Introduction
Tire tread is the designed for key properties of tire which are fuel efficiency, abrasion resistance and wet grip performance. Furthermore, tire tread mainly provides contact area between road surface and tire. Styrene butadiene rubber (SBR) is the most commonly used rubber for tire tread.1 The purpose of developing SBR compound for the tire tread is the achieve excellent mechanical and physical properties for using various application regions and long term. However, under the thermal, mechanical degradation and using for long term, the properties of tire tread decrease.2-8 This degradation of tread compound can makes the product softened or hardened depend on the conditions.4-6 The most common reason why properties of tire tread decrease is the processing oils which obtained from petroleum crude.
Processing oils are the one of key additives at rubber compound which can reduce the cost, increase processability, save energy and increase the filler dispersion. However, this processing oils can often evaporate or bleed from rubber compound that can decrease the rubber properties. Furthermore, these bleedings can be harmful for environment.9 Highly aromatic oils are most commonly used processing oils for tire industry owing to their compatibility. And, the among of highly aromatic oils, Treated Distillate Aromatic Extract (TDAE) is the more preferred oil because of its high compatibility with SBR.10-11 In order to increase tire life, the HA oils must be replaced by different processing aids which can keep the properties of tire for long term.
Research study which has recently reported shows, using liquid rubbers as a processing aid provides sufficient mechanical properties and maintain for long term at SBR based compound, which determined by extraction test.12 Liquid rubbers are low molecular weight processing aids which have appreciable viscous flow at room temperature. They can be crosslinked with the main rubber chain during the vulcanization process.13 Liquid rubbers can be polymerized by using living anionic polymerization techniques which have great superiorities such as allows to control microstructure like vinyl content and also capable to indicates low polydispersity index (PDI). When used the liquid rubber as a processing aid, these controllable properties have a major impact on determining the general characteristics of rubber compound.
One of important property of liquid rubbers is, it can customize by functionalization by living chain termination.14 After commercially introduced that silane-terminated liquid polybutadienes are used as a silane functionalized low molecular weight processing aid for tire technology, it has well reported at previous researches.15-19 These functional groups based on silane technology are capable to provide same reaction structure as coupling agents.
Resins are another low molecular weight processing aid with high glass transition temperatures which are commonly used in tire industry because of good compatibility with tire elastomers.20 And some of them called as a tackifiers which build a tack between layers of green tire at uncured stage and assembling process. Tack is related with existing of movable chain ends which are merge at room temperature under small pressure and show resistance to stress if an attempt to separate layers again. This tack may also affect viscoelastic properties of rubber compound.21-24
In this study as a liquid rubber non-functionalized polybutadiene (N-LqBR), center functionalized polybutadiene (C-LqBR); as a resin p-tert-octylphenolic resin (P-Resin) and C5 hydrocarbon resin (H-Resin) have used to find solution for bleeding of processing oils from tire tread. Furthermore, properties of tire compound such as vulcanizate structure, mechanical properties, viscoelastic properties and abrasion resistances were also evaluated.
Experimental
The materials which used for polymerization are cyclohexane (99%, Samchun chemical Co.) as solvent, n-butyl lithium as an initiator (2.0 mol/L in cyclohexane, Sigma Aldrich), 1,3-butadiene (Kumho Petrochemical Co.) as a monomer, anisole (99%, Samchun chemical Co.) as a modifier, for coupling agent tetraethyl orthosilicate (TEOS) (98%, Sigma-Aldrich). And benzyl alcohol (Junsei, guaranteed reagent) was used as a termination agent.
Materials which used in this study; SSBR 5220M (Kumho Petrochemical Co., styrene content: 26.5 wt%, vinyl content: 26 wt%, non-oil extended), silica (Ultrasil 7000GR, Evonik), bis-[3-(triethoxysilyl)-propyl]-tetrasulfide (TESPT) as silane coupling agent. As a processing oil; treated distillate aromatic extracted (TDAE, Tg: -48°C), center functionalized liquid butadiene rubber (C-LqBR, Tg: -93°C), non-functionalized liquid butadiene rubber (N-LqBR “LBR-305, Kuraray”, Tg: -95°C), alkyl phenolic resin (P-Resin “p-tert-octlyphenol”, softening point 95°C~100°C, Tg: 56°C KORESIN), hydrocarbon resin (H-Resin “C5”, softening point 95.8°C, Tg: 58°C) were used. Other additives include zinc oxide (ZnO), steric acid (CH3(CH2)16COOH), antioxidant N-(1,3-dimethyl butyl) -N-phenyl-p-phenylenediamine (6PPD) was used in the compound. Sulfur, n-cyclohexyl benzothiazyl-2-sulfenamide (CBS) and 1,3-diphenylguanidine (DPG) were used as vulcanization agents. Table 1 shows the information about processing aids.
Center functionalized liquid butadiene rubber (C-LqBR) was polymerized by anionic polymerization at 50°C. For polymerization the C-LqBR, at first, non-functionalized liquid butadiene rubber was polymerized by anionic polymerization at 50°C by adding cyclohexane, anisole, 1,3 butadiene and n-butyllithium to reactor. The amount of N-butyllithium (initiator) was used to control molecular weight of liquid butadiene rubber. Hereupon, TEOS diluted with cyclohexane added to synthesize C-LqBR. Lastly, benzyl alcohol added to terminate polymerization reaction.
Compounds were prepared using an internal mixer (kneader, 300 mL) based on the formulation shown in Table 2. The mixing procedure is shown in Table 3. The dump temperature was set at 150°C~155°C and the filler factor was set at 70% of the mixer capacity. The input unit was administered on a rubber basis with the parts per hundred rubber (phr). For 2nd stage, masterbatches from 1st stage had been mixed with curatives at 50°C initial temperature.
1H-Nuclear magnetic resonance spectroscopy (1H NMR; Varian, Unity Plus 300 spectrometer, Garden State Scientific, USA) was used to determine the vinyl content and functional groups in liquid butadiene rubber.
Molecular weight and molecular weight distribution were measured by gel permeation chromatography (GPC, Shimadzu, Japan). GPC was measured using solvent delivery unit, reflective index detector and three types of column (Stryagel column (HT 6E, 10 μm, 7.8 mm × 300 mm), styragel column (HMW 7, 1520 μm, 7.8 mm × 300 mm) and styragel column (HMW 6E, 1520 μm, 7.8 mm × 300 mm). Calibration of GPC were prepared by using polystyrene standard.
Storage modulus was measured by the rubber process analyzer 2000 (RPA 2000) from Alpha Technologies (Hudson, OH, USA) at 60°C and between 0.28%~40.04% strain range.
Processability of rubber was evaluated by Mooney viscometer (Vluchem IND, Korea) according to ASTM D1646 at 100°C and 2 rpm rotor speed. (ML1+4@100°C)
Compound cure characteristic was measured by moving die rheometer (MDR, ALR-3, TOYOSEIKI, Japan) under 160°C for 30 mins at oscillation angle of ± 1° to determine optimized vulcanization time.
Vulcanizates samples were prepared in 10 mm × 10 mm × 2 mm sizes and immersed to 30 mL THF for two days then, 30 mL hexane for 1 days to determine organic extraction mass. After drying at the room temperature for 1day weight loss gives organic extraction loss. Hereafter, the samples were immersed to toluene for 24 hours and weighed again to determine crosslink density. Crosslink density was calculated by using Flory-Rehner equation (1).
V : Crosslink density (mol/g)
Mc : average molecular weight between crosslink points (g/mol)
Vr : the volume fraction of rubber in the swollen gel at equilibrium
Vs : the molar volume of solvent (cm3/mol)
ρ : the density of the rubber sample (g/cm3)
χ : the polymer-solvent interaction parameter
Vr value at the Flory-Rehner Equation was obtained from the equation (2)
Wd : Weight of dried sample after swelling
Wf : Weight of filler in sample
Ws: Weight of sample after swelling
ρs : Solvent density
ρr : Rubber density
Mechanical properties which are tensile strength, elongation at break and the modulus were tested by universal testing machine (UTM, Model: KSU-05M-C, KSU Co, Korea). Specimens were prepared according to ASTM D412 which is 100 mm × 25 mm × 2 mm sized.
Results and Discussion
Reaction mechanism of C-LqBR which explained in Figure 1 shows that it is possible to make four different type functionalized liquid butadiene.25 Molecular weight and molecular weight distribution were determined by GPC and shown in Figure 2. Determination has done at two steps. First, during the polymerization, the sample (aliquot) had been taken before adding coupling agent and measured the molecular weight and then after adding coupling agent another sample (final) had been taken to determine molecular weight. Determination of those two samples are shown in Table 4. Increasing molecular weight to two times verify us polymerization reaction is prone to create final product (b) in Figure 1. Additionally, microstructure of C-LqBR was determined by 1H-NMR and shown in Figure 3. Liquid polybutadiene contains 1,2 vinyl group which showed peak at 4.2~5,1 (d) and 1,4 addition of polybutadiene at 5,1~5,7 (c). Considering the peaks in Figure 3 the vinyl content in final C-LqBR have calculated as 14%. Also, ethoxy peaks at 3.75~3.80 (e) from Figure 3 verify C-LqBR successfully functionalized.
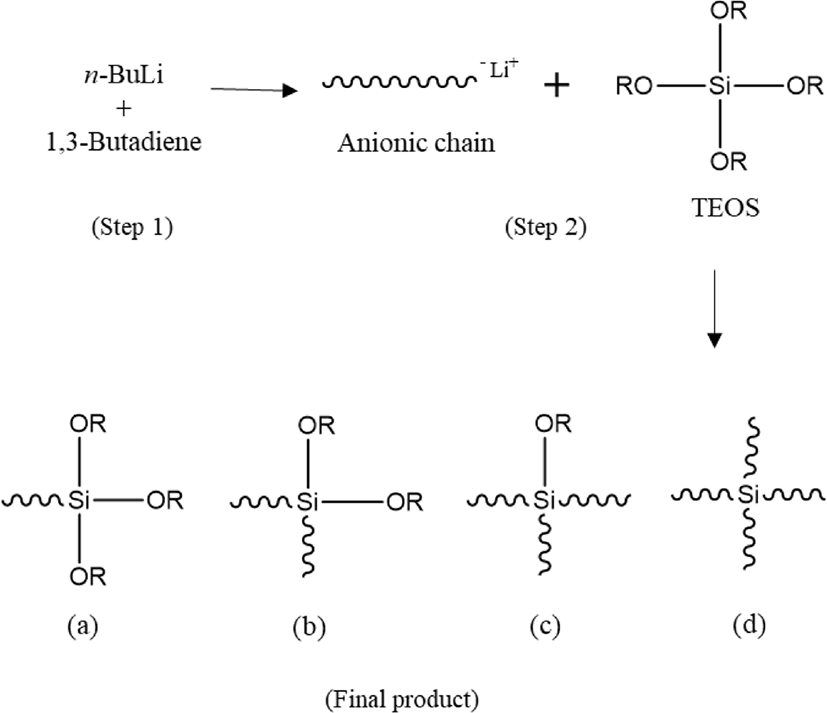

Aliquot | Final | |
---|---|---|
Mn (g/mol) | 12,000 | 24,000 |
PDI | 1.1 | 1.1 |
Vinyl content (%) | - | 14 |
Payne effect can describe as the difference of storage modulus (G’) at low and high strains which represents dispersion of silica in rubber compounds.26 Usually, high difference of storage modulus between high strain and low strain shows strong filler-filler interaction.27 In this study, the storage modulus was measured by the rubber process analyzer 2000 (RPA 2000) from Alpha Technologies (Hudson, OH, USA) at 60°C and shown in Figure 4&5. Table 5 shows ΔG’ value of compounds. N-LqBR and C-LqBR compounds are showing lower ΔG’ value than TDAE compound. Processing oils are the lubricants which are basically lowering the intermolecular interactions. However, liquid butadiene rubbers and main polymer of compound (SBR) have similar structure which increase the possibility of lubrication. Liquid butadiene rubbers can also improve the silica dispersion due to the increased viscosity compared to TDAE oil. Furthermore, ethoxy groups of C-LqBR can react with the silanol groups on silica surface and reduce the polarity of silica, which improves the dispersion of silica. Thus C-LqBR compound shows lower ΔG’ value than N-LqBR compound.
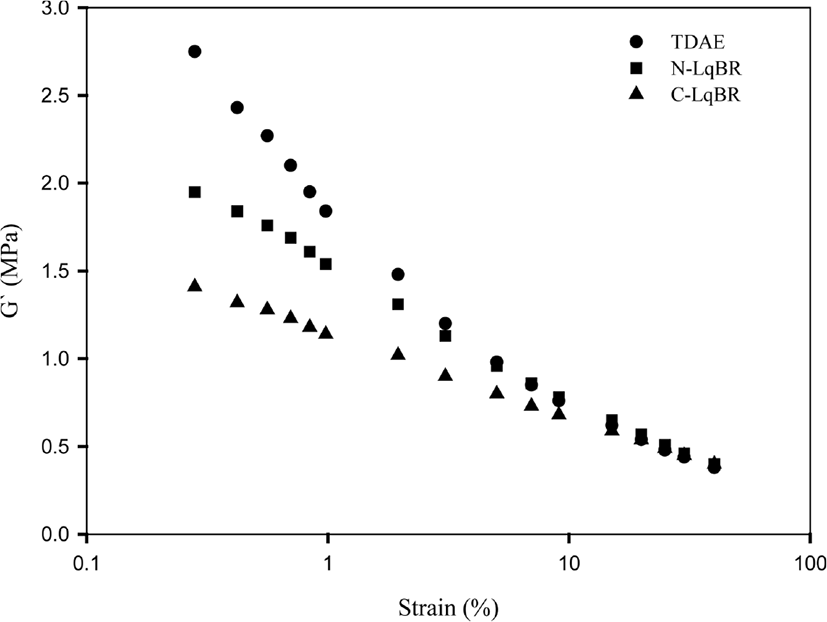
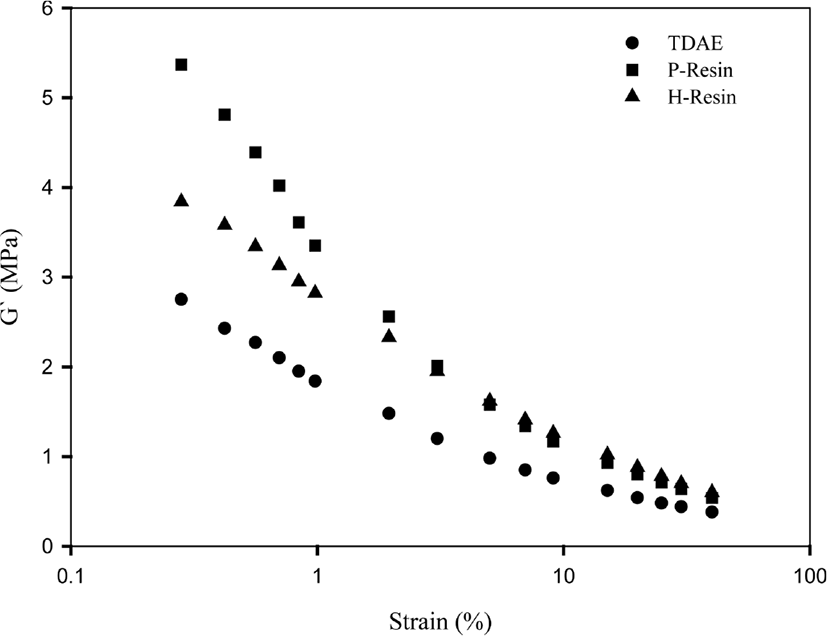
Compound | TDAE | N-LqBR | C-LqBR | P-Resin | H-Resin |
---|---|---|---|---|---|
ΔG’ (MPa) (0.28%-40.04%) | 2.37 | 1.55 | 1.01 | 4.83 | 3.24 |
In the case of resin including compounds, they show higher ΔG’ value than TDAE compound. Resins that we have used in our research are solid materials when the temperature below 95°C~100°C and the temperature of test condition of RPA is 60°C, thus, resin compounds show high G’ values at low strain.28 Besides, -OH group of phenolic resin forms hydrogen bond network.29 When the filler dispersed in the rubber, it forms weak chemical interaction between filler particles. This filler-filler network can be broken under the strain. But in the case of P-Resin, -OH groups additionally form hydrogen bonds with the silica surface and increase storage modulus at low strain. This property of P-Resin may cause to high storage modulus than H-Resin.
Cure characteristics which were measured by moving die rheometer are shown in Figures 6 and 7. ΔT (Tmax – Tmin) has described difference between maximum torque and minimum torque, and ΔT is very commonly related to crosslink density, which means high ΔT indicates high crosslink density.30 However, ethoxy groups of C-LqBR can react with the silanol groups on silica surface and increases the filler rubber interaction, which increases ΔT of rubber. H-Resin used compound has similar ΔT value as a TDAE compound which doesn’t show crosslink reaction from the MDR data on the other side P-Resin used compound shows lower ΔT than TDAE compound. P-Resin and H-Resin are the tackifiers which provide tack at uncured stage. Tacky stocks often cause air entrapment in the building process which can lead to cure defects.31 In the case of phenolic resin polar-polar interaction between polar accelerators and polar group of phenolic resin cause the partial loss of accelerators and decreases the cured properties.
From the molecular weight difference between TDAE oil and liquid butadiene rubbers we can expect that liquid butadiene rubber used compounds may have higher Mooney viscosity. Table 6 shows that, liquid butadiene rubbers show similar Mooney viscosity as TDAE oil; even though, liquid butadiene rubbers have higher molecular weight than the TDAE oil, structure similarity between liquid butadiene rubbers and SBR increases the lubrication and lower the Mooney viscosity. Although resins have not so higher molecular weight than TDAE oil, they have higher Mooney viscosity than TDAE oil compound. Resins have high softening point which is between 95°C~100°C; test condition of Mooney viscosity is (100°C), not enough to heat the resins. Thus, resin compounds have higher Mooney viscosity.
There are two factors which affect the crosslink density of vulcanizate rubber; filler-rubber interactions and chemical crosslinks.32 The sum of these two factors can be defined as a total crosslink density. During the vulcanization, the liquid butadiene rubbers consume sulfur which decreases the crosslink density of rubber compound. This is the reason why N-LqBR and C-LqBR compounds have less crosslink density. Figure 8 shows the crosslink density of C-LqBR compound increases with functional groups. Ethoxy groups of C-LqBR react with the silanol group on silica surface and it increases the filler rubber interaction which effects crosslink density. In the case of resin compounds, H-Resin compound shows similar crosslink density as the TDAE compound; unlike H-Resin compound, P-Resin compound has less crosslink density because of the partial loss of accelerators.
It has known that TDAE oil has bleeding problem from the rubber compound which decreases the properties. The extraction test verified crosslink reaction between liquid butadiene rubbers and SBR which prevents the bleeding in compounds as shown in Figure 9. Extraction loss difference between liquid butadiene rubbers, caused by the silanization reaction of functional groups of C-LqBR. Unless the liquid butadiene rubbers, resins show similar crosslink density value as TDAE oil which means they don’t have crosslink reaction with main rubber. Thus, resin compounds have similar weight loss as TDAE oil compound.
The mechanical properties of compounds which measured by universal testing machine and DIN abrasion loss values are shown in Figure 10&11 and Table 7. Usually, mechanical properties and crosslink density of the compounds show similar behavior.33 And modulus at 300% elongation (M300%) is most commonly related with filler rubber interaction.34 Liquid butadiene rubber compounds show lower modulus at M300% than TDAE oil compound as expected from crosslink density. However, unlike the liquid butadiene rubber compounds, resin compounds show different trends. Although, the H-Resin compound has similar crosslink density as TDAE compound, when comparing the cure characteristics and mechanical properties of H-Resin, it can be seen that Tmax and M300% values of H-Resin compound higher than the TDAE oil compound. This may be caused by characteristics of H-Resin. Furthermore, due to partial loss of accelerator effect from cure state and less crosslink density in Figure 8 resulted as low mechanical property for P-Resin compound.
Commonly abrasion loss increases with increasing glassy transition temperature35; resin compounds have higher Tg than the other compounds that caused higher abrasion loss. Between two resin compounds, H-Resin compound has higher crosslink density which decreases abrasion loss. Thus, H-Resin compound has better abrasion resistance than P-Resin compound.34 LqBRs have much lower Tg than the TDAE oil and resins which resulted as less abrasion loss. Furthermore, the reason why C-LqBR has better abrasion resistance than N-LqBR is caused from higher crosslink density.
Results of dynamic viscoelastic properties are shown in Figure 12&13 and Table 8. Dynamic viscoelastic properties are mostly related with the tire performance. Loss modulus (G”) is a loss factor at low temperature conditions (0°C-20°C) which indicates the wet traction; higher value of G” higher the wet trac-tion.36 During the repeated deformation, the energy applied to rubber is converted into heat as the result of destruction and regeneration of filler networks, because of this, the temperature of rolling tire rises up to 60-80°C. So, Tan δ at 60°C can represent rolling resistance of tire.37 Hysteresis has been known the main reason of energy loss in tire tread compound.38Table 8 verify the N-LqBR and C-LqBR compounds with free chain ends which are visualized in Figure 14, have higher rolling resistance which cause the hysteresis at compound compare to TDAE compound.
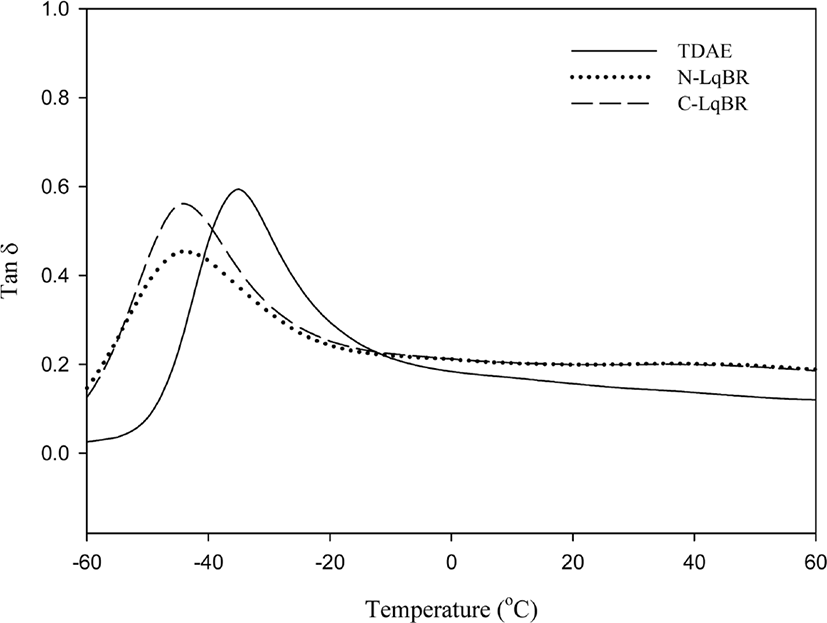
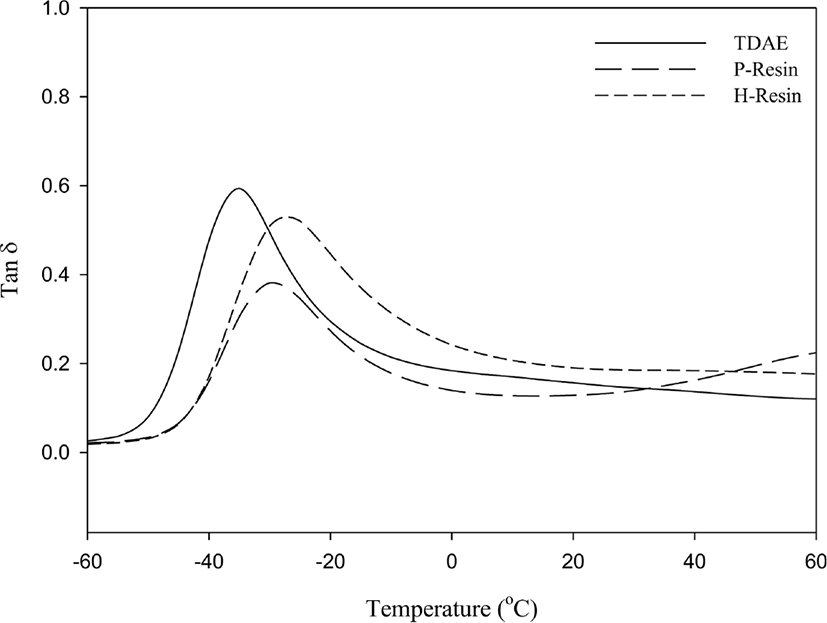
Compound | Snow traction | Rolling resistance | Wet traction |
---|---|---|---|
G’@-30°C (MPa) | tan δ 60°C | G”@0°C (MPa) | |
Ref. | 130 | 0.120 | 6.6 |
LqBR | 67 | 0.188 | 5.2 |
C-LqBR | 54 | 0.185 | 4.4 |
P-Resin | 446 | 0.224 | 17 |
H-Resin | 396 | 0.176 | 11.4 |
Another main reason which causes the hysteresis is filler dispersion; the filler-filler network is relatively weak and breaks easily under the influence strain which causes energy losses, that means better filler dispersion better rolling resistance.39 From the Payne effect results; resin compounds have high filler-filler interaction, bad dispersion which cause higher rolling resistance than the other compounds.
Resins are processing aids which have high glass transition temperature (Tg). Higher Tg of resin at Table 8 can higher Tg of rubber compound and increases the energy dissipation, thus resin compounds have higher wet traction.40,41 Incompatible resin forms secondary peak in the range of the resin Tg in the vulcanizates as it can be seen in Figure 13. So, this poor compatibility resin forms separated phase at compound. Phase separation can increase the hysteresis and cause the bad rolling resistance at resin compound.20 This effect can be seen at P-Resin compound.
It has indicated that softer compounds with higher resilience, had higher friction on ice road in the temperature range of -30°C to 0°C. The rubber compounds with low Tg were recommended for the best traction performance of tread compounds on ice and snow road.42Table 8 shows that liquid butadiene rubbers have lowest storage modulus (G’) values which indicates snow traction, because of their low Tg properties. Also, at the low temperatures processing oils can migrate or bleed out from the rubber; so, tire tread gets stiffer and low temperature performance decreases.9 Liquid butadiene rubbers crosslink the main polymer, prevent the extraction loss.
Conclusion
In this study different type processing aids were used to reduce migration and evaluate the physical properties of SSBR/silica compounds. Two different type of liquid butadiene rubbers and two different resins were applied. Solvent extraction test showed excellent results that crosslinkable liquid butadiene rubbers reduce extraction loss from the compounds. Liquid butadiene rubbers not only reduce the extraction but also increase abrasion resistance and filler dispersion. Furthermore, liquid butadiene rubbers keep elasticity properties of tire and provide long life time at low temperature conditions which is important for snow tire.
Resins are processing aids with high glass transition temperature which can also called as a tackifier. Tack is related with easily movable chain ends that occurs, entanglement under small pressure to resist separation at rubber compound but unlike the liquid butadiene rubber compounds, resin compounds do not show chemical interaction. Compared to TDAE compound, they have shown similar extraction and crosslink density results. High Tg of resin increased abrasion loss but resin compounds showed better wet traction than the TDAE compound.