Introduction
최근 천연자원인 화석연료, 석유, 석탄 등이 빠르게 소모되고 있으며, 자동차 배기가스에 포함되어 있는 이산화탄소 배출에 관한 환경규제 정책이 강화되고 있다. 따라서 전 세계적으로 천연소재, 친환경 에너지원 등에 관한 산업이 대두되고 있다. 특히 자동차 산업에서 연비효율을 향상시켜 이산화탄소 배출량을 줄이고,1 타이어의 마모로 인한 미세 입자의 유해성을 줄이는 친환경 타이어가 요구되고 있다.2 자동차 연비효율을 향상시키기 위해서는 타이어의 가장 외부 층인 트레드 회전저항이 감소되어야 하며, 이와 trade-off 관계가 있는 습윤제동의 감소까지 동시에 이루어져야 한다. 따라서 타이어의 주요 성능인 회전저항, 습윤제동 및 내마모성을 모두 만족하는 타이어 트레드에 대한 연구가 필요하다.
타이어 트레드에는 내마모성이 뛰어나고 수명이 긴 스티렌-부타디엔 고무(SBR)가 많이 사용되고 있다. 또한 타이어 트레드의 비용 절감 및 성능 향상을 위해 보강 충전제를 도입하여 사용하고 있다.3,4 보강 충전제로 많이 쓰이던 카본블랙은 기본적인 탄화수소 구조로 이루어져있고 고무와 잘 섞이며 표면의 작용기들로 인해 우수한 기계적 물성을 나타낸다.5 하지만, 에너지 절약, 환경 보호라는 세계적 트렌드에 맞춰 카본블랙은 친환경 소재인 실리카로 지난 10년간 대체되어 왔다.6
실리카를 적용한 타이어 트레드는 카본블랙을 적용했을 때 대비 기계적 물성, 내마모성, 회전저항 및 습윤제동에서 우수한 성능을 보였다.7,8 하지만 실리카는 표면의 친수성 작용기인 실라놀기로 인해 소수성인 고무와 잘 섞이지 않는다는 단점이 있으며, 하이드록실기 간의 수소결합으로 인해 응집현상이 발생하여 분산성이 떨어진다.9-12 이러한 문제점을 해결하기 위해 최근 Wet Master Batch (WMB) 공정이 도입되었다. WMB 공정은 기존 모든 첨가물을 한 번에 고온에서 섞는 Dry Master Batch (DMB) 공정과는 달리 수상에서 혼합이 이뤄지기 때문에 실리카 분산성이 우수하고 고무컴파운드의 가공성도 우수하다. 또한 이미 표면이 개질된 실리카를 사용하기 때문에 공정에서의 에너지효율이 향상되고 알코올 등의 부산물 발생이 없고, 수상에서 이뤄지기 때문에 실리카 먼지가 줄어들어 작업환경이 개선되는 장점도 있다.13-16
WMB 공정에서 고무컴파운드의 가공성을 향상시키기 위해 고무배합유(Process oil)를 넣어준다. 고무배합유는 고분자를 팽윤시키고 윤활성을 부여해 뻣뻣한 고무사슬을 연화시킨다. 또한, 가공성을 개선하여 혼합과정을 용이하게 하고, 배합시간을 단축시킨다.17-20 고무배합유의 종류에는 파라핀계, 나프텐계, 아로마틱계로 분류되며 SBR고무에 대해서는 고무 분자와 상용성이 우수한 아로마틱계 고무배합유를 주로 사용한다. 하지만 고무배합유를 다량 첨가 시 고무분자끼리의 가교반응을 방해해 고무컴파운드의 가교밀도가 낮아지는 단점이 있어,21 고무배합유의 양을 조절하여 고무컴파운드의 가공성과 가교밀도를 적절히 조절하는 것이 매우 중요하다.
본 연구에서는 실리카-SBR 컴파운드를 제조하기 위하여 WMB 공정을 적용하고, 고무배합유를 적절하게 사용하여 최종 컴파운드의 가공성과 물성을 향상시키고자 하였다. 이에 따라, WMB공정으로 제조한 실리카-SBR 고무컴파운드에 고무배합유를 함량별로 투입하였고, 가황특성, 동적점탄특성, 기계적물성 및 내마모성을 비교하여 최적의 투입량을 선정하였다.
Experimental
실리카-SBR 컴파운드 제조를 위해 E-SBR 1723 (KUMHO PETROCHEMICAL, South Korea)를 사용하였으며 10 wt%의 bis [3-(triethoxysilyl) propyl] tetrasulfide (TESPT)로 표면개질 처리된 표면개질실리카 NK153 (MIRAESI, South Korea)가 사용되었고 응고제로는 2 wt% CaCl2가 사용되었다. 고무배합유로는 TDAE oil (KUMHO PETROCHEMICAL, South Korea)이 사용되었고, zinc oxide (ZnO)와 stearic acid (S/A)는 가교활성제로 사용되었으며, N-(1,3-dimethyl-butyl)-N'-phenyl-p-phenylenediamine (6PPD, Sigma Aldrich, United States)는 산화방지제로 사용되었다. sulfur (SAMCHUN, South Korea)는 가교제로 사용되었으며 1차 가황촉진제로 N-cyclohexyl-2-benzothiazole sulfonamide (CBS, Tokyo Chemical Industry, Japan), 2차 가황촉진제로 diphenyl guanidine (DPG, Sigma Aldrich, United States)가 사용되었다.
실리카-SBR 컴파운드는 WMB, SMB, FMB (final master batch) 총 3단계에 걸쳐 제조된다. WMB 공정에서는 ESBR에 실리카를 첨가하여 교반하였고, 가공유를 첨가하였고, ESBR을 응집시키기 위해 응집제로서 CaCl2를 첨가하여 진행하였다. SMB 공정에서는 ZnO와 S/A가 가황촉진제로, 6PPD가 산화방지제로 사용되었다. FMB공정에서는 sulfur가 가황을 위해 사용되었고, CBS, DPG, TBzTD가 가황촉진제로 사용되었다.
Figure 1은 실리카-SBR 컴파운드 제조를 위한 WMB, SMB, FMB 공정을 나타내었다. TESPT로 표면개질된 실리카를 증류수에 첨가하여 5분 동안 1000RPM으로 교반 후 1300RPM으로 5분 동안 교반을 진행한다. 이후 ESBR을 첨가하고 5분동안 교반을 진행한 후에 가공유를 첨가한다. 5분 동안 교반 진행 후 ESBR의 응집을 위해 CaCl2를 첨가해준다. 응집된 실리카-SBR 컴파운드를 증류수로 세척한 후 60°C에서 24시간 동안 건조를 진행한다.
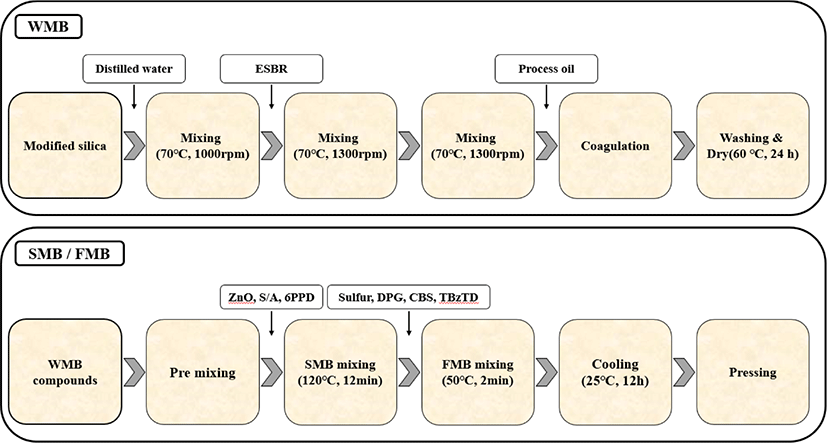
건조된 실리카-SBR 컴파운드를 가지고 SMB공정을 진행하였다. 건조된 실리카-SBR 컴파운드와 ZnO, S/A 및 6PPD를 니더기(Kneader)에 넣고 120°C에서 12분간 배합하였다. 이후 투롤밀(Two Roll Mill)을 이용하여 SMB화합물을 제조했다. FMB공정은 SMB공정과 유사하게 진행된다. SMB화합물과 sulfur, CBS, DPG, TBzTD를 니더기에 넣고 50°C에서 2분간 배합을 진행하였다. 이후 투롤밀을 이용하여 실리카-SBR 컴파운드를 준비하였다. 실리카-SBR 컴파운드의 구성성분은 Table 1에 표시되어 있다. 이때 phr은 E-SBR의 함량을 100 phr로 잡았을 때 각각의 함량을 나타낸다.
WMB | SMB | FMB | |||
---|---|---|---|---|---|
E-SBR/Silica (phr) | 10 wt% 1TESPT Modified silica (phr) | TDAE-oil | 2ZnO/3(S/A)/46PPD (phr) | Sulfur/5CBS/6DPG/7TBzTD (phr) | |
O40 | 100 | 110 | 40 | 4.5/(3)/1.5 | 3/3/0.2 |
O20 | 20 | ||||
O15 | 15 | ||||
O10 | 10 |
Measurement
제조가 완료된 실리카-SBR 컴파운드의 가황특성은 진동 각 ±1°, 온도 160°C 조건으로 moving die rheometer (MDR, MDR2020, MYUNGJI TECH)로 30분간 측정되었으며 최소 토크 값(Tmin), 최대 토크 값(Tmax), 스코치 시간(t10) 및 최적 가황 시간(t90)을 측정했다.
실리카-SBR 컴파운드 동적 점탄성 특성은 온도 –100°C에서 80°C, 진폭 30 μm, 주파수 10 Hz, 가열속도 3°C/min의 조건으로 DMTA (dynamic mechanical thermal analyzer, GABO, Germany)로 측정되었으며 저장 탄성률(E'), 손실 탄성률(E"), 연비특성(tan δ)을 측정했다.
Results and Discussion
고무배합유를 첨가한 실리카-SBR 컴파운드의 가황특성을 Figure 2와 Table 2에 표시하였다. t10 값은 실리카-SBR 컴파운드의 전체 가황단계의 10%까지 도달한 시점을 의미하며 일반적으로 스코치타임으로 불린다. 값이 클수록 가황이 이루어지기 전 고무의 물성을 조절할 수 있는 시간이 길어져 고무 가공작업성이 향상된다. 실험 결과에서 t10 값이 고무배합유를 20 phr 첨가하였을 때 가장 높은 값을 나타내고 이후 비슷한 값을 나타냄을 확인할 수 있다. 이로 인해 고무배합유를 20 phr 첨가하였을 때 최대의 고무 가공작업성을 나타냄을 알 수 있다. t90 값은 실리카-SBR 컴파운드의 전체 가황단계의 90%까지 도달한 시점을 의미하며 일반적으로 최적가황시간으로 불린다. 값이 작을수록 가황 종결이 빨리 일어나므로 가공속도가 빠르다. 실험 결과에서 t90 값이 고무배합유를 20 phr 첨가 시 최대값으로 가공속도가 가장 느리고 15 phr 첨가 시 큰 폭으로 감소하여 최소값을 보이며 가장 빠른 가공속도를 나타낸다. Tmin 값은 실리카-SBR 컴파운드의 최소 토크 값을 나타낸다. 값이 낮을수록 실리카-SBR 컴파운드의 점도가 낮아 유동성이 좋음을 의미하고 이는 실리카의 분산성이 좋음을 의미한다. 실험 결과에서 고무배합유의 함량이 낮아질수록 Tmin 값이 상승함을 확인할 수 있다. 이는 고무배합유의 첨가량이 감소할수록 실리카-SBR 컴파운드의 점도가 높아져 유동성이 감소하였고 이로 인해 실리카-SBR 컴파운드의 배합이 제대로 이루어지지 않아 실리카 분산성이 저하된 것으로 여겨진다. Tmax 값은 실리카-SBR 컴파운드의 최대 토크 값을 의미한다. 값이 높을수록 실리카-SBR 컴파운드가 딱딱함을 의미하며 기계적 물성과 깊은 관련이 있다. 실험 결과에서 고무배합유의 첨가량이 줄어들 때 Tmax 값이 증가하다가 15 phr에서 최대값을 나타낸 뒤 약간 감소함을 확인했다. 이는 고무배합유의 첨가량이 줄어들수록 실리카의 분산성이 저하되고 실리카의 응집현상이 일어나서 Tmax 값이 향상된 것으로 여겨진다. Tmax-Tmin 값은 실리카-SBR 컴파운드의 최대 토크값에서 최소 토크값을 뺀 값이며 가교밀도를 나타낸다. 고무배합유의 첨가량이 줄어들수록 Tmax-Tmin 값이 향상되다가 15 phr 첨가시에 최대값을 나타내고 이후 감소함을 확인하였다. 임계점 이후에는 실리카-SBR 컴파운드의 점도가 과하게 증가하여 가교밀도에 악영향을 끼치는 것으로 여겨진다.
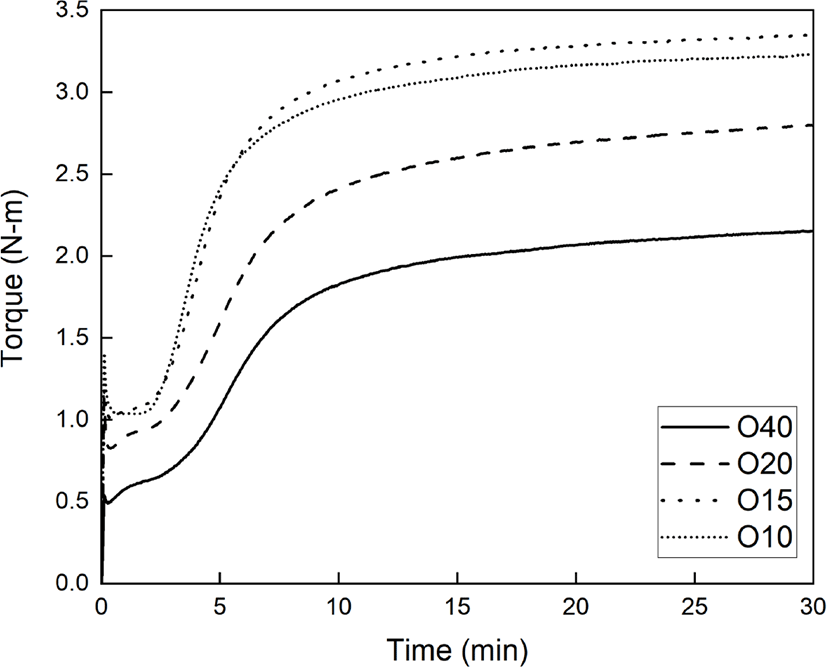
고무배합유를 첨가한 실리카-SBR 컴파운드의 동적점탄특성을 Figure 3과 Table 3에 표시하였다. 일반적으로, tan δ는 손실 탄성률(E'')을 저장 탄성률(E')로 나눈 값이다. tan δ 값이 높으면 점성 특성에 가깝고 tan δ 값이 낮으면 탄성 특성에 가깝다.22 고무의 점탄성 특성인 tan δ(=E''/E')는 회전저항, 습윤제동 등 타이어의 주요 특성들과 밀접한 관련이 있다. 일반적으로 고무를 포함한 고분자 재료는 온도에 따라 탄성율이 변화하는데, 낮은 온도에서는 유리상태(glassy state)의 단단한 고체의 특성을 나타내고, 높은 온도에서는 고무상태(rubbery state)의 특성을 지닌다. 이러한 두 종류의 상태가 공존하는 온도영역, 즉 유리상태에서 고무상태로 전이하는 온도를 유리전이 온도(Tg)라고 한다. Tg는 고무의 내마모성과 밀접한 관련이 있으며 60°C에서의 tan δ 값은 타이어의 회전저항 (rolling resistance)를 나타내며, 0°C에서의 tan δ 값은 습윤제동(wet traction)을 나타낸다. Tg 값의 경우 고무배합유의 첨가량이 줄어들수록 감소하다가 15 phr 첨가 시 최소값을 나타내고 이후 증가한다. Tg 값은 낮아질수록 실리카-SBR 컴파운드의 유연성이 향상됨을 의미하는데 이는 가황특성에서 확인하였던 Tmax 값과 유사한 경향을 나타낸다. Tg 에서의 tan δ 값은 실리카 분산성을 의미하며, 값이 낮을수록 실리카 분산성이 낮다는 것을 의미한다. 실험 결과에서 고무배합유 첨가량이 줄어들수록 Tg 에서의 tan δ 값도 감소하다가 15 phr에서 최소값을 나타내고 이후 증가하는 경향을 나타낸다. 이는 가황특성에서 실리카 분산성을 나타내는 Tmin 값과 비슷한 경향을 나타내는 것을 알 수 있다. 0°C에서의 E'' 값은 습윤제동을 나타내며 값이 높을수록 젖은 노면에서의 제동이 우수함을 나타낸다. 실험결과에서 0°C에서의 E'' 값은 고무배합유의 첨가량이 줄어들수록 증가하다가 15 phr 첨가 시에 최대값을 나타내고 이후 감소하는 경향을 나타낸다. 이는 고무배합유의 첨가량이 줄어들수록 실리카의 분산성이 감소하여 응집현상이 일어나 에너지의 손실이 발생하여 습윤제동이 향상됨을 나타낸다. 60°C에서의 tan δ 값은 회전저항을 나타내며 값이 낮을수록 회전저항도 낮음을 나타낸다. 실험 결과에서 60°C에서의 tan δ 값은 고무배합유의 첨가량이 줄어들수록 증가하다가 20 phr 첨가 시에 최대값을 나타내고 이후 감소하는 경향을 나타낸다. 일반적으로 고분자 사슬 말단의 mobility가 실리카-SBR 컴파운드의 hysteresis를 유발한다고 알려져 있다. 따라서 고무배합유의 첨가량이 줄어들수록 가교밀도가 상승하고 고분자 사슬 말단의 mobility가 제한을 받아 hysteresis의 영향을 덜 받게 되어 60°C에서의 tan δ 값이 낮아진 것을 확인하였다. 이는 고무배합유의 첨가량이 줄어들수록 회전저항이 줄어 연비특성이 개선되었음을 나타낸다.
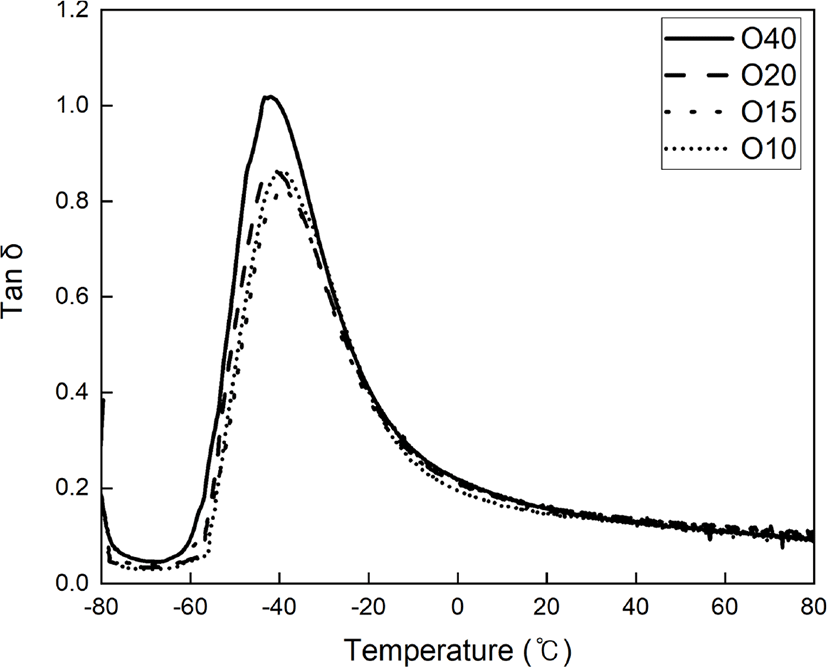
고무배합유를 첨가한 실리카-SBR 컴파운드의 기계적 물성을 Table 4에 표시하였다. Hardness는 실리카-SBR 컴파운드의 딱딱한 정도를 나타내며 일반적으로 실리카 간 상호작용과 관련이 있다. 실험 결과에서 고무배합유의 첨가량이 줄어들수록 실리카 분산성이 감소하여 실리카 간 응집이 발생하여 실리카-실리카 상호작용이 활발해져 경도가 증가하는 경향을 나타냄을 알 수 있다. M100%, M300% 는 각각 100%, 300% 신장에서의 모듈러스를 나타낸다. Elongation at break은 실리카-SBR 컴파운드가 파열될 때까지의 신장율을 %로 나타낸 수치이며 Tensile strength는 실리카-SBR 컴파운드가 파열될 때까지의 최대인장하중을 단면적으로 나눈 값이다. Elongation at break는 가교밀도와 반비례하는 경향이 있고 나머지 기계적물성들은 가교밀도에 비례하는 경향이 있다. 가황특성 결과에서 Tmax-Tmin 값을 통해 가교밀도는 고무배합유의 첨가량이 줄어들수록 증가하다가 15 phr에서 최대값을 나타낸 뒤 이후 감소하는 경향을 확인하였다. M100%, M300% 및 Tensile strength 값 또한 같은 경향을 나타낸다. 이는 고무배합유의 첨가량이 줄어들수록 실리카 분산성이 감소함에 따라 응집현상이 발생하여 가교밀도가 증가하고 또한 실리카-SBR 컴파운드의 점도가 높아지고 딱딱한 성질을 나타내기 때문으로 여겨진다. 또한 가교밀도가 증가함에 따라 가교점 사이의 사슬길이가 감소하게 되고 Tensile strength가 증가하는 경향을 나타낸다.23
고무배합유를 첨가한 실리카-SBR 컴파운드의 내마모성을 Figure 4에 표시하였다. 내마모성은 실리카-SBR 컴파운드가 지면과의 마찰로부터 저항하는 능력을 의미하며 고무-충전재 간 상호작용과 관련이 있다. 실험 결과에서 고무배합유의 첨가량이 줄어들수록 내마모성이 개선됨을 확인할 수 있다. 이는 고무배합유의 존재가 실리카-SBR 컴파운드를 제조 및 가공하는 공정에서는 가공성 개선, 실리카 분산성 개선 등의 역할을 하는 유의미한 첨가제이지만 내마모성의 측면에서는 고무-충전재간 상호작용을 방해하는 불순물로 작용하는 것으로 여겨진다. 따라서 고무배합유의 첨가량이 줄어들수록 고무-충전재간 상호작용의 강화로 인해 내마모성이 향상됨을 나타낸다.
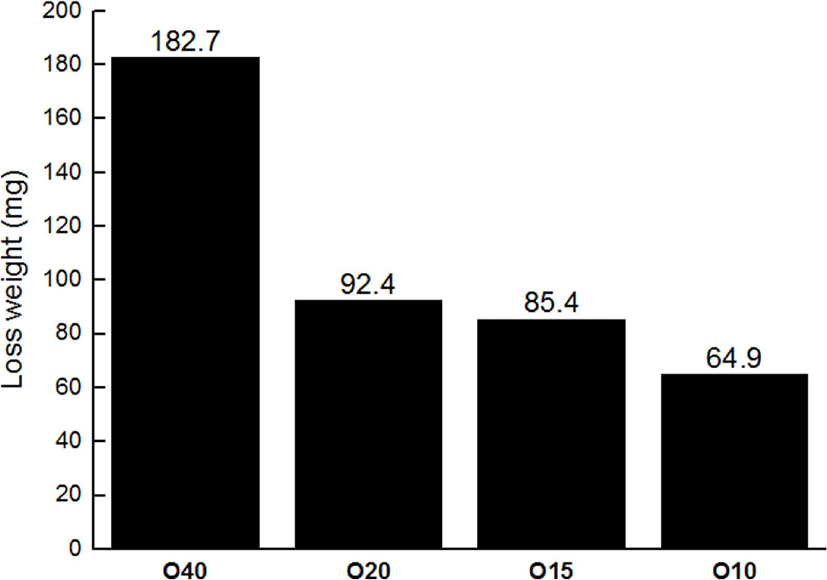
Conclusions
본 연구는 고무배합유의 첨가량이 실리카-SBR 컴파운드의 기계적 물성과 내마모성에 어떠한 영향을 미치는지 확인하기 위해 진행하였다. 고무배합유의 첨가량은 각 40, 20, 15, 10 phr 이 첨가되었고, 각 제조된 실리카-SBR 컴파운드의 가황특성, 동적점탄특성, 기계적 물성 및 내마모성을 비교하였다. 고무배합유의 첨가량이 줄어들수록 실리카-SBR 컴파운드 배합 시 점도가 높아져 유동성이 감소하고, 실리카 분산성은 감소하였다. 이에 따라, 가교밀도가 증가하고 실리카-SBR 컴파운드의 점도가 증가하여 경질의 특성을 나타내는 것을 확인하였다. 또한, 응집현상에 의한 에너지 저하로 실리카-SBR 컴파운드의 습윤제동이 개선되었고, 고분자 사슬 말단의 mobility가 제한을 받아 hysteresis의 영향을 덜 받게 되어 연비특성이 개선되었다. 일반적으로 습윤제동과 연비특성은 trade-off 관계임에도 불구하고 고무배합유의 첨가량을 줄였을 때 습윤제동과 연비특성이 동시에 개선되는 효과를 확인하였다. 기계적 물성의 경우 고무배합유의 첨가량이 줄어들수록 실리카-SBR 컴파운드의 가교밀도가 증가함에 따라 가교점 사이의 사슬길이가 감소하게 되고 M100%, M300% 및 Tensile strength가 증가하는 경향을 확인하였다. 내마모성 또한, 고무배합유의 첨가량이 줄어들수록 내마모성이 개선됨을 확인하였다. 이처럼 고무 배합유는 실리카-SBR 컴파운드의 가공성 개선, 실리카 분산성 개선 등의 역할을 하지만, 적정량의 고무배합유를 사용하여 타이어의 습윤제동 및 연비특성과 같은 주요 물성을 보존하고, 고무 컴파운드의 기계적 물성 및 내마모 특성을 개선시킬 수 있음을 확인하였다.