Introduction
Polymers, because of their inexhaustible properties, ease of processability, abundant availability, environmental stability, light weight, geometric conformability, comparatively low-cost, became parts and parcel towards developing almost all materials to be needed in our daily life, which includes but not limited to the house-hold commodities, agricultural utensils, aeronautics, automobile, biomedical, and so on.1,2 But, the depletion of fossil fuels from the earth crust limits the resource of the polymers in future.3 On the other hand, the petro-polymers commonly used as commodity plastics such as polyethylene (PE), polypropylene (PP), polystyrene (PS), halogenated polymers, etc., are in general non-degradable, and consequently threatening the environment especially with huge negative effect to the soil and water.1,2 If the thermal treatment is considered effective disposal of the polymer wastes, the environmental air quality is expected to pollute again. Normally, biodegradation of the solid wastes under the influence of humidity, air-oxygen and microbes is considered as sustainable towards the safe environment.1,2 In search of alternatives to the non-biodegradable petro-polymers, many researches have been attempted to develop the biodegradable polymers (BP) that minimize the long term accumulation of the polymers in the environment. BPs are generally classified into two major categories: natural polymers (e.g., cellulose, chitin/chitosan, proteins/peptides, polyesters like polylacticacid (PLA), etc.) and synthetic polymers (e.g., poly(butylene adipate-co-terapthalate (PBAT).1-5 In contrast to other BPs, PBAT, because of its 100% biodegradability, biocompatibility, ease of processability, and high flexibility with high elongation at break, has attracted significant research interest. However, similar to most of the biodegradable polymers, mechanical properties (e.g., tensile property) of PBAT is considerably poor, which limits its applicability in wide range of applications.1,2,6-10 Use of fillers as mechanical reinforcement can improve the tensile property of the matrix. To ensure the effective reinforcement, the fillers are required to be compatible with the PBAT matrix confirming its well dispersion, while maintaining the biodegradability of the composite.11 Presence of abundant polar functionalities of PBAT makes it compatible with different inorganic and organic filler materials towards developing the mechanically well performing PBAT composites to be applied in different industries. Cost-effectiveness remains another major concern to ensure its acceptability by the customers. Nowadays, calcium carbonate (CaCO3), a naturally abundant low-cost material is being used as a filler with different polymers. Specifically, in a recent report, CaCO3 has been used as a filler to develop a low-cost PBAT composite having good mechanical and thermal property.11 Similar to the carbonate salt of calcium i.e., CaCO3, gypsum (CaSO4) is a sulfate salt of calcium, and it is a waste by-product of phosphate and sulfuric acid industries. The gypsum being a solid waste became a threatening to the environment and needed to be properly disposed.12-16 But the disposal procedures are complicated and cost-intensive. Thus, there should be an effort to enable the “trash to treasure” by formulating the gypsum-based polymer composites. Improved compatibility and better dispersion of inorganic fillers through their surface modification by employing proper surface modifying agents are reported to develop the polymer composites with enhanced performance.17-24 For effective modification, the modifying agents are expected to have sufficient polar functionalities. Polyethelene glycol (PEG), stearic acid (SA), and maleic anhydride are the examples of a few of the commonly used surface modifying agents. In this study, instead of these modifying agents, malic acid (MA) extracted from the apple, has been used to modify the gypsum surface towards developing a low-cost, bio-degradable, and more bio-compatible gypsum/PBAT composite, and compared with that of the PEG and SA treated gypsum.25-27
Experimental
The PBAT (Polybutylene adipate terephthalate) (Solpol 1000) was purchased from GIOSOL Ltd. (South Korea). The by-product gypsum was supplied by Namhae Chemical Co. Ltd. (South Korea). The gypsum was treated with stearic acid (SA), polyethylene glycol (PEG), and malic acid (MA). The treated gypsum samples were designated as SA-gypsum, PEG-gypsum and MA-gypsum, respectively. Typically, each of the surface modifying agents (as 6 phr) were added first with 100 part of water and stirred (with 500-600 rpm stirring speed) for 3 hours at room temperature. Later, the dispersions were filtered through filter paper (5 μm pore size) and dried at 150°C for 24 hours.
At first, the dried polymers were premixed individually with the modified-gypsum powders (20 wt% of total quantity) by tumbling, and then, the mixtures were compounded by a co-rotating twin screw extruder (BA-19, BauTek) to obtain the blends of PBAT with SA-gypsum, PEG-gypsum and MA-gypsum. The velocity of screw rotation was 80 rpm. The temperature of zones from hopper to die were 130, 140, 150, 160, 170, 180, and 190 °C. The extruded blends were cooled in water bath and then pelletized. The pelletized blends were injection-molded by an injection-molding machine (WL-HV-80, Wonil Hydraulic). Corresponding injecting temperature of zones from hopper to nozzle were 130, 140, 150, and 150°C. Instead of changing the filler contents, different fillers (i.e., the gypsum modified with different surface modifying agents) at a fixed content (i.e., 20 wt%) has been examined here to realize the effect of the surface modifying agent for developing a better quality PBAT composite to ensure the future prospect of waste gypsum towards enriching the concept “circular economy”.
Mechanical properties of the composites were investigated using the universal tensile tester (Tensometer 2000, Myung Ji tech). The tensile strength and elongation at break were measured according to the ASTM D638 standard under crosshead speed of 50 mm/min. The thermal properties of the composites were examined by using the thermogravimetric analysis (TGA). For TGA, the samples were heated to 600°C with a heating rate of 20°C/min in nitrogen atmosphere. The field emission scanning electron microscopy (FE-SEM) (JSM-7610F, JEOL) was used to investigate the morphologies of the composites.
Results and Discussion
In this work, gypsum with or without its surface modification has been used as filler towards developing mechanically improved low-cost PBAT composite. In this regard, the waste gypsum has been treated with different modifying agents namely SA, PEG and MA through simple solution technique. The electrostatic interaction between the gypsum surface and polar functionalities of surface modifying agents is considered as the main reason for the effective surface treatment. Consequently, the modifier having a greater number of polar functionalities is expected to be more effective. In the present investigation thus, MA, because of its hydroxyl (-OH) and carboxyl (-COOH) functional groups, pertain to more effective surface modifying agent compared to the SA and PEG. For clarity, Figure 1(a) depicts the chemical structure of SA, PEG and MA. In addition to the polar –COOH group in SA, the long aliphatic chain, because of its possible non-interacting behavior with the gypsum, can be considered for the improper and ineffective surface treatment. On the contrary, PBAT (as shown in Figure 1(b)), because of its abundant polar functional groups, also can cause well dispersion of gypsum within the polymer matrix. The compatibility and dispersion can be improved after surface modification because of synergistic influence of both the polar-polar and nonpolar-nonpolar interaction among the PBAT matrix and surface functionalities of the modified gypsum (as schematically represented in Figure 1(c)).
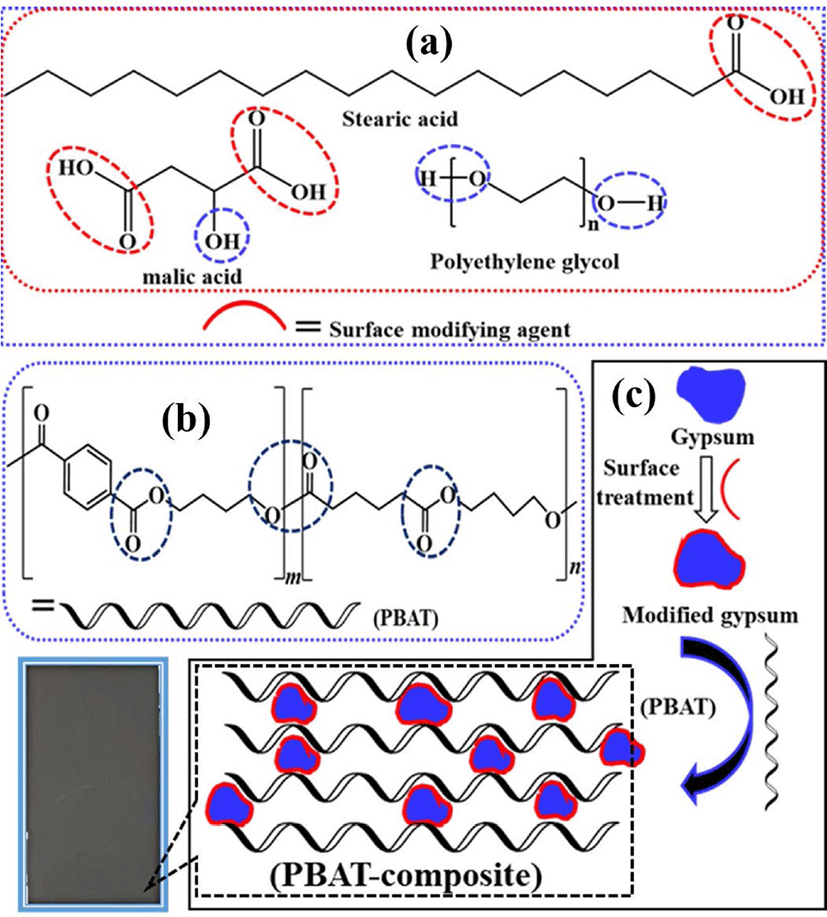
Figure 2 represents the SEM micrographs of the gypsum-PBAT composites. It can be observed that the composite of PBAT with untreated gypsum exhibits good morphology but has agglomeration (as marked by black circle) (Figure 2(a)). Although, because of abundant polar functionalities, PBAT is expected to execute electrostatic interaction with the gypsum, the dispersion gypsum within the PBAT matrix was observed not to be homogenous. Considering the enhanced dispersibility by increasing the filler-matrix compatibility through the surface modification of filler, herein we have modified the gypsum surface with different surface modifying agents namely, SA, PEG and MA. For SA-modified gypsum, it can be noticed that although the fillers are supposed to be homogeneously dispersed, the surface morphology is not good (as shown in Figure 2(b)). The long aliphatic chain of SA can be considered here to prevent the dispersion of filler within the matrix. In contrast, the PEG-modified gypsum shows better dispersion, but again the morphology is not good (as shown in Figure 2(c)). It is supposed here that if the polar functionalities of the surface modifying agent are increased, the better modification followed by better dispersion and formulation of good PBAT composite can be achieved. From Figure 2(d), it can be observed that the morphology of the PBAT composite containing MA-modified gypsum shows a better morphology. In contrast to SA and PEG, the greater number of polar functional groups i.e. both the -OH and -COOH of MA is supposed here as the key contributing factor for this better morphology of MA modified gypsum-PBAT composite. As a consequence of better dispersion as evidenced from Figure 2, it is expected that the PBAT composite of MA modified gypsum (i.e., PBAT/MA-gypsum) will exhibit better thermal and mechanical properties.
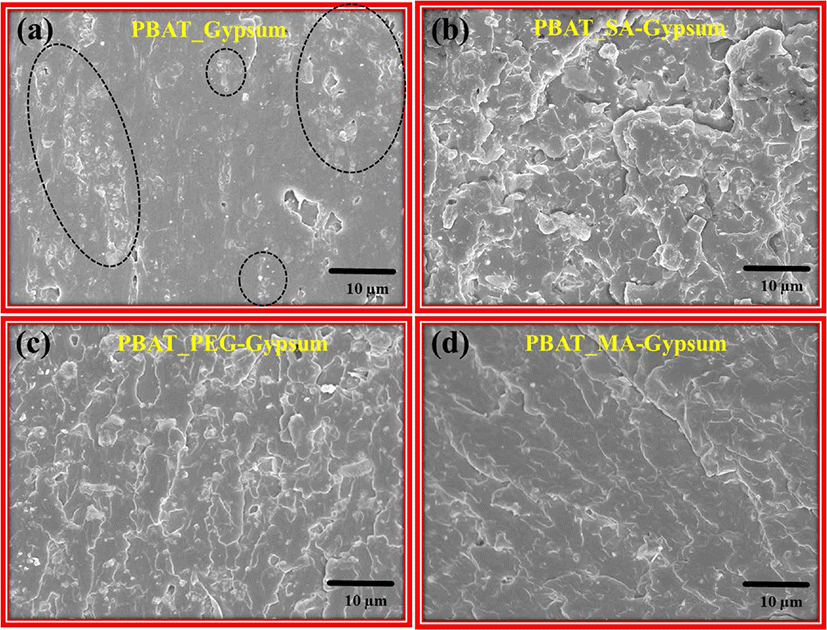
The tensile tests of the samples were performed under uniaxial disposition (strain) according to the ASTM D638 standard. The results of the comparative tensile strength, secant modulus and the elongation at break of the composites are shown in Figure 3. It can be observed that the composites containing PEG-gypsum and MA-gypsum exhibit enhanced tensile strength (Figure 2(b)) in comparison to that of the untreated and SA-treated gypsum. When analyzing the secant modulus (Figure 2(b)), it was observed that the composite of MA-gypsum exhibits slightly lower value of secant modulus which implies its lower stiffness. In case of elongation at break, it is observed that the composite containing MA-gypsum exhibits higher value of elongation at break in comparison to that of the SA-gypsum and PEG-gypsum. Thus, it can be said that the MA-treatment of gypsum enables the formulation of mechanically improved PBAT-composite in comparison to that of the SA- and PEG-treatment. The better filler-matrix interaction followed by formulation of homogenously dispersed PBAT composite is proved by the improved mechanical property. Considering the good mechanical performance of the composite (i.e., higher value of tensile strength, and considerable elongation at break), and the bio-availability of MA, it can be said that the PBAT composite with MA-gypsum may be considered as superior composite for industrial upscaling.
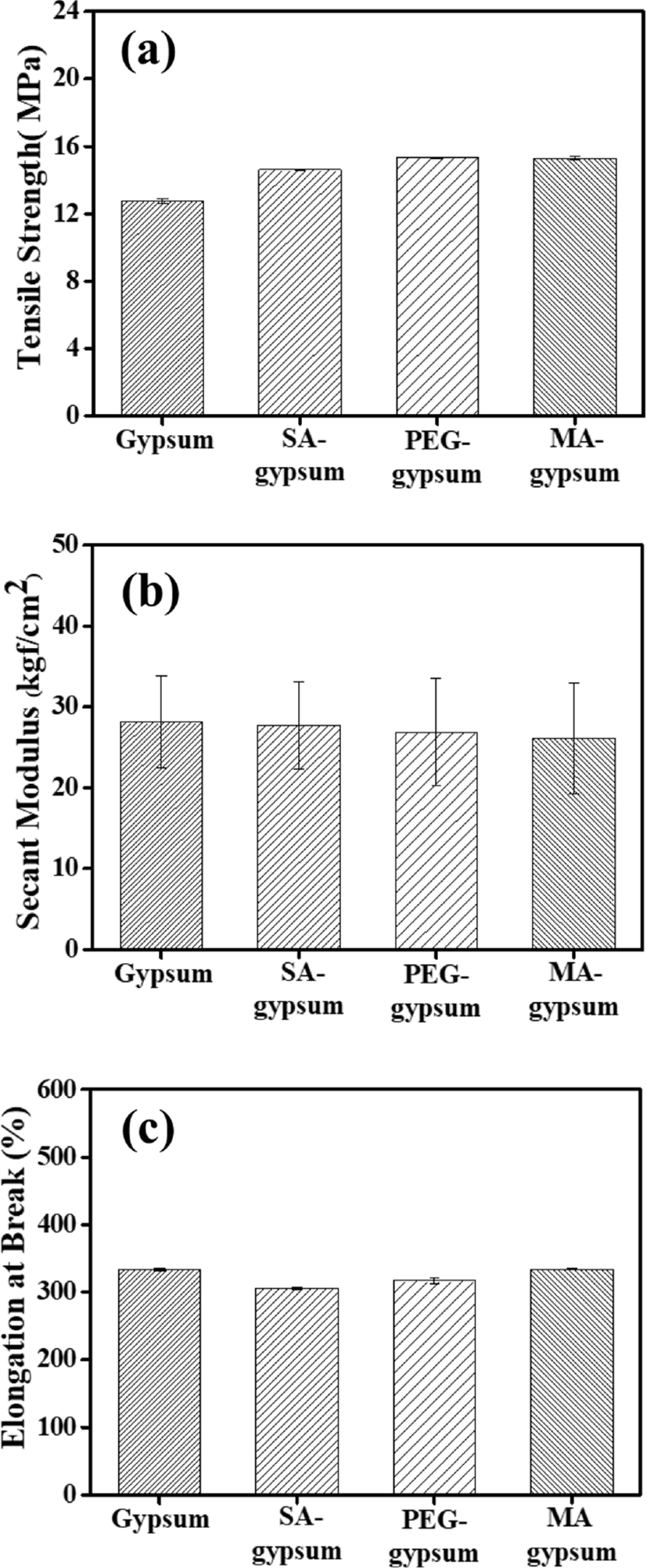
The TGA of the composite samples was investigated to check their thermal stability, as shown in Figure 4. It can be observed that the composite containing MA-gypsum exhibits better thermal stability in the region of 300°C (as shown in Figure 4 and its enlarged part) in comparison to that of other composites. Better dispersion of the MA-gypsum in the composite is the reason for this enhanced thermal stability. Thus, the results obtained from thermal analyses well corroborates with our presumption and the mechanical properties.
Again, to confirm the effect of MA-treated gypsum (i.e., MA-gypsum) content on the mechanical performance of corresponding PBAT composites (i.e., MA-gypsum/PBAT), the tensile strength and elongation at break of the composite containing various amount of the treated gypsum (i.e., 0, 20, 30 and 40 wt%) have been compared with that of the untreated gypsum (as shown in Figure 5(a) and (b)). From the figures, it can be observed that the maximum tensile strength and elongation at break was achieved for 20 wt% of MA-gypsum loading, which infers that this particular content of treated gypsum met the perfect filler/matrix ratio.
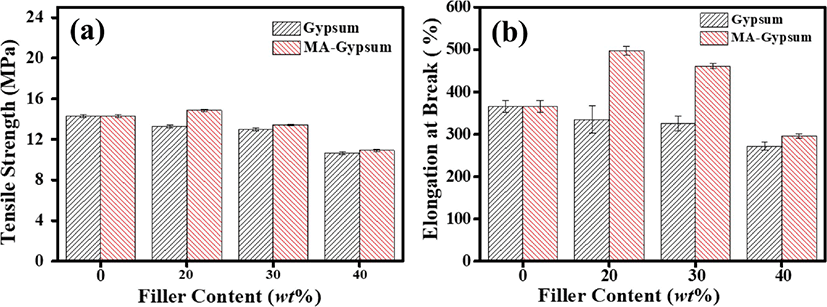
Further, considering the PLA being a biopolymer having outstanding mechanical performance (especially strength and modulus)8,28 the composite of PLA with the PBAT/MA-gypsum has been formulated where the gypsum content was kept constant (i.e., 20 wt%) and the content of PLA and PBAT were varied. Figure 6(a) and (b) exhibit the comparative tensile strength and elongation at break of the gypsum/PLA/PBAT and MA-gypsum/PLA/PBAT. Both the tensile strength and elongation at break was found to be improved at a PLA content of 7.5 wt% for the composite containing the MA treated gypsum. For the composites containing untreated gypsum, incorporation of PLA showed no such changes in their mechanical performances. Improvement in the mechanical performances of MA-gypsum/PLA/PBAT is the consequence of better dispersion of PLA in the MA-gypsum/PBAT through the polar-polar interaction among all the ingredients. Thus, an improved mechanical performance of PBAT was achieved through addition of MA-treated gypsum and PLA.
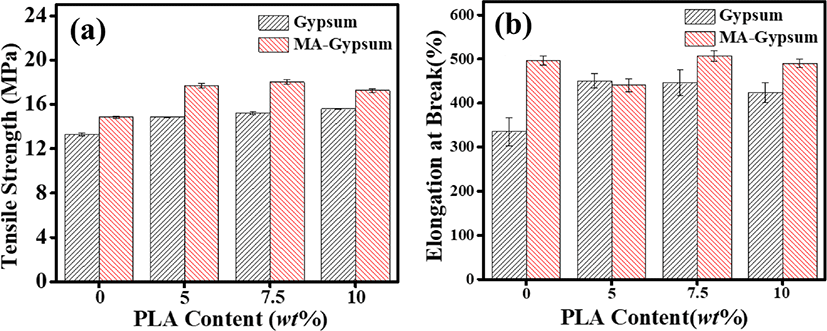
Conclusions
Herein, we have attempted to investigate the usability of waste gypsum for developing the mechanically improved biodegradable PBAT composites to be used in production of different commodity products. Different surface modifying agents e.g. stearic acid (SA), polyethylene glycol (PEG), and malic acid (MA) have been used to modify the gypsum ensuring better dispersion of gypsum within the PBAT matrix towards preparing a mechanically improved PBAT composite having both the higher value of tensile strength and elongation at break. Compared to the other surface treated gypsum, MA-gypsum enabled better performing PBAT composite. Addition of PLA was found to enhance the mechanical performance of MA-gypsum/PBAT. Choice of surface modifying agent for effective surface treatment of waste gypsum followed by its use as filler material towards developing a low-cost and high-performing PBAT-composites (with or without PLA) can be considered as futuristic industrial approach.