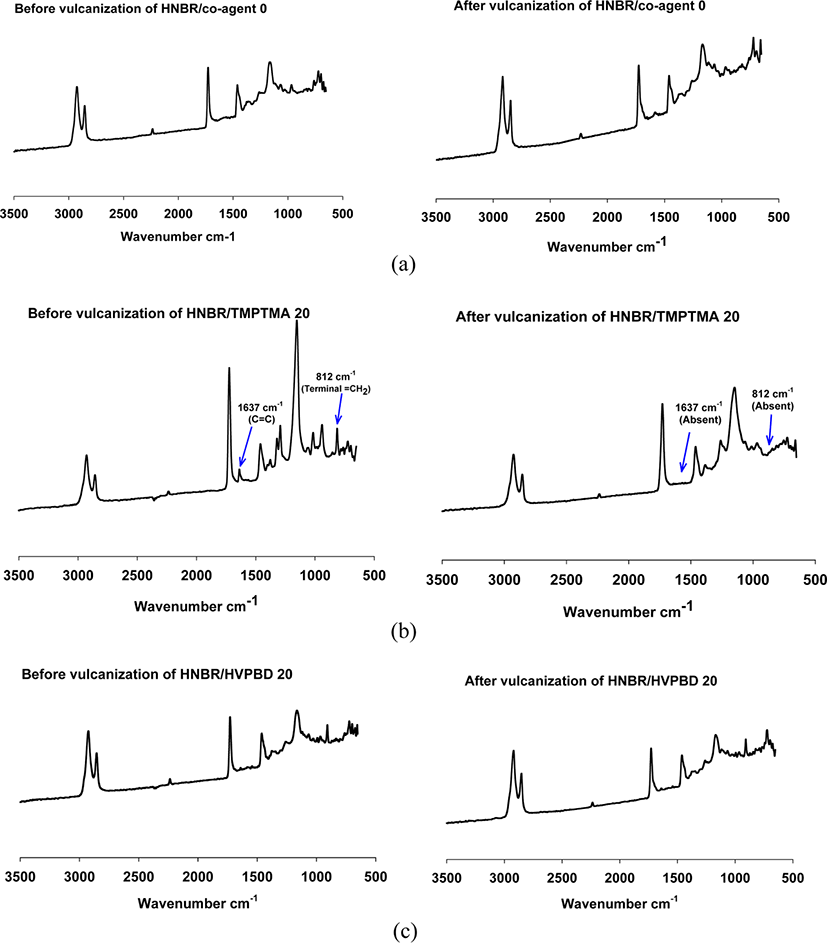
공가교제의 종류와 함량에 따른 HNBR 복합소재의 기계적물성 및 내열성변화를 확인하기 위하여 내열 노화 전, 후의 Shore A 경도, 10% 모듈러스 및 파단신율을 측정하고 Figure 5에 나타내었다. Shore A 경도 및 10% 모듈러스의 경우 공가교제 함량이 증가 할수록 선형적으로 상승하는 결과를 나타내었으며, 공가교제의 종류에 따라서는 증가하는 정도에 차이를 나타내었다. HNBR/TMPTM 복합소재는 TMPTMA 함량이 5 phr 증가 할수록 Shore A 경도는 약 9 point씩 상승하였으며, HNBR/TMPTMA 20의 10% 모듈러스는 0.52 MPa에서 약 10.4배 증가 하여 5.43 MPa를 나타내었다. HNBR/HVPBD 복합소재는 HVPBD 함량이 5 phr 증가 할수록 Shore A 경도는 약 4 point씩 상승하였으며, 10% 모듈러스의 경우 HNBR/HVPBD 20이 1.82 MPa를 나타내어 HNBR/co-agent 0 복합소재에 비하여 3.5배 증가 하는 결과를 나타내었다. HNBR/TMPTMA 복합소재의 파단신율은 공가교제가 첨가되지 않은 HNBR/co-agent 0 복합소재의 파단신율은 435%를 나타내었으며, 공가교제 함량이 증가함에 따라 지속적으로 감소하여 HNBR/TMPTMA 20이 66%, HNBR/HVPBD 20이 276%를 각각 나타내었다. 이러한 현상은 공가교제가 과산화물에 의해 형성된 라디칼의 효율을 향상시키고 고분자 체인 간 가교 다리(cross-link bridge)를 형성시켜 나타나는 현상으로, TMPTMA가 HVPBD보다 가교효율 향상과 기계적물성에 영향을 미치는 유효한 가교밀도 향상에 더 큰 기여를 하기 때문에 나타나는 현상으로 판단된다. 즉 TMPTMA가 HVPBD에 비해 HNBR에서 동일한 가류제 함량에서 더 많은 가교 다리를 형성시킴을 추정할 수 있다. 고무복합소재의 경우 가교밀도가 증가 할수록 경도 및 모듈러스는 증가하고 신율은 감소하는 것으로 알려져 있다.
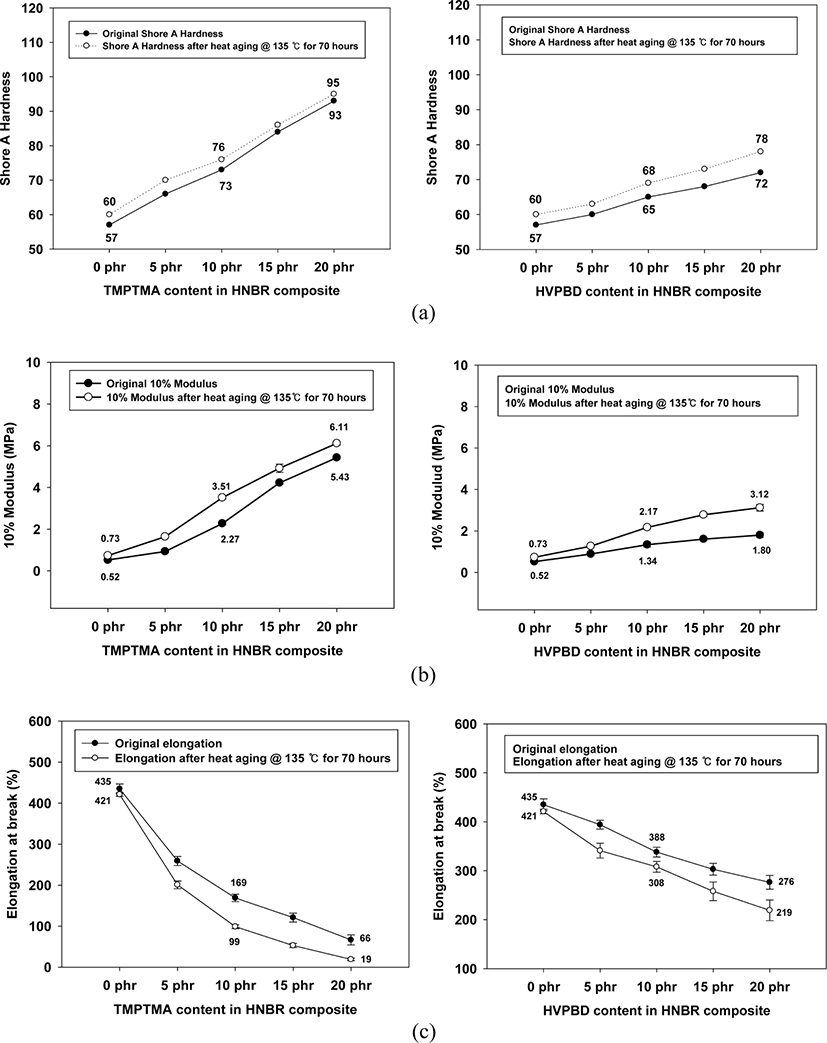
내열 노화 전, 후의 Shore A 경도 및 10% 모듈러스 값을 비교하여보면 HVPBD의 함량이 증가함에 따라 HNBR/HVPBD 복합소재의 Shore A 경도 및 10% 모듈러스 증가폭이 HNBR/TMPTMA 복합소재에 비하여 높게 나타났다. HNBR/TMPTMA 20의 Shore A 경도는 노화 전에 비하여 2 point가 상승하였으며, 10% 모듈러스는 12% 상승하였다. 반면에 HNBR/HVPBD 20은 경도가 6 point 증가하고 10% 모듈러스가 73% 증가하는 결과를 나타내었다. 이러한 증가의 주요원인은 과량 첨가로 인하여 잔류된 공가교제의 불포화 관능기(unsaturated functional group)가 열에 의해 산화되면서 추가적 가교점을 형성시켜 나타난 현상으로 사료되며, 증가의 차이는 잔류된 공가교제의 불포화 관능기의 함량차이에 기인한 것으로 판단된다. HVPBD의 경우 TMPTMA 보다 라디칼 반응성이 낮은 비닐기가 다량 함유되어있는 반면 TMPTMA의 경우 라디칼 반응성이 높은 알릴기를 1 분자 당 3개 함유하고 있다. 고무복합소재는 일반적으로 내열노화 시 고무복합소재에 잔류된 가교제 및 열 산화반응에 의해 추가적 가교 다리를 형성시켜 가교밀도가 증가하게 된다.
공가교제의 종류와 함량에 따른 HNBR 복합소재의 압축영구줄음율 변화를 Figure 6에 나타내었다. 압축영구줄음율은 복합소재의 가교밀도의 영향을 받는 것으로 알려져 있다. HNBR 복합소재의 가교특성 및 기계적물성 측정 결과 TMPTMA 및 HVPBD 함량이 증가함에 따라 가교밀도가 증가함을 추정 할 수 있다. 하지만 압축영구줄음율 측정 결과 HNBR/HVPBD 복합소재의 경우 가교밀도 증가와 다른 경향을 나타내었다. HNBR/TMPTMA 복합소재의 경우 TMPTMA 함량이 증가함에 따라 압축영구줄음율이 지속적으로 감소하여 HNBR/TMPTMA 20이 HNBR/co-agent 0 복합소재에 비하여 7.5% 감소하는 결과를 나타내었다. 반면에 HNBR/HVPBD 복합소재의 경우 HVPBD 함량 5 phr 이후부터 압축영구줄음율이 증가하였으며, HNBR/HVPBD 20의 경우 HNBR/co-agent 0 복합소재 대비 2.7% 증가하는 결과를 보였다. 이러한 증가 현상은 압축변형 상태에서 형성된 새로운 가교 다리가 기존에 형성된 가교 다리에 의한 복원을 저해하여 나타난 현상으로 판단된다. 새로운 가교 다리의 형성은 내열노화 후의 기계적물성 변화에서 나타낸 바와 같이 과량으로 첨가된 공가교제의 불포화 기에 기인한 것으로 추정 할 수 있다. 따라서 내열노화에 의해 형성된 추가적 가교다리는 HNBR 복합소재의 내열성과 압축영구줄음율을 저하시킴을 알 수 있다.
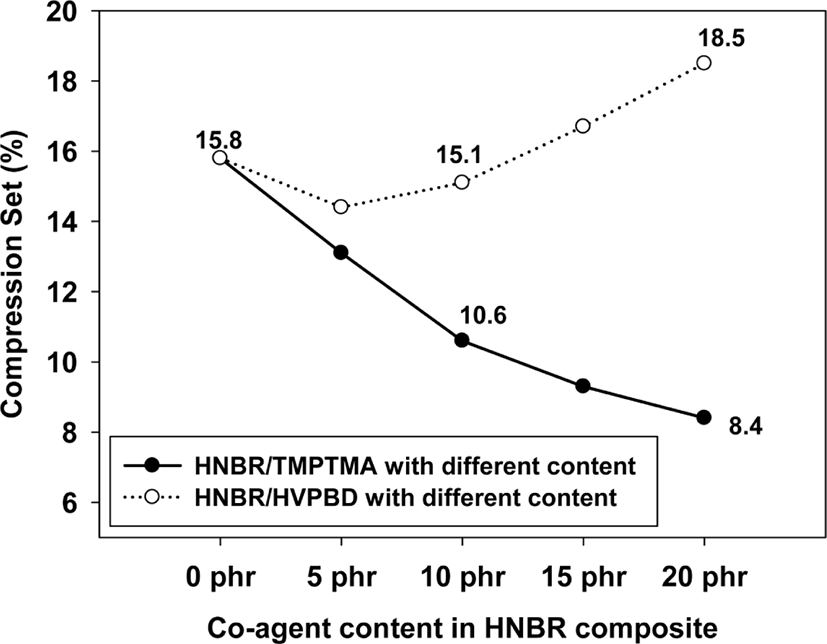
Conclusions
본 연구에서 TMPTMA 및 HVPBD 공가교제의 함량이 HNBR 복합소재의 가교특성, 기계적 물성, 내열특성 및 압축영구줄음율에 미치는 영향을 연구하였다. 가교특성은 TMPTMA 및 HVPBD 공가교제의 함량이 증가함에 따라 HNBR 복합소재의 △M은 증가하여 공가교제 첨가로 인한 가교밀도 향상을 확인 하였다. 스코치시간은 HNBR/TMPTMA가 HNBR/HVPBD 복합소재에 비하여 짧아진 결과 값을 나타내어 TMPTMA가 HVPBD 공가교제 보다 과산화물로 인해 형성된 라디칼에 빠르게 반응함을 알 수 있었다. 기계적 물성은 공가교제 첨가에 따른 가교밀도 증가로 인하여 Shore A 경도 및 10% 모듈러스가 증가하였으며, HNBR/TMPTMA가 HNBR/HVPBD 복합소재에 비하여 더 높은 증가를 나타내었다. 내열성은 공가교제 함량이 증가 할수록 HNBR/TMPTMA 복합소재에 비하여 HNBR/HVPBD 복합소재의 내열성이 저하됨을 확인하였다. 압축영구줄음율은 TMPTMA의 함량이 증가 할수록 지속적 감소를 나타내는 반면 HNBR/HVPBD 복합소재의 경우 HVPBD 5 phr 함유 이후부터 상승하는 결과를 확인하였다. 따라서 HNBR 복합소재의 가교효율 및 기계적 물성향상을 위해 TMPTMA 공가교제가 HVPBD 공가교제에 비하여 더 효과 적임을 알 수 있었다.