Introduction
타이어의 수명과 교체 시기는 주로 트레드의 마모 정도에 의해 결정된다. 또한 타이어 트레드의 마모는 안전과 직결되는 것은 물론이고 비배기관 유래 미세먼지의 주요 발생원이기도 하다.1 비배기관 유래 오염 중 타이어 마모에 의한 비중은 30% 정도로 보고하고 있으나, 도로와 주행 조건 그리고 타이어 상태 등에 따라 그 정도가 달라진다.2-4 도로에서 발생된 타이어 트레드 마모입자는 강, 하천, 호수, 바다 등에 흘러 들어가 퇴적되거나 토양에 축적될 수 있으므로, 타이어 마모입자가 환경에 미치는 영향에 대한 관심이 증대되고 있다.
실제 주행에 의해 타이어 마모 특성을 연구하기 위해서는 많은 시간과 노력이 필요하고 비용도 적지 않게 들기 때문에 다양한 마모시험기를 사용하고 있다.5-8 Laboratory Abrasion Tester (LAT 100)는 여러 주행 조건을 반영하여 평가할 수 있는 실험실용 타이어 마모시험기로 이를 이용한 ISO 규격과 타이어 마모에 대한 연구 결과를 발표한 사례들이 있다.9-12 본 연구에서는 버스/트럭 타이어 트레드용 모델 고무 배합물로 NR/BR 블렌드 시험편을 제조하여 LAT 100 실내 마모시험기로 고무 조성비와 슬립각(slip angle, 횡활각, 미끄럼각, 옆미끄럼각)에 따른 마모 특성을 연구하였다. 마모속도와 마모입자 크기를 분석하여 고무 조성비와 슬립각이 마모 특성에 미치는 영향을 조사하였다.
Experimental
본 연구에서 사용한 모델 고무 시험편의 고무 조성은 NR = 100 (sample code: NRBR0), NR/BR = 80/20 (sample code: NRBR2), NR/BR = 60/40 (sample code: NRBR4)이며, 카본블랙(N234) 함량은 60 phr로 일정하게 하였다. 고무 조성을 제외한 나머지 성분과 함량은 동일하게 설계하였다. 시험편 코드(sample code)는 NR과 BR의 블렌드로 BR 함량을 수치로 표기하여 NRBR#로 나타내었다.
VMI group의 LAT 100 실험실 마모시험기를 사용하여 마모시험을 진행하였다. 로드 하중은 75 N이고, 속도는 25 km/h, 슬립각은 1°와 7°이다. 마모 시험편의 크기는 직경 83 mm이고 두께 19 mm이다. 연마판(abrasive disk)은 VMI group의 Electro Corundum Disc Grain 60을 사용하였다. 마모 입자는 Octagon 200 (Endecotts Co.) 체진동기를 사용하여 크기별로 분리하였다. 사용한 체의 크기는 1 mm, 500 μm, 212 μm, 106 μm, 63 μm, 38 μm이다. 입자 형상 분석은 영상분석기(image analyzer, EGVM 35B, EG Tech)를 사용하여 실시하였다.
Results and Discussion
체진동기를 이용하여 크기별로 분류한 결과를 원그래프(pie chart)로 나타내었으며 고무 조성별로 제시하였다(Figures 1-3). 시험편 NRBR0 (NR = 100)의 경우, 마모입자는 매우 커서 대부분 1,000 μm 이상이었다. 슬립각 1° 일 때는 1,000 μm 이상의 마모입자가 99% 정도였으며, 슬립각 7°일 때는 90% 정도였다(Figure 1). 슬립각이 1° 에서 7° 로 커지면 212-1,000 μm의 마모입자가 8배 정도 증가하였으며 미량이나마 63 μm 미만의 작은 크기의 마모입자도 검출되었다. Figure 2는 NR/BR = 80/20인 시험편 NRBR2의 마모입자 크기 분포를 나타낸 것으로, 슬립각 1° 일 때는 1,000 μm 이상의 마모입자가 90% 정도로 대부분을 차지하였으나, 슬립각 7° 에서는 1,000 μm 이상의 마모입자가 10%로 매우 크게 감소했음을 알 수 있다. 슬립각이 1° 에서 7° 도 커지면서 1,000 μm 이상의 큰 마모입자가 1/9로 줄어들었고 이보다 작은 마모입자가 9배 늘었다. 슬립각 7°에서는 212-500 μm의 마모입자가 66%로 월등히 높은 비율을 차지했으며 슬립각 1° 대비 20배 이상 증가하였다. 슬립각 1° 에서는 38 μm 미만의 마모입자는 검출되지 않았으나, 슬립각 7°에서는 20 μm 미만의 마모입자도 매우 적은 양이지만 생성되었다.
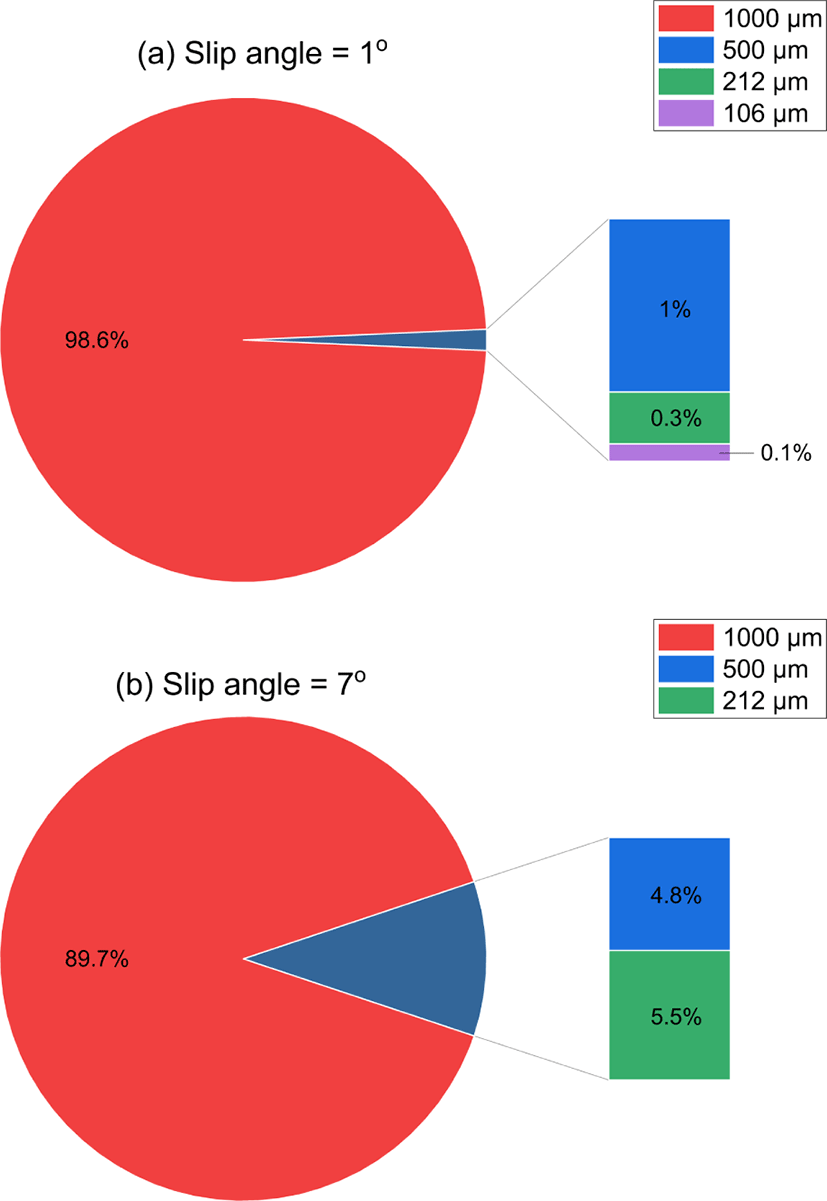
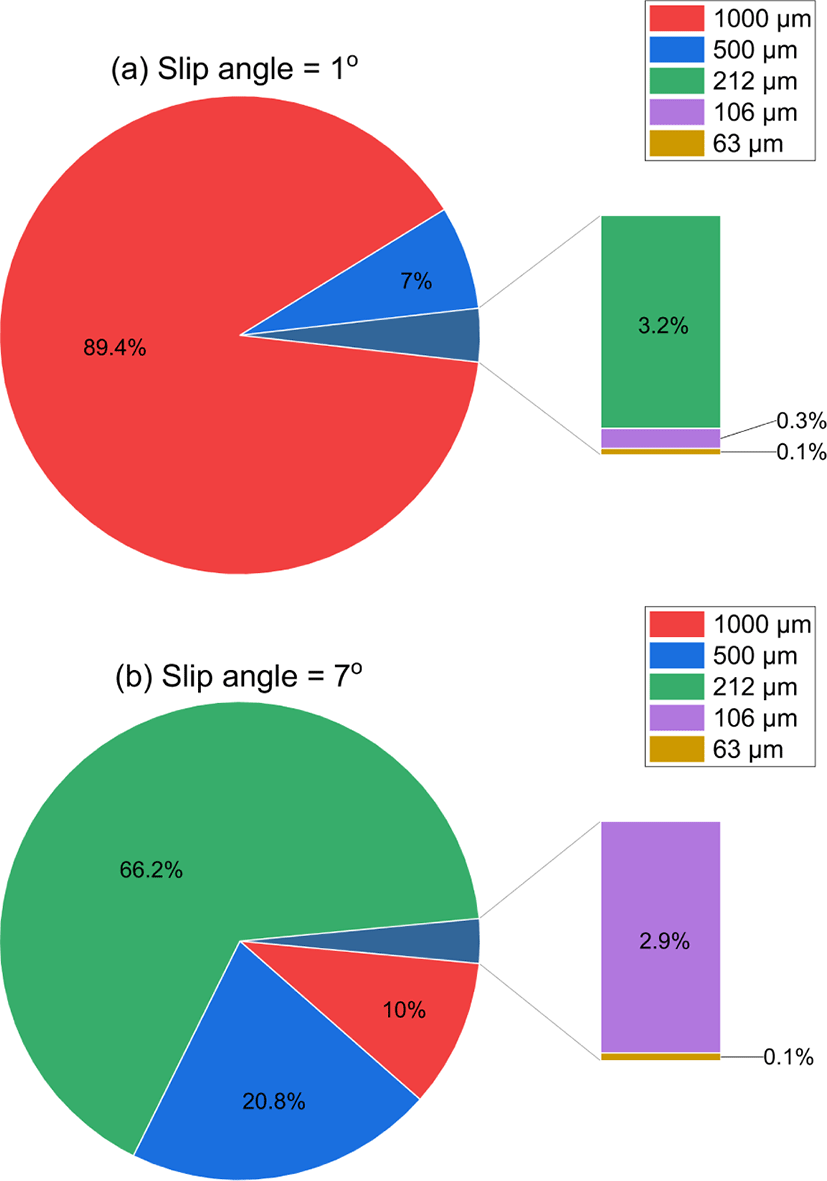
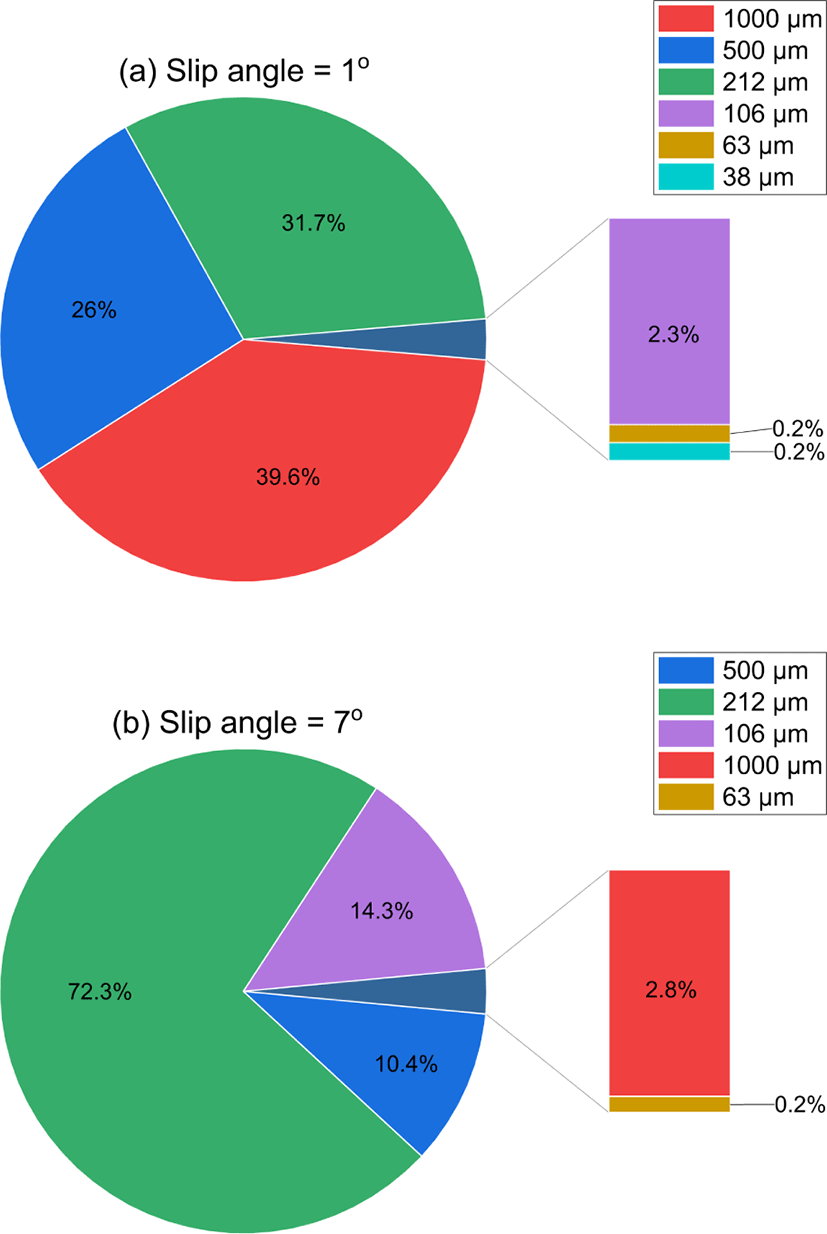
NR/BR = 60/40인 시험편 NRBR4의 경우에는 다른 시험편보다 슬립각 1° 에서 1,000 μm 이상의 마모입자 비율이 크게 감소하였으나 여전히 40% 정도로 가장 높은 비율을 차지하고 있다(Figure 3). 슬립각 7° 에서는 1,000 μm 이상의 마모입자 비율은 크게 감소하여 3% 정도였다. 슬립각이 1° 에서 7°로 커지면서 1,000 μm 이상의 큰 마모입자가 1/14로 줄어든 반면 나머지 크기의 마모입자는 1.5배 증가하였다. 특히, 슬립각 7° 에서는 212-500 μm의 마모입자가 70% 이상으로 가장 많이 차지하였으며, 106-212 μm의 마모입자도 슬립각 1°보다 6배 이상 높았다. 슬립각 1° 에서도 212-500 μm의 마모입자 비율은 30%가 넘었다. 슬립각 1° 에서는 1,000 μm 이상, 500-1,000 μm, 212-500 μm의 마모입자 비율이 거의 비슷하여 삼등분하는 분포를 나타내었다. 슬립각 7° 에서는 212-500 μm의 마모입자를 중심으로 더 큰 입자와 더 작은 입자 쪽으로 비율이 작아지는 분포를 나타내었다. 시험편 NRBR4도 시험편 NRBR2와 마찬가지로 슬립각 1° 에서는 38 μm 미만의 마모입자는 검출되지 않았으나, 슬립각 7° 에서는 38 μm 미만의 마모입자뿐만 아니라 20 μm 미만의 마모입자도 매우 적은 양이지만 검출되었다.
슬립각에 따른 마모입자 크기 분포 결과에서 슬립각이 커지면 고무 조성비에 무관하게 생성된 마모입자의 크기가 상대적으로 작아지는 것을 확인할 수 있었다. 이는 슬립각이 커지면 횡력(lateral force)이 크게 작용하기 때문으로 해석할 수 있다. 횡력이 크게 작용하면 연마판과 맞닿은 시험편 부분이 크게 변형되고 마찰력도 증가하기 때문이다.
고무 조성과 슬립각에 따른 마모속도(abrasion rate) 변화를 Table 1에 정리하였다. 마모속도는 시험편 마모량을 주행거리(= 시험시간 × 속도)로 나눈 값이다. 슬립각이 1° 에서 7° 로 커지면 마모속도가 수십 배 이상 급격히 증가하였다: 시험편 NRBR0, NRBR2, NRBR4의 경우 각각 마모속도가 139 배, 89 배, 46 배 증가하였다. 슬립각이 1° 에서 7° 로 증가함에 따른 마모속도의 증가는 BR 함량이 증가할수록 그 정도가 감소하였다. 슬립각이 1° 로 변형이 작은 경우에는 BR 함량이 증가할수록 마모속도가 크게 증가하였다. NR = 100인 시험편(NRBR0)보다 NR/BR = 80/20인 시험편(NRBR2)의 마모속도가 2배 이상 높았으며, NR/BR = 60/40인 시험편(NRBR4)의 마모속도는 NR/BR = 80/20인 시험편(NRBR2)의 마모속도보다 2배 정도 높았다. 하지만 슬립각이 7° 로 변형이 큰 경우에는 고무 조성에 따른 마모속도의 차이는 크게 줄었으며, 시험편 NRBR4의 마모속도는 시험편 NRBR2의 마모속도보다 오히려 낮았다. 일반적으로 BR은 NR에 비해 탄성과 내마모성이 우수하다고 알려져 있으나, 본 연구 결과에 의하면 NR에 BR을 혼합하면 오히려 마모속도가 증가하는 것으로 나타났다.
Sample code | NRBR0 | NRBR2 | NRBR4 | |||
---|---|---|---|---|---|---|
Slip angle | 1° | 7° | 1° | 7° | 1° | 7° |
Abrasion rate | 4.1 | 568.9 | 9.1 | 815.4 | 17.4 | 795.3 |
고무 조성에 따른 마모입자의 크기 분포 변화를 Figures 4와 5에 나타내었다. 슬립각이 1° 인 경우에는 마모입자의 크기가 1,000 μm 이상인 것의 비율이 가장 높았으며, BR 함량이 증가할수록 1,000 μm 이상이 마모입자 비율은 크게 줄어들었으며 크기가 작은 마모입자의 비율이 상대적으로 증가하였다. 이는 NR이 BR보다 더 잘 늘어나서 작은 변형에 의해 마모입자가 잘 발생하지 않고 시험편 표면에 흠집(크랙 등)이 누적되어 상대적으로 큰 마모입자를 형성하기 때문으로 여겨진다. 슬립각이 1°인 경우에는 38 μm 이하의 미세 마모입자가 생성되지 않았다. 슬립각이 7°인 경우, NR = 100인 시험편에서는 여전히 1,000 μm 이상의 마모입자 비율이 90% 정도였으나 NR/BR 블렌드 시험편에서는 1,000 μm 이상의 마모입자 비율이 10% 이하로 크게 감소하였다. NR/BR 블렌드 시험편에서 가장 비율이 높은 마모입자의 크기는 212-500 μm 였으며 그 비율도 50% 이상으로 매우 높았다. 슬립각이 7° 인 경우에는 38 μm 이하의 미세 마모입자가 미량으로나마 발생하였다. 슬립각이 커지면 작은 크기의 마모입자가 상대적으로 증가하였으며 BR 함량이 증가할수록 작은 크기의 마모입자 함량이 증가하였다. 실험 결과에 의하면 NR에 BR을 혼합함으로써 발생되는 마모입자 크기는 작아진다고 할 수 있다.
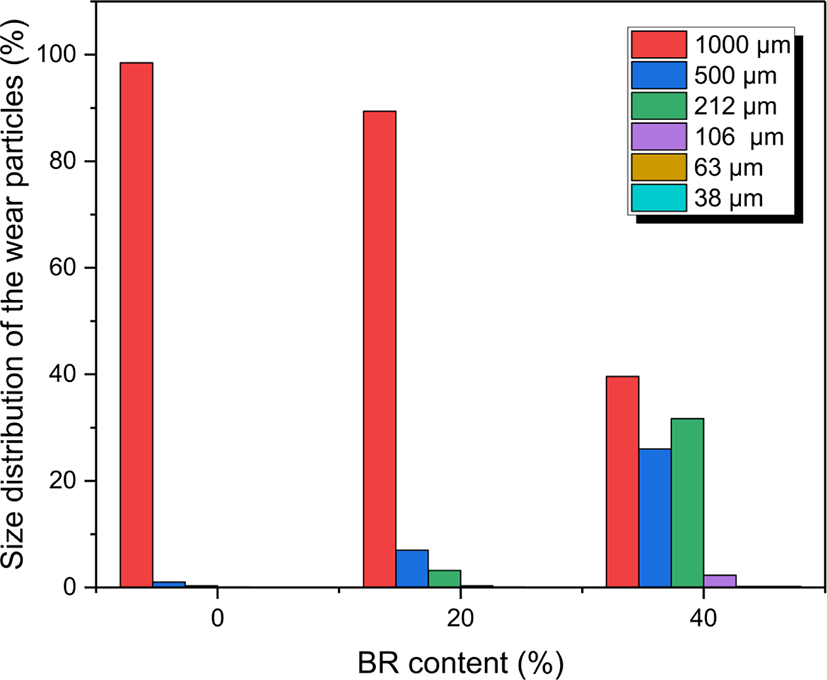
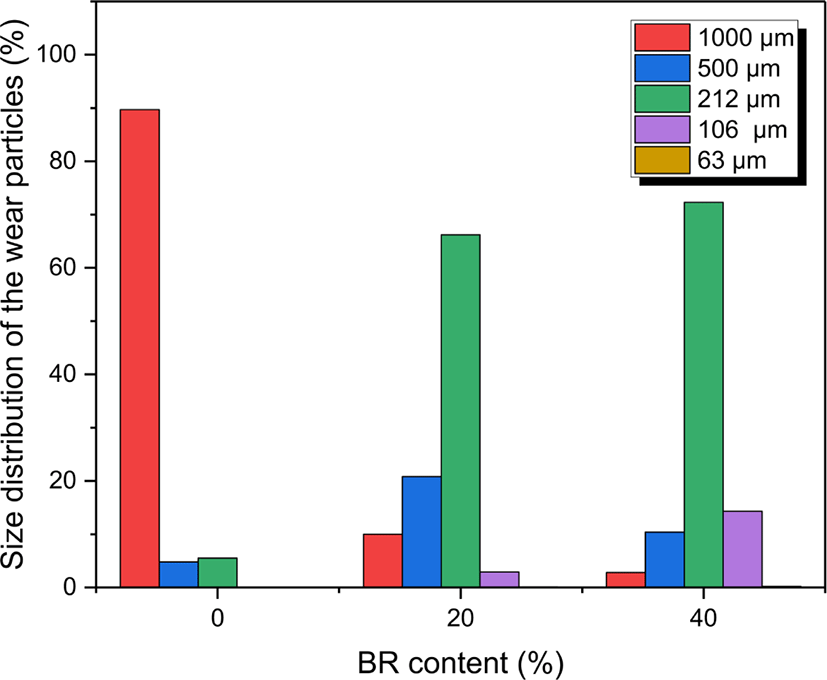
마모입자의 형상을 확대 관찰하였으며 그 결과를 Figures 6-9에 제시하였다. 1,000 μm 이상의 마모입자는 대부분 일정한 형태를 보이지 않고 덩어리를 이루고 있는 형상이었다. 슬립각 7° 에서 생성된 마모입자의 표면 요철이 슬립각 1°에서 생성된 것보다 상대적으로 더 심한 경향을 보였다(Figure 6). 1,000 μm 이하의 마모입자는 Figures 7-9에서 보는 바와 같이 주로 길쭉한 형상을 보이나 둥그런 형태의 것도 있다. 500-1,000 μm 마모입자에는 어느 정도 큰 덩어리를 이루고 있는 것도 있으며, 슬립각 7° 에서 생성된 마모입자에는 슬립각 1°에서 생성된 것보다 곁가지가 있는 것들이 상대적으로 더 많이 나타났다. 212-500 μm 마모입자의 형상은 대체적으로 길쭉하였으며, 슬립각 1° 에서 생성된 마모입자에는 요철이 심하지 않았으나, 슬립각 7° 에서 생성된 마모입자에는 요철이 상대적으로 많았으며 곁가지가 있는 것들도 나타났다. 106-212 μm 마모입자의 형상도 대체적으로 길쭉하였으나 큰 마모입자에 비해 표면 요철이 더 심하게 나타났다. 마모입자의 형상은 마모입자 크기나 고무 조성비 그리고 슬립각에 따라 약간의 차이는 보이나 그 형상이 다양하여 뚜렷한 차이점은 발견되지 않았다.
Conclusions
버스/트럭 타이어 트레드용 모델 고무 배합물로 NR/BR 블렌드 시험편을 제조하여 실내 마모시험기로 고무 조성비와 슬립각에 따른 마모 특성을 연구하였다. NR에 BR을 혼합하면 오히려 마모속도가 증가하는 경향을 보였으며, 특히 슬립각이 작은 1°인 경우에 BR 함량 증가에 따른 마모속도 증가 경향이 뚜렷하게 나타났다. 일반적으로 BR은 NR에 비해 탄성과 내마모성이 우수하다고 알려져 있으나, 본 연구 결과에 의하면 NR = 100인 시험편보다 NR/BR 블렌드 시험편의 마모속도가 더 큰 것으로 나타났다. 슬립각이 커지면 마모입자 크기는 크게 줄어들었으며, 이러한 경향은 NR = 100인 시험편보다 NR/BR 블렌드 시험편에서 두드러지게 나타났다. 슬립각이 커지면 작은 크기의 마모입자가 상대적으로 증가하였으며 BR 함량이 증가할수록 작은 크기의 마모입자 함량이 증가하였다. BR 함량이 증가할수록 작은 크기의 마모입자 함량이 증가하는 것은 NR이 더 잘 늘어나서 상대적으로 큰 마모입자를 형성하는 것으로 해석할 수 있다. 마모입자의 형상은 매우 다양하였으며 마모입자 크기나 고무 조성비 그리고 슬립각에 따른 뚜렷한 차이점은 발견되지 않았다.